Have you ever wondered, what is a CNC lathe? How does it work? What makes it different from traditional lathes? Why is it considered essential in modern manufacturing? Can a CNC lathe really produce parts with such high precision? How does it automate the machining process? What kind of industries rely on CNC lathes for production?
A CNC lathe (Computer Numerical Control lathe) is an advanced machine tool that uses computer programming to automate the turning of metal or other materials into high-precision parts. Powered by CNC systems, it performs complex machining tasks with exceptional accuracy and repeatability. From simple cylindrical components to intricate aerospace or medical parts, CNC lathes deliver consistent quality. Their ability to streamline production while maintaining tight tolerances makes them indispensable in today’s precision-driven manufacturing landscape.
Continue reading this guide to learn what a CNC lathe is, how it works, the key components that drive its precision, types of CNC lathes, and their real-world applications across industries.
What is a CNC Lathe?
A CNC lathe, or Computer Numerical Control lathe, is a type of machine tool that uses computer programs to automate the machining of cylindrical parts. Unlike traditional lathes, which rely on manual control, CNC lathes operate based on a set of programmed instructions that guide the cutting tool’s movement, feed rate, spindle speed, and depth of cut.
At the core of a CNC lathe is its ability to rotate a workpiece around a central axis while a cutting tool removes material to achieve the desired shape. The cutting process typically occurs along two axes: the Z-axis (longitudinal movement) and the X-axis (radial movement). Operations such as turning, facing, threading, boring, drilling, and grooving are commonly performed on these machines.
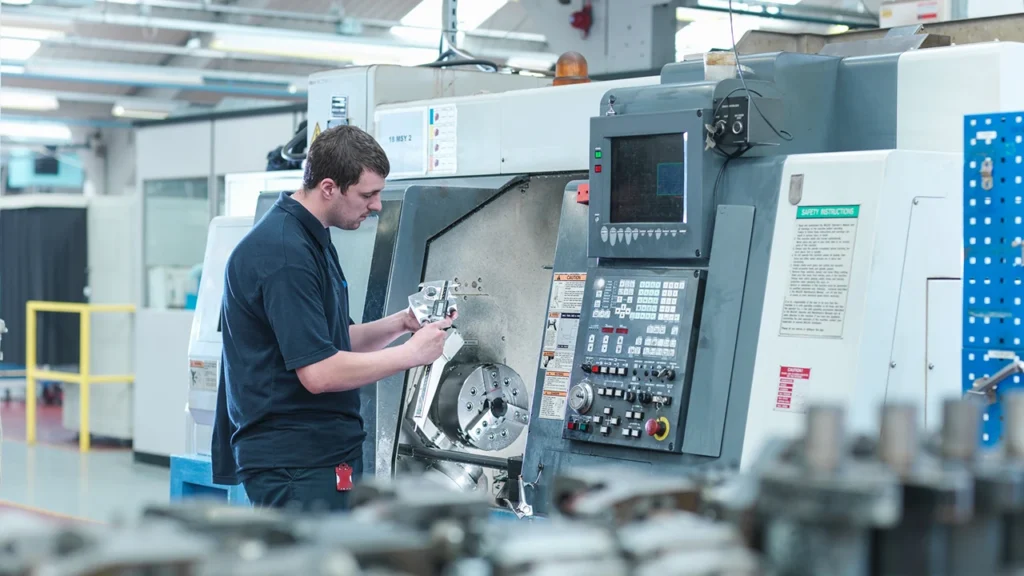
CNC lathes are known for their precision, repeatability, and ability to handle complex geometries. Once a digital program is created, the machine can produce identical parts with high accuracy and minimal variation. This makes CNC lathes ideal for industries where component consistency is critical, such as aerospace, automotive, medical, and electronics manufacturing.
In addition to precision, CNC lathes improve productivity by reducing manual labor and setup time. Operators input the machining program, mount the raw material, and monitor the process, while the machine carries out the rest. This efficiency is especially valuable in high-volume production environments, where downtime and human error must be minimized.
Understanding what a CNC lathe is and how it functions is the foundation for exploring its broader role in modern manufacturing. As digital control becomes more advanced and accessible, CNC lathes continue to evolve as an essential tool for turning raw materials into finished, high-quality components.
How Does a CNC Lathe Work?
A CNC lathe operates by combining mechanical motion with computer programming to automate the turning process. At its core, the process begins when a machinist prepares a digital program—usually written in G-code—that defines how the machine should cut the workpiece. The program includes commands for tool movements, spindle speeds, feed rates, and tool changes. Once the program is loaded into the CNC control system, the lathe executes the instructions automatically with high precision.
The basic working principle revolves around rotating the workpiece while the cutting tool moves along one or more axes. Most CNC lathes use two primary axes: the X-axis for radial movement and the Z-axis for longitudinal movement. The workpiece is mounted in the spindle chuck, which spins it at a designated speed. Cutting tools are mounted on the tool post or turret and are brought into contact with the rotating workpiece. Material is removed layer by layer to shape the part to the specified dimensions.
CNC lathes also support a variety of machining operations in a single setup. These include turning (external diameter), boring (internal diameter), facing (end surfaces), grooving (slots or reliefs), threading (internal and external threads), and drilling. Some advanced machines may include a Y-axis, live tooling, or sub-spindles, enabling milling, tapping, and cross-drilling functions without removing the workpiece.
What sets CNC lathes apart is their integration of sensors, feedback systems, and real-time data processing. During operation, the control system continuously monitors the position of the tool and spindle to ensure precise adherence to the programmed path. This closed-loop control helps maintain dimensional accuracy even under varying loads or cutting conditions.
In high-volume manufacturing environments, CNC lathes provide a streamlined and repeatable process that minimizes setup time and human intervention. Operators focus on setup, programming, and monitoring rather than manual machining, which not only improves efficiency but also enhances safety and consistency.
CNC Program and Setup
The operation of a CNC lathe begins with creating a machining program using G-code, a standardized programming language used in CNC systems. The program includes specific commands that dictate the movement of the cutting tool, spindle speed, feed rate, coolant control, and tool changes. Machinists or engineers often use CAM (Computer-Aided Manufacturing) software to generate the code based on a 2D or 3D part model.
Once the G-code is prepared, the operator loads it into the CNC controller. Machine setup follows, which includes installing the correct cutting tools in the tool turret, mounting the raw workpiece securely in the chuck, and setting zero positions for all axes. These setup operations ensure that the machine references the correct starting point for all tool movements, reducing errors and enhancing machining accuracy.
Tool offsets, cutting depths, and workpiece material parameters are also configured at this stage. These settings help the CNC system compensate for variations in tool geometry and ensure the programmed dimensions match the actual cutting environment.
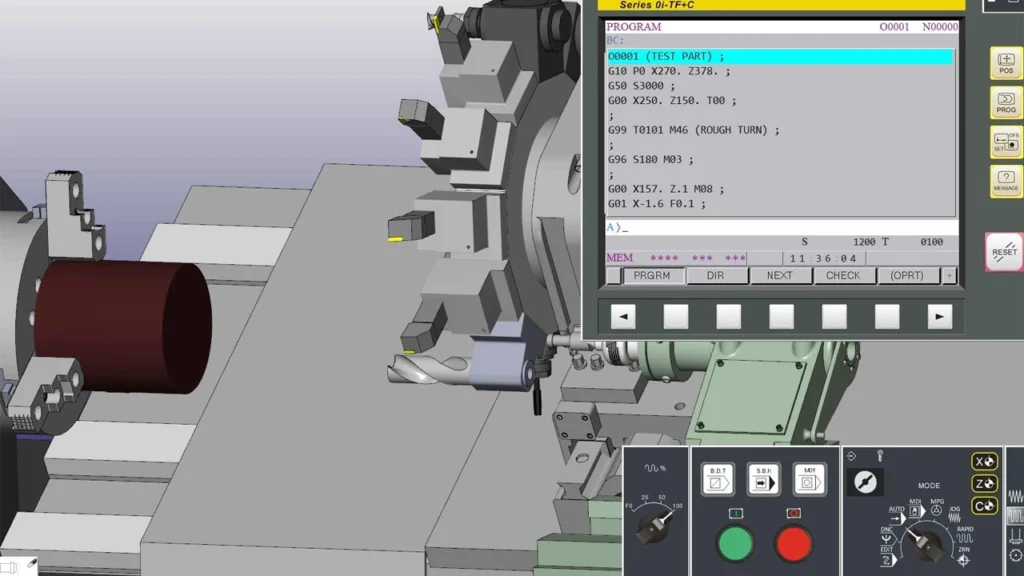
Tool Selection and Spindle Operation
Tool selection is a critical part of CNC lathe operation. The type of cutting tool used depends on the material of the workpiece and the specific machining process being performed, such as rough turning, finish turning, threading, or drilling. Common tools include carbide inserts, boring bars, threading tools, and center drills.
Once the appropriate tools are loaded into the turret, the spindle plays its role by rotating the workpiece at a designated speed. The spindle speed is determined based on the material, tool type, and desired surface finish. Higher speeds are typically used for softer materials and finishing operations, while lower speeds are better for harder materials and roughing cuts.
The stability and precision of spindle operation are essential for accurate machining. Many CNC lathes use variable-frequency drives or servo motors to maintain consistent rotation under changing loads, helping ensure uniform surface finishes and dimensional control.
Workpiece Rotation and Tool Movement
The machining process involves coordinated movement between the rotating workpiece and the cutting tool. The workpiece, held securely in the chuck or collet, spins around the spindle axis. At the same time, the cutting tool mounted on the tool post or turret moves along predefined paths on the X and Z axes.
The X-axis movement controls the tool’s radial position, affecting the diameter of the cut, while the Z-axis controls its longitudinal movement along the length of the workpiece. These movements are controlled by the CNC program with exacting precision, often down to microns.
By combining rotational motion with precise linear tool movements, the machine removes material to form the desired geometry. Depending on the operation, the tool may cut the outer diameter, face the end of the workpiece, or bore internal features. Advanced machines may include a Y-axis for off-center milling or tapping operations.
Threading, Facing, Drilling and Boring
CNC lathes are capable of performing a wide variety of machining tasks beyond basic turning. Each operation serves a different purpose and is performed using a specific tool and motion path.
