Have you ever wondered what is a machining center and how it transforms modern manufacturing? Do you know the different types of machining centers and what different applications they are used for? Have you explored how a machining center performs milling, drilling, and boring operations with precision? Perhaps you’re curious about how these versatile machines improve efficiency and consistency in complex manufacturing processes?
A machining center is an advanced CNC machine tool that combines milling, drilling, boring, and tapping into a single automated system. Equipped with an automatic tool changer (ATC) and a CNC control system, it performs multiple operations in one setup, minimizing errors and reducing production time. Machining centers come in various types, such as vertical, horizontal, and 5-axis, catering to a wide range of applications across industries. They significantly improve precision, efficiency, and consistency in manufacturing.
Continue reading this article to uncover what is a machining center and the different types of machining centers, explore their key features, understand their working principles, and discover how they can revolutionize efficiency and precision in your manufacturing processes.
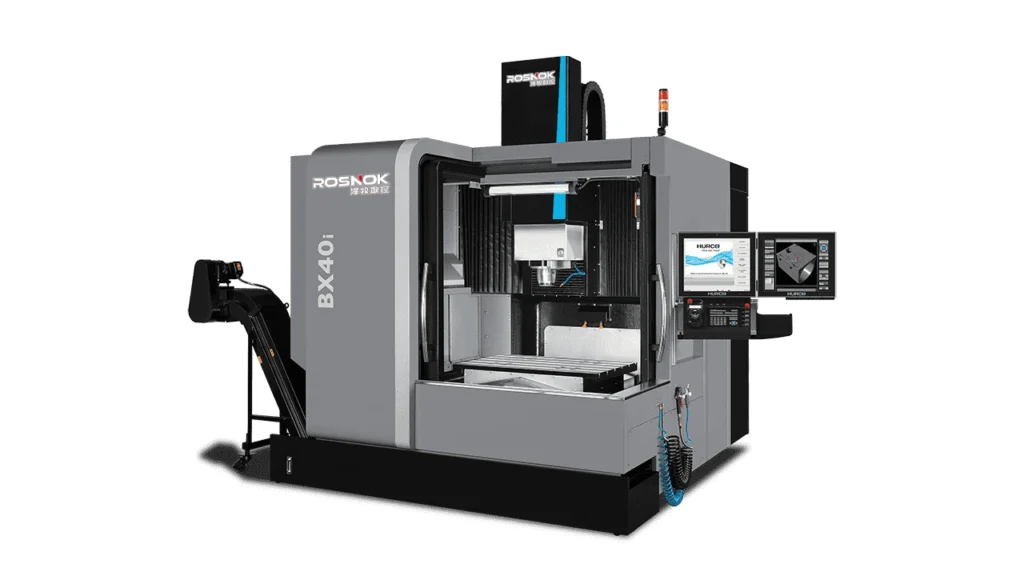
What is a Machining Center?
Machining center definition: A machining center is a CNC (Computer Numerical Control) machine tool with a very high degree of automation that performs multiple machining operations—such as milling, drilling, boring, tapping, and, in some cases, even turning—in a single setup. Designed to reduce manual intervention and increase efficiency, machining centers automate complex machining processes with high precision and consistency.
These machines are equipped with a CNC control system that governs tool movements and ensures accuracy throughout the machining process. Additionally, most machining centers feature an automatic tool changer (ATC) that switches between different tools seamlessly, minimizing downtime and enhancing productivity.
Due to their ability to combine various machining processes in one machine, machining centers are widely used in industries requiring high-precision, high-efficiency production. They offer exceptional flexibility and reliability, making them a cornerstone of modern manufacturing.
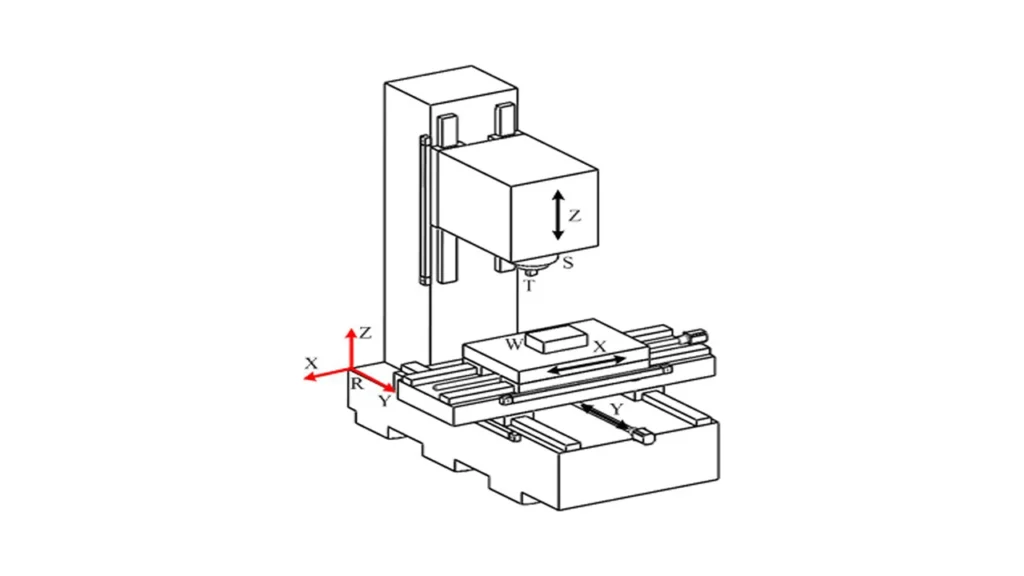
How Does a Machining Center Work?
A machining center operates through a highly automated process governed by a CNC (Computer Numerical Control) system, enabling precise control over the machine’s movements and operations. By integrating multiple machining functions into a single machine, machining centers minimize errors, reduce production time, and maintain consistent part quality.
The entire machining process is carried out following a pre-programmed CNC code (G-code and M-code) that defines the tool paths, spindle speed, feed rate, and other essential machining parameters. Let’s break down the process step by step to understand how a machining center works.
CNC Program and Setup
The machining center’s operation begins with the creation of a CNC program, which defines the machining sequence and movements. The program typically includes:
- G-code for defining tool movements, positions, and cutting parameters.
- M-code for controlling auxiliary functions like coolant, tool changes, and spindle operation.
Once the program is written and loaded into the CNC control system, the operator sets up the workpiece and secures it on the worktable or fixture to prevent movement during machining. The correct cutting tools are loaded into the automatic tool changer (ATC) to ensure smooth transitions between different machining operations.
Tool Selection and Spindle Operation
After setup, the machining center automatically selects the required cutting tool from the tool magazine using the ATC. The spindle rotates the selected tool at the pre-set speed and feeds it along the designated tool path. The spindle’s speed and direction are carefully controlled based on the material type and machining requirements.
In multi-operation machining processes, the ATC seamlessly switches between tools, allowing for continuous machining without manual intervention.
Workpiece Movement and Machining Process
The CNC system moves the worktable or the spindle in the X, Y, and Z directions, guiding the tool to execute precise cuts. Depending on the type of machining center:
- Vertical Machining Centers (VMC): The spindle moves vertically along the Z-axis, while the worktable moves horizontally along the X and Y axes.
- Horizontal Machining Centers (HMC): The spindle operates horizontally, making it easier to handle deep cavities and large workpieces.
- 5-Axis Machining Centers: Both the worktable and the spindle can move simultaneously along multiple axes to create complex geometries.
Automatic Tool Changes
During machining, different tools may be required for various operations, such as milling, drilling, or tapping. The ATC automatically swaps tools as needed, significantly reducing downtime and increasing efficiency. The process includes:
- Retracting the current tool and returning it to the magazine.
- Retrieving the next tool from the magazine.
- Positioning the new tool with minimal delay to continue the machining process.
Coolant and Chip Removal
Coolant is continuously applied during the machining process to keep the cutting area cool and to prevent excessive tool wear. The coolant also helps in flushing away chips generated during cutting, preventing them from interfering with the machining process.
Modern machining centers come equipped with advanced chip management systems to ensure that chips are efficiently removed, reducing the risk of surface damage and ensuring smooth machining operations.
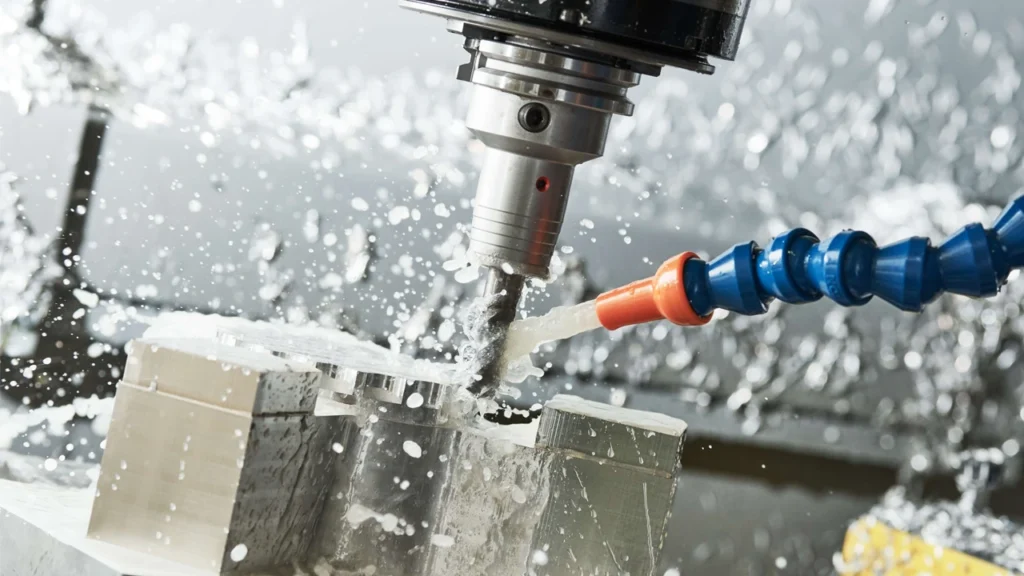
Machining Completion and Quality Inspection
Once all machining operations are completed, the workpiece is inspected for dimensional accuracy and surface finish. High-precision machining centers often include probing systems that automatically check for dimensional accuracy during machining, ensuring that the part meets the required specifications.
With these processes seamlessly integrated into a machining center, manufacturers achieve high-quality, consistent parts while minimizing manual labor and reducing the likelihood of errors.
Key Components of a Machining Center
A machining center consists of multiple highly specialized components that work together to ensure accurate and efficient machining operations. Each component plays a crucial role in maintaining precision, reducing downtime, and enhancing overall productivity. Understanding these components is essential for choosing the right machining center and ensuring optimal performance.
CNC Control System
The CNC control system acts as the brain of the machining center, managing and directing all movements and operations. It processes the pre-programmed G-code and M-code to control tool paths, spindle speed, and feed rate with micrometer-level accuracy.
Key functions of the CNC control system include:
- Translating programmed instructions into machine movements.
- Ensuring synchronized movement of the tool and workpiece.
- Monitoring and adjusting machining parameters in real-time.
Popular CNC control systems include brands such as Fanuc, Siemens, Heidenhain, and Mitsubishi, offering different levels of precision and customization.
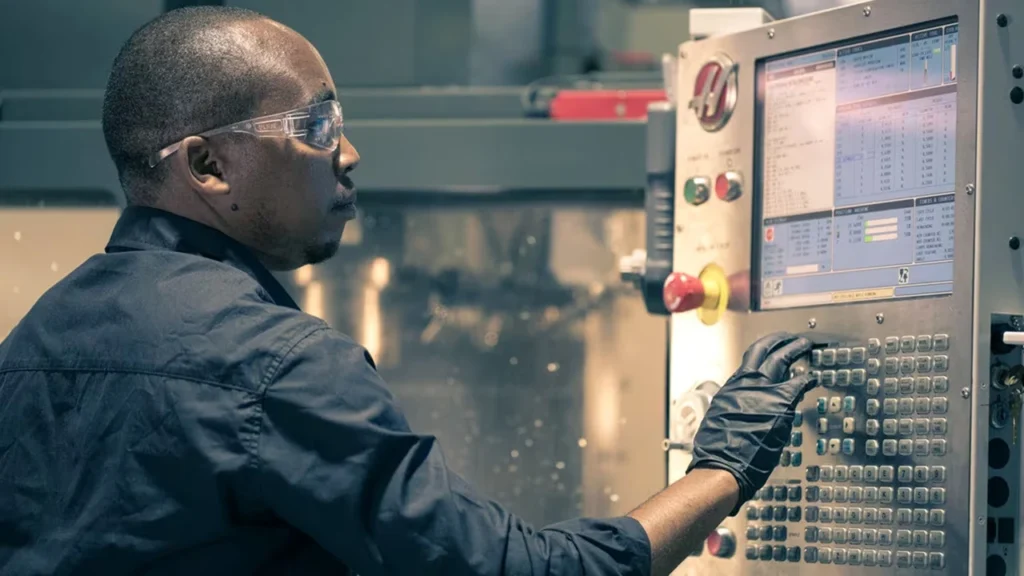
Spindle and Drive System
The spindle is the heart of the machining center, responsible for rotating the cutting tool at high speeds to perform various machining operations. Driven by a motor and gearbox system, the spindle can operate at speeds ranging from a few hundred to tens of thousands of RPM, depending on the application.
There are typically three types of spindles:
- Belt-Driven Spindle: Suitable for general machining applications.
- Direct-Drive Spindle: Offers higher precision and faster speeds.
- Motorized (Built-in) Spindle: Provides ultra-high-speed rotation for specialized applications.
The spindle’s ability to maintain stability at high speeds ensures high-precision cutting and consistent surface finishes.
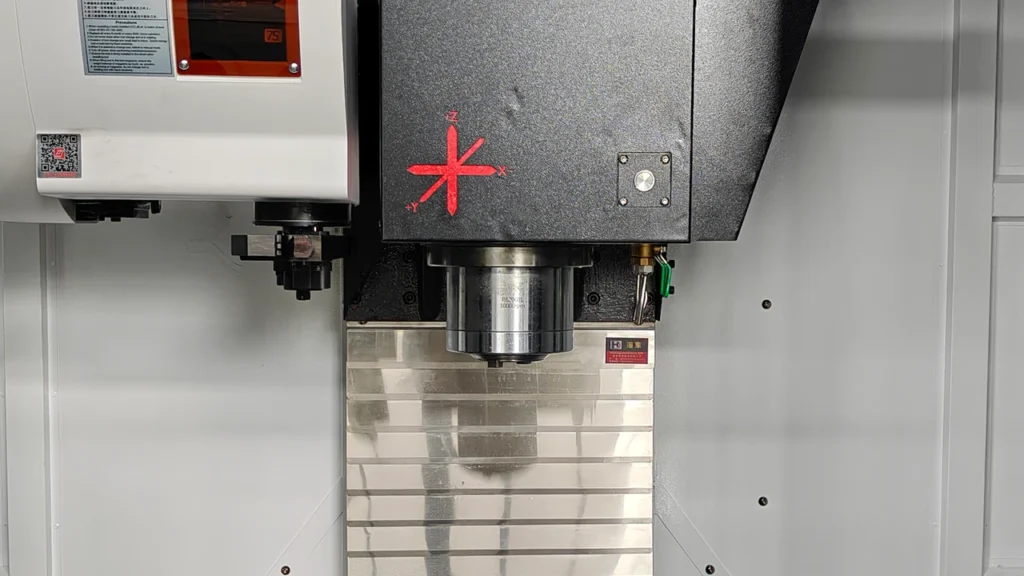
Automatic Tool Changer (ATC)
The automatic tool changer (ATC) enhances the machining center’s flexibility by enabling rapid tool changes during machining. The ATC automatically swaps tools from the tool magazine based on the programmed tool path, minimizing downtime and ensuring seamless transitions between operations.
Types of tool magazines include:
- Carousel Type: Compact and suitable for smaller machining centers.
- Chain-Type/Arm-Type: Provides faster tool changes and higher tool capacity, making it ideal for large-scale production.
Tool Magazine
The tool magazine stores and organizes various cutting tools required for different machining operations. Modern machining centers can accommodate a wide range of tools, from drill bits and end mills to taps and reamers. The capacity of a tool magazine can range from a few tools to over 100, depending on the machine type and configuration.
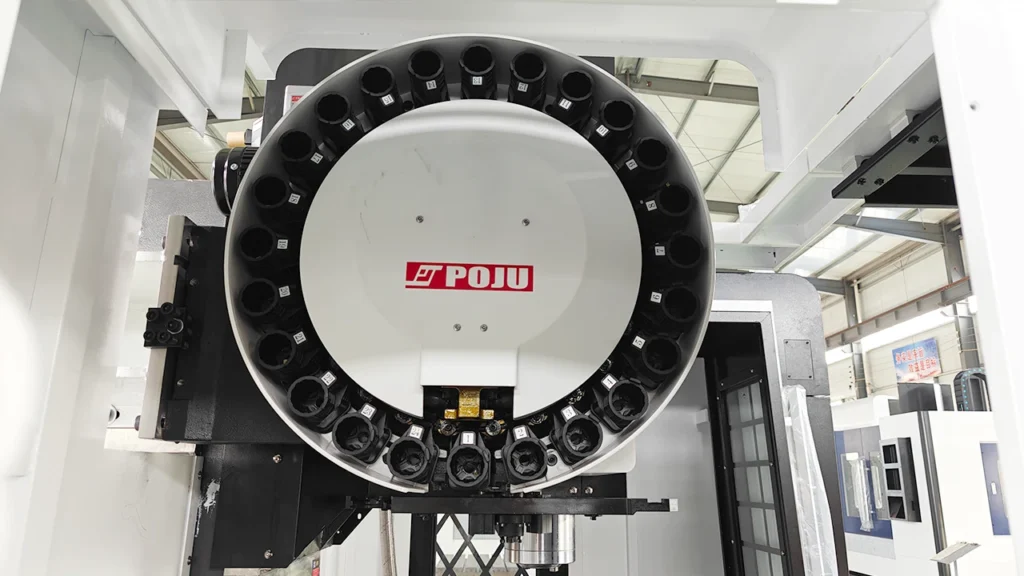
Worktable and Fixturing System
The worktable serves as the platform where the workpiece is clamped and secured. Depending on the type of machining center, the worktable may move along the X, Y, and Z axes to position the workpiece accurately.
