Do you want to understand what is a gantry machining center? What makes it different from other machining centers? How does it work, and what structures and components make it up? What types of operations can it perform, and what is its advantage? What types of workpieces or industries is it best suited for?
A gantry machining center is a large-format CNC machine with a bridge-style structure, designed for high-precision, multi-axis machining of heavy or oversized parts. Unlike conventional vertical or horizontal machines, the gantry system allows the cutting head to move freely across the working area above a stationary worktable, offering greater stability, broader travel range, and excellent load-bearing capacity. This makes it ideal for complex contouring, deep cavity milling, and large-part fabrication—especially where accuracy, rigidity, and versatility are critical.
Continue reading to learn what a gantry machining center is, how it works, what makes it different, its advantages, applications, and how to choose the right one for your needs.
What Is a Gantry Machining Center?
A gantry machining center is one of the most powerful machines in precision metalworking. In this section, we’ll break down exactly what it is, how it’s built, and why it’s become essential in today’s high-demand manufacturing environments.
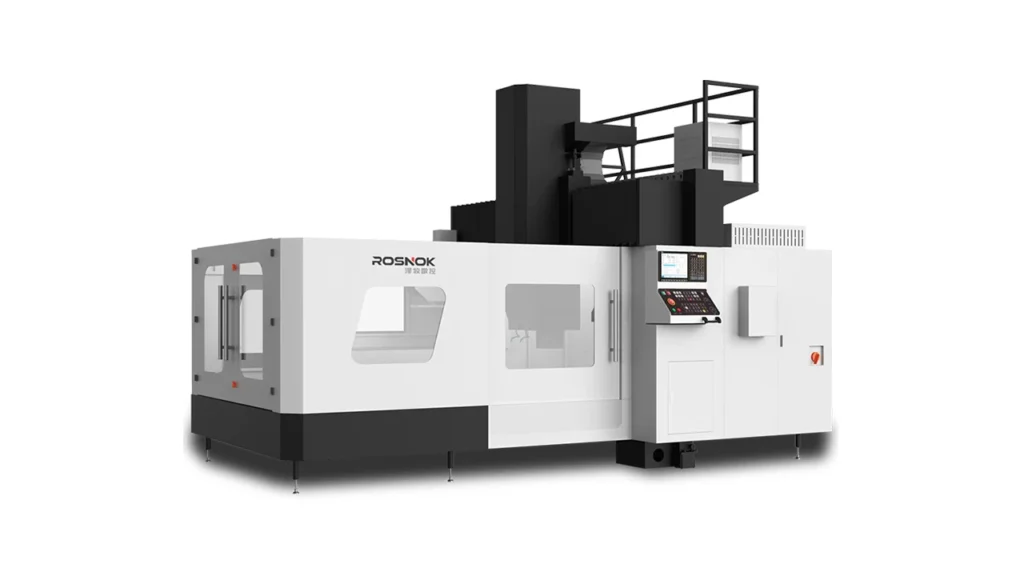
Basic Definition of Gantry Machining Center
A gantry machining center is a large-format CNC machine specifically designed to handle heavy, oversized, or geometrically complex parts. It features a bridge-style frame—known as the gantry—that spans across a fixed worktable. This structure supports a moving spindle head, which travels along multiple axes to perform machining operations without the need to reposition the workpiece.
The defining characteristic of this machine is the separation between the static worktable and the mobile cutting unit. The spindle moves over the part in multiple directions, allowing for consistent cutting paths and stable processing, even with long or wide components. This structural concept makes the gantry machining center ideal for tasks that demand both scale and precision. These machines often come with multi-axis systems, automatic tool changers, and advanced CNC controls to accommodate various metalworking applications.
Why It Matters in Modern Manufacturing
In today’s competitive manufacturing environment, industries face growing pressure to produce larger components, achieve tighter tolerances, and maintain consistent output quality. Sectors such as mold making, aerospace, and energy infrastructure rely on precision machining for mission-critical parts that often cannot be processed by standard equipment.
These demands have made gantry machining centers a go-to solution in modern workshops, valued not just for their structure but for the production efficiency and reliability they offer under pressure. Their ability to support heavy-duty operations while maintaining precision across large surfaces allows manufacturers to reduce cycle times, integrate multiple processes, and boost overall productivity without sacrificing accuracy.
Key Components of a Gantry Machining Center
Every gantry machining center is built on a combination of high-rigidity structures and precise motion systems. Its component layout determines how well it performs under load, how stable it remains during heavy machining, and how efficiently it handles complex parts. In this section, we’ll break down the key components that make up this powerful CNC machine and explain how each contributes to its performance and reliability.
