Have you ever wondered, what is a Swiss lathe? How does it work? What makes it so different from traditional CNC machines? Why is it trusted for such a wide range of complex machining tasks? Can it truly meet the extreme precision standards demanded by today’s most advanced industries? What industries count on Swiss lathes to get the job done right?
A Swiss lathe is a high-precision CNC machine built to handle small, complex parts with extraordinary accuracy. Its defining features include a dual-spindle configuration, multiple tool stations, and the ability to perform turning, drilling, milling, and threading operations—all in a single setup. This integration dramatically improves efficiency, reduces part handling, and ensures unmatched consistency across every cycle, making it the machine of choice for demanding, high-precision production environments.
In this guide, you’ll learn what a Swiss lathe is, how it operates, its structural features, supported machining functions, key advantages, and the industries where it delivers exceptional value.
What Is a Swiss Lathe
A Swiss lathe, also known as a Swiss-type CNC lathe or Swiss turning center, is a high-precision machine tool engineered specifically for machining small, complex, and tight-tolerance components. Unlike standard CNC lathes, which are often used for general-purpose turning, the Swiss lathe is uniquely designed to deliver extreme accuracy, smooth surface finishes, and uninterrupted multi-operation workflows—making it a go-to solution in the field of ultra-precise CNC machining.
What sets a Swiss lathe apart is its uncompromising dedication to micromachining. It is purpose-built to process very small parts, often with diameters under 32mm, although some models can handle slightly larger sizes. These parts typically require tolerances within microns, ultra-smooth surfaces, and multi-step geometries—all of which must be achieved without repositioning or reclamping the material. That’s where the Swiss lathe excels.
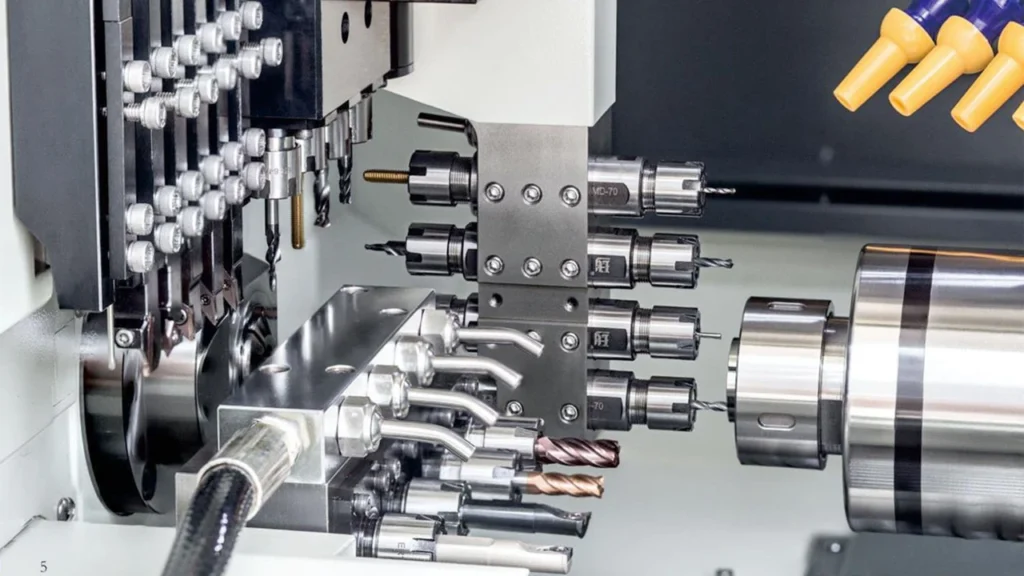
Instead of being just another turning machine, a Swiss lathe represents an entirely different category of high-performance CNC equipment. It prioritizes continuous processing, tool-path coordination, and material stability, even when machining extremely slender or delicate parts. This makes it particularly effective in scenarios where standard lathes may struggle with vibration, tolerance control, or part deformation due to tool pressure.
The term “Swiss” doesn’t merely refer to its heritage—it has become a synonym for reliability, engineering sophistication, and production excellence. Today’s Swiss-type lathes are fully CNC-controlled, highly automated, and capable of supporting advanced manufacturing workflows that demand speed, precision, and minimal human intervention.
Whether used in prototyping or mass production, the Swiss lathe is best understood as a specialized tool designed to solve a very specific problem: how to manufacture small, precise, and complex components with maximum efficiency and minimal variation.
To better understand its significance in precision manufacturing, let’s take a closer look at where the Swiss lathe originated—and how it evolved into what it is today.
Origin and Evolution of Swiss-Type Lathes
The origin of the Swiss lathe dates back to the late 19th century in Switzerland, where the demands of the booming watchmaking industry required new levels of machining precision. Traditional lathes at the time were not capable of producing the incredibly small, highly intricate components required for timepieces—such as tiny shafts, screws, and pinions—without issues like deflection, vibration, or inconsistent dimensions. In response, Swiss engineers developed a new type of sliding headstock lathe that would later become known as the Swiss-type lathe.
What made this machine unique was its ability to support the material very close to the cutting point using a guide bushing, while the workpiece itself moved axially during machining. This configuration allowed the machine to process very slender parts with high stability and minimal tool pressure. Early Swiss lathes were manually operated and mechanically simple, but they set a new standard for precision turning and became the backbone of Swiss micro-manufacturing.
As global industries began to adopt miniaturized components in fields like medical instruments, electronics, and aerospace, the concept of the Swiss lathe started gaining international attention. Manufacturers outside of Switzerland began to recognize its advantages, especially in producing small parts with long length-to-diameter ratios or complex geometries.
The real transformation occurred with the integration of CNC (Computer Numerical Control) systems in the late 20th century. Swiss lathes evolved from manually controlled machines into sophisticated, fully automated systems capable of performing multiple operations in a single cycle. CNC control enabled more axes, tighter tolerances, faster tool changes, and the ability to process parts with unmatched repeatability—even in high-volume production settings.
Today, the Swiss-type lathe is no longer limited to watchmaking. It has become a critical asset in industries where component precision, size constraints, and complexity cannot be compromised. The evolution from a mechanical watchmaking tool to a fully automated precision production platform reflects not only technological advancement, but also the changing demands of modern manufacturing.
Definition and Positioning in CNC Machining
A Swiss lathe, in the context of CNC machining, is not merely a specialized version of a conventional lathe—it is a distinct class of machine tool engineered with a singular purpose: to achieve exceptional precision and efficiency in the production of small, complex parts. In manufacturing environments where micrometer-level tolerances, fine surface finishes, and intricate geometries are non-negotiable, the Swiss lathe is positioned as the machine of choice.
Unlike standard CNC lathes, which typically fix the workpiece in a chuck or collet and bring the tools to the rotating part, a Swiss lathe is configured around a sliding headstock mechanism, supported by a guide bushing. This architecture allows the material to move axially during machining, keeping the cutting action extremely close to the point of support. The result is minimal deflection and vibration—critical factors when machining components with small diameters or long length-to-diameter ratios.
Functionally, Swiss lathes excel where conventional lathes begin to struggle. When a part demands multiple operations—such as turning, drilling, milling, grooving, and threading—within a single cycle, a Swiss-type machine can execute these processes simultaneously or in sequence with minimal repositioning. The integration of multiple tool stations, high spindle speeds, and complex multi-axis control places the Swiss lathe in a unique performance category.
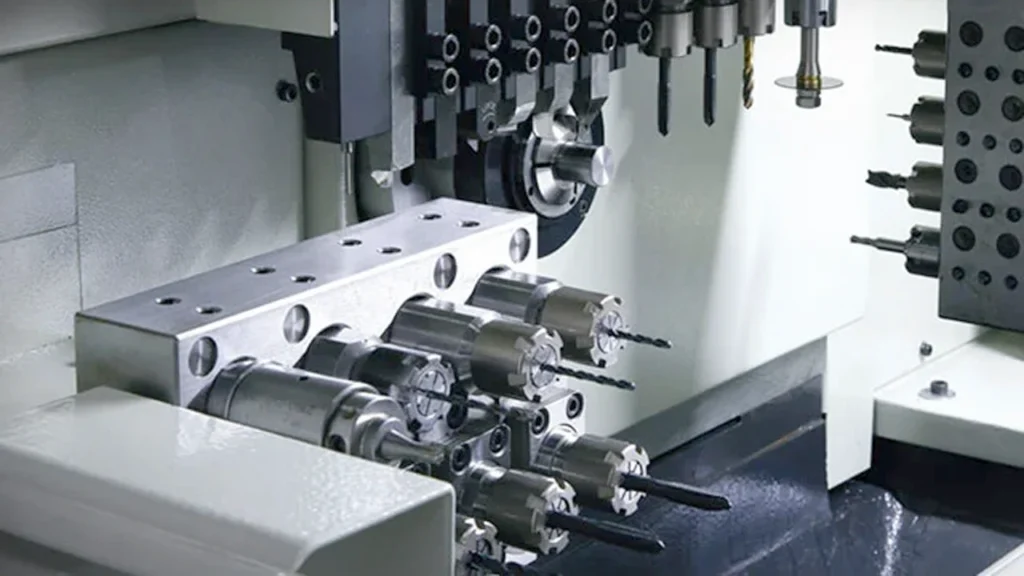
In terms of market positioning, Swiss lathes are viewed as high-precision, high-throughput machines that sit at the intersection of micro-manufacturing and automation. They are not general-purpose machines, nor are they the best choice for large or simple parts. Their strengths shine in environments where part complexity, consistency, and tight tolerances are prioritized over raw material removal rate or flexibility.
This makes Swiss lathes highly relevant for modern manufacturing strategies such as lean production, lights-out machining, and zero-defect quality control. They are an essential solution for shops and factories focused on scalable, precision-driven part production, where investment in performance and consistency yields long-term cost efficiency.
How Does a Swiss Lathe Work
A Swiss lathe operates with a fundamentally different approach compared to standard CNC lathes. While both rely on rotary cutting and CNC control, the Swiss lathe introduces unique motion dynamics and tool coordination strategies to enhance stability and precision—especially for small, slender, or highly detailed parts.
The key lies in how the machine manages part movement and tool engagement. Instead of treating each operation as an isolated step, the Swiss lathe is built to integrate multiple processes within a single, uninterrupted cycle. This allows for more efficient material handling, tighter tolerances, and consistent output even during extended production runs.
In the following sections, we’ll break down how this machine actually works, what makes it operationally different from conventional CNC lathes, and how its workflow delivers continuous, high-precision machining.
General Operating Concept
At the heart of the Swiss lathe’s function is a different way of thinking about how a part is machined. Traditional CNC lathes rely on a fixed workpiece held in a chuck or collet while various tools move in to perform turning, facing, or drilling operations. The Swiss lathe, by contrast, takes a more dynamic approach—one where both the workpiece and the tools are in coordinated motion throughout the machining cycle.
In a Swiss lathe, material is fed through the machine in bar form. During operation, the bar stock itself moves axially—meaning it slides in and out—rather than remaining stationary. At the same time, multiple cutting tools are precisely controlled along different axes to engage the material close to its point of support. This dual-motion concept is central to the Swiss lathe’s ability to maintain precision and eliminate deflection, especially when machining long or slender parts.
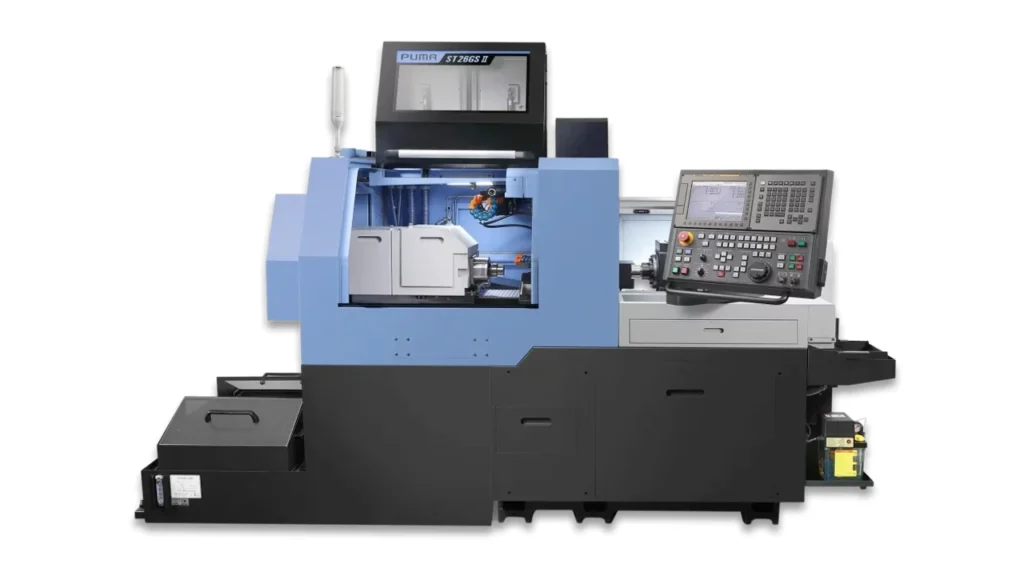
What defines the Swiss machining concept is not just simultaneous tool movement, but the integration of multiple operations within a single process. It is common for turning, milling, drilling, grooving, and threading to occur in one continuous cycle, using various tool stations positioned around the part. This enables the machine to complete highly complex parts without intermediate steps or manual handling.
