Have you ever wondered what is a machine tool does and why it’s so important in manufacturing? How do industries create precise metal components, automotive parts, and aerospace structures with such accuracy? Without machine tools, production would be slow, inconsistent, and expensive. But how exactly do these machines work, and why are they indispensable?
A machine tool is a precision device designed to cut, shape, drill, grind, or form materials with high accuracy. Whether manually controlled or fully automated with CNC technology, machine tools ensure precision, repeatability, and efficiency in manufacturing. Used across various industries, these machines enable large-scale production, minimize material waste, and improve product consistency. From simple hand-operated lathes to advanced multi-axis CNC machining centers, machine tools play a vital role in shaping the modern industrial world.
Machine tools come in many forms, each designed for specific applications. In this guide, we’ll explore the different types of machine tools, their functions, and how they revolutionize modern manufacturing.
Machine Tool Definition: What Is a Machine Tool?
A machine tool is a power-driven device used to cut, turn, mill, drill, bore, grind, shape, slot, form, and more with extreme precision. These machines are the backbone of modern manufacturing, allowing industries to mass-produce complex components with high accuracy and efficiency. Machine tools can be manually controlled or fully automated using CNC (Computer Numerical Control) technology, ensuring repeatability and consistency in production.
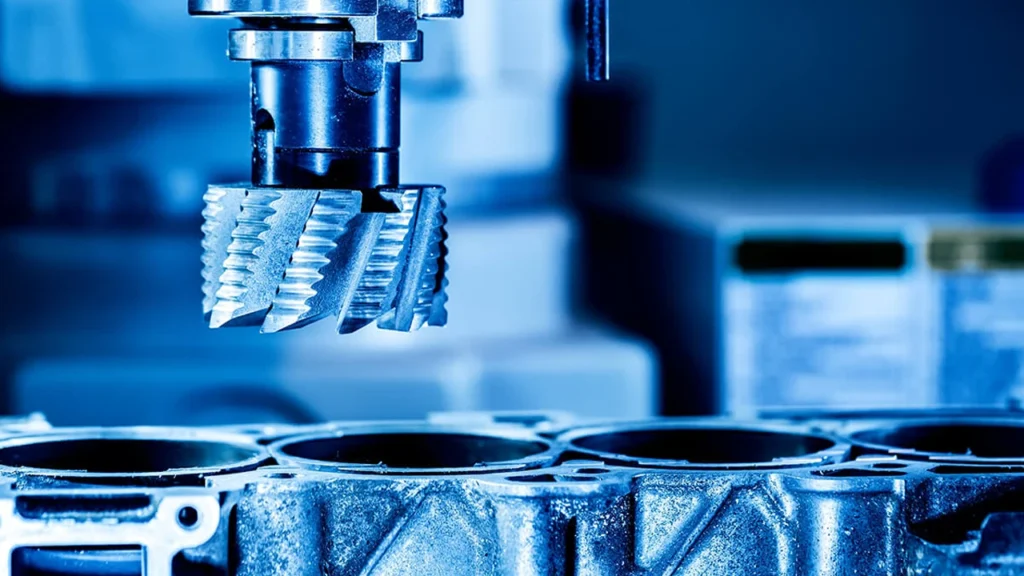
Unlike hand tools, machine tools utilize mechanical power, electrical motors, or hydraulic systems to perform high-speed, high-precision machining operations. They are indispensable in industries such as aerospace, automotive, medical, construction, and metal fabrication, where precision and standardization are critical.
Machine tools vary widely in function, from simple lathes and milling machines to advanced multi-axis CNC machining centers. Regardless of complexity, all machine tools share the same purpose—transforming raw materials into precisely engineered components that drive modern technology and industry.
A Short History of Machine Tools
Early Origins: The Birth of Machine Tools
Machine tools have a long history dating back thousands of years, evolving from simple hand tools to highly automated CNC machining centers. The earliest machine tools can be traced to ancient Egypt and Mesopotamia, where craftsmen used hand-powered lathes and drilling tools to shape wood, stone, and metal.
During the Middle Ages, blacksmiths and artisans developed water-powered trip hammers and rudimentary lathes, increasing the efficiency of metalworking. These early innovations laid the groundwork for more advanced machines that would drive industrial progress.
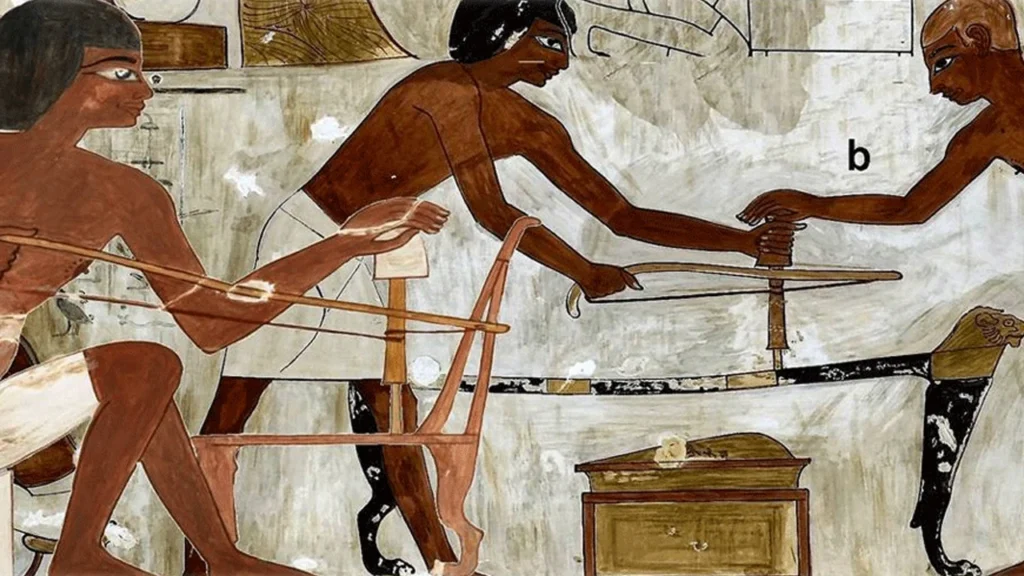
The Industrial Revolution: The Rise of Mechanized Machine Tools
The 18th and 19th centuries marked a turning point in machine tool development. The Industrial Revolution (1760–1840) led to steam-powered and mechanized machine tools, revolutionizing manufacturing by improving precision, speed, and efficiency.
- Some key inventions during this period include:
- Henry Maudslay’s Screw-Cutting Lathe (1797) → The foundation of modern lathes, enabling standardized thread cutting.
- Joseph Bramah’s Hydraulic Press (1795) → Introduced hydraulic power for metal forming.
- James Nasmyth’s Steam Hammer (1839) → Revolutionized forging processes, allowing large-scale metal shaping.
- Eli Whitney’s Milling Machine (1818) → Allowed for mass production of interchangeable parts.
With these innovations, factories replaced manual craftsmanship with mechanized, mass-production methods, setting the stage for modern manufacturing.
The 20th Century: The Birth of CNC Technology
The 20th century saw electrification and automation, drastically improving machine tool performance. Electric motors replaced steam power, making machine tools faster, more precise, and more versatile.
However, the biggest breakthrough came in the 1950s with the development of Computer Numerical Control (CNC) technology. The first CNC machine was invented by John T. Parsons and Frank L. Stulen, funded by the U.S. Air Force to improve aircraft manufacturing.
By the 1970s and 1980s, CNC technology became widespread, allowing machine tools to:
- Follow pre-programmed instructions for precision machining.
- Automate repetitive tasks, reducing human error.
- Improve accuracy and efficiency, making large-scale manufacturing more cost-effective.
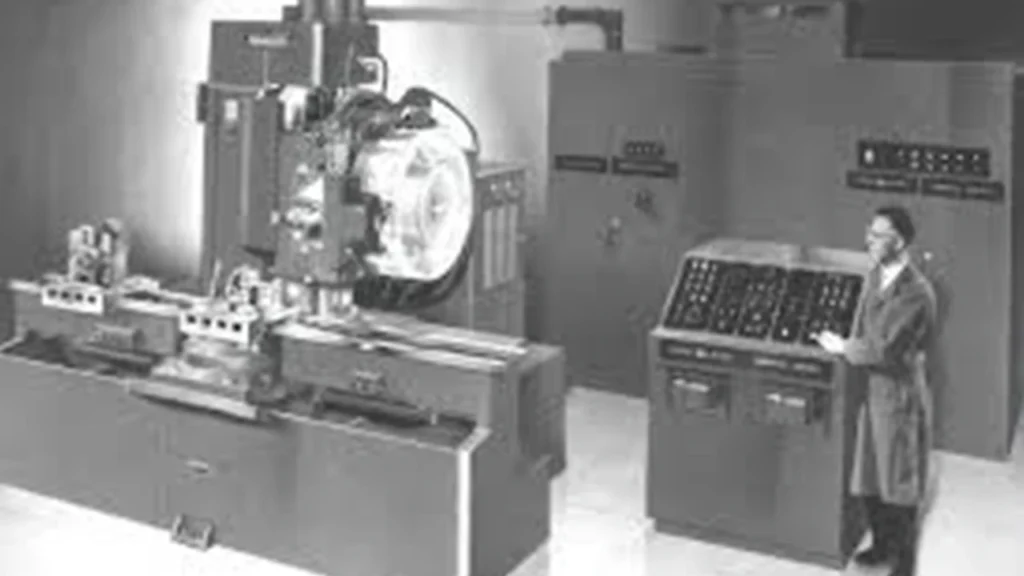
The 21st Century: Smart Machine Tools & Industry 4.0
Today, machine tools are more advanced and interconnected than ever. The rise of Industry 4.0 has introduced AI-driven automation, IoT-enabled smart factories, and hybrid manufacturing that combines CNC machining with 3D printing and robotics.
Modern innovations in machine tools include:
- 5-axis and 6-axis CNC machines → Allowing for complex, multi-directional machining.
- AI-powered predictive maintenance → Preventing machine failures before they happen.
- Energy-efficient & eco-friendly machining → Reducing material waste and optimizing power usage.
From hand-cranked lathes to AI-driven precision machining, the evolution of machine tools continues to redefine modern manufacturing.
Summary: The Evolution of Machine Tools
From hand-operated lathes in ancient times to AI-powered CNC machining centers today, machine tools have revolutionized manufacturing. Each era—the Industrial Revolution, the rise of electricity, and CNC automation—has brought advancements that improve precision, efficiency, and scalability. As Industry 4.0 continues to evolve, machine tools will become even smarter, faster, and more efficient, shaping the future of modern production.
What Are the Types of Machine Tools?
Machine tools come in many different types, each designed for specific machining operations like cutting, milling, drilling, grinding, shaping, and forming materials with high precision. Whether manually operated or fully automated with CNC technology, these tools play a vital role in manufacturing.
In this section, we’ll explore the most commonly used machine tools, how they work, their core components, and how they are used in different industries.
1. Lathe Machine (Turning Operations)
What Is a Lathe Machine?
A lathe machine is one of the most fundamental and widely used machine tools in manufacturing. It operates by rotating a workpiece while a stationary cutting tool removes material, creating cylindrical or symmetrical shapes.
Lathes are primarily used for turning and can also perform threading, facing, drilling, boring, tapering, and other operations. They can work with materials such as metals, wood, plastics, and composites. Depending on the setup, they can be manually operated or CNC-controlled for higher precision and automation.
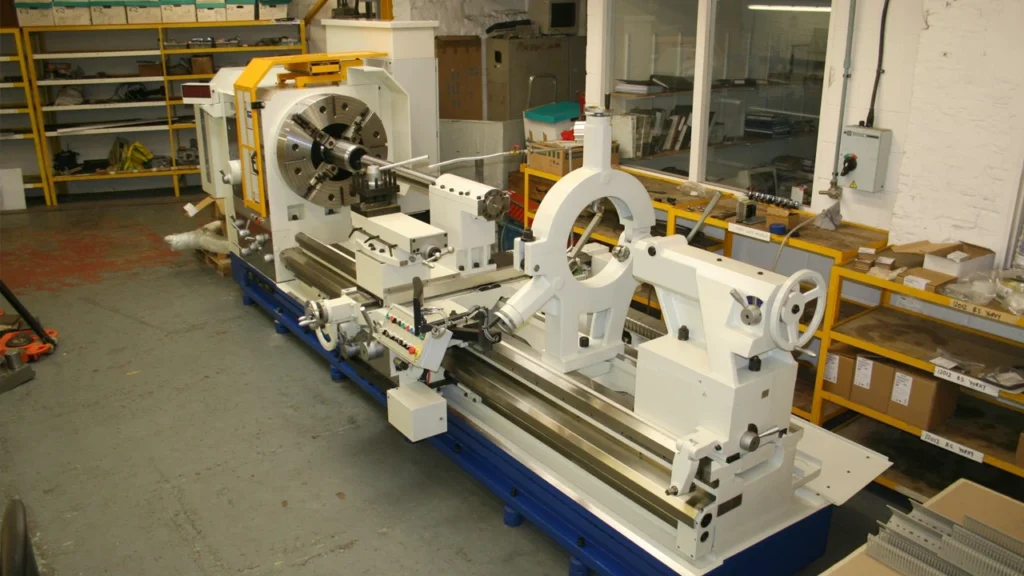
Types of Lathe Machines
- Manual Lathe – Requires operator control; ideal for custom parts, small-batch production, repairs, and prototyping.
CNC Lathe – Fully automated and programmed with G-code for high-precision production.
Swiss-Type Lathe – Used for small, high-precision components like watch gears and medical implants.
Vertical Lathe (VTL) – Designed for machining extremely large, heavy components such as railway wheels, wind turbine bearings, ship propeller hubs, and aerospace engine casings. - Pipe Threading Lathe → Specially designed for cutting threads on pipes and tubing, widely used in the oil & gas, plumbing, and construction industries.
- Turning Center → More advanced than a standard CNC lathe, capable of milling, drilling, and tapping operations in a single setup to enhance productivity and efficiency.
Main Components of a Lathe Machine & Their Functions
1. Headstock – Located on one end of the lathe, it houses:
- The main spindle, which holds and rotates the workpiece.
- The speed control system, which adjusts spindle speed.
- The gearbox, which controls power transmission.
2. Tailstock – Found on the opposite end, it:
- Supports long workpieces to prevent bending or vibration.
- Holds drill bits and boring tools for precise hole-making.
- Can move along the bed to adjust to different workpiece lengths.
3. Carriage – Moves along the lathe bed and holds the cutting tool. It consists of:
- Tool Post – Holds and rotates multiple cutting tools.
- Cross Slide – Moves the tool perpendicular to the spindle.
- Compound Rest – Adjusts the cutting angle for tapering.
4. Chuck – The mechanism that clamps and rotates the workpiece. Types include:
- 3-jaw chucks for round parts (self-centering).
- 4-jaw chucks for irregular shapes (independent movement).
5. Lathe Bed – The rigid foundation that supports all components. It:
- Ensures stability and precision by absorbing vibrations.
- Has hardened guideways for smooth carriage movement.
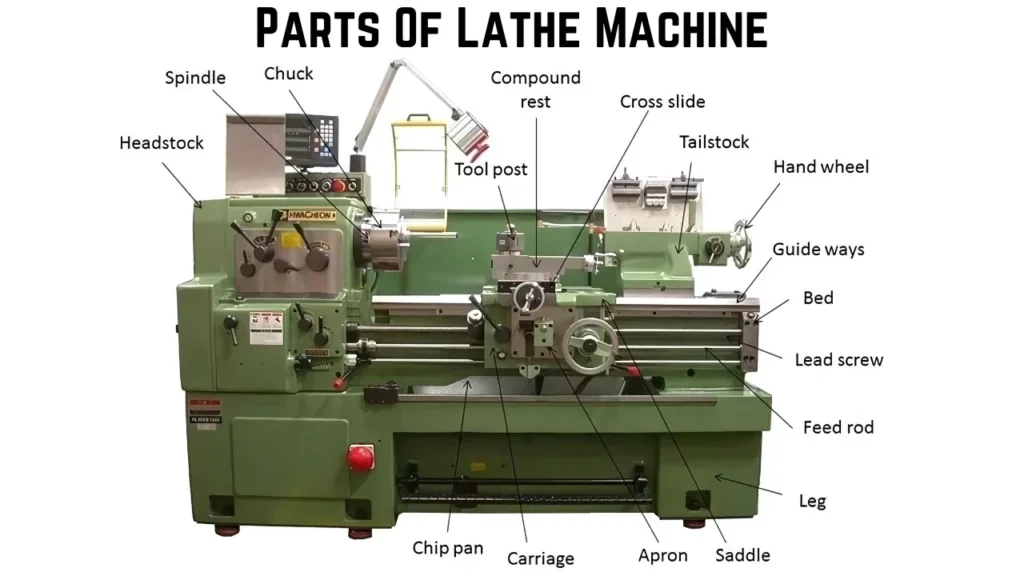
How Does a Lathe Machine Work?
- The workpiece is mounted onto the spindle using a chuck.
- The spindle rotates at the desired speed.
- The cutting tool is moved into the rotating workpiece, removing material layer by layer.
- The operator (or CNC system) controls the feed rate, depth of cut, and tool movement.
- The finished workpiece is removed after machining.
Key Applications of Lathe Machines
- Automotive Industry – Used to create engine shafts, pistons, gears, and brake drums.
- Aerospace Industry – Produces precision turbine parts, landing gear components, and aircraft fasteners.
- Medical Industry – Used for surgical implants, orthopedic components, and dental tools.
- General Manufacturing – Ideal for custom metal fabrication, threading, and prototyping.
Final Summary: Lathe Machine
The lathe machine is an essential machine tool for turning, drilling, boring, and threading operations. With various configurations, from manual to fully CNC-controlled, lathes are widely used in automotive, aerospace, medical, and precision engineering industries.
Lathe machines provide unmatched accuracy and efficiency, making them a must-have tool in modern manufacturing.
2. Milling Machine (Multi-Axis Turning & Shaping)
What Is a Milling Machine?
A milling machine is one of the most versatile and essential machine tools in manufacturing. Unlike a lathe that rotates the workpiece, a milling machine rotates the cutting tool while the workpiece remains stationary or moves along different axes. This allows for the machining of flat surfaces, slots, gears, and even complex 3D shapes.
Milling machines can be manually operated or CNC-controlled, with multi-axis capabilities to enable advanced contouring, drilling, and finishing operations.
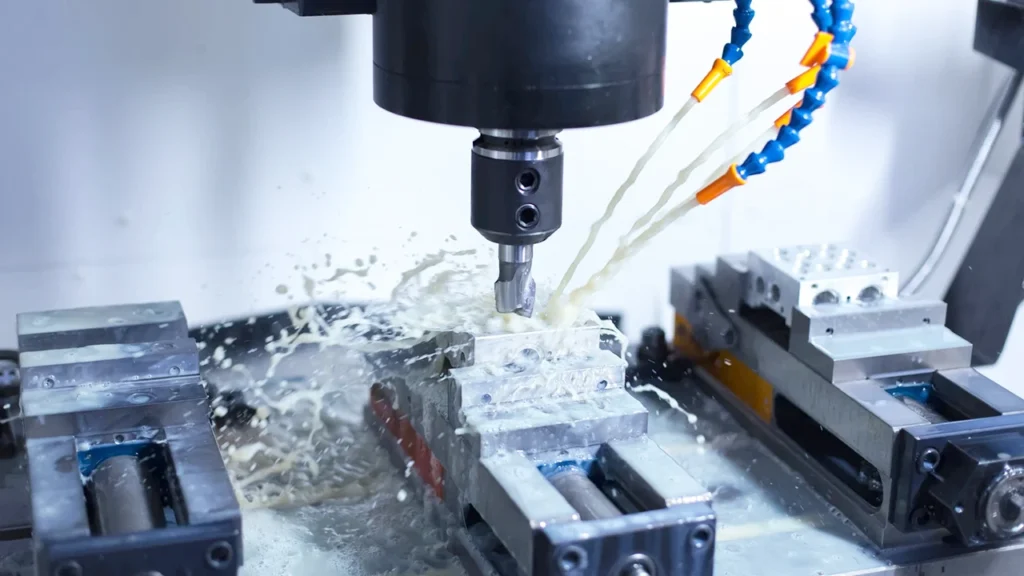
Types of Milling Machines
- Manual Milling Machine → Operated by a machinist, used for prototyping and custom machining.
