What is a CNC machine—and why is everyone in manufacturing talking about it? Can traditional machines still meet today’s demand for precision and speed? How are global factories producing thousands of flawless parts with zero human error? And more importantly—are you already behind if you’re not using CNC machines?
A CNC machine, or Computer Numerical Control machine, is an automated metalworking tool controlled by precise digital instructions—typically G-code. Unlike manual machines, CNC equipment executes pre-programmed tool paths to perform cutting, drilling, milling, or turning operations with extreme accuracy. It replaces human control with computer logic, enabling high-speed, high-volume, and high-precision production. From simple parts to complex components, CNC machines are the backbone of modern manufacturing, ensuring consistency, efficiency, and scalability across industries.
Continue reading this guide to learn what a CNC machine is, how it works, the key components that enable its precision, types of CNC machines, and their real-world applications.
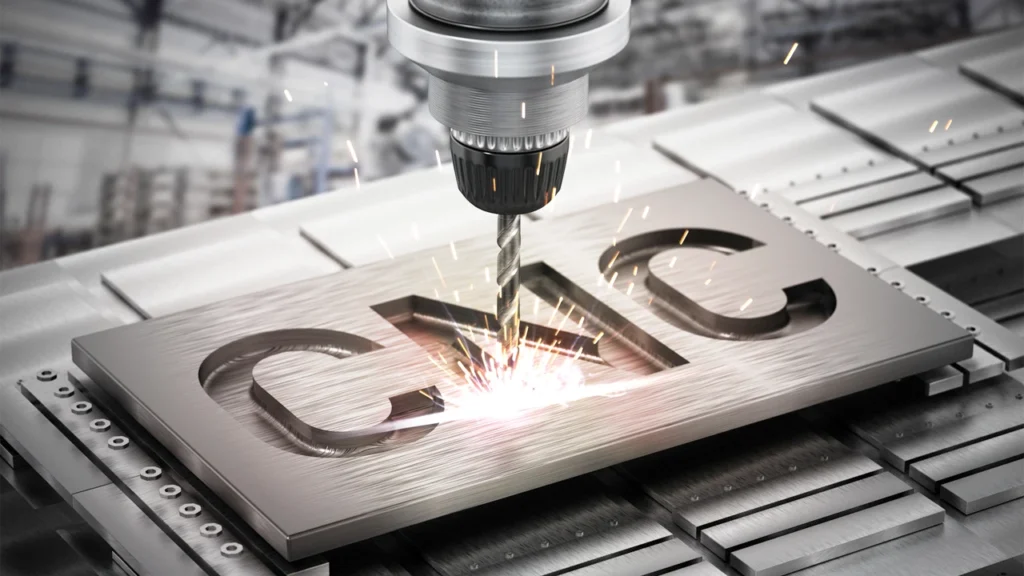
What is a CNC Machine?
CNC Machine Definition and Core Concept
A CNC machine, short for Computer Numerical Control machine, is an advanced, automated machine tool used to perform precise manufacturing tasks—such as cutting, drilling, milling, turning, and more—by following digitally coded instructions, usually written in G-code. Unlike traditional manual machines that rely on skilled hand operations, CNC machines execute pre-programmed tool paths with micron-level accuracy, ensuring repeatability, efficiency, and uninterrupted operation.
At its core, a CNC machine combines mechanical components (like spindles, guideways, and beds) with electronics (motors, sensors, control systems) and software (CAD/CAM integration, G-code execution). This integration allows it to convert a digital design into a tangible, finished metal part—automatically, consistently, and with minimal human intervention.
In today’s metalworking industry, CNC machines are essential for high-volume production, complex geometries, and tight tolerances. They form the backbone of modern manufacturing in sectors like automotive, aerospace, medical devices, and heavy equipment.
History and Evolution of CNC Technology
The origins of CNC machines trace back to the mid-20th century, when mechanical automation first appeared through punched tape controls. By the 1950s, engineers developed early numerically controlled (NC) machines, relying on simple programs and motors.
In the 1970s and 1980s, the rise of microprocessors ushered in the era of full computer numerical control, which enabled greater precision, multi-axis capabilities, and integrated software workflows. The 1990s introduced machining centers, automated tool changers, and CAD/CAM connectivity, expanding CNC applications across industries.
Today, CNC machines feature multi-axis motion, real-time diagnostics, remote control, and are integrated with IoT, AI, and cloud-based monitoring. They continue to redefine what modern machining is capable of.
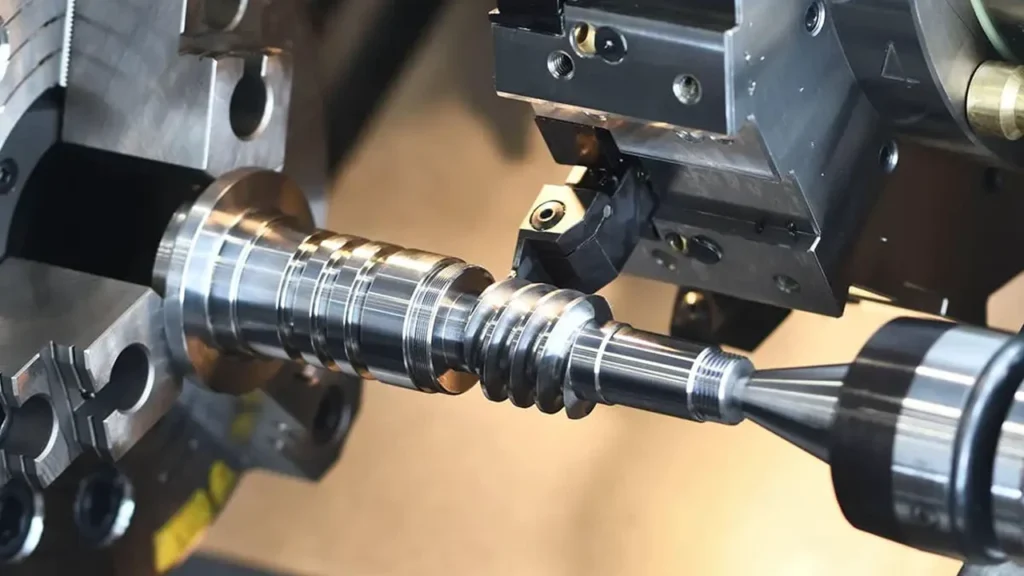
How Does a CNC Machine Work?
CNC Programming and Code Execution
At the heart of every CNC machine lies a digital control system that interprets specific coded instructions—commonly G-code and M-code—to guide the machine’s every movement. These codes define the toolpath, cutting depth, feed rate, spindle speed, and more.
Operators use CAD (Computer-Aided Design) software to design the part and CAM (Computer-Aided Manufacturing) software to convert the design into machine-readable instructions. These programs are then uploaded to the CNC controller, which executes each command in real time with remarkable precision.
For example, a G01 command tells the tool to move in a straight line, while M03 starts spindle rotation. The system processes these commands sequentially, ensuring the tool follows a meticulously defined path to shape the workpiece exactly as intended.
Spindle and Feed Motion
Once the program is loaded, the machine’s spindle starts rotating at the programmed RPM, while servo motors begin moving the tool or workpiece along the X, Y, and Z axes. This coordinated motion is the essence of CNC machining.
Ball screws, linear guideways, and encoders work in harmony to enable smooth and accurate movements. Each axis can be positioned to within microns, thanks to feedback control systems that constantly monitor and adjust position.
For example, when cutting a slot into an aluminum plate, the spindle spins the cutting tool while the feed system moves it steadily across the surface—ensuring perfect depth and alignment.
Tool Engagement and Material Removal
As the tool approaches the workpiece, it engages the surface and begins the material removal process. This can be done through various methods, such as turning, milling, drilling, or boring. The machine maintains constant contact between tool and material at the programmed speed and depth, gradually shaping the part.
The advantage of CNC machines is that this process is controlled automatically and consistently, eliminating human variability. This leads to smoother finishes, tighter tolerances, and faster production cycles.
Multi-Axis Synchronization
Many modern CNC machines feature 3, 4, or even 5-axis movement, enabling the tool to rotate or tilt for machining complex geometries from multiple angles. This is especially useful for aerospace components, medical parts, and molds that require compound surfaces.
In a 5-axis machine, for example, the cutting tool can simultaneously move in X, Y, and Z directions, while also rotating along the A and B axes. This allows for one-pass machining of highly intricate parts, reducing the need for multiple setups and manual repositioning.
Key Components of a CNC Machine
CNC Control System
The CNC control system is the “brain” of the entire machine. It interprets the G-code program and sends precise commands to every moving component—spindles, servo motors, tool changers, and more. Modern control units like FANUC, Siemens, and Mitsubishi are equipped with high-speed processors, touchscreen interfaces, real-time diagnostics, and even AI-assisted optimization tools.
These systems also include memory storage for multiple programs, connectivity options (USB, Ethernet), and intuitive operating software that allows both manual and automatic adjustments. Without a powerful and reliable control system, CNC precision and repeatability would be impossible to achieve.
Machine Bed and Linear Guideways
The machine bed is the foundation on which the entire CNC structure is built. It is typically made of cast iron or high-strength steel, designed to absorb vibrations and resist thermal deformation during heavy-duty machining.
Mounted on the bed are linear guideways or box ways, which direct the movement of the machine’s axes. Linear guideways offer high-speed, low-friction motion, ideal for precision parts. Box ways, though slower, provide greater rigidity and are suited for heavy cutting operations. A stable, precision-machined bed is critical for long-term machine accuracy and reliability.
Spindle System
The spindle is the power-delivery unit that holds and rotates the cutting tool or workpiece. Its speed, power, and bearing precision directly influence surface finish, cycle time, and tool life. CNC spindles are typically driven by servo motors or inverter-controlled motors, offering a wide RPM range—from a few hundred to over 20,000 RPM.
High-end CNC spindles may use ceramic bearings for minimal thermal expansion and advanced cooling systems (air or oil) to maintain stability during extended high-speed cutting.
Tool Holding and Changing System
The tool holder connects the cutting tool to the spindle, often using standardized systems such as BT, HSK, or CAT tapers. These holders are designed for quick tool exchange while maintaining precise alignment and rigidity.
For machining centers, an Automatic Tool Changer (ATC) is essential. It allows the machine to switch tools automatically during the machining process, following the programmed sequence. ATCs typically hold between 12 to 120 tools, and switching time ranges from 1 to 5 seconds. This system dramatically improves productivity and reduces operator intervention.
Servo Motors and Drive Mechanism
Servo motors and amplifiers control the linear and rotary axes of a CNC machine. These components ensure the tool follows exact paths with dynamic responsiveness. Feedback is constantly relayed via encoders or resolvers, allowing the controller to correct any deviations in real-time.
The drive mechanism—usually made of precision ball screws or linear motors—translates the servo motor’s rotation into smooth, backlash-free motion. Precision-grade components here ensure micron-level movement and positioning.
Coolant and Chip Evacuation
Efficient coolant systems are critical in CNC machining. They prevent tools and workpieces from overheating, remove chips from the cutting zone, and improve surface finish. CNC machines typically use flood coolant, high-pressure coolant (HPC), or minimum quantity lubrication (MQL) depending on the material and process.
Chip conveyors, augers, or vacuum systems are used to remove chips continuously, preventing buildup that could damage the tool or reduce accuracy.
Touch Probes and Sensors (Optional)
Many modern CNC machines are equipped with touch probes, used for automatic workpiece measurement, alignment, and zero-point setting. These probes eliminate the need for manual gauging, reducing setup time and increasing accuracy.
Sensors can also detect tool wear, breakage, coolant levels, or even vibration. Some advanced systems incorporate laser measurement and vision cameras for real-time quality control.
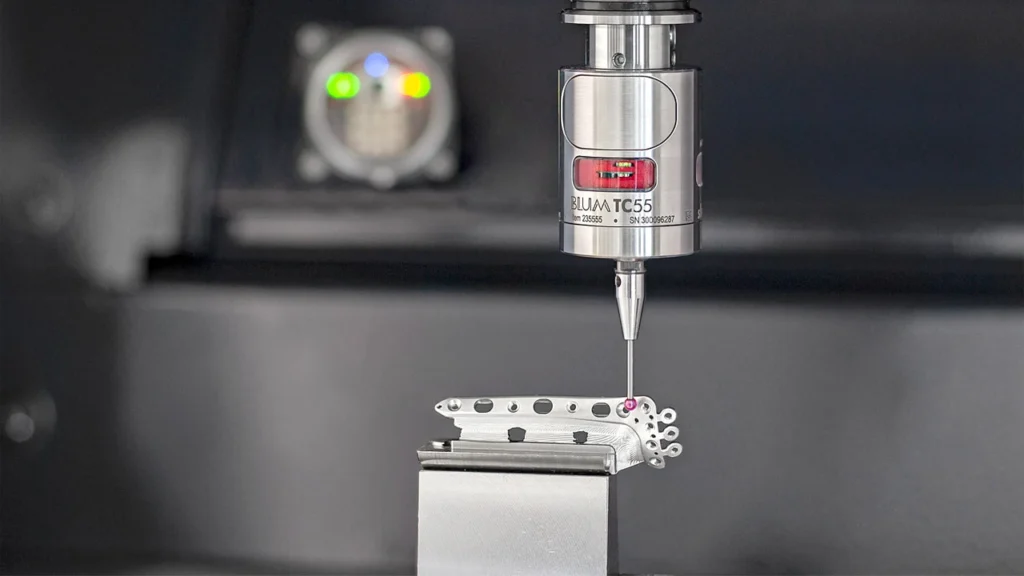
Types of CNC Machines and Their Applications
CNC Lathe
A CNC lathe is a high-precision machine designed to shape metal or plastic parts by rotating the workpiece against a fixed cutting tool. It excels in creating perfectly symmetrical, round components with high efficiency and repeatability.
The machine typically operates along two axes: X (radial) and Z (longitudinal). During operation, the material spins while the tool moves to cut external diameters, internal bores, and threads. CNC lathes can handle a wide range of operations including turning, facing, grooving, boring, and threading. Many models feature live tooling or sub-spindles to allow complex parts to be completed in a single setup.
CNC lathes are essential in manufacturing components like shafts, bushings, collars, and threaded fittings. They’re commonly used in the automotive industry, fluid control systems, general machining, and parts requiring cylindrical geometry and tight tolerance.