Unlike traditional setups where the part is repositioned or re-chucked between operations, Swiss lathes are designed to minimize interruption. The combination of synchronized movement, tool coordination, and continuous bar feeding results in higher throughput, more consistent tolerances, and smoother surface finishes—even across long production runs.
Swiss lathes also offer multi-axis flexibility, allowing live tools to engage with the workpiece at various angles. While not all machines have the same configuration, the general operating concept is built around doing more with fewer setups, fewer handling steps, and more tightly controlled machining environments.
In essence, the Swiss lathe’s operating concept is about integration, balance, and precision. It represents a shift from linear machining to a system-oriented workflow where all elements—material, tools, axes, and automation—are aligned to produce complex small parts with unmatched stability and efficiency.
Swiss Lathe Machine Workflow
The workflow of a Swiss lathe is designed to execute high-precision machining in a continuous, fully integrated process. From the moment bar stock enters the machine to the final part ejection, every step is optimized for efficiency, accuracy, and repeatability. Unlike conventional turning methods that separate operations into multiple stages, the Swiss lathe combines them into a seamless sequence, minimizing idle time and manual intervention.
Once the material is fed into the machine, the machining cycle begins immediately. Multiple tools are already positioned and programmed to work in a synchronized manner. Turning, milling, drilling, threading, and other operations are executed in rapid succession, often with overlapping tool engagement. This coordination allows several features of a part to be completed simultaneously, drastically shortening cycle times while maintaining micron-level tolerances.
Tool transitions are automated, with the CNC control managing the engagement sequence. The system ensures that each tool contacts the material only when required, optimizing tool life and surface finish. At no point during the cycle does the part need to be repositioned or re-clamped—this stability contributes directly to dimensional consistency and geometric integrity.
Bar advancement is incremental and precisely timed with the cutting sequence. As material is consumed, new bar length is fed forward, ensuring continuous production with minimal downtime. Swiss-type machines typically integrate auxiliary systems like chip conveyors and coolant delivery, which support thermal stability and clean cutting conditions during long, unattended runs.
By orchestrating part movement, tool activation, and feed control into one unified process, the Swiss lathe achieves a level of workflow efficiency unmatched by conventional turning systems. This integrated methodology is what makes it ideal for mass production of complex, small-diameter components where repeatability, speed, and surface quality are equally critical.
Swiss lathes are also engineered to run continuously. Equipped with automated bar feeders, chip conveyors, and coolant systems, they support “lights-out” manufacturing—allowing production to continue through the night or across multiple shifts with minimal human supervision.
In essence, the workflow of a Swiss lathe is not defined by individual cutting actions, but by how those actions are coordinated, automated, and optimized for high-precision, high-volume part production. It is a system where tool choreography, part movement, and process control come together to deliver outstanding results with minimal interruption.
Key Components and Functional Capabilities
A Swiss-type CNC lathe is not defined by a single feature, but by the precise coordination of its internal systems. Each core component—from the spindles and tool systems to the control unit and chip management—is engineered to support high-precision, continuous, and automated machining. Unlike general-purpose lathes that operate in more isolated cycles, the Swiss lathe operates as a tightly integrated system where every element contributes to accuracy, stability, and speed.
This chapter introduces the major functional components that make a Swiss lathe unique. Rather than focusing on design details, we’ll examine how each component works in harmony to enable seamless machining, efficient tool transitions, multi-operation support, and reliable lights-out production. Understanding these functions is key to appreciating the system-level intelligence behind Swiss-type manufacturing.
Spindle Arrangement and Synchronized Movement
The Swiss lathe typically features a dual-spindle configuration: a main spindle and a sub-spindle. The main spindle performs the initial machining tasks, such as front-end turning, facing, and drilling. Once these are completed, the sub-spindle seamlessly takes over, grabbing the part and rotating it to machine the rear side. This handoff occurs without removing the part or manual repositioning, which greatly improves concentricity and reduces handling errors. Both spindles are synchronized by the CNC system, allowing for smooth transitions and enabling “done-in-one” machining, where all operations are completed in a single cycle.
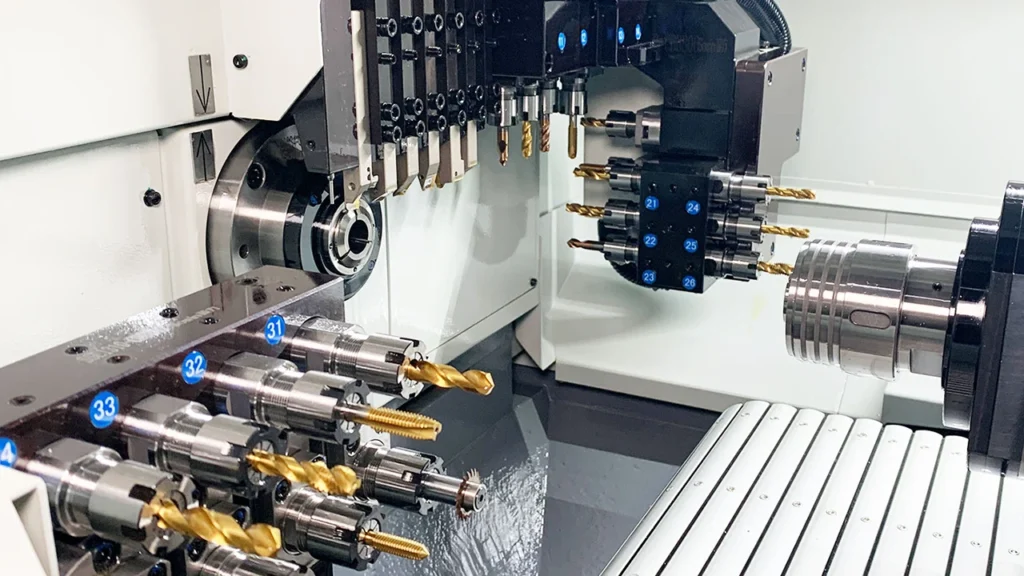
Tool System and Multi-Operation Support
Swiss lathes are equipped with multiple tool posts that hold both static and live tools. These tools are arranged around the workpiece to perform a wide range of operations including turning, cross drilling, grooving, milling, and threading. Thanks to the multi-position layout, several tools can work simultaneously or in quick succession. This minimizes tool change time and allows multiple features to be machined on a single part without re-fixturing. The tool system plays a vital role in supporting complex part geometries and reducing total cycle time.
Feed System and Bar Feeding Configuration
One of the defining features of Swiss lathes is the use of bar stock, which is fed axially into the machine. The feeding system is integrated with an automatic bar feeder that pushes the raw material forward incrementally as machining progresses. This setup enables continuous production and supports long, slender parts with excellent rigidity during cutting. By advancing the bar in precise steps, the machine ensures that only the section being worked on is exposed, reducing deflection and improving dimensional stability.
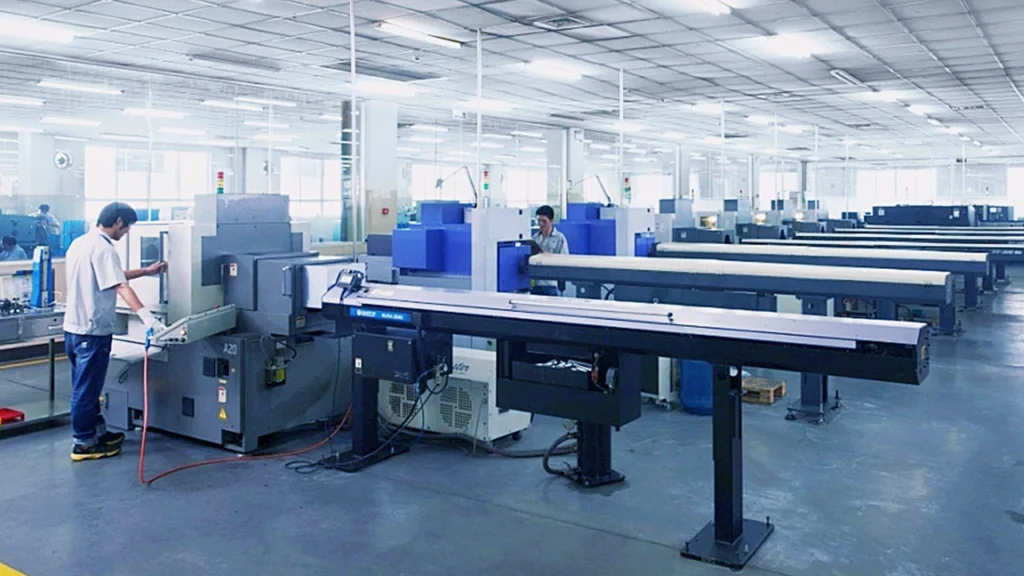
Multi-Axis Control and Live Tooling
Most Swiss lathes support 5-axis or even higher multi-axis configurations. In addition to X and Z axes for linear movement, machines often include Y-axis motion for off-center features and C-axis rotation for synchronized spindle control. Live tooling enables dynamic operations such as milling or cross-drilling while the spindle is stationary or rotating. These capabilities allow for the machining of complex 3D features without transferring the part to another setup, further improving efficiency and accuracy.
Control System Integration
The CNC control system is the brain of the Swiss lathe. It manages all aspects of machining—from spindle speeds and axis movements to tool timing and bar advancement. Advanced control software enables the machine to execute multi-operation sequences with high precision and real-time adjustments. Many systems also support simulation, error detection, and adaptive toolpath control. This level of integration ensures consistent part quality, high productivity, and reduced risk of tool crashes or programming errors.
Chip Evacuation and Coolant Delivery
Efficient chip management is crucial for long-term precision and machine reliability. Swiss lathes are equipped with high-pressure coolant systems that flush chips away from the cutting zone and reduce thermal buildup. Chip conveyors remove waste material from the enclosure automatically, allowing for longer unattended operation. Together, these systems maintain a clean machining environment, protect tool edges, and ensure smooth cutting conditions—especially important for long, uninterrupted cycles.
Structural Rigidity and Motion Stability
Swiss lathes are built with high-rigidity machine beds, linear guides, and precise ball screws that minimize vibration and thermal deformation. This structural stability is essential for micromachining applications, where even slight movement can lead to out-of-tolerance parts. The mechanical foundation of the machine supports all the dynamic components and ensures accurate positioning under high-speed conditions. This base-layer stability is one of the key enablers of the Swiss lathe’s unmatched repeatability and precision.
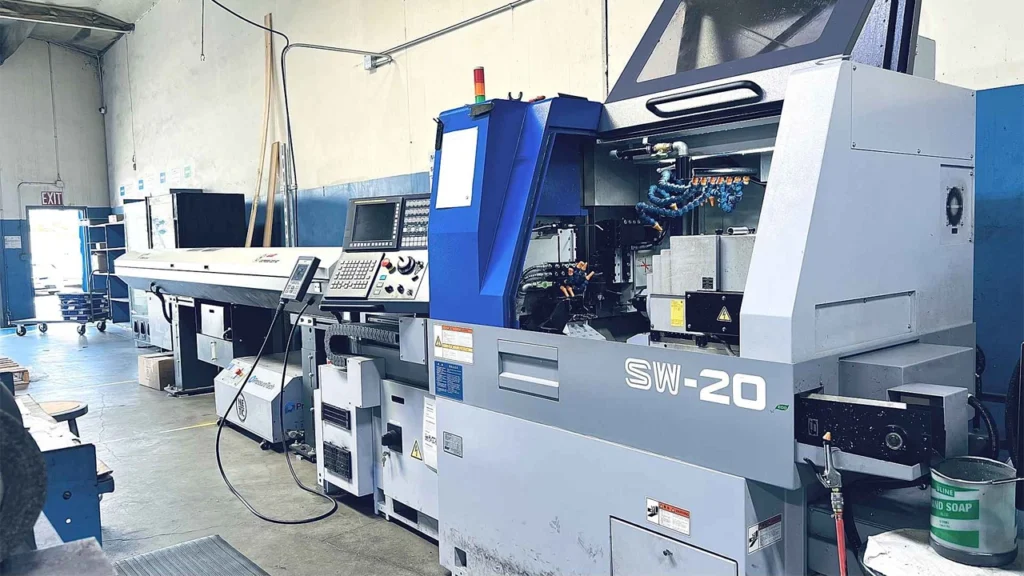
Machining Capabilities of a Swiss Lathe
Swiss lathes are highly specialized machines designed to perform a wide range of machining operations with extreme precision. Their versatility allows them to execute multiple operations on a single workpiece without the need for repositioning or re-fixturing, making them a cornerstone of efficient, high-precision manufacturing. Below, we’ll explore the various machining operations supported by a Swiss lathe, the types of geometries it excels at, and its capabilities in terms of size, accuracy, surface quality, and cycle time efficiency.