Common types of worktables include:
- Fixed Worktable: Provides stability during machining and is used in smaller machining centers.
- Rotary/Indexing Table: Used in 4-axis and 5-axis machining centers to rotate the workpiece, enabling multi-sided machining without re-clamping.
The fixturing system ensures that the workpiece remains securely in place throughout the machining process, minimizing errors caused by vibration or misalignment.
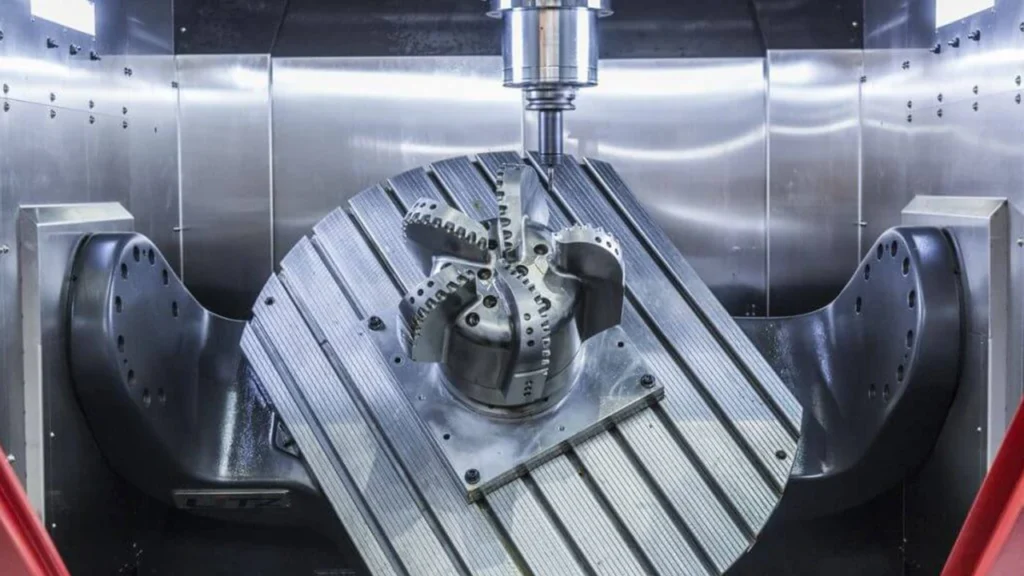
Coolant and Chip Management System
A coolant system is essential to prevent overheating and maintain optimal cutting conditions. Coolant is directed at the cutting area to reduce friction, prolong tool life, and improve surface finish.
The chip management system efficiently removes chips generated during machining to prevent build-up, which can damage the tool or affect the quality of the finished part. Some advanced machining centers use chip conveyors and filtration systems to ensure smooth chip evacuation.
Probe and Inspection System (Optional)
High-end machining centers often come equipped with probing and inspection systems that automatically measure the workpiece’s dimensions and alignment. These systems can detect deviations and make necessary adjustments during the machining process, ensuring high precision and reducing the need for manual quality checks.
Machine Bed and Column
The machine bed forms the structural foundation of the machining center, providing the necessary support for all other components. Typically made of high-strength cast iron or cast steel, the bed ensures maximum rigidity, minimizing deformation and vibrations during machining.
- Machine Bed: Supports the worktable and absorbs the cutting forces generated during machining, ensuring stability and maintaining dimensional accuracy.
- Column: Vertically mounted on the machine bed, the column provides structural support for the spindle head and crossbeam. It ensures stability when the spindle moves along the Z-axis, maintaining precise tool positioning.
The combination of a rigid machine bed and column contributes significantly to the machining center’s ability to deliver high-precision results over prolonged machining operations.
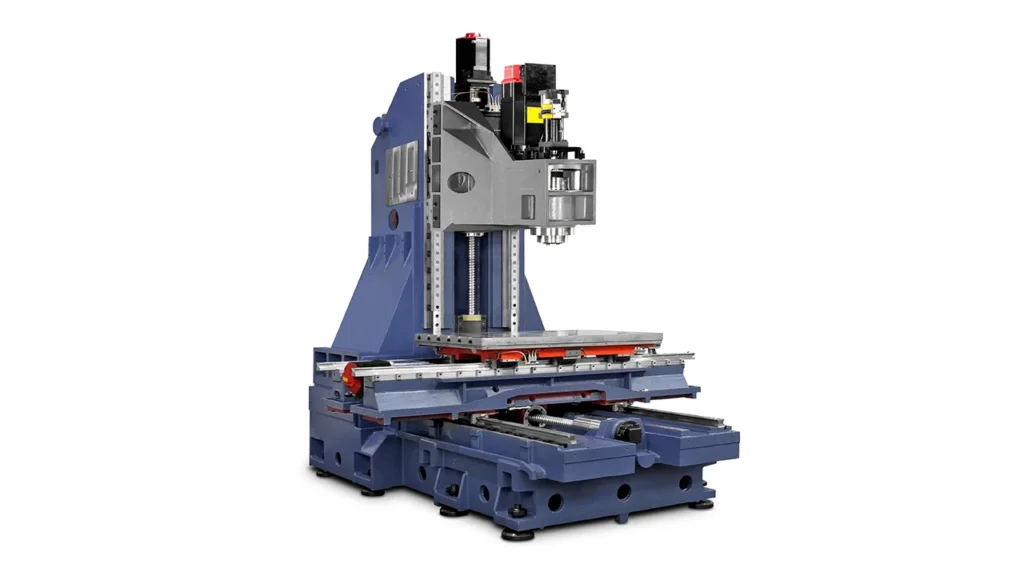
Types of Machining Centers and Their Specialties
Machining centers can be classified based on two primary factors:
- Structure: The orientation and configuration of the machine’s spindle and worktable.
- Number of Axes: The degrees of freedom that control the movement of the cutting tool and workpiece.
Below, we’ll explore these categories in detail and examine the specialties of each type.
Classification by Structure:
Vertical Machining Center (VMC)
A vertical machining center (VMC) features a spindle that is aligned vertically with the worktable. It is ideal for machining flat surfaces, cavities, and intricate designs. VMCs are commonly used in mold manufacturing, aerospace, and automotive industries where high precision is essential.
Key Features:
- Spindle Orientation: Vertical alignment with the worktable.
- Worktable Movement: Moves along the X and Y axes, while the spindle moves along the Z-axis.
- Ideal Applications: Surface machining, die/mold manufacturing, and precision milling.
Specialties:
- High-speed machining for small and medium-sized parts.
- Easy workpiece setup and tool changes.
- Suitable for 3-axis, 4-axis, and 5-axis configurations.
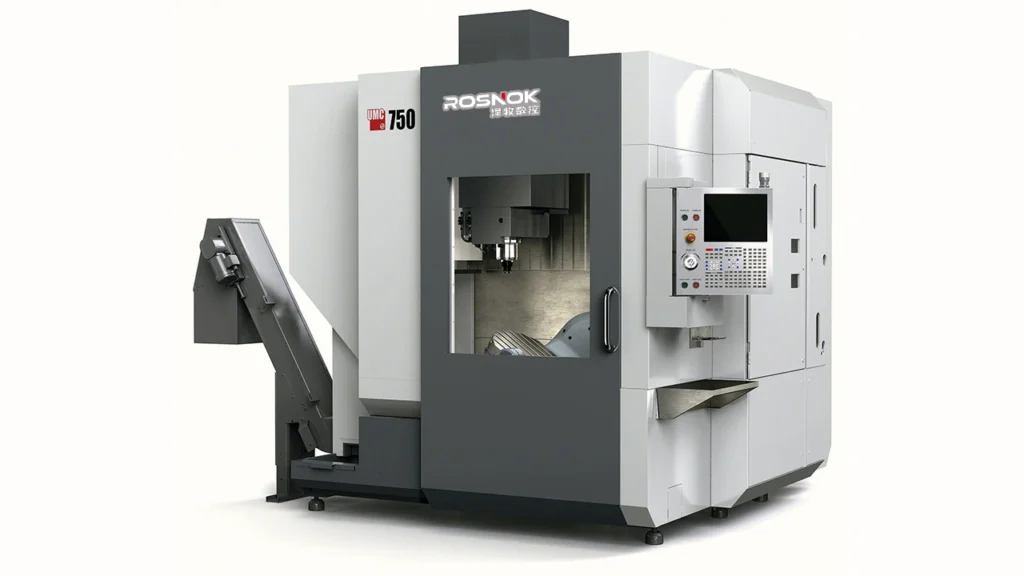
Horizontal Machining Center (HMC)
A horizontal machining center (HMC) features a spindle aligned horizontally with the worktable, allowing for deeper cavity machining and more effective chip evacuation. It excels in high-volume production environments where continuous operation is required and is particularly well-suited for machining large, heavy workpieces that require stability and precision during prolonged machining cycles.
Key Features:
- Spindle Orientation: Horizontal alignment with the worktable.
- Worktable Movement: Moves along the X and Y axes, while the spindle moves along the Z-axis.
- Ideal Applications: Deep cavity machining, large component manufacturing, and mass production.
Specialties:
- Superior chip evacuation, reducing heat buildup and tool wear.
- Ideal for machining complex shapes and deep pockets.
- Capable of high-speed, high-accuracy machining for large workpieces.
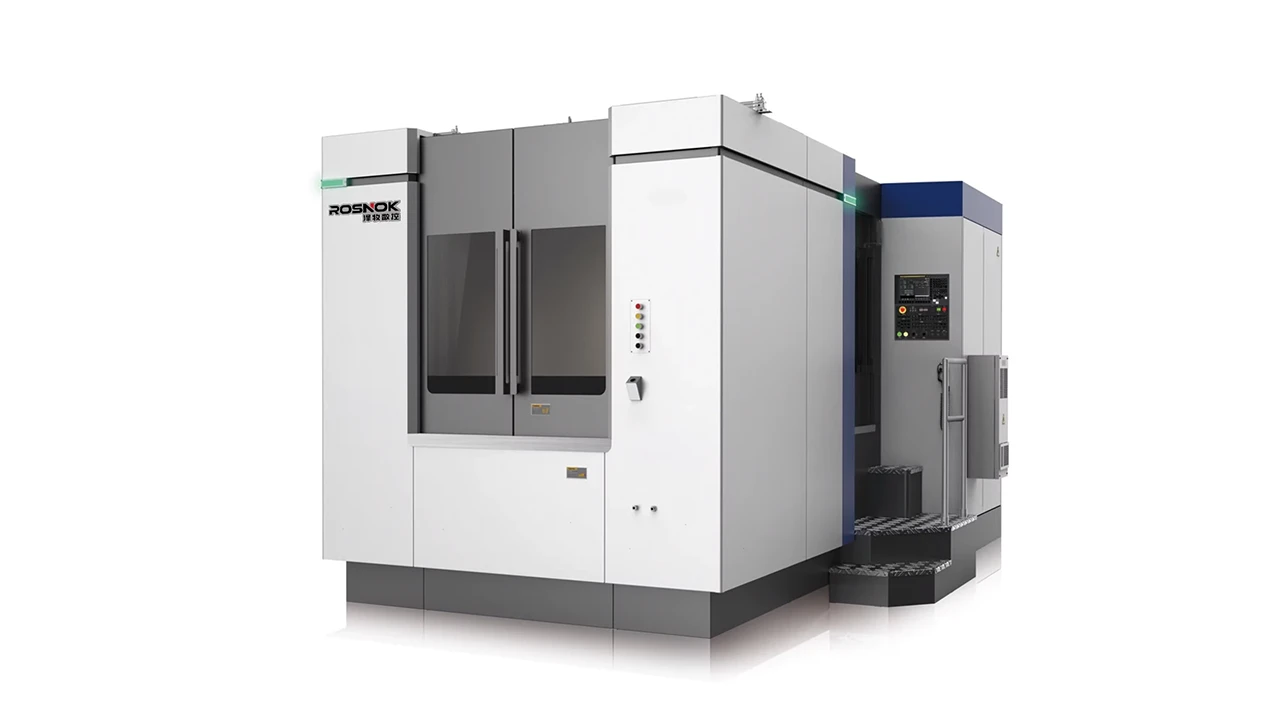
Gantry Machining Center (Double Column Machining Center)
A gantry machining center (also known as a double column machining center) features a bridge-like structure with two columns supporting the crossbeam. The spindle moves along the gantry, making it suitable for machining large, heavy workpieces. Gantry machining centers are widely used in industries such as aerospace, heavy machinery, and automotive sectors.
Key Features:
- Spindle Orientation: Can be either vertical or horizontal depending on the configuration.
- Worktable Movement: Large worktable capable of handling oversized components.
- Ideal Applications: Machining of large parts with high precision and heavy-duty operations.
Specialties:
- Exceptional stability and accuracy for machining large workpieces.
- Ideal for multi-axis machining of complex geometries.
- Suitable for both milling and boring operations.
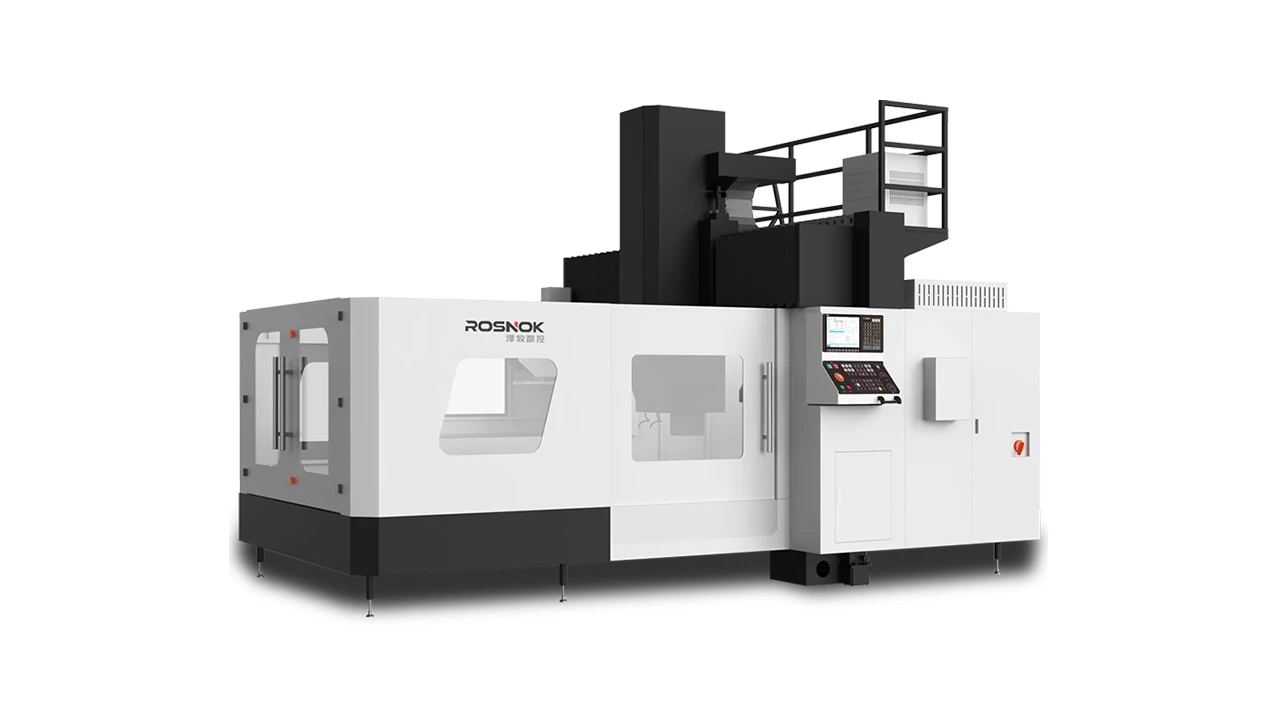
Classification by Number of Axes:
3-Axis Machining Center
A 3-axis machining center controls the movement of the cutting tool along the X, Y, and Z axes. It is the most common configuration and is used for basic milling, drilling, and tapping operations.
Key Features:
- Movement: X-axis (left and right), Y-axis (front and back), Z-axis (up and down).
- Ideal Applications: Milling, drilling, and simple contouring.
Specialties:
- Suitable for small to medium-sized workpieces.
- Cost-effective solution for simpler machining tasks.
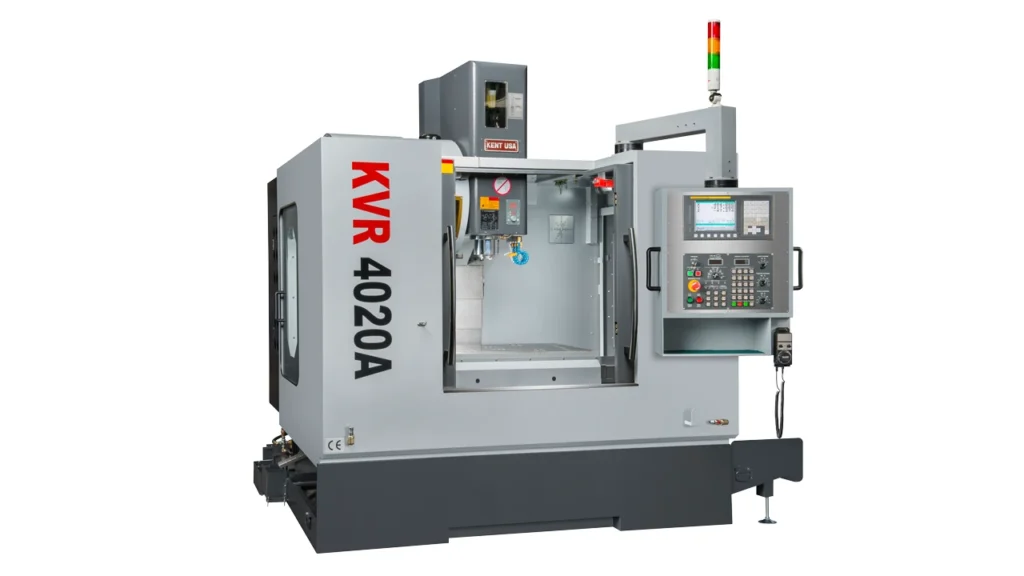
4-Axis Machining Center
A 4-axis machining center adds an additional rotary axis (typically the A-axis), allowing the workpiece to rotate around the X-axis. This configuration allows for machining on multiple sides without the need for repositioning.