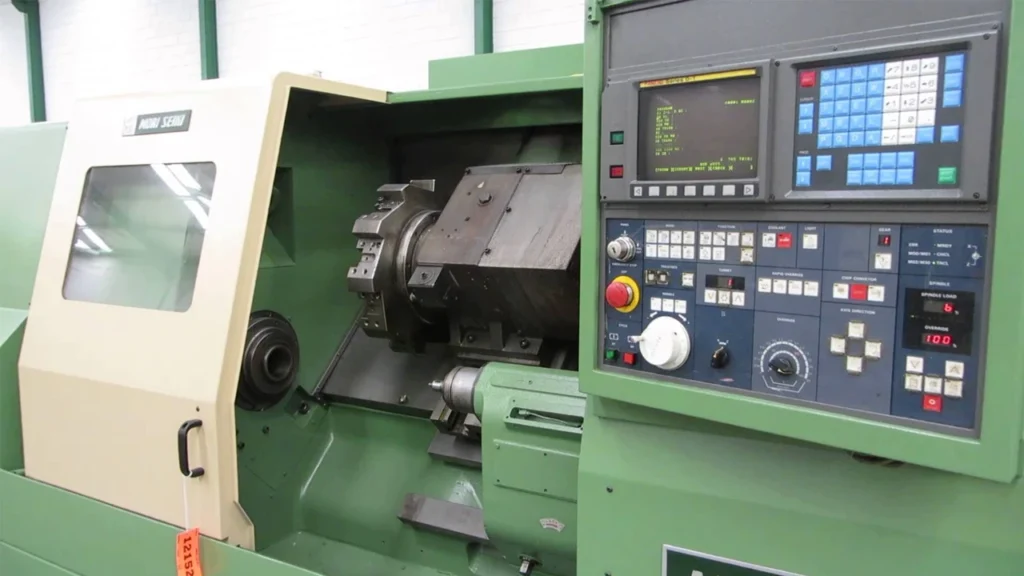
CNC Milling Machine
A CNC milling machine removes material from a workpiece using a rotating multi-point cutting tool. It is one of the most versatile CNC machines for creating flat surfaces, slots, pockets, and complex contours.
These machines come in vertical and horizontal configurations. Vertical milling machines are great for precision work and simpler setups, while horizontal types offer better chip removal and multi-side machining. Depending on configuration, machines may operate in 3, 4, or 5 axes, allowing them to execute complex part geometries from multiple orientations. Many systems include automatic tool changers and digital probing systems.
CNC milling machines are widely used in mold and die making, aerospace brackets, structural components, and a broad range of industrial metal parts requiring contour accuracy and flatness.
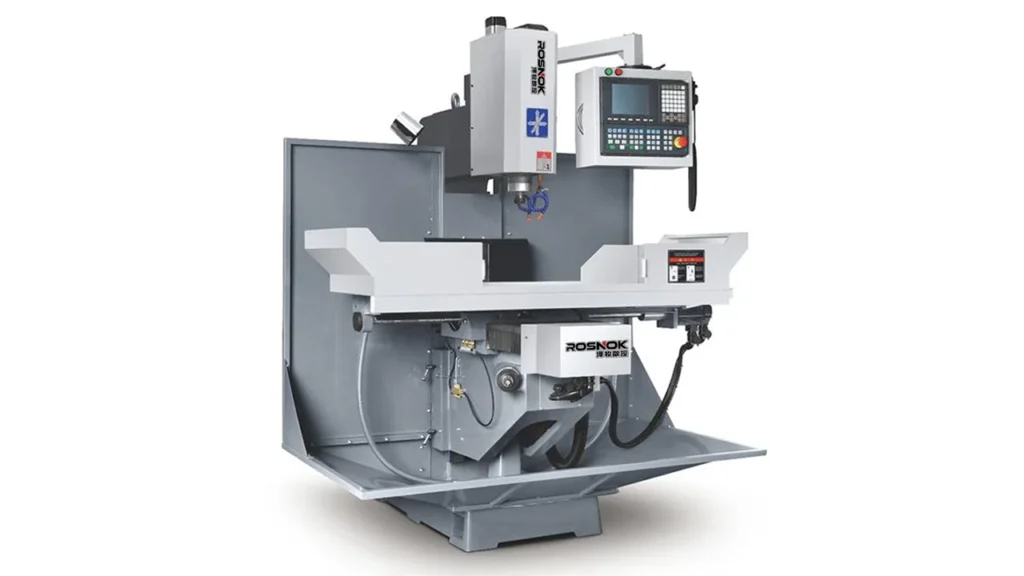
CNC Machining Center
A CNC machining center is an advanced milling-based system that integrates multiple operations like milling, drilling, boring, and tapping into one fully automated process. It is valued for its efficiency, tool-changing ability, and multi-operation handling.
It typically features a spindle, automatic tool changer (ATC), tool magazine, and a fixed or movable worktable. Vertical machining centers (VMC) are more compact and easier to set up, while horizontal machining centers (HMC) are ideal for complex part geometry and deep cavity access. Some models include 5-axis control for simultaneous motion, enabling precise, multi-surface machining.
Machining centers are indispensable in high-volume precision part production—particularly in aerospace, automotive engine components, industrial molds, and tooling plates.
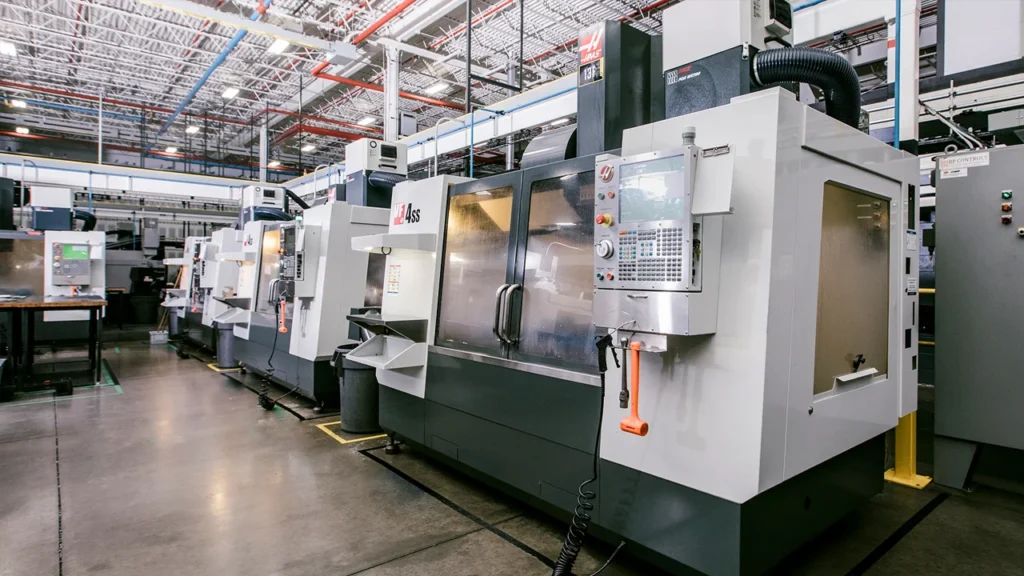
Swiss-Type CNC Lathe
A Swiss-type CNC lathe is a specialized lathe designed for high-precision production of small, slender, and long parts. Its signature feature is a sliding headstock that pushes the bar stock through a guide bushing while cutting tools operate near the support point.
These machines often support 5 to 11 axes and are capable of multi-task machining, including drilling, milling, threading, and part-off—all within a single cycle. Advanced versions come with backworking tools and sub-spindles, which eliminate secondary operations and reduce overall cycle time.
Swiss lathes are commonly used for components in medical devices, watchmaking, electronics, and aerospace—particularly where tight tolerances, high repeatability, and micro-dimensions are required.
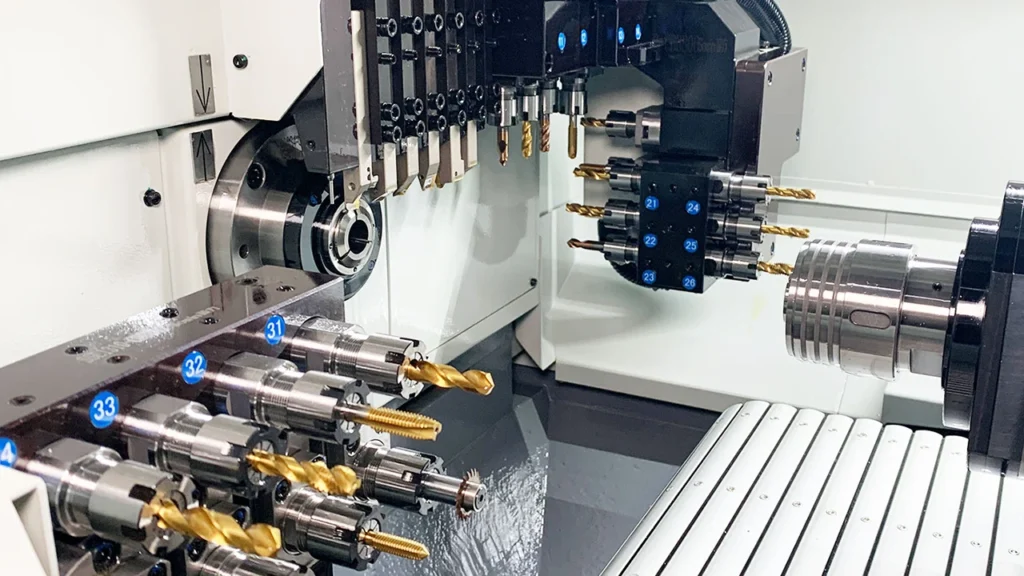
CNC Grinding Machine
A CNC grinding machine is a precision tool used to achieve tight tolerances and superior surface finishes on metal components. Unlike cutting tools that remove material in chips, grinders use an abrasive wheel that removes very small amounts of material with high speed and low pressure.
CNC grinders are commonly divided into surface grinders, cylindrical grinders, and centerless grinders. Surface grinders are ideal for flat surfaces; cylindrical grinders handle shafts, rods, and similar parts; and centerless grinders support continuous production without clamping, which makes them perfect for high-volume output.
These machines are often equipped with multi-axis control, automatic wheel dressing, in-process gauging, and even robotic part loading systems. CNC technology ensures consistent part geometry across long production runs.
Grinding is essential in automotive transmissions, bearing journals, aerospace turbines, and precision mold components—anywhere where sub-micron surface finish and form accuracy are required.
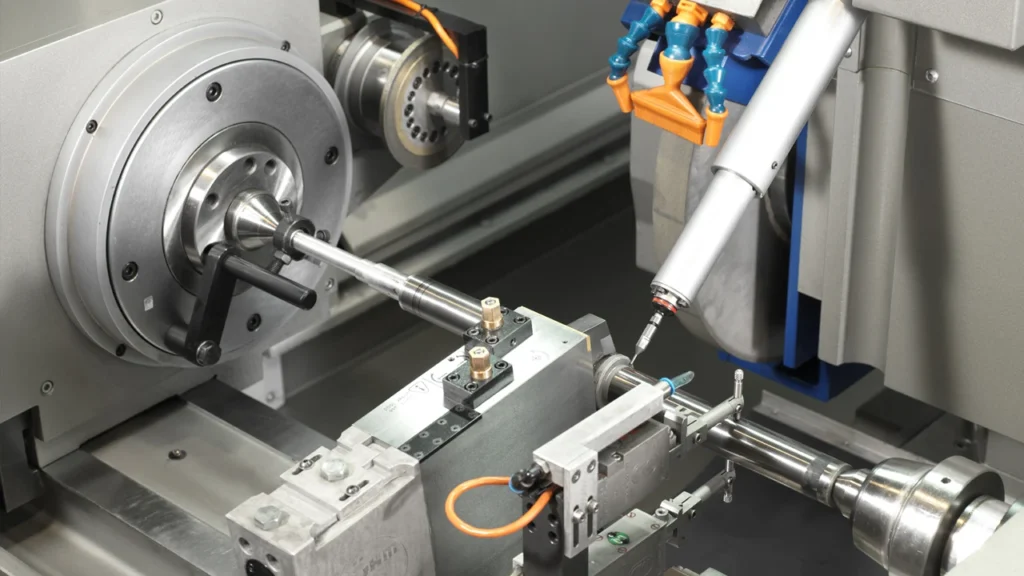
CNC EDM (Electrical Discharge Machine)
A CNC EDM machine removes metal from conductive materials using high-frequency electrical discharges. It is ideal for parts that require extremely fine detail, sharp corners, or internal geometries that traditional cutting tools cannot reach.
There are two primary types: wire EDM and sinker EDM. Wire EDM uses a thin wire as the electrode to cut through material like a bandsaw, while sinker EDM uses custom-shaped electrodes to erode cavities into the workpiece. EDM machines operate in dielectric fluid and are capable of sub-micron precision with very tight tolerances.
CNC EDMs are widely used for mold cavities, aerospace turbine parts, custom tooling, and hardened steel components that are difficult to machine mechanically.
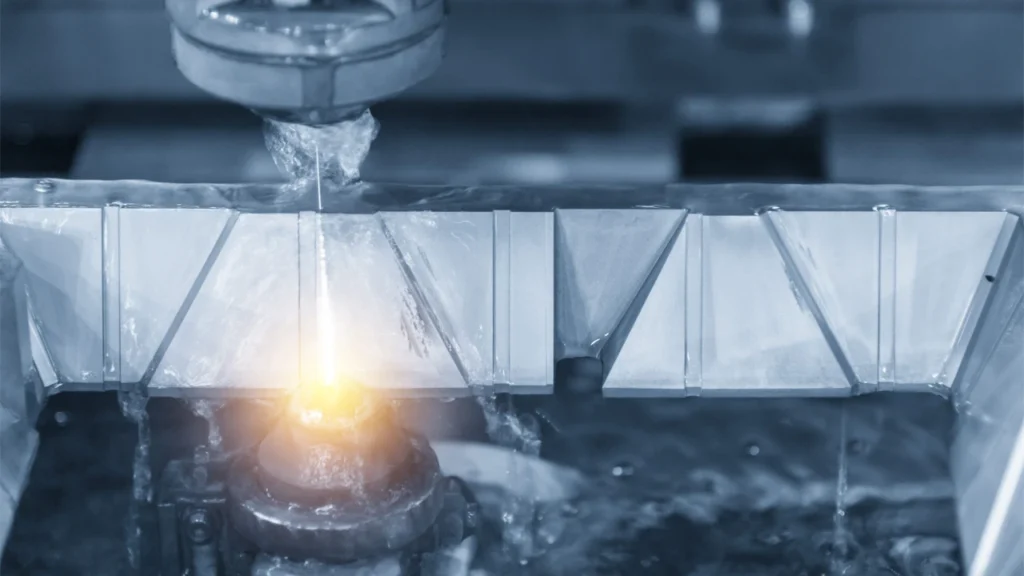
CNC Drilling Machine
A CNC drilling machine is built to automate and accurately execute drilling operations on a wide range of materials. It provides consistent hole diameters, depth control, and high-speed repetition for both single-hole and mass-drilling patterns.
