Have you ever wondered what is a milling machine and why it plays such a vital role in manufacturing? What makes it different from other machine tools, and how does it shape metal, wood, and other materials with incredible precision? Whether you’re an engineer, a machinist, or just curious about machining, understanding milling machines is essential. From crafting intricate parts in aerospace to producing custom components in the automotive industry, milling machines are indispensable in modern production.
A milling machine is a powerful machining tool that uses a rotating cutting tool to remove material from a workpiece with high precision. Unlike lathes, which rotate the workpiece, milling machines hold the material stationary while the cutter moves in multiple directions to create complex shapes. These machines come in various types, including manual, CNC, vertical, and horizontal milling machines, each designed for specific applications in industries such as aerospace, medical, and industrial manufacturing. With precise control over cutting speed, feed rate, and tool selection, machinists can produce intricate workpieces with exceptional accuracy and efficiency.
Milling machines are more than just machining equipment; they are the backbone of precision manufacturing. Whether you’re a beginner looking to explore machining or a professional seeking advanced knowledge, this guide will cover everything you need to know about milling machines, their components, types, and real-world applications. Let’s dive in!
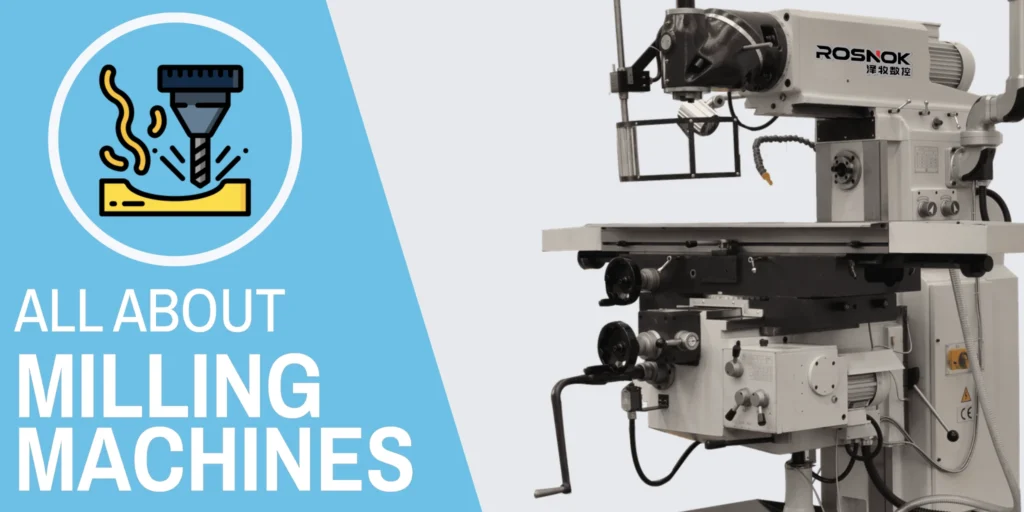
Milling Machine Definition: What is a Milling Machine?
A milling machine is a powerful and precise machining tool used to remove material from a workpiece using a high-speed rotating cutting tool. Unlike a lathe, where the workpiece rotates while the cutting tool remains stationary, a milling machine keeps the workpiece fixed while the cutting tool moves along multiple axes to carve, shape, and refine the material. This unique approach allows for the creation of complex geometries, flat surfaces, grooves, and detailed contours, making milling machines an indispensable tool in precision manufacturing.
Milling machines function by securing the workpiece onto a movable worktable, which can traverse along the X, Y, and Z axes for controlled and highly accurate machining. The rotating cutter interacts with the material, gradually removing excess material to achieve the desired shape. With their ability to perform both rough and fine machining, milling machines are widely utilized in industries that demand high precision, repeatability, and versatility, such as automotive, aerospace, and mold fabrication.
Beyond basic milling, these machines can accommodate a variety of interchangeable tools, including drill bits, boring bars, and tapping tools, allowing for additional processes such as drilling, boring, and thread cutting. This versatility enhances productivity by consolidating multiple machining functions into a single workstation, reducing the need for additional equipment. Available in vertical and horizontal configurations, milling machines offer specialized solutions for various applications, making them essential for crafting non-rotational components, intricate parts, and customized designs with exceptional accuracy and efficiency.
History of Milling Machines: From Manual to CNC
Milling machines have revolutionized manufacturing, evolving from simple hand-operated devices to highly sophisticated CNC-controlled systems. Their ability to shape complex components with precision has made them essential in industries such as automotive, aerospace, and metal fabrication. Let’s take a journey through the key milestones that have defined the evolution of milling technology.
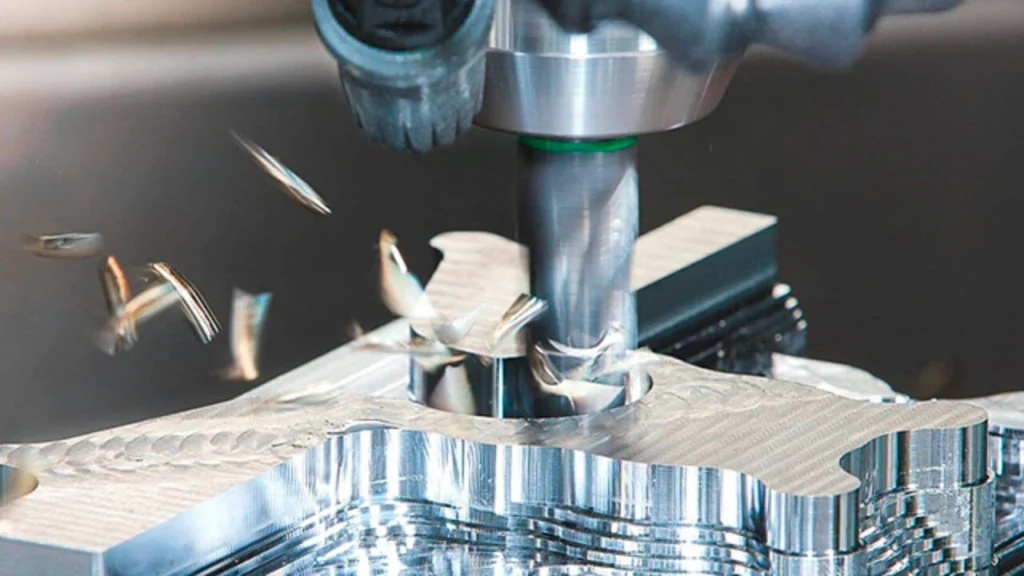
Key Milestones in Milling Machine Development
18th Century: The Birth of Milling Technology
The first milling machines appeared in the late 18th century, designed to improve efficiency and precision in metalworking. These early machines used rotary cutters to shape materials more consistently than traditional hand tools.
1818: Eli Whitney’s Milling Machine
In 1818, American inventor Eli Whitney introduced the first recognizable milling machine, which played a crucial role in producing interchangeable firearm parts. This innovation paved the way for mass production and standardized manufacturing.
19th Century: Industrial Advancements in Milling
During the Industrial Revolution, milling machines became larger, more powerful, and more precise. The development of horizontal and vertical milling machines expanded their capabilities, allowing for more complex and efficient machining processes.
20th Century: The Rise of CNC Milling Machines
By the mid-20th century, the introduction of numerical control (NC) technology led to the development of CNC (Computer Numerical Control) milling machines. This advancement allowed for automated, programmable machining, drastically improving accuracy and production speed.
21st Century: Multi-Axis and AI-Driven Milling
Modern milling machines incorporate 5-axis capabilities, AI optimization, and automated systems, enabling manufacturers to create high-precision components for industries like aerospace, medical devices, and automotive engineering.
How Does a Milling Machine Work? The Operational Workflow
Milling machines are versatile machining tools that remove material from a workpiece using a high-speed rotating cutting tool. Unlike lathes, which rotate the workpiece, milling machines keep the material stationary while the cutting tool moves along multiple axes. This allows for precise milling, shaping, drilling, and finishing of components in various industries, including aerospace, automotive, and medical manufacturing.
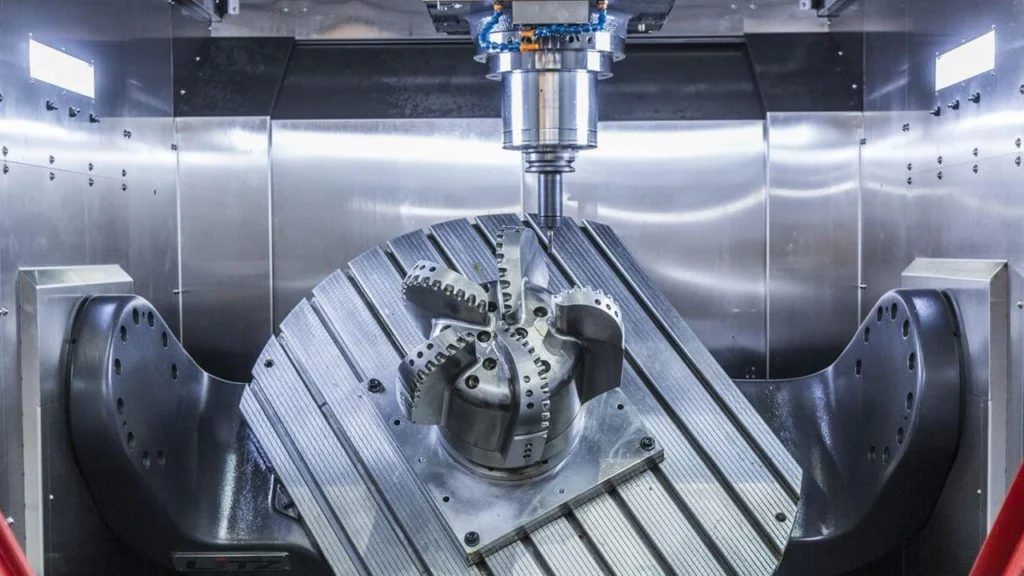
The Milling Process: Step-by-Step Workflow
1. Securing the Workpiece
Before machining begins, the workpiece is firmly clamped onto the worktable. Depending on the type of milling operation, vises, clamps, or fixtures may be used to hold the material in place. In CNC milling, automated setups ensure repeatability and accuracy.
2. Selecting the Right Cutting Tool
Milling machines use a variety of cutting tools, each designed for specific tasks:
- End Mills: Used for general cutting, slotting, and contouring.
- Face Mills: Ideal for flat surface machining.
- Drills & Taps: Used for creating holes and threading.
- Ball Nose Cutters: Suitable for curved surfaces and 3D profiling.
3. Setting the Cutting Parameters
Before machining starts, operators must configure:
- Spindle Speed: Determines how fast the cutting tool rotates.
- Feed Rate: Controls how fast the workpiece moves relative to the cutter.
- Depth of Cut: Defines how much material is removed in a single pass.
In manual milling machines, these settings are adjusted manually, whereas in CNC milling machines, pre-programmed instructions define these parameters.
4. Executing the Milling Operation
Once everything is set, the spindle activates the cutting tool, and the milling operation begins. Depending on the required machining, different movements occur:
- X-Axis: Moves the worktable left and right.
- Y-Axis: Moves the worktable forward and backward.
- Z-Axis: Adjusts the height of the cutting tool.
Advanced multi-axis CNC milling machines include additional rotational axes (A, B, C axes) for more complex machining.
5. Finishing and Inspection
After machining is complete, the finished component is measured and inspected to ensure it meets the required tolerances and surface finish. Many modern CNC milling machines feature automatic probing systems to verify accuracy in real-time.
Why Milling Machines Are So Efficient
- They can create intricate shapes and geometries.
- They handle various materials, including metal, plastic, and composites.
- They support automation and high-precision machining, reducing errors.
Modern milling machines are at the heart of precision manufacturing, offering unparalleled accuracy and efficiency.
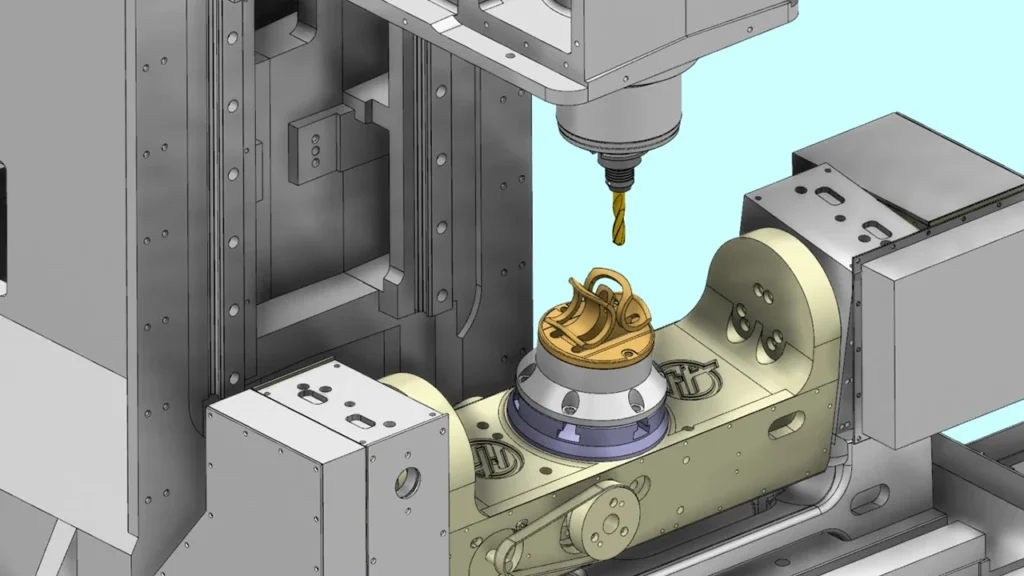
Key Components of a Milling Machine
Milling machines consist of several critical components that work together to achieve high precision machining. Whether manual or CNC-controlled, these parts play a vital role in shaping, drilling, and finishing materials. Understanding these components helps machinists optimize performance, improve efficiency, and ensure accurate machining results.