Key Features:
- Axes Movement: X, Y, Z, and A (rotational movement).
- Ideal Applications: Machining multi-sided parts with moderate complexity.
Specialties:
- Increased flexibility for machining multi-sided parts.
- Enhanced productivity by reducing setup time.
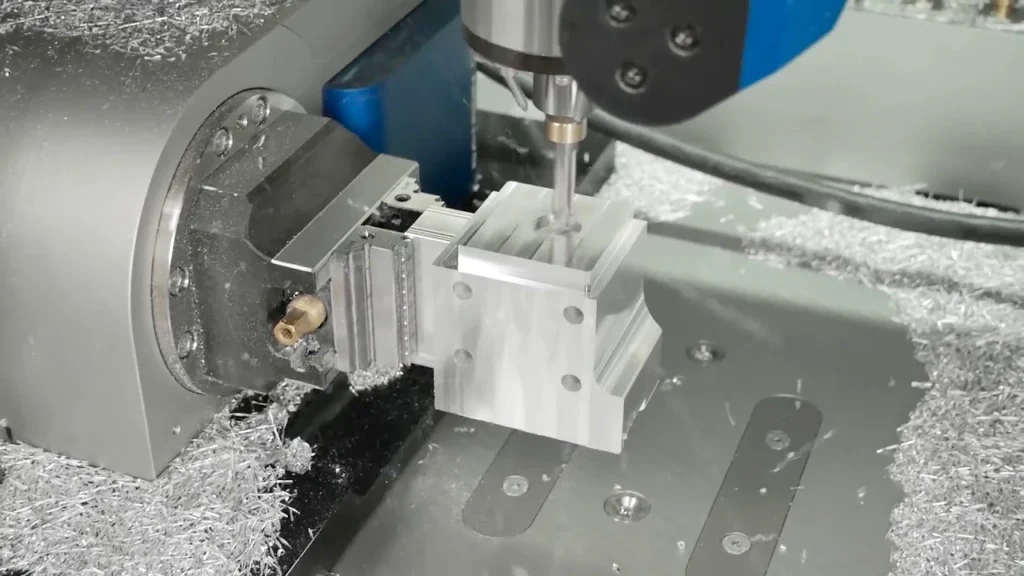
5-Axis Machining Center
A 5-axis machining center offers the highest level of flexibility and precision by allowing the cutting tool or workpiece to move along five different axes simultaneously. It is widely used in industries such as aerospace, medical, and mold manufacturing.
Key Features:
- Axes Movement: X, Y, Z, and two additional rotary axes (A and B or C).
- Ideal Applications: Machining complex geometries, turbine blades, and aerospace components.
Specialties:
- Reduced setup time by machining multiple sides in one go.
- Ability to create intricate 3D geometries with superior accuracy.
- Enhanced surface finish and consistency in complex parts.
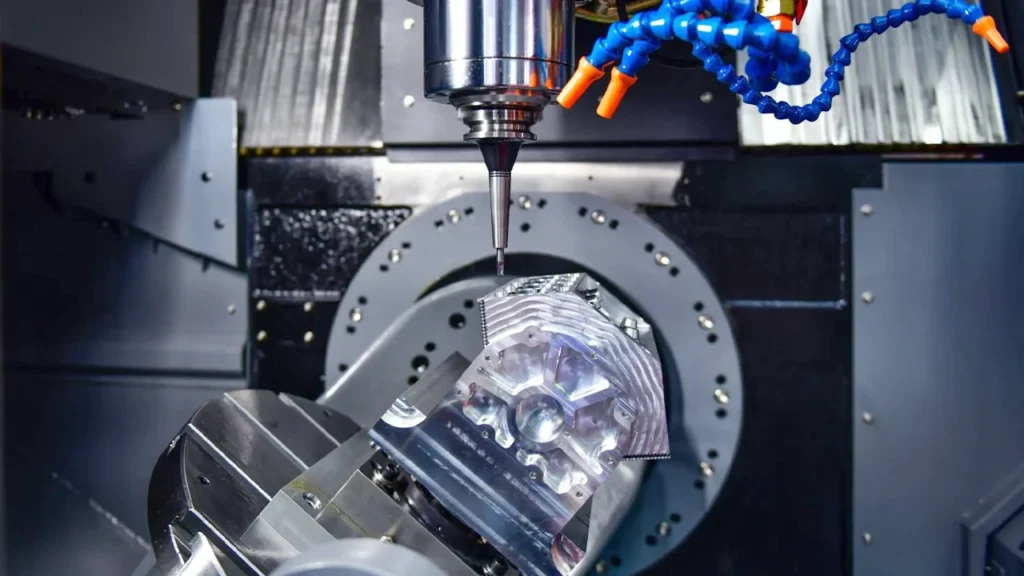
Machining Processes Performed by a Machining Center
A machining center is a highly versatile machine capable of performing a wide range of machining operations with high precision and efficiency. By integrating multiple processes into a single setup, machining centers reduce production time, minimize errors, and optimize workflow. Below is a list of the most common machining processes that a machining center can perform, along with the conditions and prerequisites required for each operation.
1. Milling
Milling is the most common operation performed on a machining center, where a rotating cutting tool removes material from a stationary workpiece to create flat surfaces, slots, pockets, and contours. Machining centers can handle various types of milling, including face milling, end milling, slot milling, and contour milling.
Prerequisites:
- Appropriate tool selection (end mills, face mills, etc.).
- Proper workholding to secure the workpiece.
- Accurate CNC program defining the milling path and cutting parameters.
Ideal Machine Types:
- Vertical Machining Center (VMC)
- Horizontal Machining Center (HMC)
- 5-Axis Machining Center for complex contour milling
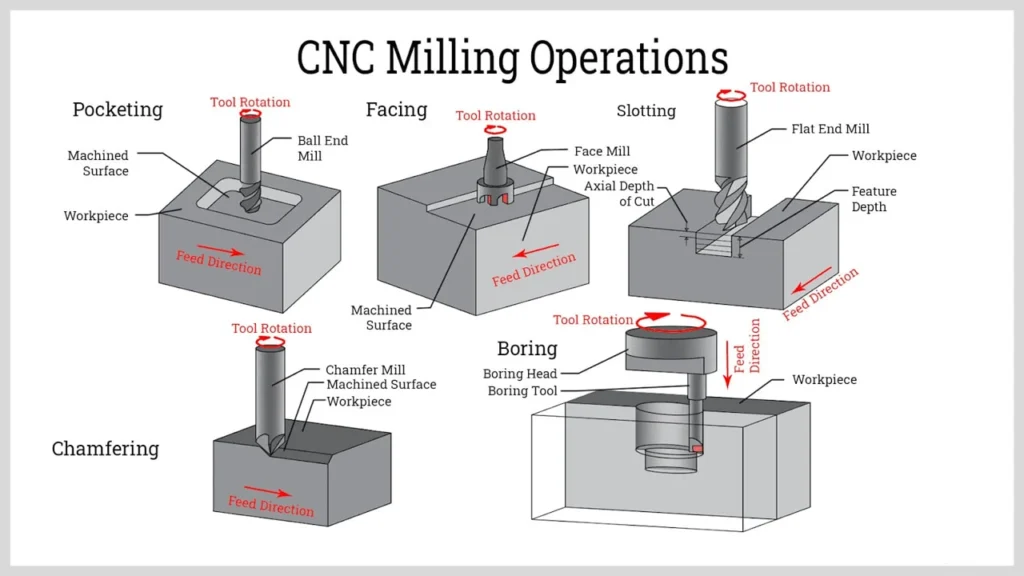
2. Drilling
Drilling involves using a rotating drill bit to create cylindrical holes in the workpiece. Machining centers can perform various drilling operations, including spot drilling, peck drilling, and deep-hole drilling.
Prerequisites:
- Selection of drill bits appropriate for the material and hole size.
- Correct spindle speed and feed rate settings.
- Adequate coolant supply to prevent overheating.
Ideal Machine Types:
- Vertical Machining Center for vertical drilling operations.
- Horizontal Machining Center for deep-hole drilling applications.
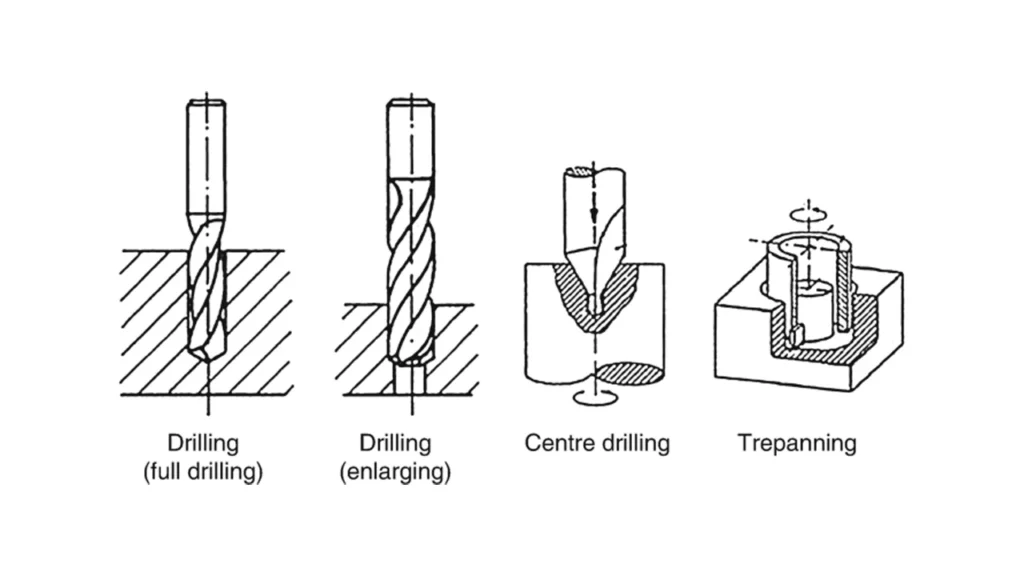
3. Tapping
Tapping is the process of cutting threads inside a drilled hole to create a threaded interior that can accept bolts or screws. Machining centers perform both rigid tapping and floating tapping depending on the type of CNC system and spindle.
Prerequisites:
- Proper drill size to create a pre-hole for tapping.
- Use of appropriate tap tools based on thread size and pitch.
- Correct tapping speed and feed settings.
Ideal Machine Types:
- Vertical Machining Center for general tapping operations.
- 5-Axis Machining Center for tapping at multiple angles.
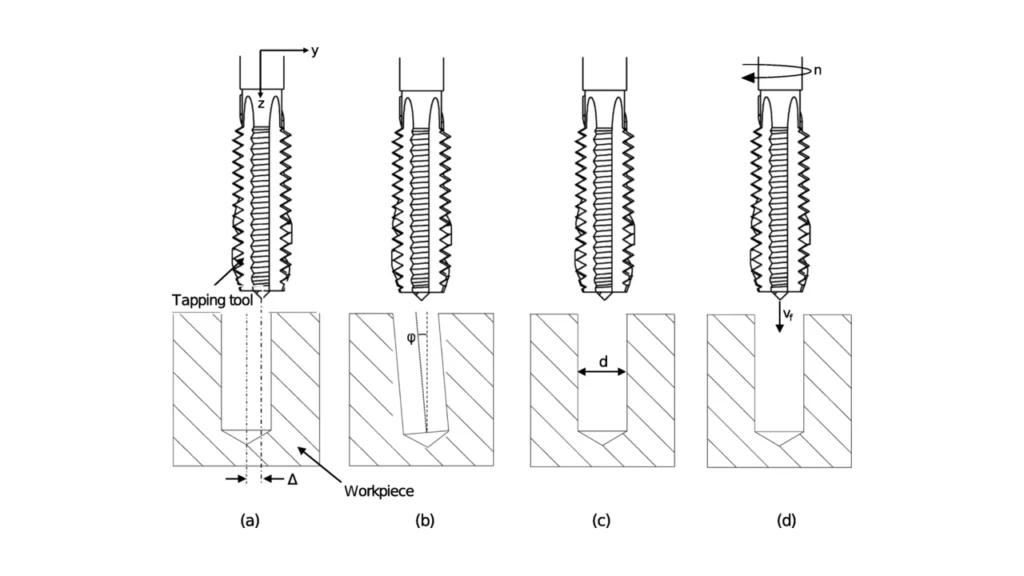
4. Boring
Boring enlarges an existing hole to achieve a precise diameter and smooth finish. Machining centers can perform rough boring, fine boring, and back boring operations to meet tight tolerances.
Prerequisites:
- Pre-drilled hole of smaller diameter.
- High-precision boring bars and tool holders.
- CNC programming to control depth and diameter.
Ideal Machine Types:
- Horizontal Machining Center for deep-hole boring.
- Gantry Machining Center for large component boring.
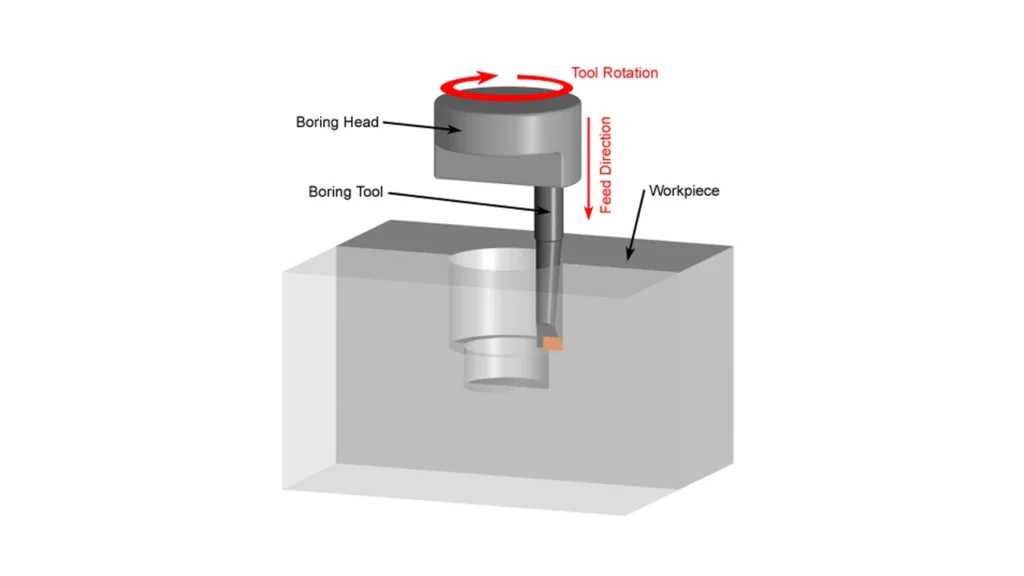
5. Reaming
Reaming is used to refine the dimensions and surface finish of a pre-drilled hole by removing small amounts of material. This process improves the accuracy of the hole’s diameter and ensures a smoother surface.
Prerequisites:
- Proper pre-drilled hole size for reaming.
- Correct reamer selection for material and finish requirements.
- Slow spindle speed to avoid damaging the tool or workpiece.
Ideal Machine Types:
- Vertical and Horizontal Machining Centers for general reaming applications.
- 5-Axis Machining Center for complex hole geometries.
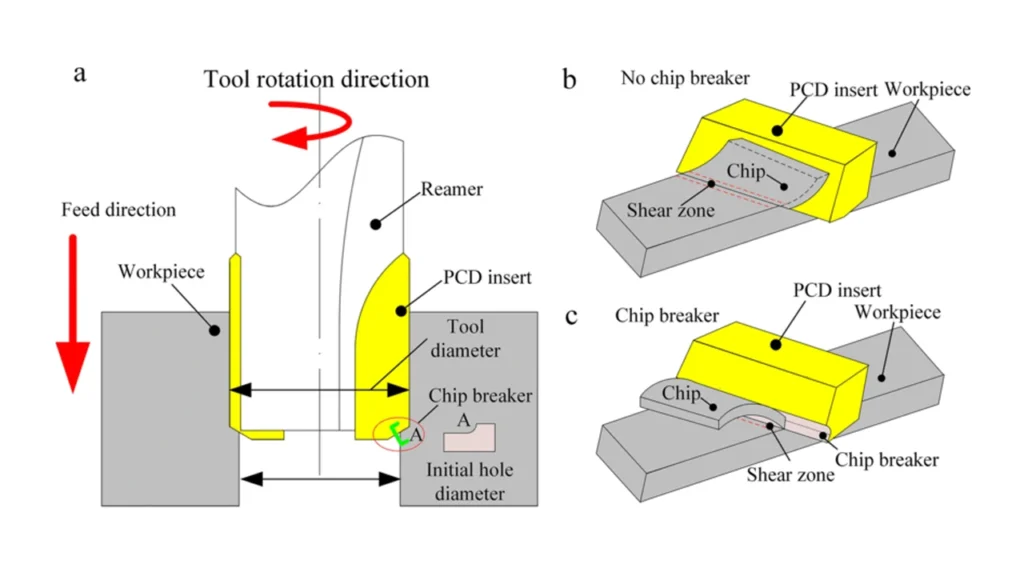
6. Countersinking and Counterboring
Countersinking creates a conical hole at the surface of a drilled hole to allow a screw or bolt to sit flush with the workpiece. Counterboring creates a flat-bottomed hole to seat a bolt or fastener below the surface.
Prerequisites:
- Proper countersink or counterbore tools with the desired angles.
- Correct feed rate and depth control.
- Accurate CNC programming to ensure consistent hole placement.
Ideal Machine Types:
- Vertical Machining Center for flat workpieces.
- Horizontal Machining Center for large or complex parts.