- Threading involves synchronizing the spindle rotation with tool feed to create internal or external threads with consistent pitch and depth. This requires precise control to match industry-standard thread profiles.
- Facing is performed by moving the tool radially inward across the face of the rotating workpiece, creating a flat surface perpendicular to the axis.
- Drilling is achieved by using a stationary or rotating drill bit fed along the centerline of the workpiece, creating axial holes.
- Boring enlarges and finishes internal diameters using a boring bar, often with higher precision than the original drilled hole.
Each of these operations can be programmed into a single machining cycle, reducing the need for multiple setups and enhancing workflow efficiency.
Coolant and Chip Removal
Coolant and chip management are vital aspects of CNC lathe operation, as they affect both machining performance and machine longevity. During cutting, significant heat is generated due to friction between the tool and the workpiece. Coolant systems are used to control this heat, maintain dimensional stability, and extend tool life.
Coolants can be delivered in various forms, such as flood coolant, mist, or through-tool delivery, depending on the operation and machine configuration. They also help flush away chips from the cutting zone, preventing recutting and surface damage.
Chip removal systems, such as chip conveyors or augers, automatically extract chips from the machine enclosure. This keeps the work area clean, reduces the risk of machine jamming, and minimizes manual intervention, especially during unattended operations.
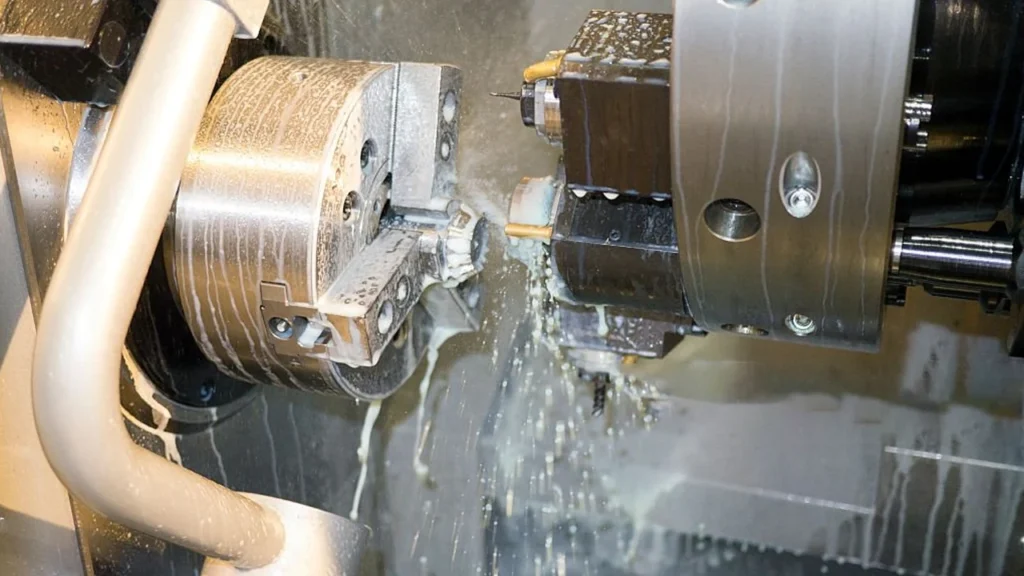
Machining Completion and Quality Inspection
Once all machining operations are complete, the CNC lathe stops automatically, and the finished part can be removed for inspection. Many CNC lathes are integrated with probes or sensors that perform in-process measurement, reducing the need for manual checking during production runs.
For quality control, parts are typically measured using micrometers, calipers, dial indicators, or coordinate measuring machines (CMMs). Operators check for dimensional accuracy, surface finish, and thread quality, depending on the application.
High-end production lines may use automated inspection systems to validate critical dimensions before moving to the next process step. This ensures that any deviation is caught early, preventing defective parts from reaching customers and reducing scrap rates.
Key Components of a CNC Lathe
A CNC lathe is a complex electromechanical system composed of several key components that work together to perform automated, high-precision turning operations. These core mechanical parts provide structural rigidity, motion accuracy, and functional integration, enabling the lathe to execute detailed machining tasks under strict tolerances. Each component plays a distinct role in positioning, supporting, rotating, or cutting the workpiece.
Understanding these components is essential not only for operators and technicians, but also for engineers involved in machine selection, setup, and maintenance. The following sections introduce the primary structural and motion systems found in most CNC lathes.
Machine Bed
The machine bed forms the foundation of the CNC lathe. Typically made of high-strength cast iron or mineral cast, it provides the structural support for all other components. The bed must possess high rigidity, dimensional stability, and excellent vibration damping characteristics to maintain machining accuracy under dynamic cutting forces.
The design of the bed also incorporates the mounting surfaces for guideways, screws, and auxiliary components. Slant-bed designs, where the bed is inclined at an angle (often 30°–45°), are commonly used to improve chip flow, increase operator accessibility, and enhance rigidity.
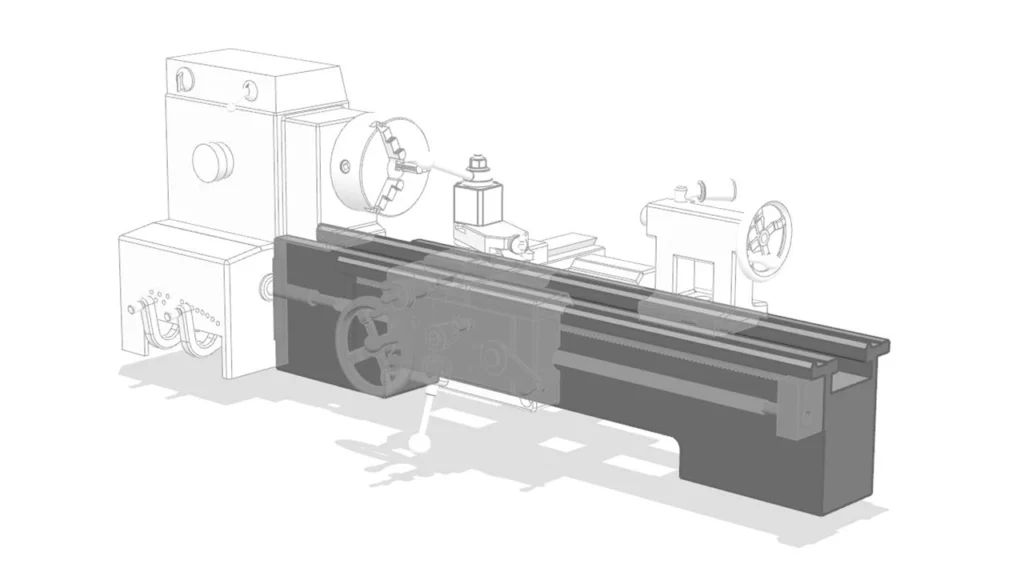
Headstock and Spindle System
The headstock houses the spindle, which is responsible for rotating the workpiece during machining. The spindle is typically driven by a variable-speed AC motor or servo motor and supported by high-precision bearings to ensure minimal runout.
Spindle performance directly affects machining quality, particularly surface finish and concentricity. Advanced CNC lathes may include features such as hollow spindles for bar feeding, high-speed spindles for small-diameter parts, or gear-driven systems for heavy-duty cutting. The headstock also contains the transmission system, which adjusts torque and speed according to machining requirements.
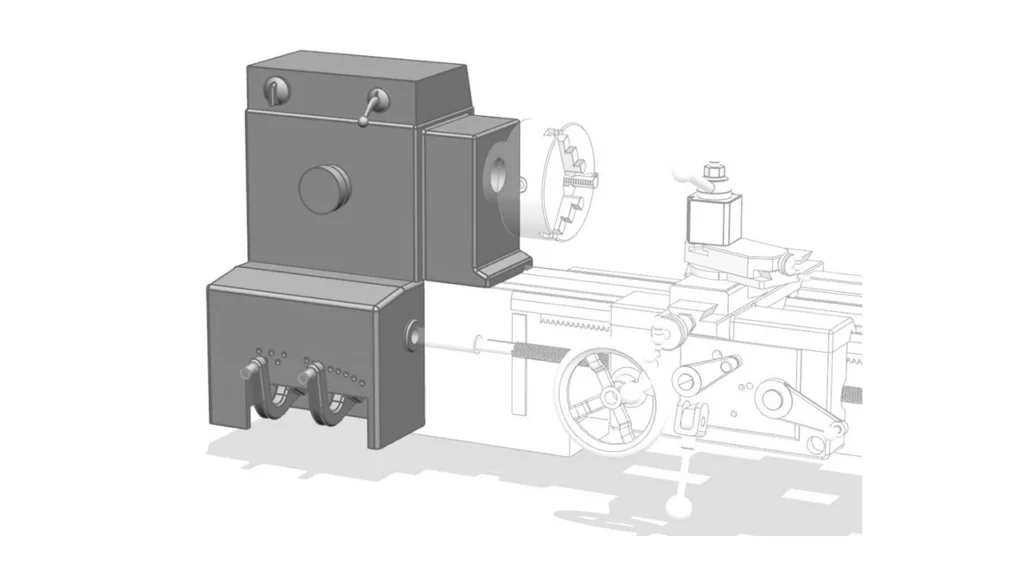
Chuck
The chuck is the component that clamps the workpiece onto the spindle. Most CNC lathes use a power chuck, operated hydraulically or pneumatically, to enable quick and repeatable clamping. Three-jaw chucks are common for cylindrical parts, while four-jaw or collet chucks are used for irregular shapes or high-precision needs.
A well-balanced and properly maintained chuck is critical for preventing slippage, reducing vibration, and ensuring accurate part alignment during high-speed rotation.