Main Parts of a Milling Machine
1. Frame & Base
The base provides structural support and stability to the machine. It houses the motor and other essential components, absorbing vibrations during operation. Cast iron or steel construction ensures durability and rigidity, preventing deflection while machining.
2. Worktable
The worktable holds the workpiece securely in place using vises, clamps, or fixtures. It moves along the X and Y axes, allowing the cutting tool to remove material from different angles. In CNC milling machines, automated tool paths control the worktable movement with high precision.
3. Spindle & Spindle Motor
The spindle is the rotating component that holds and drives the cutting tool. It is powered by a spindle motor, which determines the rotational speed (RPM). A higher spindle speed allows for faster cutting and finer surface finishes, making it crucial for CNC and high-speed milling operations.
4. Column & Knee (For Manual Milling Machines)
In manual milling machines, the column supports the spindle, while the knee adjusts the height of the worktable along the Z-axis. These components allow operators to manually control depth and cutting angles.
5. CNC Controller (For CNC Milling Machines)
In CNC milling machines, the CNC controller is the brain of the operation. It processes G-code programming to automate tool movements, cutting speeds, and feed rates, ensuring consistent and precise machining. Modern CNC controllers also support AI-based toolpath optimization for maximum efficiency.
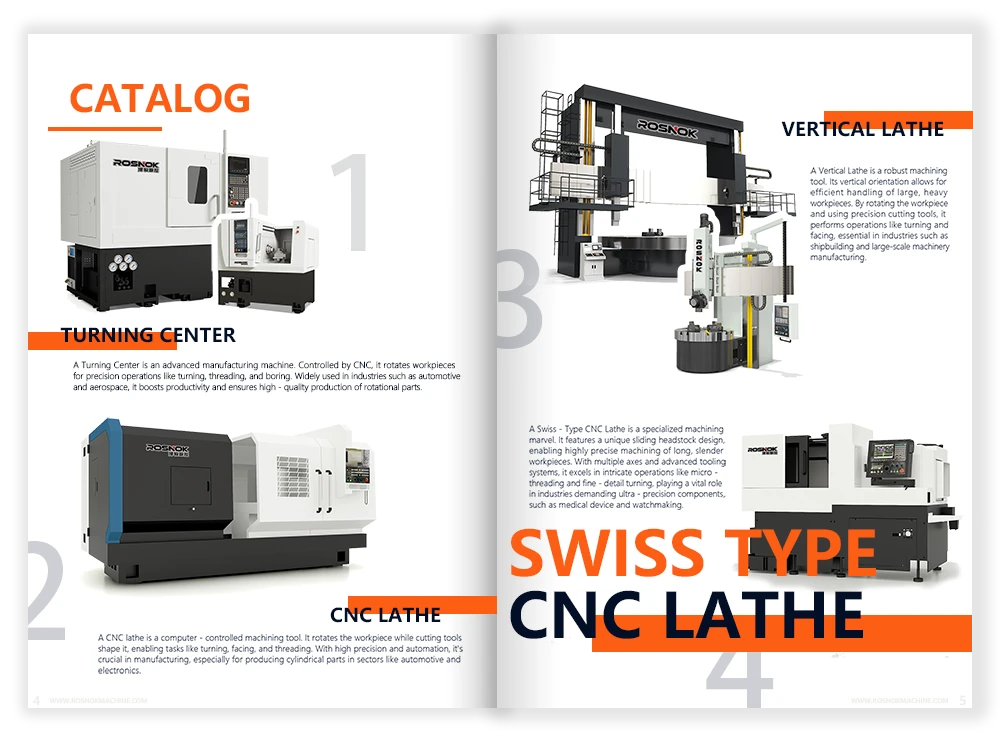
6. Tool Changer & Tool Magazine (For CNC Milling Machines)
Automatic Tool Changers (ATC) store multiple cutting tools and switch them automatically during machining. This feature is crucial for multi-step operations, reducing downtime and increasing productivity. The tool magazine holds tools such as:
- End mills (for general cutting)
- Face mills (for flat surfaces)
- Drills and taps (for hole-making and threading)
7. Feed Mechanism & Guideways
The feed mechanism controls the movement of the worktable in X, Y, and Z directions. Guideways ensure smooth motion, reducing wear and increasing accuracy. Linear guideways in CNC machines provide precise movement and minimal friction, enhancing machining quality.
8. Coolant System
The coolant system prevents overheating by lubricating and cooling the cutting tool and workpiece. It also removes metal chips, improving surface finish and tool life. Common cooling methods include oil-based lubricants and air-blast cooling systems.
Why Understanding Milling Machine Components Matters
- Optimizing each component improves machining efficiency.
- Proper maintenance extends machine lifespan and prevents breakdowns.
- Knowing key parts helps operators troubleshoot performance issues.
Each component of a milling machine works together to ensure precision, stability, and efficiency. Understanding these key parts allows machinists to operate the machine effectively, troubleshoot potential issues, and maximize performance in machining operations.
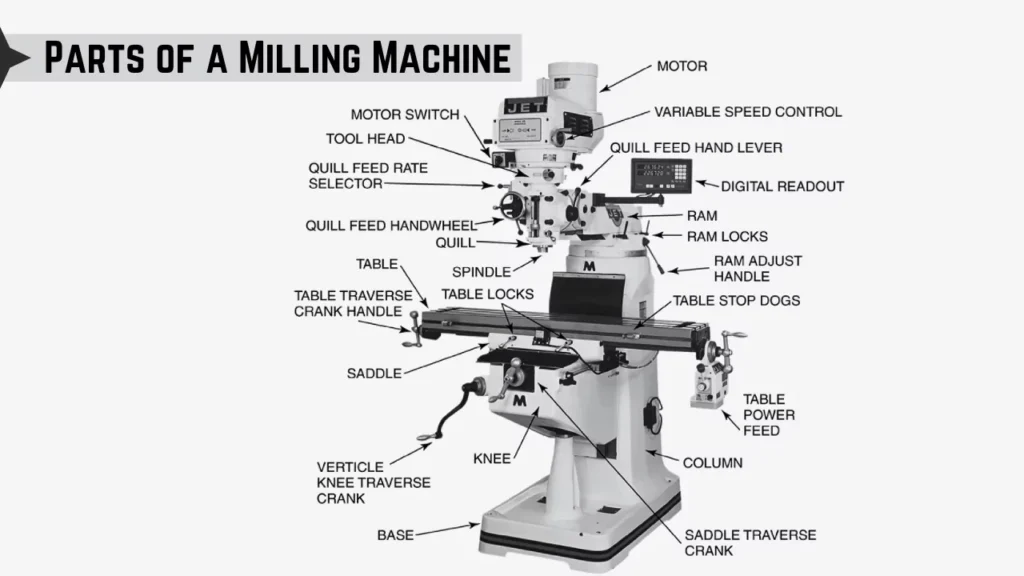
Common Types of Milling Machines
Milling machines are classified based on different design aspects, functionality, and control mechanisms. Each type serves a specific purpose, making it essential to choose the right one for the required machining operation. Below, we explore the major classifications of milling machines based on spindle orientation, the number of axes, structural design, and control method.
Classification Based on Spindle Orientation
The spindle’s position determines how the cutting tool interacts with the workpiece, affecting machining efficiency and accuracy.
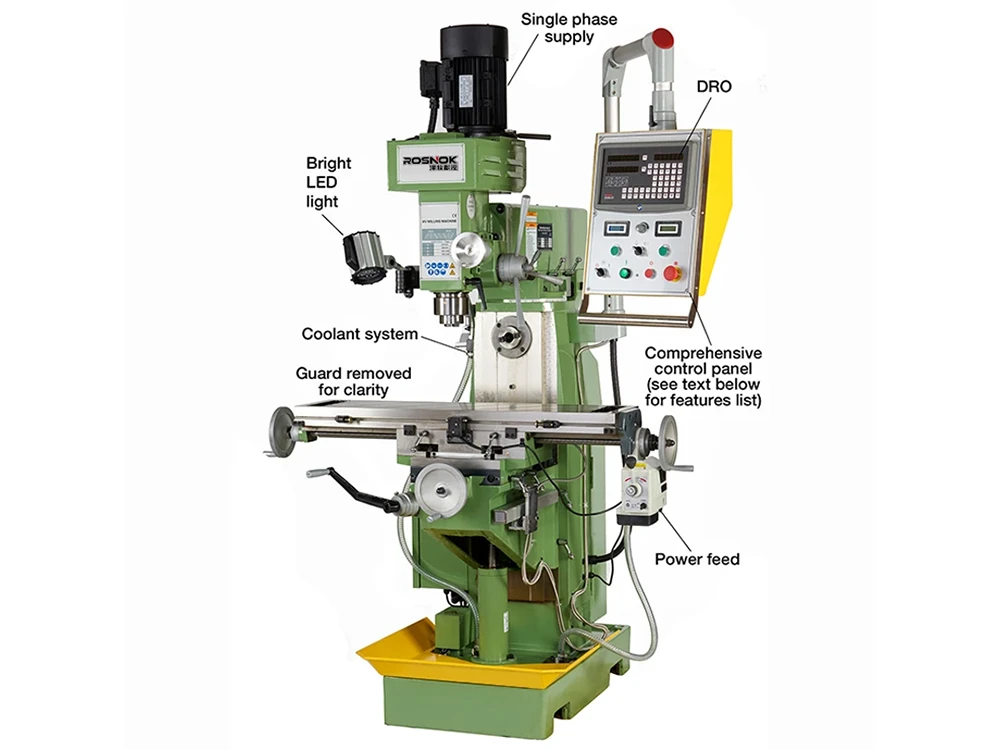
Vertical Milling Machines
In vertical milling machines, the spindle is vertically aligned, allowing the cutting tool to move up and down. These machines are widely used for face milling, drilling, and slotting, offering excellent precision for detailed machining work.
Horizontal Milling Machines
A horizontal milling machine has a spindle positioned parallel to the worktable, enabling side-cutting operations. It is ideal for heavy-duty material removal and is often equipped with multiple cutting tools to improve productivity.
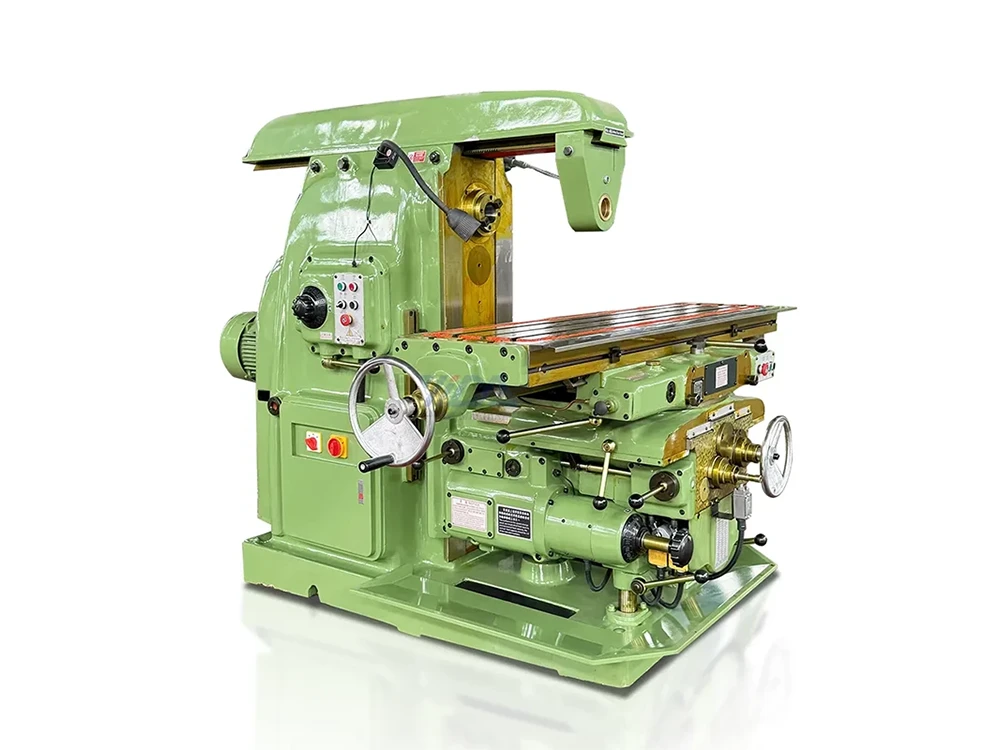
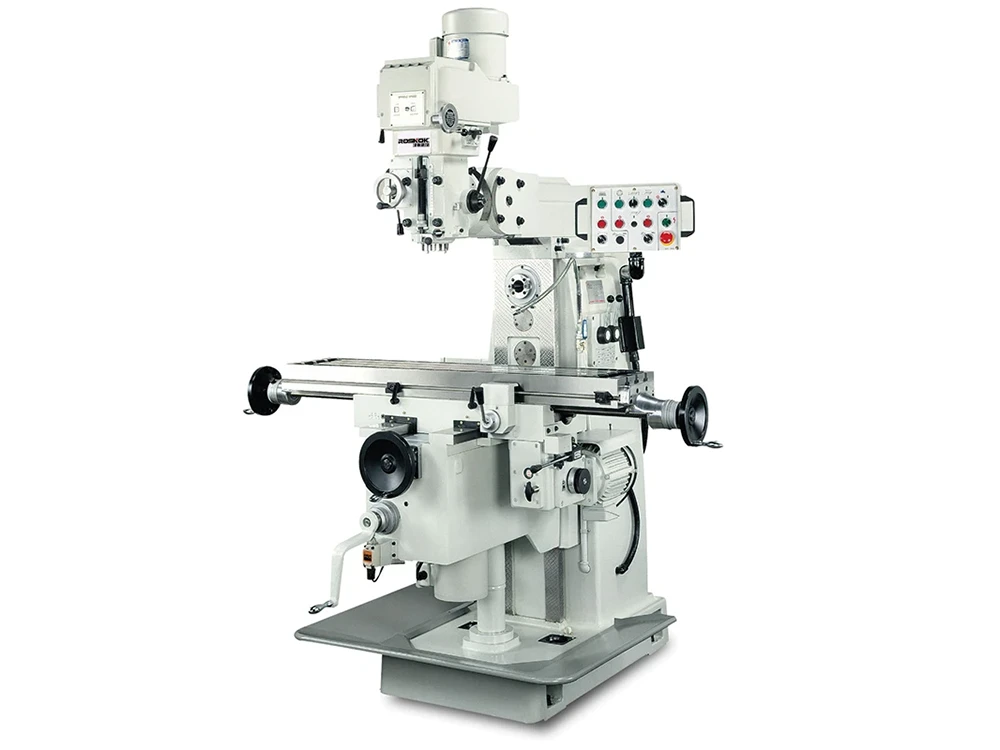
Universal Milling Machines
A universal milling machine integrates both vertical and horizontal milling capabilities. It features a rotating worktable, allowing it to perform angular and helical milling operations for increased flexibility in machining.