- CNC Milling Machine → Automated and programmed with G-code, allowing for high-precision production with minimal operator input.
- Vertical Milling Machine (VMC) → The spindle is vertically oriented, best for face milling, slotting, and drilling.
- Horizontal Milling Machine (HMC) → The spindle is horizontally aligned, ideal for heavy-duty cutting and gear manufacturing.
- 4-Axis CNC Milling Machine → Adds a rotational axis, allowing the tool to access different sides of a workpiece.
- 5-Axis CNC Milling Machine → Offers full 3D machining, making it essential for aerospace, medical, and mold-making industries.
- CNC Machining Center → Highly automated, multi-functional milling machine with automatic tool changers (ATC), coolant systems, and enclosed workspaces for high-speed, precision machining.
Main Components of a Milling Machine & Their Functions
1. Spindle – The rotating axis that holds and drives the cutting tool.
- Provides power for milling operations.
- Can be horizontally or vertically aligned, depending on the machine type.
- Controls the speed and direction of the cutting tool.
2. Worktable – The surface that holds the workpiece.
- Moves along X, Y, and Z axes in CNC milling.
- Can hold fixtures, vises, or rotary tables for positioning.
- Supports precise movement for detailed cutting.
3. Column & Base – The main structural components providing support.
- Column houses the spindle and supports vertical movement.
- Base provides stability and absorbs vibrations.
4. Knee & Saddle – Adjusts the vertical and horizontal positioning of the worktable.
- Knee → Moves the table up/down for depth adjustments.
- Saddle → Moves the worktable forward/backward for precision machining.
5. Tool Changer (CNC Milling Machines Only) – Automatically swaps tools for different operations.
- Reduces manual intervention and increases efficiency.
- Found in CNC machining centers for high-speed multi-tool production.
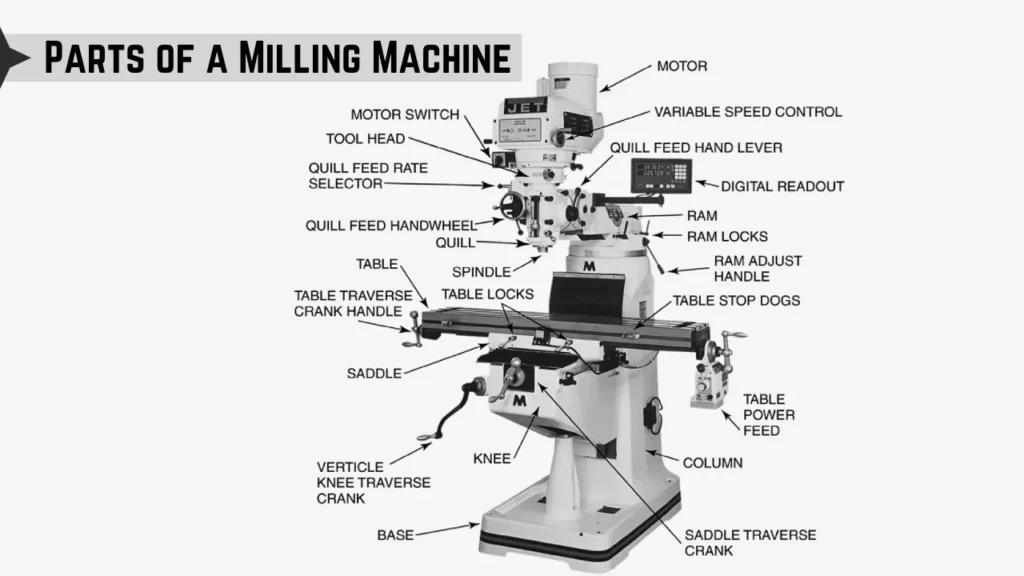
How Does a Milling Machine Work?
- The workpiece is secured on the table using clamps or a vise.
- The cutting tool (end mill, face mill, or drill bit) is mounted in the spindle.
- The spindle rotates, and the cutting tool moves across the workpiece.
- The operator (or CNC program) controls movement along multiple axes to shape the part.
- The finished part is removed, and additional operations like surface finishing can be performed.
Key Applications of Milling Machines
- Aerospace Industry – Used for aircraft components, turbine blades, and fuselage structures.
- Automotive Industry – Produces engine blocks, transmission cases, and suspension parts.
- Medical Industry – Used to create surgical implants, prosthetics, and precision medical tools.
- General Manufacturing – Ideal for custom metal fabrication, gear cutting, and mold-making.
Final Summary: Milling Machine
The milling machine is an essential multi-functional machine tool that allows for precise shaping, milling, drilling, slotting, boring, tapping, contouring, and more. With manual and CNC-controlled options, milling machines are used in industries ranging from automotive and aerospace to medical and general fabrication.
CNC milling machines offer multi-axis movement, automation, and high-precision machining, making them a cornerstone of modern manufacturing.
3. Drilling Machine (Precision Hole-Making)
What Is a Drilling Machine?
A drilling machine is a machine tool used for creating precise, round holes in materials such as metal, wood, plastic, and composites. It works by rotating a drill bit at high speed while applying downward pressure to remove material and form a hole. Drilling machines vary from simple manual drill presses to highly automated CNC drilling systems, offering precision, efficiency, and consistency in mass production.
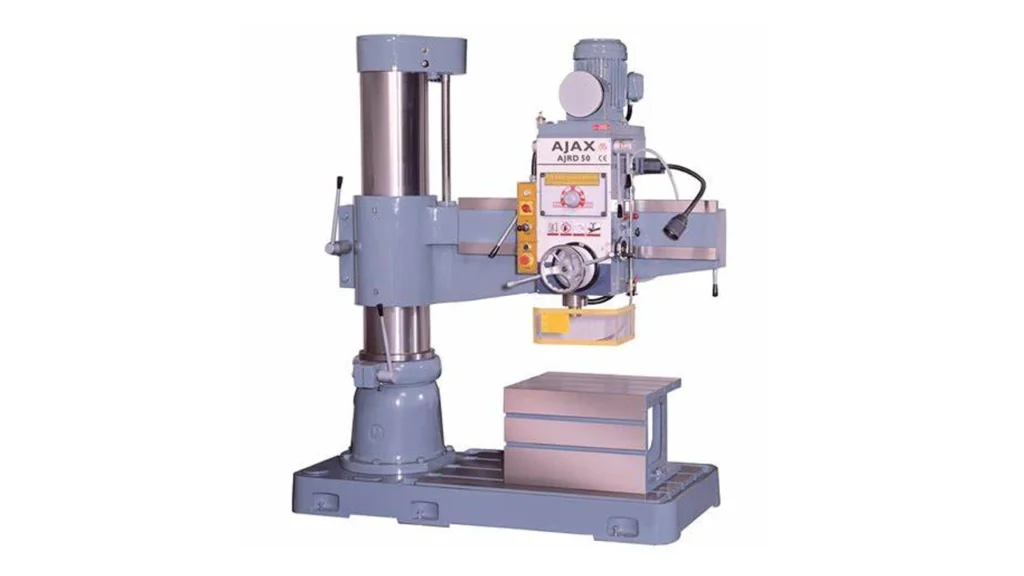
Types of Drilling Machines
- Bench Drilling Machine → A small, compact drill press for light-duty workshop tasks.
- Radial Drilling Machine → Features a movable radial arm, allowing drilling on large, heavy workpieces.
- Gang Drilling Machine → Has multiple drill heads in a row, enabling simultaneous multi-hole drilling.
- Multi-Spindle Drilling Machine → Uses multiple rotating spindles to increase productivity in mass production.
- Deep Hole Drilling Machine → Specialized for deep precision drilling, used in aerospace and oil industries.
- CNC Drilling Machine → A computer-controlled drilling system for automated, high-precision hole-making.
Main Components of a Drilling Machine & Their Functions
1. Spindle – The rotating shaft that holds and drives the drill bit.
- Controls drilling speed, feed rate, and depth of cut.
- Provides stability and precision during high-speed operations.
2. Drill Head – Contains the spindle, motor, and feed mechanism.
- Moves up and down along the column for controlled drilling.
- Houses automatic tool changers in CNC drilling machines.
3. Worktable – Supports and secures the workpiece.
- Adjustable height and angle for multi-angle drilling.
- Equipped with T-slots or clamps to hold materials securely.
4. Column & Base – Provides structural support for the entire machine.
- The column supports the drill head and worktable.
- The base absorbs vibrations and enhances machine stability.
5. Feed Mechanism – Controls the downward motion of the drill bit.
- Can be manual (lever-operated) or automatic (motorized feed).
- Ensures a consistent and precise cutting motion.
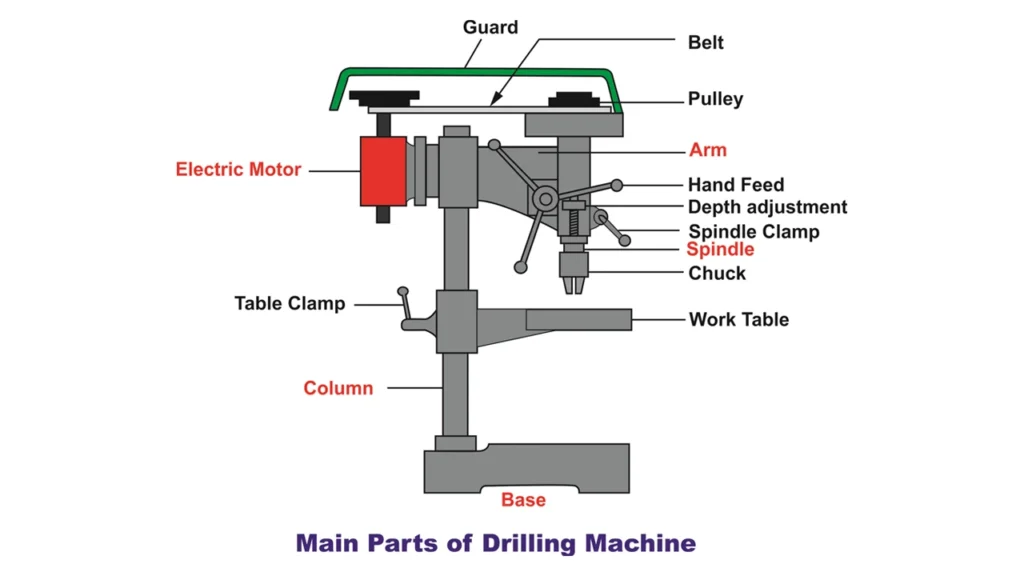
How Does a Drilling Machine Work?
- The workpiece is secured on the worktable using clamps or a vise.
- The drill bit is aligned with the target hole position.
- The spindle rotates, driving the drill bit into the material.
- The feed mechanism ensures a controlled cutting motion for accurate hole dimensions.
- Once drilling is complete, the bit retracts, and the workpiece is removed for further processing.
Key Applications of Drilling Machines
- Metal Fabrication → Drilling holes in steel, aluminum, and alloys for machinery and automotive parts.
- Woodworking → Used for furniture, cabinetry, and architectural components.
- Heavy Equipment Manufacturing → Drilling precise holes for agricultural, construction, and industrial machinery components.
- Shipbuilding & Structural Metalwork → Used for drilling holes in large metal plates, frames, and heavy steel structures.
- Aerospace & Automotive → Used in aircraft components, engine blocks, chassis frames, and transmission systems.
Final Summary: Drilling Machine
A drilling machine is a vital machine tool for precision hole-making in metal, wood, plastic, and composite materials. From basic manual drills to advanced CNC drilling systems, these machines ensure high-speed, high-accuracy machining for modern industrial applications.
4. Grinding Machine (Precision Surface & Cylindrical Finishing)
What Is a Grinding Machine?
A grinder is a machine tool that uses a grinding tool (usually a grinding wheel) to grind the surface of a workpiece. Unlike cutting tools, grinding machines achieve high accuracy and smooth surface finishes, making them ideal for tight-tolerance machining. These machines are essential for metal finishing, sharpening, and precision grinding in various industries, from aerospace to tool manufacturing.
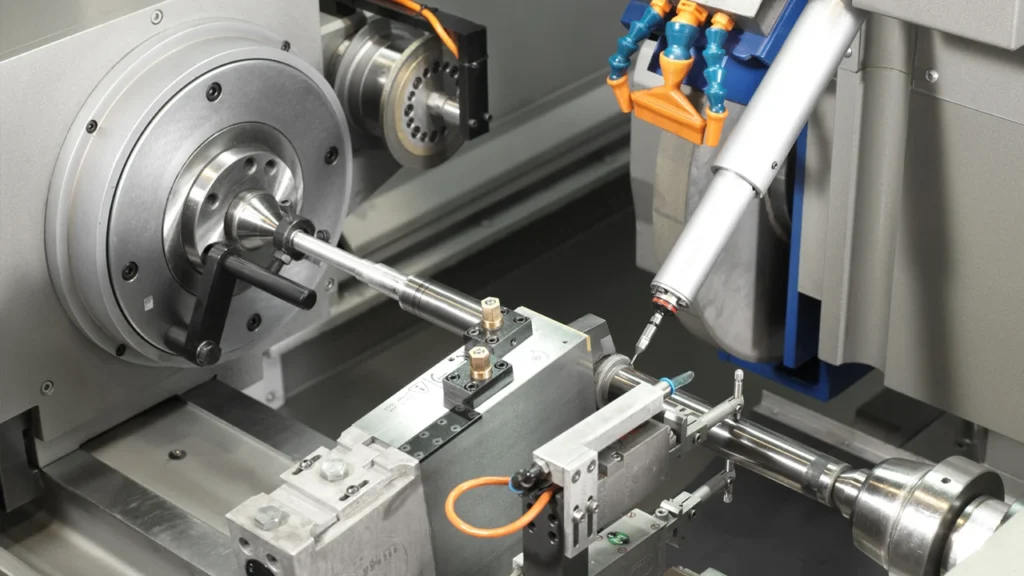
Types of Grinding Machines
- Surface Grinding Machine → Used for flat surface finishing in toolmaking and die manufacturing.
- Cylindrical Grinding Machine → Rotates the workpiece for precision outer diameter (OD) or inner diameter (ID) grinding.
- Centerless Grinding Machine → Grinds cylindrical parts without using a center fixture, ideal for mass production.
- Tool & Cutter Grinding Machine → Designed for resharpening tools like drills, milling cutters, and lathe tools.
- CNC Grinding Machine → Uses computer-controlled movement for high-precision automated grinding.
Main Components of a Grinding Machine & Their Functions
1. Grinding Wheel – The primary tool that removes material.
- Made of abrasive grains bonded together for precision cutting.
- Comes in various shapes, sizes, and materials for different applications.
2. Worktable – Holds and moves the workpiece.
- Can be manual or motor-driven, allowing precise positioning.
- Some CNC grinding machines feature rotary tables for advanced shaping.
3. Wheel Head & Spindle – Houses and rotates the grinding wheel.
- Ensures high-speed rotation and stability for precise grinding.
- Advanced machines have programmable spindle speeds for different materials.
4. Dresser Unit – Maintains the grinding wheel’s sharpness and shape.
- Removes worn-out abrasive particles.
- Ensures consistent material removal rates and precision finishes.
5. Coolant System – Prevents overheating and improves finish quality.
- Uses coolants or lubricants to reduce heat and extend tool life.
- Essential for high-speed precision grinding.
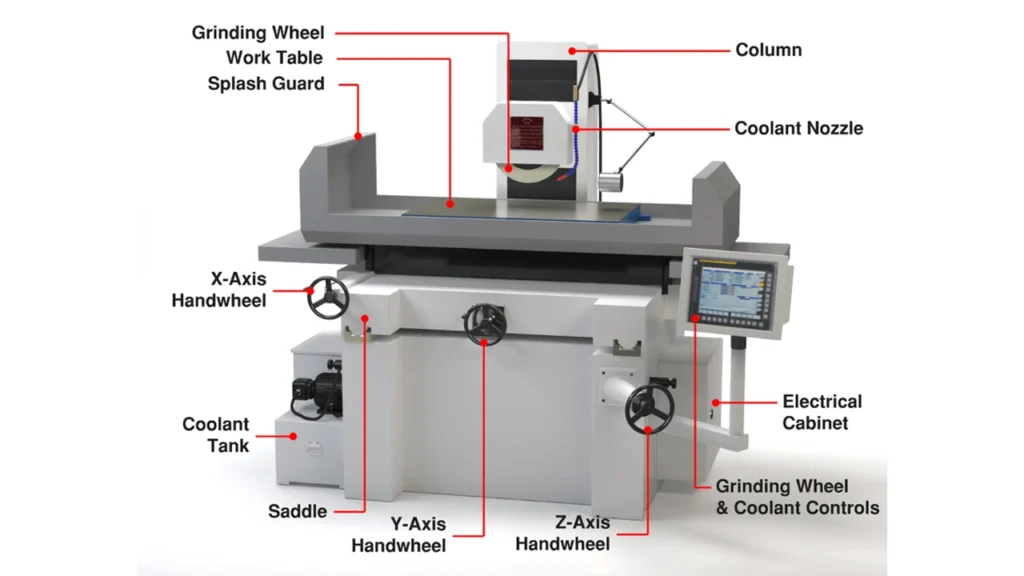
How Does a Grinding Machine Work?
- The workpiece is secured on the worktable or rotating chuck.
- The grinding wheel rotates at high speed.
- The workpiece is fed into the grinding wheel under controlled pressure.
- Abrasive particles remove material to achieve a precise finish.
- Coolants reduce heat, preventing workpiece distortion and wheel wear.
Key Applications of Grinding Machines
- Metalworking & Manufacturing → Achieves tight tolerances and ultra-smooth finishes for precision components.
- Aerospace Industry → Used for grinding turbine blades, landing gear parts, and aircraft engine components.
- Automotive Industry → Produces cylindrical engine parts, gears, and transmission components.
- Tool & Die Making → Sharpens and reshapes cutting tools and dies for manufacturing.
- Medical Industry → Creates high-precision surgical tools and implants with smooth finishes.
Final Summary: Grinding Machine
A grinding machine is a precision machine tool used for removing material, improving dimensional accuracy, and achieving fine surface finishes. By using abrasive wheels or belts, these machines produce high-precision components with tight tolerances. Essential in metalworking, automotive, aerospace, and tool manufacturing, grinding machines range from manual models to advanced CNC-controlled systems, ensuring superior part quality and production efficiency.
5. Electrical Discharge Machine (EDM)
What Is an Electrical Discharge Machine (EDM)?
An Electrical Discharge Machine (EDM) is a non-contact machine tool that removes material using electrical discharges (sparks) instead of physical cutting tools. EDM is ideal for machining hard metals, complex shapes, and fine details that would be difficult to achieve with traditional cutting methods. By using controlled electrical sparks between an electrode and the workpiece, EDM ensures high precision, minimal mechanical stress, and intricate detailing, making it essential in industries like aerospace, medical, and toolmaking.
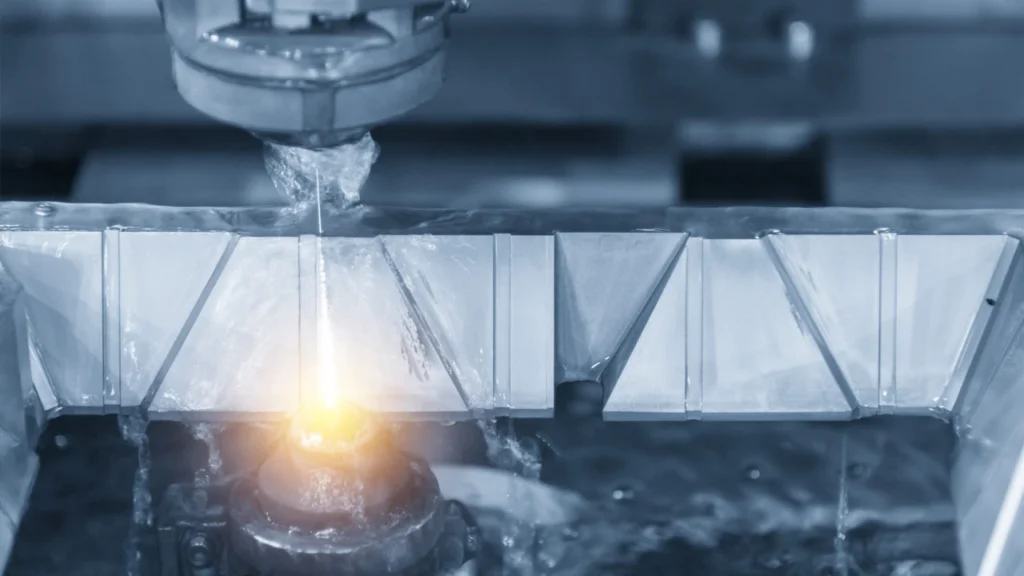
Types of Electrical Discharge Machines (EDM)
- Wire EDM (Wire-Cut EDM) → Uses a thin, continuously fed wire to create precise cuts and contours.