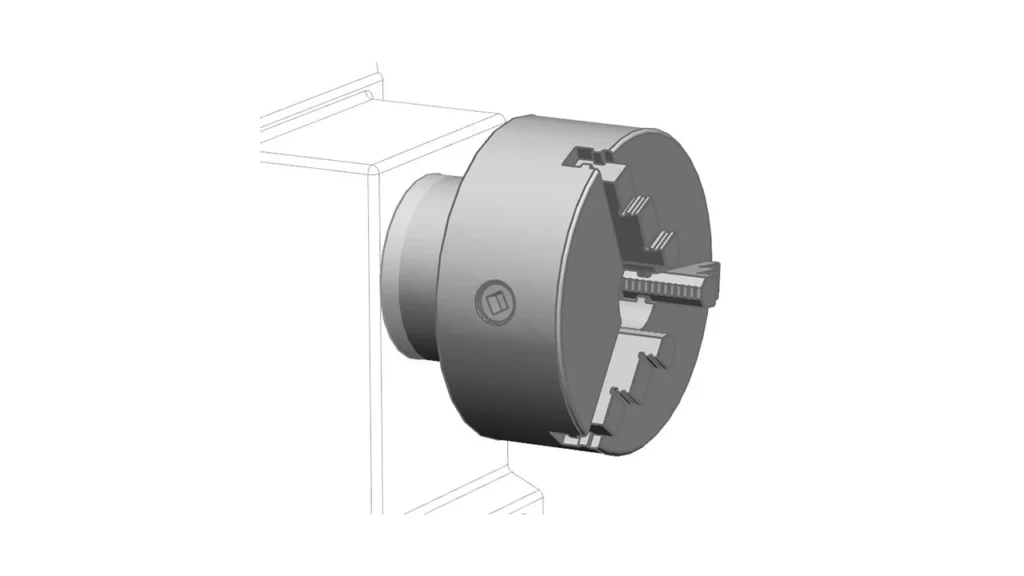
Guideways
Guideways are the linear motion paths that support the movement of key assemblies such as the carriage, cross-slide, and turret. Two common types of guideways are:
- Box ways: Offer excellent rigidity and vibration resistance, suitable for heavy cutting.
- Linear guideways: Enable high-speed movement with low friction, ideal for fast positioning and light-to-medium cutting loads.
The accuracy and smoothness of the guideways directly impact tool positioning, repeatability, and surface quality.
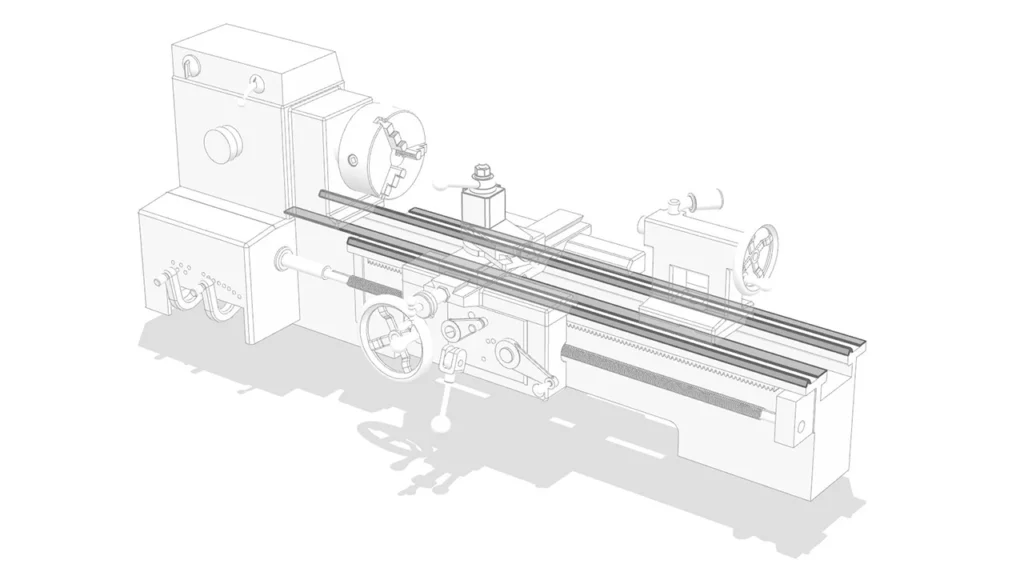
Leadscrew System
The leadscrew system converts rotary motion into linear feed for the tool carriage or slide. Most CNC lathes use ball screws, known for their low friction, high positioning accuracy, and compatibility with servo-driven systems. They enable smooth, precise motion and are often preloaded to minimize backlash.
For heavy-load or high-frequency applications, some machines may use roller screws, which offer greater durability and load capacity. In contrast, trapezoidal screws are occasionally found in cost-sensitive or simpler setups, though they lack the precision needed for advanced CNC work.
The selection of leadscrew type depends on the application, but ball screws remain the industry standard for most precision CNC turning operations.
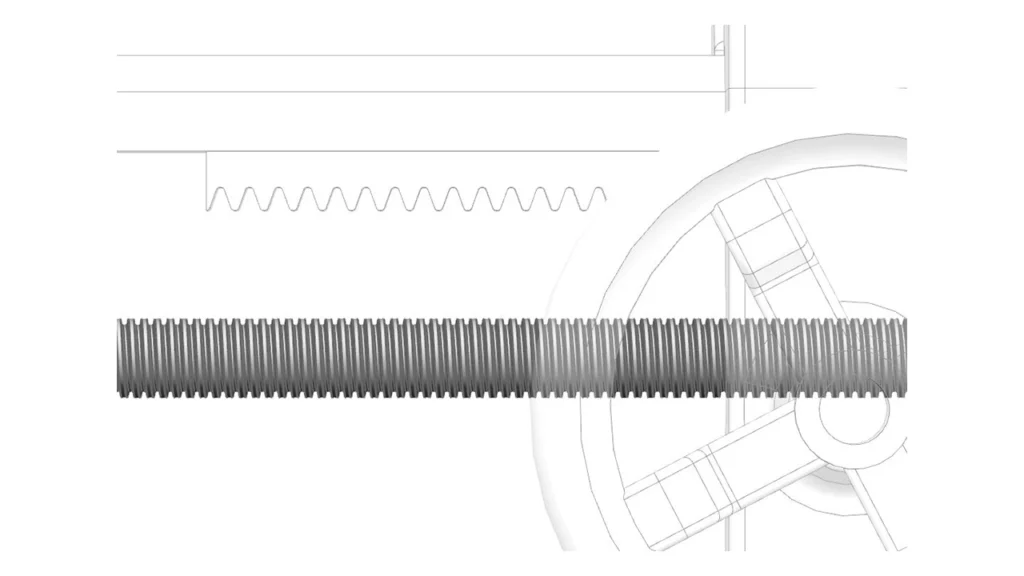
Turret or Tool Post
The turret (or tool post in simpler machines) holds and indexes the cutting tools. CNC lathes typically feature automatic indexing turrets that can accommodate multiple tools, enabling multi-step machining in a single setup.
Turrets are often servo-driven and can rotate bidirectionally to minimize tool change time. They support turning tools, boring bars, threading tools, and even driven tools (in machines with live tooling capabilities). Accurate turret positioning ensures proper tool alignment and cutting geometry.
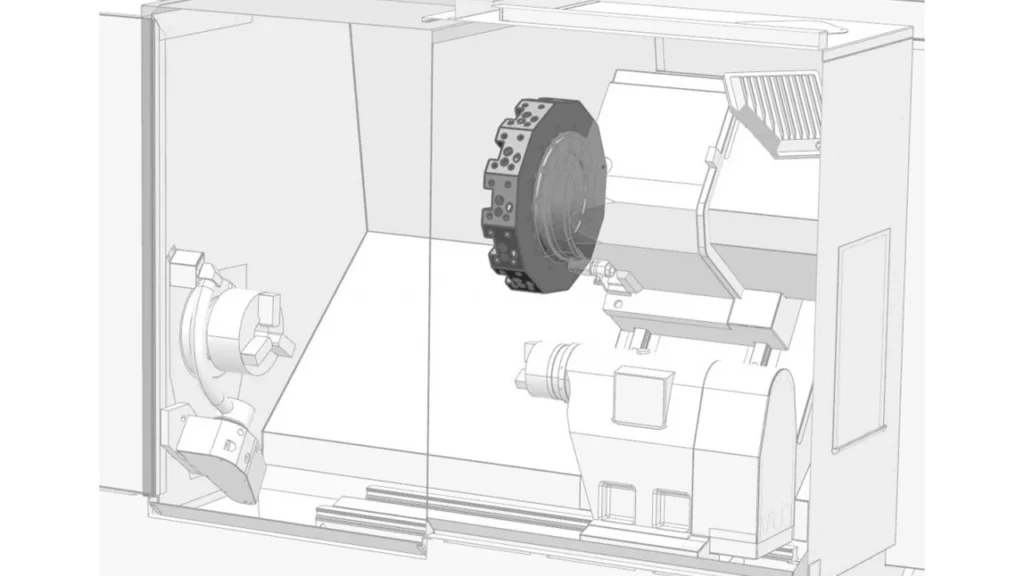
Tailstock
The tailstock provides additional support for long or flexible workpieces during machining. It is positioned opposite the headstock and can be adjusted along the Z-axis bed slide.
A tailstock typically includes a quill that holds a live center, which rotates with the workpiece to support axial loads without generating friction. This component is essential when turning long shafts, pipes, or components that might deflect under cutting forces.
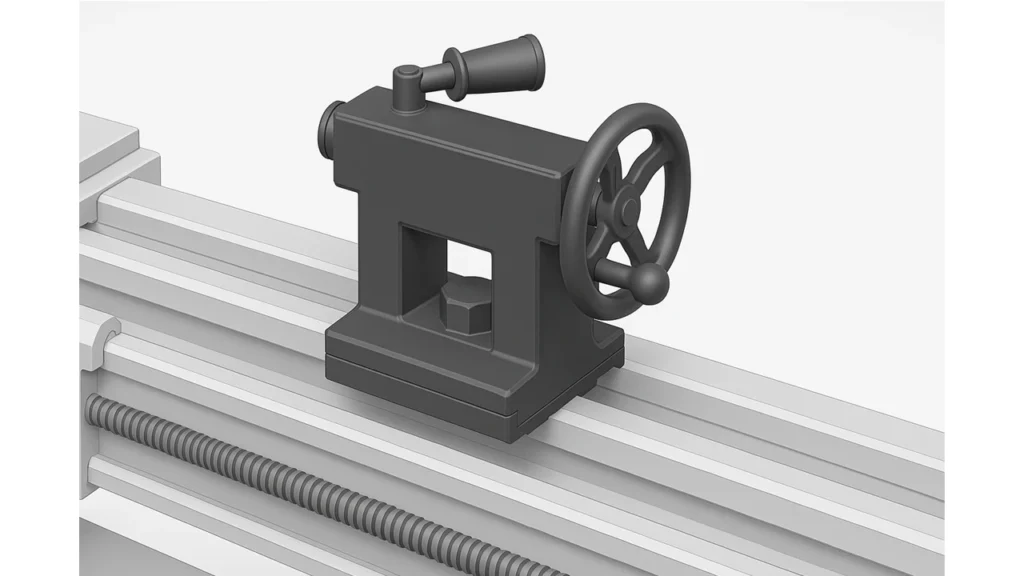
CNC Control Unit
The CNC control unit is the system that interprets the programmed instructions (usually in G-code) and issues real-time commands to the motors, actuators, and subsystems. It manages spindle rotation, feed rates, tool changes, and coolant flow.