Classification Based on the Number of Axes
The number of axes determines how many directions the cutting tool and workpiece can move, influencing machining complexity and precision.
3-Axis Milling Machine
The most common type, a 3-axis milling machine, allows movement along X, Y, and Z axes. It is suitable for basic cutting, drilling, and slotting operations.
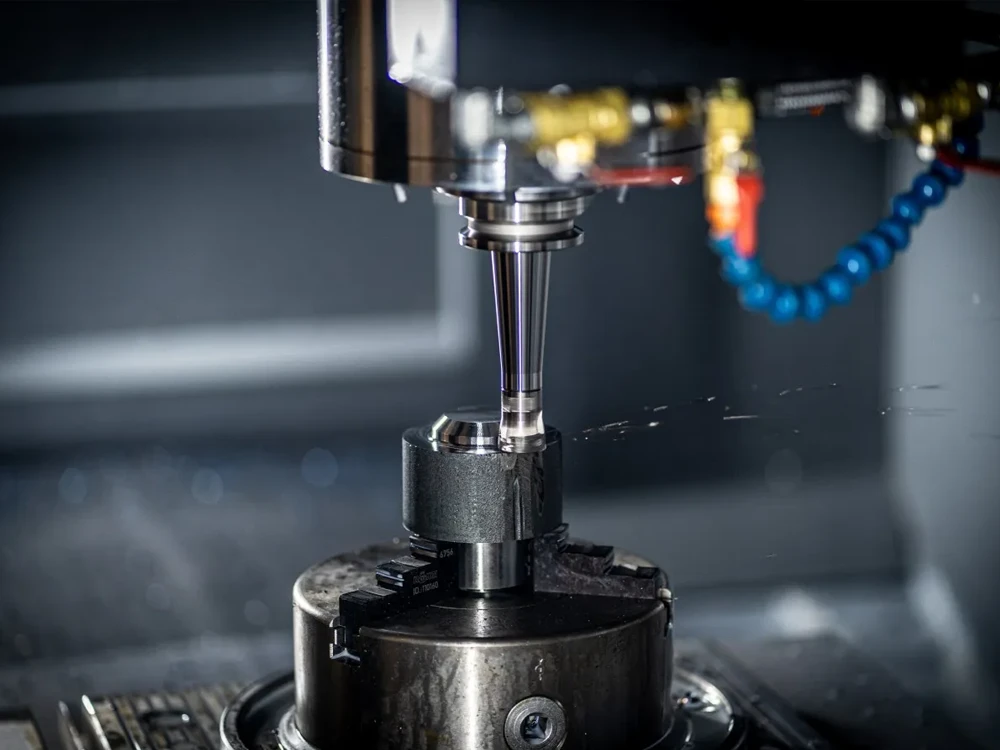
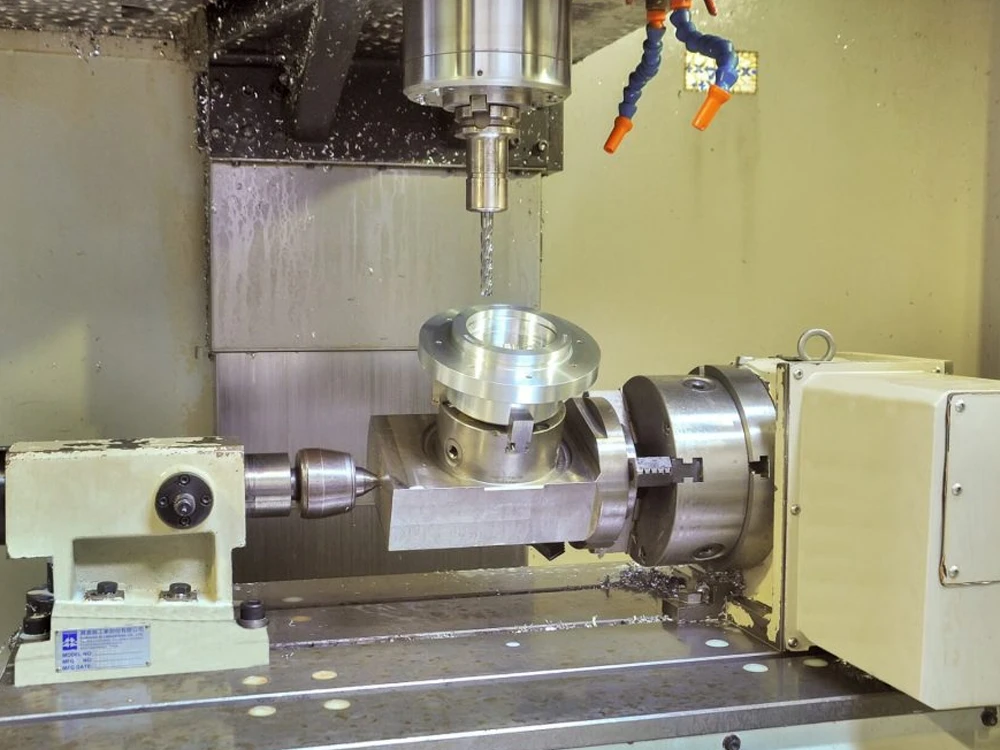
4-Axis Milling Machine
A 4-axis milling machine adds a rotational A-axis, allowing for machining on multiple sides without repositioning the workpiece manually.
5-Axis Milling Machine
A 5-axis milling machine introduces two additional rotation axes (A and B), enabling high-precision machining of complex geometries, such as turbine blades and aerospace components.
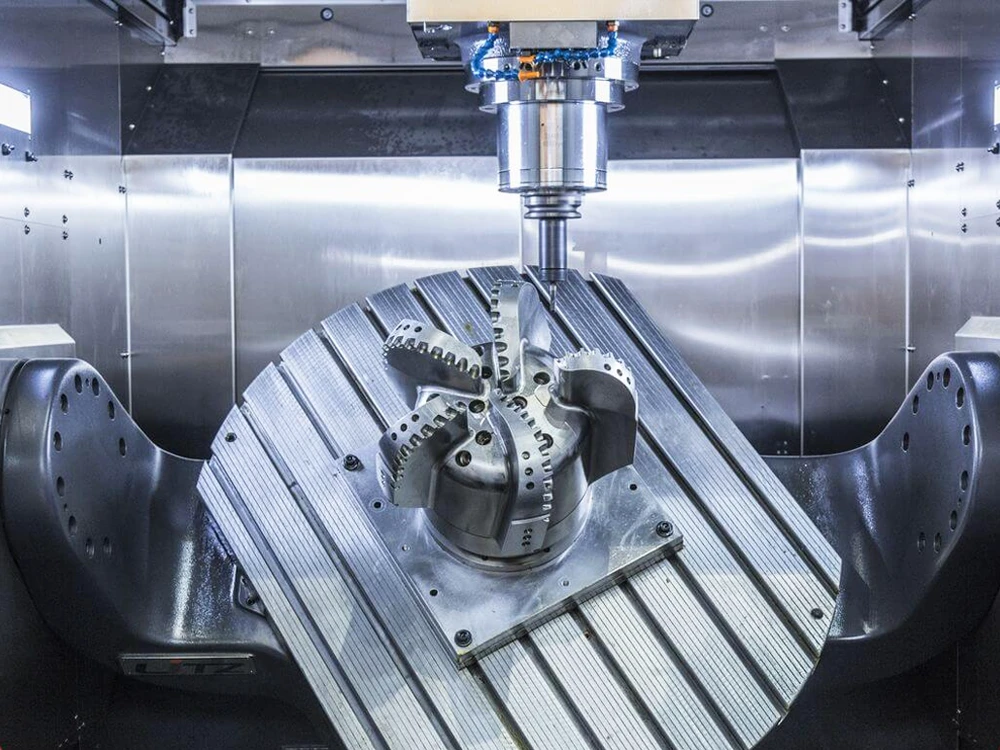
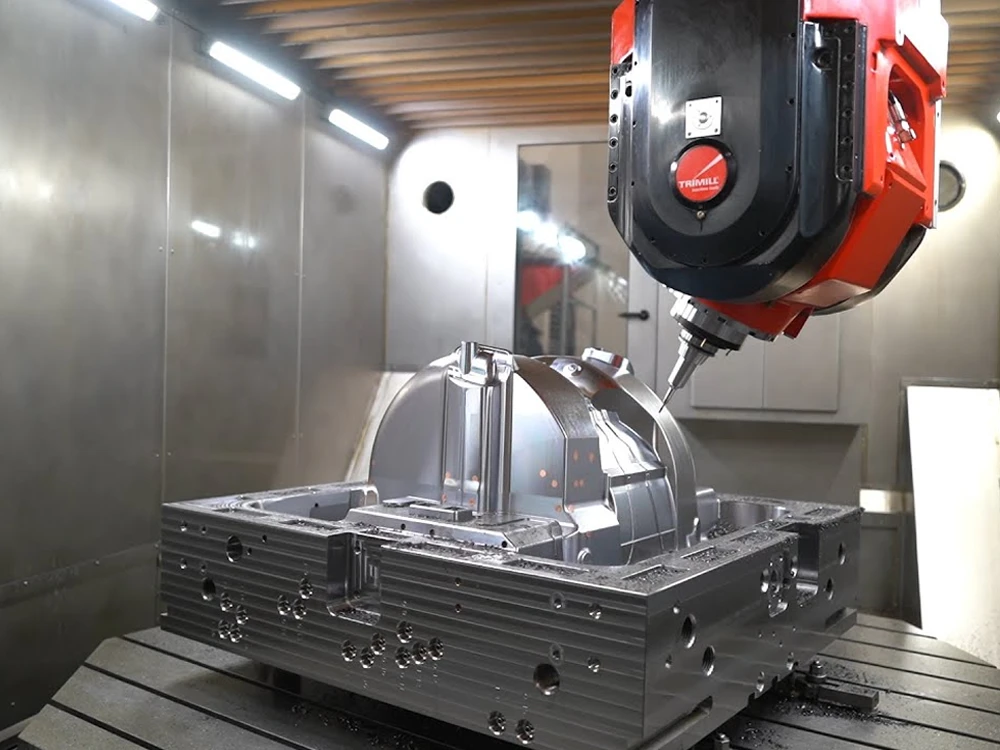
6-Axis Milling Machine
The most advanced configuration, a 6-axis milling machine, provides full flexibility in machining intricate parts, reducing setup time while enhancing accuracy and surface finish.
Classification Based on Machine Structure
Different structural designs affect stability, load capacity, and machining flexibility.
Fixed Bed Milling Machine
A fixed bed milling machine has a stationary worktable while the cutting tool moves. It is commonly used for heavy and large workpieces that require stability.