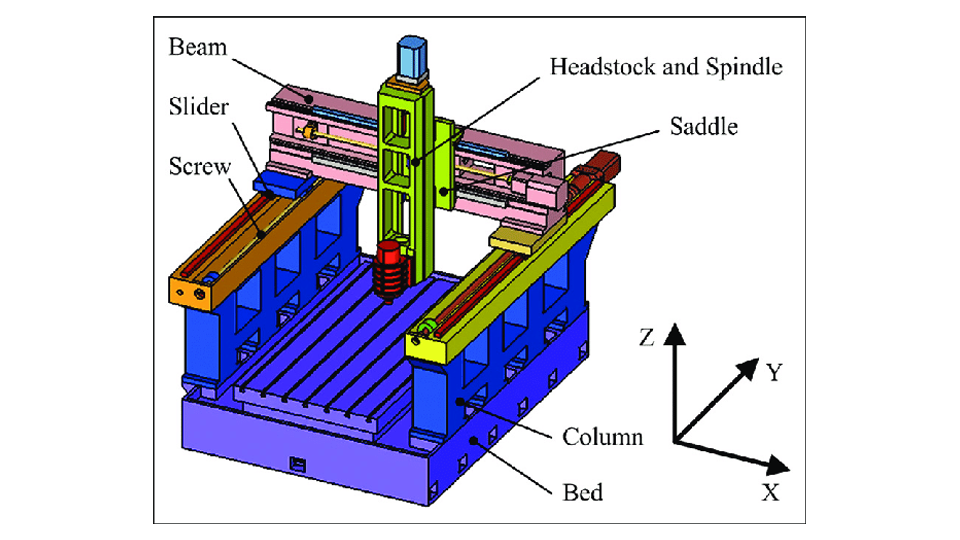
Gantry Frame and Dual-Column Stability
The gantry frame is the backbone of the machine. It consists of two vertical columns and a horizontal crossbeam, forming a rigid bridge structure that spans the entire worktable. These dual columns provide high structural stability and excellent resistance to bending and vibration—critical factors when machining heavy or long workpieces.
The frame components are typically made from reinforced cast materials that absorb dynamic forces during cutting. Their balanced design also minimizes thermal distortion, helping the machine maintain accuracy throughout long production cycles. The dual-column configuration is a key reason why gantry machining centers can deliver stable, precise results even under heavy workloads.
Multi-Axis Head and Cutting Range
At the heart of the gantry system is the spindle head, which moves along multiple linear axes. In most machines, this includes X (left-right), Y (front-back), and Z (up-down) movements. More advanced models may offer additional rotary axes for full five-axis simultaneous machining.
This multi-axis configuration expands the machine’s cutting range, enabling it to reach complex angles and perform detailed contours without repositioning the workpiece. This flexibility is especially valuable in gantry machines, where accessing large parts from multiple directions is essential for accuracy and efficiency.
Fixed Worktable and Load Capacity
Unlike other machining centers where the worktable may move during operation, gantry machining centers feature a fixed table. This design provides a stable base for holding oversized or heavy workpieces that require consistent support throughout the machining process.
The worktable is engineered for high load-bearing capacity, often supporting several tons of material without compromising flatness or stability. T-slots, grid plates, or custom fixturing systems are used to secure the part firmly in place. By keeping the table static, the machine reduces vibration and mechanical stress on the part, resulting in better surface finishes and dimensional accuracy.
Tool Magazine and Automatic Tool Changer
To support multi-step machining operations, gantry centers come equipped with tool magazines and automatic tool changers (ATC). These systems store and switch between various cutting tools such as drills, taps, roughing mills, and finishers—allowing the machine to handle complex tasks in a single setup.
Depending on the machine’s configuration, the magazine may hold 20 to over 100 tools. This setup reduces manual intervention, shortens production time, and enables the machine to complete a full machining sequence without interruption.
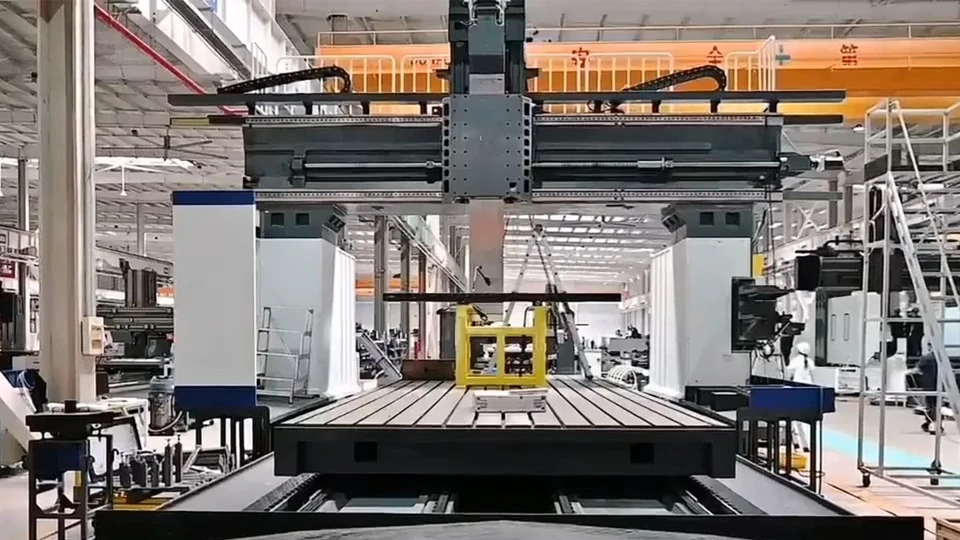
Linear Guides and Ball Screws
Gantry machining centers rely on linear guides and ball screws to move the gantry frame and support the precise movement of the cutting head. Linear guides are like rails that keep the movement straight and stable, while ball screws are spiral rods that push the moving parts along those rails. Together, they ensure smooth motion and accurate positioning across all axes.