- Sinker EDM (Die-Sinking EDM) → Uses a custom-shaped electrode to imprint detailed cavities.
- Hole-Drilling EDM → Creates high-precision micro holes in hard metals.
- CNC EDM → Fully automated EDM controlled by pre-programmed CNC instructions for high precision and repeatability.
Main Components of an EDM Machine & Their Functions
1. Electrode – The tool that generates electrical discharges to remove material.
- Acts as the cutting tool in EDM machining.
- Made of copper, graphite, tungsten, or brass, depending on the application.
- Shapes and sizes vary based on the machining process (e.g., wire for Wire EDM, solid shapes for Sinker EDM).
2. Workpiece & Dielectric Fluid – Crucial for material removal and insulation.
- The workpiece must be electrically conductive (e.g., steel, titanium, carbide).
- Dielectric fluid (oil or deionized water) cools the process, prevents arcing, and flushes debris away.
- Maintains a stable spark gap and enhances machining precision.
3. Servo Control System – Maintains a constant distance between the electrode and workpiece.
- Prevents direct contact, ensuring sparks occur at the right distance.
- Dynamically adjusts the electrode position to maintain consistent material removal.
- Crucial for automation and high-precision machining.
4. Power Supply Unit – Controls the electrical discharge and spark generation.
- Converts DC power into controlled pulses to create the spark.
- Regulates voltage, frequency, and duration for different materials and machining speeds.
- Determines material removal rate, surface finish, and tool wear.
5. CNC Control Panel (for CNC EDM Machines) – Automates the machining process.
- Pre-programs electrode movement, depth, and cutting path.
- Improves repeatability, accuracy, and efficiency in mass production.
- Advanced systems include AI-driven optimization for reduced tool wear and energy efficiency.
6. Filtration & Debris Removal System – Maintains clean dielectric fluid.
- Filters out metal particles and debris generated during machining.
- Prevents contamination of the dielectric fluid, ensuring consistent machining performance.
- Essential for long EDM lifespan and high-precision results.
7. Worktable & Clamping System – Secures the workpiece in place.
- Designed for rigid, vibration-free holding of parts during machining.
- Adjustable for multi-axis movement, improving flexibility in complex shapes.
- Uses fixtures and vises for repeatable accuracy.
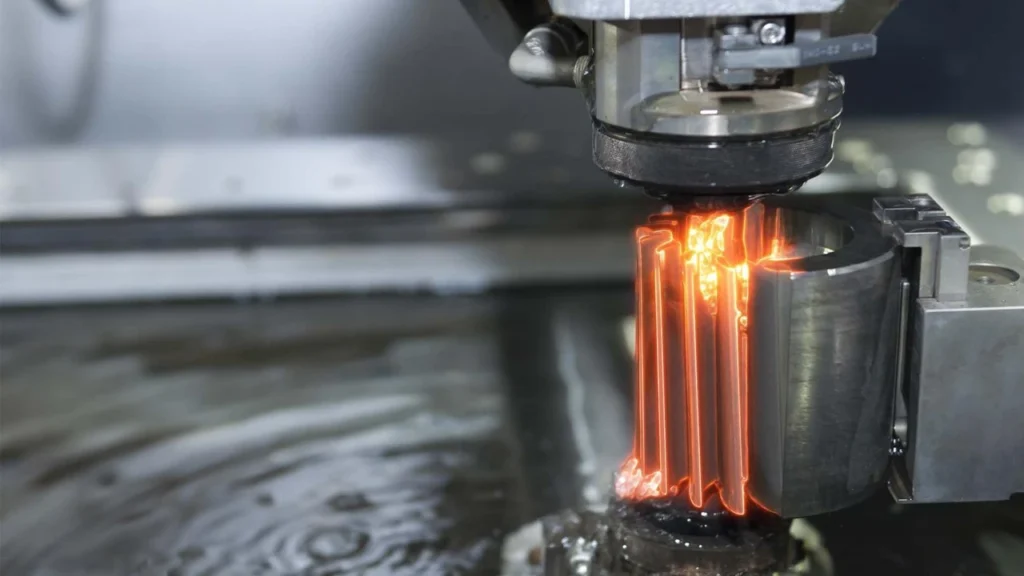
How Does an EDM Machine Work?
- The workpiece and electrode are submerged in dielectric fluid.
- A high-voltage electrical spark is generated between the electrode and workpiece.
- The spark erodes material, forming the desired shape without physical contact.
- Dielectric fluid cools the area and flushes away tiny metal particles.
- The process continues until the final shape is achieved with extreme precision.
Applications of Electrical Discharge Machines (EDM)
- Aerospace & Defense → Machining heat-resistant alloys for turbine blades and aircraft components.
- Medical Industry → Producing surgical implants and micro-scale medical tools.
- Tool & Die Making → Creating molds, dies, and extrusion tools with extreme accuracy.
- Automotive Industry → Manufacturing fuel injection components, transmission gears, and engine parts.
- Electronics Industry → Precision machining of circuit board components and micro-connectors.
Summary: Electrical Discharge Machine (EDM)
An EDM machine is a non-traditional machining tool that uses electrical discharges to remove material and create intricate, high-precision parts. Unlike conventional machining, EDM does not use physical force, making it ideal for hard metals, fine details, and delicate geometries. Industries like aerospace, medical, and toolmaking rely on EDM for precision manufacturing.
6. CNC Plasma Cutting Machine (High-Speed Metal Cutting with Ionized Gas)
What Is a CNC Plasma Cutting Machine?
A CNC plasma cutting machine is a thermal cutting machine tool that uses a high-temperature plasma arc to cut through electrically conductive materials like steel, aluminum, and copper. Controlled by CNC (Computer Numerical Control) technology, these machines offer precise, fast, and efficient cutting for industries like metal fabrication, shipbuilding, and automotive manufacturing.
Unlike mechanical cutting tools, plasma cutting melts and blows away material using an ionized gas stream, allowing it to cut through thick metals quickly and accurately with minimal material distortion.
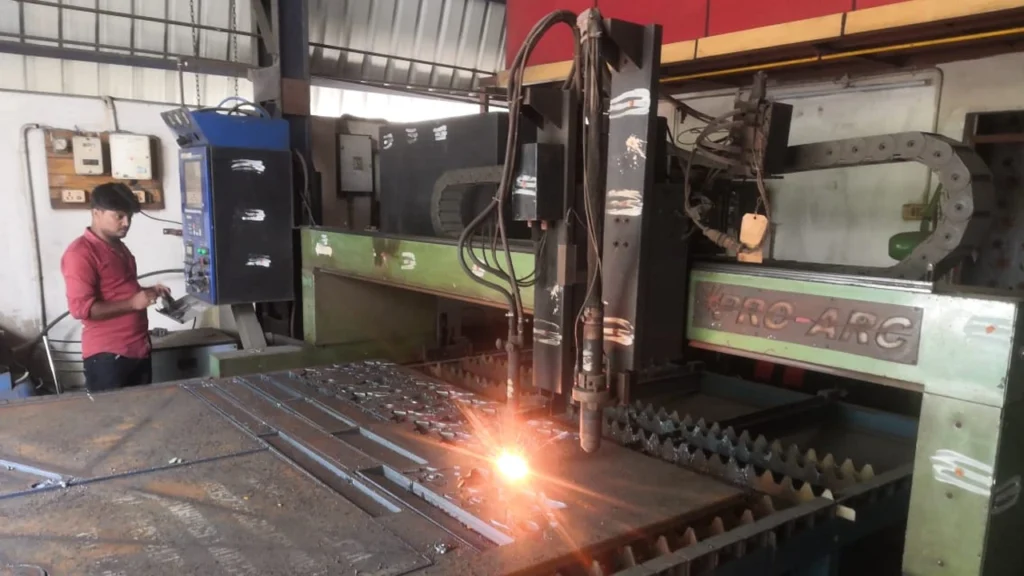
Types of CNC Plasma Cutting Machines
- 2D Plasma Cutting Machine → Cuts flat sheets and plates with high precision.
- 3D Plasma Cutting Machine → Can cut at different angles for bevels and weld prep.
- Tube & Pipe Plasma Cutting Machine → Specializes in cutting cylindrical workpieces.
- High-Definition Plasma Cutting Machine → Offers superior edge quality with minimal dross.
- CNC Plasma Gantry Machine → Used for large-scale industrial metal cutting.
Main Components of a CNC Plasma Cutting Machine & Their Functions
1. Plasma Torch – The core cutting tool that generates the plasma arc.
- Contains electrodes that ionize gas to create a high-energy arc.
- Uses gases like compressed air, nitrogen, oxygen, or argon-hydrogen to sustain the plasma.
- Moves along a CNC-controlled toolpath to execute precise cuts.
2. CNC Controller – The brain of the machine that automates cutting operations.
- Converts CAD/CAM designs into machine instructions.
- Controls torch movement, cutting speed, and pierce height.
- Ensures repeatability and accuracy for mass production.
3. Power Supply – Generates the necessary energy to create the plasma arc.
- Provides high-voltage electricity to ionize the gas.
- Controls current intensity, which affects cutting thickness and speed.
- Helps maintain stable arc performance for consistent cuts.
4. Gas Supply System – Feeds gas to the plasma torch for cutting.
- Uses gases like oxygen, nitrogen, argon, or compressed air.
- Controls gas flow rate and pressure for different materials and cutting thicknesses.
- Affects cut quality, edge smoothness, and dross formation.
5. Cutting Table (Slatted Bed) – Supports the metal workpiece during cutting.
- Designed with heat-resistant slats to minimize heat distortion.
- Some advanced tables include water beds to reduce smoke and sparks.
- Can be CNC-controlled to move during cutting for increased precision.
6. Exhaust & Fume Extraction System – Removes smoke, dust, and metal fumes.
- Essential for worker safety and environmental compliance.
- Some machines use water tables to capture airborne particles.
How Does a CNC Plasma Cutting Machine Work?
- The workpiece is placed on the cutting table.
- The CNC controller directs the plasma torch along the programmed toolpath.
- The power supply ionizes the gas, creating a high-temperature plasma arc.
- The plasma jet melts the metal, while the high-velocity gas blows away molten material.
- The cut is completed, leaving clean, precise edges with minimal finishing required.
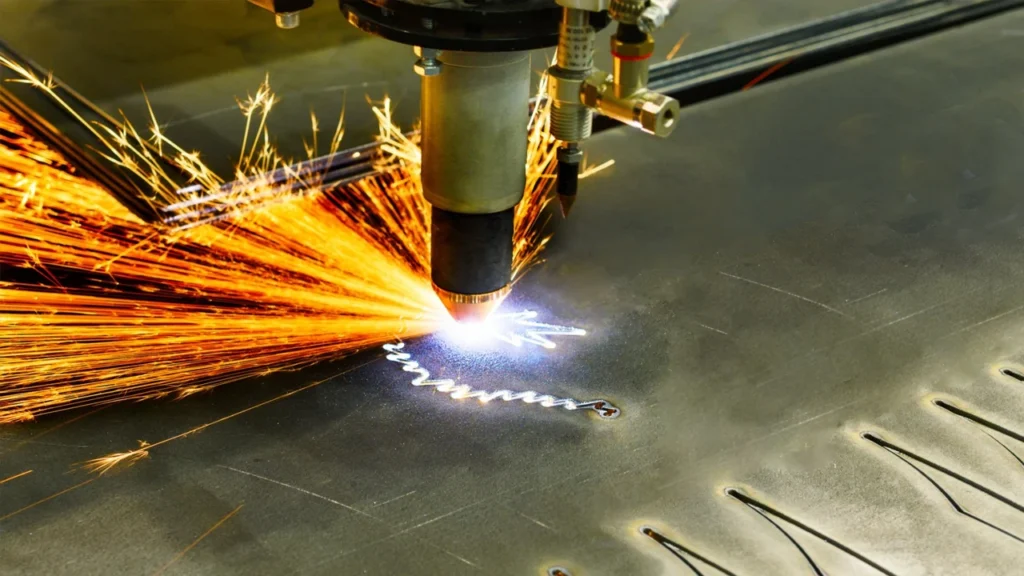
Applications of CNC Plasma Cutting Machines
- Metal Fabrication & Welding Prep → Cuts precise metal sheets for structural fabrication.
- Shipbuilding & Heavy Machinery → Produces large steel components with minimal waste.
- Automotive & Aerospace → Used for chassis parts, brackets, and engine components.
- Construction & Infrastructure → Creates steel beams, supports, and piping components.
- Artistic Metal Cutting & Signage → Used for custom metal signs and decorative designs.
Summary: CNC Plasma Cutting Machine
A CNC plasma cutting machine is a high-speed, precision cutting tool that uses an ionized gas arc to melt and remove metal. Ideal for cutting thick, conductive materials, it is widely used in fabrication, automotive, aerospace, and construction industries. With advanced CNC automation, plasma cutters deliver clean, accurate cuts with minimal material waste.
7. CNC Water Jet Cutting Machine (Precision Cutting with High-Pressure Water)
What Is a CNC Water Jet Cutting Machine?
A CNC water jet cutting machine is a high-precision cutting tool that uses a high-pressure stream of water, sometimes mixed with abrasives, to cut a wide range of materials. Unlike thermal cutting methods (such as plasma and laser cutting), water jet cutting is a cold cutting process, meaning it does not generate heat, preventing material distortion or warping.
Water jet cutting is highly versatile, capable of cutting metals, composites, stone, glass, rubber, and even food products with extreme precision. This makes it widely used in aerospace, automotive, architectural, and custom manufacturing industries.
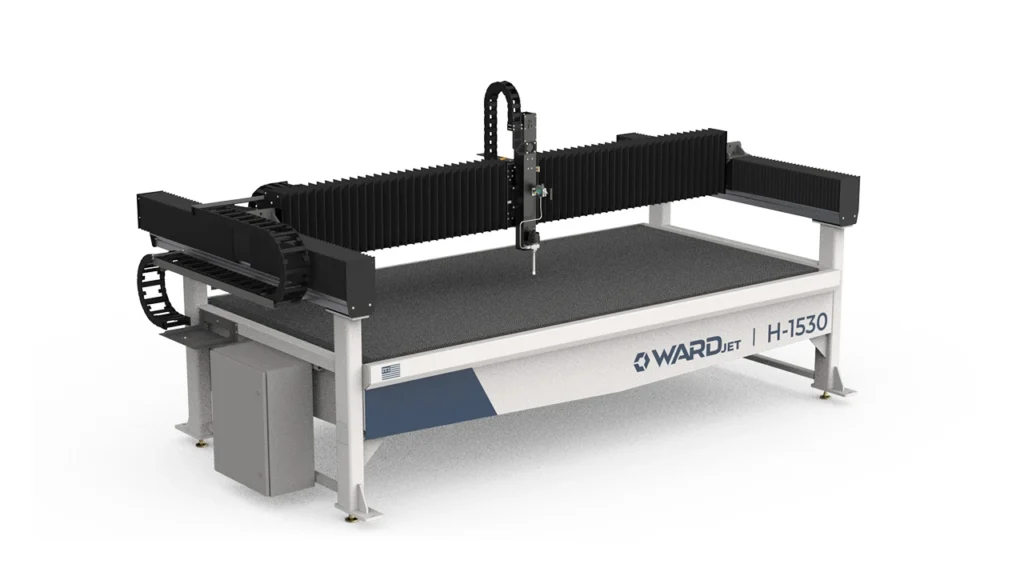
Types of CNC Water Jet Cutting Machines
- Pure Water Jet Cutting Machine → Uses only water, ideal for soft materials like rubber, foam, and textiles.
- Abrasive Water Jet Cutting Machine → Mixes abrasive particles with water for cutting metals, ceramics, and composites.
- 5-Axis Water Jet Cutting Machine → Allows multi-angle cutting for complex geometries.
- Micro Water Jet Cutting Machine → Used for precision micro-cutting in electronics and medical applications.
Main Components of a CNC Water Jet Cutting Machine & Their Functions
1. High-Pressure Pump – Generates water pressure for cutting.
- Uses intensifier pumps or direct drive pumps to create pressures up to 90,000 PSI.
- Determines cutting speed and thickness capacity.
2. Cutting Head & Nozzle – Directs the water stream for precision cutting.
- Uses a tiny jewel orifice (diamond, ruby, or sapphire) to focus the water stream.
- In abrasive water jet cutting, garnet or aluminum oxide is mixed into the water stream to cut harder materials.
3. CNC Controller – Automates and controls the cutting process.
- Converts CAD/CAM designs into precise toolpaths.
- Controls water pressure, nozzle speed, and cutting angles.
4. Abrasive Delivery System – Feeds abrasive materials into the water stream.
- Essential for cutting metals, glass, ceramics, and composite materials.
- Controls abrasive flow rate to optimize cutting speed and precision.
5. Worktable & Catcher Tank – Supports the material and absorbs excess water.
- The slatted worktable holds the workpiece in place.
- The catcher tank captures and recycles water, reducing waste.
6. Filtration & Recycling System – Maintains water quality and efficiency.
- Filters out used abrasives and metal particles.
- Helps reduce operational costs and environmental impact.
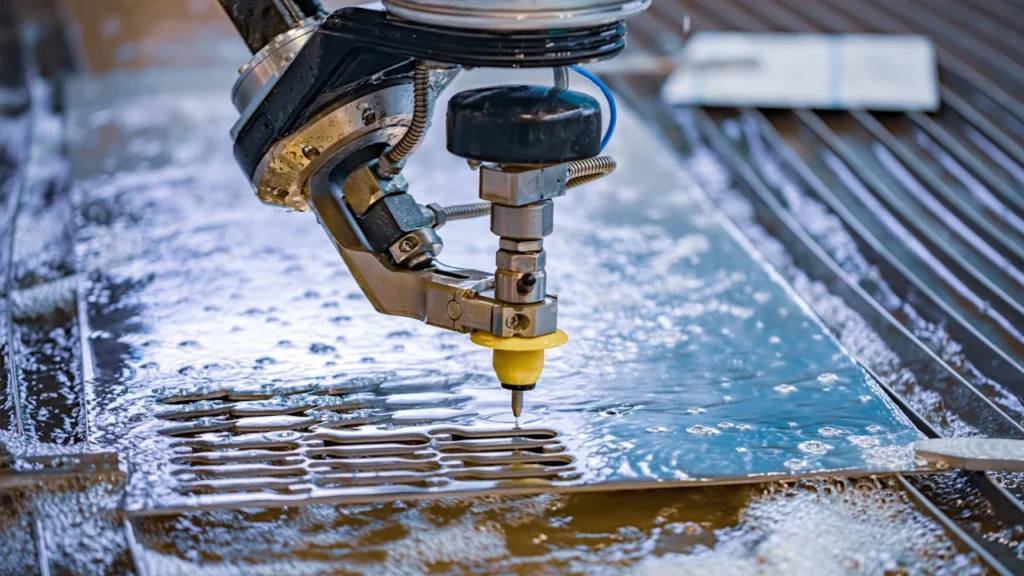
How Does a CNC Water Jet Cutting Machine Work?
- The high-pressure pump generates water pressure, up to 90,000 PSI.
- Water flows through a tiny nozzle, creating a high-speed water stream.
- For hard materials, abrasives are mixed into the stream to enhance cutting power.
- The CNC system guides the cutting head, following a precise toolpath.
- Water and debris are collected in the catcher tank for filtration and recycling.
Applications of CNC Water Jet Cutting Machines
- Metal Fabrication → Cuts stainless steel, aluminum, titanium, and alloys without heat distortion.
- Aerospace & Defense → Used for cutting precision aircraft parts and composite materials.
- Automotive Industry → Produces car frames, brake components, and engine parts.
- Glass & Stone Processing → Cuts marble, granite, and glass for architectural and artistic designs.
- Food Industry → Used for cutting frozen food, meat, and baked goods with zero contamination.
Summary: CNC Water Jet Cutting Machine
A CNC water jet cutting machine is a cold-cutting tool that uses high-pressure water to cut a variety of materials without heat damage. With pure water jet cutting for soft materials and abrasive water jet cutting for metals and composites, these machines offer high precision and versatility across aerospace, automotive, fabrication, and architectural industries.