Types of Machining Operations Supported
Swiss lathes can perform a broad array of machining operations, allowing manufacturers to produce complex parts in a single, uninterrupted cycle. Some of the key operations that a Swiss lathe can handle include:
Turning
Turning is the primary operation on any lathe, and in the Swiss platform, it is elevated to a new level of precision. With the workpiece supported closely and precisely positioned, the turning tools engage with superior stability, making it ideal for achieving tight diameter tolerances and excellent surface finishes on small, slender components. Whether rough turning or fine finishing, the Swiss lathe offers the control and rigidity needed for consistent results.
Drilling
Swiss lathes can perform both on-axis and cross-axis drilling with extremely accurate positioning. Tooling is arranged to allow for hole-making in both front and side orientations of the workpiece. Thanks to the controlled feed and rigidity of the setup, Swiss machines are capable of producing high-precision drilled holes with tight tolerances in depth, diameter, and location—without the need for secondary machining.
Milling
Live tooling in a Swiss lathe enables light to moderate milling operations, such as flats, slots, or complex geometric features on cylindrical parts. Multi-axis capability allows the tool to approach the part from different angles, providing flexibility to machine features that would otherwise require transfer to a milling center. While heavy-duty milling is not its primary strength, for many small parts, the Swiss lathe provides all the required milling functions within the same cycle.
Threading
Internal and external threading—both metric and imperial—can be performed directly on the Swiss lathe using specialized threading tools or live tools for thread milling. This eliminates the need to transfer the part to a tapping station or threading machine, saving cycle time and preserving alignment accuracy. The lathe can handle both standard and custom thread profiles, including those with tight tolerances and precise lead-in features.
Grooving and Parting
Grooving tools are used to cut precision channels, undercuts, or internal features. In a Swiss lathe, these are typically performed with excellent repeatability and control, thanks to the solid tool support and precise toolpaths. Parting off the finished component is also fully automated and integrated into the cycle—often synchronized with sub-spindle pickup for immediate rear-end finishing.

Boring and Reaming
Swiss lathes can also perform boring operations to enlarge or refine internal diameters, as well as reaming to achieve precise internal sizing and fine finishes. These operations are valuable in industries like medical or aerospace, where internal feature quality is critical. The tight process control of the Swiss lathe ensures high concentricity and surface smoothness in these operations.
Tapping
Tapping operations for internal threads are handled via synchronized rotation between the tool and the spindle. This allows for controlled depth, clean thread formation, and minimal tool breakage—even in small-diameter holes. Thread tapping on the Swiss lathe is fully integrated into the machining cycle, improving process efficiency and dimensional consistency.
Custom Features and Special Operations
Modern Swiss machines also support custom features such as polygon turning, engraving, broaching, and eccentric drilling. These capabilities are especially valuable in complex part geometries like connector housings, surgical implants, or custom fasteners. Thanks to the machine’s multi-axis coordination and live tooling flexibility, many of these complex operations can be completed without changing setups.
Geometries and Part Features It Excels At
Swiss lathes are particularly well-suited for machining parts with complex geometries that would be challenging for conventional machines. Some of the key part features that Swiss lathes excel at include:
- Long, slender shafts: The Swiss lathe’s guide bushing supports the workpiece close to the cutting point, allowing for the machining of long, slender parts without deflection or vibration. This makes Swiss lathes ideal for parts such as shafts, pins, and rods.
- Thin-walled components: Swiss lathes can handle thin-walled parts with delicate features due to their precise control over material movement and tool engagement, preventing deformation and maintaining dimensional integrity.
- Deep holes: Swiss lathes are capable of drilling and boring deep holes with high precision. Their feed systems can handle long workpieces while maintaining tight tolerances, making them ideal for applications like hydraulic components and medical devices.
- Small-diameter, complex curved surfaces: Swiss lathes excel at machining parts with small diameters and complex geometries, such as micro-electromechanical systems (MEMS), medical implants, and aerospace components.
Size Range and Dimensional Limitations
Swiss lathes are designed to work with small-diameter parts, typically in the range of 0.5 mm to 32 mm in diameter. However, some models can handle slightly larger diameters, depending on the design and tooling capabilities.
The key advantage of Swiss lathes lies in their ability to machine parts with high length-to-diameter ratios. This allows manufacturers to produce long, slender components, such as rods or shafts, with exceptional precision, even at high volumes.
However, the size limitations of Swiss lathes should be considered for particularly large parts. The machining capabilities are best suited for parts that fit within the smaller size range, and very large or heavy parts may require a different type of machine.
Accuracy and Surface Quality
Swiss lathes are renowned for their high accuracy and ability to achieve micron-level tolerances, often within ±0.001 mm or better. This level of precision is essential in industries where the parts must fit together perfectly, such as in medical devices, aerospace, and electronics.
Surface quality is another area where Swiss lathes shine. Due to the stability of the workpiece and the controlled movement of tools, Swiss lathes can achieve excellent surface finishes, often in the range of Ra 0.1 μm or better. This is critical for components requiring smooth surfaces or those that must meet stringent quality standards.
In total, the Swiss lathe acts as an all-in-one solution for precision small-part manufacturing. Its ability to consolidate these operations into a single, uninterrupted process not only improves cycle times and part quality, but also eliminates the risks of misalignment, handling damage, and dimensional drift common in multi-machine workflows. The Swiss lathe ensures consistent part quality that would be difficult to achieve with separate machine transfers.
Swiss Lathe vs Other CNC Solutions
Swiss lathes are often viewed as the solution for high-precision, small-part manufacturing, but they are not always the best choice in every situation. When considering a Swiss lathe for a specific project, it’s important to compare it with other CNC technologies, such as traditional CNC lathes and machining centers, to ensure the right machine is selected for the job. This section will focus on the key differences between Swiss lathes and other CNC solutions, exploring when Swiss lathes truly shine and when other machines might be more appropriate.
Swiss Lathe vs Traditional CNC Lathe
The main difference between a Swiss lathe and a traditional CNC lathe lies in how they handle workpieces. A traditional CNC lathe holds the part stationary and uses tools that move along the X, Y, and Z axes to remove material. This setup is effective for producing a wide range of parts, but when it comes to small, slender components or those with long length-to-diameter ratios, traditional CNC lathes often fall short.
In contrast, a Swiss lathe features a sliding headstock that feeds the workpiece through the machine while keeping it supported near the cutting point. This reduces the risk of deflection, vibration, and inaccuracies when machining long, thin components. Additionally, Swiss lathes often support multi-operation machining, combining turning, milling, drilling, and threading in one continuous process—this integration minimizes setup time and improves overall cycle efficiency.
While traditional CNC lathes are highly versatile for larger or less intricate parts, Swiss lathes excel when precision and small part size are critical factors. Swiss lathes are ideal for high-precision, high-volume production of small, complex parts.
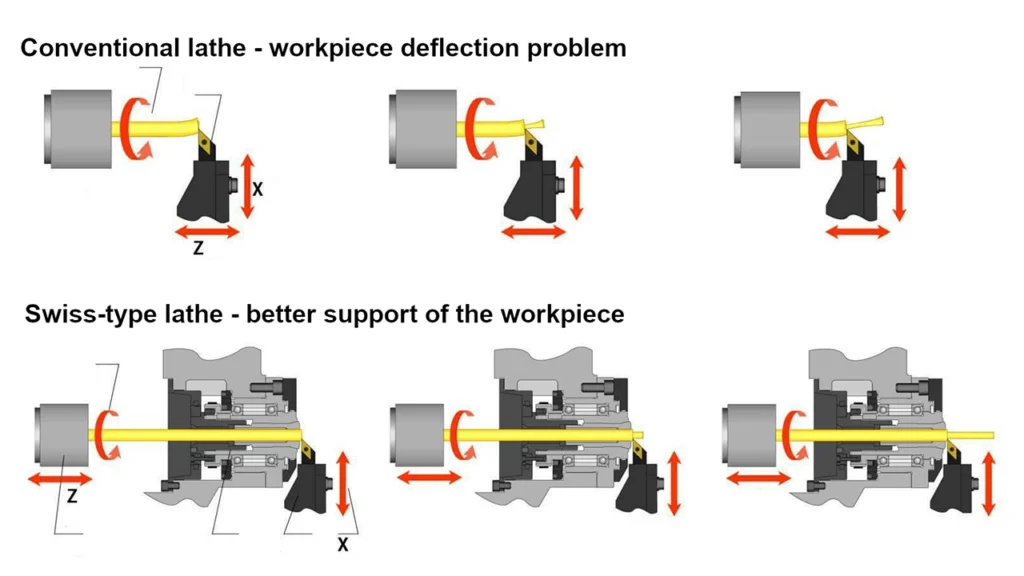
Swiss Lathe vs Machining Center (for Small Parts)
Machining centers are typically used for larger, more complex parts that require multi-axis machining. While they are highly effective for multi-axis milling and can perform turning operations, they are often not optimized for machining small parts with tight tolerances. In contrast, Swiss lathes are specifically designed to handle small-diameter parts—often those with diameters under 32mm—and achieve micron-level precision.
Swiss lathes offer an advantage in multi-operation machining for small parts, where turning, drilling, milling, and threading can all occur in one continuous process. This ability to perform multiple operations in a single cycle minimizes downtime and reduces the chances of errors introduced during part transfers. Machining centers, on the other hand, typically require multiple setups to perform these same operations, leading to higher labor costs and longer cycle times.
For small, high-precision parts where tight tolerances and multi-operation workflows are essential, Swiss lathes provide a more efficient, cost-effective solution compared to machining centers.
When Swiss Lathes Outperform Other Technologies
Swiss lathes outperform other CNC technologies in specific scenarios where extreme precision, small part sizes, and high-volume production are required. Some key areas where Swiss lathes excel include:
- High Precision: Swiss lathes can achieve tolerances in the micron range, which is critical for parts used in medical, aerospace, and electronics industries.
- Small, Complex Parts: Swiss lathes are the go-to choice for machining long, slender shafts, micro parts, and components with complex geometries that require tight tolerances.
- Multi-Operation Integration: Swiss lathes excel in combining multiple machining operations (turning, drilling, milling, threading) into a single uninterrupted process, reducing cycle times and improving productivity.
- High-Volume Production: With automated bar feeders, chip conveyors, and coolant systems, Swiss lathes can run continuously for long production runs, making them ideal for mass production.
In scenarios requiring high precision and tight tolerances for small parts, Swiss lathes outperform traditional CNC lathes and machining centers, delivering superior results with minimized handling and faster throughput.
When Swiss Lathes Are Not the Ideal Solution
While Swiss lathes excel in certain applications, they are not always the best solution. Here are scenarios where other CNC technologies may be more appropriate:
- Large Parts: Swiss lathes are optimized for small-diameter parts. For large, heavy parts that require complex milling operations, machining centers or traditional CNC lathes may be more suitable due to their larger working envelopes and higher milling capabilities.
- Low-Volume Production: Swiss lathes are ideal for high-volume production, but the initial cost and the need for automation may make them less cost-effective for low-volume production or prototyping. In these cases, traditional CNC machines or manual machines may be a more affordable option.
- Heavy Milling Operations: While Swiss lathes are excellent for turning and light milling, they are not designed for heavy milling. If the part requires extensive milling or complex surface machining, a machining center may offer better performance.