These components are hidden within the machine frame but play a crucial role in every movement. Without them, the machine could not deliver consistent accuracy, especially when handling long toolpaths or heavy cutting loads. Their rigidity and durability directly impact machining quality and reliability over time.
Chip Removal System
During high-volume metal cutting, gantry machines generate a large amount of chips. If not removed promptly, these metal fragments can clog the work area, damage components, and reduce machining accuracy. The chip removal system solves this by automatically transporting chips away from the cutting zone using conveyors or flushing systems.
This system keeps the workspace clean and prevents overheating or tool jamming. For large or continuous operations, efficient chip removal is essential—it not only protects the machine but also helps maintain productivity and consistent surface finishes on the part.
Cooling System
Machining creates heat, especially during long cuts or high-speed operations. Excessive heat can cause tools to wear out quickly and may deform the workpiece. That’s why gantry machining centers include a cooling system—usually with coolant spray or oil mist—to keep both the tool and the work area at a stable temperature.
The cooling system helps extend tool life, improves surface quality, and ensures better dimensional accuracy. It also supports uninterrupted machining by reducing the chances of thermal expansion or material warping. Even for beginners, understanding this system is key to running the machine efficiently and safely.
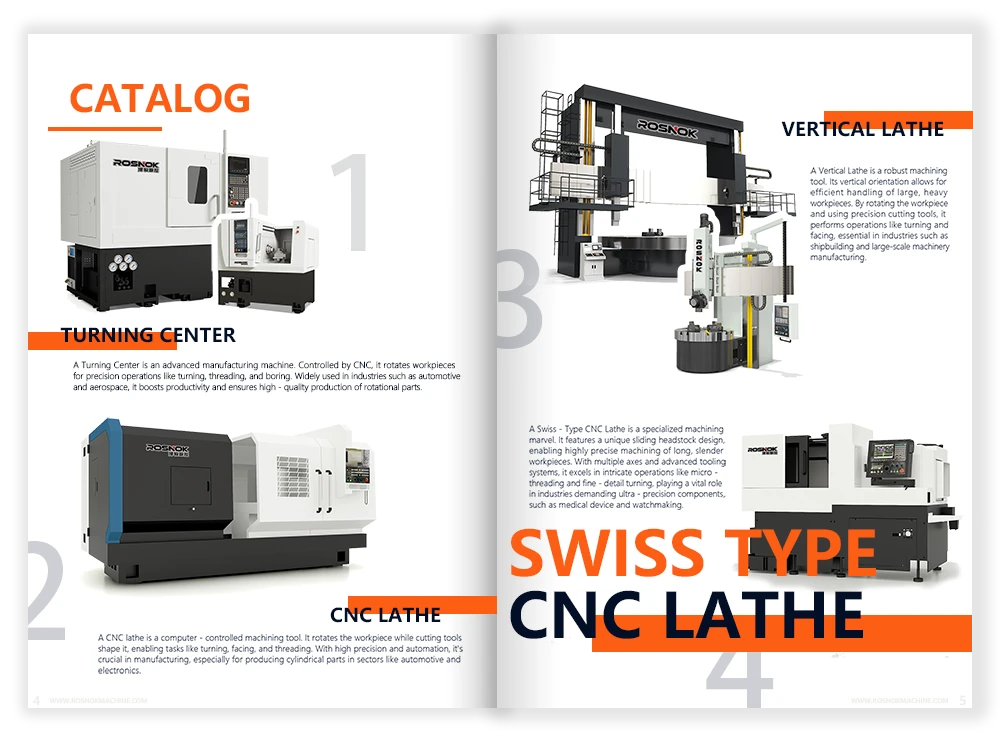
How Does a Gantry Machining Center Work?
Understanding how a gantry machining center operates provides essential insight into its real-world performance—from workpiece setup to precision control. In this section, you’ll see how the machine transforms code into movement and how its internal systems keep everything accurate, efficient, and consistent.
The Workflow from Setup to Finish
Operating a gantry machining center follows a clear, repeatable process. It begins with the operator securing the workpiece onto the fixed table using clamps, T-slots, or custom fixtures. Proper alignment at this stage ensures accuracy throughout the job.
The CNC program is then loaded. It contains the tool paths, speeds, depths, and operation sequence for the part. The program also prepares the automatic tool changer for the required operations, ensuring smooth tool transitions.
Once machining starts, the gantry frame moves along the X-axis while the spindle head follows the programmed path on the Y and Z axes. Ball screws and linear rails guide these movements with precision. The machine handles all tool changes automatically.
Meanwhile, chip removal and cooling systems work continuously to keep the work area clear and temperatures stable. When finished, the operator removes the part for inspection or the next step.
This streamlined process is built for speed, consistency, and accuracy—especially when dealing with large or complex parts.
CNC System Control and Accuracy Feedback
A gantry machining center’s precision depends on its CNC system. The controller translates the program into exact motor movements across all axes, coordinating the gantry, spindle, tool changer, and support systems in real time.
Servo motors and encoders constantly monitor positions. If the machine detects any deviation, it adjusts instantly. This closed-loop system corrects for tool wear, vibration, or thermal shifts.