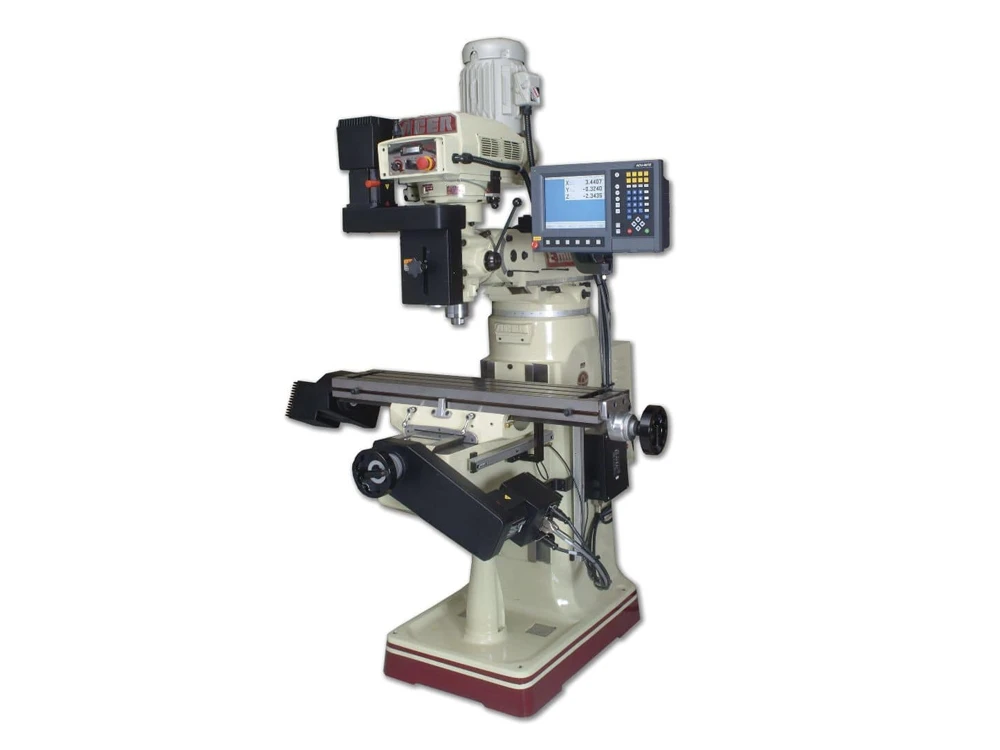
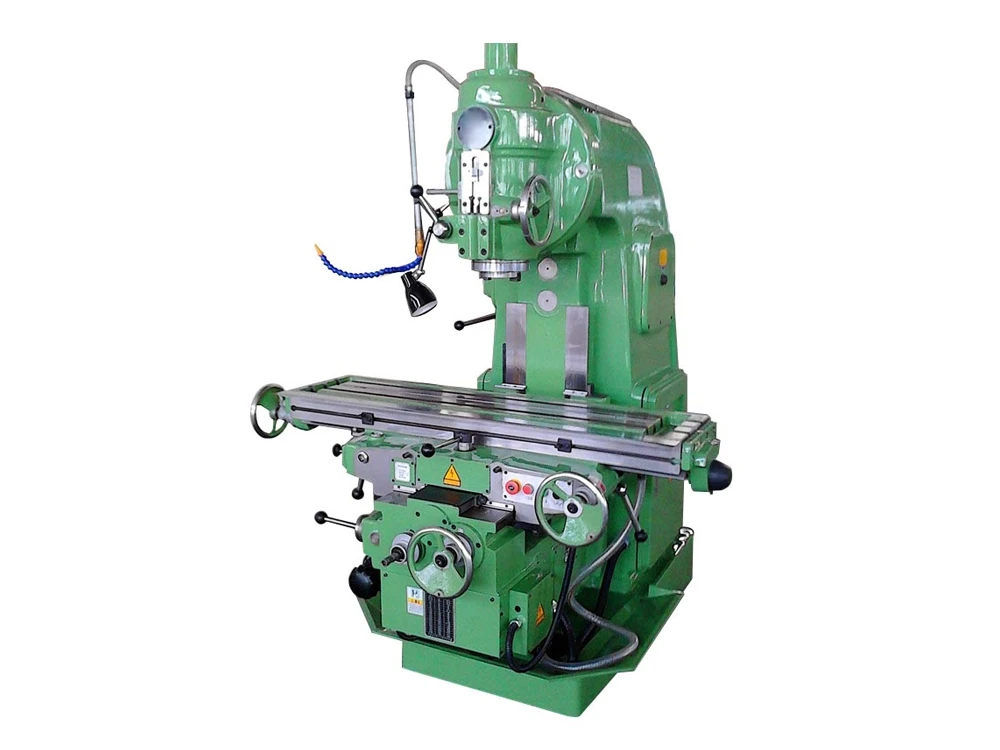
Knee-Type Milling Machine
A knee-type milling machine features an adjustable knee that supports the worktable, making it suitable for manual height adjustments during machining.
Planer-Type Milling Machine
A planer-type milling machine is designed for large-scale machining and is commonly used in industries requiring high precision and heavy-duty milling operations.
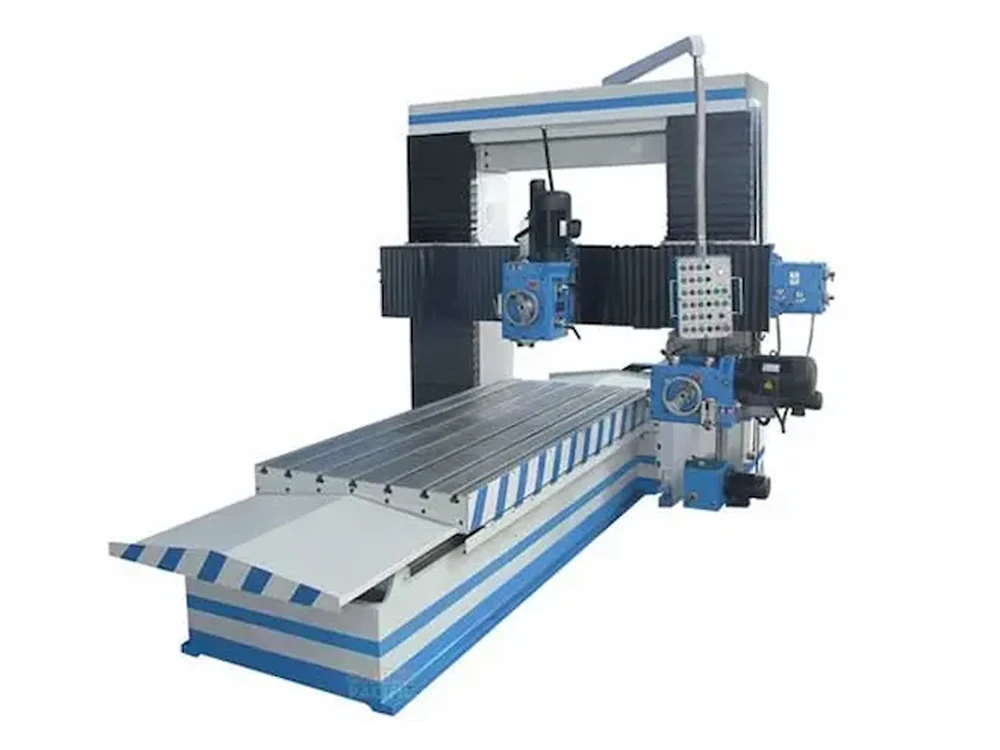
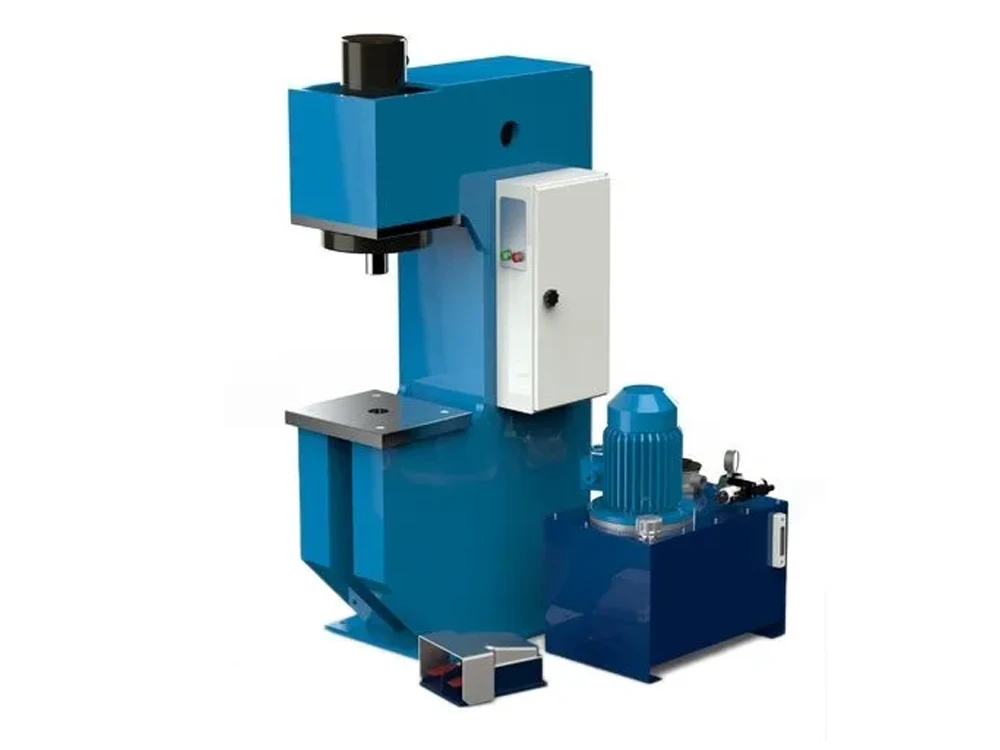
C-Frame Milling Machines
A C-frame milling machine is structured with a rigid vertical frame, making it highly stable and ideal for repetitive industrial applications.
Travelling Column Milling Machines
A travelling column milling machine allows the column to move while the worktable remains fixed, enhancing machining efficiency for long workpieces.
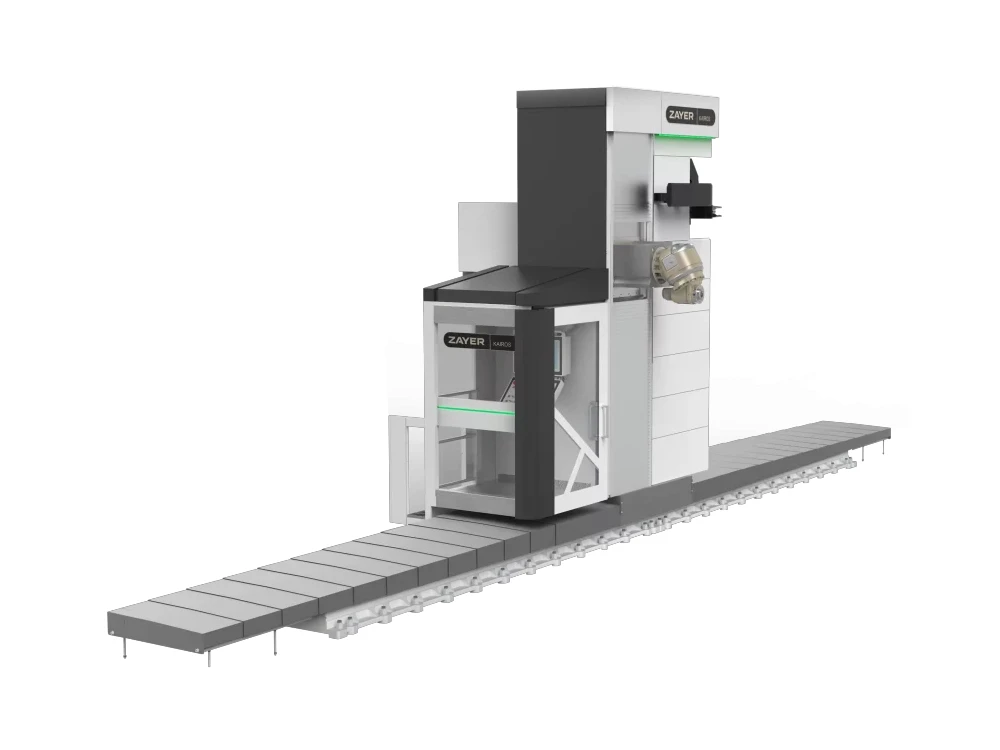
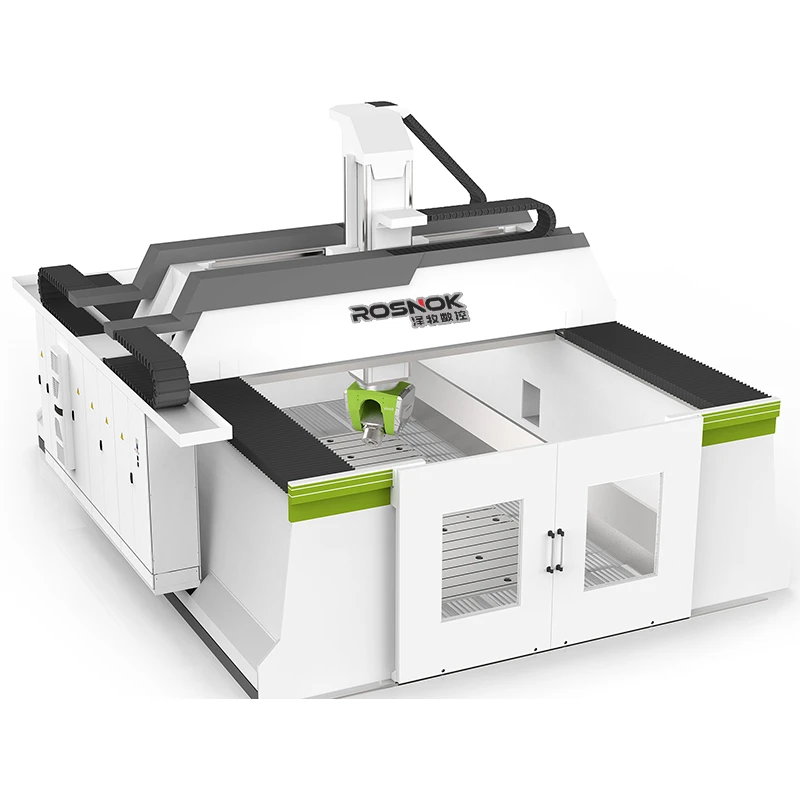
Gantry Milling Machine
A gantry milling machine features a large bridge structure, with the cutting tool suspended from above. This type is used for machining massive parts, such as aerospace components and shipbuilding materials.
Classification Based on Control Method
The control method dictates how the machine is operated—ranging from manual operation to full automation.
Manual Milling Machine
A manual milling machine requires the machinist to manually control feed rates, tool positioning, and cutting depth, making it ideal for small-scale workshops and prototyping.