These machines often feature multi-spindle heads, programmable feed rates, and automatic tool changers. Some advanced models also include tapping, reaming, countersinking, and peck drilling functions in a single setup. Drill tables can be configured for flat panels, tubular sections, or angled surfaces.
CNC drilling machines are widely used in electronics manufacturing, heat exchanger fabrication, automotive components, and structural steel work—anywhere large quantities of precisely located holes are needed.
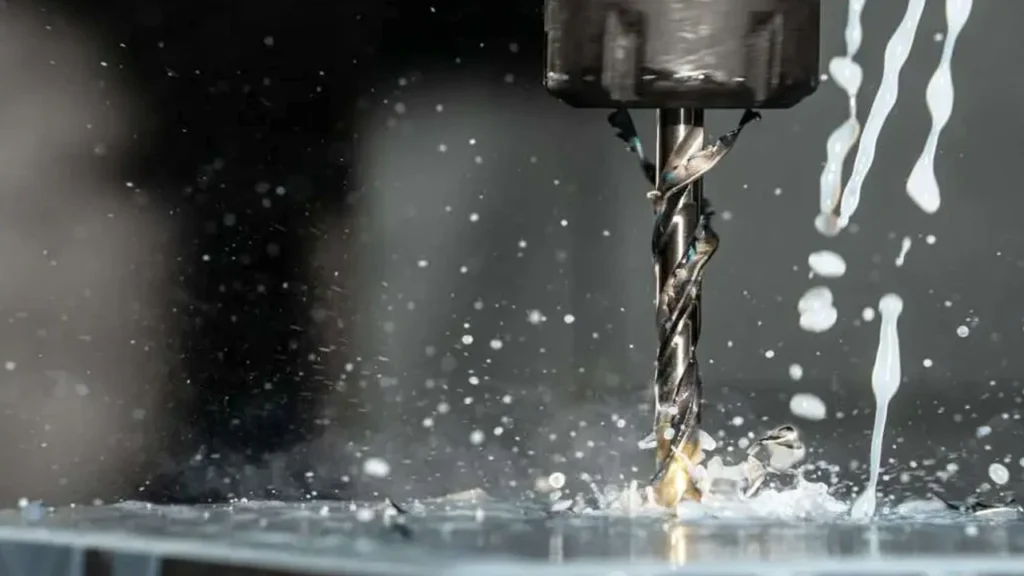
CNC Boring Machine
A CNC boring machine is specialized for enlarging existing holes with extreme accuracy, making it essential for applications that require precision alignment and tight dimensional control. It is typically used on large or heavy workpieces.
Equipped with horizontal or vertical spindles, boring machines operate with long travels and adjustable boring heads. They can handle large castings, welded frames, and deep cavities, with the ability to fine-tune diameters to microns. Some models are equipped with rotary tables and floor plates for large industrial parts.
These machines are indispensable in industries like power generation, marine, heavy machinery, and engine manufacturing, where precise internal bores are critical to component performance.
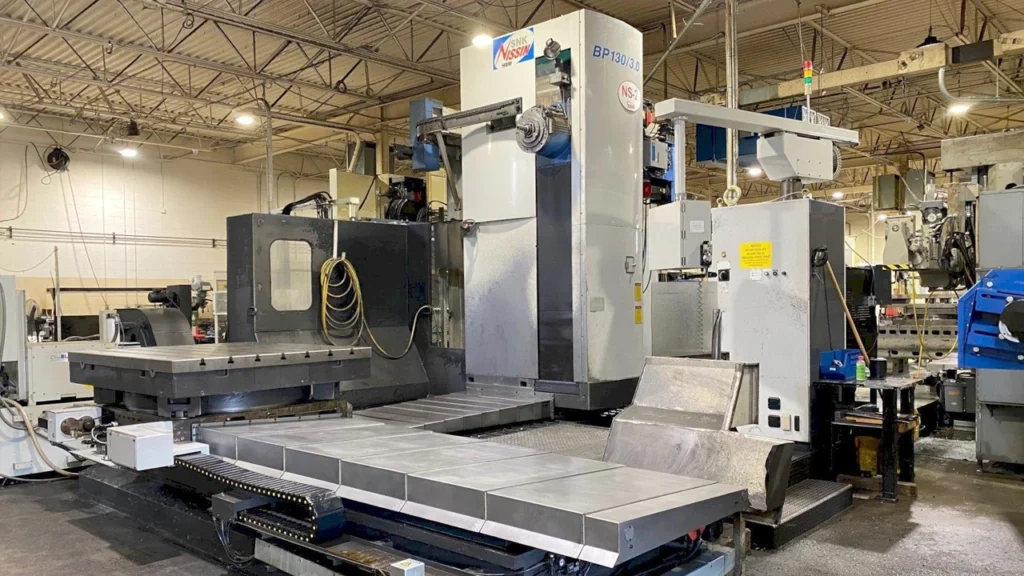
CNC Router
A CNC router is a lightweight yet highly versatile machine used to cut, engrave, or shape soft materials like wood, plastics, composites, foam, and occasionally aluminum. It operates similarly to a milling machine but with higher spindle speeds and optimized tool paths for softer materials.
Routers typically come with vacuum worktables, dust collection systems, and nesting software to maximize material efficiency. Most models are configured as gantry-style with 3 or 4 axes of movement. They are ideal for producing 2D and 2.5D profiles, text engraving, and light-duty 3D carving.
CNC routers are commonly used in furniture production, signage, packaging, interior panels, and aerospace composite trimming, where speed and surface finish are key.
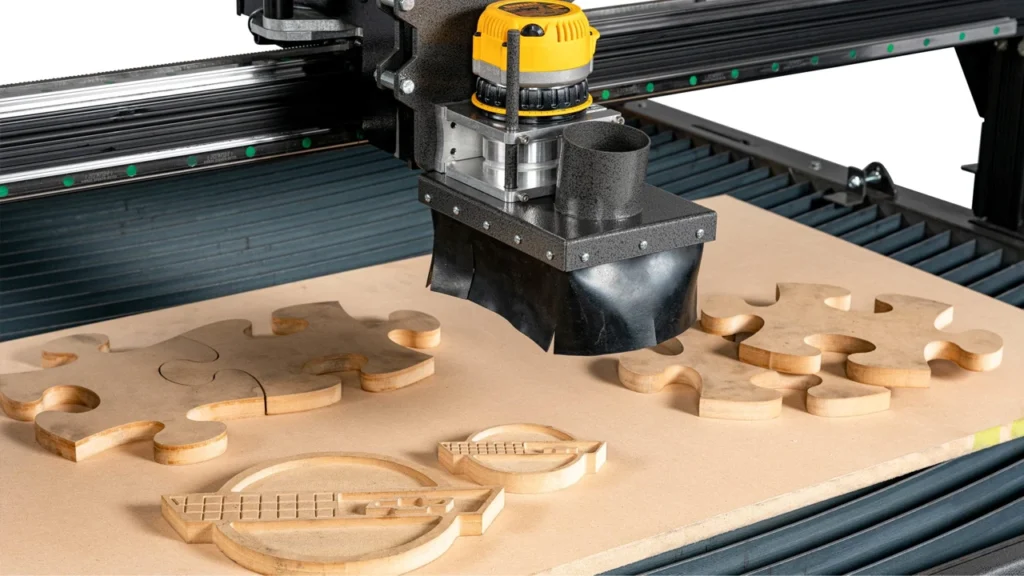
CNC Laser Cutter
A CNC laser cutter uses a focused beam of light to melt, burn, or vaporize material along a pre-programmed path. It is known for delivering extremely clean, high-speed cuts with tight tolerances and minimal material distortion.
Laser cutters operate on CO₂, fiber, or YAG laser sources depending on the material. They often include auto-focus heads, gas-assisted cutting, and nesting optimization software. With contact-free cutting, they eliminate tool wear and reduce the need for post-processing.
They are widely used in industries like precision sheet metal fabrication, electrical enclosure production, signage, decorative panel making, and thin-gauge aluminum or stainless steel components.
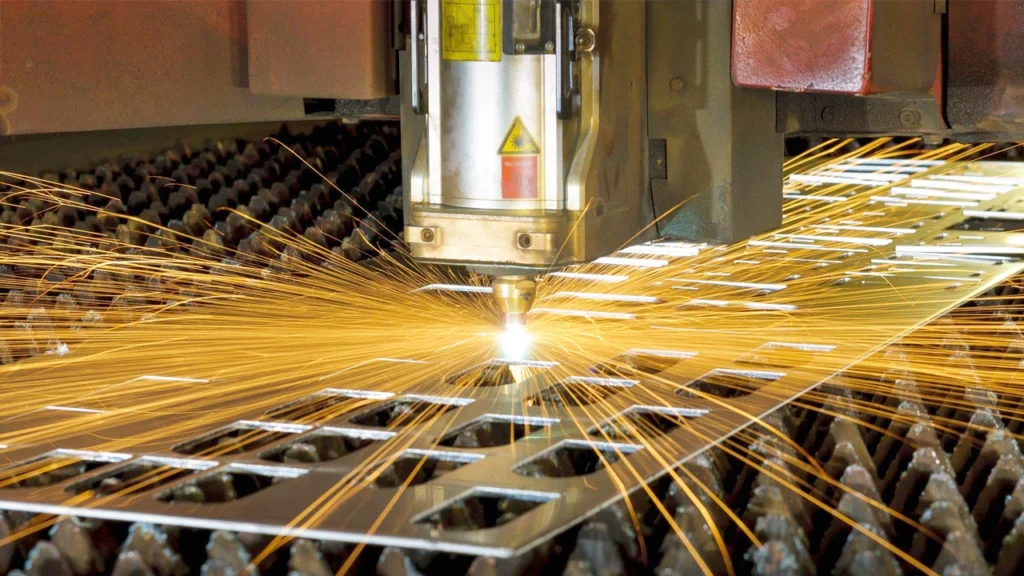
CNC Plasma Cutter
A CNC plasma cutter cuts electrically conductive materials using a high-velocity jet of ionized gas (plasma). It’s a cost-effective method for cutting medium- to thick-gauge metals with decent edge quality at high speeds.
Plasma cutters operate with compressed air, oxygen, or inert gases and are often integrated with torch height control and water tables for smoother finishes and heat management. They are easy to set up and maintain, and compatible with large-format sheet and plate materials.
Common in the construction and fabrication industries, plasma cutters are used to cut structural steel, machine frames, signage blanks, truck parts, and heavy-duty brackets.
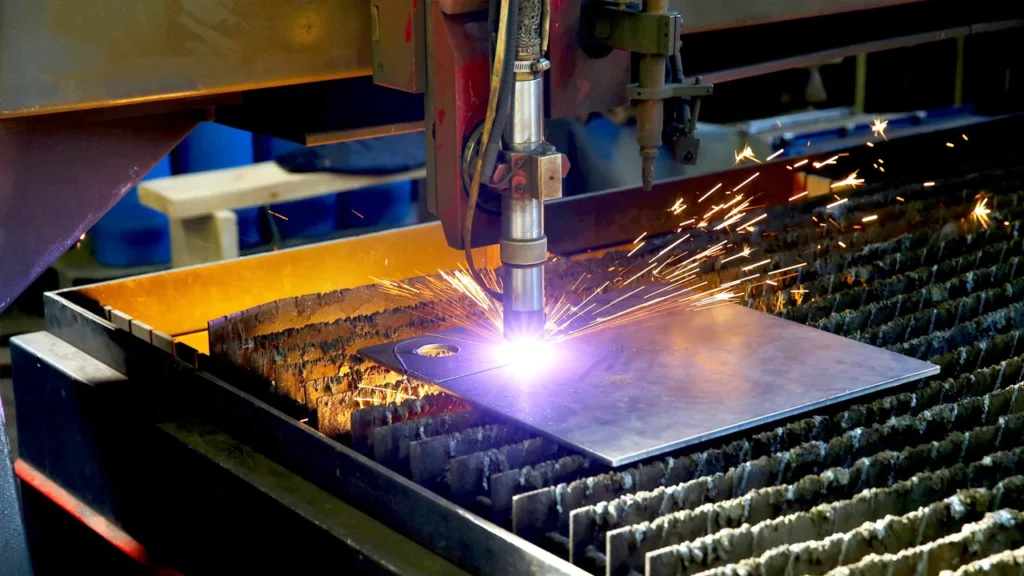
CNC Waterjet Cutter
A CNC waterjet cutter uses a high-pressure stream of water, often mixed with abrasives, to cut through a wide range of materials. Unlike laser or plasma, waterjet cutting is a cold process, meaning it doesn’t generate heat, distortion, or hardening.
These machines are capable of cutting metals, ceramics, glass, stone, rubber, and composite materials with exceptional edge quality. Precision control systems allow tight tolerances, and multi-axis heads enable beveled or contoured cuts. They are ideal for thick or layered materials and complex nesting tasks.
Waterjet technology is commonly applied in aerospace, architectural stone, defense, and industrial component cutting—especially where thermal damage must be avoided.