Advanced models also compensate for load changes and temperature fluctuations during long operations. Some use sensors and smart algorithms to maintain accuracy even under demanding conditions.
This system is what enables gantry machining centers to achieve micron-level accuracy across large parts. Even beginners should understand that these machines don’t just follow instructions—they correct themselves to stay precise.
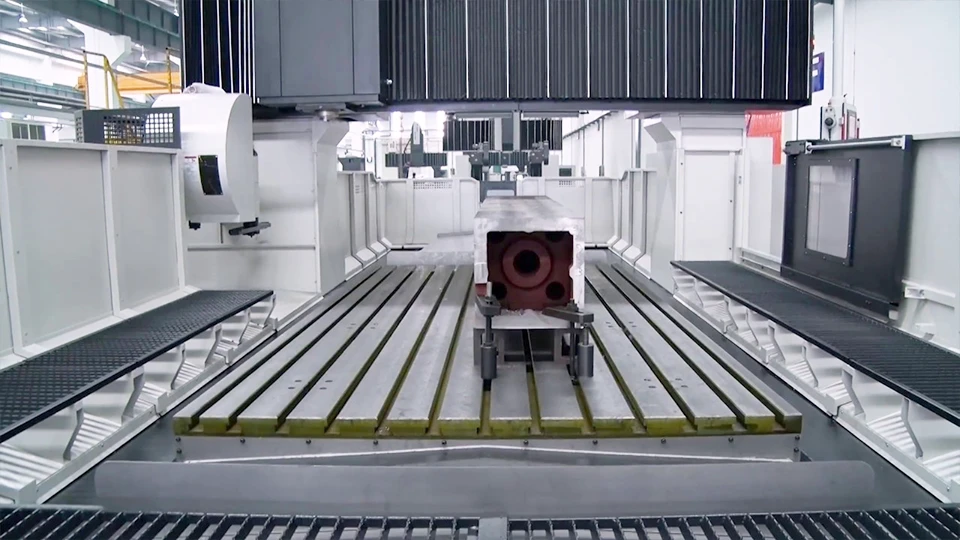
What Operations Can a Gantry Machining Center Perform?
Gantry machining centers support a range of core metal-cutting processes. Their rigidity, size, and multi-axis capabilities make them suitable for operations requiring both high precision and large working envelopes. Below are the most common machining tasks these systems perform.
Milling – Surface, Slot, and Cavity Work
Milling is the foundation of gantry machining. With its rigid gantry frame and precise spindle control, the machine handles both rough and finish milling across large surfaces. It easily manages contouring passes, deep cavity shaping, and pocket milling.
Slotting and grooving are also common, especially in mold making and structural work. The machine maintains excellent dimensional accuracy over long toolpaths, minimizing tool deflection and vibration. With proper fixturing and toolpath strategy, it can produce flatness and perpendicularity well within industry tolerances.
Drilling and Tapping – Holes and Threads
Gantry machining centers are well-equipped for high-precision drilling and tapping. The fixed worktable allows for stable hole positioning even on oversized parts. Whether it’s shallow pilot holes, deep drilled passages, or rigid tapping for internal threads, the machine delivers repeatable results.
Thread milling can be substituted where higher accuracy or non-standard threads are required. Combined with automated tool changes and Z-axis compensation, these machines ensure accurate hole depths, clean thread forms, and uniformity across multiple hole types and patterns.
Boring – Precision Inner Diameter Machining
Boring is critical when a part demands exact internal diameters. Gantry machining centers support boring operations with excellent concentricity and finish quality. The system minimizes vibration during tool engagement, which is key for maintaining roundness and surface accuracy in holes.
Whether enlarging an existing hole or achieving fine tolerances in a large bore, the rigid structure and stable tool movement allow for deep, straight internal cuts. This is especially important in mold bases, bearing seats, and heavy equipment housings.
Contouring and Profiling – Complex Shape Machining
Contouring refers to machining along complex paths, particularly 3D curves or compound surfaces. With multi-axis control, gantry machining centers can create complex profiles in a single setup, eliminating the need for manual repositioning.
This makes them ideal for mold cavities, die surfaces, turbine components, and other parts that require variable-depth cuts and smooth transitions. Precision control over each axis ensures surface quality remains high, even on difficult geometries or multi-directional curves.