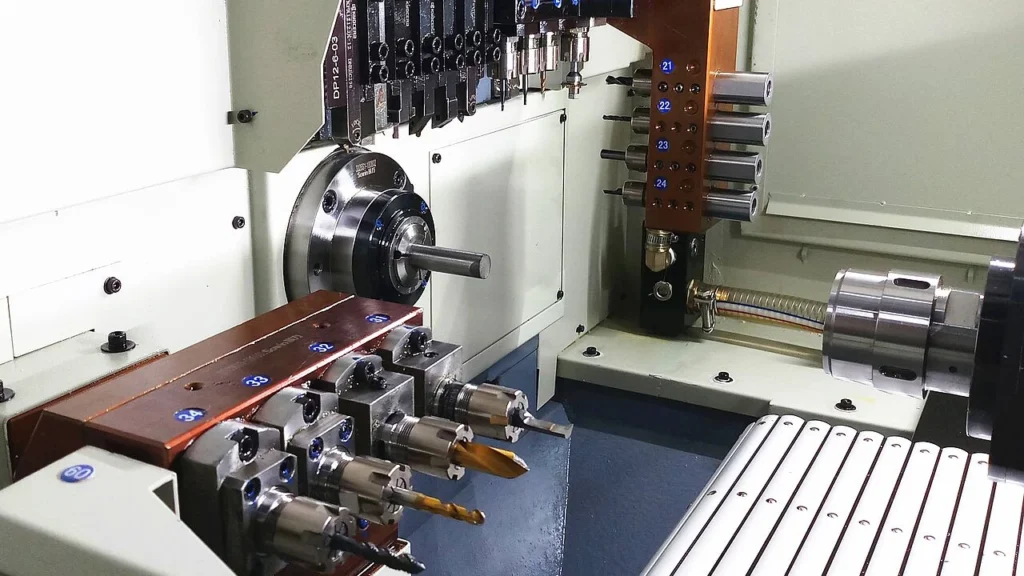
Suitable Boundaries for Swiss Lathes
Swiss lathes are best suited for small, high-precision parts, typically with diameters under 32mm. They excel in applications requiring tight tolerances and multi-operation machining. However, when part sizes exceed this range or when heavy milling is required, other CNC machines such as machining centers or traditional CNC lathes may be a better fit.
Is it Suitable for Multi-Variety, Small-Batch Production?
Swiss lathes are well-suited for multi-variety, small-batch manufacturing. Their ability to quickly switch between different part types, along with their flexibility to handle different operations in a single cycle, makes them a great choice for high-precision small-batch production. However, for parts that require extensive milling or complex features outside the Swiss lathe’s capabilities, a machining center may be better.
When Should You Consider Using a Swiss Lathe
Swiss lathes are highly specialized machines that offer superior precision and efficiency in machining small, complex parts. However, they are not always the ideal solution for every manufacturing scenario. In this section, we will explore the specific situations when a Swiss lathe is the best choice, based on the dimensions, tolerances, operations, volumes, and part complexities involved.
When Part Dimensions Require Stability
Swiss lathes are particularly well-suited for machining parts with small diameters (typically ≤32mm) and high length-to-diameter ratios (L/D). This makes them ideal for machining slender, long parts that would otherwise be prone to deflection, vibration, or inaccuracies when processed on traditional lathes. The guide bushing in Swiss lathes supports the workpiece as it moves through the machine, offering greater stability and reducing the risk of deformation compared to conventional lathes.
On standard CNC lathes, machining thin or long parts can lead to issues such as chatter and poor surface finishes, especially when the material is subjected to tool pressure. With Swiss lathes, the material is better supported, allowing for accurate cutting, even in parts with a high length-to-diameter ratio, making them perfect for industries that require high-precision pins, shafts, and rods.
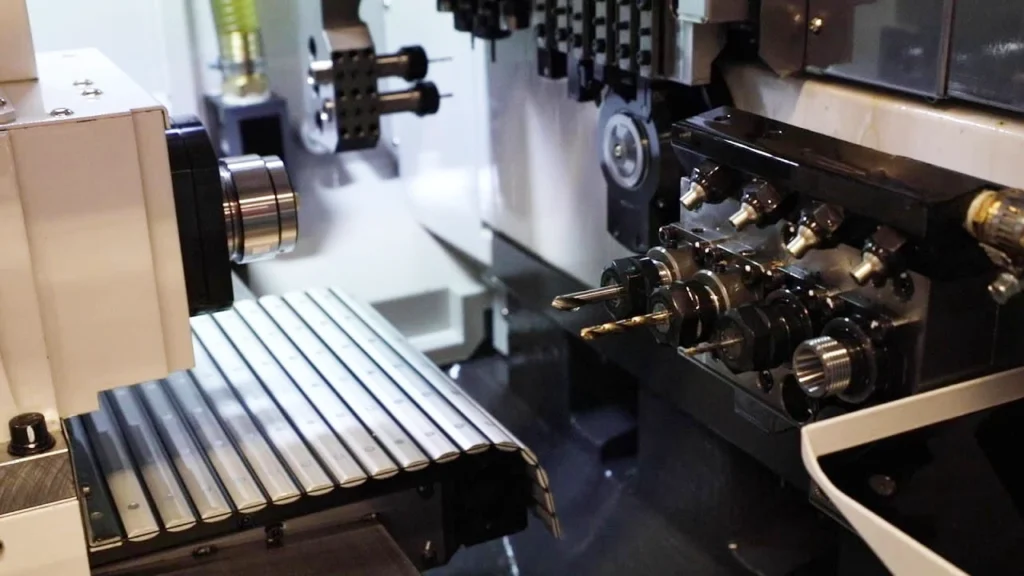
When Tight Tolerances and Surface Finish Matter
Swiss lathes are renowned for their ability to achieve tight tolerances, often as small as ±0.005mm. This level of precision is essential in industries such as aerospace, medical devices, and electronics, where parts must fit together with near-perfect alignment. The precision of Swiss lathes ensures that dimensional accuracy is maintained throughout the manufacturing process, even when producing thousands of identical parts.
In addition to tight tolerances, Swiss lathes also excel at producing smooth surface finishes. With Swiss lathes, the tools are positioned closer to the material, and there is reduced deflection, resulting in minimal tool pressure and low surface roughness. This ability to achieve high-quality finishes without the need for secondary operations (such as polishing or grinding) makes Swiss lathes ideal for parts that demand both tight tolerances and smooth surfaces.
When You Need Multi-Operation Machining in One Setup
One of the biggest advantages of Swiss lathes is their ability to perform multiple operations (turning, milling, drilling, and threading) in a single setup. This eliminates the need for transferring parts between machines or changing fixtures multiple times. Swiss lathes can perform these operations simultaneously or in rapid succession, saving significant cycle time and reducing the risk of errors due to repositioning or re-clamping.
This feature is particularly valuable when producing parts that require complex geometries or multi-step operations. For example, a Swiss lathe can simultaneously turn, mill, and drill on a part without requiring multiple setups, which improves consistency, reduces handling time, and ensures better alignment. This level of integration is especially beneficial in high-volume production, where speed and accuracy are critical.
When You’re Producing in Medium to High Volumes
Swiss lathes are ideal for medium to high-volume production environments. Their ability to run continuously and automate processes allows for lights-out manufacturing, meaning they can operate overnight or across multiple shifts with minimal human supervision. With features like automated bar feeders, chip conveyors, and coolant systems, Swiss lathes ensure consistent production with little downtime.
These automated capabilities also reduce labor costs and increase throughput. Whether it’s for producing medical implants, automotive components, or precision electronics, Swiss lathes can handle large production runs efficiently, while maintaining the precision required for these demanding applications.
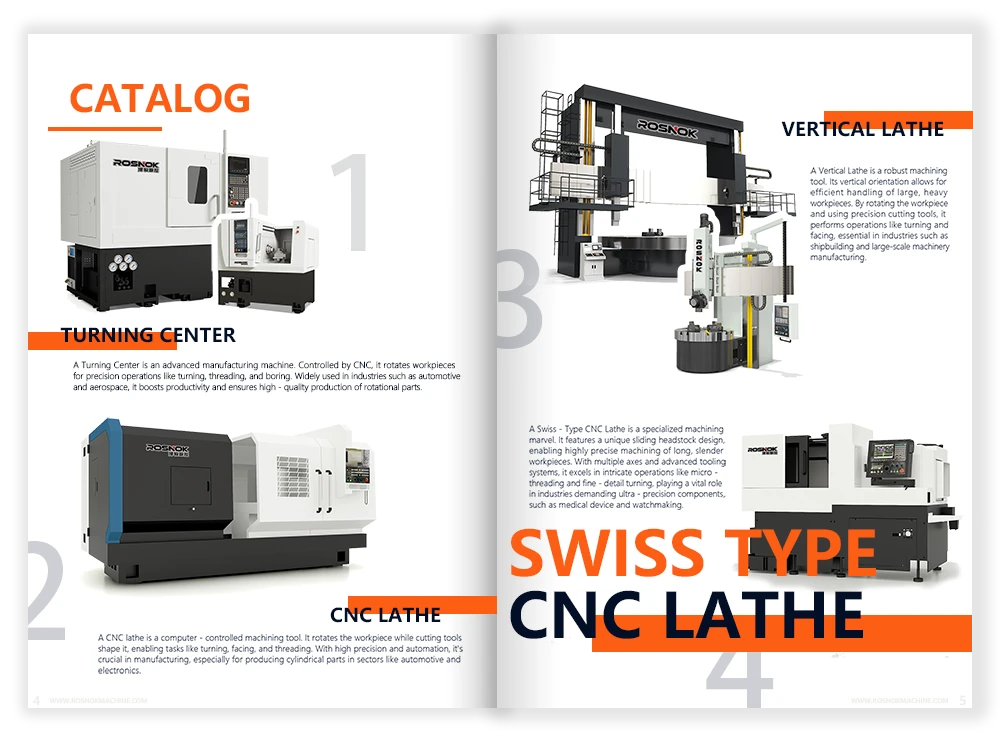
When Part Complexity Prevents Using Standard Lathes
When manufacturing parts with complex geometries, such as stepped shafts, double-ended features, or internal/external grooves, Swiss lathes are often the best solution. Traditional CNC lathes may struggle with these types of parts due to limitations in tool access or the need for multiple machines and setups. For example, parts with deep holes, internal threads, or multi-feature designs can often be produced on a Swiss lathe in a single cycle, reducing the chances of misalignment or errors.
Swiss lathes can handle asymmetric features or irregular shapes, which might require several stages of machining on traditional lathes. This multi-operation integration allows the Swiss lathe to produce highly complex parts, reducing the need for costly secondary operations or multiple machines.
When You Want to Maximize Process Stability and Repeatability
For applications where process stability and repeatability are critical, Swiss lathes provide significant advantages. The guide bushing helps eliminate deflection and ensures the material remains stable throughout the cutting process. Additionally, Swiss lathes are designed to produce identical parts with minimal variation over long production runs. This makes them ideal for industries with strict quality control requirements, such as aerospace, medical devices, and automotive manufacturing.
The Swiss lathe’s ability to maintain consistency throughout the production process makes it the perfect choice for environments where high repeatability and precise control over dimensional variation are crucial for part performance and compliance with industry standards.
When Your Shop Prioritizes Lights-Out Manufacturing
Swiss lathes are well-suited for lights-out manufacturing, which is ideal for shops that prioritize automation and minimizing human intervention. With features like automated bar feeders, chip conveyors, and coolant delivery systems, Swiss lathes can operate with little to no supervision. This is especially beneficial for high-volume production environments where labor costs are high or where 24/7 production is needed to meet demand.
By reducing the need for manual handling, Swiss lathes help improve both efficiency and safety, while allowing shops to maximize machine uptime. This feature is particularly advantageous for high-volume, low-labor cost environments, such as automotive parts manufacturing or precision component production.
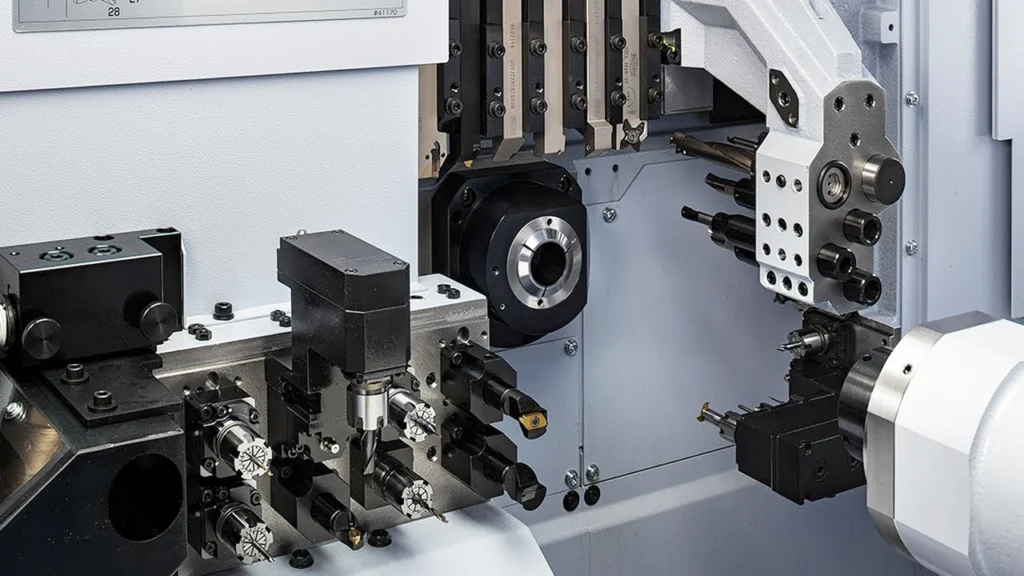
When Cost per Part Needs to Be Minimized Over Time
Although the initial capital investment for a Swiss lathe can be high, the long-term return on investment (ROI) can be excellent, particularly in high-volume production scenarios. Swiss lathes offer exceptional cost-effectiveness over time due to their ability to reduce cycle times, minimize setup costs, and automate production. The reduction in labor costs and the elimination of the need for additional machines or fixtures makes Swiss lathes an attractive option for stable, high-demand orders.