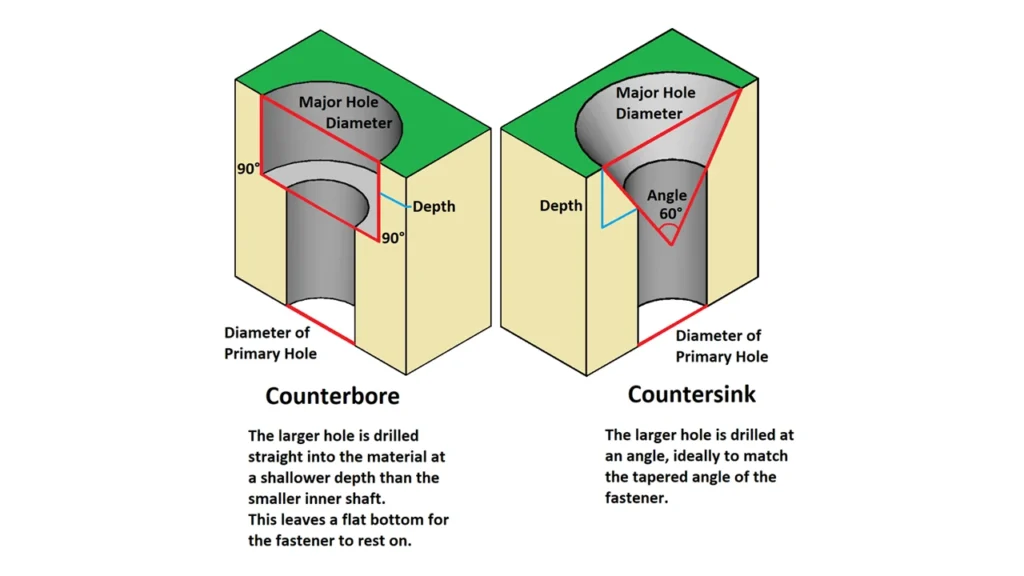
7. Thread Milling
Thread milling creates internal or external threads using a rotating multi-point cutting tool. This process offers greater flexibility and control compared to traditional tapping and is commonly used for producing large or non-standard thread sizes.
Prerequisites:
- Appropriate thread mill cutter based on thread size and type.
- Proper CNC program with helical interpolation.
- Correct spindle speed and feed rate for the material.
Ideal Machine Types:
- 5-Axis Machining Center for multi-directional threading.
- Vertical Machining Center for standard threading tasks.
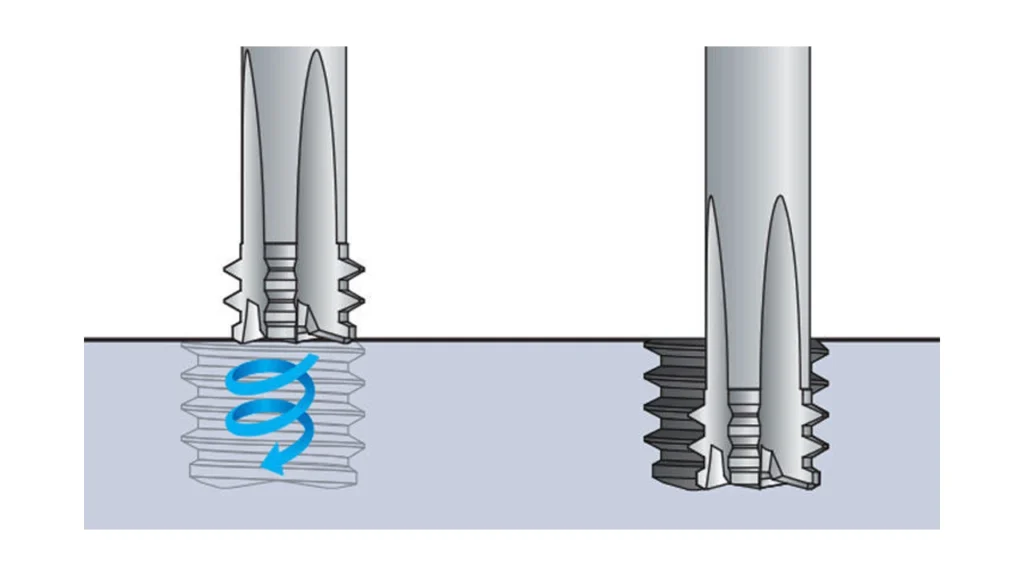
8. Facing
Facing involves machining a flat surface on the end of a workpiece to achieve smoothness and dimensional accuracy. This process is commonly used to prepare the surface of a part before performing other machining operations.
Prerequisites:
- Suitable face mill cutter or fly cutter.
- Proper clamping and alignment of the workpiece.
- CNC programming for even material removal.
Ideal Machine Types:
- Vertical Machining Center for flat workpieces.
- Gantry Machining Center for large surface areas.
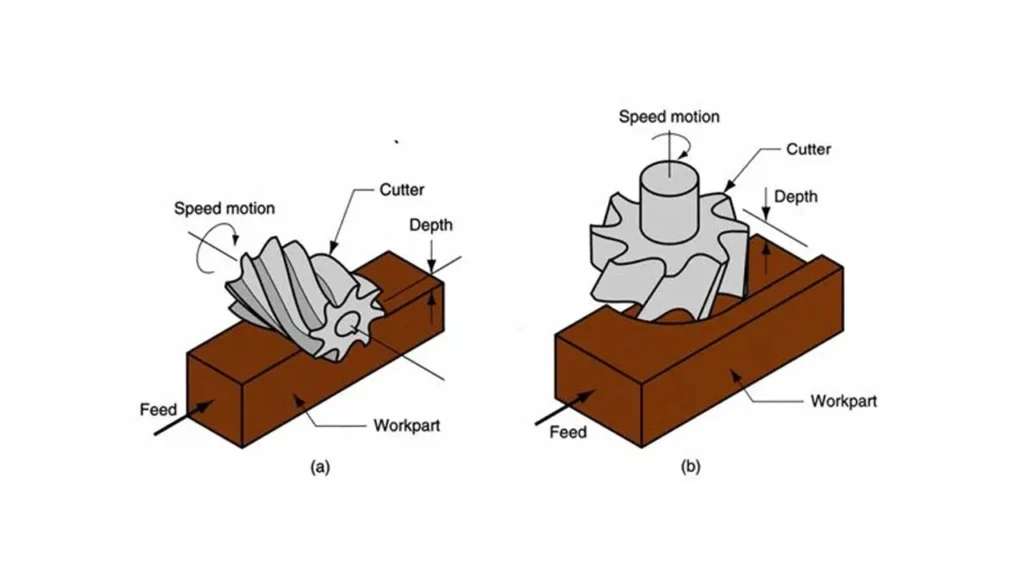
9. Engraving and Marking
Engraving and marking allow for the addition of logos, serial numbers, or text on a workpiece. This operation is typically used in aerospace, medical, and electronics industries for part identification.
Prerequisites:
- High-speed spindle with engraving tools.
- CNC software that supports engraving paths.
- Proper toolpath and depth settings to avoid damaging the workpiece.
Ideal Machine Types:
- 3-Axis and 5-Axis Machining Centers.
- CNC Vertical Machining Center with engraving attachments.
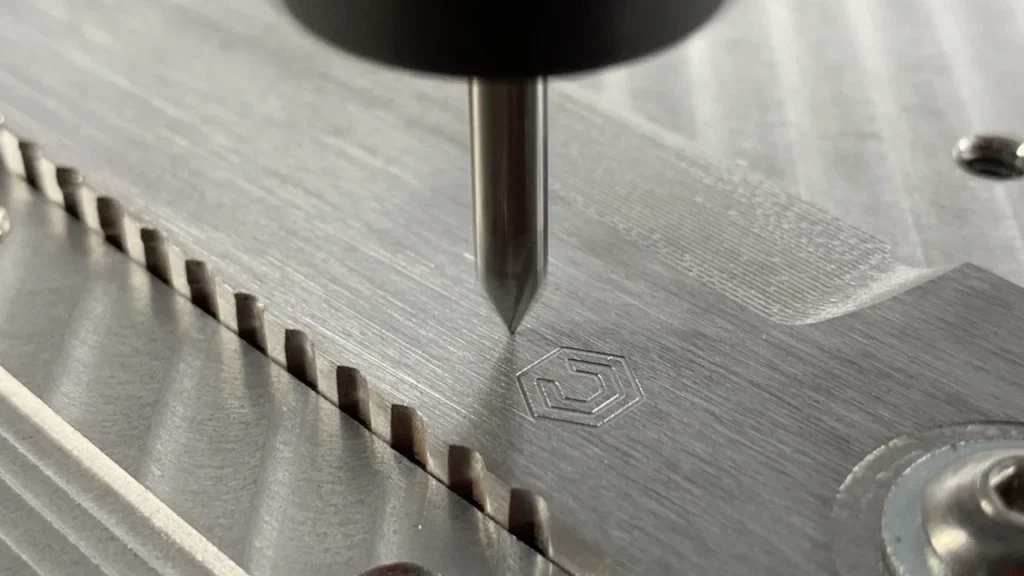
10. Grinding (Optional in Specialized Machining Centers)
Certain hybrid machining centers are equipped with grinding attachments that allow for surface grinding, cylindrical grinding, and precision finishing. Grinding operations are typically used to achieve a high-quality surface finish and tight tolerances.
Prerequisites:
- Suitable grinding wheel for the material.
- Adequate coolant supply to prevent overheating.
- Proper spindle speed and feed rate adjustments.
Ideal Machine Types:
- 5-Axis Machining Centers with hybrid capabilities.
- Specialized Machining Centers with grinding modules.
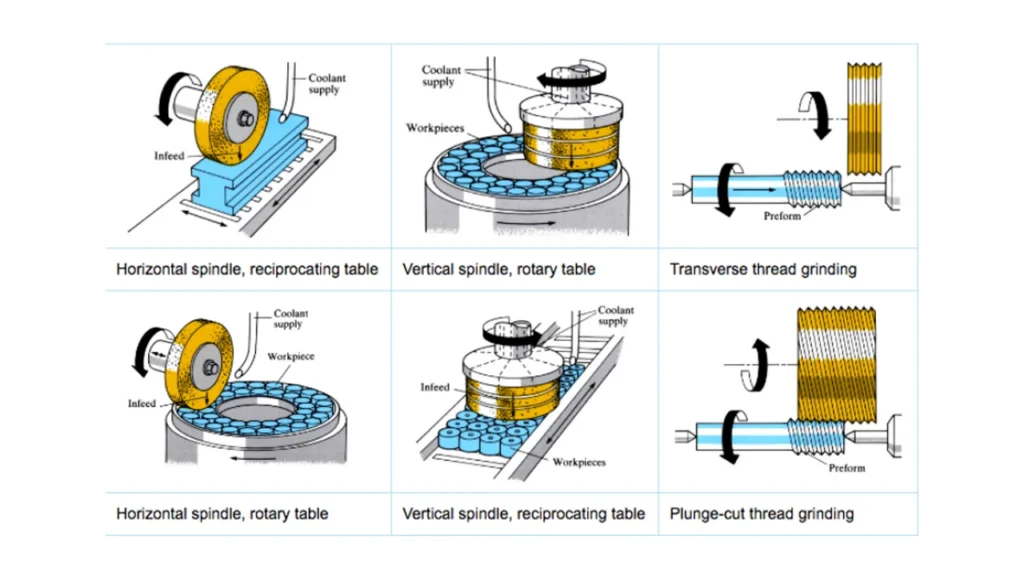
11. Turning (Limited in Some Hybrid Machining Centers)
Although turning is typically performed on CNC lathes, certain mill-turn machining centers or hybrid machines can perform light turning operations using a rotating workpiece and stationary cutting tool.
Prerequisites:
- Rotary table or workpiece clamping system to enable rotation.
- Proper cutting tools designed for turning applications.
- CNC system that supports mill-turn functionality.
Ideal Machine Types:
- Mill-Turn Machining Centers.
- 5-Axis Machining Centers with rotary tables.
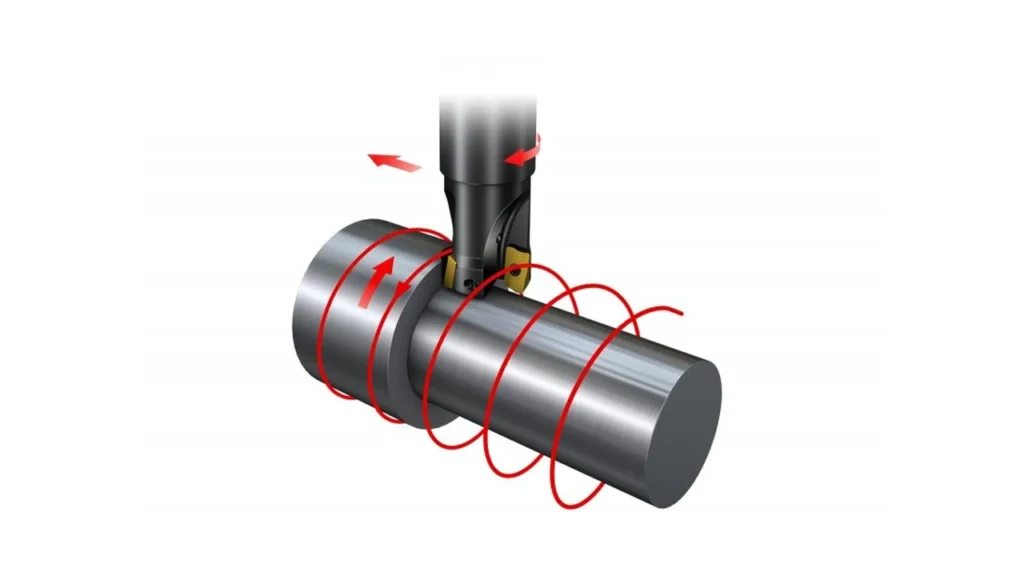
Applications of Machining Centers
Machining centers are widely used across various industries due to their ability to perform multiple operations with high precision and efficiency. From manufacturing intricate aerospace components to producing high-volume automotive parts, machining centers play a vital role in delivering consistent quality and enhanced productivity. Below, we’ll explore the most common applications of machining centers across different industries.
Aerospace Industry
In the aerospace industry, machining centers are used to manufacture highly complex and safety-critical components that require tight tolerances and impeccable surface finishes. Parts such as turbine blades, aircraft engine components, wing structures, and landing gear components are often produced using 5-axis machining centers that allow for simultaneous multi-axis movement to create intricate geometries.
Key Benefits:
- High precision and accuracy for aerospace-grade materials.
- Ability to machine lightweight alloys such as titanium and aluminum.
- Multi-axis machining reduces the need for multiple setups.
Automotive Industry
The automotive industry relies heavily on machining centers for the mass production of precision parts that form the backbone of vehicles. From engine blocks and transmission housings to suspension components and brake systems, machining centers ensure that these critical parts are produced with consistent accuracy and durability.
Key Benefits:
- High-speed machining for mass production with minimal downtime.
- Consistent quality and dimensional accuracy for complex automotive parts.
- Ability to perform multiple operations, reducing cycle times.
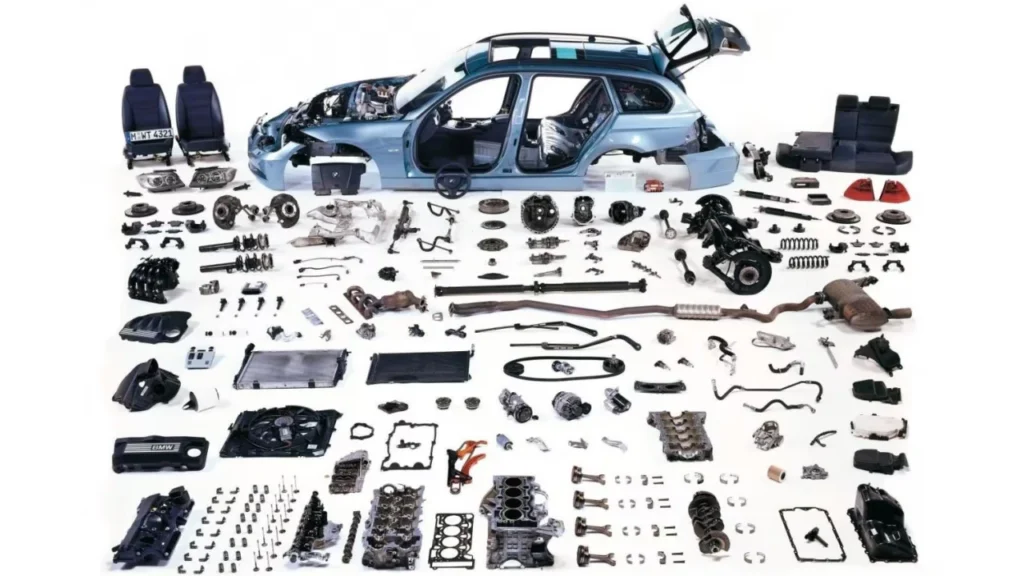
Mold and Die Industry
In the mold and die industry, machining centers are essential for creating highly detailed and intricate molds used in plastic injection molding, die casting, and stamping. 3-axis and 5-axis machining centers allow manufacturers to produce complex mold cavities and cores with high precision, ensuring that the final product meets design specifications.
Key Benefits:
- High-precision milling of intricate mold geometries.
- Reduced lead times by eliminating the need for multiple setups.
- Ability to handle complex 3D surfaces and contours.
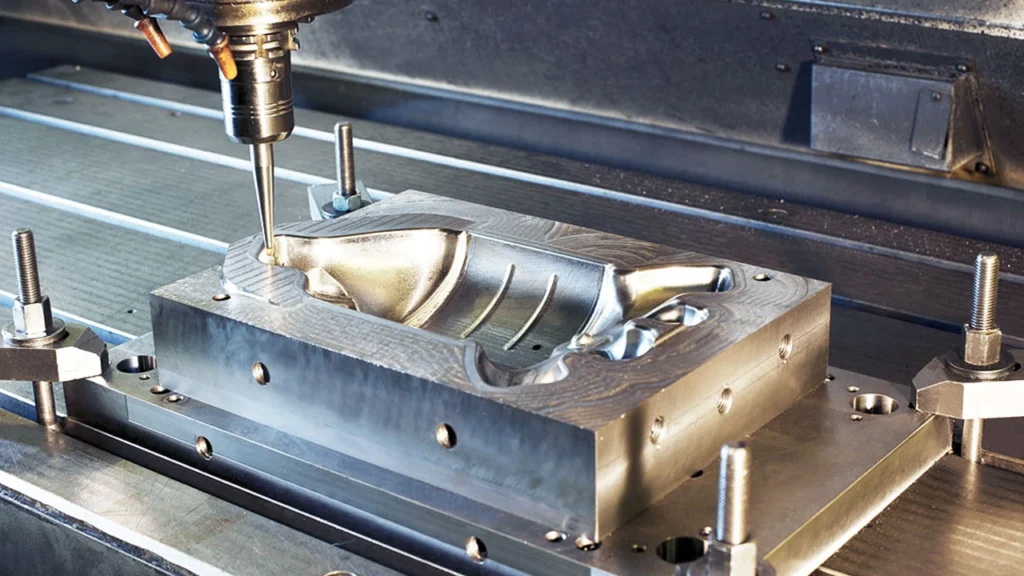
Medical Device Industry
The medical device industry demands extreme precision and flawless surface finishes for components such as surgical instruments, orthopedic implants, and prosthetic devices. 5-axis machining centers are often used to ensure the highest levels of accuracy required for biocompatible materials like titanium and stainless steel.