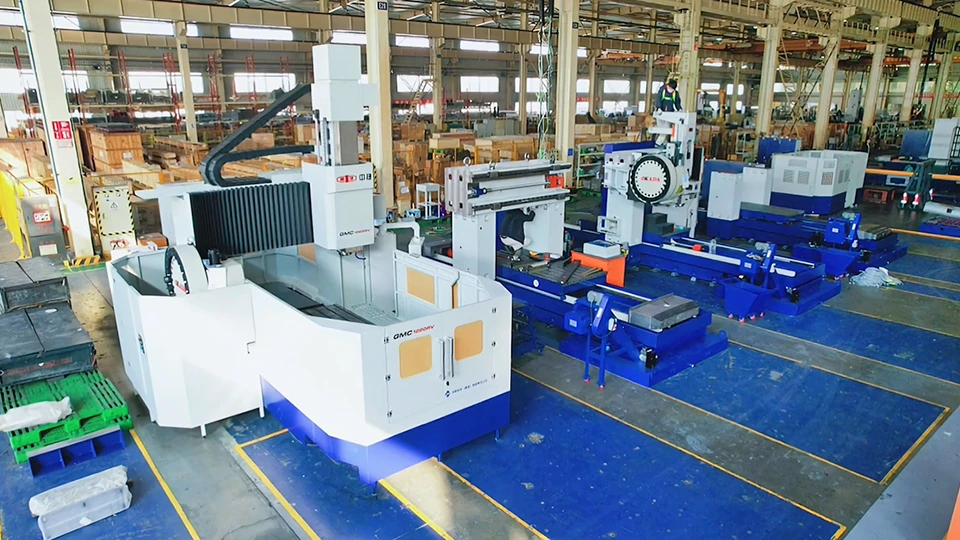
Advantages of Gantry Machining Centers
Beyond their sheer size, gantry machining centers bring a set of unique advantages that make them indispensable in modern manufacturing. Below are four core benefits that distinguish them from other CNC systems.
High Precision and Rigidity
One of the primary advantages of a gantry machining center is its exceptional structural rigidity. The double-column bridge frame ensures minimal deflection even during high-load operations. This rigidity is crucial for achieving tight tolerances, especially in deep cavity milling, 3D contouring, or fine detail work.
In addition, thermal stability plays a major role in maintaining accuracy. Most gantry machines are designed with heat-dissipating structures and compensating controls to offset thermal drift. This means the machine stays dimensionally consistent even during long production cycles, minimizing rework and ensuring part reliability.
Large-Part Machining Capability
Gantry machining centers are purpose-built to handle oversized and heavy workpieces. The fixed worktable and extended X/Y/Z travels provide ample space for components such as molds, aerospace frames, energy sector plates, or structural beams.
Traditional machines often require repositioning or multiple setups for large parts, but gantry centers eliminate this by offering full-area coverage in one setup. This not only saves time but also avoids alignment errors that could compromise quality. The ability to machine an entire large component in a single cycle makes gantry systems ideal for industries that deal with high-volume, large-scale components.
Process Integration and Flexibility
Flexibility is another standout strength of the gantry machining center. These machines support multiple operations—milling, drilling, tapping, boring, and more—within one unified system. With multi-axis heads and automatic tool changers, the machine adapts quickly to different tasks.
This integration allows manufacturers to reduce machine handovers and optimize cycle times. Whether producing custom parts or running high-mix batches, gantry machines provide the flexibility needed to switch seamlessly between operations while maintaining process consistency. This adaptability is a major asset in today’s lean and just-in-time production environments.
Stability Over Long Production Cycles
In many industrial applications, parts require extended machining times that stretch across hours or even full shifts. Gantry machining centers are specifically designed to maintain dimensional stability throughout these long runs. The combination of rigid mechanics, balanced design, and thermal compensation allows the machine to maintain accuracy without drift.
High-end models often include real-time monitoring of temperature, vibration, and axis deviation. This feedback is used to apply automatic corrections, ensuring that parts machined at hour six remain just as precise as those produced at hour one. This kind of long-cycle consistency is critical for industries where precision cannot degrade over time.
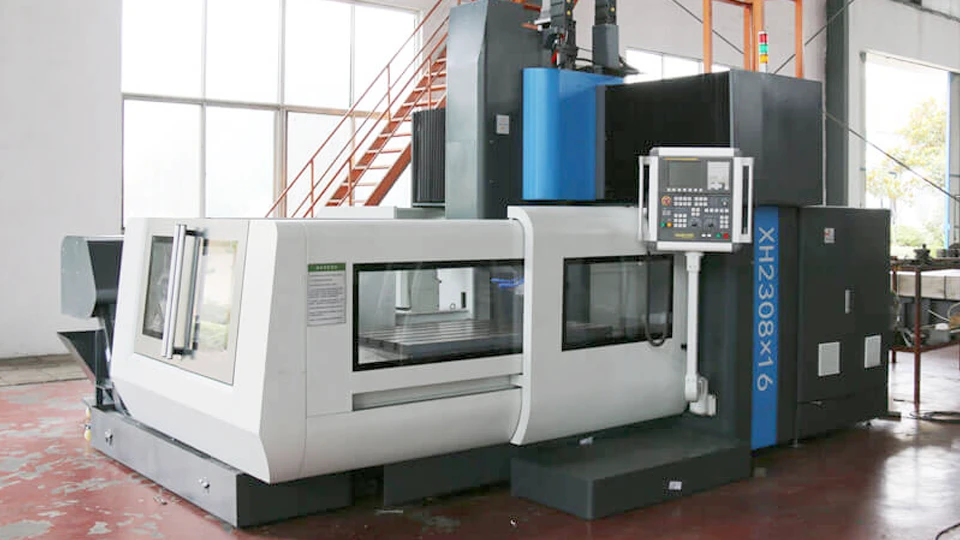
Gantry Machining Center vs Other CNC Machines
Gantry machining centers are powerful, but they’re not always the best fit for every job. How do they stack up against other common CNC machine types? Here’s a breakdown of their differences across structure, use cases, and performance.