For stable large orders (such as in the automotive or medical industries), the cost per part can be significantly reduced as production volumes increase. The Swiss lathe’s efficiency in handling these parts over long production runs provides substantial cost savings, making it an ideal choice for applications where cost control is a key factor in maintaining competitive pricing.
Application Areas for Swiss Lathes
Swiss lathes are ideal for applications that demand ultra-high precision and the ability to machine small, complex parts at scale. Their multi-operation, high-speed capabilities make them essential in industries where tolerances are tight, geometries are intricate, and the volume of parts is high. Below, we’ll explore some of the key industries that rely on Swiss lathes to deliver high-quality components with minimal downtime.
Aerospace Industry
In aerospace, components must meet stringent quality standards, as even the smallest defects can affect performance and safety. Swiss lathes are often used to machine critical parts such as turbine blades, fasteners, housings, and connectors, all of which require tight tolerances and high reliability. These machines can produce parts with excellent surface finishes and superior dimensional accuracy, which is essential in aerospace applications. Their ability to handle materials like titanium and special alloys further enhances their importance in this industry.
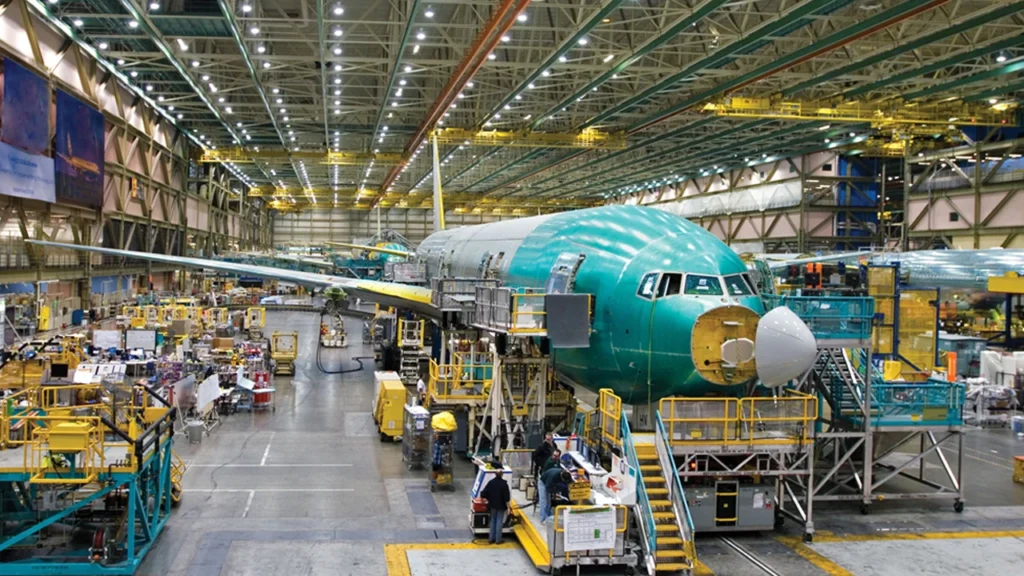
Medical Device Industry
Swiss lathes are indispensable in the medical device industry, where small and highly complex components are required for implants, surgical instruments, and diagnostic devices. Parts such as bone screws, guidewires, needles, and stents often need to meet rigorous standards of precision and biocompatibility. The Swiss lathe’s ability to produce these parts with micron-level accuracy and minimal surface imperfections ensures their functionality and safety in medical procedures. Additionally, the continuous production capabilities of Swiss lathes support high-volume medical device manufacturing.
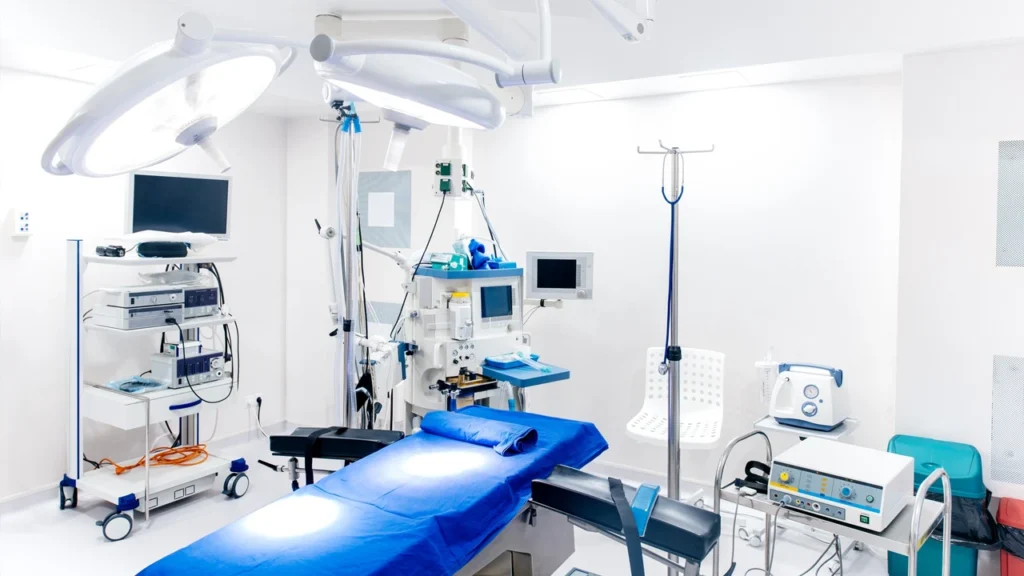
Automotive Industry
The automotive industry also benefits significantly from Swiss lathes, particularly in the production of small, high-precision parts that are integral to vehicle performance. Swiss-type machines are used to manufacture components like fuel injectors, brake components, valve parts, and connectors. The ability to efficiently produce these small, intricate components while maintaining stringent tolerances is vital in ensuring the reliability of automotive systems. Swiss lathes are also able to handle a wide range of materials, from lightweight alloys to hardened steels, making them versatile for various automotive applications.
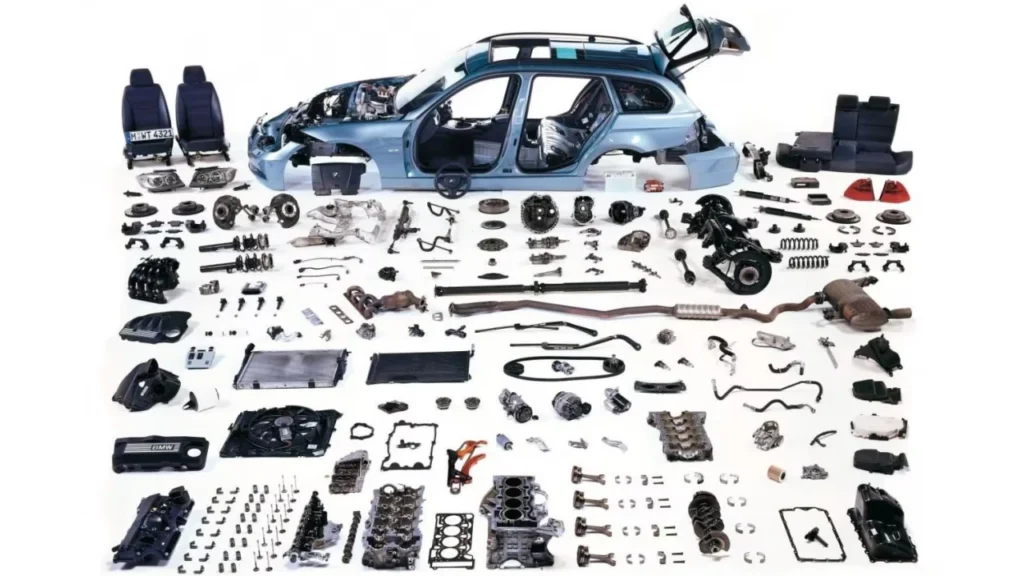
Electronics and Precision Components
Swiss lathes play a key role in the electronics industry, particularly in the manufacturing of connectors, housings, and microcomponents that require high precision and fine features. The demand for smaller, more powerful electronics has driven the need for components that are manufactured with extreme accuracy. Swiss lathes are capable of producing tiny, complex parts such as connectors for mobile devices, circuit board components, and microelectromechanical systems (MEMS) with high repeatability and efficiency. Their ability to perform multiple operations in one cycle is especially advantageous in producing high-volume, small-diameter components for consumer electronics.
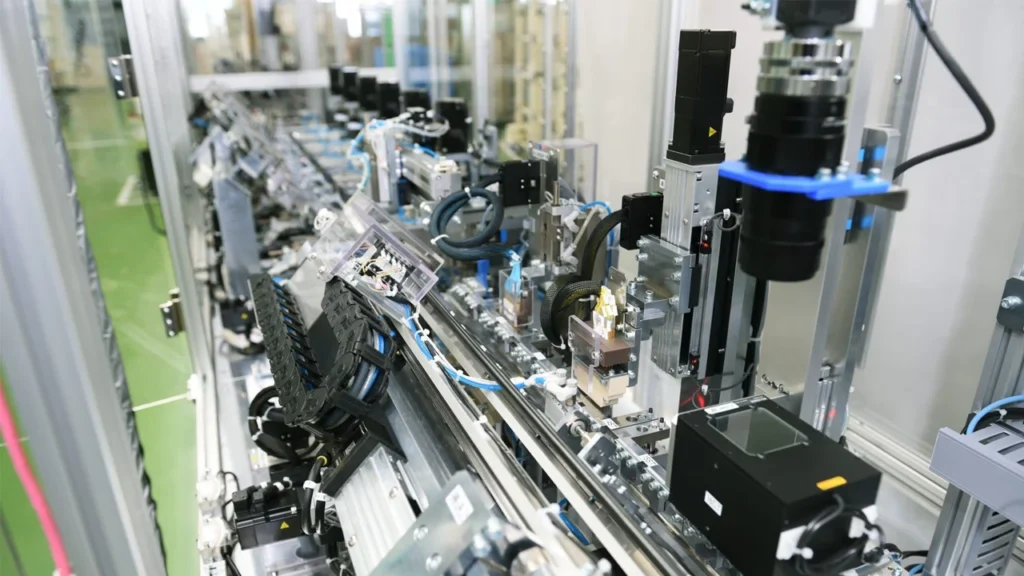
Defense Industry
In the defense sector, Swiss lathes are used to produce critical components for weapons systems, communication devices, and military vehicles. The need for high-strength, high-precision components that can withstand extreme conditions makes Swiss-type machines the perfect solution. Components such as missile guidance systems, launchers, and ammunition casings often require the type of dimensional accuracy and surface quality that Swiss lathes can provide. The machines’ versatility in handling a wide range of materials, including high-strength alloys, is another reason they are essential in defense manufacturing.
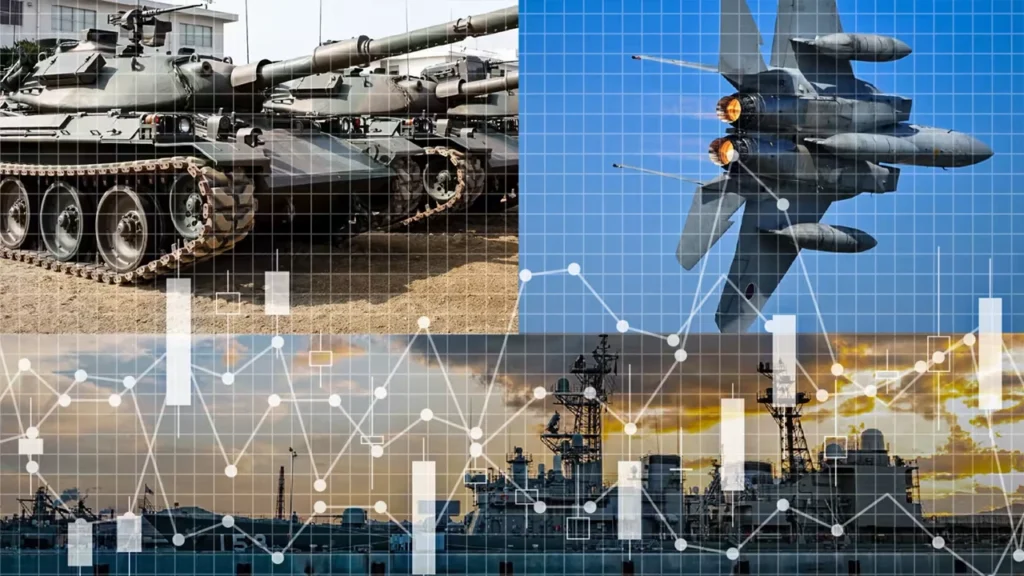
Oil and Gas Industry
The oil and gas industry also relies on Swiss lathes for the production of complex, durable parts used in drilling and extraction equipment. Components such as valves, couplings, fittings, and pumps must be able to withstand high pressures, corrosive environments, and harsh conditions. Swiss lathes are well-suited for machining these components with the required precision and strength. Their ability to produce small, intricate parts with high repeatability makes them an ideal choice for the oil and gas sector, where component failure is not an option.