Most CNC systems include a graphical user interface, manual data input (MDI) panel, emergency stops, and communication ports. Popular systems like FANUC, Siemens, and Mitsubishi offer advanced features such as tool radius compensation, adaptive feed control, and real-time diagnostics.
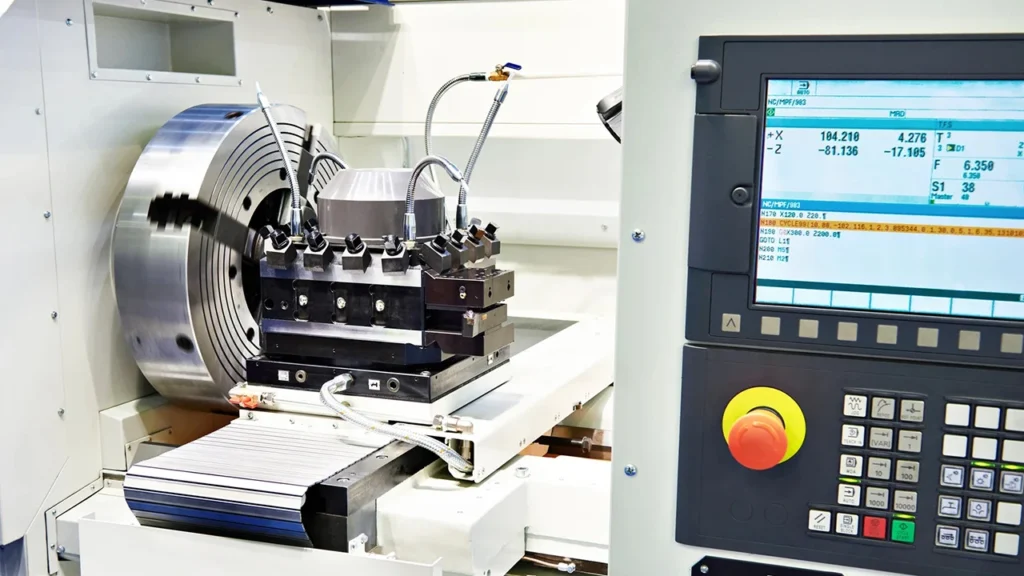
Coolant and Chip Removal System
Efficient chip evacuation and cooling are essential for maintaining cutting performance, extending tool life, and ensuring machine cleanliness. CNC lathes use flood or mist coolant systems to manage cutting heat and lubricate the tool-workpiece interface.
Chip conveyors or augers remove metal chips from the cutting area and transfer them to a collection bin. Poor chip management can lead to recutting, surface defects, and machine damage, making this subsystem critical to long-term reliability.
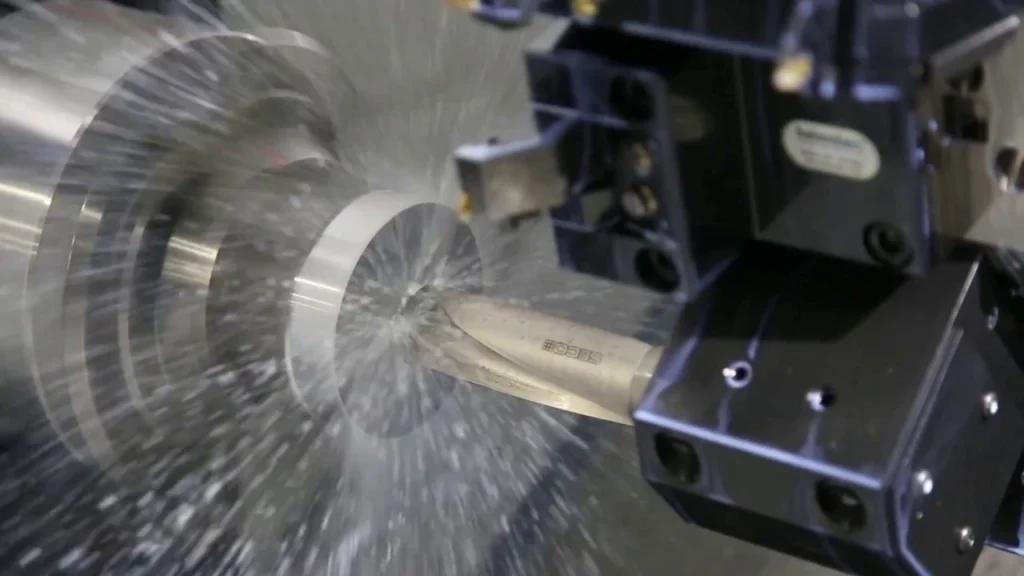
Types of CNC Lathes and Their Specialties
CNC lathes come in several configurations, each designed to accommodate different types of workpieces, machining requirements, and production volumes. The classification is typically based on spindle orientation, axis configuration, and tool system complexity. Selecting the appropriate type of CNC lathe depends on the part geometry, precision level, material properties, and available floor space.
Some machines are optimized for simple cylindrical parts, while others are engineered for complex, multi-surface components requiring simultaneous operations. The following are the most common types of CNC lathes found in modern manufacturing environments, each with distinct structural and functional characteristics.
Horizontal CNC Lathe
The horizontal CNC lathe is the most widely used configuration. In this setup, the spindle is mounted horizontally, and the tool turret or tool post moves along the X and Z axes. Workpieces are held in a chuck mounted on the spindle, and chips fall naturally downward, making cleanup efficient.
This type of lathe is suitable for machining a wide variety of shaft-type and disc-type parts. It is ideal for external and internal turning, facing, threading, and drilling. Horizontal CNC lathes are highly versatile and can be found in applications ranging from small batch prototyping to high-volume production lines.
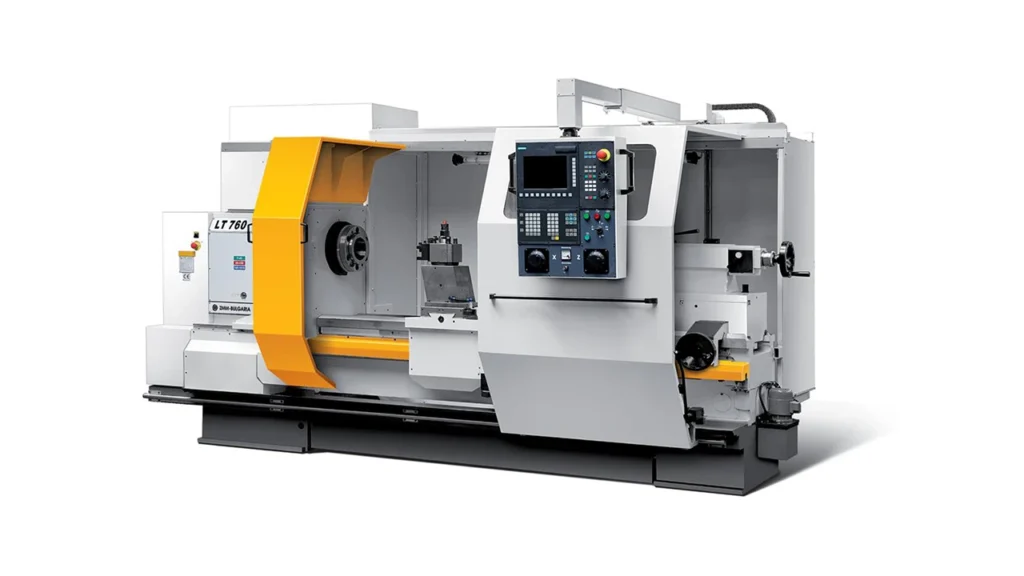
Vertical CNC Lathe
In a vertical CNC lathe, the spindle is oriented vertically, and the workpiece is mounted on a horizontal rotating table. This configuration is especially useful for machining large, heavy, or asymmetrical parts that would be difficult to support on a horizontal axis.
Vertical lathes are commonly used in industries such as energy, heavy equipment, and aerospace, where large flanges, casings, or rotors need to be machined. The vertical setup provides better support for gravity-sensitive components and simplifies the loading of heavy workpieces using cranes or lifts.
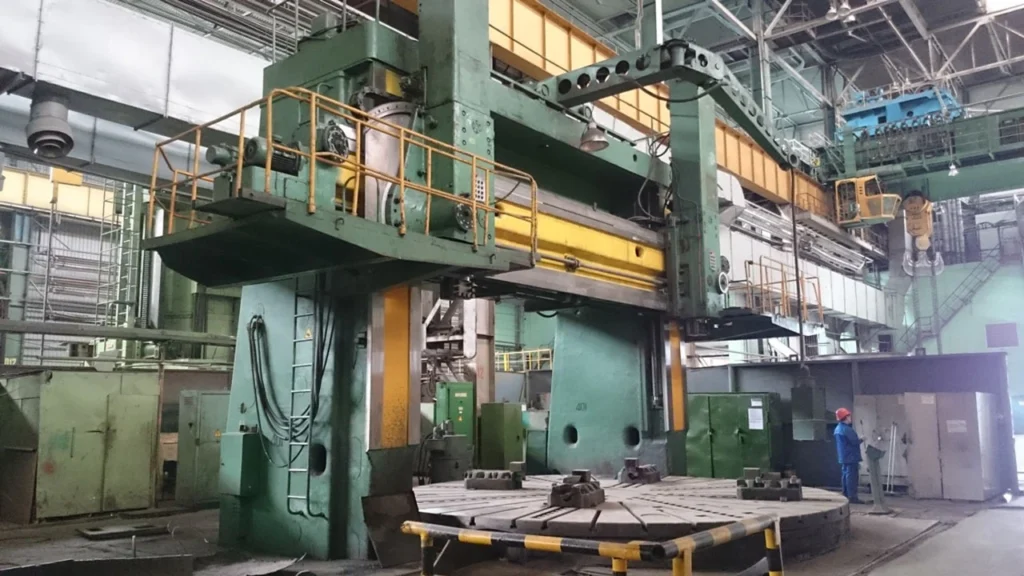
Swiss-Type CNC Lathe
Swiss-type CNC lathes, also known as sliding headstock lathes, are designed for high-precision, small-diameter parts. In these machines, the workpiece moves axially through a guide bushing while the cutting tools remain fixed. This unique configuration reduces deflection and improves accuracy during long, slender part machining.