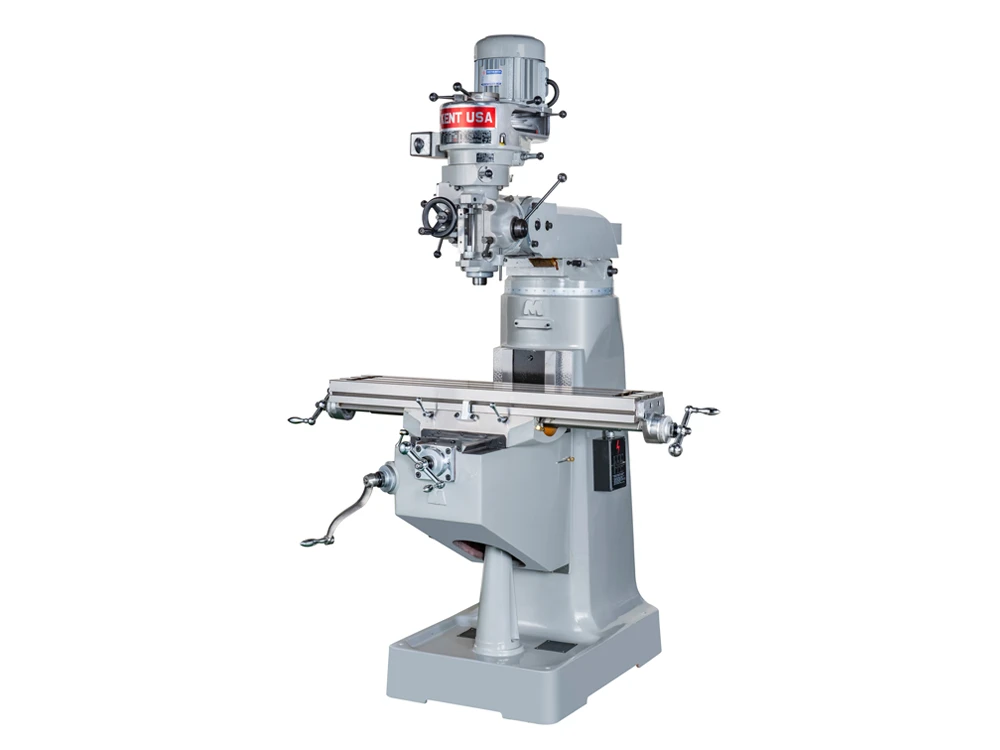
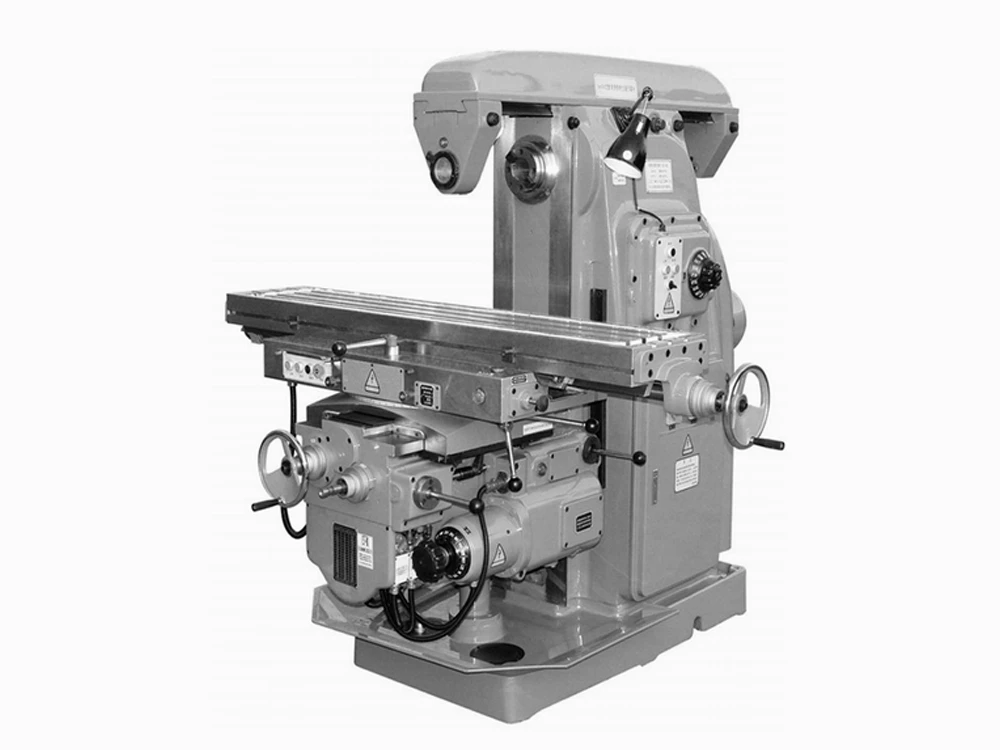
Tracer-Controlled Milling Machines
A tracer-controlled milling machine follows a predefined pattern or template, commonly used in duplicating parts or mold-making applications.
Milling Machine with DRO (Digital Readout System)
A milling machine with a digital readout (DRO) provides precise position feedback, helping operators achieve accurate cutting and repeatability without full CNC automation.
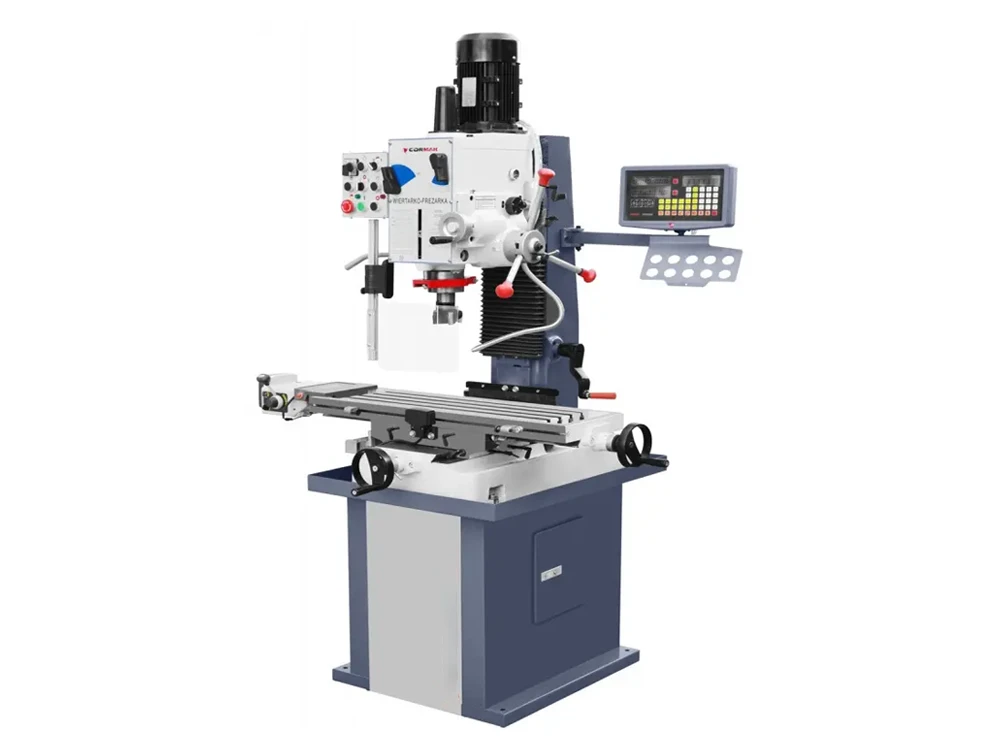
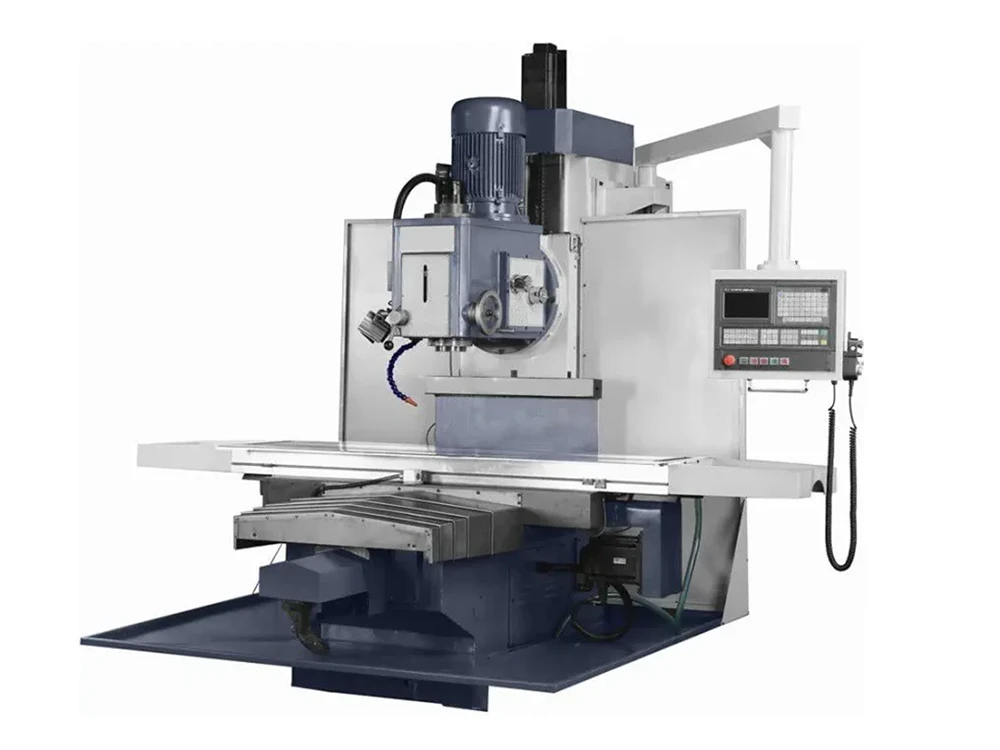
CNC Milling Machines (Computer Numerical Control)
A CNC milling machine is controlled via computer programming, allowing for automated, high-precision machining with minimal operator intervention. CNC milling is widely used in mass production, aerospace, and high-precision industries.
Highly Automated Milling Machine: Machining Center
What is a Machining Center?
A machining center is a highly automated and advanced form of a milling machine that integrates multiple machining functions, including milling, drilling, tapping, and even turning in some cases. Unlike conventional milling machines, machining centers are equipped with automatic tool changers (ATC), high-speed spindles, and multi-axis capabilities, allowing for high-precision, high-speed, and high-efficiency machining. These features make machining centers essential for mass production and complex precision manufacturing in industries such as aerospace, automotive, and medical device production. By combining multiple machining processes within a single system, machining centers eliminate the need for multiple setups, improving productivity and ensuring consistent accuracy in modern manufacturing.
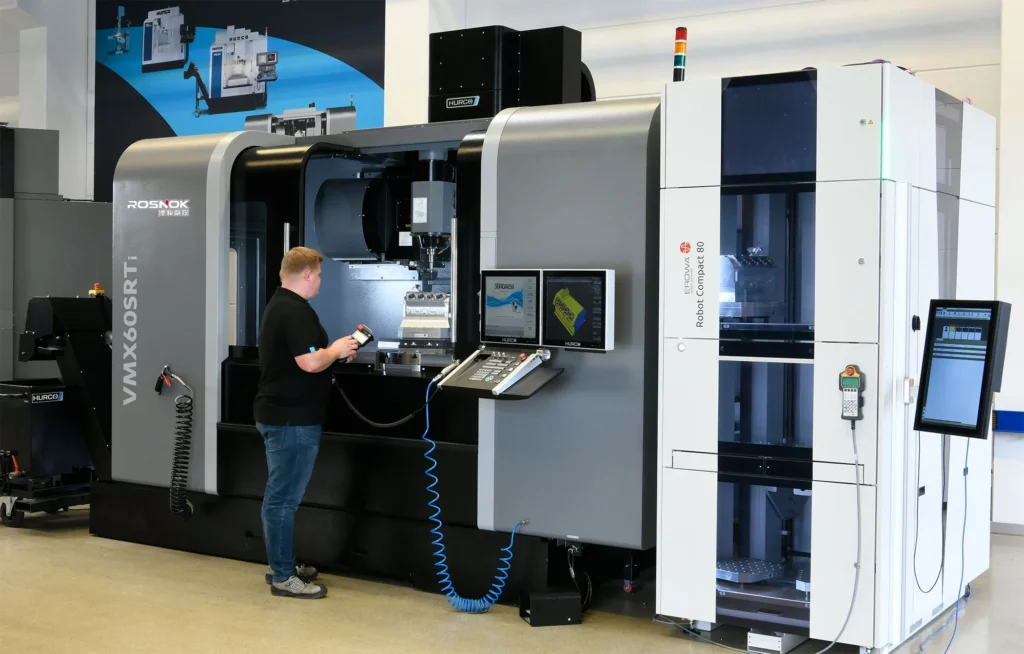
How a Machining Center Differs from a Conventional Milling Machine
- Full Automation: Unlike manual or basic CNC milling machines, machining centers are equipped with automatic tool changers (ATC), automatic workpiece changers (AWC), and robotic interfaces, allowing them to operate without human intervention for long periods.
- Multi-Axis Capabilities: Many machining centers come in 3-axis, 4-axis, 5-axis, and even 6-axis configurations, allowing them to handle complex geometries and intricate cuts with a single setup.
- High-Speed Machining (HSM): They support higher spindle speeds, advanced cooling systems, and optimized toolpaths, enabling faster production cycles without compromising accuracy.
- Live Monitoring & AI Optimization: Some modern machining centers have real-time monitoring, AI-driven adjustments, and predictive maintenance systems, ensuring maximum productivity and minimal downtime.
- Integrated Multi-Functionality: Machining centers can perform not just milling but also drilling, tapping, boring, and even grinding, making them a complete manufacturing solution rather than just a milling machine.
How to Choose the Right Type of Milling Machine?
Choosing the right milling machine depends on:
- Material & Workpiece Size – Large workpieces require gantry or fixed bed mills, while small parts are suited for vertical mills.