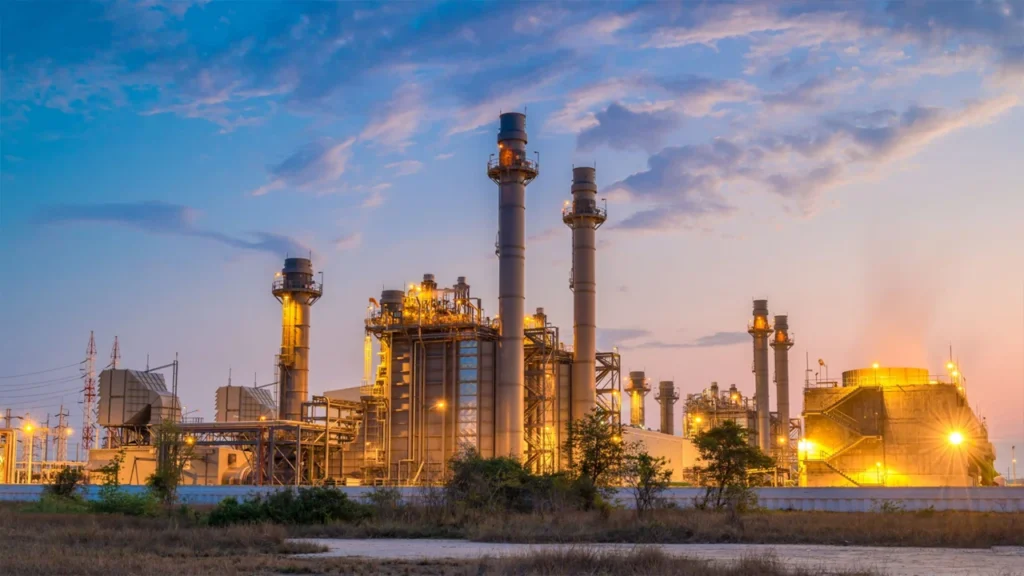
In conclusion, Swiss lathes are highly versatile machines that serve a broad range of industries. Their ability to machine small, complex parts with micron-level accuracy, combined with their ability to handle a wide variety of materials, makes them indispensable in industries where precision and high performance are paramount. Whether it’s in aerospace, medical, automotive, electronics, defense, or oil and gas, Swiss lathes continue to drive innovation and productivity in critical manufacturing sectors.
Advantages of Using a Swiss Lathe
Swiss lathes offer a unique set of advantages that make them the go-to solution for machining small, high-precision parts in industries where quality, speed, and consistency are crucial. The following outlines the key benefits of using a Swiss lathe in your manufacturing operations.
High Precision and Consistency
One of the standout advantages of Swiss lathes is their ability to maintain high precision across large production runs. Thanks to the close support provided to the material by the guide bushing and the synchronized movement of the spindles and tools, Swiss lathes can consistently produce parts with tight tolerances, often within microns. This level of accuracy is essential in industries like aerospace, medical devices, and electronics, where even the smallest deviation can result in failure. Swiss lathes’ design minimizes the risk of deflection and vibration, further enhancing the overall precision of the machining process.
Increased Efficiency and Productivity
Swiss lathes are engineered for continuous, high-speed production. Their ability to perform multiple operations—such as turning, drilling, milling, and threading—within a single setup significantly reduces cycle times. Unlike traditional CNC lathes, which require multiple setups and transfers between machines, Swiss lathes allow for uninterrupted operations, reducing overall production time. This makes them ideal for high-volume production of small parts where time efficiency and productivity are key factors in maintaining cost-effectiveness.
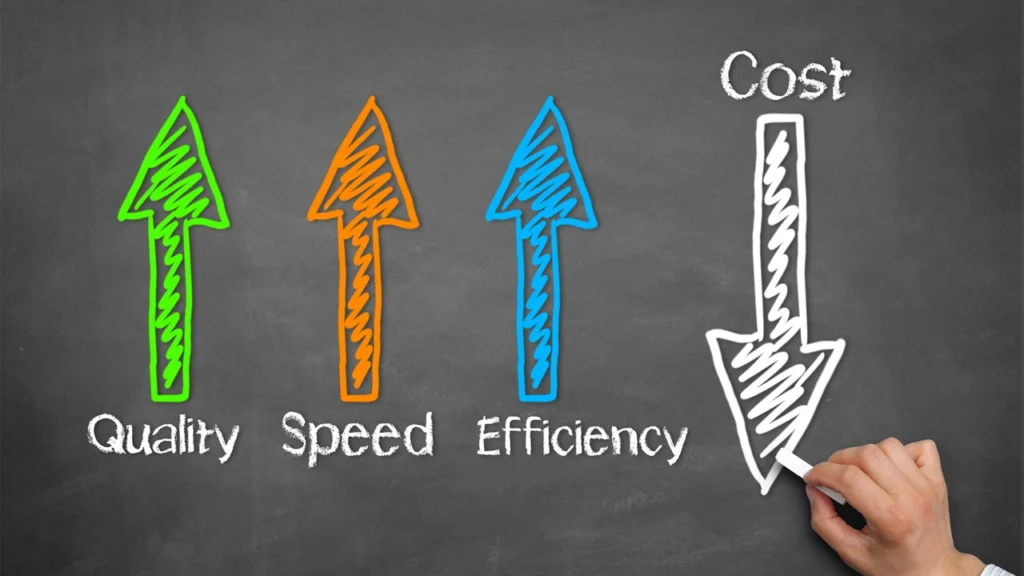
Versatility for Diverse Applications
Swiss lathes excel at machining a wide variety of parts and materials, offering versatility that is unmatched by other machines. They can process small-diameter components with complex geometries, whether those parts are made from metals, plastics, or composite materials. Additionally, the machine’s ability to perform multiple operations in a single cycle makes it suitable for custom parts production where specialized features such as grooves, threads, or internal channels are required. This versatility allows Swiss lathes to be used across a broad spectrum of industries, from aerospace to medical devices, and automotive to electronics.
Reduced Labor Costs and Manual Intervention
Swiss lathes are designed to operate with minimal manual intervention. With integrated automation features such as automated bar feeders, chip conveyors, and coolant management systems, Swiss lathes can operate in lights-out manufacturing environments. This means they can run unattended for extended periods, reducing the need for manual labor and allowing manufacturers to maximize machine uptime. The reduced dependency on operators translates to lower labor costs and enhanced operational efficiency, making Swiss lathes a highly cost-effective option in mass production scenarios.
Improved Safety and Operator Convenience
Safety is always a top concern in any industrial setting, and Swiss lathes offer several features that help enhance safety and improve the working environment. With automated functions like part feeding, tool changes, and chip removal, operators are less likely to be exposed to the hazards associated with manual part handling and machine setup. Additionally, many Swiss lathes are designed with user-friendly interfaces that make it easier for operators to monitor the machine’s performance and make adjustments as needed. This improved ergonomics and ease of use reduce operator fatigue and minimize the risk of accidents.
Cost-Effectiveness in Mass Production
While Swiss lathes represent a significant upfront investment, they are incredibly cost-effective in high-volume manufacturing environments. The ability to perform multiple operations in a single cycle reduces the need for multiple machines, setups, and fixtures. Over time, this not only cuts labor and tooling costs but also increases production throughput. The efficiency gains, combined with the high precision and low scrap rate, make Swiss lathes a great investment for manufacturers looking to produce small, complex parts at scale without compromising on quality.
Ability to Perform Multi-Axis Machining
Swiss lathes are equipped with multi-axis control, allowing for highly complex part geometries to be machined without the need for re-fixturing or repositioning. This multi-axis capability enables the machine to perform operations such as 3D contouring, cross-drilling, and off-center milling with high accuracy and minimal setup time. For manufacturers producing intricate or multi-featured parts, the Swiss lathe’s multi-axis flexibility is a game-changer, providing both precision and versatility in a single machine.
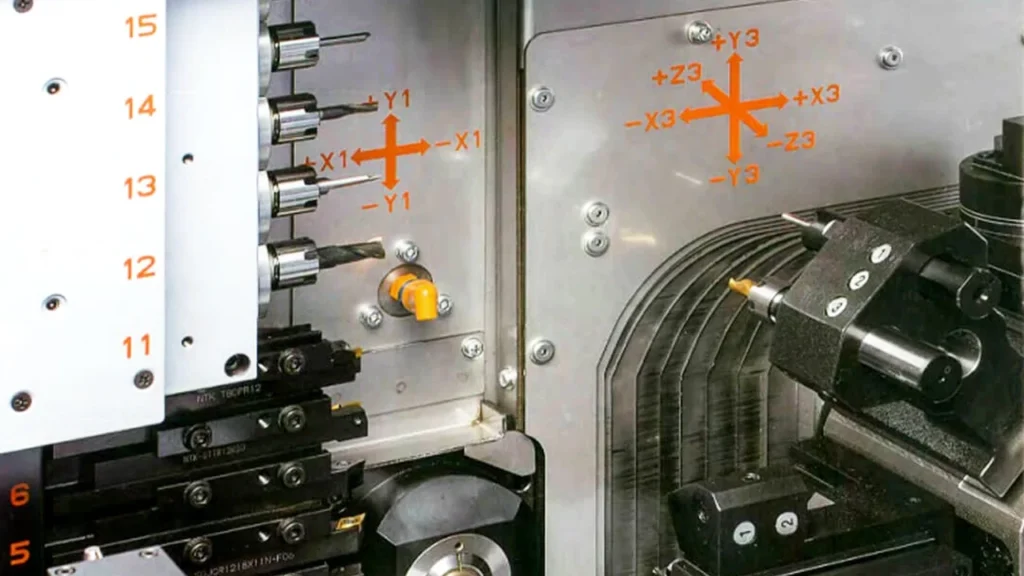
Scalability for Future Production Needs
As demand increases or design specifications change, Swiss lathes can easily scale up to meet production needs. Whether through upgrading CNC software, adding additional tool stations, or enhancing automation, these machines are designed with scalability in mind. The modular design and advanced control systems allow Swiss lathes to adapt to new part designs or higher production volumes, making them a future-proof solution for growing manufacturing businesses.
Environmentally Friendly and Energy Efficient
Swiss lathes are also designed with energy efficiency in mind. The automated systems and advanced drive technologies used in these machines help reduce energy consumption by optimizing machine cycles and minimizing idle times. Additionally, by reducing material waste and increasing production efficiency, Swiss lathes contribute to sustainability goals by lowering overall environmental impact. For companies looking to improve their energy usage and reduce carbon footprints, Swiss lathes are a highly effective solution.
In conclusion, Swiss lathes are a powerful tool for any high-precision, high-volume manufacturing process. Their ability to produce small, intricate parts with high accuracy, combined with their efficiency, versatility, and low operational costs, makes them an invaluable asset across many industries. From reducing labor costs to improving safety and maximizing productivity, the Swiss lathe continues to prove itself as an indispensable machine for precision manufacturing.
Challenges and Limitations of Swiss Lathes
While Swiss lathes offer numerous advantages in precision machining, they also come with certain challenges and limitations that manufacturers need to be aware of. Understanding these drawbacks is crucial when deciding whether a Swiss lathe is the right solution for a particular application. In this section, we will explore some of the common challenges and limitations associated with Swiss lathes.
High Initial Investment
One of the most significant drawbacks of Swiss lathes is their high initial cost. The machines themselves, along with the necessary automation equipment (e.g., bar feeders, chip conveyors), can be a large financial investment, which may not be feasible for every manufacturer—especially those working with lower-volume or prototype parts. The upfront costs are higher compared to traditional CNC lathes, which can make Swiss lathes less appealing for businesses with limited capital or those that produce low-volume runs.
However, the long-term ROI can be exceptional, especially for high-volume production. The efficiency, precision, and reduced labor costs offered by Swiss lathes can offset the initial investment over time, particularly in industries with high-volume needs like medical devices, automotive, and aerospace.

Limited Flexibility for Larger Parts
Swiss lathes are optimized for small-diameter, precision machining, and they excel in the production of long, slender parts with tight tolerances. However, they are generally not suited for machining larger parts with more complex geometries that require extensive milling or heavy-duty turning. Traditional CNC lathes or machining centers are typically better suited for handling larger parts with a wider range of dimensions and more intricate machining needs.