Swiss lathes often feature multiple axes (up to 9 or more), live tooling, and dual spindles, enabling simultaneous machining on both ends of the part. They are commonly used in the medical, electronics, and watchmaking industries for producing components with extremely tight tolerances and fine features.
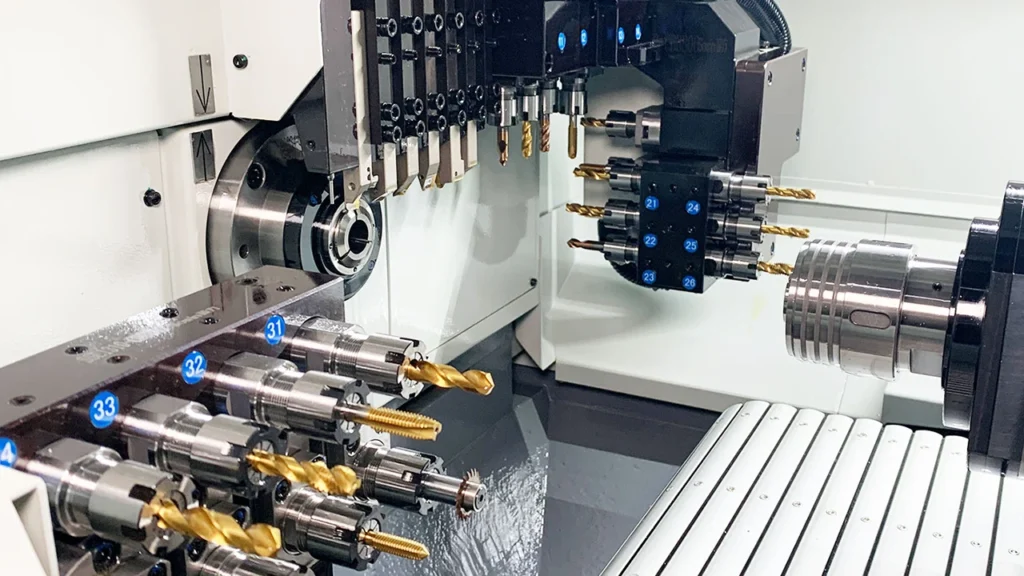
Pipe Threading Lathe
Pipe threading lathes are specialized CNC machines designed specifically for cutting various types of threads on large-diameter pipes. These machines are typically equipped with a heavy-duty spindle, reinforced bed, and high-torque drive systems to handle the size and weight of pipe materials.
They can cut external and internal threads, including taper threads, API threads, and trapezoidal threads. These lathes are widely used in the oil and gas, plumbing, and petrochemical industries, where threaded pipe connections are standard. The machines often include thread compensation and synchronization systems to ensure consistent quality.
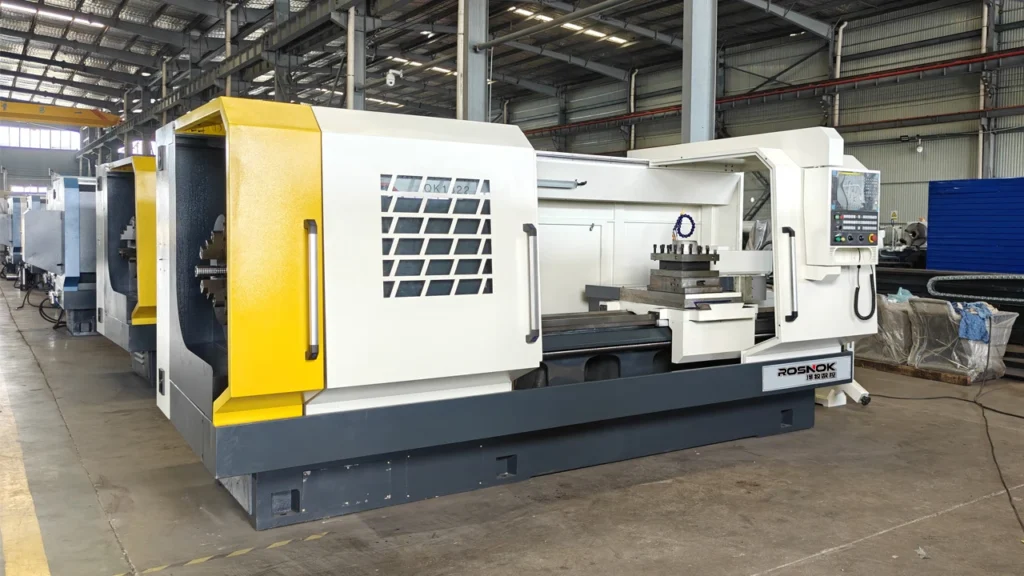
Slant Bed CNC Lathe
A slant bed CNC lathe features an inclined machine bed, typically set at an angle between 30° and 60°. This design improves both the structural rigidity of the machine and the efficiency of chip evacuation. The angled layout allows gravity to assist in moving chips away from the cutting zone, which helps maintain a clean work area and prevents chip accumulation during continuous operations.
The slant bed also enhances operator ergonomics by providing better access to the tool turret and workpiece. This configuration allows for a compact footprint while maintaining high rigidity, making it suitable for medium to high-speed cutting applications. It is widely used in general-purpose turning, especially where improved cutting stability and accessibility are desired.
Slant bed lathes are a common choice in automotive parts machining, general metalworking, and applications requiring strong structural support during aggressive cutting cycles.
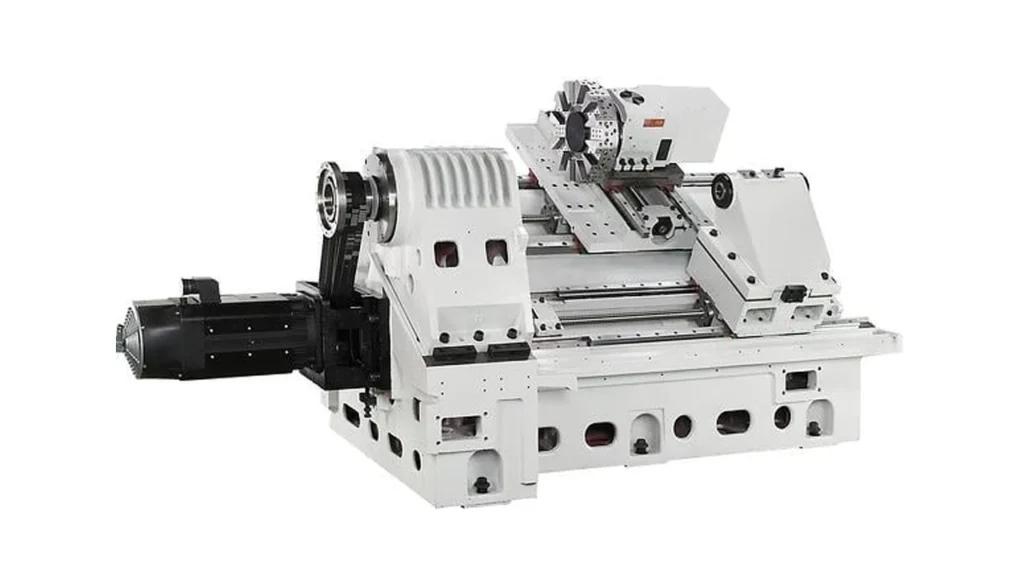
Multi-Turret CNC Lathe
A multi-turret CNC lathe is equipped with two or more tool turrets, allowing multiple tools to operate simultaneously on the same or different sections of a workpiece. These machines significantly increase productivity by reducing idle time between tool changes and enabling parallel machining operations.
In dual-turret configurations, one turret typically handles external turning while the other may perform internal boring or threading simultaneously. Triple-turret lathes offer even greater flexibility, especially in complex, multi-feature parts or short-cycle production. Synchronization between turrets is controlled by the CNC system to avoid collisions and ensure smooth transitions.
This type of lathe is ideal for industries requiring high-volume output with minimal cycle time, such as precision automotive components, hydraulic parts, and connectors.
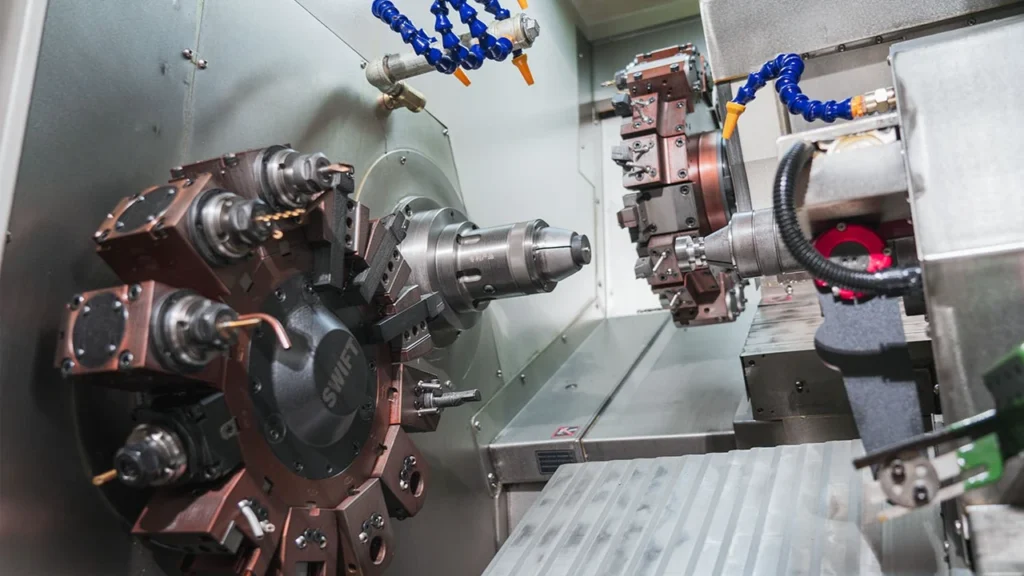
CNC Turning Center (Mill-Turn Lathe)
A CNC turning center, also known as a mill-turn lathe, is an advanced lathe that combines traditional turning capabilities with milling, drilling, tapping, and sometimes even Y-axis motion. These machines are equipped with live tooling, which allows rotary tools to perform non-rotational operations without transferring the part to a separate milling machine.