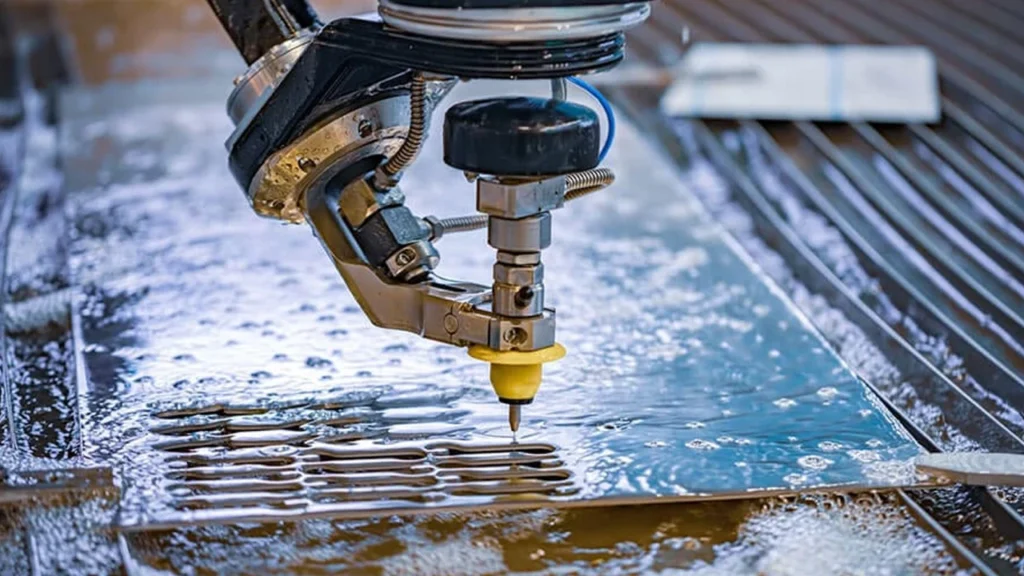
CNC Machining Processes
CNC machines are capable of performing a wide range of precision operations that remove material from a workpiece. These processes—collectively known as CNC cutting operations—are the foundation of modern manufacturing, enabling high-speed production of complex, high-accuracy components.
Turning
Turning is a foundational CNC process where the workpiece rotates, and a single-point cutting tool removes material along the outer or inner surface. It is performed on CNC lathes and is ideal for creating cylindrical or conical shapes.
Key variations include:
- Facing: Flattening the end of the part
- Parting: Cutting off a section from the stock
- Threading and Grooving
Turning is widely used for parts like shafts, bushings, pipe fittings, and bearing seats in industries including automotive, oil & gas, and general machining.
Milling
Milling uses a rotating cutting tool to remove material from a stationary workpiece. Performed on CNC milling machines or machining centers, this method allows for precise shaping of flat surfaces, slots, pockets, and contours.
Milling can be done in:
- 3-axis setups for flat and stepped surfaces
- 4- and 5-axis configurations for complex 3D geometry
It is essential for mold bases, structural parts, housings, and aerospace brackets requiring multi-surface detail and tight tolerances.
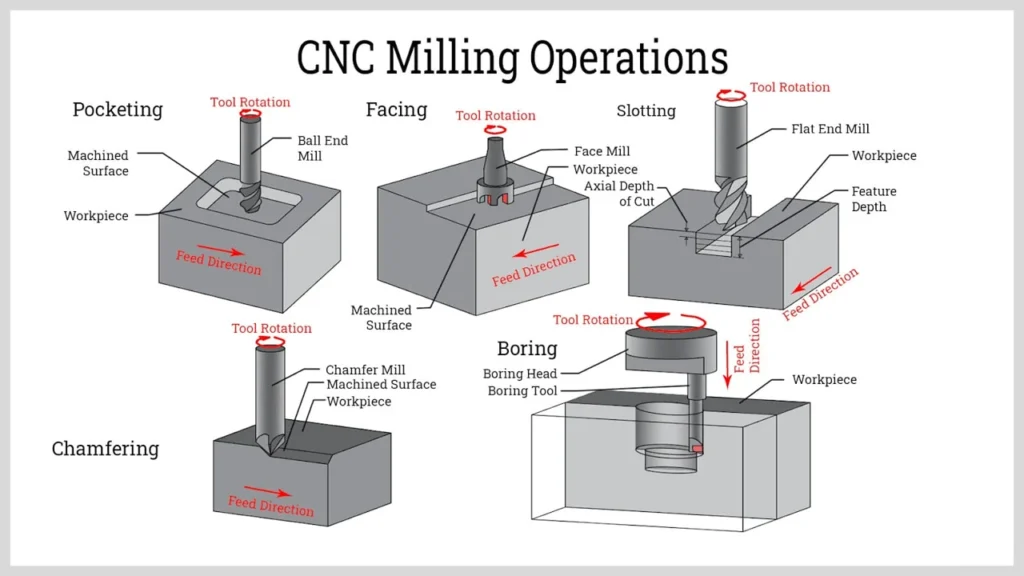
Drilling
Drilling involves using a rotating drill bit to create round holes in a part. CNC drilling enables consistent hole positioning, depth control, and integration with follow-up processes like tapping or reaming.
Variants include:
- Spot drilling to locate hole centers
- Peck drilling for deep holes
- Countersinking and counterboring
This process is fundamental in electronics, automotive, energy, and fabrication industries—anywhere precise hole patterns are needed.
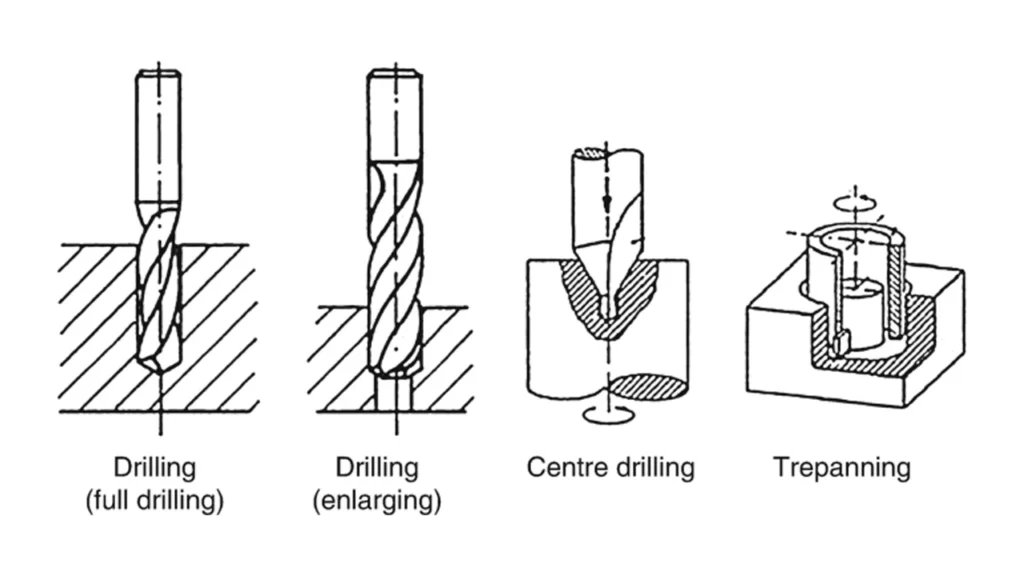
Tapping
Tapping is used to create internal screw threads inside a pre-drilled hole. CNC tapping cycles synchronize the spindle and feed rate, allowing for clean and repeatable thread cutting, especially in high-volume runs.
Commonly used in:
- Mechanical assemblies
- Electronic enclosures
- Automotive parts with bolted connections
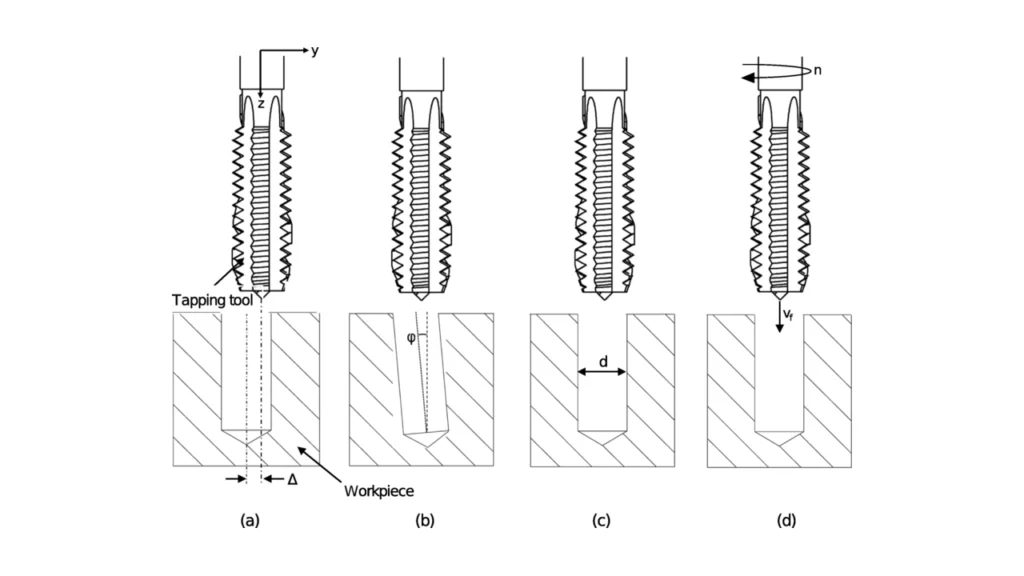
Boring
Boring enlarges and refines pre-existing holes, improving concentricity and dimensional accuracy. CNC boring machines and machining centers are used when holes need precise internal diameters and fine surface finishes.
Applications include:
- Engine cylinder bores
- Turbine housings
- Gearbox cavities
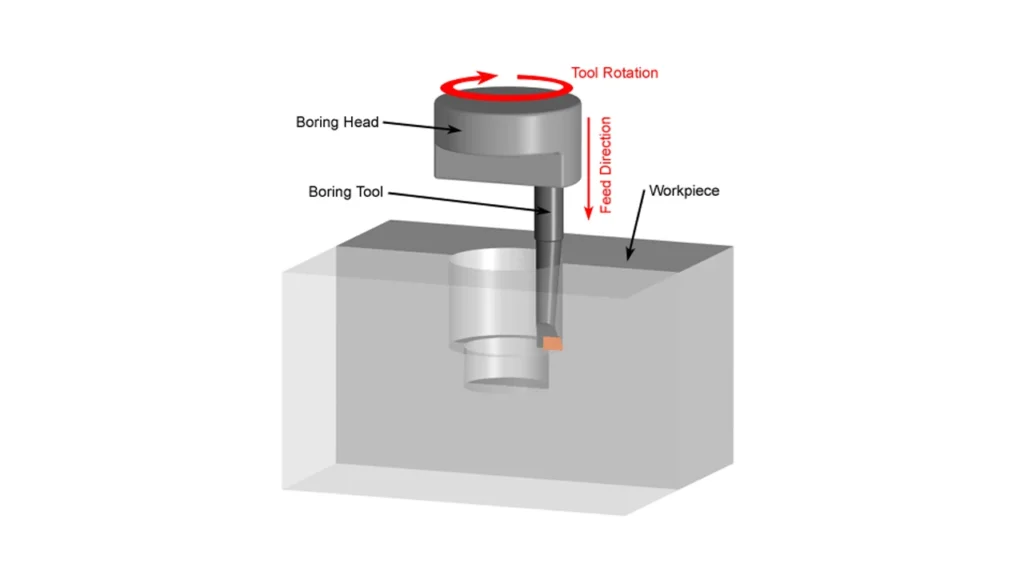
Reaming
Reaming is a finishing process that brings a drilled hole to an exact size with a smooth surface. It is often used when tight hole tolerances or press-fit accuracy is required.
Industries rely on reaming for:
- Valve seats
- Fuel rails
- Hydraulic system components
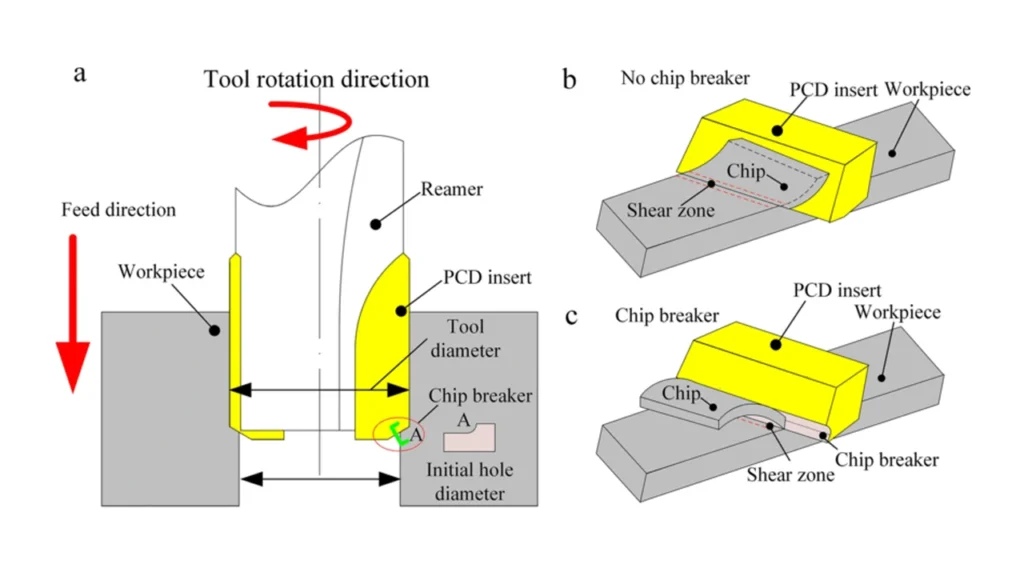
Thread Milling
Thread milling uses a rotating tool that follows a helical path to cut internal or external threads. Unlike tapping, it is suitable for large-diameter holes, exotic materials, and variable thread profiles.
Advantages:
- One tool for multiple thread sizes
- Reduced risk of tool breakage
- Better chip evacuation
Laser Cutting
Laser cutting is a non-contact, thermal CNC process that uses a high-powered, focused laser beam to melt, burn, or vaporize material along a predefined path. Controlled by CNC, the laser achieves exceptionally fine detail, minimal burring, and clean edges without touching the part.
Ideal for cutting thin to medium metal sheets, plastics, and composites, laser cutting is commonly used in industries like electronics, sheet metal fabrication, signage, and aerospace.
Engraving and Marking
Engraving involves using a fine tool, laser, or diamond cutter to etch text, logos, or serial numbers into a component surface. It is often part of product identification or traceability systems in regulated industries.