Gantry vs Vertical Machining Center
Vertical machining centers (VMCs) are compact and cost-effective, making them ideal for small to medium-sized parts. The spindle moves vertically over a moving worktable, limiting part size and cutting flexibility. In contrast, gantry machining centers feature a bridge-style structure with a fixed table and moving gantry, allowing them to handle much larger and heavier parts.
While VMCs are excellent for high-speed work on simpler geometries, they fall short in rigidity, travel range, and multi-axis flexibility compared to a gantry system. If your operations involve large molds, dies, or structural frames, a gantry machine offers unmatched stability and processing scope.
Gantry vs Horizontal Machining Center
Horizontal machining centers (HMCs) position the spindle horizontally and often use a rotary table or pallet changer for multi-face access. This makes them efficient for box-type components and parts requiring frequent reorientation. HMCs shine in mid-sized production environments where fast tool access and chip evacuation matter.
However, HMCs have limited space and often require multiple setups for very large parts. Gantry machines, with their stationary table and open bridge structure, excel at machining oversized workpieces in one setup. While HMCs are great for throughput, gantry centers are superior for large-scale, high-precision structural machining.
Gantry vs Boring and Bridge Mills
Traditional boring mills and bridge mills are known for handling large components with precision. However, their designs often lack the dynamic range and automation features found in modern gantry machining centers. Boring mills typically rely on manual or semi-automated tool changes and have limited multi-axis flexibility.
Gantry machining centers integrate automatic tool changers, advanced CNC systems, and simultaneous multi-axis motion. This results in faster setup, more complex geometry support, and reduced human intervention. For operations that demand high throughput and tight tolerances on large parts, gantry machines offer a modern alternative with greater efficiency and process control.
Applications of Gantry Machining Centers
Gantry machining centers are used across a wide range of industries where size, precision, and process reliability are critical. Below are the most common industrial sectors where these machines have become essential.
Aerospace and Aviation
In aerospace manufacturing, gantry machining centers are relied upon for producing large structural components such as fuselage frames, wing spars, and landing gear housings. These parts often require tight dimensional control over long spans, which gantry machines deliver through their stable architecture and multi-axis precision.
Their ability to process titanium alloys, high-strength aluminum, and composites also makes them indispensable in this sector. With increasing demand for fuel-efficient aircraft, these machines help maintain accuracy while reducing cycle times for large part production.
Automotive and Industrial Equipment
Automotive and heavy equipment sectors use gantry machining centers for producing large molds, chassis components, stamping dies, and machinery frames. Their wide work envelope and rigid structure make them ideal for handling bulky parts that require consistent tolerances.
These machines are particularly useful in tool and die shops supporting automotive production lines. The ability to switch between different operations—milling, drilling, tapping—on the same setup improves productivity and minimizes downtime.
Energy and Infrastructure
The energy and infrastructure sectors often deal with oversized components such as wind turbine hubs, nuclear power brackets, and bridge support plates. These parts demand high rigidity and large cutting capacity, both of which are core strengths of gantry machining centers.
Their compatibility with heavy-duty materials and extended cutting ranges makes them ideal for long-run, high-force machining tasks in demanding environments. When dimensional integrity and throughput are equally critical, gantry machines prove to be the solution of choice.
Mold and Die Making
Mold and die manufacturing requires deep cavity milling, fine surface finishing, and complex contouring—all of which are strengths of gantry machining centers. These machines are widely used for making plastic injection molds, die-casting molds, and stamping dies.
The ability to support multi-axis interpolation and maintain surface accuracy over large molds helps reduce post-processing. Gantry systems are especially valuable in precision mold production, where repeatability and high-quality finishes are non-negotiable.
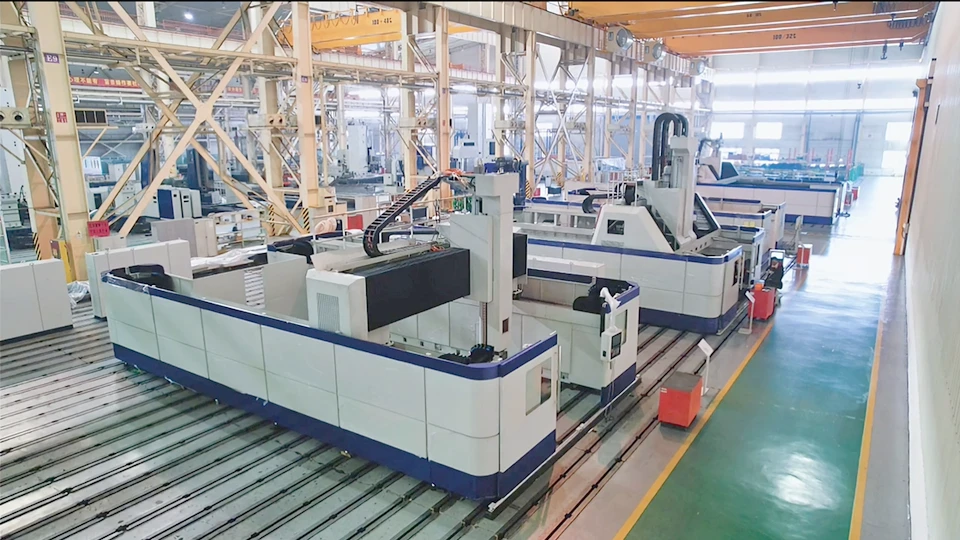
How to Choose the Right Gantry Machining Center
Selecting the right gantry machining center is not just about machine size or price. It’s about finding the best match for your specific parts, production goals, and factory conditions. Here’s how to make the right decision based on technical and operational priorities.