Turning centers often include sub-spindles, Y-axes, and tool turrets capable of indexing both static and driven tools. This integration enables complete part machining in a single setup, reducing total production time and improving dimensional accuracy.
These machines are commonly used for complex parts that require both turning and secondary operations, such as aerospace fittings, precision medical implants, and high-value custom components. Their versatility makes them a popular choice for manufacturers seeking to streamline operations and minimize handling.
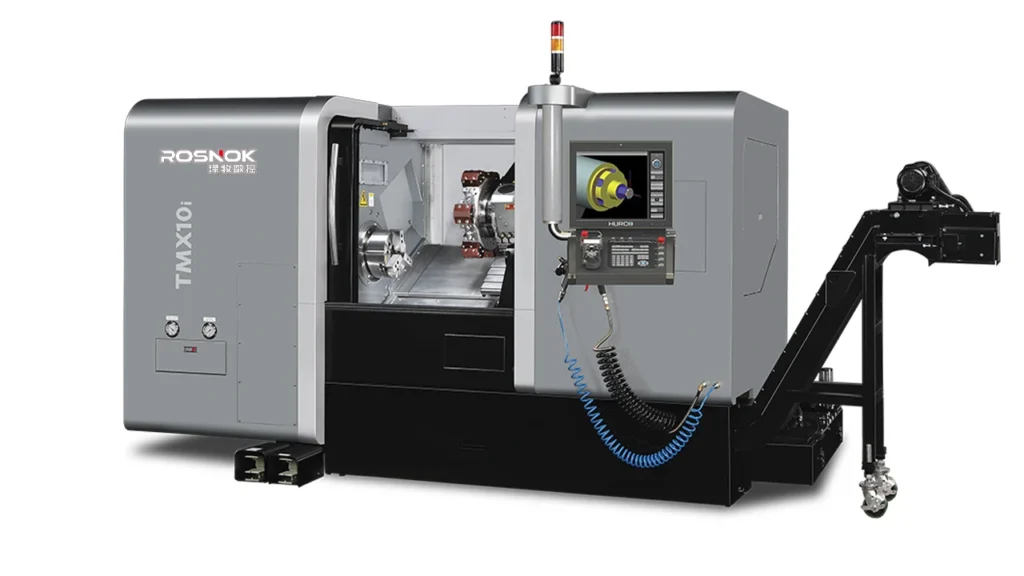
Machining Operations Performed on a CNC Lathe
A CNC lathe is designed to execute a wide range of machining operations that involve shaping material—typically metal—by rotating the workpiece and applying cutting tools in controlled paths. These operations are performed automatically based on the programmed instructions and the configuration of the machine’s tooling and axis system.
CNC lathes can handle simple processes like turning and facing, as well as more complex operations such as internal boring, threading, and grooving. In advanced models with live tooling or Y-axis capability, even functions like drilling, milling, and tapping can be performed without moving the workpiece to another machine. The result is a highly efficient, multi-functional machining process that reduces production time and enhances dimensional accuracy.
Below are the common operations that a CNC lathe can perform, each contributing to the part’s final geometry and surface quality.
1. External Turning
External turning is the most fundamental operation performed on a CNC lathe. It involves removing material from the outside diameter of a rotating workpiece using a single-point cutting tool. The tool moves parallel to the axis of rotation (Z-axis) to reduce the diameter and shape the outer contour.
This process is commonly used to create cylindrical shapes, steps, tapers, and shoulders. Surface finish and dimensional accuracy depend on cutting speed, feed rate, tool geometry, and material properties.
2. Internal Boring
Internal boring is used to enlarge and finish pre-drilled holes in a workpiece. A boring bar, held in the turret, moves inside the rotating part along the Z-axis to refine the internal diameter to a precise tolerance.
Boring provides better concentricity and surface finish than drilling alone. It’s essential for applications where internal diameters must meet tight dimensional or surface specifications, such as in bearing housings or fluid components.
3. Thread Cutting
Thread cutting on a CNC lathe involves synchronizing the tool movement with the spindle rotation to form internal or external threads. This can be done using single-point threading tools or tapping tools if live tooling is available.
CNC programs control pitch, depth, and lead angle, allowing for metric, imperial, trapezoidal, and custom thread profiles. The process ensures consistent thread geometry across batches, making it ideal for parts requiring repeatability and sealing performance.
4. Facing
Facing creates a flat surface on the end of a workpiece by moving the tool perpendicular to the spindle axis (X-axis). It’s typically the first operation in a turning cycle and establishes the reference surface for all subsequent cuts.
This process ensures squareness and flatness at the part’s end, which is critical for components that must seat or align properly with other parts in an assembly.
5. Grooving
Grooving involves cutting a narrow channel or recess on the external or internal surface of a part. Grooves are used for O-rings, retaining rings, snap rings, or reliefs for threading.
Specialized grooving tools are used, and depth control is critical to maintain function without weakening the part. CNC programming allows precise placement and repeatable dimensions.
6. Drilling
CNC lathes equipped with axial or radial drilling capability can drill holes into the face or diameter of a part. For axial holes, the tool moves along the spindle centerline; for radial holes, live tooling and a Y-axis are often required.
Drilling is often followed by reaming or boring to refine the hole, especially for press-fit or fluid passages.
7. Parting-Off
Parting-off, or cutoff, is the operation where the finished component is separated from the remaining bar stock. It uses a thin, sharp tool to slice through the rotating workpiece along the radial axis.
Proper chip evacuation and coolant flow are crucial to prevent tool breakage or poor surface finish on the separated edge.
8. Taper Turning
Taper turning creates a gradually decreasing or increasing diameter along the length of the part. This is done by moving the tool simultaneously along the X and Z axes at a defined angle.
Tapered sections are used for shafts, mating parts, and components requiring friction fits. CNC control ensures precise taper angles and transition lengths.
9. Knurling
Knurling forms a textured pattern—usually cross-hatched or straight—on the outer surface of a part. It is a cold-forming process done with special knurling wheels pressed against the rotating workpiece.
Knurling improves grip on hand-operated parts like knobs and handles. Since it displaces rather than cuts material, machine rigidity is important.
10. Profile Turning
Profile turning refers to machining complex contours or curves along the part’s length. It combines multiple turning paths and tool movements to generate non-uniform geometries such as radii, grooves, and shoulders.
This operation is often used in decorative components, ergonomic designs, and parts with functional curves, such as camshafts or handles.
11. Milling (With Live Tooling)
In advanced CNC lathes equipped with live tooling, milling operations can be performed on the rotating workpiece while it is still clamped in the chuck. This includes operations like face milling, slot milling, and profile milling.
Live tooling allows the lathe to perform these operations without the need to transfer the part to a separate milling machine, significantly improving efficiency and reducing handling time. This feature is especially valuable for complex parts that require both turning and milling, such as gear components, housings, and multi-featured mechanical parts.
12. Tapping (With Live Tooling)
Tapping, the process of creating threads in a drilled hole, can also be carried out on CNC lathes with live tooling. A tapping tool is rotated while the workpiece is fed into the tool in a controlled manner. CNC lathes allow for both internal and external threading through tapping, as well as custom thread profiles.
Live tooling capabilities allow tapping at various angles (including radial or axial directions) for added versatility. The machine’s CNC system ensures precise synchronization between the feed motion and spindle rotation to create consistent thread depth and pitch.
13. Boring (With Live Tooling)
While boring is a common turning operation, certain CNC lathes with live tooling can use a rotary tool to perform external or internal boring operations. Boring allows for the creation of highly accurate, smooth holes with tight tolerances.
It is particularly useful when the initial hole diameter needs to be precisely refined or when machining deep holes, such as for hydraulic cylinders or pump components. Using live tooling, CNC lathes can complete both rough and finish boring operations in one setup.
14. Milling and Drilling (With Sub-Spindles)
Some CNC lathes come with sub-spindles that allow for additional operations like milling and drilling to be done while the main spindle is engaged with the part. The sub-spindle can hold the part while the main spindle continues working, making it ideal for multi-step operations.
In such setups, the part does not need to be removed or re-clamped for secondary operations, reducing setup times and improving overall process efficiency.
Applications of CNC Lathes
CNC lathes are versatile machines that can be used in a variety of industries for manufacturing parts with high precision and repeatability. Their ability to perform complex operations, such as turning, boring, threading, and even milling, makes them essential in sectors where accuracy and efficiency are crucial. CNC lathes are particularly beneficial for industries requiring high volumes of parts, intricate geometries, and tight tolerances.
Below are some of the key industries that rely heavily on CNC lathes for their manufacturing processes.
Aerospace Industry
In the aerospace sector, CNC lathes are essential for manufacturing high-precision components such as turbine blades, engine shafts, and airframe parts. These components often require complex geometries and tight tolerances to meet safety and performance standards.
CNC lathes with live tooling and multi-axis capabilities allow for the production of intricate parts in a single setup, reducing handling time and improving part consistency. These machines also support the use of advanced materials, such as titanium and high-strength alloys, which are commonly used in aerospace applications.