Key Benefits:
- High precision for producing complex medical components.
- Consistent quality in critical parts for patient safety.
- Machining of biocompatible materials with tight tolerances.
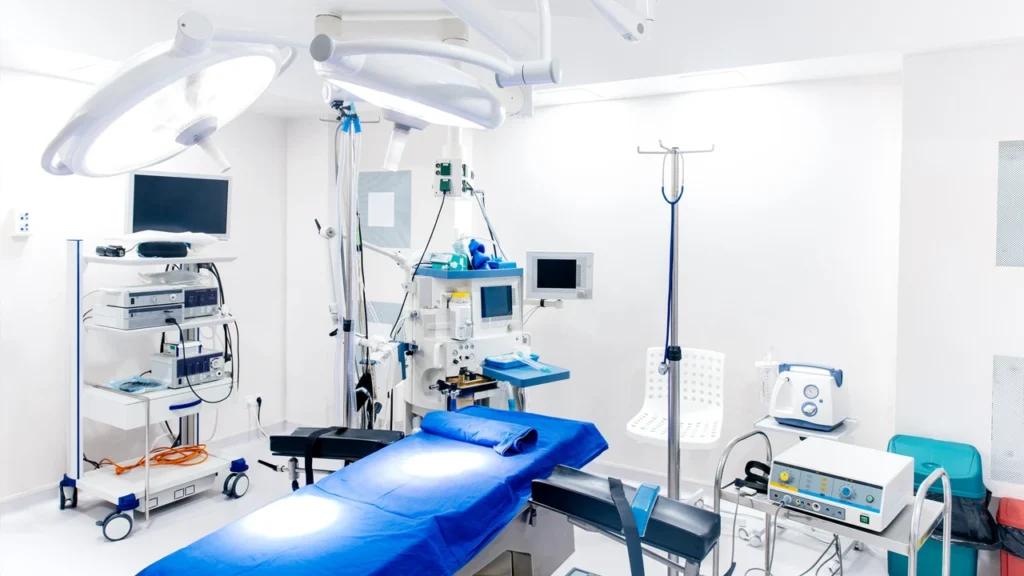
Electronics and Precision Components
In the electronics industry, machining centers are used to manufacture small, high-precision components such as connectors, circuit boards, and microelectronic housings. Due to the delicate nature of these components, machining centers with high-speed spindles and minimal vibration are used to ensure precision and prevent damage.
Key Benefits:
- High-speed, high-precision machining for small components.
- Consistency in producing micro-sized parts.
- Reduced rejection rates with consistent part quality.
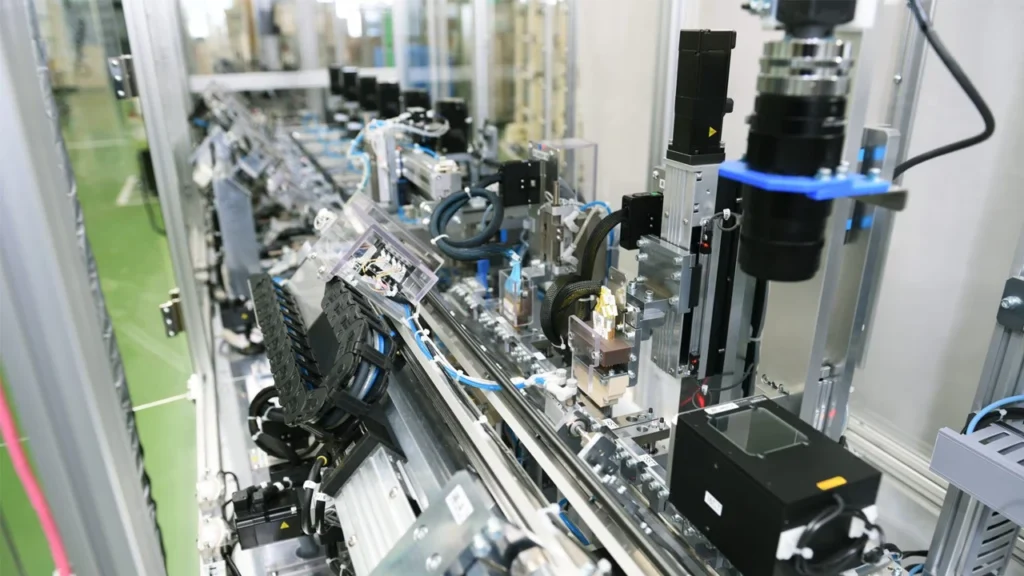
Energy and Power Generation Industry
The energy sector uses machining centers to produce critical components for power plants, wind turbines, and oil and gas equipment. These parts often require high durability and resistance to extreme conditions, which machining centers can achieve through high-precision cutting and finishing.
Key Benefits:
- High durability for energy sector components.
- Precision machining of large, heavy-duty parts.
- Efficiency in producing high-volume parts for power generation.
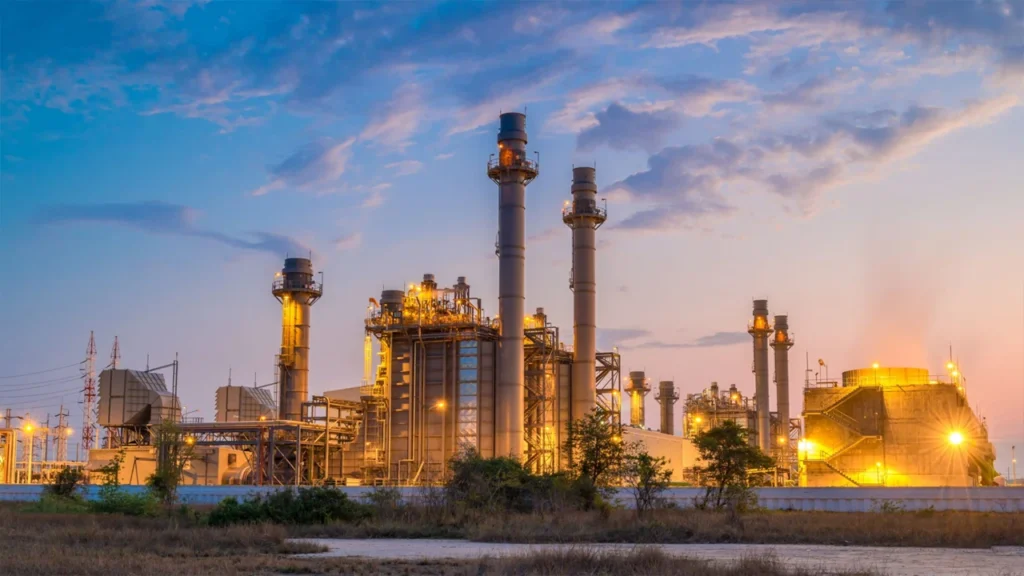
Heavy Machinery and Industrial Equipment
Machining centers play a crucial role in the manufacturing of heavy machinery and industrial equipment such as construction machinery, mining equipment, and industrial gearboxes. Gantry-type and double-column machining centers are commonly used to handle large and heavy workpieces.
Key Benefits:
- Ability to handle oversized and heavy-duty workpieces.
- High rigidity and accuracy for machining large parts.
- Reduced machining time for complex geometries.
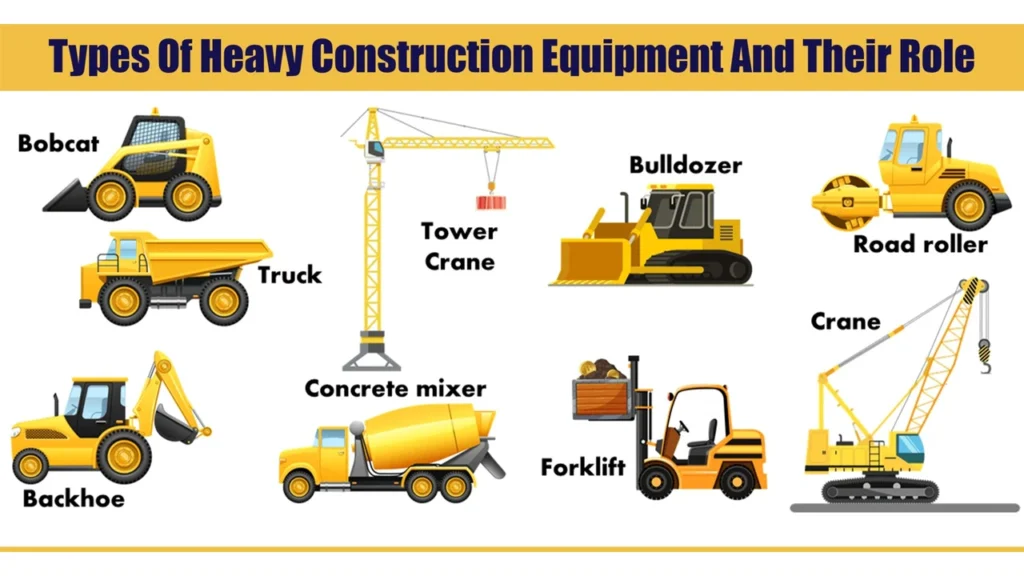
Advantages of Using a Machining Center
Machining centers offer numerous advantages that make them indispensable in modern manufacturing environments. Their ability to perform multiple operations with high precision, efficiency, and consistency has revolutionized industries ranging from aerospace and automotive to medical device manufacturing. Below are the key advantages of using a machining center.
High Precision and Consistency
One of the most significant advantages of a machining center is its ability to deliver high precision and repeatable accuracy across multiple operations. The integration of CNC (Computer Numerical Control) systems ensures that even the most complex machining tasks are performed with micrometer-level precision.
Why It Matters:
- Consistent dimensional accuracy reduces the need for rework.
- Tolerances are maintained across large production runs, ensuring uniform quality.
- Ideal for industries requiring intricate and high-precision parts, such as aerospace and medical devices.
Increased Efficiency and Productivity
Machining centers enhance production efficiency by combining multiple operations into a single setup, eliminating the need for manual intervention and reducing downtime. The automatic tool changer (ATC) allows for seamless tool changes, enabling continuous operation with minimal disruption.
Why It Matters:
- Reduced cycle time through automated tool changes.
- Ability to perform milling, drilling, tapping, and boring in one setup.
- Enhanced throughput and faster turnaround for high-volume production.
Versatility for Diverse Applications
Modern machining centers are designed to handle a wide range of materials and machining operations, making them highly versatile. They can perform tasks such as milling, drilling, boring, tapping, and even turning with ease. Whether you’re machining aluminum, titanium, or hardened steel, machining centers can adapt to different materials and production requirements.
Why It Matters:
- Flexibility to handle various machining tasks in different industries.
- Capability to switch between different machining processes without re-clamping.
- Suitable for prototyping as well as mass production.
Reduced Labor Costs and Manual Intervention
By automating most machining processes, machining centers reduce the reliance on manual labor, minimizing the risk of human error and increasing overall efficiency. CNC programming and automated tool changes mean that operators can manage multiple machines simultaneously, reducing operational costs.
Why It Matters:
- Lower labor costs and reduced need for skilled operators.
- Increased consistency by reducing the likelihood of manual errors.
- Enhanced operator safety by minimizing direct interaction with cutting tools.
Improved Safety and Operator Convenience
Machining centers prioritize operator safety through automated operations and minimal manual handling. Advanced safety features, such as enclosed work areas and emergency stop systems, reduce the risk of accidents and protect operators from hazards.
Why It Matters:
- Enhanced safety through reduced operator-machine interaction.
- Protection from flying chips, coolant splashes, and other machining hazards.
- Greater convenience and ease of use for machine operators.
Cost-Effectiveness in Mass Production
While the initial investment in a machining center may be high, the long-term cost benefits make it a cost-effective solution for mass production. Machining centers significantly reduce setup time, machining time, and labor costs, resulting in higher ROI (Return on Investment) over time.
Why It Matters:
- Lower per-part cost in large production runs.
- Reduced machine idle time through continuous operation.
- Minimal maintenance and downtime due to high machine reliability.
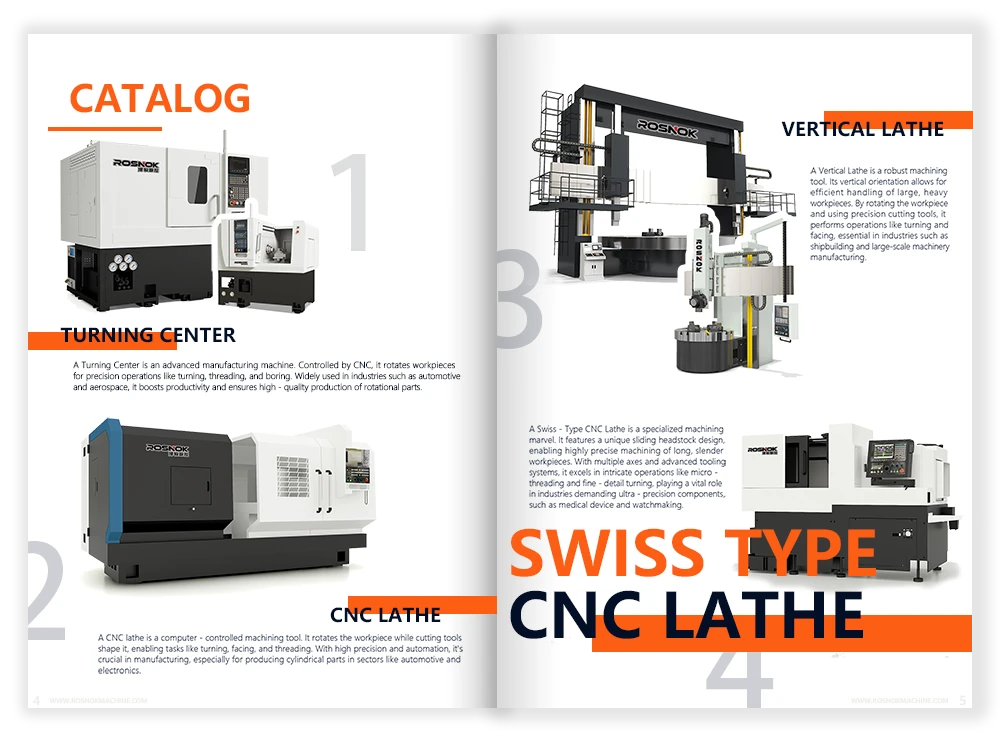
Ability to Perform Multi-Axis Machining
Advanced machining centers, such as 5-axis machining centers, offer the capability to perform multi-axis machining, allowing for the production of highly complex geometries in a single setup. This reduces the need for repositioning the workpiece and minimizes errors.
Why It Matters:
- Faster production of intricate 3D parts and geometries.
- Increased accuracy by avoiding multiple setups.
- Improved surface finish and part quality.
Scalability for Future Production Needs
Machining centers offer scalability for manufacturers looking to expand their production capabilities. Many modern machining centers can be upgraded with additional axes, automation systems, and software improvements, ensuring that they remain relevant as production needs grow.
Why It Matters:
- Future-proof investment to accommodate evolving production demands.
- Ability to handle increased production volumes without significant modifications.
- Flexibility to adapt to new machining technologies and processes.
Environmentally Friendly and Energy Efficient
Modern machining centers are designed to be energy efficient, reducing power consumption and minimizing waste during the machining process. Many models incorporate coolant recycling systems and chip management technologies to reduce environmental impact.
Why It Matters:
- Lower energy consumption leads to reduced operating costs.
- Environmentally responsible manufacturing through waste reduction.
- Compliance with sustainability regulations and industry standards.
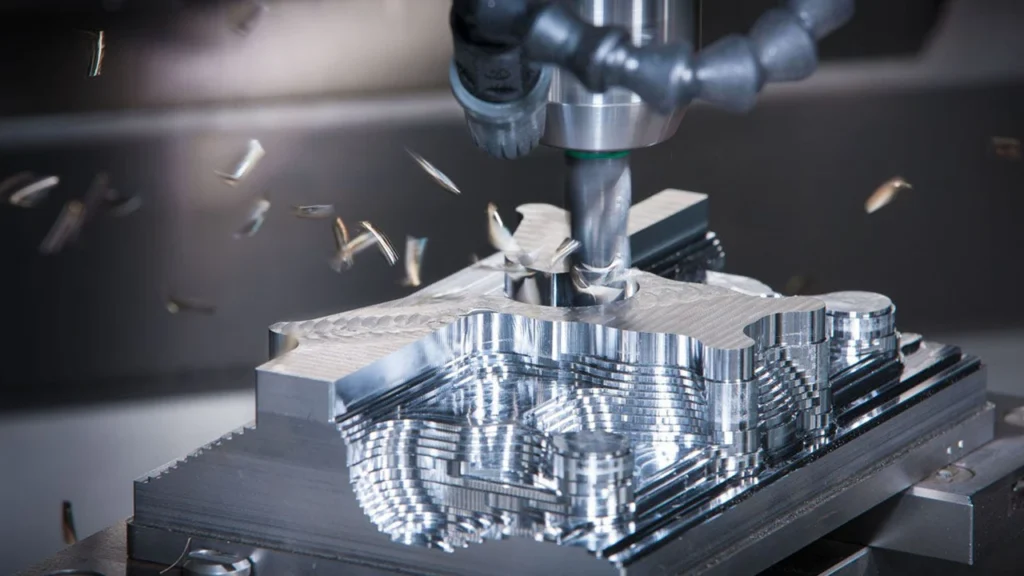
Challenges and Limitations of Machining Centers
While machining centers offer numerous advantages, they are not without their challenges and limitations. Understanding these limitations helps manufacturers make informed decisions and optimize their machining processes for maximum efficiency and profitability. Below, we’ll explore some of the key challenges associated with machining centers.