Match Machine Size to Workpiece Size
The first step is to align the machine’s travel range, table size, and load capacity with your largest and most demanding workpieces. Oversized molds, structural beams, or turbine housings require machines with extended X, Y, and Z axes, as well as a rigid table base. Be sure to include fixture dimensions and future part expansions when estimating space requirements. Under-sizing the machine risks repeated setups and compromised accuracy.
Consider Accuracy, Speed, and Tooling
Evaluate the spindle’s speed, power, and torque characteristics—especially if you work with hardened steel or aluminum alloys. Higher RPMs may be suitable for light finishing, while high-torque spindles are essential for roughing large cavities. Consider the automatic tool changer (ATC) capacity as well. If your workflow involves frequent tool changes, a larger ATC system reduces downtime and operator intervention. Look for machines with high positioning accuracy and thermal stability to ensure consistent results.
Evaluate Control System and Automation
The CNC control unit is the brain of the machine. Systems like FANUC and Siemens offer robust performance, wide compatibility, and scalable functions. Entry-level users may prefer simpler interfaces, while experienced operators benefit from advanced toolpath control, probing, and diagnostics. Don’t forget to assess automation readiness—options like automatic pallet changers, robotic loading, and remote monitoring can significantly improve efficiency in high-mix or long-run production setups.
Budget, Power, and Installation Requirements
Beyond the machine itself, consider the full cost of ownership. Gantry machining centers often require reinforced foundations, three-phase power supply, high ceilings, and wide doors for transport. Factor in shipping fees, installation time, maintenance access, and required air or coolant systems. A well-chosen machine should not only fit your technical needs but also your facility’s layout and operating budget.
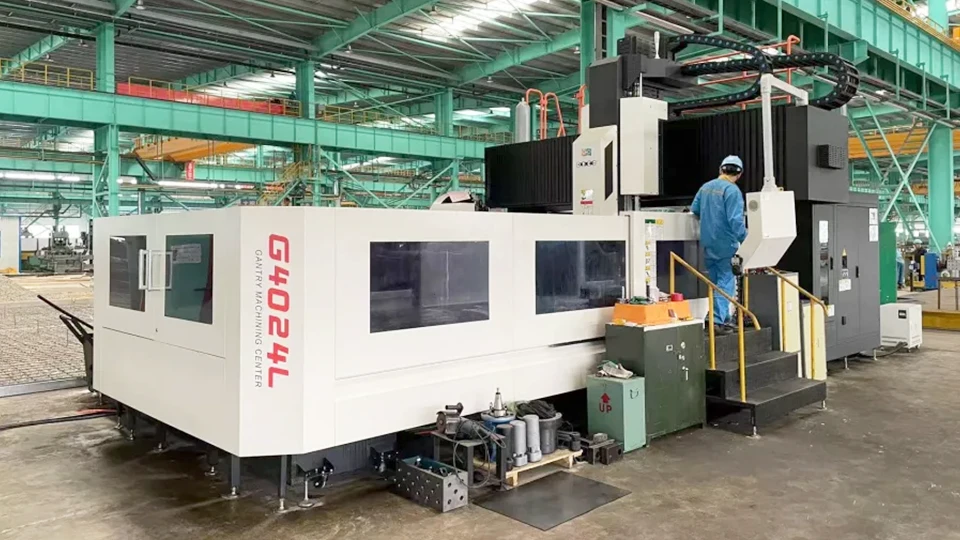
Common Mistakes Beginners Should Avoid
Buying a gantry machining center is a major investment, and beginners often make costly mistakes due to inexperience. Below are some common pitfalls to watch out for when selecting and installing this type of machine.
Oversizing or Undersizing the Machine
One of the most frequent mistakes is choosing a machine that doesn’t match the actual part requirements. Oversizing leads to excessive floor space usage, higher energy costs, and underutilized capacity. On the other hand, undersizing causes repeated repositioning, setup errors, and long-term workflow inefficiencies.
Always match the machine’s travels, table size, and load rating to the largest typical part—not just occasional outliers. It’s smarter to optimize around 80–90% of your production needs rather than over-invest in occasional extremes.
Ignoring Power, Floor Space, and Foundation
Many first-time buyers underestimate the machine’s infrastructure requirements. Gantry machining centers often need three-phase power, high ceilings, reinforced foundations, and specific floor layouts to accommodate travel ranges and safe operation.
Skipping this analysis can delay installation, cause voltage instability, or lead to mechanical imprecision from vibration or poor support. Always coordinate with your facility engineer to assess electrical capacity, ground stability, and machine access before placing an order.
Misunderstanding Maintenance and Operation
Another common oversight is assuming the machine will run itself without routine attention. Gantry machining centers require regular lubrication, spindle alignment checks, coolant monitoring, and chip evacuation maintenance. Skipping these basics leads to breakdowns, poor finish quality, and unnecessary downtime.