8. CNC Boring Machine (Precision Machining for Large Workpieces)
What Is a CNC Boring Machine?
A CNC boring machine is a high-precision machine tool designed to enlarge existing holes in a workpiece using a rotating cutting tool (boring bar). Unlike drilling machines that create new holes, boring machines refine and increase hole diameter with extreme accuracy. CNC boring machines are essential for machining engine blocks, industrial equipment, heavy-duty components, and precision aerospace parts.
CNC control allows for automated, multi-axis boring, making these machines highly efficient, repeatable, and capable of handling large, heavy workpieces.
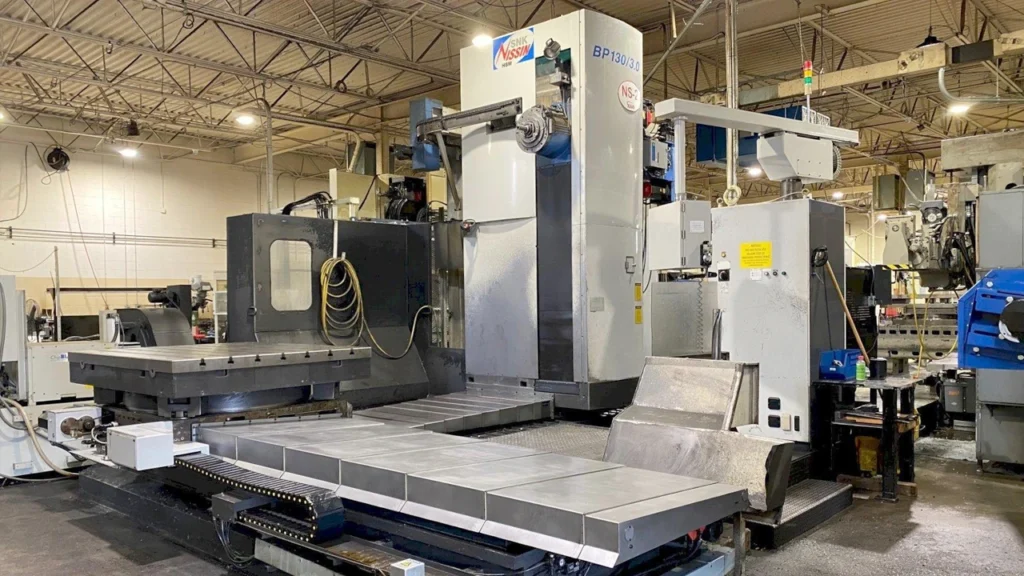
Types of CNC Boring Machines
- Horizontal Boring Machine → Ideal for large, heavy parts like engine blocks, turbines, and industrial equipment.
- Vertical Boring Machine → Best for boring holes in large, round components like wheel hubs and gear housings.
- Jig Boring Machine → Ultra-precise for fine-tolerance hole boring in aerospace and high-precision applications.
- Table-Type Boring Machine → Has a movable worktable, ideal for machining different angles and depths.
- Floor-Type Boring Machine → Used for very large parts that cannot fit on a standard worktable.
Main Components of a CNC Boring Machine & Their Functions
1. Boring Head & Boring Bar – Performs the material removal.
- The boring bar holds and rotates the cutting tool.
- The boring head adjusts for precise hole size control.
- CNC controls allow for programmable tool positioning.
2. Spindle & Drive System – Provides rotational power to the cutting tool.
- Spindle speed and feed rate are optimized for different materials.
- High-torque motors ensure consistent and stable machining.
3. CNC Control Panel – Automates the boring process.
- Converts CAD/CAM designs into programmed tool movements.
- Controls multi-axis positioning for precise hole finishing.
4. Worktable & Fixtures – Secures large, heavy workpieces.
- Heavy-duty clamps and fixtures hold engine blocks, gear housings, and structural components.
- Can be fixed or rotating, depending on machine configuration.
5. Coolant & Chip Removal System – Maintains machining precision.
- Coolant reduces heat buildup and prolongs tool life.
- Chip conveyors remove metal shavings and debris.
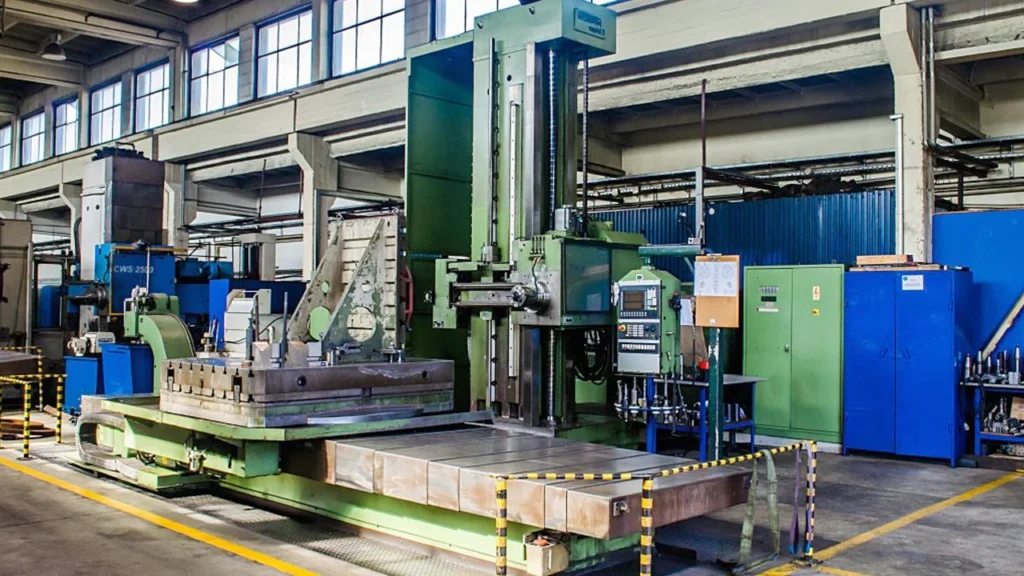
How Does a CNC Boring Machine Work?
- The workpiece is clamped securely onto the worktable.
- The CNC controller moves the boring tool to the programmed location.
- The spindle rotates the boring bar, cutting away material to enlarge the hole.
- Coolant flows to prevent overheating and ensure a smooth finish.
- The process repeats until the final precise bore diameter is reached.
Applications of CNC Boring Machines
- Aerospace & Defense → Machining aircraft engine components, missile casings, and landing gear housings.
- Automotive Industry → Used for engine blocks, transmission cases, and cylinder heads.
- Heavy Machinery & Industrial Equipment → Creates precision holes for hydraulic systems, turbines, and pumps.
- Shipbuilding & Marine Industry → Boring large holes in ship engine parts and structural components.
- Oil & Gas Industry → Used for pipeline connectors, drilling equipment, and pressure vessels.
Summary: CNC Boring Machine
A CNC boring machine is a precision machine tool designed to enlarge existing holes in large workpieces with high accuracy and efficiency. Used in automotive, aerospace, heavy machinery, and industrial equipment manufacturing, these machines are critical for creating perfectly machined bores in engine blocks, turbines, and large structural components.
9. CNC Gear Machines (Precision Gear Manufacturing for Industry Applications)
What Are CNC Gear Machines?
CNC gear machines are specialized machine tools designed for cutting, shaping, grinding, and finishing gears with high precision and efficiency. Gears are crucial components in automotive, aerospace, robotics, heavy machinery, and power transmission systems. These machines ensure that gear teeth are accurately formed, aligned, and finished for smooth and reliable mechanical operation.
CNC-controlled gear machines increase productivity, minimize errors, and improve consistency compared to traditional gear manufacturing methods.

Types of CNC Gear Machines
- CNC Gear Hobbing Machine → Uses a rotating hob cutter to progressively cut external gears. Best for spur, helical, and worm gears.
- CNC Gear Shaping Machine → Uses a reciprocating shaper cutter for internal and external gear cutting. Ideal for internal gears and splines.
- CNC Gear Grinding Machine → Finishes and refines gear teeth for high-precision applications. Used in aerospace, robotics, and high-speed transmissions.
- CNC Gear Milling Machine → Uses a rotary cutter to machine gears with complex profiles. Best for custom and prototype gear designs.
- CNC Bevel Gear Cutting Machine → Specializes in machining bevel and spiral bevel gears for differentials and gearboxes.
Main Components of CNC Gear Machines & Their Functions
1. Gear Cutting Tool (Hob, Shaper Cutter, or Grinding Wheel) – Forms gear teeth.
- Hob cutters are used in gear hobbing machines to progressively cut gear teeth.
- Shaper cutters are used in gear shaping machines for internal and external gear cutting.
- Grinding wheels in gear grinding machines refine gear teeth for superior surface quality.
2. Worktable & Spindle – Holds and rotates the gear blank.
- Ensures synchronized movement between the cutting tool and the workpiece.
- Supports various gear sizes and profiles.
3. CNC Control Panel – Automates and synchronizes the cutting process.
- Converts gear design specifications into precise cutting commands.
- Controls tool movement, spindle rotation, and cutting speed for different gear types.
4. Tailstock & Steady Rest – Provides stability during machining.
- Supports longer shafts or large-diameter gears to prevent vibration.
- Ensures precision in gear tooth alignment.
5. Coolant & Chip Management System – Maintains cutting efficiency.
- Lubricates cutting tools, reducing wear and extending tool life.
- Removes metal chips and debris, ensuring a clean machining environment.
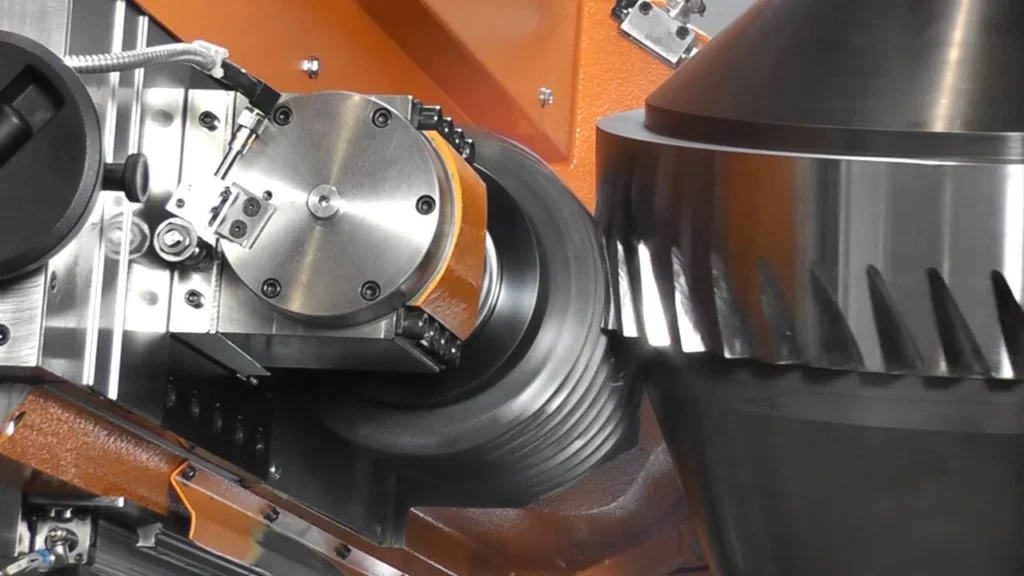
How Do CNC Gear Machines Work?
- The gear blank is clamped onto the worktable.
- The CNC system guides the cutting tool along the programmed path.
- The tool progressively cuts or grinds the gear teeth, depending on the machine type.
- Coolant is applied to prevent overheating and improve cutting precision.
- The final gear is inspected, ensuring perfect tooth alignment and meshing.
Applications of CNC Gear Machines
- Automotive Industry → Produces transmission gears, differential gears, and axle gears for cars and trucks.
- Aerospace & Defense → Manufactures high-precision gears for jet engines, landing gears, and navigation systems.
- Heavy Machinery & Industrial Equipment → Cuts large-diameter gears for mining, construction, and manufacturing equipment.
- Robotics & Automation → Creates precision gears for robotic arms, actuators, and motion control systems.
- Wind & Renewable Energy → Used for gearboxes in wind turbines and hydroelectric generators.
Summary: CNC Gear Machines
CNC gear machines are essential tools for precision gear manufacturing, ensuring high accuracy, efficiency, and repeatability in automotive, aerospace, robotics, and industrial machinery. With CNC automation, these machines can hob, shape, grind, and mill gears to meet strict industry standards for smooth operation and durability.
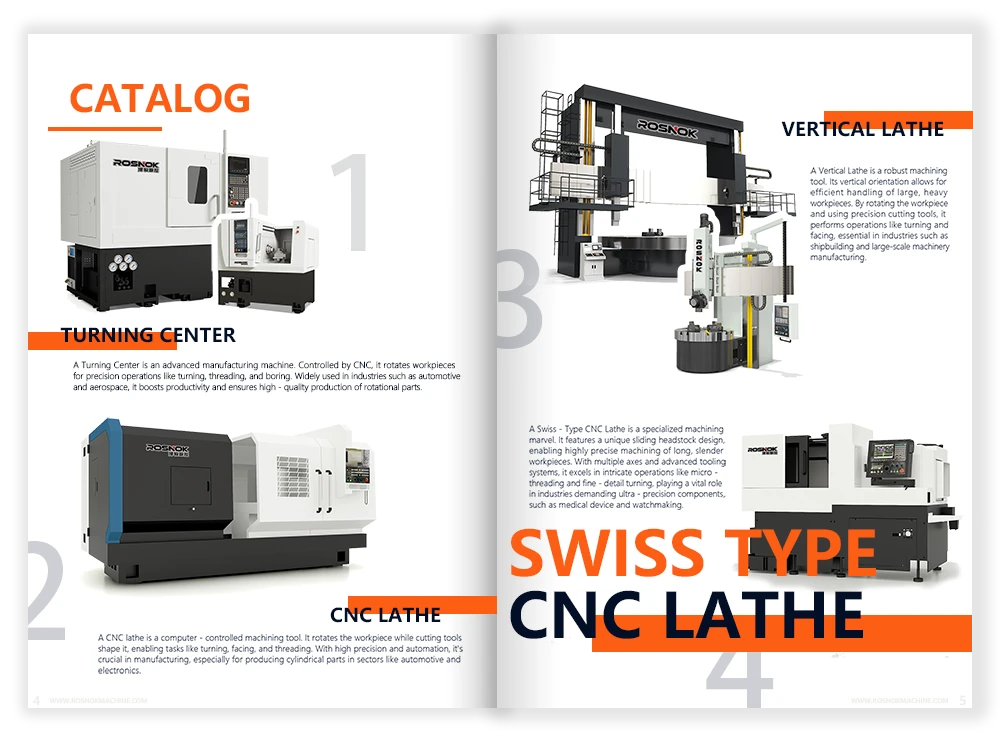
10. Planing Machine (Precision Surface Machining for Large Workpieces)
What Is a Planing Machine?
A planing machine is a heavy-duty machine tool used to machine large, flat surfaces by moving a cutting tool across a workpiece in a linear motion. Unlike milling machines, which use rotary cutters, planers use single-point cutting tools to create highly accurate, smooth, and straight surfaces.
Planing machines are widely used in heavy industries, including shipbuilding, locomotive manufacturing, steel fabrication, and construction, where large metal and structural components require high-precision machining.
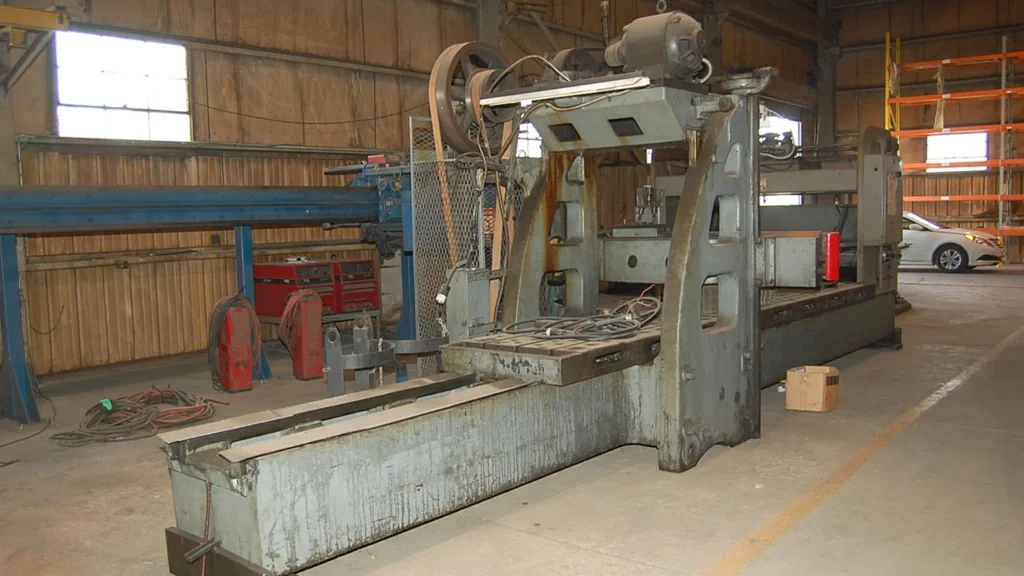
Types of Planing Machines
- Open-Side Planing Machine → Has a single-column design, allowing machining of extra-wide workpieces.
- Double-Column Planing Machine → Uses two vertical columns, providing better support for long, heavy materials.
- Edge Planing Machine → Specially designed for machining the edges of large metal plates.
- Gantry Planing Machine → Features a gantry structure, enabling high-precision machining of oversized workpieces.
- CNC Planing Machine → Offers automated, high-precision machining with programmable tool paths.
Main Components of a Planing Machine & Their Functions
1. Planer Bed & Worktable – Supports and moves the workpiece.
- The worktable slides back and forth, moving the workpiece under the cutting tool.
- Heavy-duty rails and guides ensure precision and stability.
2. Cutting Tool & Tool Head – Removes material from the surface.
- Uses single-point or multi-point cutting tools for precise machining.
- Cutting tools can be adjusted for different depths and feed rates.
3. Column & Crossrail – Provides vertical and horizontal tool movement.
- Columns support the tool head, allowing height adjustments.
- The crossrail enables lateral positioning of the cutting tool.
4. Power System & Feed Mechanism – Controls movement and speed.
- Hydraulic, mechanical, or CNC-driven motors provide movement.
- Controls the speed and stroke of the worktable for uniform machining.
5. Chip Removal & Lubrication System – Improves efficiency and tool life.
- Lubricants reduce tool wear and overheating.
- Chip conveyors remove material debris, preventing tool damage.
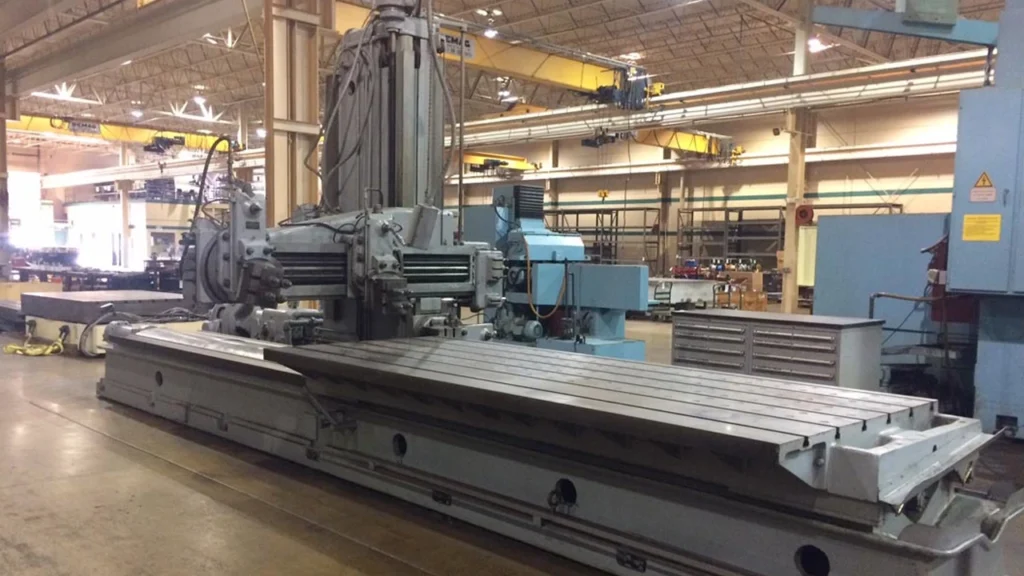
How Does a Planing Machine Work?