High Initial Investment
One of the biggest challenges of adopting a machining center is the high initial cost associated with purchasing and installing the machine. Advanced CNC machining centers, especially 5-axis and double-column models, require significant capital investment, making them less accessible for small-scale manufacturers.
Challenges:
- High upfront costs for machine purchase and setup.
- Additional costs for software, tooling, and automation integration.
- Longer ROI (Return on Investment) periods for smaller production volumes.
Mitigation:
- Consider leasing or financing options to spread out the cost.
- Opt for refurbished or used machining centers to reduce initial expenses.
Skill and Training Requirements
Operating and maintaining a machining center requires highly skilled operators and programmers who are familiar with CNC systems, tooling setups, and maintenance protocols. Without proper training, operators may struggle to optimize the machine’s performance, leading to errors and production delays.
Challenges:
- Need for skilled CNC programmers and machinists.
- Ongoing training required for software and equipment upgrades.
- Increased risk of errors and downtime due to operator inexperience.
Mitigation:
- Invest in regular training programs to upskill operators.
- Provide on-the-job mentoring and workshops to enhance technical knowledge.
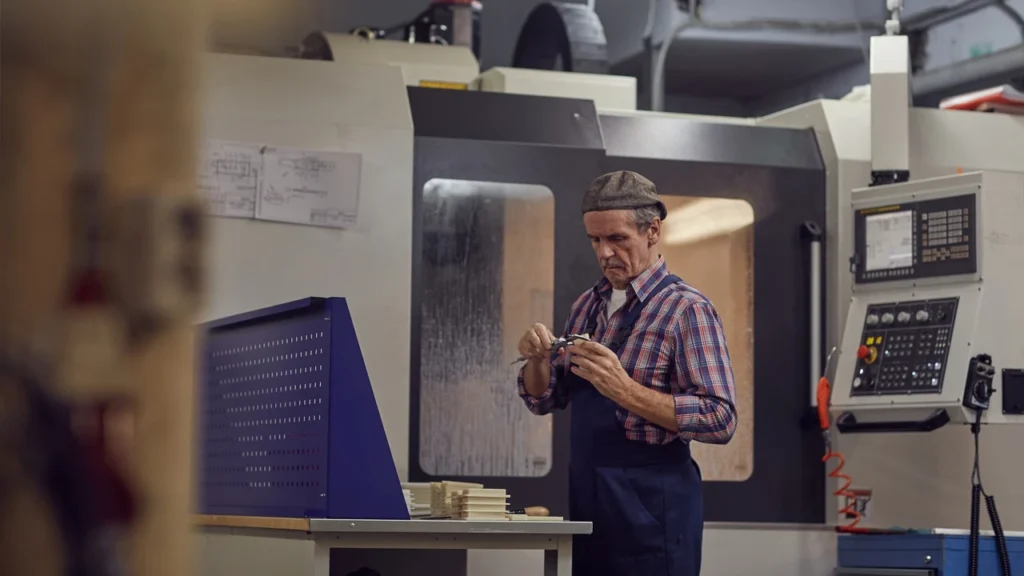
Maintenance and Downtime Risks
Regular maintenance and servicing are essential to ensure the smooth operation of a machining center. However, unexpected breakdowns and component failures can lead to costly downtime and production losses. Components such as the spindle, tool changer, and coolant system require periodic inspection and replacement to prevent unexpected failures.
Challenges:
- Downtime caused by machine malfunctions and unexpected breakdowns.
- High costs associated with replacing worn-out components.
- Difficulty in sourcing spare parts for older models.
Mitigation:
- Implement a preventive maintenance schedule to reduce unexpected breakdowns.
- Keep a stock of critical spare parts to minimize downtime during repairs.
- Use predictive maintenance systems with IoT integration to monitor machine health.
Programming Complexity for Advanced Operations
While machining centers offer multi-axis capabilities and complex machining functions, programming these advanced operations can be time-consuming and complex. Creating CNC programs for 5-axis machining centers or multi-part operations requires specialized knowledge and attention to detail.
Challenges:
- Increased complexity in writing CNC programs for multi-axis machining.
- Risk of errors due to incorrect toolpath programming.
- Longer programming times for intricate geometries.
Mitigation:
- Use CAM (Computer-Aided Manufacturing) software to streamline programming.
- Provide ongoing training to CNC programmers to handle advanced operations.
- Utilize simulation tools to validate programs before machining.
High Energy Consumption
Machining centers, especially high-speed and multi-axis models, consume a considerable amount of energy during operation. Long machining cycles and high spindle speeds contribute to increased energy usage, which can impact operational costs and sustainability goals.
Challenges:
- Increased energy consumption during prolonged machining operations.
- Higher operational costs due to increased power requirements.
- Difficulty in maintaining energy efficiency during high-speed machining.
Mitigation:
- Use energy-efficient machining strategies and optimize tool paths.
- Incorporate variable frequency drives (VFDs) to reduce energy waste.
- Consider machining centers equipped with energy-efficient motors and cooling systems.
Limited Flexibility for Low-Volume Production
While machining centers excel in high-volume production, they may not be the most cost-effective solution for low-volume or custom part manufacturing. The time required for setup, tooling changes, and CNC programming may outweigh the benefits for smaller batch sizes.
Challenges:
- Longer setup times for smaller production runs.
- Higher per-part costs for low-volume production.
- Limited flexibility for quick design changes.
Mitigation:
- Use hybrid manufacturing approaches for low-volume production.
- Opt for quick-change tooling systems to reduce setup time.
- Consider modular fixturing solutions to accommodate varying part designs.
Space and Infrastructure Requirements
Machining centers, particularly large double-column and gantry models, require significant floor space and a stable foundation to accommodate their size and operational needs. Smaller workshops may find it challenging to integrate such machines without substantial infrastructure modifications.
Challenges:
- Large footprint requiring dedicated floor space.
- Need for reinforced foundations to support heavy equipment.
- Increased ventilation and coolant management requirements.
Mitigation:
- Plan factory layouts with optimized space utilization.
- Assess floor load capacity before installing heavy machining centers.
- Upgrade ventilation systems to handle increased coolant and chip disposal.
How to Choose the Right Machining Center
Selecting the right machining center is a critical decision that can significantly impact your production efficiency, part quality, and overall operational costs. With various types of machining centers available, including vertical, horizontal, 5-axis, and gantry models, it’s essential to consider key factors that align with your production requirements. Below, we’ll explore the most important aspects to consider when choosing the right machining center for your needs.
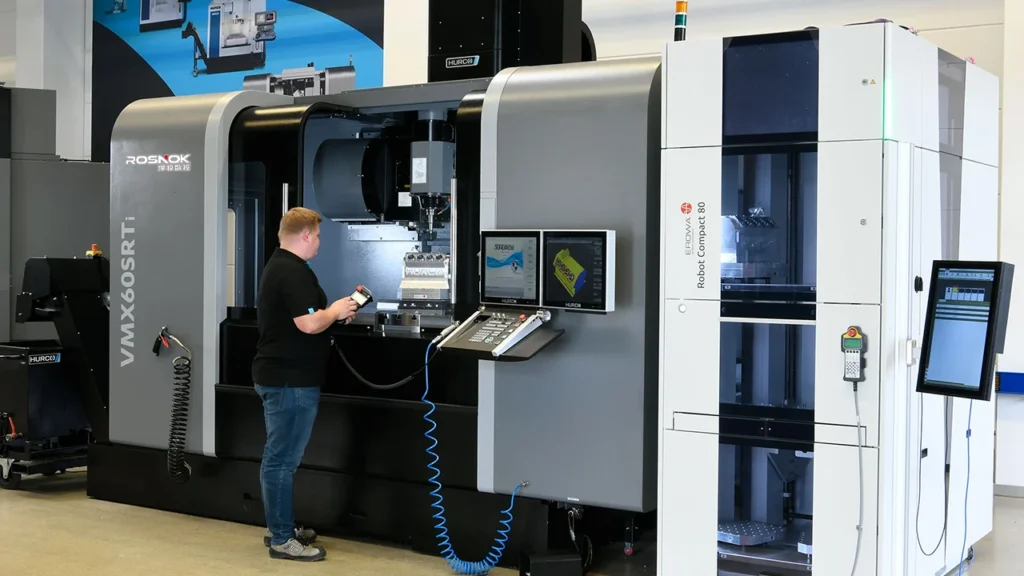
Understand Your Production Needs
Before investing in a machining center, it’s essential to thoroughly analyze your production needs. Consider the type of materials you’ll be machining, the complexity of the parts, and the required tolerances. A machining center that’s suitable for high-volume production may not be the best fit for prototyping or custom part manufacturing.
Key Considerations:
- Are you producing high-volume or low-volume parts?
- Do your parts require multi-axis machining or simple 3-axis operations?
- Will the machine be used for precision components or heavy-duty parts?
Recommendation:
- For high-volume production, consider horizontal machining centers (HMCs) that excel in continuous operation.
- For complex, multi-sided parts, opt for a 5-axis machining center to reduce the need for multiple setups.
Consider Machine Size and Workpiece Dimensions
The size and weight of your workpieces will determine the appropriate machining center size and configuration. Choosing a machine that’s too small can lead to limitations in machining capability, while an oversized machine may result in wasted resources and higher operational costs.
Key Considerations:
- What are the dimensions and weight of your typical workpieces?
- Do you require a large work envelope for oversized components?
- Will you need multi-axis movement to access hard-to-reach surfaces?
Recommendation:
- For large and heavy workpieces, a gantry machining center or double-column machining center is ideal.
- For small to medium-sized parts, a vertical machining center (VMC) offers a more cost-effective solution.
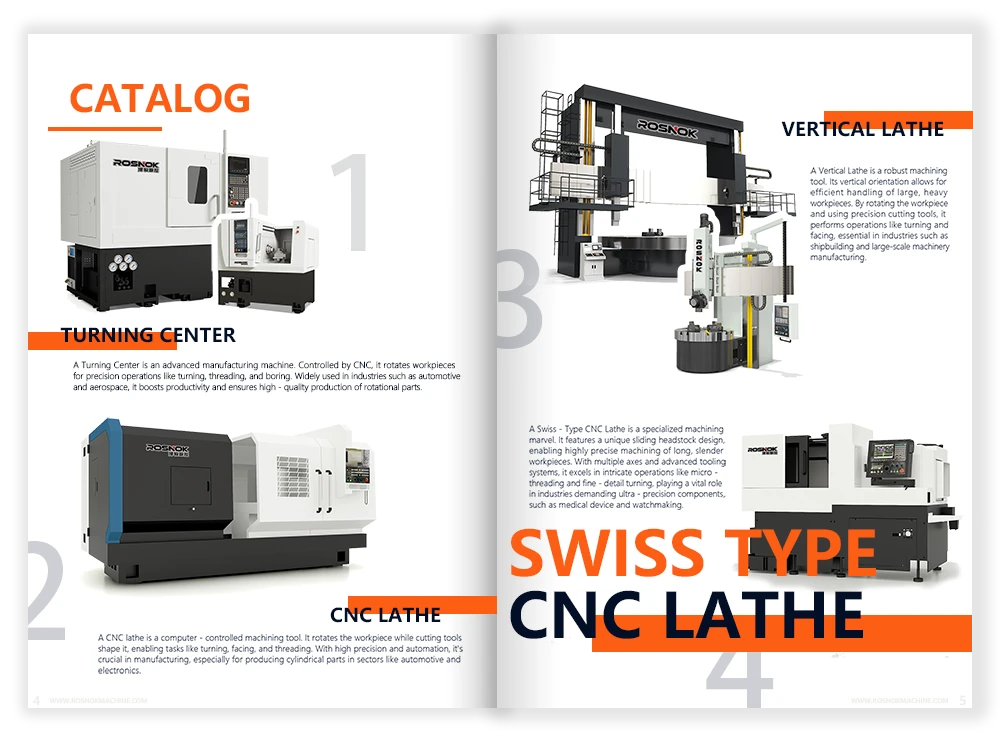
Evaluate CNC Control System and Software
The CNC control system plays a pivotal role in determining the machining center’s performance, accuracy, and ease of use. Different control systems offer varying levels of functionality, programming capabilities, and compatibility with CAD/CAM software.
Key Considerations:
- Is the CNC control system user-friendly and suitable for your team’s skill level?
- Does the system support advanced features such as 5-axis interpolation and toolpath optimization?
- Is it compatible with your existing CAD/CAM software?
Recommendation:
- Choose a control system from reputable brands such as Fanuc, Siemens, Heidenhain, or Mitsubishi.
- Ensure that the system supports G-code and M-code programming to handle complex machining operations.
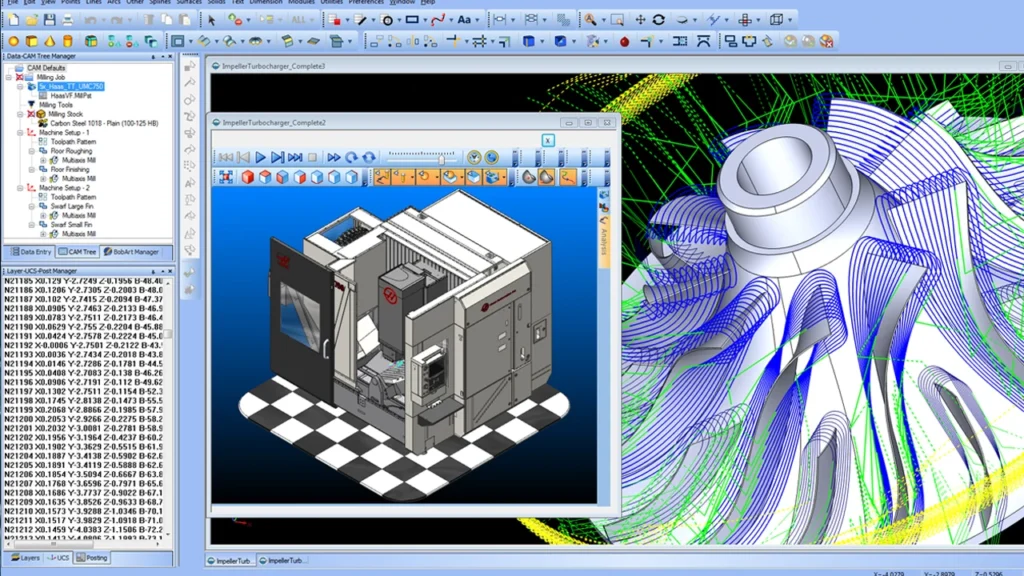
Assess Spindle Speed and Power
The spindle speed and power of a machining center directly impact the cutting performance and material removal rate. Different materials and machining applications require specific spindle speeds to achieve the desired surface finish and dimensional accuracy.
Key Considerations:
- What types of materials will you be machining?
- Do you require high-speed machining for soft metals or high-torque machining for hard alloys?
- Will you be performing deep cavity machining or contour milling?
Recommendation:
- For aluminum and softer materials, opt for a high-speed spindle with RPMs exceeding 10,000.
- For steel, titanium, and hardened alloys, choose a high-torque spindle that maintains stability under heavy cutting loads.
Examine Tool Capacity and Automatic Tool Changer (ATC)
The tool capacity and automatic tool changer (ATC) determine how many tools can be loaded into the machine and how efficiently they can be changed during machining operations. A higher tool capacity ensures greater flexibility and reduced downtime.
Key Considerations:
- How many tools are typically required for your machining operations?
- Do you need frequent tool changes for multi-step machining processes?
- Will the ATC support the tool sizes and types you’ll be using?
Recommendation:
- Choose a machining center with a carousel or chain-type ATC if frequent tool changes are required.
- For complex machining tasks, opt for a machine with a high-capacity tool magazine to minimize manual intervention.
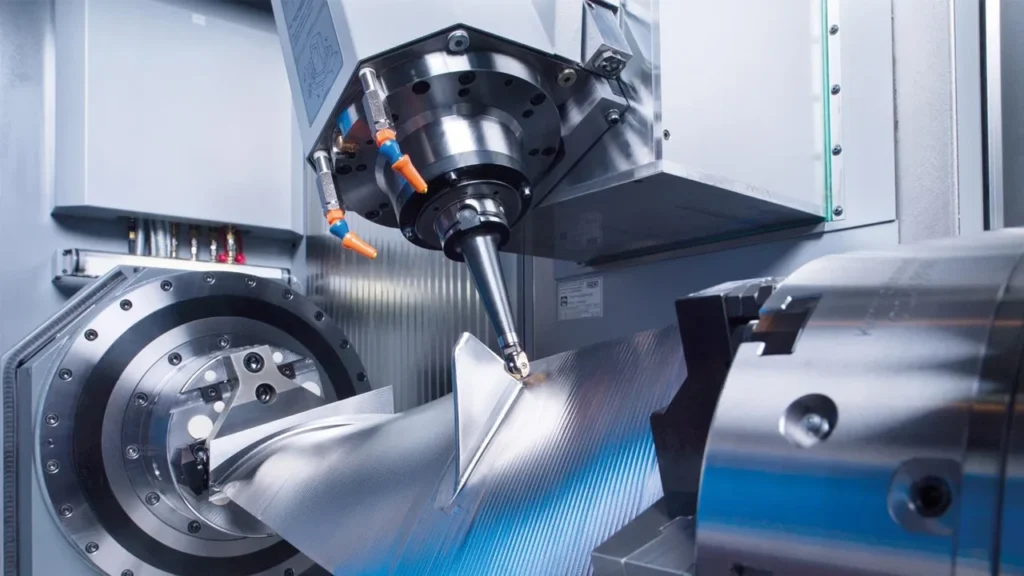
Check for After-Sales Support and Warranty
Purchasing a machining center is a long-term investment, and ensuring reliable after-sales support and warranty coverage is crucial for minimizing downtime and maintaining operational efficiency.
Key Considerations:
- Does the manufacturer offer comprehensive after-sales support and training?