Used for:
- Branding logos
- Part codes
- Safety warnings
Grinding (Optional in Hybrid Machines)
Some high-end CNC machines support grinding operations, enabling in-process finishing of hardened materials or mold surfaces without secondary setups. Though not common on all machines, this function improves dimensional control and reduces total lead time.
Applications include:
- Mold cavity polishing
- Bearing surfaces
- Post-hardening precision finishing
Note: Many advanced multi-tasking machines and mill-turn centers combine turning, milling, drilling, and grinding in one setup. These hybrid systems allow complex parts to be manufactured in a single clamping, improving accuracy and cycle time without switching machines.
Applications of CNC Machines in Industries
CNC machines are the backbone of modern manufacturing, enabling industries across the globe to achieve mass production, precision engineering, and consistent quality at scale. From automotive components to medical implants, CNC machining is indispensable where complex geometries and tight tolerances are non-negotiable.
Let’s explore how various industries rely on CNC machines to maintain performance, efficiency, and global competitiveness.
Automotive Industry
The automotive sector depends heavily on CNC machines for producing both high-volume components and critical engine parts. CNC lathes, machining centers, and grinders are used to manufacture:
- Engine blocks and cylinder heads
- Transmission shafts and gear housings
- Brake calipers and rotors
- Suspension components and hubs
With CNC machining, automotive manufacturers achieve interchangeability, tight tolerances, and automation-ready workflows, enabling them to produce thousands of identical parts with minimal variation. The rise of electric vehicles (EVs) has also increased the demand for lightweight aluminum and composite machining, where CNC precision is crucial.
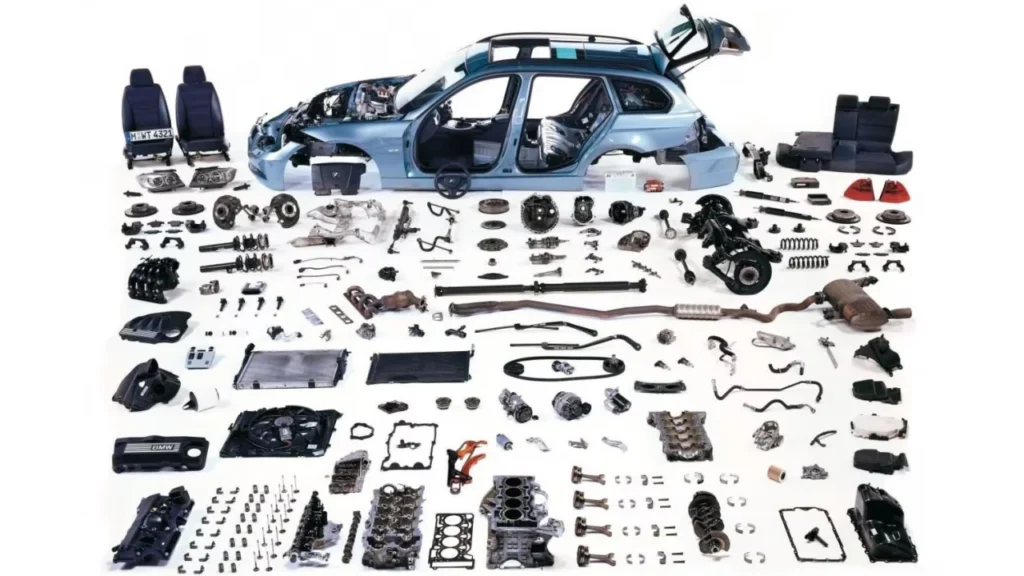
Aerospace Industry
In aerospace, precision is a matter of safety. CNC machines are used to create complex, high-strength, lightweight components that must meet exacting standards under extreme operating conditions.
Typical CNC-machined aerospace parts include:
- Turbine blades and housings
- Structural brackets and frames
- Engine mounts and landing gear parts
- Satellite components and control panels
Multi-axis machining centers and Swiss-type lathes are essential for producing tight-tolerance, multi-surface parts from materials like titanium, Inconel, and aerospace-grade aluminum. CNC ensures repeatability, traceability, and compliance with aerospace certifications.
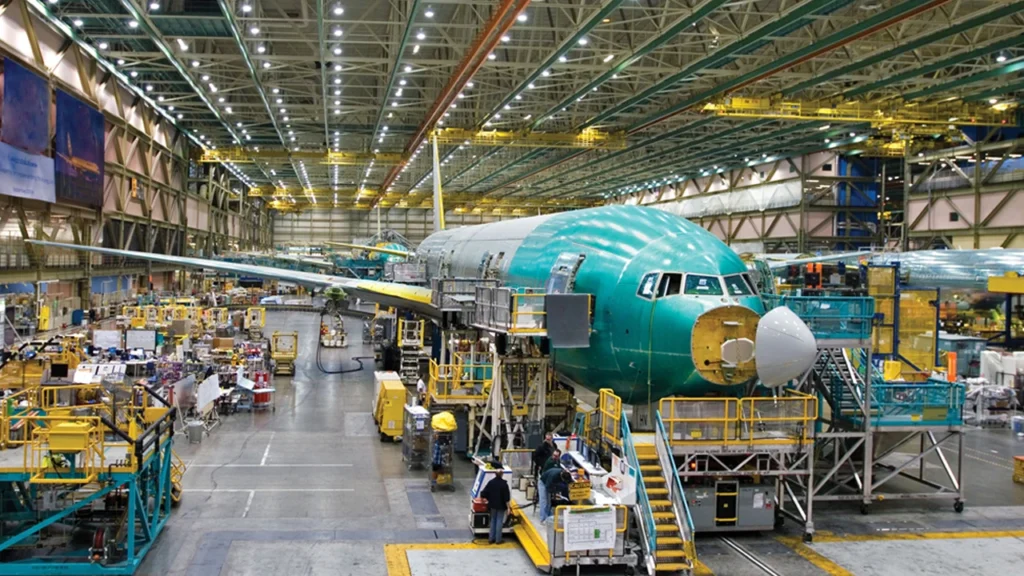
Medical Device Industry
The medical field relies on CNC machining for producing implants, surgical instruments, and diagnostic equipment. Swiss-type lathes and micromachining centers are used to make tiny, intricate parts with exceptional precision.
Common applications include:
- Bone screws, plates, and joint replacements
- Dental components
- Stents and catheters
- Surgical cutting tools and clamps
These parts often require biocompatible materials such as titanium or stainless steel, along with ultra-fine surface finishes. CNC machining allows manufacturers to meet strict quality and sterilization standards required by medical regulators.
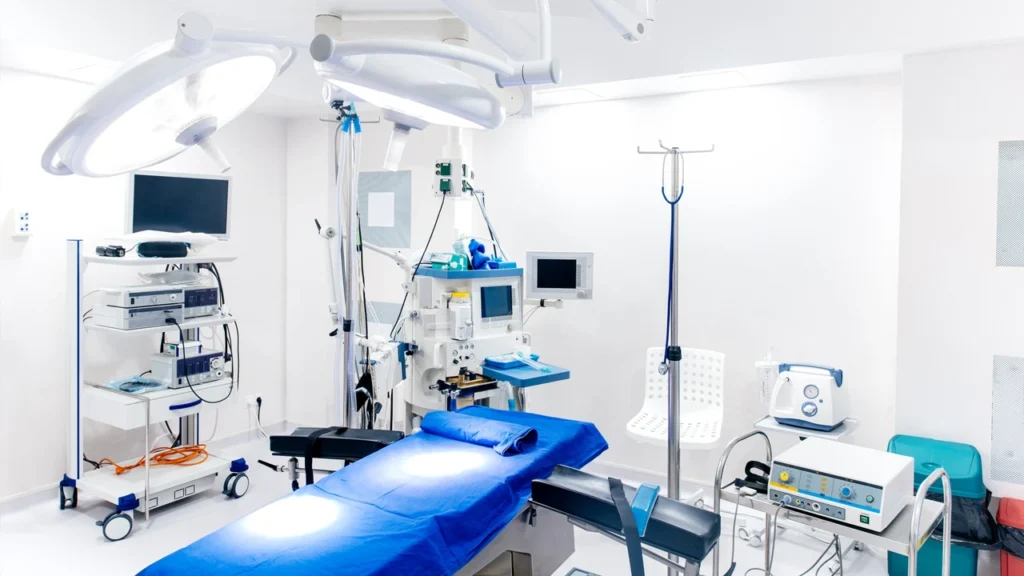
Electronics and Precision Components
CNC machines play a major role in producing enclosures, connectors, and heat sinks for electronic devices. High-speed milling machines and routers are used to machine aluminum, plastics, and composites for:
- Smartphone and tablet housings
- Printed circuit board (PCB) holders
- Cooling systems for CPUs and GPUs
- Precision optical device frames
With miniaturization becoming the norm, micron-level precision and fine engraving capabilities make CNC machining the go-to method for electronics manufacturers worldwide.
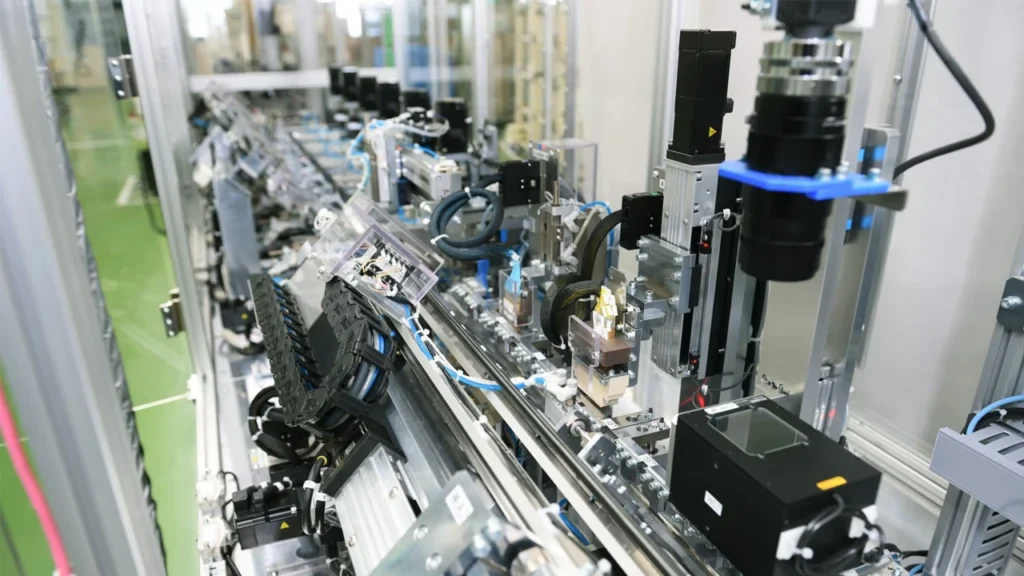
Energy and Power Generation
The energy sector, including oil & gas, wind, and nuclear industries, uses CNC machines to produce large, heavy-duty parts that demand structural integrity and reliability under pressure.
Key applications include:
- Valve bodies and flanges
- Heat exchanger components
- Pump casings and impellers
- Turbine rotors and generator housings
Vertical lathes, boring mills, and pipe-threading lathes are common in this sector, handling components with diameters exceeding 1 meter and weights of several tons—all while maintaining dimensional accuracy and concentricity.
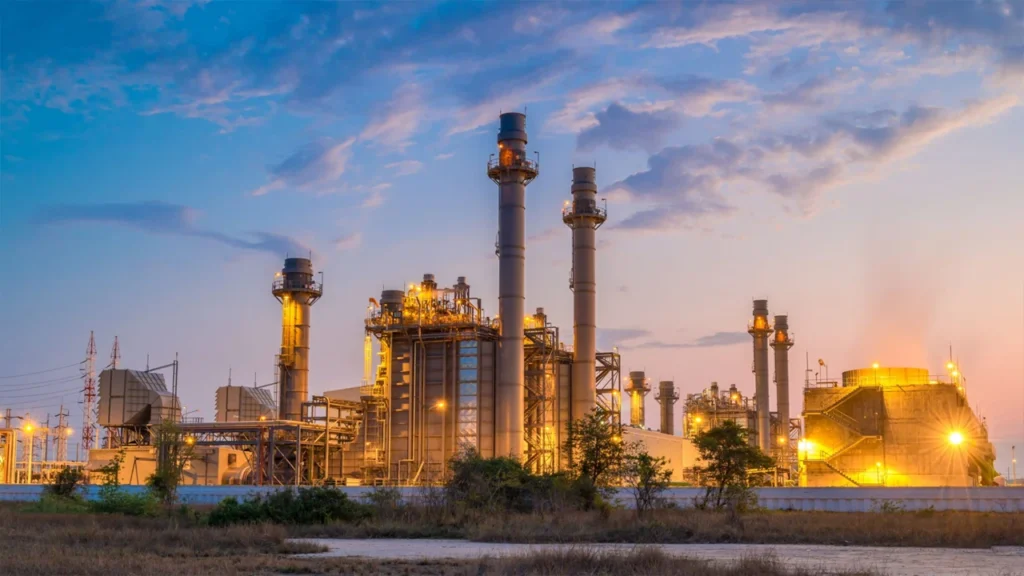
Mold and Die Industry
Tooling is where CNC machining truly shines. CNC milling machines and machining centers are used to craft precision molds and dies for plastic injection, stamping, and die-casting.
Applications include:
- Plastic injection molds for consumer products
- Automotive panel dies
- Progressive stamping tools
- Pressure die-casting molds for metal housings
The mold and die industry benefits from 3-axis to 5-axis machining, surface finishing capabilities, and electrode production for EDM, all of which are powered by CNC systems.