For manufacturers working with larger parts or parts that require extensive milling, Swiss lathes may not be the best option. In such cases, a machining center or traditional CNC lathe would be a more efficient and cost-effective solution.
Complex Setup and Tooling
Swiss lathes require specialized tooling and precise setups to achieve optimal performance. The tool holders, guide bushings, and tool posts must be set up and adjusted correctly to ensure that parts are machined accurately and consistently. For manufacturers who are not familiar with Swiss lathes, this can lead to a learning curve when configuring the machine for new parts or applications.
Additionally, the machine’s tooling and setup complexity can also increase the time and cost associated with changing over from one part type to another. While Swiss lathes are excellent for high-volume, repetitive production, they may require additional time and expertise when switching between different part types, which can be a limitation in low-volume, multi-variety environments.
Tool Life and Maintenance
Swiss lathes have many moving parts and components that require regular maintenance and upkeep. The guide bushings, spindles, and tools must be carefully monitored for wear, and the coolant and lubrication systems must be kept in top condition to ensure optimal performance. If proper maintenance is not performed, it can result in decreased accuracy, increased downtime, and higher operational costs.
Additionally, tool life can be a concern, especially when machining tough or abrasive materials. Tools on a Swiss lathe may wear faster than on traditional CNC machines, requiring more frequent tool changes and higher tool costs. As such, manufacturers need to factor in tooling costs and maintenance as part of their total cost of ownership when considering Swiss lathes.
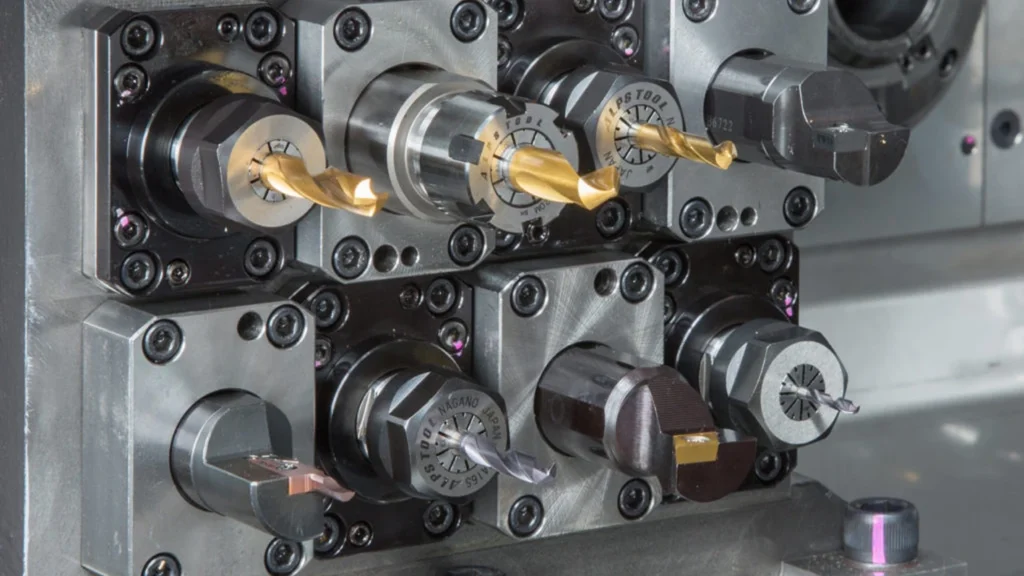
Not Ideal for Low-Volume Prototyping
Although Swiss lathes are ideal for high-volume production, they may not be the most suitable option for low-volume prototyping. The setup times and tooling costs associated with Swiss lathes may not justify the investment for producing just a few parts, especially if the part designs are not final or are subject to frequent changes. Traditional CNC lathes or machining centers are often more suitable for prototyping or small-batch production, where flexibility and quick setup are more important than the efficiency of high-volume production.
For prototyping, the flexibility of traditional CNC machines and the ability to easily reconfigure setups make them a more cost-effective and versatile solution for low-volume runs.
Operator Skill Requirements
Swiss lathes require highly skilled operators to program and manage the machines effectively. The complexity of the multi-axis control systems, advanced tooling, and machine setup means that operators need a high level of expertise to get the best results. As such, businesses may need to invest in training or hire skilled operators, which can increase labor costs.
This reliance on skilled operators can be a limiting factor for smaller shops or businesses that lack the necessary workforce or resources to operate Swiss lathes to their full potential.
Conclusion: Weighing the Pros and Cons
Swiss lathes are an indispensable tool for high-precision machining of small, complex parts. They excel in high-volume production and offer outstanding accuracy and stability, particularly for parts with tight tolerances and long, slender geometries. However, they come with high initial costs, setup complexity, and maintenance requirements. Additionally, Swiss lathes are not the ideal solution for large, complex parts, low-volume prototyping, or applications requiring heavy milling.
For manufacturers focused on producing small, high-precision parts in medium to high volumes, Swiss lathes provide a highly effective solution that maximizes productivity and minimizes downtime. However, businesses must carefully consider the machine’s limitations and evaluate whether it fits within their specific manufacturing needs and budget.
How to Choose the Right Swiss Lathe
Choosing the right Swiss lathe for your manufacturing needs can be a complex decision, but it is critical to ensure that you get the best performance and value for your specific requirements. There are several key factors to consider when selecting a Swiss lathe, including part tolerances, machine specifications, automation capabilities, and future scalability. This section will walk you through the essential aspects to keep in mind when choosing the right machine for your shop.
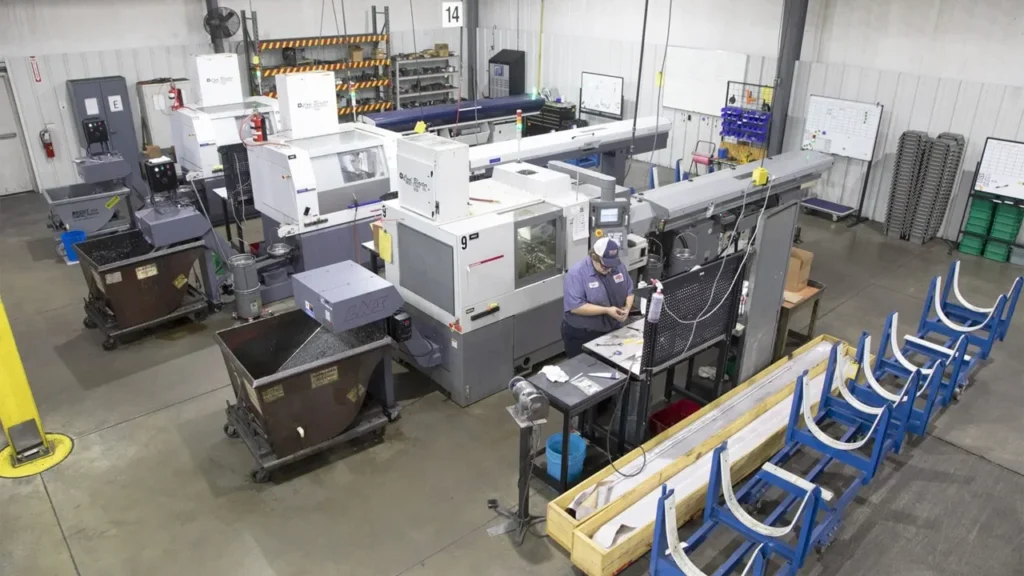
Define Your Part Tolerance and Surface Goals
Before selecting a Swiss lathe, it’s essential to clearly define the tolerances and surface finish requirements of the parts you plan to manufacture. Swiss lathes are known for their ability to produce parts with micron-level precision, but the degree of accuracy needed for your specific application will affect the choice of machine.
- If you require tight tolerances (e.g., ±0.005mm or tighter), you will need a machine that provides rigid support and precise tool positioning.
- Additionally, consider the surface finish you need. Swiss lathes can achieve high-quality finishes, often in the range of Ra 0.1 μm or better, but this may require additional tooling or specific setup adjustments.
By clearly understanding the precision and surface quality required for your parts, you can narrow down the machines that can meet your production standards.
Match Machine Axis and Tooling Specs to Your Part Design
The machine axes and tooling capabilities are another critical factor in choosing the right Swiss lathe. The number of axes and the types of tools available will directly impact the complexity of the parts you can produce.
- Multi-axis machines (e.g., 5-axis Swiss lathes) are ideal for parts with complex geometries or those that require multi-directional cutting. If your parts involve intricate features, multiple angles, or cross-drilling, a machine with advanced multi-axis capabilities will be necessary.
- Tooling specifications also play a significant role. Some parts may require live tooling for operations such as milling or drilling, while others may require a more basic tool setup. Be sure to match the machine’s tooling capacity to the specific operations required by your part design.
Assess Spindle Speed, Bar Diameter, and Guide Bushing Setup
The spindle speed, bar diameter, and guide bushing setup are critical parameters that will determine how well the Swiss lathe can handle your specific part sizes and machining requirements.
- Spindle speed: Swiss lathes are available in different spindle speed ranges. High-speed spindles are better suited for smaller parts, while lower-speed spindles are typically needed for larger, harder materials.
- Bar diameter: Swiss lathes are optimized for small-diameter bar stock, typically up to 32mm in diameter. When selecting a machine, make sure the bar feeder and spindle are capable of handling the size of material you plan to process.
- Guide bushing setup: The guide bushing supports the workpiece during machining, reducing deflection and improving precision. For small, slender parts, a machine with an adjustable or customizable guide bushing is crucial to maintain stability and accuracy.
Make sure the machine you choose is compatible with your specific part sizes and material requirements.
Evaluate CNC Control Software and Automation Support
The CNC control system is the brain of the Swiss lathe, and it plays a significant role in the machine’s overall performance. The software allows you to program and control all aspects of the machining process, so it’s important to choose a machine with a user-friendly, reliable, and advanced CNC system.
- Look for a Swiss lathe with modern CNC controls that offer flexibility in programming and easy integration with your existing systems.
- Some Swiss lathes offer advanced features such as live tool synchronization, real-time error detection, and programming aids that can significantly improve efficiency and reduce errors during production.
In addition, automation support is another important factor. Many Swiss lathes offer automated bar feeders, chip conveyors, and coolant systems that can significantly reduce labor costs and increase production efficiency, especially for high-volume manufacturing.
Review Service, Warranty, and After-Sales Support
The service, warranty, and after-sales support provided by the manufacturer are critical considerations when purchasing a Swiss lathe. Because these machines are highly technical and require regular maintenance, it is essential to have reliable support to keep your machine running smoothly.
- Warranty: Ensure the machine comes with a comprehensive warranty that covers both parts and labor. A strong warranty can provide peace of mind in case something goes wrong.
- Service: Look for manufacturers that offer timely support, ideally with local service teams to minimize downtime in case of machine failure.
- After-sales support: Ensure the manufacturer offers training, technical assistance, and spare parts availability. Having access to fast, reliable support will help minimize any disruptions to your production schedule.
Consider Future Capacity and Modularity
When choosing a Swiss lathe, it’s important to consider your future capacity needs and whether the machine is modular enough to grow with your business. While it’s essential to meet your current production requirements, you should also ensure that the machine can handle increased demand or more complex parts in the future.
- Scalability: Consider machines that can be easily upgraded to accommodate larger volumes, additional tool stations, or higher precision.
- Modularity: Some Swiss lathes offer modular designs, allowing you to add extra spindles, tool stations, or axes as needed. This ensures that your machine can evolve as your production needs change.
By selecting a Swiss lathe that is flexible and scalable, you can avoid the need for expensive upgrades or replacements down the line.
Maintenance and Best Practices
Regular maintenance is essential for the long-term performance and reliability of Swiss lathes. Proper care ensures precision, reduces downtime, and enhances the machine’s longevity.
Daily and Weekly Machine Care
- Daily Maintenance: Start by inspecting the machine for any debris or obstructions that could interfere with the cutting process. Check the coolant levels and tool functionality, ensuring that there is no contamination or clogging in the coolant system. Clean any exposed surfaces to avoid material buildup that could affect part quality.
- Weekly Maintenance: Perform a more detailed inspection of the machine’s components, including checking tooling wear, ensuring the spindle is properly lubricated, and confirming that the machine’s alignment is accurate. Take time to clean the bar feeder and ensure chip conveyors are functioning smoothly to avoid blockages.
Toolholder and Live Tool Maintenance
- Toolholders: Toolholders must be kept clean and secure to prevent any machining errors. Regularly check for wear or damage to the tool clamping mechanism, ensuring that the tools are held securely and are positioned correctly for accurate cuts.
- Live Tools: Live tooling often experiences higher wear than stationary tools due to its constant movement. Lubrication is essential to maintain smooth operation and prevent overheating. Regularly inspect the live tools for vibration or misalignment, as any issue here can directly impact part quality.