- Are spare parts readily available for the machine model?
- What is the duration and coverage of the warranty?
Recommendation:
- Partner with reputable machining center manufacturers who provide prompt technical support and maintenance services.
- Verify the availability of replacement parts and ensure that the warranty covers critical machine components.
Analyze Automation and Integration Capabilities
Modern machining centers often come with automation features such as robotic tool changers, pallet changers, and IoT-enabled monitoring systems. These features enhance productivity and enable lights-out manufacturing for increased efficiency.
Key Considerations:
- Do you require automation for high-volume, continuous production?
- Will your machining center need to integrate with existing ERP or MES systems?
- Are you planning to implement IoT-based predictive maintenance systems?
Recommendation:
- Opt for machining centers with advanced automation options to reduce labor costs and increase throughput.
- Consider models that support integration with Industry 4.0 technologies for real-time monitoring and predictive maintenance.
Maintenance and Best Practices for Machining Centers
To ensure that a machining center operates at peak efficiency and maintains high precision over its lifetime, regular maintenance and adherence to best practices are essential. Neglecting maintenance can lead to machine breakdowns, reduced accuracy, and costly downtime. Below, we’ll explore the critical maintenance tasks and best practices that can prolong the lifespan of your machining center and optimize its performance.
Daily Maintenance Checklist
Performing a daily maintenance routine helps to prevent the buildup of debris and ensures that critical components operate smoothly. Daily inspections also allow operators to identify potential issues before they escalate.
Daily Tasks:
- Clean the worktable, spindle, and tool magazine to remove chips and debris.
- Check the lubrication system and ensure that oil levels are adequate.
- Inspect coolant levels and refill if necessary.
- Verify that the automatic tool changer (ATC) operates smoothly.
- Monitor spindle temperature to detect early signs of overheating.
Weekly and Monthly Maintenance Tasks
In addition to daily tasks, weekly and monthly maintenance routines focus on inspecting and calibrating critical machine components to ensure long-term accuracy and reliability.
Weekly Tasks:
- Inspect the spindle and tool holder for signs of wear or damage.
- Check the condition of the coolant system and clean the filters.
- Verify the accuracy of the tool changer and ensure that tools are properly seated.
- Inspect all safety systems, including emergency stop mechanisms.
Monthly Tasks:
- Clean and lubricate linear guides and ball screws to prevent friction.
- Check the alignment and calibration of the spindle and worktable.
- Inspect electrical connections for any signs of wear or overheating.
- Evaluate the condition of the coolant hoses and replace if necessary.
Importance of CNC Software and System Updates
Keeping the CNC software and control system up to date is essential to maintain optimal machining performance and ensure compatibility with advanced programming features. Manufacturers regularly release firmware updates that improve system stability, enhance machining capabilities, and fix bugs.
Best Practices:
- Regularly check for CNC software updates and install them as recommended by the manufacturer.
- Back up machine parameters and CNC programs to prevent data loss.
- Verify compatibility between the CNC system and new CAD/CAM software versions.
- Conduct periodic training sessions to ensure that operators are familiar with updated features.
Proactive Spindle and Toolholder Maintenance
The spindle and toolholder are critical components that directly impact the quality of machining operations. Regular inspection and maintenance can prevent spindle failure and ensure that the toolholder maintains a secure grip on the cutting tool.
Best Practices:
- Clean the spindle taper and toolholder interface to prevent contamination.
- Inspect the spindle bearings for signs of wear and replace them if necessary.
- Check the drawbar for consistent clamping force and make adjustments as needed.
- Use high-quality cutting fluids to reduce heat buildup and extend spindle life.
Coolant System and Chip Management
A well-maintained coolant system prevents overheating, reduces tool wear, and improves surface finish. Efficient chip management ensures that chips do not accumulate in the work area, reducing the risk of tool breakage and maintaining machining accuracy.
Best Practices:
- Monitor coolant concentration levels and adjust as needed.
- Clean coolant filters and replace them regularly to prevent clogging.
- Use chip conveyors or augers to efficiently remove chips from the work area.
- Inspect coolant nozzles to ensure that they direct coolant properly onto the cutting zone.
Lubrication and Linear Guide Maintenance
Proper lubrication reduces friction between moving components and minimizes wear, ensuring smooth machine operation. Linear guides and ball screws require regular lubrication to prevent premature wear and maintain machining accuracy.
Best Practices:
- Use manufacturer-recommended lubricants to maintain compatibility.
- Set up an automatic lubrication system to ensure consistent oil distribution.
- Inspect linear guides for signs of wear and replace damaged components immediately.
- Clean ball screws and linear rails to prevent the accumulation of dust and debris.
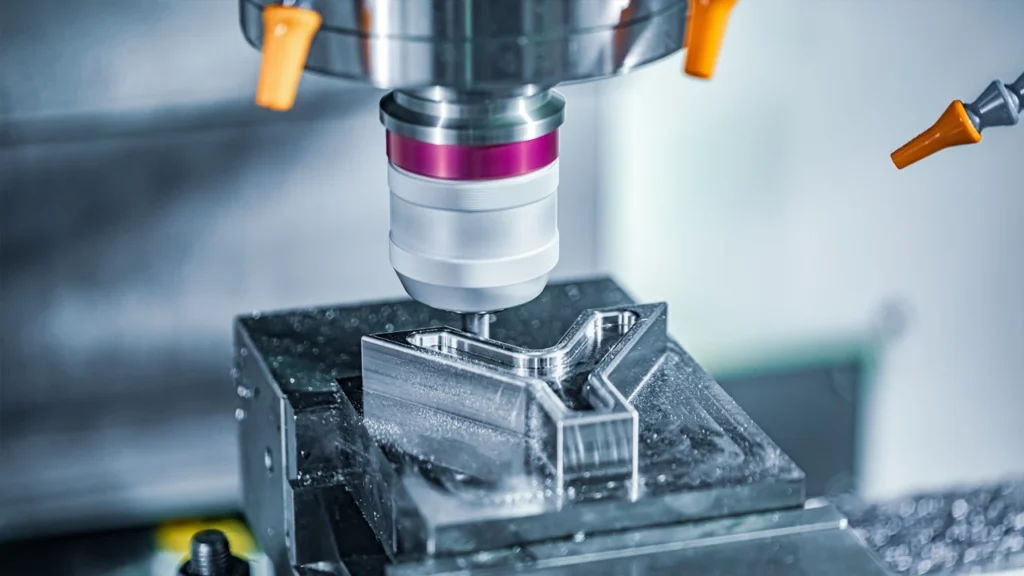
Troubleshooting Common Issues
Even with regular maintenance, unexpected issues can occur during machining operations. Being prepared to troubleshoot common problems helps reduce downtime and restore machine functionality quickly.
Common Issues and Solutions:
- Inaccurate Tool Changes: Check the ATC alignment and recalibrate if necessary.
- Excessive Vibration During Machining: Inspect the spindle and toolholder for imbalance or wear.
- Poor Surface Finish: Verify tool sharpness, adjust spindle speed, and optimize feed rate.
- Coolant Leaks: Inspect hoses, seals, and pumps for damage and replace if needed.
Preventive vs. Predictive Maintenance
While preventive maintenance involves performing scheduled tasks to keep the machine running smoothly, predictive maintenance uses data analytics and IoT-enabled sensors to predict potential failures before they occur. Implementing a combination of both approaches can maximize uptime and extend the lifespan of your machining center.
Key Differences:
- Preventive Maintenance: Regularly scheduled tasks to prevent equipment failure.
- Predictive Maintenance: Uses real-time data to anticipate equipment wear and reduce unexpected downtime.
Maintaining Machine Alignment and Calibration
Over time, machining centers may experience slight shifts in alignment, impacting machining accuracy. Regular alignment checks and calibration ensure that the machine maintains its original accuracy and performance standards.
Best Practices:
- Use laser calibration systems to check machine alignment periodically.
- Inspect worktable flatness and spindle perpendicularity to maintain dimensional accuracy.
- Perform geometric alignment to ensure consistent positioning accuracy.
Future Trends in Machining Centers
As technology continues to evolve, machining centers are becoming smarter, faster, and more efficient. The integration of advanced automation, artificial intelligence (AI), and Industry 4.0 technologies is transforming the machining industry and paving the way for a new era of precision manufacturing. Below, we’ll explore the most promising future trends shaping the world of machining centers.
Adoption of AI and Machine Learning in Machining
The integration of artificial intelligence (AI) and machine learning (ML) is revolutionizing how machining centers operate by enabling real-time decision-making and process optimization. AI algorithms can analyze vast amounts of machining data to predict equipment failures, optimize tool paths, and suggest process improvements.
Key Benefits:
- Predictive Maintenance: AI-driven predictive models can identify potential equipment failures before they occur, reducing unexpected downtime.
- Optimized Tool Paths: Machine learning algorithms can adjust tool paths dynamically to minimize tool wear and enhance surface finish.
- Automated Process Adjustments: AI can fine-tune machining parameters based on real-time data, ensuring optimal cutting performance.
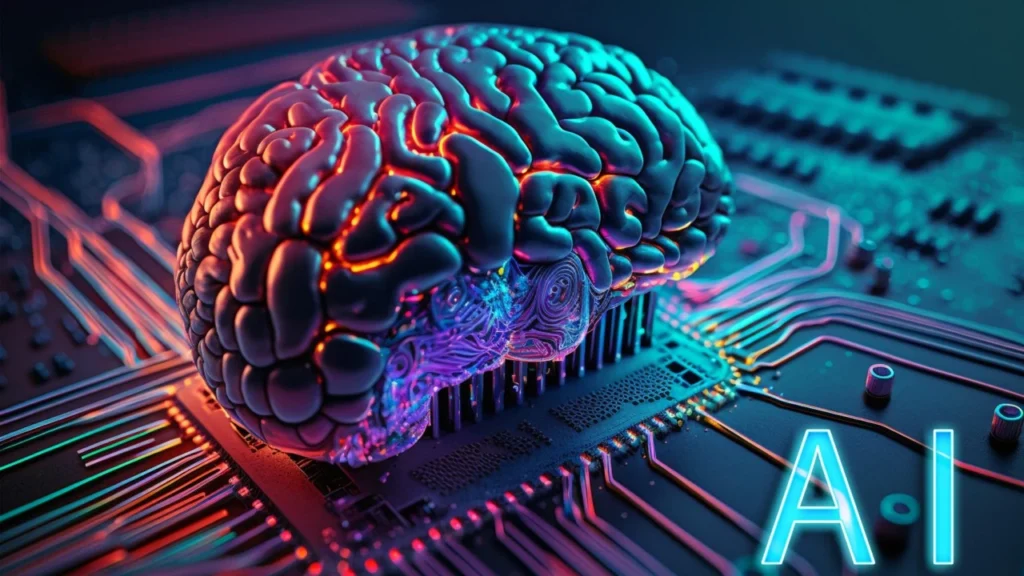
Integration of IoT and Industry 4.0 Technologies
The adoption of Industrial Internet of Things (IIoT) and Industry 4.0 technologies is enabling machining centers to become connected, intelligent, and self-monitoring systems. Sensors embedded in machining centers can collect real-time data and transmit it to cloud-based platforms for analysis and remote monitoring.
Key Benefits:
- Remote Monitoring and Control: Operators can monitor machine performance and make adjustments remotely.
- Data-Driven Insights: Continuous data collection helps identify trends and areas for process optimization.
- Enhanced Quality Control: Real-time feedback allows for immediate correction of deviations during machining.
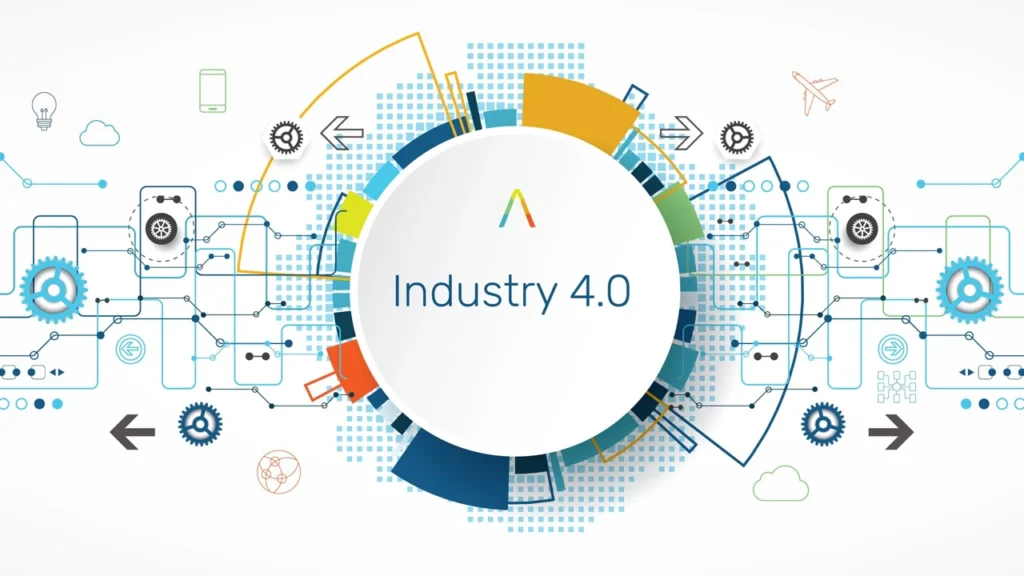
Advanced Automation and Lights-Out Manufacturing
The future of machining centers lies in lights-out manufacturing, where machines operate autonomously with minimal human intervention. Advanced automation systems, including robotic pallet changers, automatic tool changers, and robotic loading/unloading systems, are making it possible for machining centers to run 24/7.
Key Benefits:
- Increased Throughput: Lights-out operations enable continuous production, reducing idle time and increasing overall productivity.
- Lower Labor Costs: Automation reduces the need for human supervision, minimizing labor costs.
- Consistent Quality: Automated systems ensure consistent part quality by eliminating manual errors.
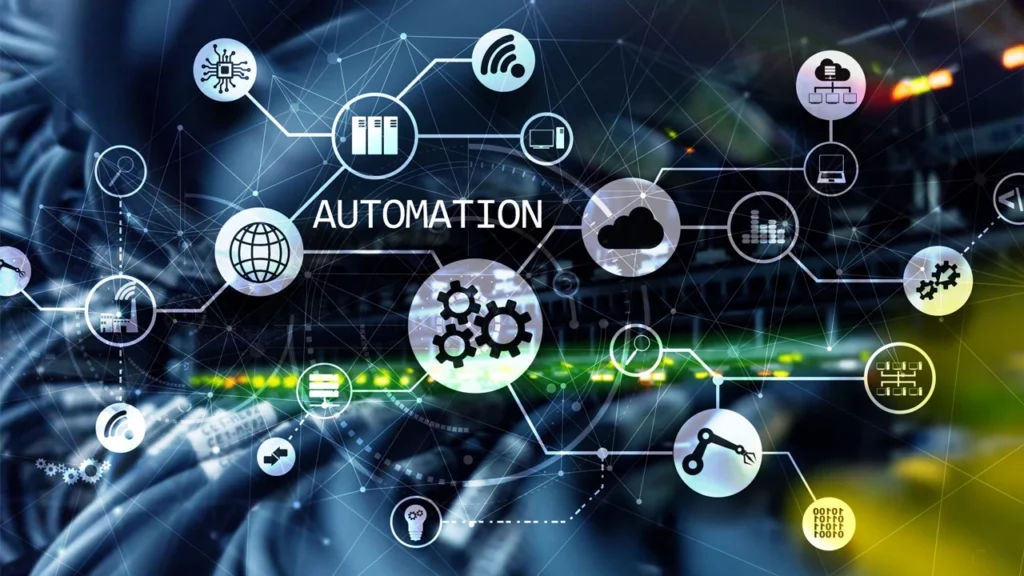
Growth of 5-Axis and Multi-Axis Machining
The demand for 5-axis and multi-axis machining centers is expected to rise as industries increasingly require the ability to machine complex geometries with minimal setups. 5-axis machining centers provide enhanced flexibility, allowing for the production of intricate parts used in aerospace, medical, and mold manufacturing.
Key Benefits:
- Reduced Setup Time: Multi-axis machining reduces the need for multiple setups.
- Improved Accuracy: Simultaneous multi-axis movement allows for precise machining of complex shapes.
- Enhanced Surface Finish: Reduced repositioning improves surface quality and reduces errors.
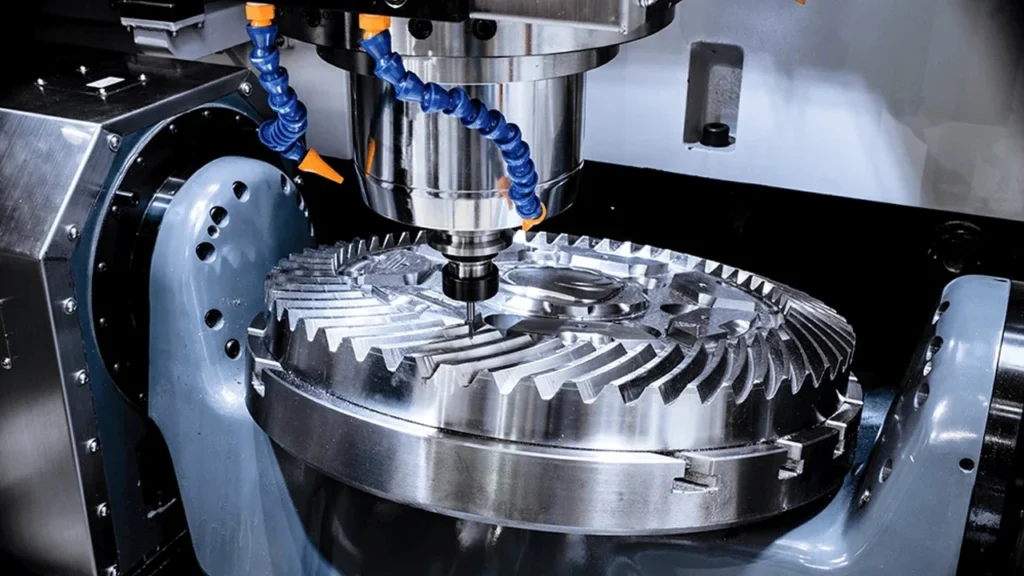
Digital Twin Technology for Virtual Machining
Digital twin technology is emerging as a game-changer in the machining industry. A digital twin is a virtual replica of a physical machining center that simulates the machining process in real-time. Manufacturers can test, optimize, and validate machining operations in a virtual environment before implementing them on the shop floor.