- The workpiece is secured onto the planing table.
- The cutting tool moves across the surface, removing material in a linear motion.
- The machine advances the cutting tool for each new pass.
- Lubrication is applied to maintain cutting efficiency and prevent overheating.
- The final machined surface is inspected, ensuring smoothness and dimensional accuracy.
Applications of Planing Machines
- Heavy Machinery Manufacturing → Machines large frames, steel plates, and industrial components.
- Shipbuilding Industry → Produces precision-machined ship hull sections.
- Locomotive & Railway Industry → Used for machining train chassis and structural parts.
- Construction & Infrastructure → Creates accurately machined beams, bridge components, and structural supports.
- Steel & Foundry Industry → Smooths and levels large castings and fabricated metal plates.
Summary: Planing Machine
A planing machine is a large-scale machine tool designed for precision machining of flat surfaces. It is widely used in heavy industry, shipbuilding, railway manufacturing, and structural fabrication. Whether manually operated or CNC-controlled, planers provide high accuracy, efficiency, and repeatability in machining large, heavy workpieces.
11. Shaping Machine (Precision Linear Machining for Flat Surfaces)
What Is a Shaping Machine?
A shaping machine is a machine tool used to cut, form, and shape flat surfaces, grooves, and slots using a reciprocating single-point cutting tool. Unlike milling machines that use rotary cutters, shaping machines use a linear motion to remove material, making them ideal for machining flat surfaces, keyways, and contoured profiles.
Shapers are commonly used in tool and die-making, metal fabrication, and maintenance workshops for low-volume precision machining.
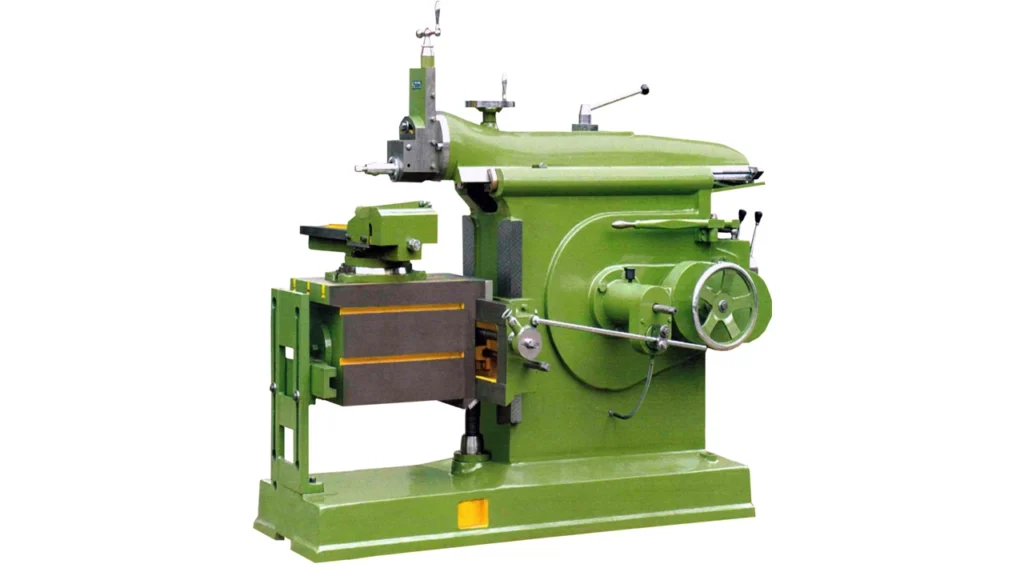
Types of Shaping Machines
- Horizontal Shaping Machine → The ram moves horizontally, best for machining flat surfaces.
- Vertical Shaping Machine → The ram moves vertically, ideal for internal keyways and slots.
- Universal Shaping Machine → Has adjustable worktable angles, allowing complex cuts.
- CNC Shaping Machine → Uses computerized automation for precision machining.
Main Components of a Shaping Machine & Their Functions
1. Ram & Cutting Tool – Moves back and forth to remove material.
- The ram holds the single-point cutting tool, which moves in a reciprocating motion.
- The cutting tool removes small amounts of material with each stroke.
2. Worktable & Vise – Holds and moves the workpiece.
- The table moves in a controlled feed motion to expose fresh material for cutting.
- Clamps and vises secure the workpiece, ensuring stability.
3. Feed Mechanism – Controls table movement.
- Adjusts cutting depth and feed rate for smooth and precise machining.
- Can be manually adjusted or CNC-controlled in modern shaping machines.
4. Base & Column – Supports the machine structure.
- Provides rigid support to minimize vibrations during machining.
5. Drive System – Controls cutting speed and stroke length.
- Uses hydraulic, mechanical, or CNC motors to regulate motion.
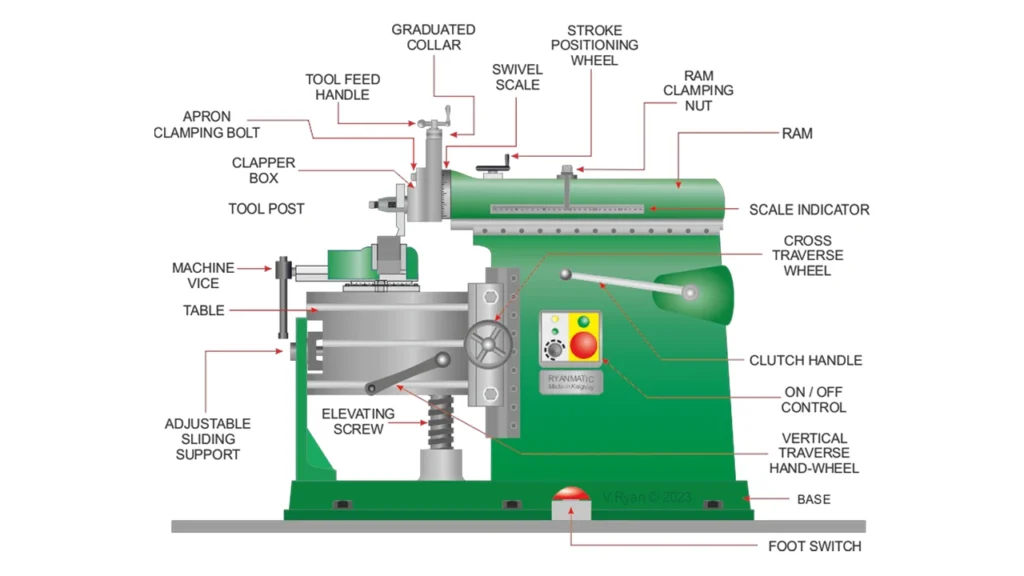
How Does a Shaping Machine Work?
- The workpiece is clamped onto the worktable.
- The cutting tool moves back and forth, removing material with each stroke.
- The worktable moves incrementally after each stroke for progressive cutting.
- The operator or CNC system adjusts feed rates for optimal surface finish.
- The finished part is inspected for dimensional accuracy and surface quality.
Applications of Shaping Machines
- Tool & Die Manufacturing → Creates precision slots, keyways, and flat surfaces in molds and dies.
- Metal Fabrication → Used for machining large metal sheets and flat components.
- Aerospace & Automotive → Produces engine parts, transmission components, and frames.
- Maintenance & Repair Shops → Used for custom shaping of replacement parts.
Summary: Shaping Machine
A broaching machine is a high-precision machine tool used to cut internal and external profiles, keyways, splines, and complex shapes in a single pass using a multi-toothed cutting tool called a broach. Unlike milling or shaping machines that gradually remove material, broaching machines perform fast, precise machining in one continuous motion, making them ideal for mass production of tight-tolerance components.
12. Broaching Machine (Precision Cutting for Internal & External Profiles)
What Is a Broaching Machine?
A broaching machine is a high-precision machine tool used to cut internal and external profiles, keyways, splines, and complex shapes in a single pass using a multi-toothed cutting tool called a broach. Unlike milling or shaping machines that gradually remove material, broaching machines perform fast, precise machining in one continuous motion, making them ideal for mass production of tight-tolerance components.
Broaching machines are commonly used in automotive, aerospace, medical, and industrial manufacturing, where precision machining is required.
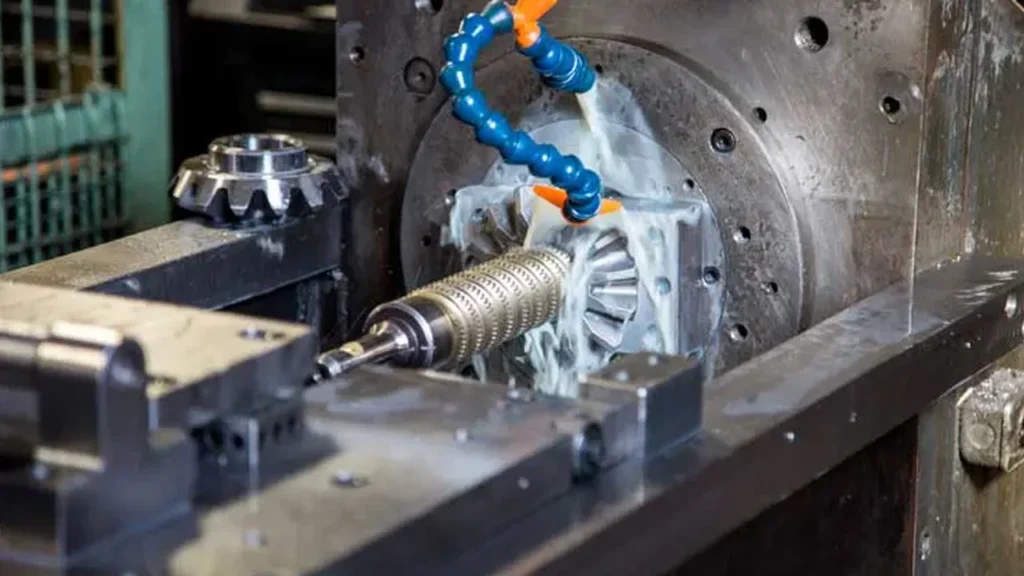
Types of Broaching Machines
Classification by Processing Object
- Internal Broaching Machine → Used for machining the inner surface of workpieces, such as holes, internal splines, and internal gears. Ideal for precision machining of automotive and aerospace components.
- External Broaching Machine → Designed for machining the outer surface of workpieces, such as external gears, flat surfaces, and keyways. Commonly used in gear manufacturing and industrial fabrication.
- Special Broaching Machine → Used for processing workpieces with unique shapes, such as pipe fittings, turbine blades, and non-standard profiles. Custom-built for specific applications in aerospace, medical, and defense industries.
Classification by Structural Form
- Vertical Broaching Machine → The broach moves vertically, making it suitable for processing heavier workpieces. Used for cutting deep internal features in thick or large components.
- Horizontal Broaching Machine → The broach moves horizontally, ideal for machining longer workpieces such as shafts, splines, and precision keyways. Commonly found in automotive and industrial gear production.
Main Components of a Broaching Machine & Their Functions
1. Broach Cutting Tool – The primary cutting element.
- A multi-toothed tool that progressively removes material in a single stroke.
- Can be custom-designed for keyways, splines, gears, or irregular profiles.
2. Workholding Fixture – Secures the workpiece.
- Holds shafts, gears, or metal plates securely during the cutting process.
- Ensures precise alignment and positioning for consistent machining.
3. Hydraulic or Mechanical Drive System – Powers the broaching process.
- Hydraulic broaching machines provide smooth and consistent cutting force.
- Mechanical broaching machines are used for high-speed, high-volume production.
4. CNC Control Panel (for CNC Broaching Machines) – Automates cutting operations.
- Controls broach speed, cutting depth, and feed rate for precise machining.
- Allows customized cutting paths and automated tool changes.
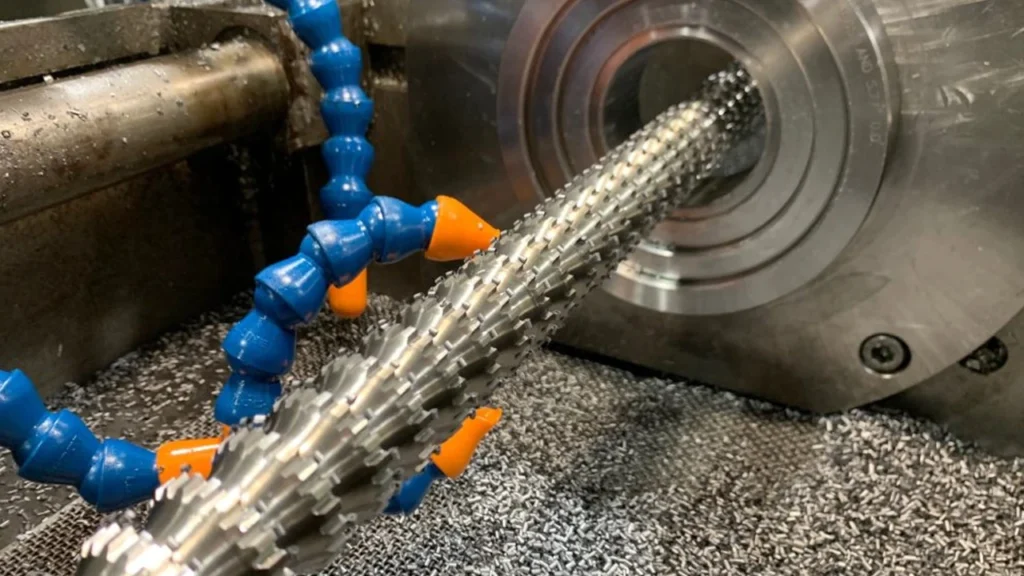
How Does a Broaching Machine Work?
- The workpiece is securely clamped into the machine.
- The broach tool moves linearly, removing material progressively in one continuous stroke.
- Each tooth on the broach removes a small amount of material, shaping the final profile.
- The machine retracts, and the finished part is removed for inspection.
- Quality control checks ensure the part meets precise tolerances.
Applications of Broaching Machines
Automotive Industry → Produces precision gears, keyways, and transmission components.
Aerospace & Defense → Used for machining turbine blades, engine parts, and structural aircraft components.
Industrial Machinery → Cuts splines, precision slots, and external profiles.
Medical Equipment → Used for manufacturing orthopedic implants, surgical tools, and medical instruments.
Summary: Broaching Machine
A broaching machine is a high-efficiency, precision-cutting tool used for machining internal and external profiles, keyways, and gears. It is widely used in automotive, aerospace, and industrial manufacturing, providing fast, accurate machining for complex shapes. Whether manual, hydraulic, or CNC-controlled, broaching machines ensure consistent quality and high-efficiency production.
13. Honing Machine (Precision Bore Finishing for High-Accuracy Applications)
What Is a Honing Machine?
A honing machine is a precision finishing machine tool used to refine the surface of bores, cylinders, and other round holes to extremely tight tolerances. It uses abrasive honing stones mounted on a rotating spindle, which oscillates inside the bore to improve its roundness, straightness, and surface finish.
Honing machines are widely used in automotive, aerospace, medical, and hydraulic component manufacturing, ensuring high-precision internal finishes for critical parts.
Types of Honing Machines
By Structural Design
- Horizontal Honing Machine → The honing tool moves horizontally, ideal for long tubes, engine cylinders, and hydraulic cylinders.
- Vertical Honing Machine → The honing tool moves vertically, best for large engine blocks, transmission parts, and deep bores.
By Operation
- Single-Pass Honing Machines → These machines finish a workpiece in a single pass of the honing tool, resulting in high production rates.
- Multi-Spindle Honing Machines → Equipped with multiple spindles that operate simultaneously, allowing for the honing of multiple workpieces at once, ideal for mass production.
- Blind Hole Honing Machines → Designed to hone holes that are closed at one end, ensuring precise bore finishing without damaging the bottom.
Main Components of a Honing Machine & Their Functions
1. Honing Tool & Abrasive Stones – The primary cutting element.
- Mounted on a rotating spindle that moves in an oscillating motion.
- Abrasives gradually remove material, improving surface finish and accuracy.
2. Workpiece Holding Fixture – Secures the part during honing.
- Ensures precise alignment and stability for uniform material removal.
- Used for cylinders, engine blocks, hydraulic components, and tubing.
3. Power Drive System – Controls honing spindle rotation and oscillation.
- Uses hydraulic, mechanical, or CNC-controlled motors for precision honing.
- Regulates speed, pressure, and feed rate for optimal surface finish.
4. Coolant & Lubrication System – Improves efficiency and tool life.
- Flushes away debris while reducing heat and tool wear.
- Uses oil- or water-based coolants to improve cutting performance.
5. CNC Control Panel (for CNC Honing Machines) – Automates honing operations.
- Pre-programmed parameters ensure consistent precision and repeatability.
- Ideal for mass production and high-tolerance applications.
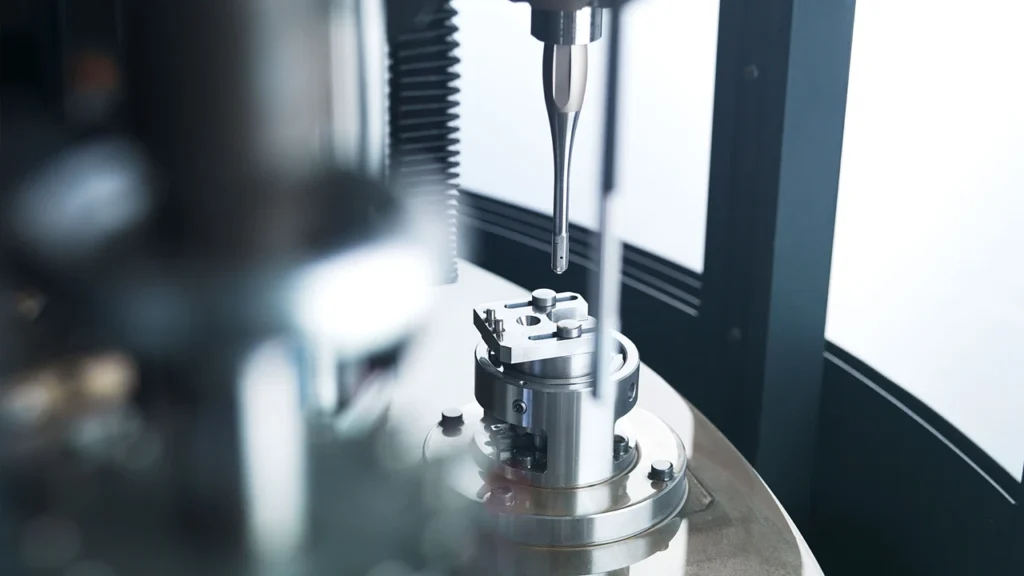
How Does a Honing Machine Work?
- The workpiece is clamped into the honing fixture.
- The honing tool rotates and oscillates inside the bore.
- Abrasive stones gradually remove material, refining the bore’s roundness and smoothness.
- Coolant is applied to improve cutting performance and prevent overheating.
- The finished bore is measured for accuracy before final inspection.
Applications of Honing Machines
- Automotive Industry → Finishing cylinder bores, pistons, and connecting rods for better performance.
- Aerospace & Defense → Producing hydraulic components, landing gear, and precision aircraft parts.
- Medical Equipment → Used for surgical tools, orthopedic implants, and high-precision tubing.
- Hydraulics & Pneumatics → Finishing valves, pumps, and cylinders for optimal fluid sealing.
Summary: Honing Machine
A honing machine is a precision finishing tool used for improving bore accuracy, roundness, and surface finish. It is widely used in automotive, aerospace, hydraulic, and medical industries to ensure tightly controlled tolerances. Whether single-pass, multi-spindle, or blind-hole honing, these machines provide high-efficiency, high-precision surface refinement.
14. Sawing Machine (Efficient Cutting for Raw Materials)
What Is a Sawing Machine?
A sawing machine is a machine tool used to cut raw materials such as metal, wood, plastic, and composites into precise shapes and sizes. Unlike manual saws, these machines provide high-speed, consistent cutting, improving efficiency and accuracy in industrial production.
Sawing machines are widely used in metal fabrication, construction, and automotive industries where materials need to be cut into specific dimensions before further machining.