- Machining Complexity – 3-axis mills handle simple jobs, while 5-axis and 6-axis machines excel in complex precision machining.
- Production Volume – CNC milling machines are ideal for high-volume production, while manual mills are better for one-off prototypes.
Understanding the different types of milling machines allows machinists, engineers, and manufacturers to select the most efficient solution for their machining needs.
Milling Machine: Essential Machining Processes
Milling machines are among the most versatile tools in manufacturing, capable of performing a wide range of machining operations. While milling is their primary function—removing material through a rotating cutting tool to shape workpieces with precision—modern machines can also handle drilling, boring, tapping, and even turning. These additional capabilities make milling machines indispensable in precision manufacturing, allowing for the creation of complex geometries, smooth surfaces, and intricate details.
To better understand these machining processes, we can divide them into two main categories:
- Common Milling Processes – Traditional operations like face milling, contour milling, and slot milling, which involve cutting material directly.
- Additional Machining Processes – Other functions a milling machine can perform, such as drilling, boring, tapping, and turning, expanding its capabilities beyond standard milling.
I. Common Milling Processes
Face Milling – Creating Flat Surfaces
Face milling involves cutting with the flat face of the tool rather than its edges. It is used to remove excess material from large surfaces, ensuring smooth and even finishes.
Peripheral Milling – Cutting Along the Edges
Also known as slab milling, this process uses the cutting tool’s sides to shape the edges of a workpiece. It is often used in contouring and shaping parts with high precision.
Slot Milling – Creating Keyways and Grooves
Slot milling involves cutting narrow channels or slots into a workpiece. It is essential for creating keyways for shafts, fastener slots, and T-slots in machine tables.
Pocket Milling – Removing Material from Within a Workpiece
Pocket milling removes material within a closed boundary, creating recesses or cavities inside the workpiece. It is commonly used in die and mold manufacturing.
Contour Milling – Producing Complex Shapes
Contour milling is used to create curved, sloped, or 3D profiles on a workpiece. With CNC-controlled multi-axis milling, machinists can achieve high-precision freeform surfaces for aerospace and automotive applications.
Thread Milling – Cutting Internal and External Threads
Unlike traditional tapping, thread milling uses a rotating cutter to cut internal and external threads with high precision and stronger results, especially in hard metals.
Gear Milling – Machining Gear Teeth
Gear milling is used to cut gear teeth into cylindrical or conical surfaces. This process is crucial in automotive transmission manufacturing and mechanical engineering.
High-Speed Milling – Rapid Material Removal
High-speed milling (HSM) utilizes faster spindle speeds and optimized tool paths to remove material quickly while maintaining tight tolerances. It is widely used in mold manufacturing, medical, and aerospace machining.
II. Additional Machining Processes Performed on a Milling Machine
Modern milling machines, especially machining centers, can perform more than just milling. These additional processes help create fully finished parts without needing extra setups on other machines.
Drilling – Creating Holes in a Workpiece
Drilling is one of the most common additional functions of a milling machine. It uses rotating drill bits to create precise holes for screws, fasteners, and assembly parts.
Boring – Enlarging Pre-Drilled Holes
Boring is used to widen and refine existing holes to achieve tighter tolerances and improved surface finish. This is critical in engine block manufacturing and aerospace part production.
Reaming – Enhancing Hole Accuracy
Reaming is a finishing operation that improves hole diameter precision and surface smoothness, ensuring perfect fitment for press-fit or precision components.
Tapping – Cutting Internal Threads
Tapping is the process of creating internal threads inside a pre-drilled hole. In CNC machining centers, automatic tapping heads allow for fast, high-accuracy thread cutting.
Chamfering – Smoothing Edges
Chamfering removes sharp edges or burrs from a part, creating beveled edges that improve part assembly and safety.
Counterboring & Countersinking – Hole Preparation for Fasteners
- Counterboring: Expands a hole’s entrance so a bolt head can sit flush.
- Countersinking: Creates a conical recess for flat-head screws.
Turning – Rotating a Workpiece for Cylindrical Machining
Some advanced milling machines (such as 5-axis machining centers) include turning capabilities, allowing the machine to rotate the workpiece while cutting. This eliminates the need for a separate lathe and improves machining efficiency for cylindrical components.
Why These Milling and Additional Processes Matter
- Reduces the need for multiple machines, increasing efficiency.
- Allows for complex part production with fewer setups.
- Expands the range of manufacturing possibilities for different industries.
With advancements in CNC technology, milling machines are evolving into multi-functional machining centers, making them essential for precision-driven industries.
Industrial Applications of Milling Machines
Milling machines are indispensable in modern manufacturing, enabling the production of precise and complex components across various industries. Their ability to cut, shape, and refine materials makes them a core tool in high-precision machining, mass production, and custom fabrication. From automotive parts to medical implants, milling machines play a crucial role in creating critical components with accuracy and efficiency.
Automotive Industry – Precision Parts for Vehicles
Milling machines are extensively used in the automotive sector for producing engine blocks, transmission housings, cylinder heads, and chassis components. High-precision CNC milling machines ensure tight tolerances and repeatability, essential for mass production in the automobile industry.
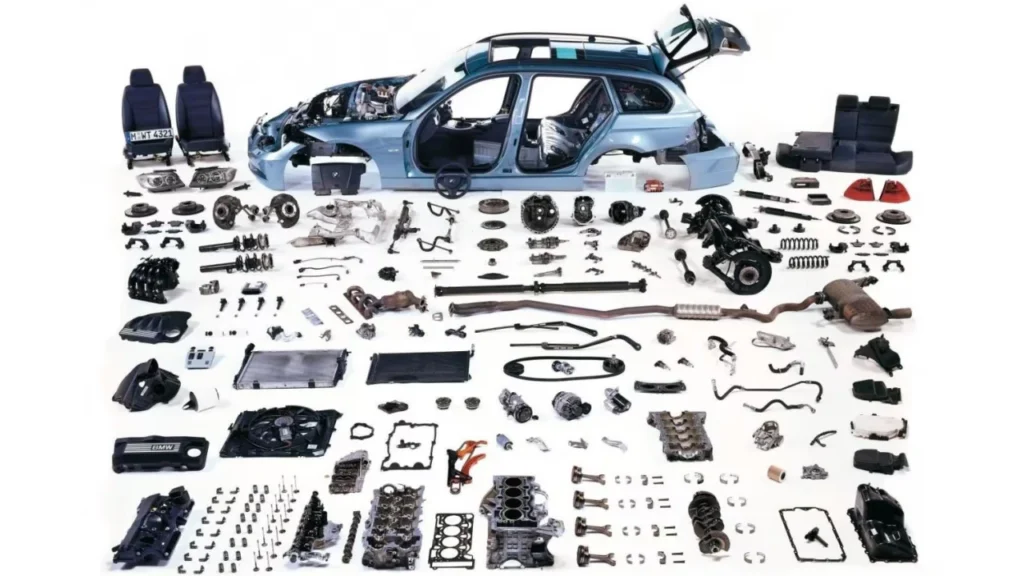
Aerospace Industry – Complex and Lightweight Components
In the aerospace sector, milling machines manufacture aircraft engine components, structural parts, and turbine blades from aluminum, titanium, and composite materials. 5-axis CNC milling enables the creation of intricate geometries required for lightweight and high-strength aerospace components.
Medical Industry – High-Precision Surgical Tools and Implants
Milling machines are widely used in medical device manufacturing to produce custom prosthetics, orthopedic implants, and surgical instruments. Materials such as titanium, stainless steel, and biocompatible plastics require ultra-precise milling techniques to meet strict medical standards.
Die and Mold Industry – Complex Tooling Production
The die and mold industry relies on milling machines for creating molds, dies, and precision tools used in injection molding, metal stamping, and plastic forming. High-speed CNC milling ensures the production of smooth and accurate cavities and contours, critical for mass production in various sectors.
Electronics Industry – Micro-Machining for Circuit Boards
In electronics manufacturing, milling machines are used for machining PCB boards, heat sinks, and micro-components. Precision micro-milling ensures high accuracy in small-scale machining, essential for the miniaturization of electronic devices.
Construction and Heavy Machinery – Large-Scale Component Manufacturing
Heavy-duty milling machines are employed in the construction and heavy machinery sectors to manufacture large parts for cranes, excavators, turbines, and steel structures. Gantry and planer-type milling machines handle large-scale machining with high accuracy.
Energy Sector – Turbines and Power Generation Components
Milling machines are crucial in the energy industry, particularly for machining wind turbine blades, hydroelectric components, and power plant machinery. The ability to mill complex, high-strength materials ensures efficient and long-lasting energy solutions.
Why Milling Machines Are Essential in These Industries
- High precision and repeatability ensure the production of critical parts.
- Versatility in machining different materials, from soft metals to hardened alloys.
- Adaptability to automation, reducing production time and labor costs.
- Support for complex geometries, essential in aerospace, medical, and die/mold industries.
Milling machines continue to be a cornerstone of modern manufacturing, driving innovation and improving efficiency across multiple industries.
Types of Cutting Tools Used in Milling Machines
Milling machines rely on a variety of cutting tools to shape, drill, and refine materials with precision. The choice of tool depends on the machining operation, material type, and required surface finish. Each tool has a specific function, allowing machinists to achieve different cutting results, from rough material removal to fine detailing.
Common Types of Milling Cutting Tools
End Mills – General-Purpose Cutting Tools
End mills are the most commonly used milling cutters, designed for a variety of operations such as profiling, slotting, and contouring.
- Flat End Mills – Used for general milling, face cutting, and slot cutting.
- Ball Nose End Mills – Ideal for 3D contouring and smooth finishing on curved surfaces.
- Corner Radius End Mills – Provide a stronger edge than flat-end mills, reducing tool wear.
Face Mills – Large Surface Machining
Face mills are wider cutting tools used to create flat surfaces on a workpiece.
- Designed for high-speed material removal.
- Often feature multiple cutting inserts for efficiency.
- Best suited for horizontal and vertical milling machines.
Shell Mills – Large Diameter Surface Cutting
Shell mills are large-diameter face milling tools with replaceable cutting inserts.
- Used in heavy-duty machining, aerospace, and industrial milling.
- Can remove large amounts of material quickly, making them efficient for big workpieces.
Slab Mills – Traditional Horizontal Milling Cutters
Slab mills are wide, cylindrical cutting tools used for removing large amounts of material in horizontal milling machines.
- Typically used for surface machining and heavy material removal.
- Common in industrial machining and steel fabrication.
Slot Drills – Two-Flute Cutting Tools for Slotting
Slot drills are similar to end mills but have only two cutting flutes, making them ideal for slotting and plunging operations.
- Used in keyway cutting, pocketing, and general-purpose slot milling.
- Ensures precise cutting when making deep slots and keyways.
Slotting Cutters – Creating Keyways and Grooves
Slotting cutters (also called woodruff cutters) are used for cutting slots, keyways, and T-slots.
- Available in straight and staggered tooth designs for different cutting depths.
- Used in industries like automotive, aerospace, and mold making.
T-Slot Cutters – Machining T-Slots in Workpieces
T-slot cutters create T-shaped slots, commonly found on milling machine tables.
- Used to secure workpieces on machine tables.
- Typically used in fixtures and tooling applications.
Chamfer Mills – Edge Finishing and Deburring
Chamfer mills create angled edges and bevels, ensuring sharp edges are removed for safety and assembly.
- Used for edge deburring, countersinking, and engraving.
- Essential in aerospace and precision engineering.
Thread Mills – Cutting Internal and External Threads
Thread mills create threads inside holes as an alternative to tapping.
- Suitable for hard metals where tapping might fail.
- Provides stronger, high-precision threads.
Fly Cutters – Single-Point Face Milling
Fly cutters use a single cutting edge to produce wide, smooth surfaces.
- Common in manual milling operations.
- Creates fine surface finishes.
Gear Cutters – Machining Gear Teeth
- Designed for cutting gears, sprockets, and involute profiles.
- Used in automotive, industrial, and mechanical applications.
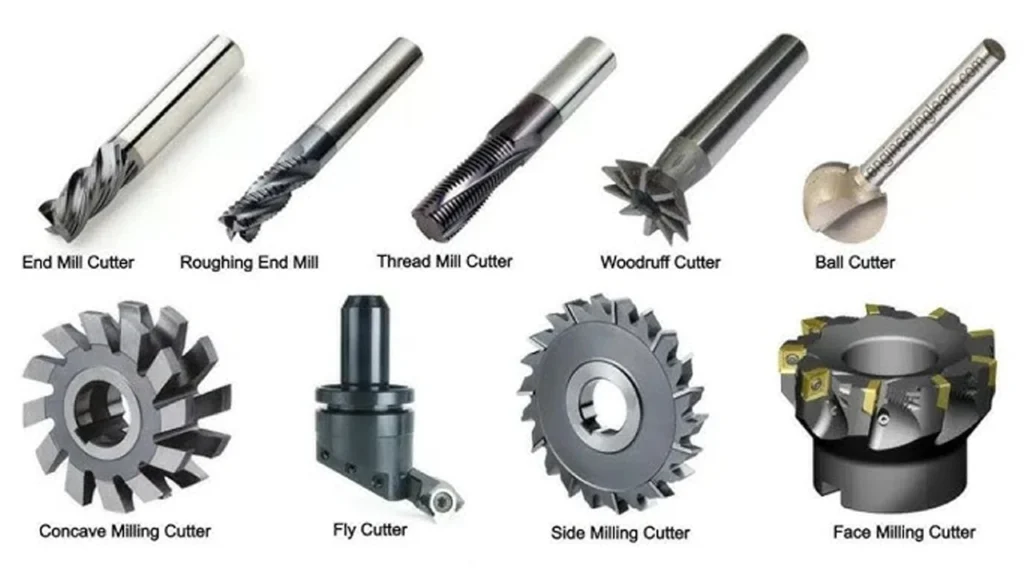
Choosing the Right Cutting Tool
The right tool depends on:
- Material Type – Hard metals require carbide or diamond-coated tools.