Key Benefits:
- Process Optimization: Digital twins allow for virtual simulations to fine-tune machining parameters.
- Reduced Errors: Identifying potential errors before actual machining reduces scrap rates.
- Faster Prototyping: Accelerates product development by validating designs in a virtual environment.
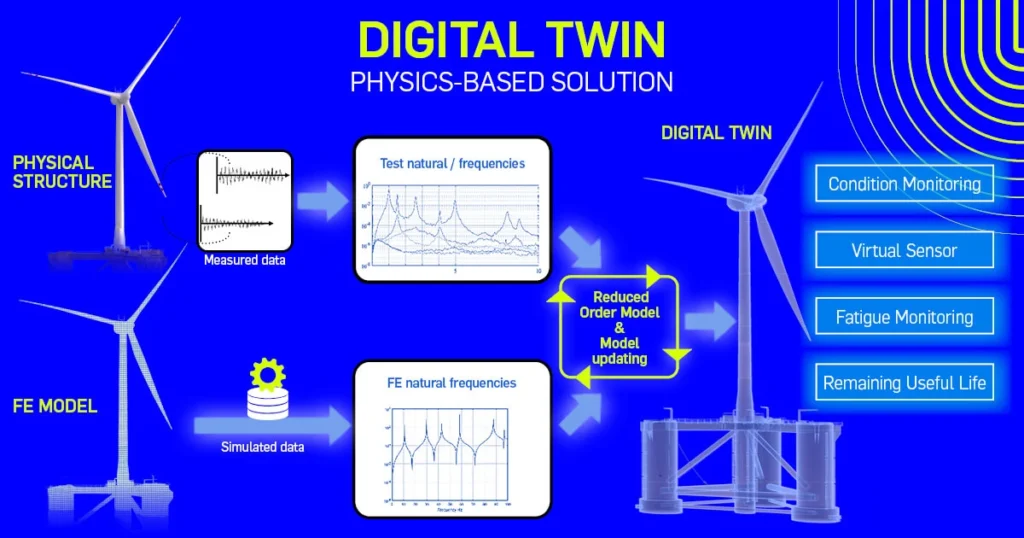
Increased Adoption of Hybrid Machining Technology
Hybrid machining centers combine additive manufacturing (AM) and subtractive machining (SM) to offer greater flexibility and efficiency in part production. These machines allow manufacturers to 3D print complex geometries and then finish them with precision machining processes.
Key Benefits:
- Reduced Material Waste: Additive manufacturing minimizes material waste compared to traditional machining.
- Faster Prototyping and Production: Hybrid machines combine printing and finishing in one setup.
- Greater Design Flexibility: Enables the production of intricate designs that were previously impossible.
Emphasis on Sustainable and Eco-Friendly Machining
Sustainability and environmentally conscious machining are becoming increasingly important as manufacturers strive to reduce their carbon footprint. Machining centers are being designed to be energy-efficient while incorporating technologies that minimize coolant usage, reduce chip waste, and optimize cutting processes.
Key Benefits:
- Reduced Energy Consumption: Energy-efficient motors and smart cooling systems lower power usage.
- Minimized Coolant Usage: Eco-friendly coolant systems reduce environmental impact.
- Sustainable Manufacturing Practices: Compliance with environmental regulations and reduced waste generation.
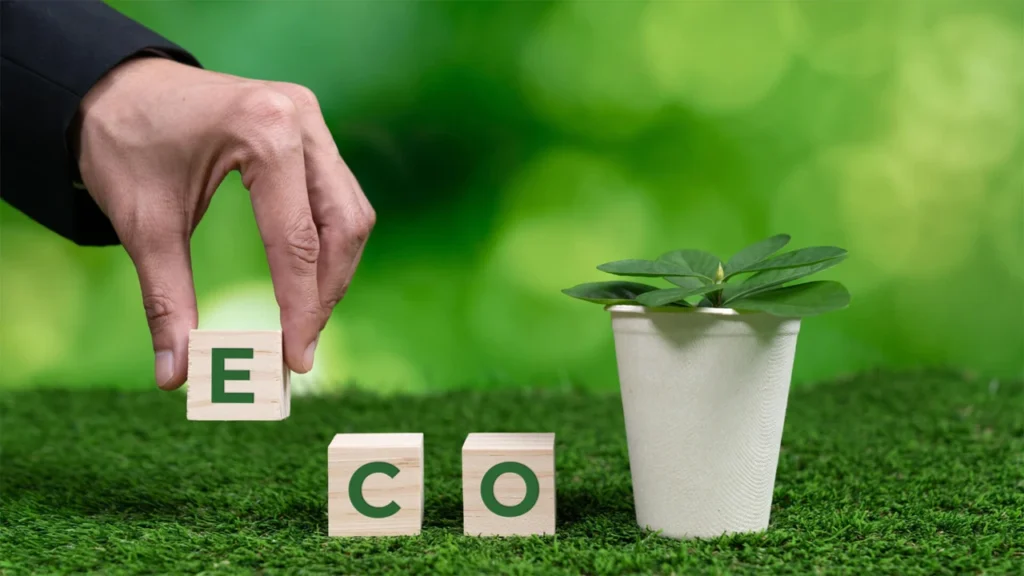
Adoption of Collaborative Robots (Cobots) in Machining Centers
The integration of collaborative robots (cobots) with machining centers is enhancing operational efficiency by enabling safe human-machine collaboration. Cobots can handle tasks such as material loading, part inspection, and quality control while working alongside human operators.
Key Benefits:
- Increased Flexibility: Cobots can be quickly reprogrammed to handle different tasks.
- Enhanced Safety: Cobots are designed to operate safely alongside human workers.
- Improved Efficiency: Automation of repetitive tasks allows human operators to focus on higher-value activities.
Expansion of AI-Driven Quality Inspection Systems
AI-driven visual inspection systems are improving quality control in machining centers by detecting defects and deviations with high accuracy and speed. These systems use machine vision and deep learning algorithms to inspect machined parts in real-time.
Key Benefits:
- Higher Accuracy: AI systems can detect minute defects that may be missed by human inspectors.
- Reduced Scrap Rates: Immediate identification of defects prevents defective parts from progressing further.
- Faster Inspection Cycles: Real-time inspection accelerates the quality control process.
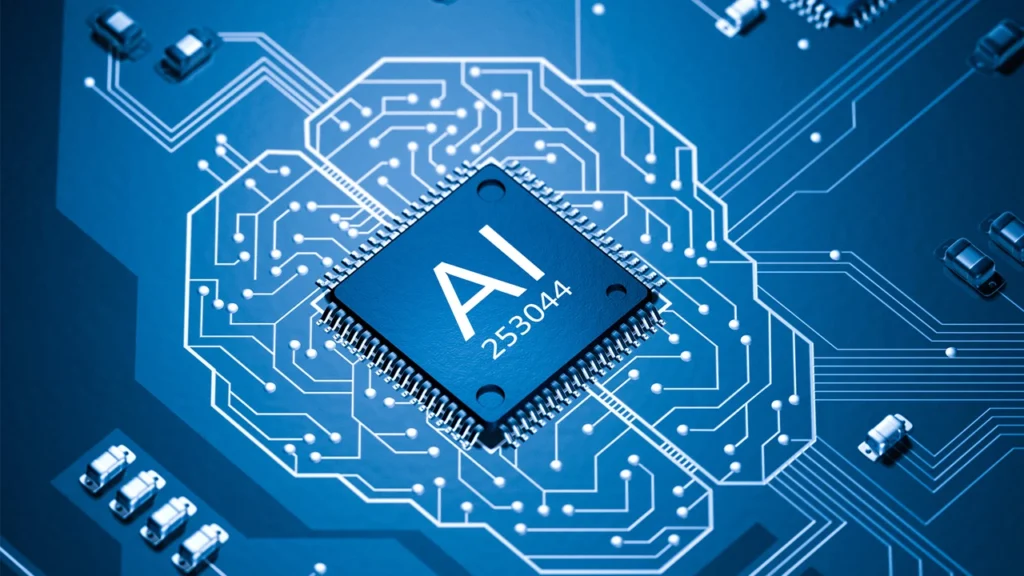
Conclusion: What is a Machining Center
As machining centers continue to revolutionize modern manufacturing, their ability to perform multiple operations with high precision, speed, and consistency makes them an essential tool across various industries. Whether you’re producing intricate aerospace components, mass-producing automotive parts, or crafting highly detailed molds, machining centers provide the versatility and efficiency needed to meet demanding production requirements.
In this comprehensive guide, we explored:
- What a Machining Center Is: Understanding its role in combining multiple machining processes.
- How Machining Centers Work: Analyzing their working principles and core components.
- Types and Specialties: Comparing vertical, horizontal, gantry, and multi-axis configurations.
- Machining Processes They Can Perform: Exploring the wide range of machining processes such as milling, drilling, tapping, boring, reaming, threading, and even light turning operations that machining centers can execute with precision.
- Applications Across Industries: Highlighting how machining centers serve aerospace, automotive, medical, and other sectors.
- Advantages and Limitations: Balancing the benefits of automation with the challenges of maintenance, cost, and training.
- Guidance on Choosing the Right Machining Center: Exploring critical factors to consider for optimal performance.
- Best Maintenance Practices: Ensuring long-term reliability through regular maintenance and system updates.
- Future Trends: Discussing how AI, IoT, hybrid machining, and digital twin technologies are shaping the future of machining centers.
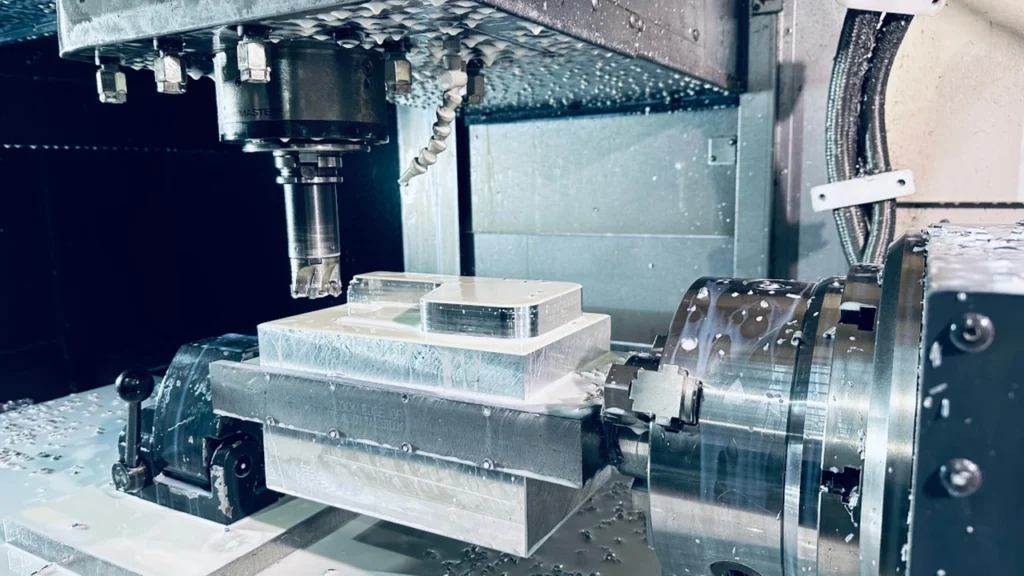
Why Investing in a Machining Center is a Game-Changer
Investing in the right machining center can dramatically enhance production efficiency, product quality, and operational flexibility. With the ability to perform multiple machining operations—such as milling, drilling, tapping, boring, and more—in a single setup, machining centers reduce cycle times, minimize human error, and improve overall workflow.
As the manufacturing landscape shifts toward automation and data-driven decision-making, machining centers equipped with AI-powered predictive maintenance, IoT-enabled monitoring, and digital twin simulations will continue to dominate the industry. Companies that embrace these innovations will gain a competitive edge by optimizing their processes and reducing overall costs.
Key Takeaways for Choosing and Maintaining a Machining Center
- Define Your Production Needs: Assess your workload, material types, and part complexity to determine the right type of machining center.
- Consider CNC Control and Spindle Power: Choose a system that supports advanced machining operations and ensures smooth performance.
- Prioritize Regular Maintenance: Implement a preventive maintenance schedule to extend machine life and maintain accuracy.
- Explore Future Technologies: Stay ahead of the competition by adopting Industry 4.0 solutions, AI-driven automation, and hybrid machining technologies.
Staying Ahead in a Competitive Industry
As global competition intensifies, staying ahead in the manufacturing industry requires continuous innovation and investment in cutting-edge technology. By leveraging the capabilities of modern machining centers, manufacturers can meet the growing demands for higher precision, reduced cycle times, and increased efficiency.
With their ability to perform a diverse range of machining processes and integrate with advanced technologies, machining centers remain a cornerstone of precision manufacturing. Whether you are an established manufacturer or an aspiring industry leader, choosing the right machining center and maintaining it properly will empower you to deliver exceptional quality and consistency while maintaining a competitive advantage.
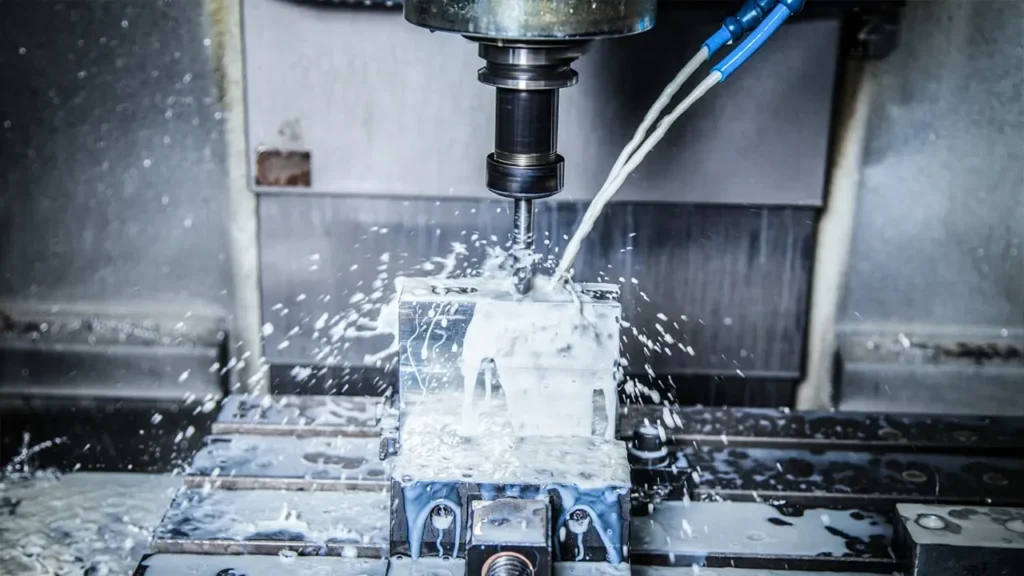
Why Choose Rosnok for Your Machining Center Needs?
At Rosnok, we specialize in providing high-quality CNC machining centers that deliver precision, durability, and efficiency for industries such as automotive, aerospace, medical, and mold manufacturing. Our machines come equipped with the latest CNC technology, automatic tool changers, and multi-axis capabilities to meet your most demanding production requirements.
With our 5 factory workshops covering over 60,000 square meters and internationally recognized certifications such as CE, ISO, TUV, CSA, and UL, we guarantee machines that meet the highest standards of quality and safety. Our commitment to after-sales support and technical expertise ensures that your operations run smoothly, maximizing productivity and minimizing downtime.
Partner with Rosnok today and experience the future of precision machining!
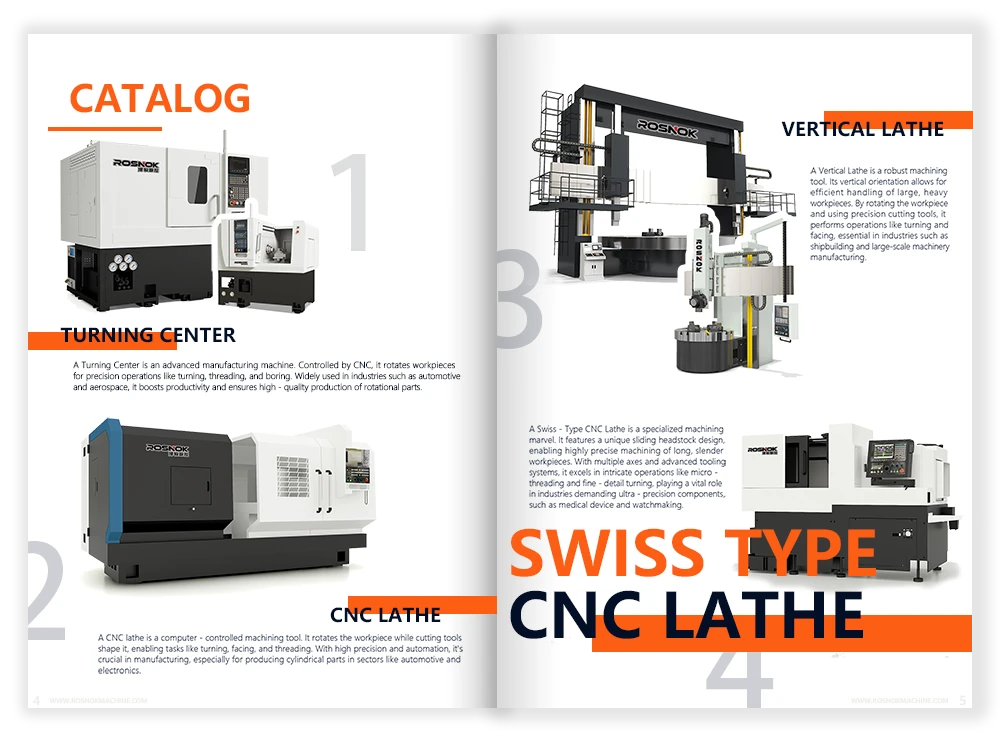