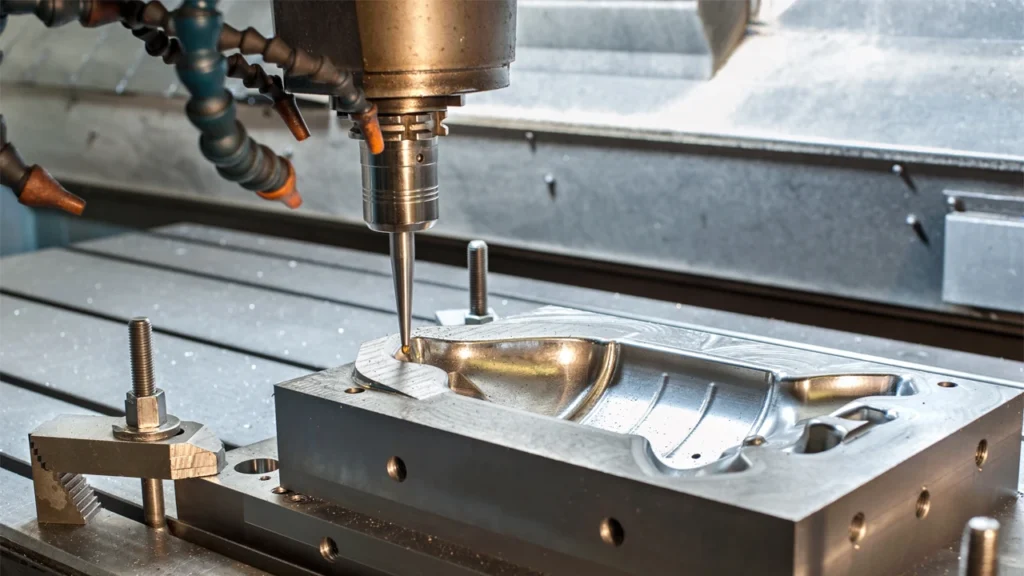
Heavy Machinery and Industrial Equipment
In heavy industry, CNC machines are used to manufacture robust parts for construction equipment, mining machines, agricultural systems, and more. These components often have large dimensions, tight press fits, and interchangeable interfaces.
Machined parts include:
- Gearboxes and reduction systems
- Hydraulic cylinders
- Bearing housings
- Chassis brackets
Gantry-type machining centers, CNC boring machines, and large-scale vertical lathes allow industrial OEMs to ensure machinability at scale, reduce lead times, and meet rigorous functional demands.
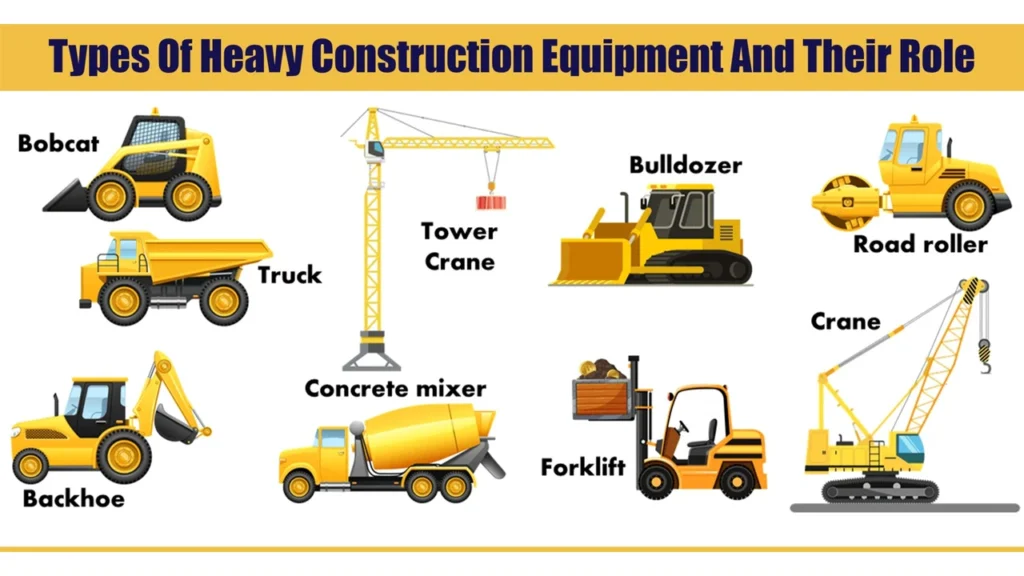
Benefits of Using CNC Machines
CNC machines have revolutionized modern manufacturing by enabling fast, precise, and repeatable production of complex parts. From mass production to high-mix, low-volume jobs, CNC technology provides manufacturers with a clear competitive edge. Below are the key benefits of using CNC machines in industrial operations:
High Precision and Consistency
CNC machines follow exact digital instructions, allowing for micron-level accuracy in every cycle. Once a program is created, the machine will replicate the same part over and over again—without deviation.
This ensures:
- Consistent part dimensions across large batches
- Tighter tolerances than manual or semi-automatic machines
- Reduced human error and variation
Such precision is essential for industries like aerospace, medical, and automotive, where even small dimensional inconsistencies can lead to critical failure.
Increased Efficiency and Productivity
With CNC machines, manufacturers can run parts 24/7 with minimal supervision. The automation of tool changes, multi-axis movement, and simultaneous operations drastically reduces idle time.
Key gains include:
- Faster cycle times
- Unmanned night shifts (lights-out machining)
- Integrated probing and in-process quality checks
This translates directly to higher output per machine, improved delivery times, and lower cost-per-part.
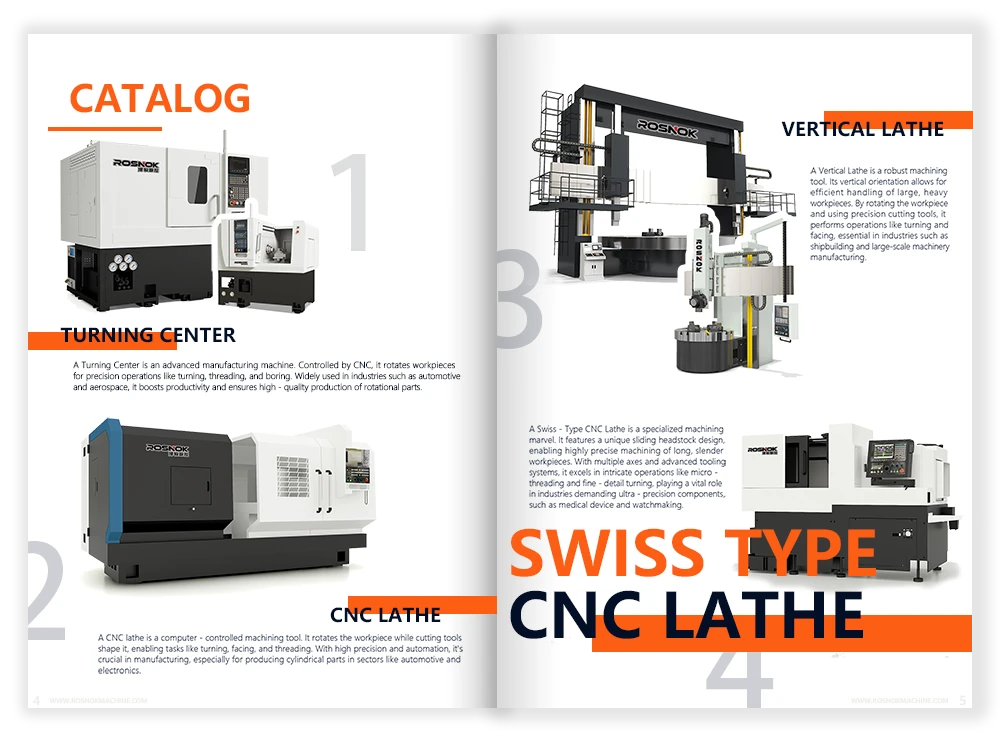
Versatility for Complex and Custom Work
CNC machines can produce a wide range of parts—from simple flanges to complex 5-axis turbine blades—using the same platform. They can switch between different operations like milling, drilling, turning, or tapping with a simple program change.
Benefits include:
- Support for both prototyping and mass production
- Quick retooling for design changes
- Reduced need for multiple machines
This flexibility is especially valuable for contract manufacturers and workshops handling diverse customer demands.
Reduced Labor Costs and Manual Intervention
Traditional machining requires skilled operators at every stage. CNC automation reduces this dependency by handling setup, execution, and even inspection with minimal human input.
Advantages:
- Fewer operators per machine
- Simplified training for staff
- Lower risk of workplace accidents
CNC systems shift the workforce from machine operation to programming, maintenance, and oversight, increasing efficiency at every level.
Cost-Effectiveness in Long-Term Production
Though CNC machines come with a higher upfront investment, their long-term operating costs are significantly lower. They produce less waste, require fewer reworks, and reduce tooling damage through optimized cutting paths.
ROI drivers:
- Improved material utilization
- Lower scrap rates
- High machine uptime
For businesses aiming for lean manufacturing, CNC is the key to sustainable profitability.
Ability to Perform Multi-Axis Machining
Advanced CNC machines support 4-, 5-, and even 9-axis machining, enabling the creation of parts with complex surfaces, compound angles, and single-pass contours.
This capability:
- Eliminates multiple setups
- Ensures perfect alignment across features
- Allows for parts that are otherwise impossible to machine
Multi-axis machining is widely used in aerospace, robotics, and advanced medical engineering.
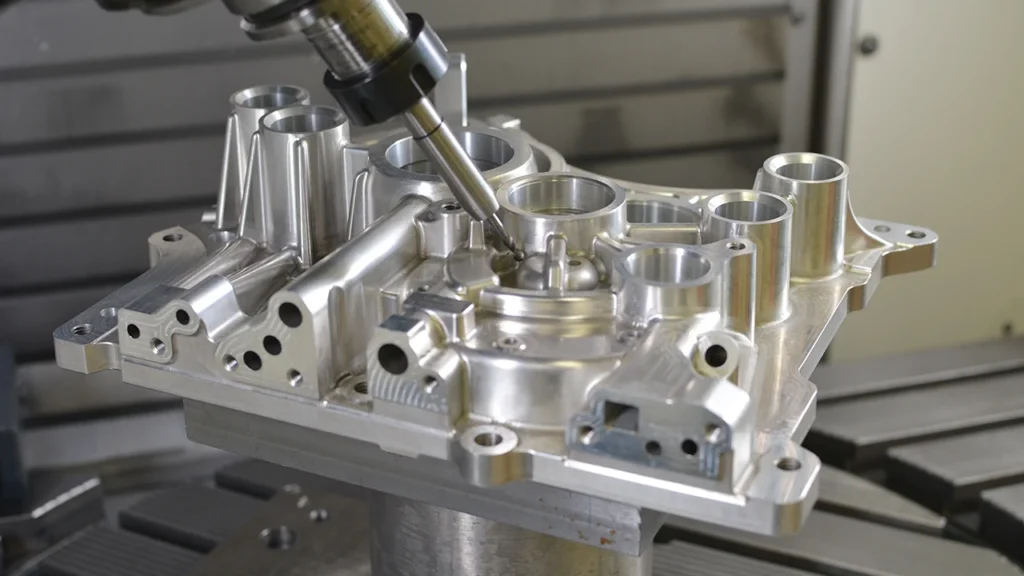
Scalability for Growing Production Needs
CNC machines can scale from one-off prototyping to full production runs with minimal changes in workflow. Adding new programs, fixtures, or automation modules is easy, making it ideal for manufacturers looking to expand.
Benefits:
- Easy transition from R&D to production
- Integration with MES and ERP systems
- Support for high-mix, low-volume flexibility
This scalability helps companies respond quickly to market changes or product development cycles.
Environmentally Friendly and Material Efficient
CNC machines contribute to greener manufacturing by:
- Reducing material waste through precise cutting
- Lowering energy usage with high-efficiency motors
- Enabling dry machining or minimal-lubrication techniques
They also produce less noise and dust compared to manual methods, supporting a cleaner and safer workspace.
Challenges and Limitations of CNC Machines
While CNC machines offer incredible advantages in precision, efficiency, and automation, they are not without challenges. From high capital costs to skill requirements and system limitations, understanding these potential drawbacks is crucial for making informed investment and production decisions.
High Initial Investment
CNC machines typically come with a significant upfront cost, especially for multi-axis machining centers or large-format models. In addition to the machine itself, buyers often need to invest in:
- Tooling and fixtures
- CAM software and licenses
- Electrical infrastructure upgrades
- Operator and programmer training
For small workshops or startups, this cost barrier can delay adoption. However, when viewed over the long term, CNC machines often offer a strong return on investment through productivity gains.
Skill and Training Requirements
Although CNC machines reduce manual labor, they require highly skilled programmers, setup technicians, and maintenance personnel to operate efficiently. Inexperience can lead to:
- Programming errors
- Tool crashes and machine damage
- Poor-quality parts or excessive downtime
Ongoing training is essential, especially as machine capabilities and software tools evolve. Finding and retaining qualified personnel remains a challenge in many regions.
Maintenance and Downtime Risks
Like any high-performance system, CNC machines require regular preventive maintenance to avoid unplanned downtime. Ignoring this can result in:
- Spindle failures
- Servo or encoder issues
- Coolant system clogs
- Tool misalignment
Even routine tasks—like lubrication, alignment checks, and software updates—require dedicated schedules and trained staff. Unplanned machine stoppages can delay deliveries and reduce profitability.
Programming Complexity for Advanced Operations
As CNC machines grow more capable, their programming also becomes more complex—particularly in multi-axis or multi-spindle systems. Creating efficient, collision-free toolpaths for complex geometries requires:
- Deep understanding of CAM software
- Simulation and verification tools
- Manual intervention for edge cases
This complexity can slow down prototyping cycles and create barriers for companies without strong in-house programming expertise.
High Energy Consumption
CNC machines, especially large machining centers, grinders, or laser cutters, can be energy-intensive. Factors contributing to power usage include:
- Continuous spindle rotation
- Servo motor movement across multiple axes
- Coolant pumps and chip conveyors
- Heating systems for temperature control
For companies in regions with high electricity costs, this can have a direct impact on operational expenses.