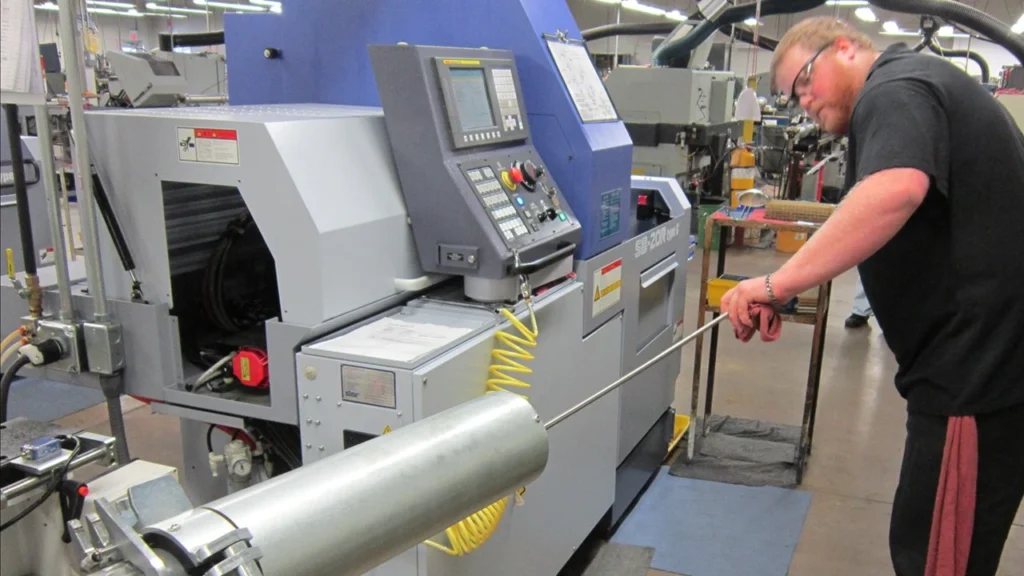
Spindle and Guide Bushing Calibration
- Spindle Calibration: The spindle is the heart of the Swiss lathe’s precision, so regular checks for wear and alignment are crucial. Inspect the spindle bearings and the tool positioning to ensure they are in optimal condition. A well-maintained spindle helps maintain high rotational accuracy and smooth operation, which is critical for tight-tolerance machining.
- Guide Bushing Calibration: The guide bushing helps reduce deflection and vibration during machining, particularly for long or slender parts. Periodically check the bushing’s alignment and condition, and recalibrate if necessary to maintain part accuracy. A well-calibrated guide bushing ensures that parts are machined without distortion, especially for small, delicate components.
Chip and Coolant Management Tips
- Chip Removal: Efficient chip management is key to maintaining clean and accurate machining. Ensure that chips are effectively removed from the cutting area during each operation. Blockages in the chip conveyor or buildup of chips on the machine can lead to tool damage, part defects, and overheating. Regularly check the chip conveyor to ensure smooth removal.
- Coolant Management: Regularly monitor the coolant quality and flow rate. Contaminated coolant or improper cooling can increase tool wear and reduce surface finish quality. Use filtration systems to keep the coolant clean and replace it when necessary. Proper coolant management helps maintain the temperature of the cutting tool and ensures consistent part quality throughout long production runs.
Preventive vs Predictive Maintenance for Swiss Lathes
- Preventive Maintenance: This approach involves regular, scheduled checks and adjustments. For Swiss lathes, preventive maintenance typically includes daily and weekly inspections of critical components like the spindle, guide bushing, and toolholders. Routine tasks include lubrication, tool alignment, and coolant system cleaning. Preventive maintenance helps prevent machine failure by addressing small issues before they become bigger problems.
- Predictive Maintenance: Predictive maintenance involves the use of real-time monitoring tools to track the condition of machine components, such as spindle temperature, vibration, and tool wear. By analyzing this data, you can predict when certain components are likely to fail and schedule maintenance accordingly, thus reducing unplanned downtime. This approach can extend the life of components and prevent costly repairs by addressing issues before they cause significant damage.
Future Trends in Swiss-Type CNC Lathes
As technology continues to evolve, Swiss-type CNC lathes are becoming more advanced, integrating cutting-edge innovations that enhance their performance, efficiency, and capabilities. In this section, we’ll explore the key trends shaping the future of Swiss lathes and how these developments are changing the landscape of precision manufacturing.
AI-Enhanced Toolpath Optimization and Wear Monitoring
One of the most exciting developments in Swiss lathes is the integration of Artificial Intelligence (AI) to improve toolpath optimization and wear monitoring. AI-driven algorithms can now analyze complex machining tasks in real time, optimizing cutting paths for maximum efficiency and minimum material waste. This leads to better surface finishes, improved cycle times, and reduced tool wear.
Additionally, AI can monitor tool condition and predict wear patterns, automatically adjusting cutting parameters or recommending tool changes before problems arise. This predictive maintenance approach can significantly reduce machine downtime and increase overall productivity by preventing unexpected tool failures.
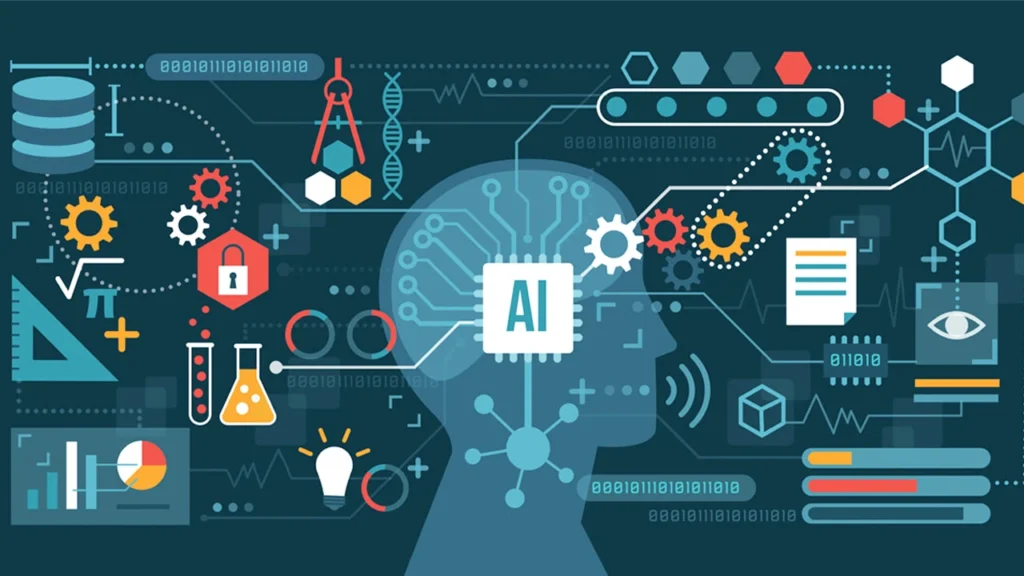
Integration with Digital Twin and Simulation
The Digital Twin concept is gaining momentum in Swiss lathes. A Digital Twin is a virtual replica of a physical machine, which allows manufacturers to simulate machining operations and predict potential issues before they happen. By integrating this technology with Swiss lathes, manufacturers can visualize toolpaths, monitor real-time performance, and perform tests on virtual models, ensuring that each machining step is optimized for precision and efficiency.
Simulation also plays a critical role in reducing material waste and setup time. Manufacturers can experiment with different machining strategies in a virtual environment, analyzing the results before applying them in real-world production. This integration enables manufacturers to make better decisions, optimize production schedules, and maintain high-quality standards with greater confidence.
Multi-Material and Hybrid Machining Capabilities
Swiss lathes are evolving to handle a broader range of materials, including composite materials, ceramics, and advanced alloys. This shift is driven by industries such as aerospace, medical, and automotive, which demand the ability to machine parts from multiple materials in a single setup.
The trend towards hybrid machining—combining additive and subtractive processes—allows Swiss lathes to 3D print parts with intricate structures or add features to existing components while performing traditional machining operations. This combination of processes allows for greater flexibility, increased design freedom, and more efficient production of complex parts with unique material requirements.
Cobots and Modular Automation for Lights-Out Operation
The use of collaborative robots (cobots) and modular automation is transforming Swiss lathe operations. Cobots, designed to work alongside human operators, provide an additional layer of flexibility in automating various tasks, such as tool changes, part transfers, and quality inspections. This integration helps reduce human labor while ensuring that machines operate continuously without disruption.
Modular automation systems further enhance lights-out manufacturing by enabling Swiss lathes to run unattended for long periods—such as overnight or across multiple shifts. With automated part loading, unloading, and chip management, Swiss lathes can operate autonomously, improving production efficiency and reducing labor costs. This trend is especially valuable for high-volume production environments where 24/7 operation is required.
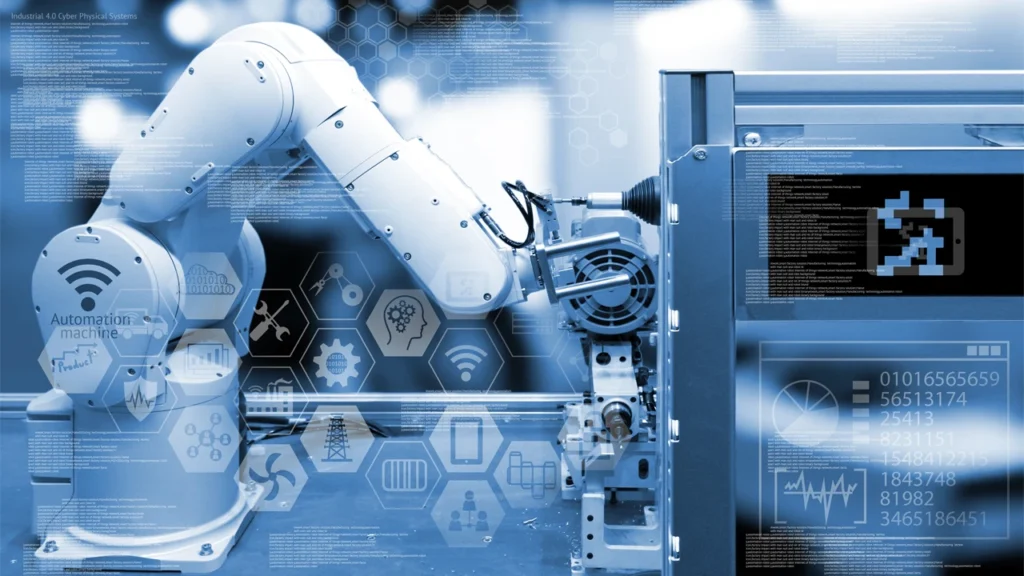
Smart Bar Feeders and Chip Management Systems
The future of Swiss lathe automation includes the development of smart bar feeders and advanced chip management systems. Smart bar feeders are equipped with sensors and data analytics capabilities, allowing them to monitor the material’s condition and adjust feeding speed accordingly. This enhances machining efficiency by reducing interruptions and ensuring that parts are fed smoothly throughout the process.
Similarly, advanced chip management systems are being integrated into Swiss lathes to optimize chip removal and prevent clogs. These systems help to automatically sort and manage chips based on material type, improving workflow and reducing the risk of tool damage. As a result, Swiss lathes can maintain optimal cutting conditions, minimize downtime, and reduce the need for manual intervention.
Sustainability and Energy Efficiency Enhancements
As environmental concerns continue to shape the manufacturing industry, sustainability and energy efficiency have become key focus areas for Swiss lathe manufacturers. New technologies are being implemented to reduce energy consumption and minimize environmental impact, such as energy-efficient motors, optimized cooling systems, and low-energy operation modes.
Additionally, Swiss lathe manufacturers are adopting practices like recycling cutting fluids, reducing material waste, and improving machine designs to make them more eco-friendly. These enhancements not only help companies meet environmental regulations but also lower operational costs and contribute to a greener manufacturing process.
Conclusion
In conclusion, Swiss-type CNC lathes are indispensable tools for producing high-precision, small components with intricate geometries and tight tolerances. Their ability to perform multiple operations within a single setup, combined with cutting-edge technologies like AI-driven optimization, hybrid machining, and advanced automation, makes them an essential asset for industries that demand high efficiency and quality, such as aerospace, medical devices, and electronics.
With these evolving trends, Swiss lathes continue to lead the way in meeting the needs of precision manufacturing. As manufacturers seek to achieve greater accuracy, productivity, and flexibility, the importance of selecting the right Swiss lathe becomes increasingly crucial. Whether considering multi-material machining, automation for lights-out operation, or cutting-edge smart technologies, understanding how these features align with your production goals ensures long-term success.
For those looking to invest in Swiss lathes or CNC solutions, the right partner can make all the difference. At Rosnok, we understand the value of high-precision machinery and offer tailored CNC machine solutions that meet the exacting standards of modern manufacturing. With a focus on providing quality, performance, and long-term support, we aim to deliver machines that not only meet today’s demands but are also prepared for the future of manufacturing.