- Machining Operation – Choose between end mills, slot cutters, or chamfer mills based on the task.
- Surface Finish & Accuracy – Use ball nose end mills for smooth contours and face mills for flat finishes.
Summary
Milling machines utilize a wide range of cutting tools, each designed for specific operations. Selecting the correct tool ensures better precision, tool longevity, and machining efficiency.
What Materials Can be Machined on a Milling Machine?
Milling machines are incredibly versatile and can process a wide range of materials, from soft woods and plastics to hard metals and ceramics. However, each material requires specific cutting tools, speeds, and machining techniques to achieve optimal results. Understanding how different materials behave during milling ensures better tool life, surface finish, and machining efficiency.
Common Materials Milled in Manufacturing
Metals
Milling machines are widely used in metalworking industries to shape and refine metal components.
- Aluminum – Lightweight, corrosion-resistant, and easy to mill; commonly used in automotive, aerospace, and electronics.
- Steel – Includes mild steel, stainless steel, and tool steel; requires carbide cutting tools to handle hardness.
- Titanium – Strong, corrosion-resistant, and used in aerospace and medical implants; requires high-speed CNC milling with precise cooling.
- Brass & Copper – Known for good machinability and electrical conductivity, used in electrical, plumbing, and decorative applications.
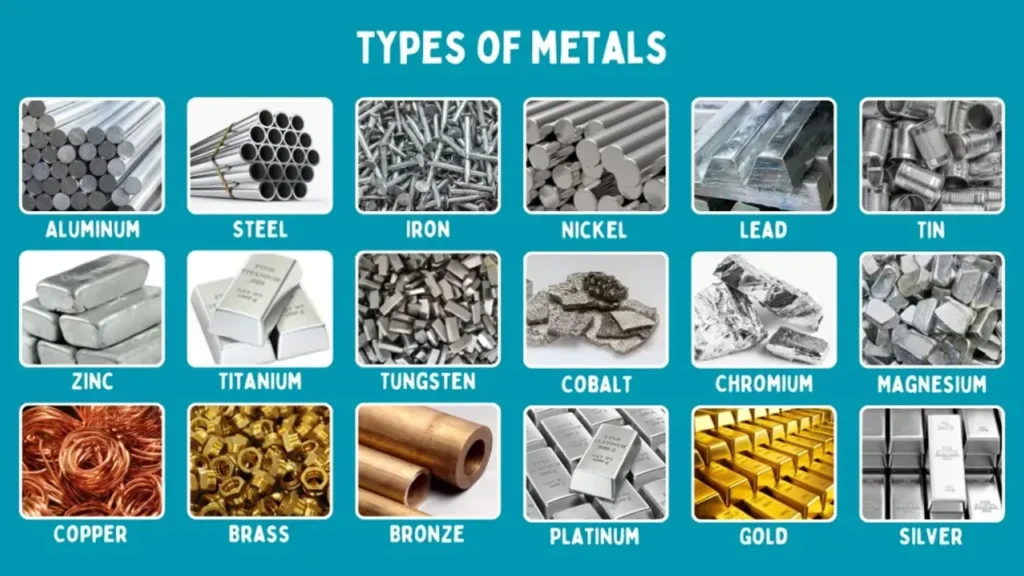
Plastics
Plastics are frequently milled for engineering components, packaging, and medical devices.
- Acrylic & Polycarbonate – Transparent materials used in automotive lighting and electronic screens.
- Nylon & POM (Delrin) – Durable, self-lubricating plastics used in gears, bearings, and mechanical parts.
- ABS & PVC – Common for prototyping and industrial components due to their toughness and affordability.
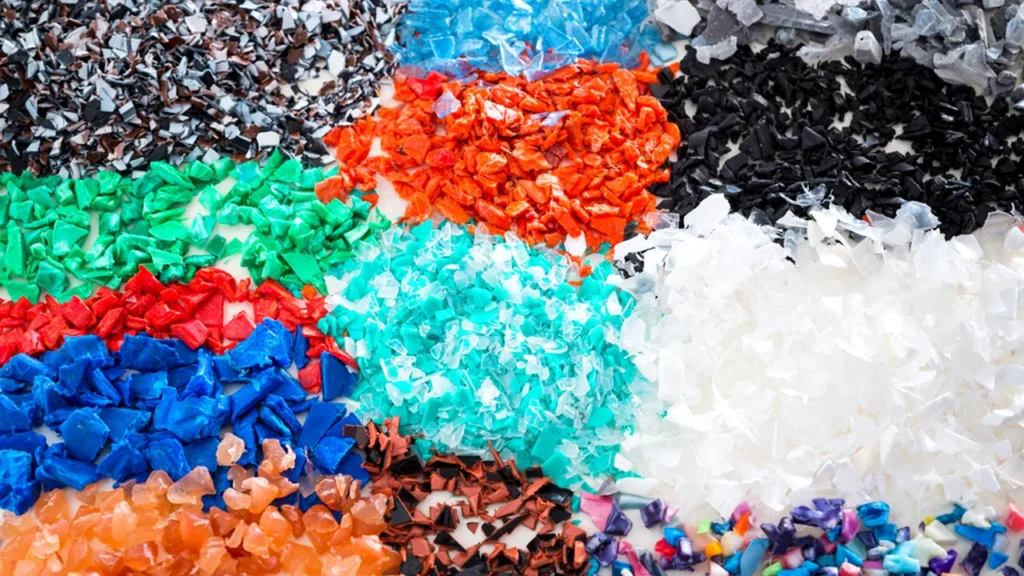
Composites & Carbon Fiber
Milling composite materials requires specialized tooling to prevent fraying or delamination.
- Carbon Fiber Reinforced Plastic (CFRP) – Used in aerospace and sports equipment for its high strength-to-weight ratio.
- Fiberglass – Found in marine, automotive, and construction applications; requires diamond-coated tools for precision.
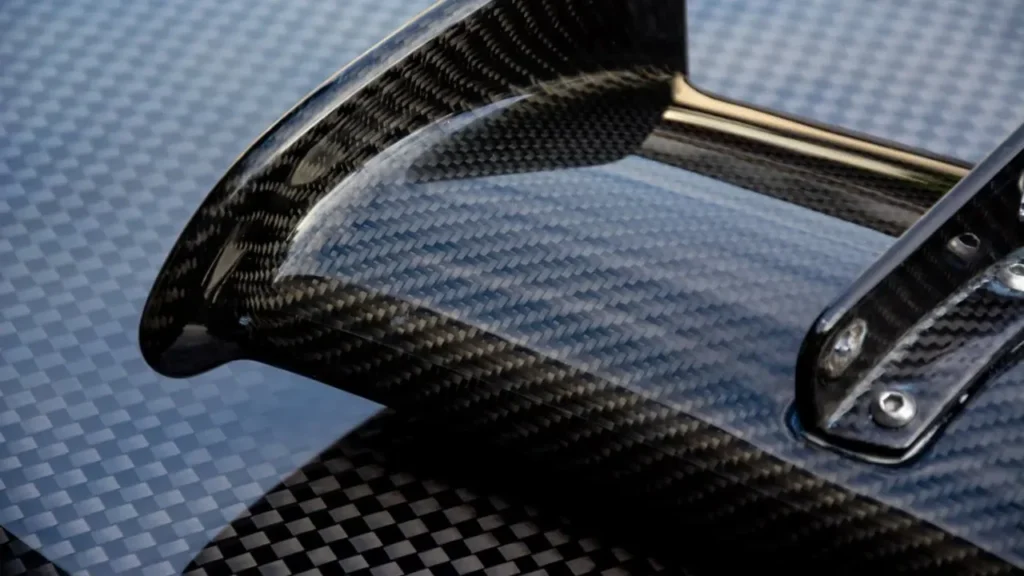
Ceramics
Ceramics are brittle but extremely hard, making them difficult to machine. Specialized milling techniques are required to avoid cracking or chipping.
- Alumina (Al₂O₃) & Zirconia (ZrO₂) – Used in medical implants, electronics, and aerospace components.
- Glass Ceramics & Silicon Carbide – High-performance materials in semiconductors and industrial cutting tools.
Considerations for Milling Ceramics:
- Use diamond-coated or ceramic tools to withstand extreme hardness.
- Reduce cutting forces by using high spindle speeds and low feed rates.
- Employ coolant or air-blast systems to prevent heat buildup and micro-cracking.
- Use ultrasonic milling for precision machining of brittle ceramics.
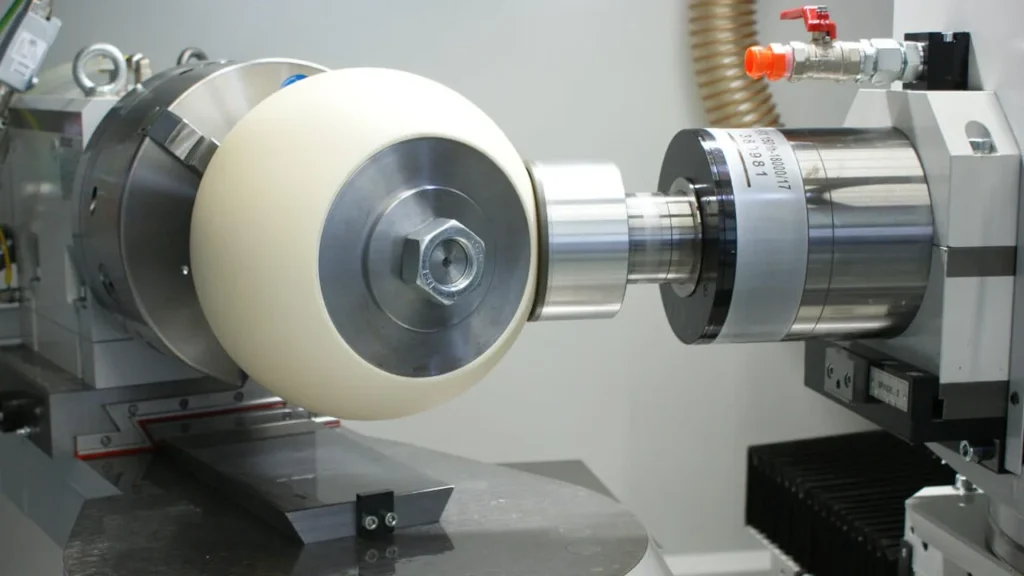
Wood
Wood is much softer than metals and ceramics, making it easier to mill. It is widely used in furniture making, carpentry, and prototype modeling.
- Hardwoods (Oak, Maple, Walnut) – Durable and used in high-end furniture and decorative components.
- Softwoods (Pine, Cedar) – Easier to mill and commonly used in construction and interior design.
- Foam & Modeling Board – Lightweight materials used for rapid prototyping and mold-making.
Considerations for Milling Wood:
- Use high-speed steel (HSS) or carbide tools for clean cuts.
- Adjust spindle speeds based on wood type (hardwoods require slower speeds than softwoods).
- Use dust extraction systems to manage wood chips and prevent overheating.
- Avoid excessive feed rates to prevent splintering or burning.
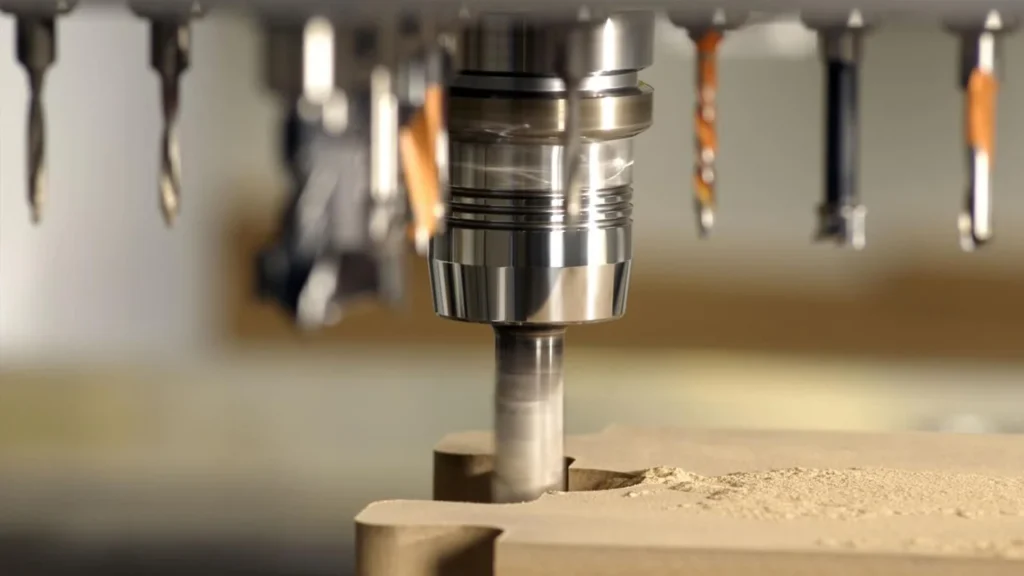
Choosing the Right Cutting Tools for Different Materials
- Carbide End Mills – Best for steel, titanium, and composites due to heat resistance and durability.
- High-Speed Steel (HSS) Tools – Suitable for plastics, wood, and soft metals like aluminum and brass.
- Diamond-Coated Tools – Essential for ceramics, composites, and glass to prevent tool wear.
Summary
Milling machines can process a vast range of materials, from soft plastics to hardened steels and ceramics, making them invaluable in various industries. Choosing the right tooling, cutting speeds, and cooling methods is essential for achieving high-quality finishes and long tool life.