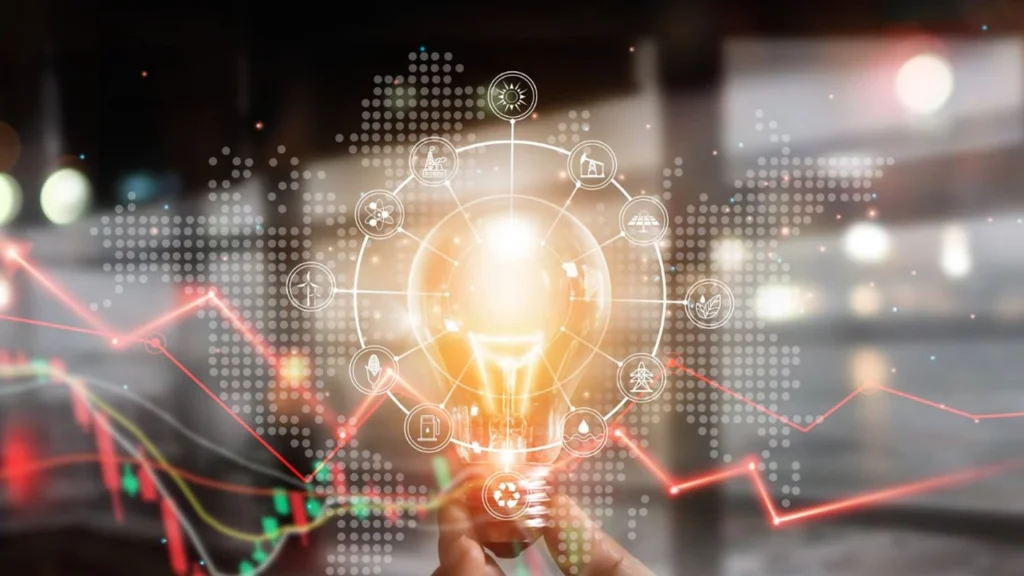
Limited Flexibility for Low-Volume Production
For small batch or custom one-off parts, the setup time and programming overhead of CNC can outweigh its benefits. It may not be the best choice when:
- Parts change frequently
- Designs are still being prototyped
- Volume doesn’t justify automation
In such cases, manual machining or hybrid approaches may be more cost-effective until the design stabilizes.
Space and Infrastructure Requirements
High-end CNC equipment requires not only significant floor space, but also specialized infrastructure such as:
- Stable foundations
- High-voltage electrical connections
- Clean air supply for pneumatic systems
- Temperature-controlled environments (especially for precision machines)
This can make CNC integration difficult in facilities with space constraints or aging infrastructure.
How to Choose the Right CNC Machine
Selecting the right CNC machine is a strategic decision that affects your production capabilities, costs, and long-term growth. Whether you’re upgrading an existing shop or building a new production line, the right machine must match your technical needs, output goals, and operational constraints. Here are the key factors to consider:
Define Required Machining Processes First
Before comparing models and features, start by identifying the specific machining processes your parts require. Every CNC machine is optimized for certain operations—selecting based on machining needs ensures better performance, accuracy, and ROI.
Ask yourself:
- Do you primarily need turning (for round parts)?
- Is milling or surface profiling the main operation?
- Will you need drilling, tapping, or boring?
- Are multi-process parts better suited for a machining center or mill-turn system?
By first understanding the machining processes, you can eliminate machines that don’t support your core tasks and focus only on platforms designed for your production reality.
This step also clarifies tooling requirements, spindle type, and axis configuration—saving time and reducing costly mismatches later.
Consider Machine Size and Workpiece Dimensions
Machine capacity is crucial. A machine that’s too small limits your projects; too large wastes floor space and energy.
Evaluate:
- Maximum X, Y, Z travel distances
- Table size and load capacity
- Spindle clearance and reach
- Door or gantry access for loading/unloading
Be sure to factor in future growth—not just current part sizes.
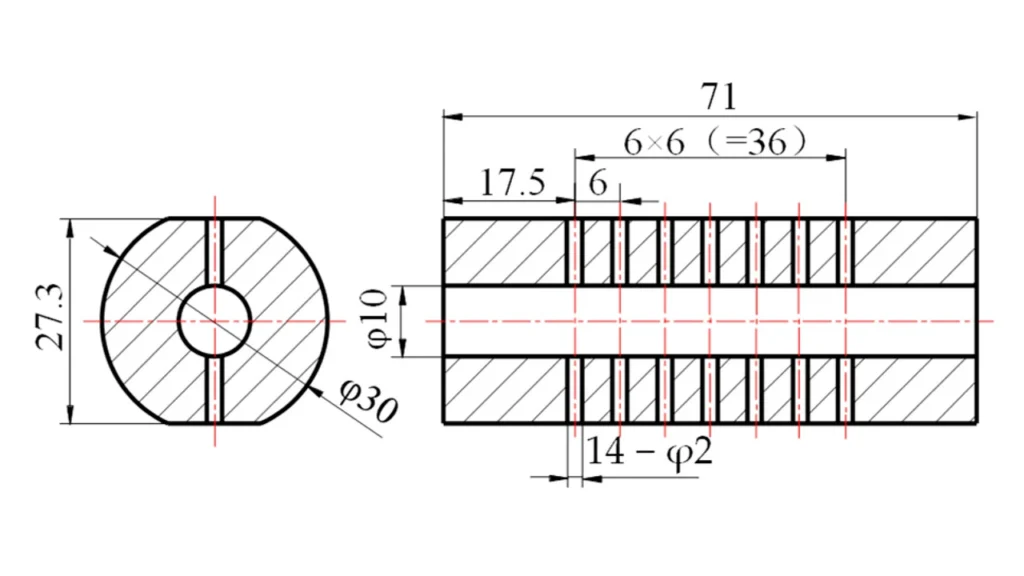
Evaluate CNC Control System and Software
The CNC control system defines how the machine interprets code and performs tasks. Popular systems include FANUC, Siemens, Mitsubishi, and Heidenhain.
Key features to consider:
- User interface and ease of operation
- Supported languages and G-code compatibility
- Simulation, probing, and real-time feedback tools
- Connectivity to CAD/CAM software and IoT systems
A good control system improves programming efficiency, operator learning curve, and machine uptime.
Assess Spindle Speed and Power
Spindle performance affects cutting speed, finish quality, and material compatibility. Depending on your material and tool size, you may require:
- High-speed spindles for aluminum and plastics
- High-torque spindles for steel and titanium
- Multi-speed gearboxes for heavy-duty cuts
Also consider spindle taper type, bearing cooling, and balance control, especially if your operations involve long cycle times or micro-finishing.
Examine Tool Capacity and Automatic Tool Changer (ATC)
If you plan to run complex parts or long, unattended cycles, the machine’s tool magazine capacity is key. Typical ranges:
- Entry-level: 12–24 tools
- Mid-range: 30–60 tools
- High-end production: 80+ tools with random-access capability
Look for fast tool change times, reliable ATC mechanisms, and compatibility with your toolholding system (BT, HSK, CAT, etc.).
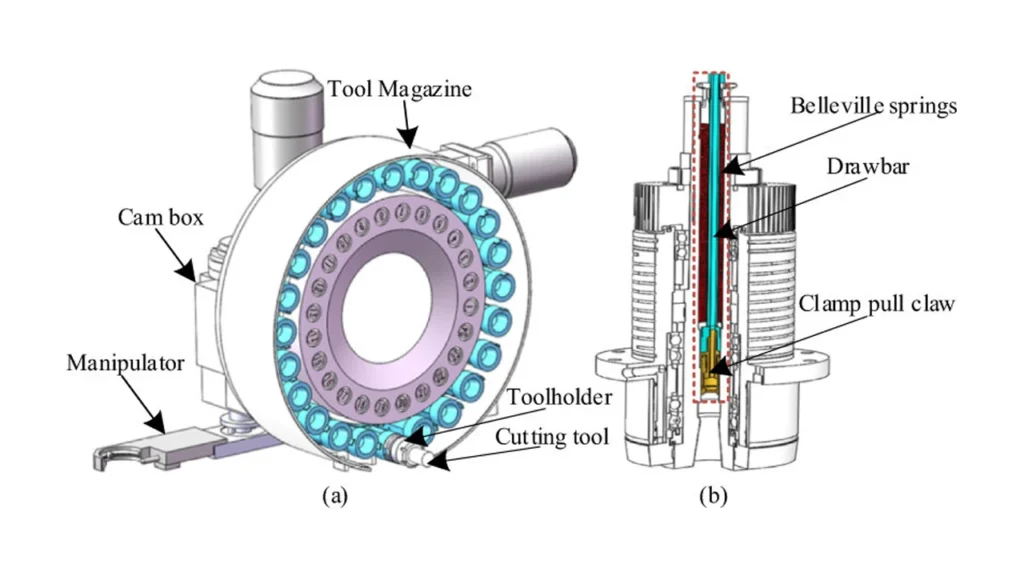
Check for After-Sales Support and Warranty
Even the best machine will need support. Choose a manufacturer or dealer who provides:
- Local service and spare parts
- Prompt on-site assistance
- Remote diagnostics and firmware updates
- Operator and programmer training
Also review warranty coverage, especially on key components like spindles, drives, and controllers.
Analyze Automation and Integration Capabilities
Modern factories often integrate CNC machines with robots, conveyors, pallet changers, and monitoring systems. If you plan to scale or automate:
- Look for Ethernet or OPC-UA connectivity
- Ensure compatibility with MES/ERP systems
- Check for space and I/O ports for automation units
Machines that are “Industry 4.0-ready” will give you an edge in smart manufacturing and future expansion.
Maintenance and Best Practices for CNC Machines
Proper maintenance is the key to keeping CNC machines running efficiently, safely, and accurately over the long term. Even the most advanced machines will underperform or fail prematurely without routine care. Implementing a structured maintenance plan helps reduce unplanned downtime, improve part quality, and extend machine lifespan.
Daily Maintenance Checklist
Basic daily maintenance tasks are critical to ensure smooth operation and catch issues early. These tasks include:
- Cleaning chips and debris from machine surfaces and chip conveyors
- Inspecting air supply pressure and filters
- Checking coolant levels and ensuring clean filtration
- Lubricating guideways and exposed sliding parts (if not automatic)
- Wiping down control panels and safety covers
These actions prevent buildup, overheating, and part contamination, and should be performed at the beginning or end of each shift.

Weekly and Monthly Maintenance Tasks
More in-depth inspections should be scheduled weekly or monthly depending on machine usage.
Weekly checks may include:
- Inspecting belts, couplings, and tool holders
- Verifying spindle taper cleanliness and runout
- Checking for air or oil leaks
- Backlash testing on lead screws or ball screws
Monthly tasks may include:
- Cleaning coolant tanks and skimmers
- Checking lubrication reservoir levels and lines
- Inspecting servo drives and motor mounts
- Checking door interlocks and emergency stop systems
These preventive measures help catch wear and misalignments before they turn into costly issues.
Importance of CNC Software and System Updates
Machine control software, CAM post-processors, and firmware updates play a major role in modern CNC performance.
Why update regularly:
- Improved cutting strategies and error prevention
- New material libraries and toolpath enhancements
- Security patches and bug fixes
- Better integration with automation systems
Coordinate with your CNC machine provider or controller manufacturer to schedule updates during planned downtime.
Proactive Spindle and Toolholder Maintenance
The spindle is the heart of the machine. Its failure is one of the most expensive repairs. Maintain it by:
- Avoiding over-tightening drawbars
- Cleaning tool tapers before insertion
- Monitoring abnormal heat or noise
- Balancing tool assemblies to reduce vibration
Similarly, toolholders should be cleaned, inspected, and replaced periodically to maintain cutting accuracy and surface quality.
Coolant System and Chip Management
Poor chip removal and contaminated coolant can cause tool breakage, poor finishes, and even machine damage.
Best practices:
- Use high-pressure coolant for deep holes and high-speed milling
- Clean coolant filters and screens weekly
- Monitor coolant pH and concentration levels
- Remove swarf and buildup from chip augers and tanks
A clean coolant system directly improves tool life, surface quality, and thermal stability.
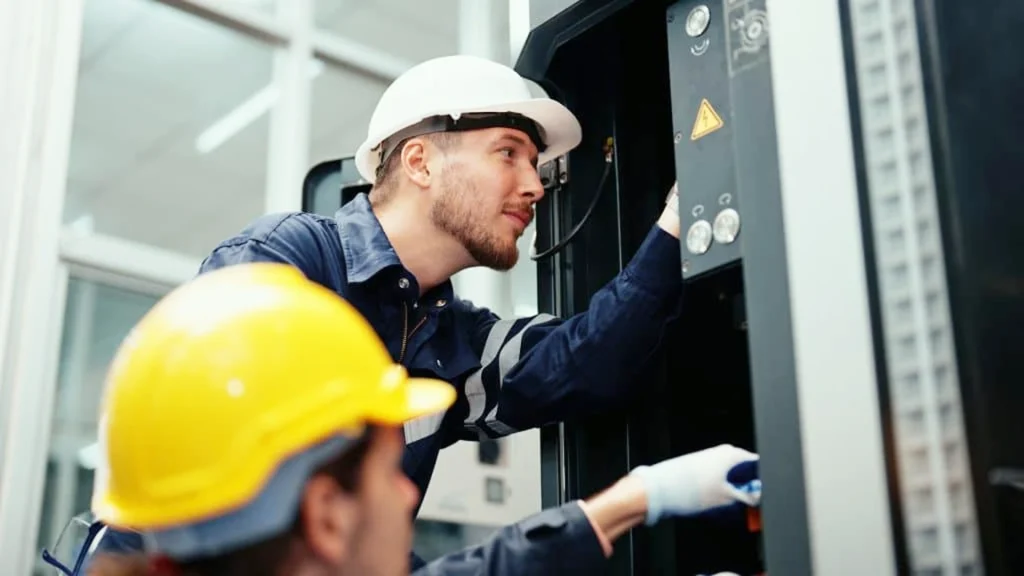
Lubrication and Linear Guide Maintenance
Linear guides and ball screws must be properly lubricated to prevent wear and maintain machine precision. If your machine has automatic lubrication, check reservoir levels and distribution regularly.
For manual systems:
- Apply the correct lubricant at manufacturer-recommended intervals
- Avoid over-lubricating, which attracts debris
- Inspect for uneven wear or scoring along the rails
Neglecting these elements often leads to vibration, chatter, and premature axis failure.
Troubleshooting Common Issues
Some common CNC problems and quick troubleshooting actions include:
- Inconsistent accuracy ➜ Check tool offset and thermal compensation
- Noise or vibration ➜ Inspect bearings, tool balance, or worn guides
- Finish defects ➜ Verify spindle alignment and check tool wear
- Axis drift or backlash ➜ Re-calibrate encoder or check ball screw preload
Logging these issues into a maintenance system helps build a predictive profile of your equipment’s health over time.