Additionally, untrained operators can misuse control systems or mishandle tools, increasing the risk of crashes and accidents. Always invest in onboarding training and assign clear responsibility for daily machine checks and upkeep.
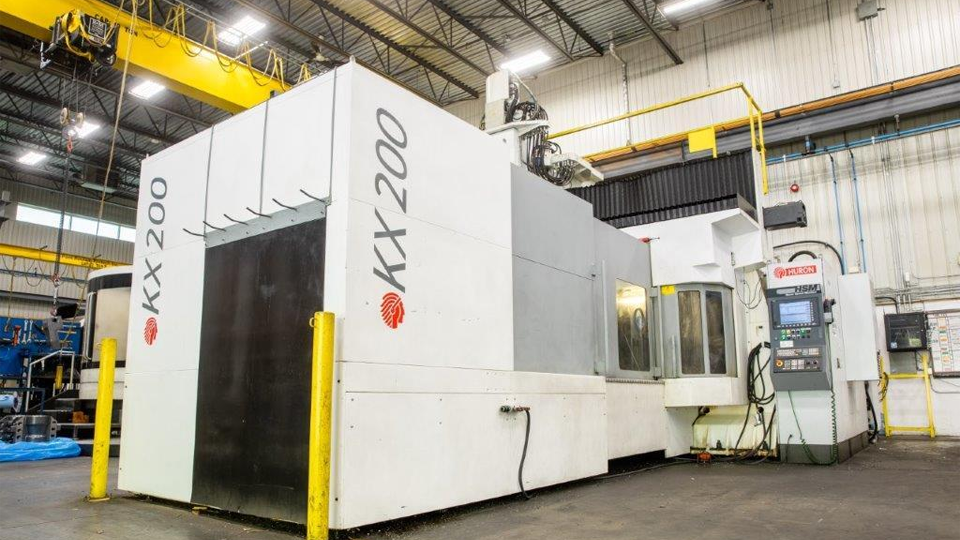
Conclusion: What Is a Gantry Machining Center
A gantry machining center is more than just a large-format CNC machine—it’s a precision tool built to handle complex, heavy, and oversized components with accuracy and stability. In this guide, we’ve explored what defines a gantry system, how it works, its core components, the types of operations it performs, and the reasons behind its growing adoption across modern industries. Whether you’re new to CNC machining or looking to expand your capabilities, understanding the structure, function, and advantages of gantry machining centers is key to unlocking their full potential.
For companies planning to adopt gantry machining centers, choosing the right equipment is more than just a purchase—it’s a strategic decision. Partnering with an experienced gantry machine builder ensures smarter investments and better long-term performance. With decades of expertise in designing and manufacturing gantry machining centers, Rosnok provides reliable, high-precision machines trusted across industries. Whether you’re upgrading equipment or expanding production capacity, working with a supplier like Rosnok means choosing precision, consistency, and lasting value.
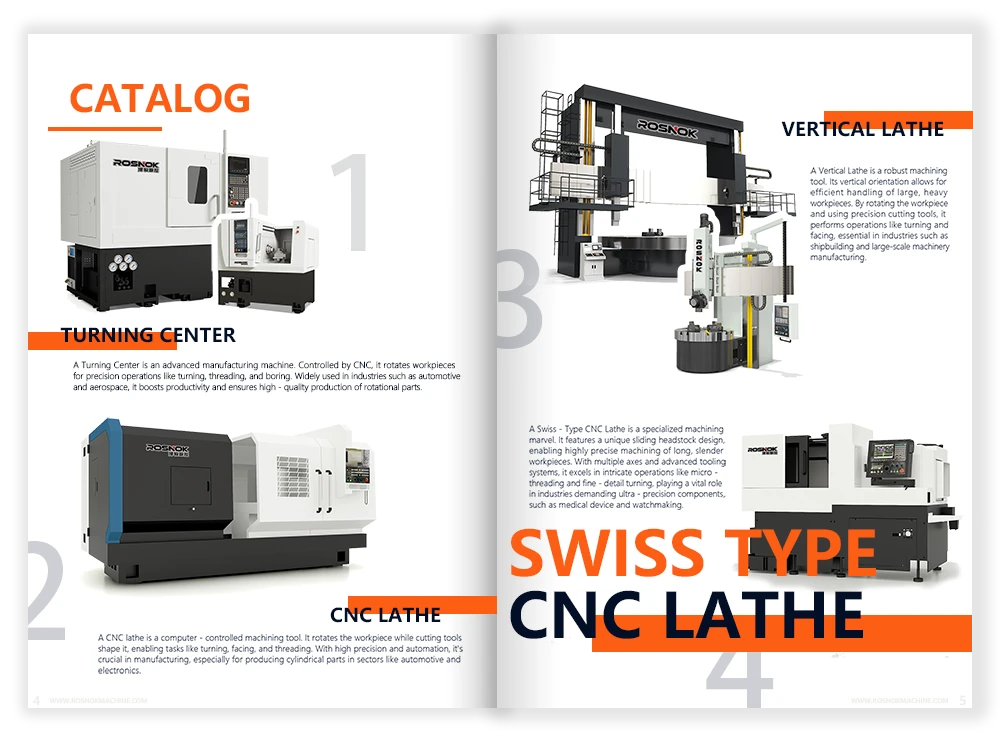