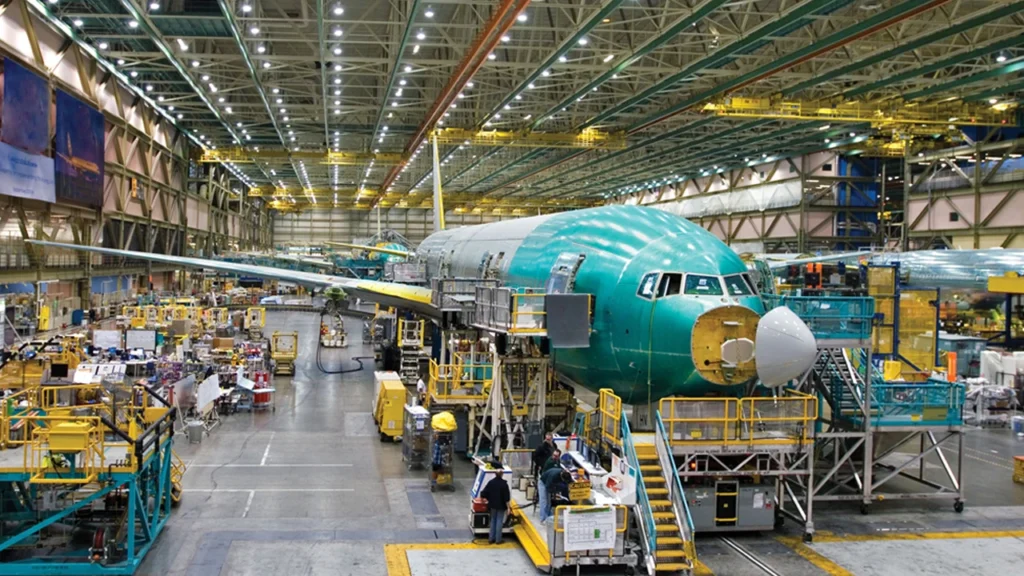
Automotive Industry
The automotive industry relies on CNC lathes for manufacturing a wide variety of components, including engine blocks, crankshafts, pistons, gears, and transmission parts. These parts require tight tolerances, smooth surface finishes, and the ability to withstand high-stress conditions.
CNC lathes offer the flexibility to produce both small and large quantities of automotive components with consistent quality. Features like sub-spindles, multi-turret configurations, and advanced tool changers allow for efficient multi-step operations and high-volume production, making them ideal for automotive manufacturing.
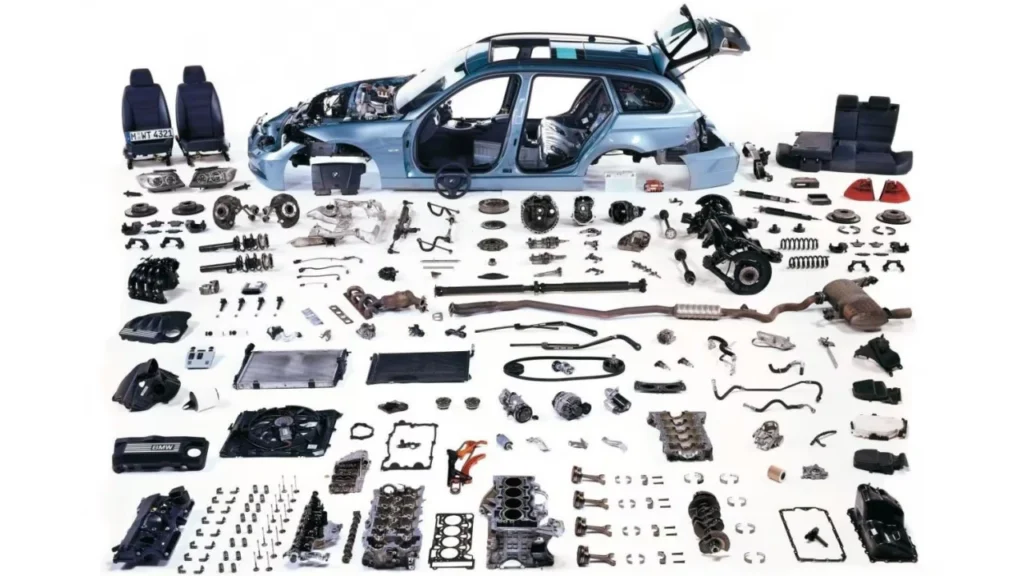
Medical Device Industry
In the medical device industry, CNC lathes are used to manufacture high-precision parts such as surgical instruments, implants, and diagnostic devices. These parts often require stringent tolerances and biocompatibility, as they must meet both functional and safety standards.
CNC lathes equipped with live tooling and multi-axis functionality are particularly useful for producing complex geometries and intricate designs, such as those required for orthopedics or dental implants. These machines are essential for both prototyping and high-volume production of medical components.
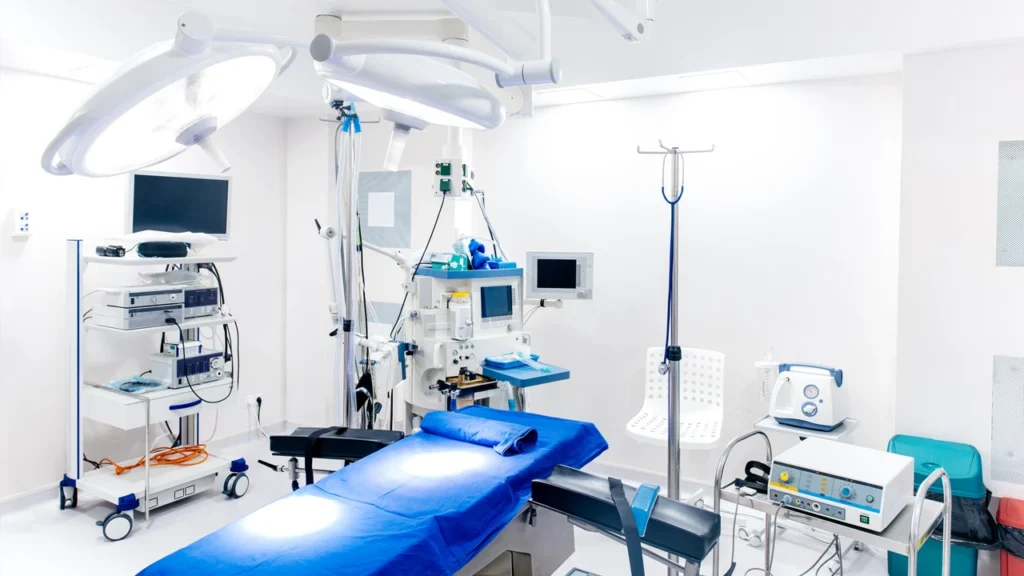
Electronics and Precision Components
CNC lathes are crucial for manufacturing small, high-precision components used in electronics, such as connectors, housings, switches, and shafts. These components often require tight tolerances, smooth finishes, and the ability to handle delicate materials like aluminum, copper, and various plastics.
With the ability to perform multiple operations, including turning, milling, and drilling, CNC lathes streamline the production of these components. Their high-speed capabilities make them ideal for meeting the fast-paced demands of the electronics industry.
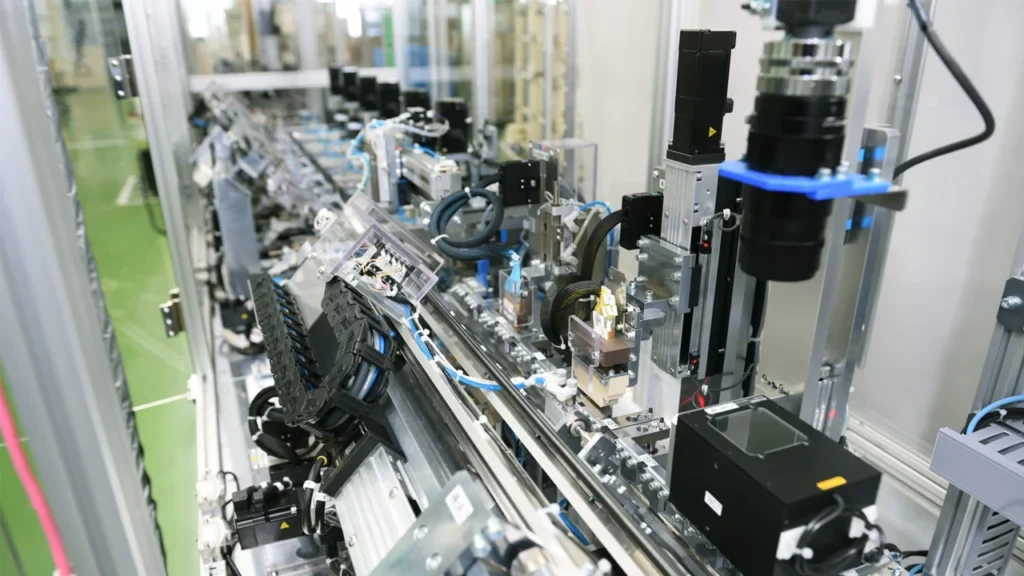
Energy and Power Generation Industry
In the energy and power generation industry, CNC lathes are used to manufacture parts for turbines, generators, pumps, and valves. These components often require heavy-duty machining and high precision to operate efficiently under extreme conditions.
CNC lathes are equipped with the power and rigidity needed for machining large, heavy parts, such as steam turbine rotors or valve bodies. The ability to perform multiple operations on the same machine reduces setup time and improves overall machining efficiency.