Preventive vs. Predictive Maintenance
Preventive maintenance involves scheduled inspections and part replacements, based on usage intervals. Predictive maintenance uses real-time data (vibration, heat, load) to forecast failures before they happen.
Modern CNC systems with IoT and sensor feedback allow predictive models that help:
- Reduce emergency breakdowns
- Lower repair costs
- Improve asset management
- Optimize maintenance scheduling
For high-volume operations, predictive systems are becoming a standard rather than an upgrade.
Maintaining Machine Alignment and Calibration
Over time, even the most rigid CNC machines can experience slight shifts in geometry. Periodic calibration ensures cutting accuracy, part consistency, and proper interaction between axes.
Best practices:
- Use laser or ball-bar calibration tools
- Recalibrate after collisions or heavy maintenance
- Keep a log of accuracy drift over time
- Involve professional service teams for multi-axis systems
This is especially important in precision industries like mold and aerospace machining.
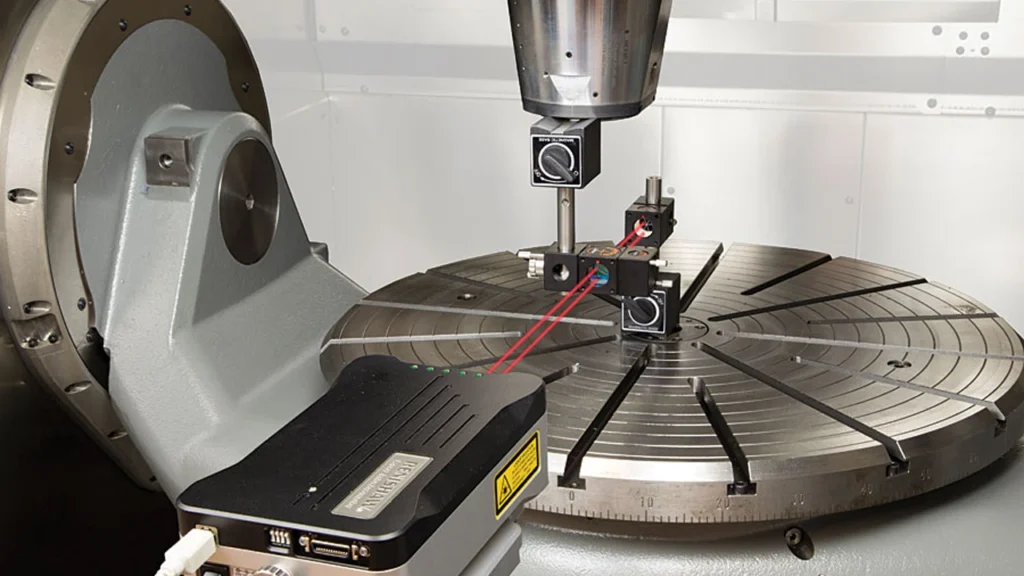
Future Trends in CNC Technology
As global manufacturing moves toward higher levels of automation, customization, and sustainability, CNC technology is evolving rapidly. New innovations are not just about faster spindles or better finishes—they’re about intelligent systems, adaptive processes, and connected factories. Here’s what the future holds for CNC machining:
Adoption of AI and Machine Learning in Machining
Artificial intelligence is increasingly being integrated into CNC controls to optimize machining parameters in real time. These smart systems can:
- Adjust feed rates and spindle speeds dynamically
- Detect tool wear and predict breakage
- Suggest optimized toolpaths based on historical data
By learning from past jobs, AI-enhanced machines can reduce scrap, improve efficiency, and even make autonomous decisions during production.
Integration of IoT and Industry 4.0 Technologies
CNC machines are becoming part of the Industrial Internet of Things (IIoT)—connected to networks that monitor, analyze, and control them remotely.
Key advantages include:
- Real-time machine monitoring
- Predictive maintenance alerts
- Centralized data dashboards
- Integration with ERP and MES platforms
This connectivity enables smart factories where production decisions can be made automatically based on live performance data.
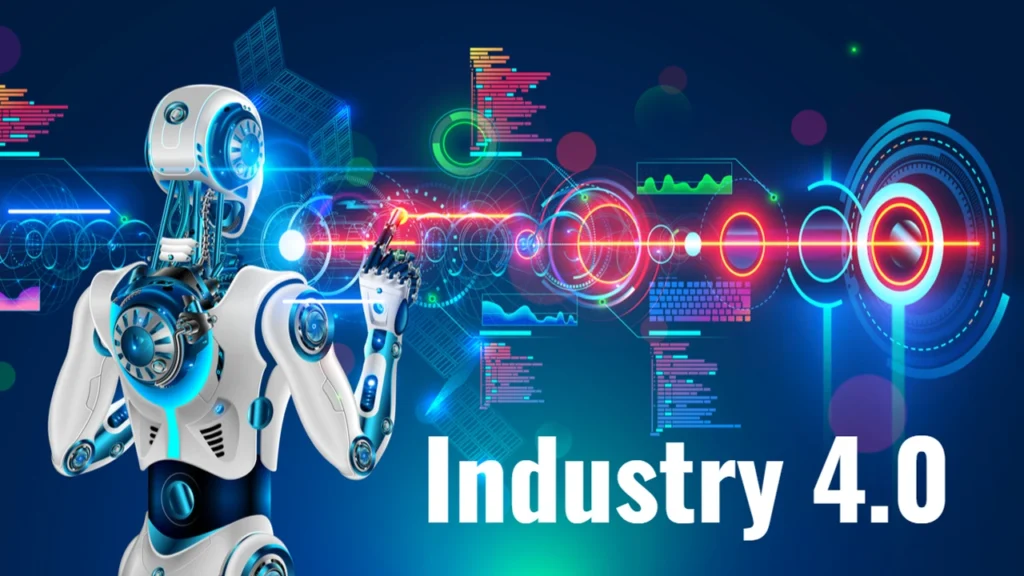
Advanced Automation and Lights-Out Manufacturing
“Lights-out machining” refers to running CNC machines with zero human supervision—often overnight or during weekends.
With the use of:
- Robotic arms for loading/unloading
- Pallet changers and tool presetting systems
- Automated inspection probes
Manufacturers can drastically increase output, reduce labor costs, and improve turnaround without expanding workforce size.
Growth of 5-Axis and Multi-Axis Machining
As part complexity increases, 5-axis and 6-axis CNC machines are gaining popularity. These systems allow:
- Machining of compound curves and deep cavities
- Reduction in setups and tool changes
- Higher precision through single-clamp workflows
Industries like aerospace, mold making, and medical benefit most from this evolution toward complete part machining in one cycle.
Digital Twin Technology for Virtual Machining
Digital twins create a virtual replica of your CNC machine, enabling simulation of every move before real execution.
Benefits include:
- Zero-risk testing of new programs
- Collision detection and cycle time optimization
- Offline troubleshooting and training
This improves first-pass yield and eliminates costly trial-and-error setups on the real machine.
Increased Adoption of Hybrid Machining Technology
Hybrid CNC machines combine multiple manufacturing processes (like milling + grinding, or turning + laser deposition) into a single platform.
This trend reduces:
- Setup times
- Part handling and clamping errors
- Machine footprint in constrained facilities
It enables complex, multi-material, or high-performance components to be made faster and more efficiently.
Emphasis on Sustainable and Eco-Friendly Machining
As environmental regulations tighten, CNC technology is moving toward low-emission, low-waste practices, including:
- Minimum Quantity Lubrication (MQL)
- Coolant recycling systems
- Energy-efficient servo drives
- Reduced idle power consumption
Green machining not only supports compliance—it also improves efficiency and brand reputation.
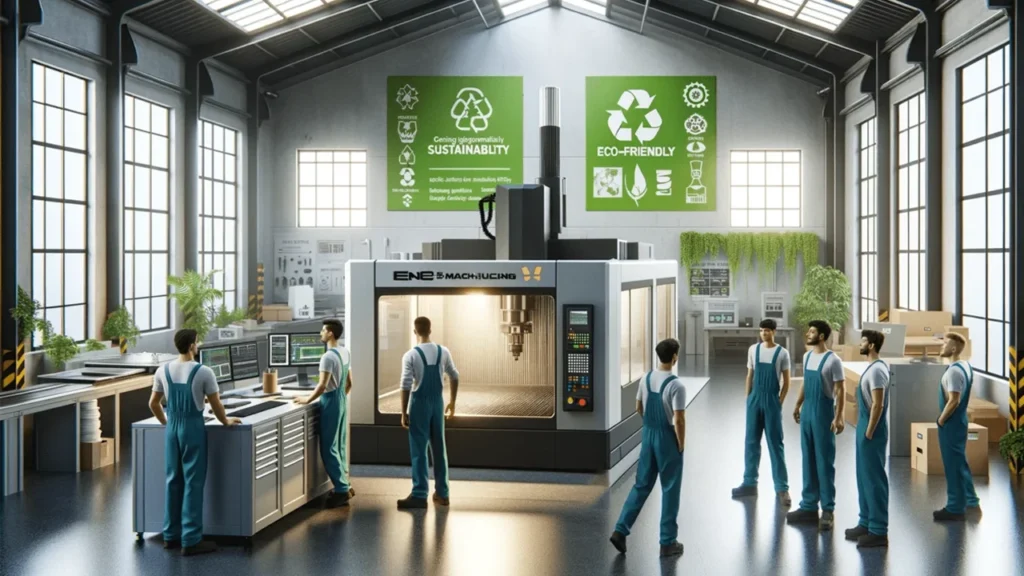
Adoption of Collaborative Robots (Cobots) in Machining Centers
Unlike industrial robots, collaborative robots (cobots) are designed to safely work alongside humans without barriers. In CNC environments, they are used for:
- Light-duty loading/unloading
- Simple secondary operations (deburring, marking)
- Inspection and part handling
Cobots enhance flexibility for small-batch and high-mix production, where full automation isn’t cost-effective.
Expansion of AI-Driven Quality Inspection Systems
AI and machine vision systems are being used more often to perform real-time part inspection directly on the machine or at the exit stage.
These systems can:
- Compare machined parts to 3D CAD models
- Identify surface defects or dimension deviations
- Auto-classify pass/fail status for sorting
In high-volume and precision industries, this ensures zero-defect manufacturing without manual inspection bottlenecks.
Conclusion: What is a CNC Machine
CNC machines have fundamentally transformed the way we manufacture—making it possible to produce complex, high-precision components at speed and scale. Whether you’re machining engine blocks, surgical implants, aerospace brackets, or custom molds, CNC technology offers unmatched accuracy, efficiency, and repeatability.
By replacing manual control with digital programming, CNC machines eliminate variability and enable consistent quality across production runs. From basic turning and milling to advanced multi-axis machining and hybrid systems, CNC has become the universal language of modern manufacturing.
If your business demands faster lead times, tighter tolerances, and reliable scalability, CNC is no longer optional—it’s essential.
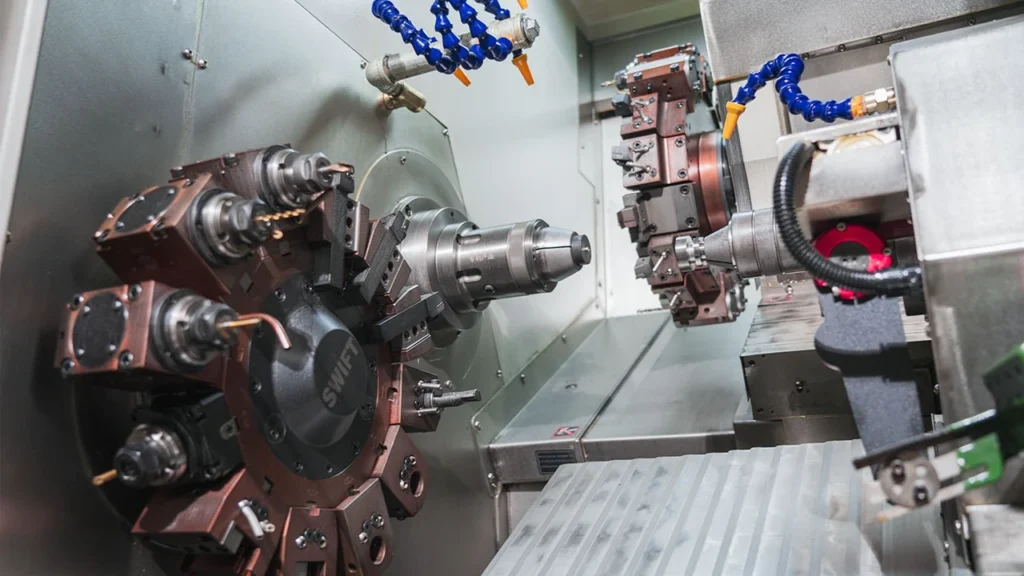
Why Investing in a CNC Machine is a Game-Changer
Adopting CNC machining gives manufacturers the ability to:
- Meet high-volume demand without sacrificing precision
- Automate production and reduce labor dependency
- Adapt quickly to new designs and materials
- Deliver consistent quality that meets global standards
This leap in capability helps businesses stay competitive, profitable, and future-ready—especially in an era of smart factories and Industry 4.0.
Key Takeaways for Choosing and Maintaining a CNC Machine
If you’re considering a CNC investment, remember to:
- Start by identifying the specific machining processes your parts require
- Match those needs with the right machine type, configuration, and control system
- Prioritize ease of maintenance, after-sales support, and future upgradeability
Good decisions made early can save hundreds of hours and thousands of dollars down the line.
Staying Ahead in a Competitive Industry
With global markets demanding faster innovation and tighter quality control, CNC machining is a cornerstone of industrial success. But it’s not just about buying the machine—it’s about building the right strategy, team, and workflow around it.
Manufacturers that embrace CNC fully are better positioned to deliver at scale, adapt to change, and lead their industries.
Why Choose Rosnok for Your CNC Machine Needs?
Whether you need a simple lathe, a high-speed machining center, or a custom-configured solution, we’re here to help. With over 60,000 square meters of production capability, global certifications, and a full range of CNC equipment, Rosnok offers:
- One-stop procurement for all major CNC technologies
- Reliable export solutions for global customers
- Tailored advice for your industry and production scale
- Fast after-sales support and engineering assistance
We’re not just machine suppliers—we’re your long-term manufacturing partner.