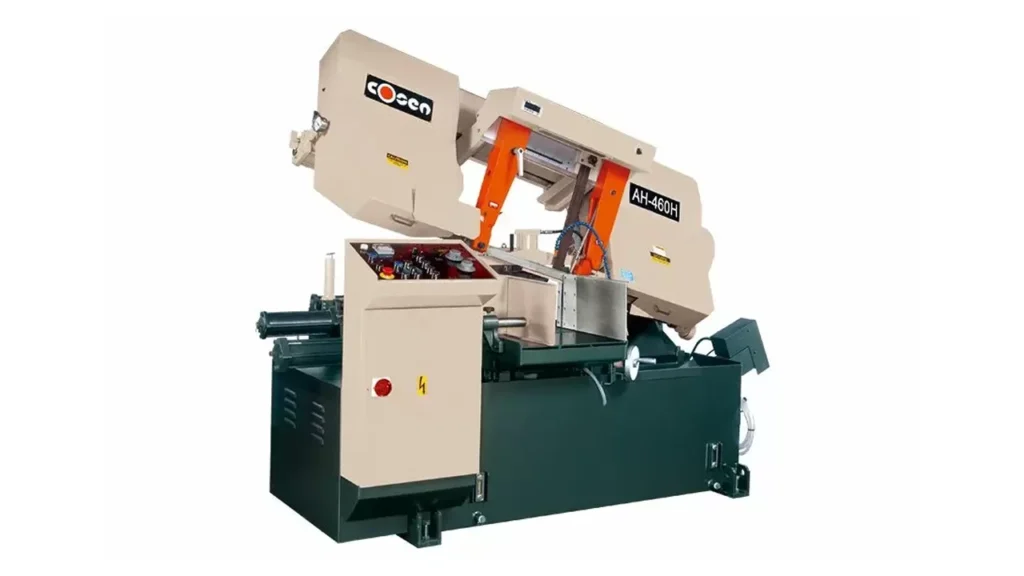
Types of Sawing Machines
- Bandsaw Machine → Uses a continuous-loop blade to cut metal, wood, and plastics with high efficiency.
- Circular Saw Machine → Features a rotating disc blade, ideal for precise and fast cutting of metal sheets and bars.
- Hacksaw Machine → Uses a reciprocating saw blade, mainly for metalworking and rough cuts.
- Cold Saw Machine → Designed for cutting metal with a high-speed toothed blade, leaving a clean, burr-free finish.
- Abrasive Saw Machine → Uses abrasive wheels instead of teeth, ideal for hard materials like steel, ceramics, and composites.
Main Components of a Sawing Machine & Their Functions
1. Saw Blade – The primary cutting tool.
- Can be continuous (bandsaw) or rotating (circular saw).
- Comes in different materials (carbide, bi-metal, diamond-coated) for specific applications.
2. Worktable & Clamping System – Holds the material in place.
- Provides a stable base for cutting, ensuring straight and accurate cuts.
- Adjustable clamps secure metal sheets, pipes, or wooden blocks during cutting.
3. Power Drive System – Controls blade movement.
- Uses electric motors or hydraulic drives to regulate blade speed and feed rate.
- Enables consistent cutting pressure for uniform material removal.
4. Coolant & Lubrication System – Improves cutting efficiency.
- Reduces heat and blade wear, ensuring smoother cuts and longer tool life.
- Common in metal-cutting saws to prevent overheating and blade dulling.
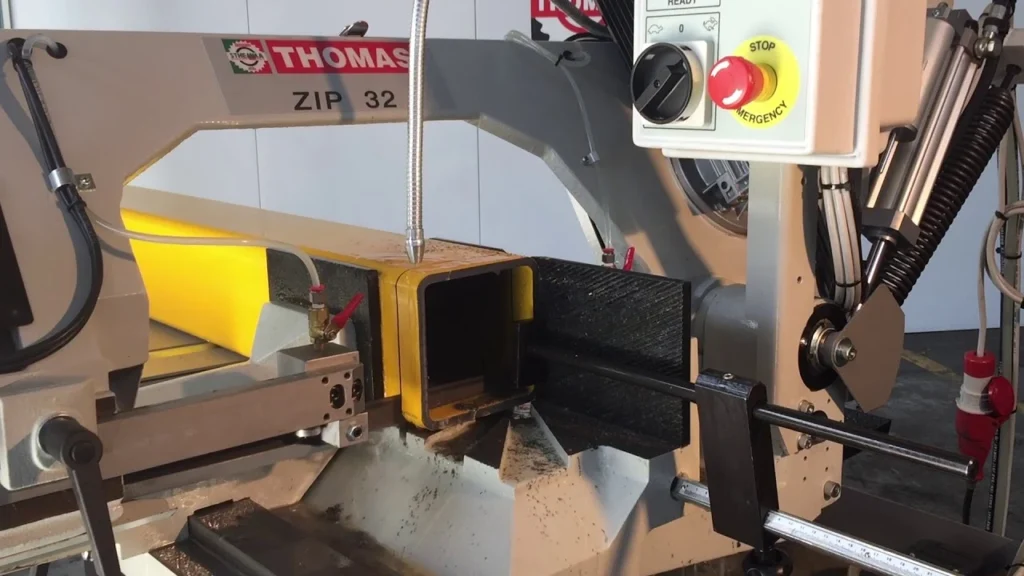
How Does a Sawing Machine Work?
- The material is securely clamped onto the worktable.
- The saw blade rotates or moves linearly, cutting through the material at a controlled speed.
- Coolant or lubrication is applied to improve cutting performance and blade life.
- Once the cut is complete, the blade retracts, and the finished piece is removed.
- The workpiece is inspected for size and accuracy before further processing.
Applications of Sawing Machines
- Metal Fabrication → Cutting steel bars, pipes, and structural components for manufacturing.
- Woodworking → Processing lumber, furniture parts, and decorative panels.
- Construction Industry → Cutting reinforcement bars (rebar), concrete blocks, and sheet metal.
- Automotive & Aerospace → Shaping chassis components, aluminum panels, and composite materials.
Summary: Sawing Machine
A sawing machine is an essential cutting tool in manufacturing, used for shaping raw materials like metal, wood, and plastic. It ensures precision, efficiency, and high-speed material removal in industries such as metal fabrication, automotive, and construction. Bandsaws, circular saws, and cold saws are among the most widely used sawing machines for high-precision industrial cutting.
15. Slotting Machine (Precision Internal Keyways & Slot Machining)
What Is a Slotting Machine?
A slotting machine is a vertical reciprocating machine tool designed for cutting internal keyways, slots, grooves, and complex profiles. Unlike a shaper machine, which moves a tool horizontally, a slotting machine operates vertically, making it ideal for internal machining and deep recesses in gears, pulleys, and other machine parts.
Slotting machines are widely used in automotive, aerospace, and general manufacturing industries where high-precision slot cutting is required.
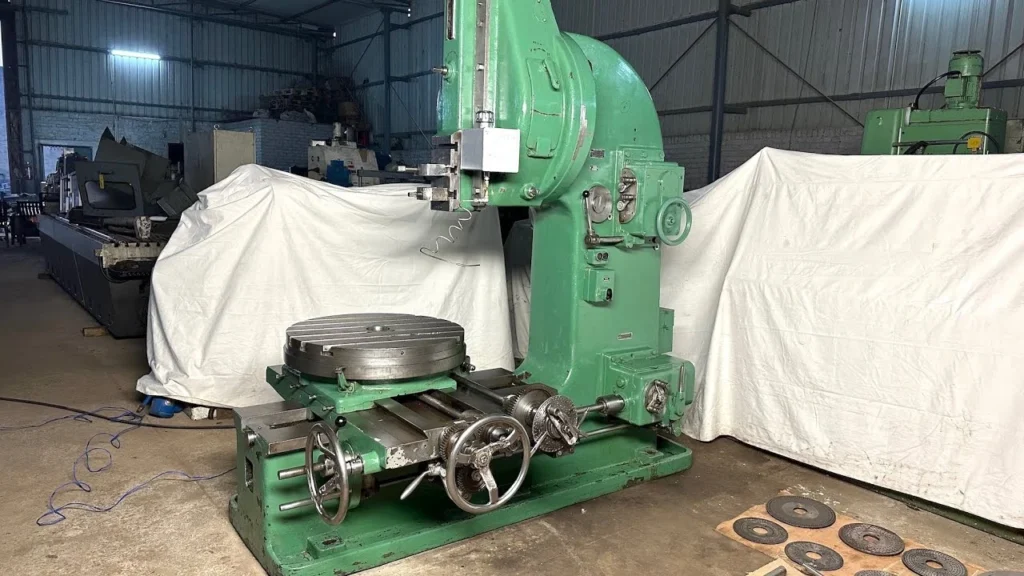
Types of Slotting Machines
By Drive Mechanism
- Crank-Type Slotting Machine → Uses a crank-driven system, ideal for general-purpose machining.
- Hydraulic Slotting Machine → Uses hydraulic power for high-speed and heavy-duty machining.
By Worktable Movement
- Standard Slotting Machine → Has a fixed worktable, best for simple keyways and slots.
- Universal Slotting Machine → The worktable tilts and rotates, allowing angular and curved slot cutting.
Main Components of a Slotting Machine & Their Functions
1. Ram & Cutting Tool – Performs the cutting operation.
- The ram holds the single-point cutting tool, moving it vertically in a reciprocating motion.
- The tool cuts material during the downward stroke and retracts during the upward stroke.
2. Worktable & Clamping System – Holds and secures the workpiece.
- The worktable moves radially, longitudinally, and vertically to position the workpiece correctly.
- The clamping system ensures stability during machining.
3. Feed Mechanism – Controls the cutting depth and direction.
- Adjusts the depth of cut for precision machining.
- Allows manual or automatic feed control.
4. Drive Mechanism – Powers the cutting tool movement.
- Uses gear-driven, hydraulic, or belt-driven systems to control the ram motion.
- Adjusts speed and stroke length for different materials.
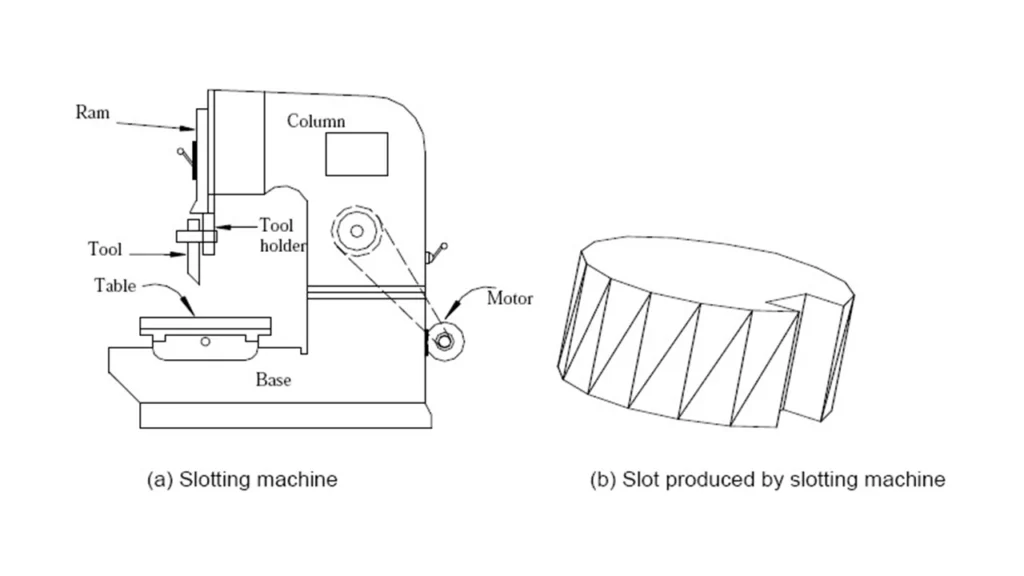
How Does a Slotting Machine Work?
- The workpiece is clamped onto the worktable.
- The cutting tool is positioned on the ram, aligned with the material.
- The ram moves downward, cutting the material in a vertical stroke.
- The tool retracts on the upward stroke, preventing unnecessary friction.
- The table moves incrementally, shaping the slot or groove with each pass.
Applications of Sawing Machines
- Metal Fabrication → Cutting steel bars, pipes, and structural components for manufacturing.
- Woodworking → Processing lumber, furniture parts, and decorative panels.
- Construction Industry → Cutting reinforcement bars (rebar), concrete blocks, and sheet metal.
- Automotive & Aerospace → Shaping chassis components, aluminum panels, and composite materials.
Summary: Slotting Machine
A slotting machine is a vertical reciprocating machine tool used for machining internal keyways, slots, and grooves. It is widely used in gear manufacturing, toolmaking, and metalworking industries. Whether crank-type or hydraulic, slotting machines provide high-precision machining for internal surfaces and recesses.
Importance of Machine Tools in Manufacturing
Why Are Machine Tools Essential?
Machine tools are the backbone of modern manufacturing, enabling industries to mass-produce high-precision components with efficiency and consistency. Without machine tools, manufacturing processes would be slow, imprecise, and labor-intensive, making large-scale industrial production impossible.
From automobiles to medical devices, aerospace components to heavy machinery, machine tools are involved in every stage of production. They allow for the cutting, shaping, grinding, drilling, and forming of materials with extreme precision, ensuring repeatability and quality control in high-volume manufacturing.
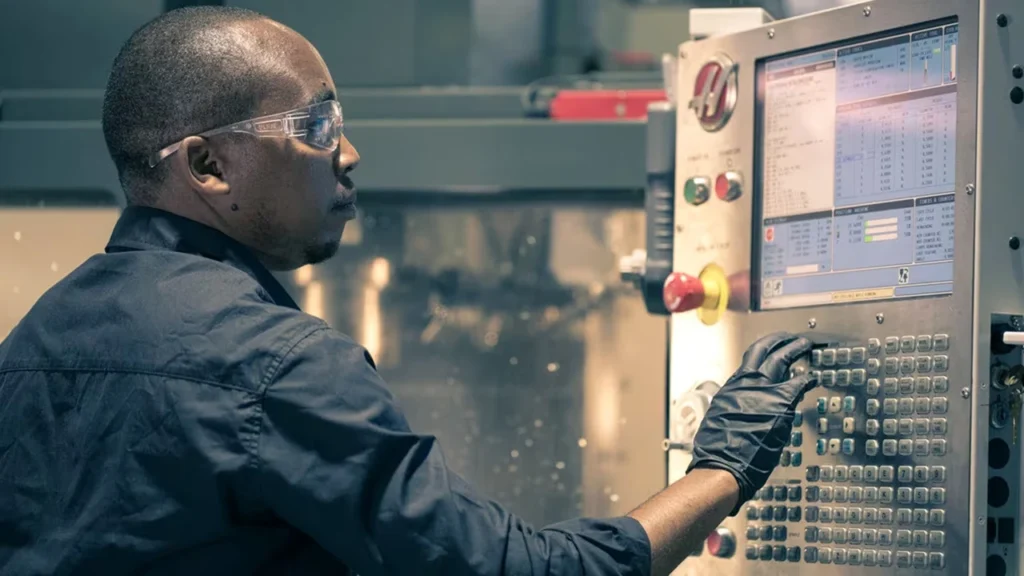
Key Roles of Machine Tools in Manufacturing
1. Precision & Accuracy in Production
- Machine tools ensure tight tolerances and dimensional accuracy, reducing errors.
- CNC-controlled machines offer sub-micron precision, essential for aerospace and medical industries.
- High repeatability ensures that every manufactured part is identical and meets quality standards.
2. High Efficiency & Productivity
- Machine tools allow for faster, automated production, reducing labor dependency.
- Multi-axis CNC machining centers enable complex parts to be produced in a single setup, saving time.
- Automated tool changers and high-speed spindles increase throughput in mass production.
3. Cost Reduction & Material Optimization
- Precision machining minimizes material waste, lowering production costs.
- CNC machines optimize tool paths and cutting strategies, ensuring efficient material removal.
- Reduced human intervention means lower labor costs and fewer operator errors.
4. Versatility Across Industries
- Automotive → Producing engine blocks, transmission parts, and suspension components.
- Aerospace → Machining aircraft fuselage, turbine blades, and landing gear.
- Medical → Manufacturing surgical implants, prosthetics, and orthopedic devices.
- Construction & Heavy Equipment → Fabricating structural steel, gears, and hydraulic components.
- Electronics → Cutting precision circuit boards, semiconductor parts, and micro-components.
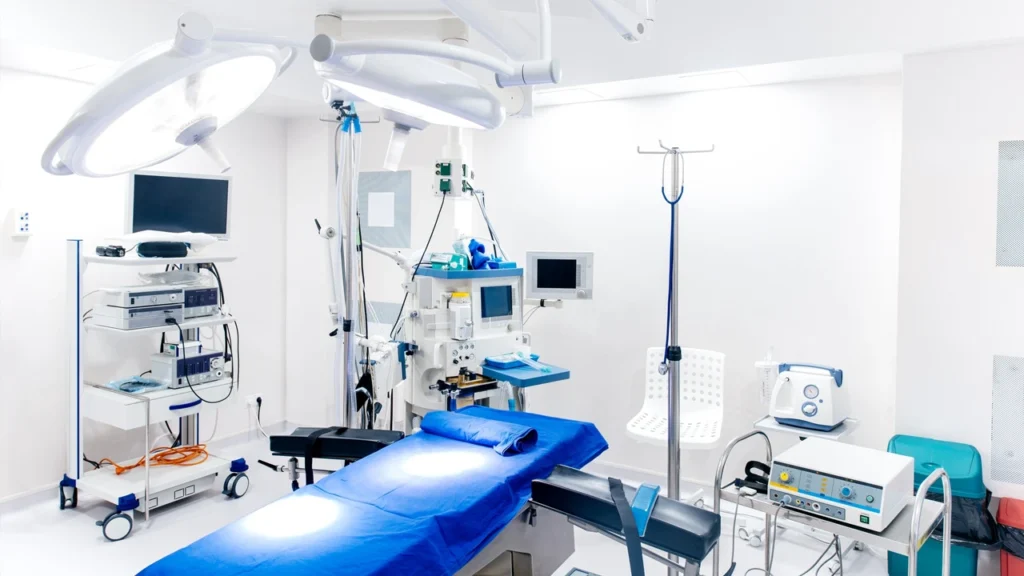
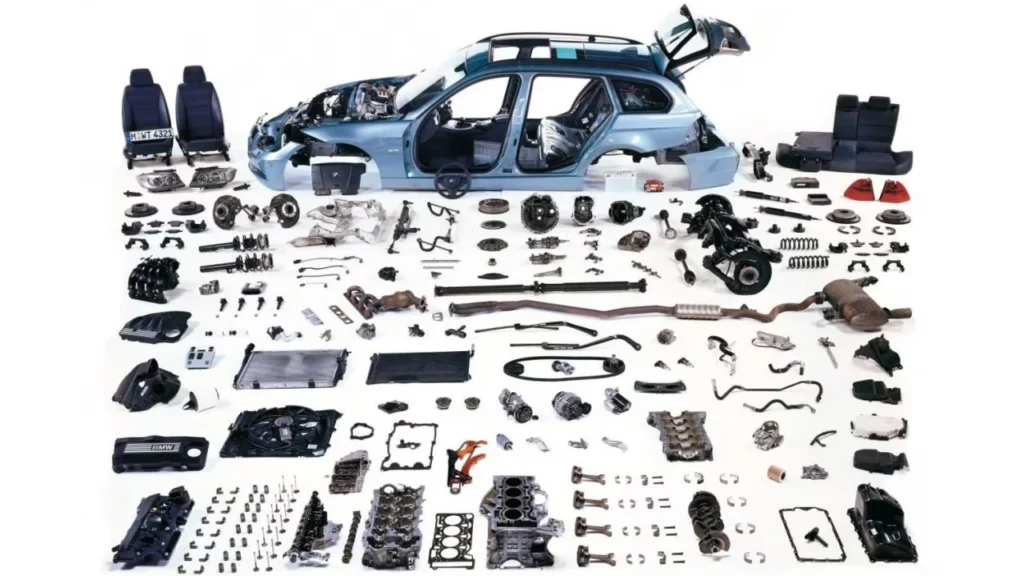
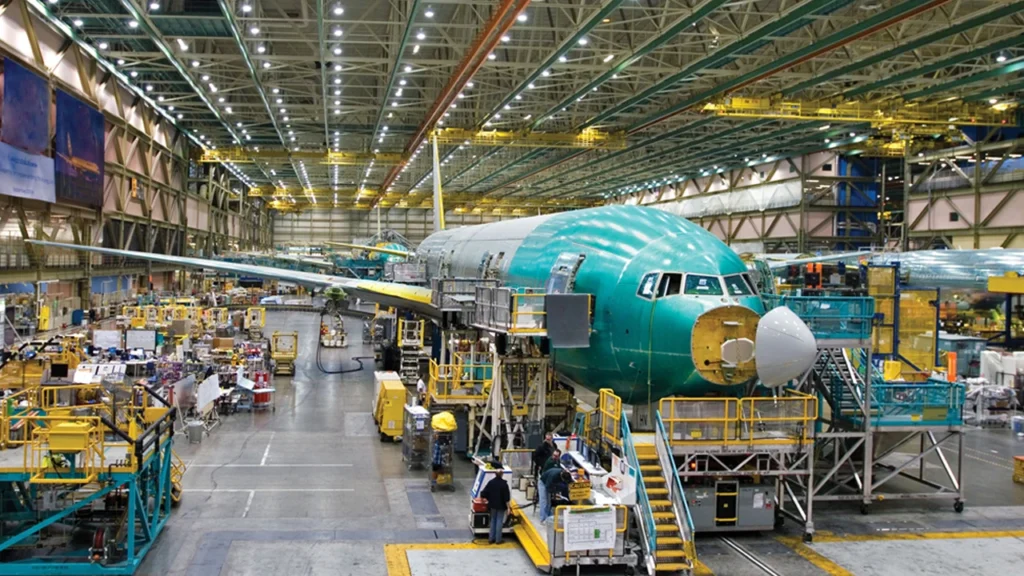
5. Integration with Advanced Technology
- Modern machine tools incorporate AI, robotics, and IoT, enabling smart manufacturing.