Milling Machines vs. Lathes: Key Differences
Milling machines and lathes are two of the most commonly used machine tools in manufacturing, each designed for specific machining operations. While both are used for material removal, they operate differently and serve distinct purposes. Understanding their key differences helps machinists and manufacturers choose the right machine for their specific applications.
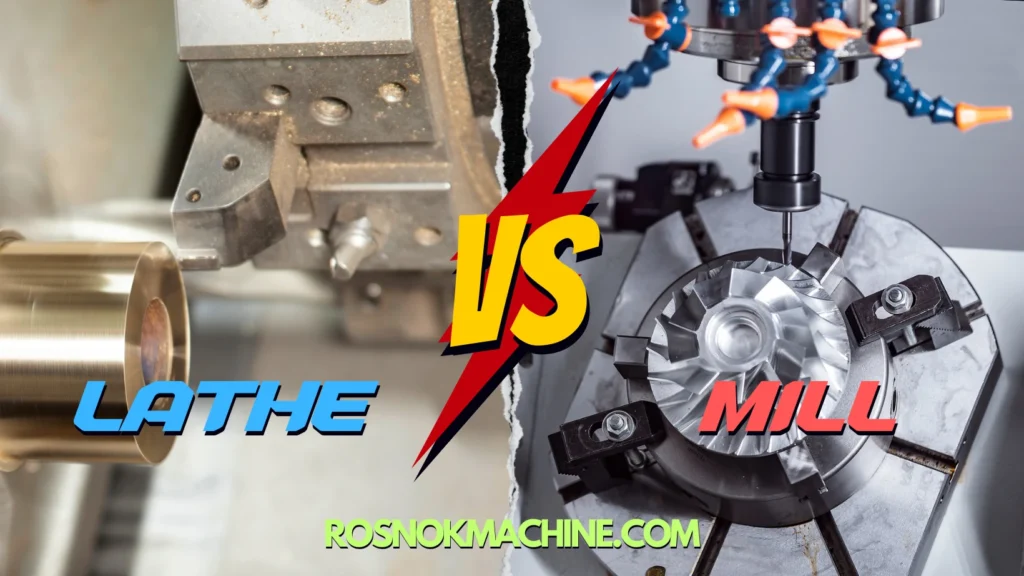
Fundamental Difference: Cutting Motion
The primary difference between a milling machine and a lathe lies in how material is removed.
Milling Machines
Milling machines keep the workpiece stationary while the cutting tool rotates, removing material to shape the part. They excel at machining flat surfaces, grooves, slots, and complex geometries.
Lathes Machines
Lathes rotate the workpiece while the cutting tool remains stationary, shaping the material into cylindrical, conical, or spherical forms.
Types of Workpieces Processed
- Milling machines are ideal for machining non-cylindrical parts, such as engine blocks, dies, and custom components.
- Lathes are primarily used for cylindrical parts, including shafts, pipes, and bushings.
Axes of Movement
Milling Machines
Milling machines move along multiple axes (X, Y, and Z), allowing for multi-directional machining. Advanced CNC mills can include 4-axis and 5-axis movement for complex geometries.
Lathes Machines
Lathes primarily operate along two axes (X and Z), making them more suitable for symmetrical components.
Tooling and Cutting Operations
Milling Machines
Milling machines use rotary cutting tools, such as end mills, face mills, and slot cutters, to remove material from different angles.
Lathes Machines
Lathes use single-point cutting tools to shape the rotating workpiece, often for turning, facing, threading, and grooving operations.
Applications in Manufacturing
Milling Machines
Milling machines are widely used in industries requiring complex, multi-surface machining, such as aerospace, die and mold making, and precision engineering.
Lathes Machines
Lathes are essential for industries producing cylindrical components, including automotive shafts, pipes, and fasteners.
Speed, Efficiency, and Automation
Milling Machines
CNC milling machines offer automated precision and high-speed multi-axis cutting, making them efficient for mass production.
Lathes Machines
CNC lathes are highly efficient for turning operations, providing excellent accuracy for symmetrical parts.
Choosing Between a Milling Machine and a Lathes Machines
The choice between a milling machine and a lathe depends on:
- Shape of the Workpiece – Cylindrical parts = Lathe, Complex geometries = Milling machine.
- Machining Requirements – If multi-axis movement is needed, a milling machine is the best option.
- Production Scale – CNC machines improve efficiency for both lathe turning and milling in high-production settings.
Summary of Key Differences
Feature | Milling Machine | Lathe |
---|---|---|
Workpiece Movement | Stationary | Rotates |
Cutting Tool Movement | Rotates and moves in multiple directions | Fixed, moves along X and Z axes |
Best for | Complex geometries, flat surfaces, slots | Cylindrical parts, threading, facing |
Common Tools | End mills, face mills, drills | Single-point cutting tools |
CNC Capabilities | 3, 4, 5-axis CNC milling | 2-axis CNC turning |
Both machines are essential in machining, but their applications are distinct. Milling machines handle intricate cuts and multi-surface machining, while lathes specialize in cylindrical shaping.
How to Choose the Best Milling Machine
Selecting the right milling machine is crucial for achieving optimal precision, efficiency, and productivity in machining operations. With various types of milling machines available, choosing the best one depends on several key factors, including workpiece size, material type, machining complexity, and production volume. Understanding these considerations helps machinists and manufacturers make informed decisions.
Factors to Consider When Choosing a Milling Machine
Workpiece Size and Material
- Small to Medium Workpieces → Vertical milling machines are ideal for the precision machining of smaller components, such as moulds, brackets, and fixtures.
- Large and Heavy Workpieces → Horizontal milling machines or gantry mills offer better support and stability for machining large parts, such as engine blocks and steel structures.
- Hard Metals (Titanium, Stainless Steel, Inconel) → High-rigidity CNC mills with carbide or coated tools are necessary to handle tough materials.
Machining Complexity and Precision Requirements
- Basic Machining Tasks → 3-axis milling machines are sufficient for standard cutting, slotting, and drilling operations.
- Advanced Contouring and Multi-Surface Machining → 4-axis or 5-axis CNC milling machines allow for multi-directional cutting and the creation of complex geometries without repositioning the workpiece.
Production Volume
- Low-Volume, Custom Machining → Manual and knee-type milling machines are suitable for workshops and prototyping.
- High-Volume Production → CNC machining centers with automatic tool changers (ATC) enhance efficiency and reduce cycle times for mass production.

Manual vs. CNC Milling Machines
Manual Milling Machines
Manual mills are operated by a machinist and require manual adjustments for feed rate, tool positioning, and depth of cut. These machines are best for:
- Prototyping and small-batch production
- Workshops and repair shops
- Simple machining tasks with frequent adjustments
CNC Milling Machines
CNC milling machines offer automated, programmable machining controlled by G-code software, ensuring high accuracy and consistency. These machines are ideal for:
- Mass production and complex machining tasks
- Industries requiring tight tolerances (aerospace, medical, and automotive)
- Reducing labor costs and improving machining efficiency
Specialized Milling Machines for Industry-Specific Applications
High-Speed Milling Machines
For industries like aerospace and medical, high-speed CNC mills provide faster material removal rates and enhanced surface finishes while maintaining precision.
Machining Centers (Multi-Function Milling Machines)
For factories requiring fully automated machining, machining centers offer milling, drilling, tapping, and even turning functions, reducing setup times and improving workflow.
Cost Considerations
The price of a milling machine varies based on:
- Type & Features – Manual mills are more affordable, while 5-axis CNC machining centers are premium investments.
- Automation Level – CNC machines with automatic tool changers and multi-axis capabilities cost more but provide higher efficiency.
- Brand & Build Quality – Machines with high-rigidity frames and durable components offer better longevity and performance.

Choosing the Right Milling Machine for Your Needs
To select the best milling machine, consider:
- The materials you will be machining.
- The complexity of the parts you need to produce.
- Your production scale and budget.
- Future expansion and automation possibilities.
By evaluating these factors, businesses and machinists can invest in the most suitable milling machine for their specific machining needs, ensuring high productivity, precision, and cost-efficiency.
Future Innovations in Milling Technology
The milling industry continues to evolve with advancements in automation, artificial intelligence, and precision engineering. As manufacturers demand higher efficiency, greater precision, and smarter machining processes, new technologies are shaping the future of milling machines. These innovations focus on speed, accuracy, sustainability, and connectivity, making modern milling machines more powerful than ever before.
Key Innovations Driving the Future of Milling Machines
Artificial Intelligence (AI) and Machine Learning in Milling
AI-powered CNC milling machines are revolutionizing machining by analyzing real-time data and making automatic adjustments to optimize cutting performance. Key benefits include:
- Automated error detection → AI can predict tool wear and adjust machining parameters accordingly.
- Optimized tool paths → Machine learning algorithms improve cutting efficiency by reducing unnecessary movements.
- Real-time adaptive machining → AI-driven software adjusts feed rates and spindle speeds based on material conditions.
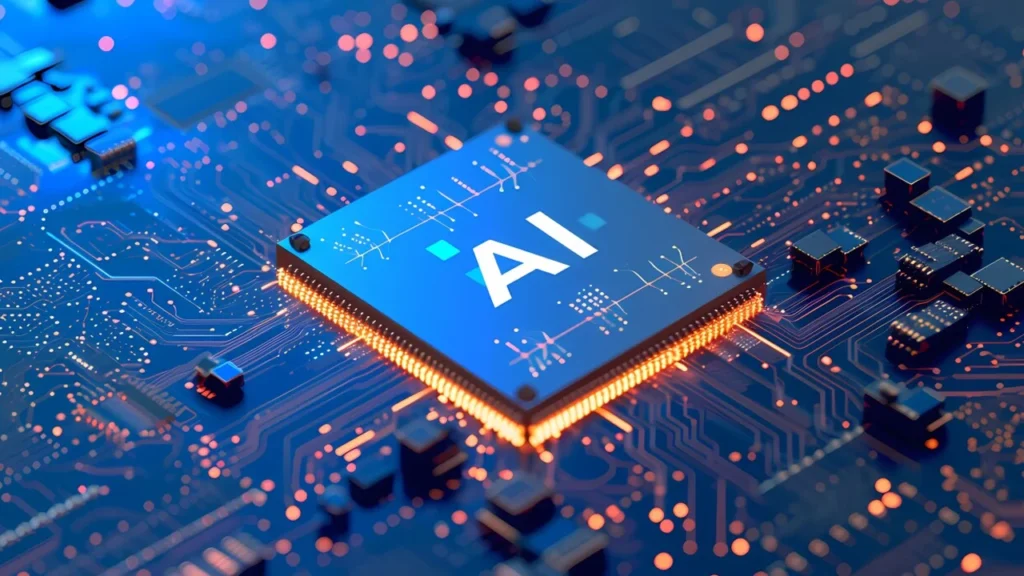
Multi-Axis and Hybrid Milling Technologies
- 5-axis and 6-axis milling machines are becoming more common, allowing for highly complex and multi-sided machining in a single setup.
- Hybrid milling machines combine additive manufacturing (3D printing) with traditional milling, enabling manufacturers to build and finish complex parts in a single process.
High-Speed and Ultra-Precision Milling
- Advances in high-speed spindle technology allow for faster material removal rates while maintaining precision.
- Ultra-precision milling is used in industries such as medical device manufacturing and semiconductor production, where tolerances are measured in microns.
Smart Factories and Industry 4.0 Integration
- Modern milling machines are now part of smart factory ecosystems, where they are connected to IoT (Internet of Things) networks.
- Real-time monitoring and predictive maintenance use sensors to track machine performance, preventing unexpected breakdowns.
- Cloud-based CNC programming allows machinists to control and monitor milling machines remotely, improving production flexibility.
Sustainable and Energy-Efficient Milling
- Eco-friendly cooling systems are being implemented to reduce the use of oil-based lubricants, minimizing environmental impact.
- Energy-efficient spindle motors help reduce power consumption while maintaining performance.
- Recyclable materials and chip recovery systems improve sustainability in manufacturing.
The Future of Milling: What to Expect
- More automation with AI-driven decision-making.
- Increased precision with advanced multi-axis capabilities.
- Faster machining speeds with high-speed spindles.
- Greater connectivity with cloud-based manufacturing solutions.
- Eco-friendly machining through sustainable cooling and energy-efficient technology.
Milling machines are no longer just traditional machining tools; they are evolving into intelligent, high-speed, and highly automated systems that are redefining the future of manufacturing.

Conclusion: What is the Milling Machine?
Milling machines have been a cornerstone of precision manufacturing, evolving from manual mills to highly advanced CNC machining centers. Their ability to cut, shape, and refine materials with exceptional accuracy makes them an essential tool in automotive, aerospace, medical, and industrial manufacturing.
From metals and plastics to ceramics and wood, milling machines can process a vast range of materials, allowing for flexibility in manufacturing. Additionally, the wide variety of cutting tools—such as end mills, face mills, slot drills, and thread mills—ensures that machinists can perform a diverse set of machining operations with precision.
As technology advances, AI-driven automation, multi-axis machining, and smart factory integration are transforming milling machines into intelligent, efficient, and highly precise tools. Whether used for custom prototyping or mass production, milling machines continue to play a vital role in modern engineering.
Choosing the right milling machine depends on workpiece material, machining complexity, production volume, and automation needs. Understanding the different types, essential machining processes, materials, and cutting tools helps businesses and machinists make informed decisions to maximize efficiency and quality.
With ongoing innovations in high-speed milling, sustainability, and AI-driven optimization, the future of milling technology promises greater productivity, precision, and environmental responsibility. For manufacturers and machinists, staying updated with these advancements will be key to remaining competitive in the evolving world of machining.