- Predictive maintenance using sensors prevents machine failures and reduces downtime.
- CNC automation allows for 24/7 production, increasing manufacturing output.
How Machine Tools Have Revolutionized Mass Production
Before the industrial revolution, manufacturing relied on manual labor, which was slow and inconsistent. The invention of machine tools in the 18th and 19th centuries led to the rise of mass production, allowing industries to produce identical parts at scale.
Today, CNC machine tools have further transformed production, enabling unattended machining, complex part fabrication, and ultra-high precision. From simple manual lathes to advanced multi-axis machining centers, machine tools have made modern industrial manufacturing possible.
Machine Tools vs. CNC Machine Tools: What’s the Difference?
Traditional Machine Tools vs. CNC Machine Tools
Machine tools have evolved significantly, shifting from manual operation to computer-controlled automation. Traditional machine tools require skilled operators to manually control cutting tools, adjust settings, and ensure precision. On the other hand, CNC (Computer Numerical Control) machine tools use pre-programmed instructions (G-code) to automate machining processes, reducing human intervention and improving consistency.
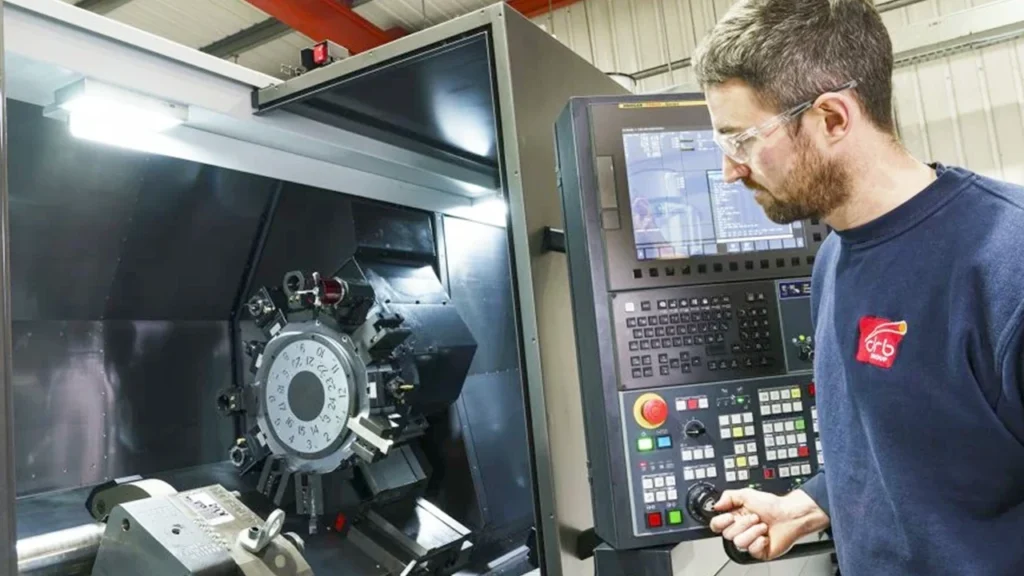
How CNC Technology Improved Precision, Automation & Repeatability
The introduction of CNC machine tools revolutionized manufacturing, bringing several improvements:
- Higher Precision → CNC tools work with micron-level accuracy, ensuring perfect repeatability.
- Automation → CNC machining allows for unattended, 24/7 production, boosting efficiency.
- Consistency → Every component produced by a CNC machine is identical, eliminating human error.
- Complexity Handling → CNC machines handle multi-axis operations, enabling intricate part production.
- Faster Production → CNC machines perform rapid machining cycles, reducing lead times.
- Digital Integration → CAD/CAM software allows for seamless part design & machining execution.
Advantages of CNC Machine Tools Over Conventional Tools
Feature | Manual Machine Tools | CNC Machine Tools |
---|---|---|
Precision | Operator-dependent, limited accuracy | Ultra-precise, automated positioning |
Speed | Slower, requires constant supervision | High-speed machining with automated tool changes |
Repeatability | Inconsistent, relies on operator skill | Perfect repeatability in mass production |
Automation | Fully manual operation | Fully automated, capable of unattended machining |
Complexity | Limited to simple cuts and shapes | Can produce multi-axis complex geometries |
Labor Cost | Requires skilled operators | Reduces labor costs with automated control |
Efficiency | Slower, more material waste | Optimized tool paths, less material waste |
CNC machine tools are faster, more precise, and more efficient, making them essential for modern high-volume production.
What Industries Prefer CNC Over Manual Tools?
Many industries have fully adopted CNC machining due to its speed, precision, and automation:
- Aerospace → Producing turbine blades, landing gear, and fuselage components.
- Automotive → Manufacturing engine blocks, transmission parts, and brake components.
- Medical → Crafting prosthetics, surgical implants, and precision tools.
- Electronics → Producing printed circuit boards (PCBs) and micro-components.
- Metal Fabrication → Cutting, drilling, and shaping structural steel and aluminum components.
While manual machine tools are still useful for custom one-off jobs and repair work, CNC technology is the gold standard for high-precision, high-efficiency production.
Summary: CNC Machine Tools vs. Traditional Machine Tools
CNC machine tools have revolutionized manufacturing, offering unmatched precision, efficiency, and automation compared to traditional manual tools. Industries requiring complex parts, high repeatability, and mass production rely heavily on CNC technology. While manual machine tools still have their place, CNC machining is the future of precision manufacturing.
Advantages of Using Machine Tools
Machine tools have revolutionized manufacturing by enabling high-precision machining, increased automation, and efficient material processing. They play a crucial role in automotive, aerospace, medical, and construction industries, ensuring high-quality, repeatable, and cost-effective production.
Increased Precision & Accuracy
- Machine tools, especially CNC-controlled, can achieve micron-level accuracy, ensuring perfect part dimensions.
- Eliminates human error, leading to consistent, high-quality production.
- Multi-axis CNC machines allow for intricate geometries and fine tolerances.
- Example: Aerospace manufacturers rely on precision machining for jet engine components and turbine blades.
Higher Production Efficiency & Automation
- Machine tools automate cutting, milling, drilling, grinding, and shaping, increasing productivity.
- CNC machines operate 24/7 with minimal supervision, enabling unattended production.
- Automated tool changers and robotic integration further reduce machining time.
- Example: Automotive factories use CNC machining centers for mass-producing engine parts, transmissions, and brake components.
Consistency & Repeatability
- Ensures identical parts in mass production, reducing quality variations.
- CNC programming guarantees that every cut, hole, and surface is precisely machined.
- Reduces defects and improves component reliability, which is crucial for medical devices and aircraft parts.
- Example: Medical implant manufacturers use CNC milling and EDM for crafting high-precision surgical implants.
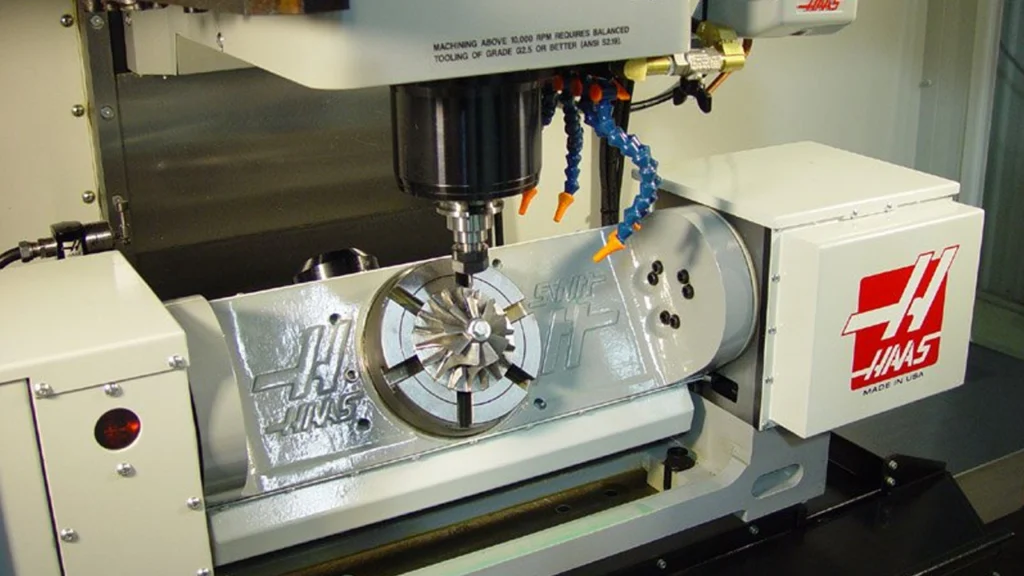
Material Waste Reduction & Cost-Effectiveness
- Optimized cutting paths and machining strategies minimize raw material waste.
- High-speed machining reduces cycle times and labor costs.
- Energy-efficient machine tools lower operational expenses.
- Example: Sheet metal fabrication companies use CNC laser cutting to maximize material usage and reduce scrap waste.
Customization & Flexibility in Design
- Machine tools support custom designs, rapid prototyping, and on-demand production.
- Advanced CAD/CAM software allows quick modifications to designs.
- 5-axis machining enables complex, multi-sided machining in a single setup.
- Example: Electronics manufacturers use CNC milling for custom aluminum casings and heat sinks.
Industries That Rely on Machine Tools
- Aerospace → Precision machining of aircraft fuselage, engine parts, landing gear.
- Automotive → Mass production of engine blocks, gears, and chassis components.
- Medical → Manufacturing prosthetics, dental implants, and orthopedic tools.
- Electronics → CNC machining of PCBs, semiconductor components, and connectors.
- Construction & Heavy Equipment → Producing steel frameworks, hydraulic cylinders, and industrial tools.
Machine tools provide unparalleled precision, automation, efficiency, and flexibility, making them indispensable for modern manufacturing. From reducing material waste to enabling high-speed production, machine tools help industries stay competitive, innovative, and cost-effective.
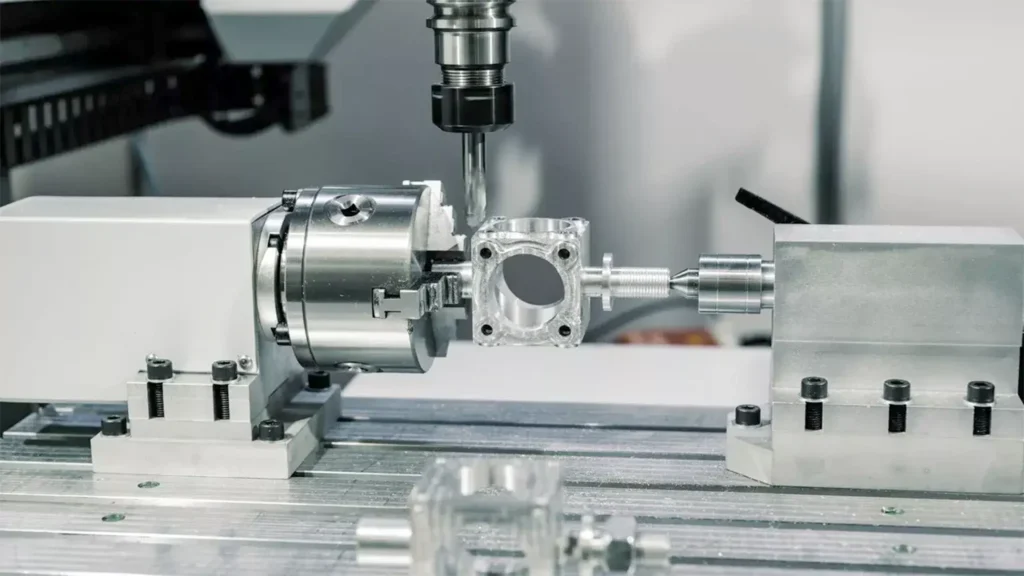
How to Choose the Right Machine Tool for Your Needs
Choosing the right machine tool is crucial for efficiency, precision, and cost-effectiveness in manufacturing. The best machine tool for your operation depends on material type, production volume, accuracy requirements, and budget. Selecting the wrong machine can result in poor-quality products, excessive costs, and inefficiency.
In this section, we’ll explore the key factors to consider when choosing a machine tool and compare different options for various manufacturing needs.
Material Type: What Are You Machining?
The first step in choosing a machine tool is understanding the material you will process. Different machines are suited for metals, plastics, composites, and ceramics:
Material Type | Recommended Machine Tools |
---|---|
Metals (Steel, Aluminum, Titanium, Brass, etc.) | CNC Lathes, CNC Milling Machines, Grinding Machines, EDM, Plasma Cutters |
Plastics & Composites | CNC Routers, Milling Machines, Water Jet Cutters |
Wood & Soft Materials | CNC Routers, Laser Cutting Machines |
Ceramics & Glass | Grinding Machines, Water Jet Cutting Machines |
Example: If you need high-precision machining of aerospace-grade titanium, a CNC milling machine or EDM machine is ideal. For wood cutting and engraving, a CNC router is a better choice.
Production Volume: High-Volume vs. Low-Volume Manufacturing
Do you need a machine for mass production or small-batch customization?
- High-volume production → CNC machining centers, automatic lathes, and robotic automation systems.
- Low-volume & prototyping → Manual lathes, milling machines, 3D printers, and small CNC routers.
Example: A medical implant manufacturer requires mass production CNC milling for identical components, while a custom furniture maker benefits more from a CNC router for small-batch projects.
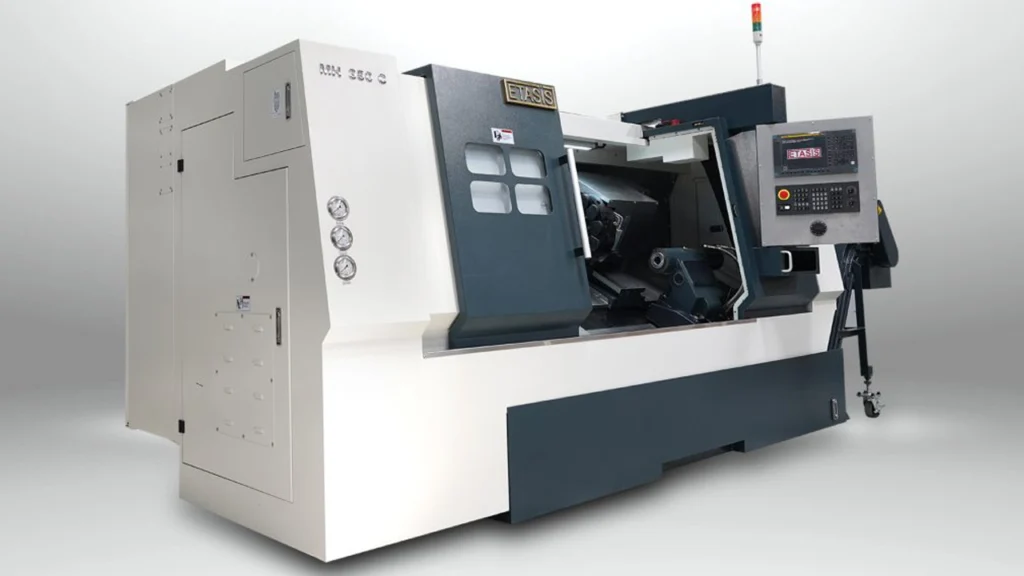
Precision Requirements: Fine-Detail Machining vs. General Cutting
- High-precision work (micron-level accuracy) → Grinding machines, CNC milling machines, EDM machines.
- General-purpose machining → Manual or CNC lathes, milling machines, shaping machines.
- Large-scale rough cutting → Plasma cutters, laser cutters, and water jet machines.
Example: If your project requires tight tolerances, a CNC grinding machine or EDM machine is ideal. If precision is less critical, a manual lathe or milling machine may be sufficient.
Budget & Long-Term Investment Costs
- Initial investment vs. operating cost → CNC machines cost more upfront but reduce labor costs.
- Maintenance & tool replacement → High-precision machines require specialized tools and maintenance.
Example: A CNC lathe costs more than a manual lathe, but it offers faster production, higher precision, and automation, reducing long-term costs.
Comparison of Machine Tools for Different Applications
Machine Tool | Best For | Pros | Cons |
---|---|---|---|
CNC Lathe | Round parts, shafts, bolts | High precision, automation | High initial cost |
CNC Milling Machine | Complex parts, mold making | Multi-axis machining, fine detailing | Requires skilled programming |
Grinding Machine | Surface finishing, precision parts | Ultra-precise, smooth finish | Slow process |
Laser Cutting Machine | Sheet metal, signage, engraving | Fast, precise, minimal material waste | Limited to thin materials |
Water Jet Cutting Machine | Heat-sensitive materials, glass, ceramics | No heat damage, high accuracy | Higher operating cost |
EDM Machine | Hard metals, fine details | Works with conductive materials, no cutting force | Slow machining speed |
CNC Router | Wood, plastic, light metals | High-speed cutting, 2D & 3D shaping | Not suitable for heavy metals |
Example: If you need to mass-produce metal components, a CNC milling machine is the best choice. If your business focuses on engraving and cutting signage, a laser cutter is more cost-effective.
Summary: Making the Right Machine Tool Choice
Choosing the right machine tool depends on material type, production volume, precision requirements, and budget. CNC machines offer automation and high precision, while manual tools are best for small-scale operations and custom work. By carefully assessing your needs, you can maximize efficiency, reduce costs, and improve production quality.
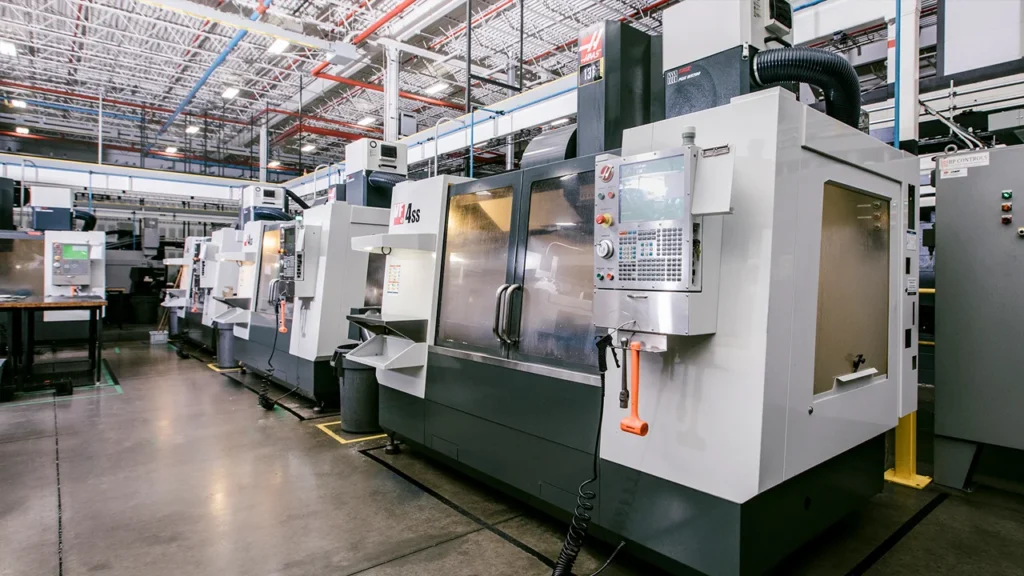
Machine Tool Maintenance and Safety Practices
Proper maintenance and safety practices are essential for keeping machine tools running efficiently, minimizing downtime, and ensuring operator safety. Neglecting maintenance can lead to premature wear, costly breakdowns, and safety hazards. Meanwhile, enforcing strict safety measures helps prevent workplace injuries and ensures compliance with industrial regulations.
In this section, we’ll cover regular maintenance routines and key safety practices that should be followed when operating machine tools.
Regular Maintenance for Machine Tools
Lubrication & Coolant System Checks
- Lubrication reduces friction between moving parts, preventing wear and overheating.
- Regularly inspect spindle bearings, guideways, ball screws, and gears for proper lubrication.
- CNC machines rely on coolant systems to prevent overheating and flush away metal chips.
- Check coolant levels, replace dirty coolant, and clean coolant filters to maintain efficiency.
Example: A CNC milling machine without proper lubrication can experience excessive tool wear and spindle overheating, reducing machine lifespan.
Cleaning & Removing Debris to Prevent Wear
- Metal chips, dust, and debris can clog machine components, affecting accuracy and causing malfunctions.
- Remove swarf, shavings, and coolant residue after each machining session.
- Keep linear rails, machine beds, and tool holders free from contamination.
- CNC machines require chip conveyors or extraction systems to handle debris efficiently.
Example: Neglecting chip removal in a lathe can jam moving parts, leading to misalignment and damaged workpieces.
Inspecting Cutting Tools for Sharpness & Wear
- Dull or damaged cutting tools reduce machining accuracy and increase cutting forces.
- Inspect end mills, lathe inserts, drill bits, and grinding wheels for wear.
- Use tool presetters to measure and calibrate tool dimensions before machining.
- Replace worn tools immediately to avoid defects and improve surface finish.
Example: In CNC milling, a worn-out tool causes poor surface quality and excessive heat buildup, shortening tool life.
Safety Measures When Operating Machine Tools
Proper Use of Personal Protective Equipment (PPE)
Operators must wear:
- Safety glasses or face shields → Prevents eye injuries from flying chips.
- Gloves (when necessary) → Avoids direct contact with sharp edges.
- Hearing protection → Required for high-noise environments (e.g., grinding machines).
- Protective footwear → Prevents injuries from dropped tools or materials.
Example: A lathe operator without eye protection risks metal shavings causing eye injuries.
Training & Skill Development for Operators
- Only trained personnel should operate machine tools.
- Machine operators should be familiar with G-code programming, tool offsets, and emergency stop procedures.
- Regular workshops and safety training keep operators updated on best practices.
- New employees should undergo supervised training before using CNC machines.
Example: Inexperienced CNC operators risk damaging high-value materials or causing machine crashes due to incorrect programming.
Emergency Stop Functions & Safety Interlocks
- Machine tools must have an accessible emergency stop (E-stop) button.
- Safety interlocks prevent operation if a machine door or guard is open.
- Pressure-sensitive mats and light curtains can stop machines if an operator enters a restricted area.
- Regularly test emergency stop functions to ensure they are operational.
Example: A grinding machine without an active safety interlock could result in serious hand injuries if an operator accidentally touches the rotating wheel.
Summary: Ensuring Machine Tool Longevity & Safety
- Routine maintenance like lubrication, cleaning, and tool inspection keeps machine tools operational and efficient.
- Proper safety measures, including PPE and training, prevent workplace accidents.
- Emergency stop functions and safety interlocks protect operators from unexpected hazards.
By following strict maintenance and safety protocols, manufacturers can reduce downtime, improve productivity, and create a safer work environment.
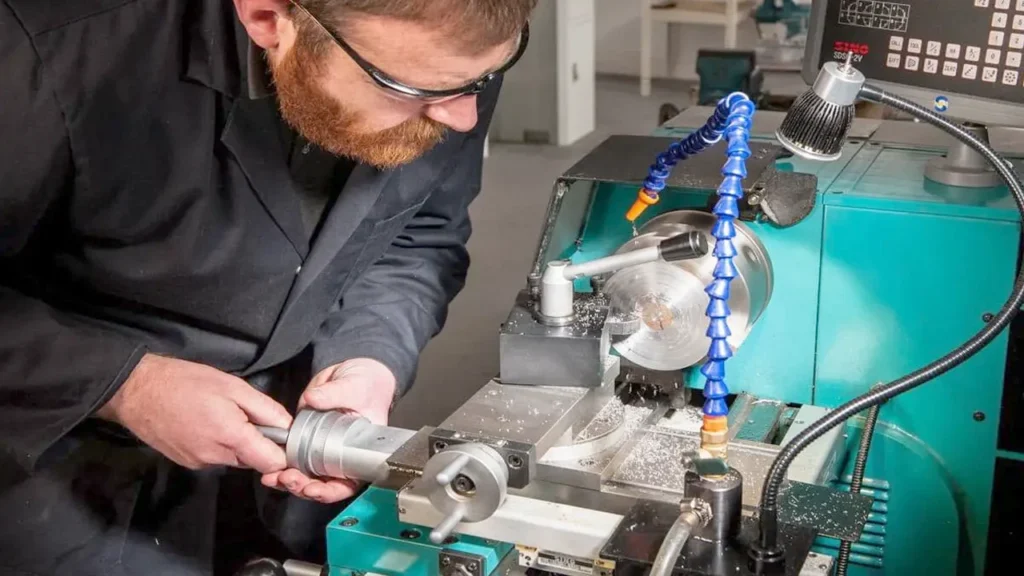
Future Trends in Machine Tool Technology
The machine tool industry is rapidly evolving with cutting-edge advancements in automation, AI, IoT, and sustainability. As Industry 4.0 reshapes global manufacturing, machine tools are becoming smarter, more efficient, and highly automated.
In this section, we’ll explore the key technological trends driving the future of machine tools, from AI-driven automation and IoT integration to energy-efficient machining and robotics.
AI-Driven Automation & Smart Factories
AI-Powered CNC Machining & Self-Optimizing Tools
- Artificial intelligence (AI) is revolutionizing machine tools by enabling self-learning algorithms to optimize cutting speeds, toolpaths, and cycle times.
- AI-driven adaptive machining automatically adjusts parameters to reduce material waste, improve precision, and prevent tool wear.
- Predictive maintenance powered by AI minimizes downtime by identifying machine issues before failures occur.
Example: AI-powered CNC systems in aerospace manufacturing adjust spindle speeds in real time to maximize cutting efficiency and tool lifespan.
Smart Factories & Fully Automated Production Lines
- Smart factories integrate CNC machines, robots, and AI-driven software to create fully automated production environments.
- Digital twins allow manufacturers to simulate and optimize machine tool performance before actual machining begins.
- Real-time data analytics improve workflow efficiency, reduce errors, and enhance quality control.
Example: Automotive plants use AI-powered machining centers with robotic arms to mass-produce engine components with minimal human intervention.
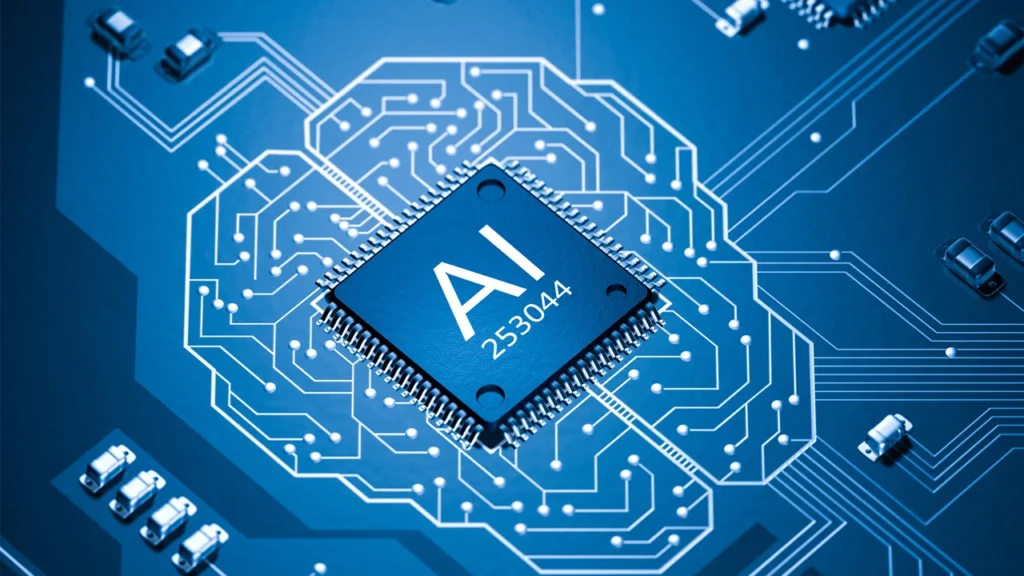
IoT (Internet of Things) Integration for Machine Monitoring
Real-Time Machine Health Monitoring & Predictive Maintenance
IoT-enabled sensors continuously track machine tool performance, including spindle speed, temperature, vibration, and tool wear.
Remote monitoring allows manufacturers to detect anomalies and schedule maintenance before breakdowns occur.
Cloud-based analytics platforms help optimize machine uptime and overall equipment effectiveness (OEE).
Example: A CNC lathe equipped with IoT sensors can send real-time alerts when excessive vibration or tool wear is detected, preventing unexpected failures.
Connected Factories & Data-Driven Manufacturing
- Machine tools can communicate with each other, exchanging real-time operational data to optimize production efficiency.
- Machine learning algorithms analyze sensor data to predict failures, improve tool performance, and optimize cycle times.
- IoT integration reduces manual inspections, allowing manufacturers to focus on high-value production tasks.
Example: Aerospace manufacturers use IoT-powered machining centers to track the performance of thousands of cutting tools across multiple facilities.
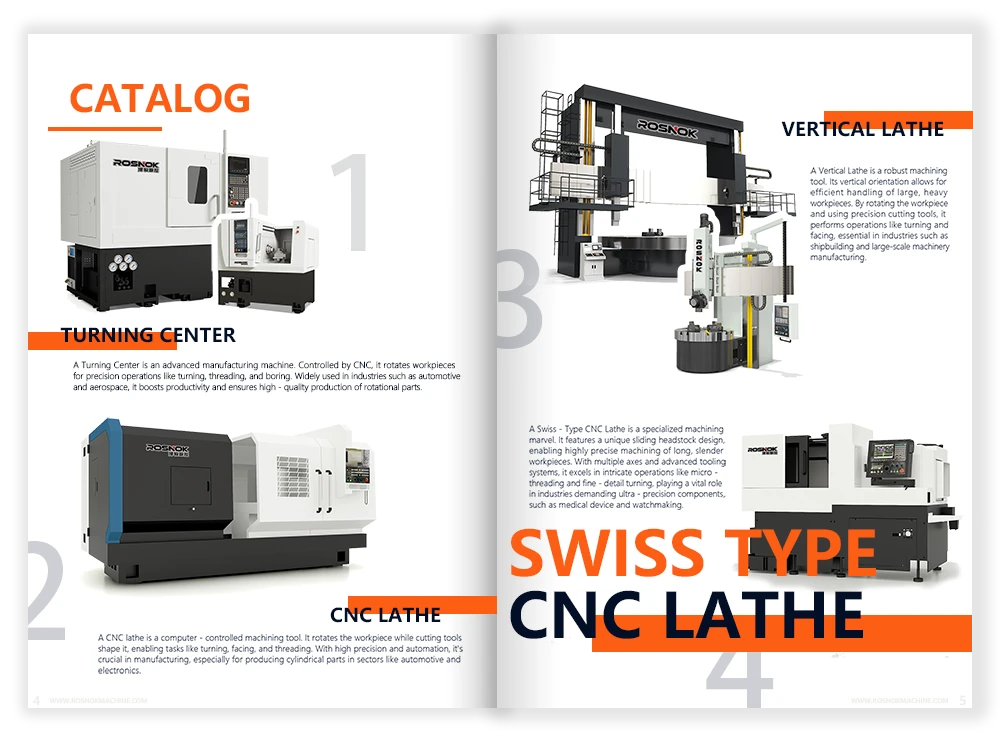
Sustainable & Energy-Efficient Machining Technologies
Energy-Efficient CNC Machines & Smart Power Management
- Next-generation CNC machines are designed to consume less energy while maintaining high-speed precision.
- Regenerative braking systems in CNC machines recover and reuse excess energy.
- AI-optimized toolpaths reduce material waste and shorten machining cycles, lowering power consumption.
Example: Energy-efficient servo motors in CNC machining centers help reduce electricity costs while maintaining high precision.
Sustainable Coolants & Eco-Friendly Cutting Technologies
- Water-based & biodegradable coolants reduce chemical waste and environmental impact.
- Minimum quantity lubrication (MQL) technology reduces excessive coolant usage while maintaining cooling efficiency.
- Dry machining techniques eliminate coolant use altogether for certain operations, lowering production costs.
Example: Automotive manufacturers use MQL technology in CNC milling operations to reduce coolant waste and improve workplace safety.
The Role of Robotics & Hybrid Manufacturing in the Future
Robotics & Machine Tool Integration
- Robotic arms assist CNC machines by loading/unloading workpieces, performing inspections, and finishing parts.
- Collaborative robots (cobots) work alongside human operators, improving productivity and reducing labor costs.
- Automated tool-changing robots enhance CNC machining flexibility and minimize downtime between processes.
Example: CNC grinding machines in medical device manufacturing use robotic arms for ultra-precise polishing and inspection.
Hybrid Manufacturing: Combining CNC & 3D Printing
Hybrid machining centers integrate CNC milling, laser cutting, and additive manufacturing (3D printing) into a single machine.
Manufacturers can print complex components and then machine critical surfaces for final precision.
Hybrid manufacturing reduces material waste, speeds up prototyping, and allows for design innovations.
Example: Aerospace manufacturers use hybrid machines to 3D print turbine blades before using CNC milling for precision finishing.
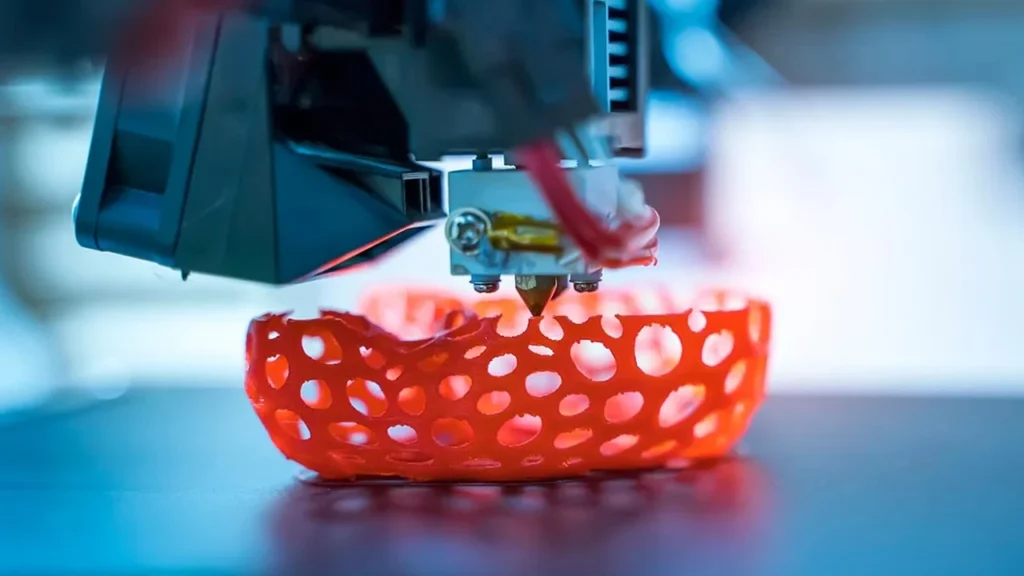
Summary: The Future of Machine Tools
- AI-driven automation & smart factories improve precision, efficiency, and predictive maintenance.
- IoT integration enables real-time monitoring, remote diagnostics, and data-driven optimizations.
- Sustainable machining technologies reduce energy consumption & environmental impact.
- Robotics & hybrid manufacturing are redefining how parts are made, combining traditional machining with next-gen innovations.
Machine tool technology is evolving rapidly, paving the way for faster, smarter, and more sustainable manufacturing. Companies that adopt these innovations will gain a competitive edge in the future of industrial production.
Conclusion: What Is a Machine Tool?
Machine tools are the foundation of modern manufacturing, allowing industries to produce precise, high-quality components efficiently. These machines, ranging from lathes and milling machines to advanced CNC machining centers, have revolutionized industrial production, enhancing speed, accuracy, and automation.
Throughout this guide, we have explored:
- The definition and significance of machine tools.
- Different types of machine tools and their specialized applications.
- Key components and functions of various machine tools.
- The difference between conventional machine tools and CNC machine tools.
- Factors to consider when selecting the right machine tool for your needs.
- The importance of maintenance and safety in machine tool operation.
- Future innovations shaping the next generation of machine tools.
With the rise of AI, IoT, and smart automation, machine tools are becoming more efficient, sustainable, and intelligent. Businesses that adopt these innovations will stay competitive in an increasingly technology-driven world.
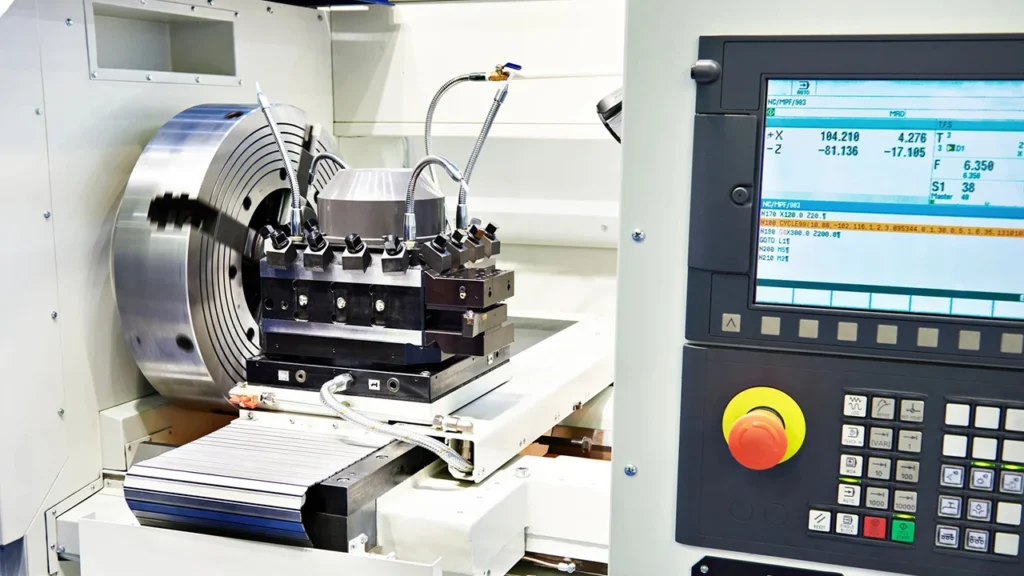
Why Choose Rosnok for Your CNC Machine Tool Needs?
At Rosnok, we manufacture high-precision CNC machine tools designed for maximum efficiency, reliability, and accuracy. Whether you need a CNC lathe, milling machine, or custom machining center, we offer:
- Cutting-edge CNC technology for superior precision.
- Energy-efficient, sustainable solutions for modern manufacturing.
- Dedicated after-sales support and operator training.
- Customizable machines to meet your exact production requirements.
Looking for the perfect machine tool solution? Contact Rosnok today to discover our full range of CNC machine tools and take your production to the next level!
FAQ: What Is a Machine Tool
Do I need programming knowledge to operate a modern machine tool?
Basic machine tool operations do not require programming knowledge. However, for CNC machine tools or advanced automated systems, understanding G-code or using CAM software is essential for efficient operation.
Can a machine tool process non-metal materials?
Yes. Many machine tools can process non-metal materials such as plastics, composites, ceramics, and even wood. The choice of cutting tools and machine settings must be adjusted for each material type.
Can multiple machine tools be integrated into a single automated production line?
Yes. Multiple machine tools can be integrated with automation systems, such as robotic arms and conveyors, to form a fully automated production line. This integration improves production efficiency and consistency.