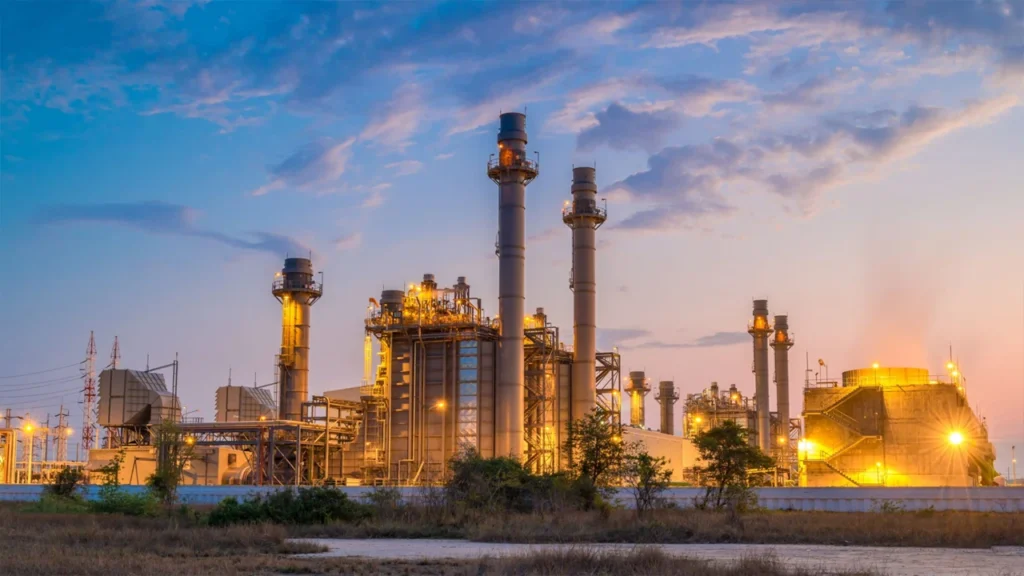
Heavy Machinery and Industrial Equipment
CNC lathes are also critical in the manufacturing of heavy machinery and industrial equipment, such as hydraulic cylinders, gearboxes, and machine components. These parts require precise machining to ensure performance and reliability under high-stress conditions.
The versatility of CNC lathes allows manufacturers to produce a wide range of parts for industries like construction, mining, and agriculture. The ability to machine large, complex parts in a single setup makes CNC lathes essential in producing heavy-duty components.
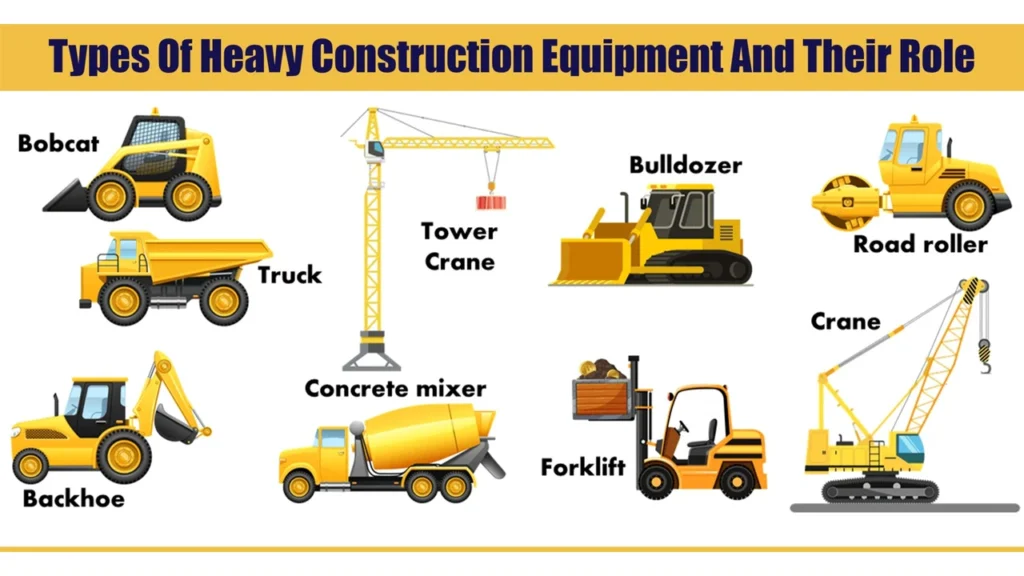
Advantages of Using a CNC Lathe
CNC lathes offer numerous benefits over traditional manual machining, making them indispensable in modern manufacturing environments. From increased precision and repeatability to reduced labor costs and shorter lead times, CNC lathes help manufacturers achieve high levels of productivity and quality while minimizing waste and errors. The integration of advanced technology has made CNC lathes essential for industries that require complex machining and consistent results.
Here are some of the key advantages of using a CNC lathe in manufacturing.
High Precision and Repeatability
One of the most significant advantages of CNC lathes is their ability to produce parts with exceptional precision and repeatability. Unlike manual lathes, where human error can lead to inconsistencies, CNC lathes operate based on pre-programmed instructions that ensure each part is made to exact specifications. This makes CNC lathes ideal for high-tolerance applications, such as aerospace and medical device manufacturing.
The high precision of CNC lathes also allows for consistent results over large production runs, which is essential for industries that require parts with identical dimensions and surface finishes.
Increased Efficiency and Productivity
CNC lathes are designed for speed and efficiency. Once the machine is set up and the program is loaded, the CNC lathe can run continuously without the need for constant supervision. This reduces downtime and allows for faster turnaround times, especially in high-volume production.
Advanced CNC lathes are capable of performing multiple operations in a single cycle, such as turning, drilling, milling, and threading. This eliminates the need to transfer the part between different machines, reducing handling time and improving overall efficiency. Additionally, CNC lathes can operate around the clock in automated systems, further increasing productivity.
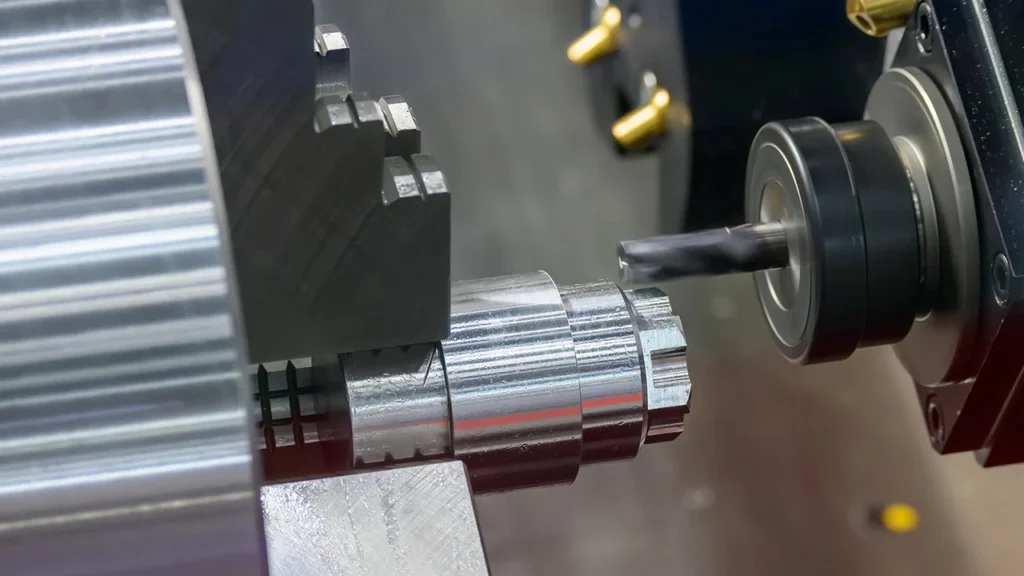
Versatility for Diverse Applications
CNC lathes are incredibly versatile machines that can be used in a wide range of applications. From simple cylindrical parts to complex components with multi-axis geometries, CNC lathes can handle a variety of materials, including metals, plastics, and composites. The ability to integrate different tools and tooling systems, such as live tooling, rotary tools, and multi-turret configurations, enhances the lathe’s capabilities and broadens its range of applications.
This versatility makes CNC lathes suitable for industries such as aerospace, automotive, medical devices, electronics, and energy, where a variety of parts and materials need to be machined with high precision.
Reduced Labor Costs and Manual Intervention
By automating the machining process, CNC lathes reduce the need for skilled labor and manual intervention. Operators are responsible for programming, machine setup, and quality control, rather than performing manual cutting or adjustments. This not only reduces the reliance on highly skilled labor but also minimizes the chances of human error, leading to more consistent quality.
Additionally, CNC lathes can run unattended for long periods, allowing manufacturers to focus on other tasks while the machine continues to work. This reduces overall labor costs and improves operational efficiency, especially in mass production settings.
Improved Safety and Operator Convenience
CNC lathes improve operator safety by minimizing direct interaction with moving parts. Since the machine operates automatically based on the program, operators are not exposed to the risks associated with manual machine operation. CNC lathes often come equipped with safety features such as automatic shutdowns, protective enclosures, and emergency stops, further enhancing workplace safety.
Furthermore, the user interface of CNC systems is designed for ease of use, with intuitive controls and real-time monitoring capabilities that allow operators to make quick adjustments as needed. This makes CNC lathes accessible to operators with various skill levels, while maintaining high levels of precision and control.
Cost-Effectiveness in Mass Production
CNC lathes are highly cost-effective for mass production due to their ability to perform repetitive tasks with consistent results. Once a program is set up and tested, the lathe can run continuously, producing large quantities of parts with minimal human intervention.
The reduced cycle times, increased throughput, and consistent quality of CNC lathes lead to significant cost savings over time. Additionally, CNC lathes can minimize material waste by optimizing cutting paths and reducing scrap rates, making them an excellent investment for manufacturers seeking to improve profitability.
Ability to Perform Multi-Axis Machining
Modern CNC lathes are often equipped with multi-axis capabilities, allowing them to perform complex machining tasks that would otherwise require multiple setups or machines. For example, CNC lathes with a Y-axis or live tooling can perform milling, drilling, and tapping operations, expanding their functionality beyond traditional turning.
This multi-axis capability enables the lathe to produce intricate parts with complex geometries in a single setup, improving accuracy, reducing setup time, and increasing efficiency. Multi-axis CNC lathes are particularly valuable for industries such as aerospace and medical device manufacturing, where parts often have complex shapes and require high precision.
Scalability for Future Production Needs
CNC lathes offer scalability to meet future production demands. As production needs grow, manufacturers can easily scale up by adding additional CNC machines or integrating existing machines into a larger automated system. The flexibility of CNC programming allows for quick adjustments to accommodate changes in part designs, materials, or production volumes.
This adaptability makes CNC lathes an ideal choice for industries that experience fluctuating production requirements or need to produce a wide variety of parts on short notice.
Environmentally Friendly and Energy Efficient
Many modern CNC lathes are designed with energy efficiency and environmental sustainability in mind. Advanced features such as energy-saving motors, efficient cooling systems, and automatic shut-off functions help reduce energy consumption during operation.
Additionally, CNC lathes often use cutting fluids that can be filtered, cleaned, and reused, reducing waste and minimizing the environmental impact of the machining process. Manufacturers who prioritize sustainability can benefit from these eco-friendly features while also improving their operational efficiency.
Challenges and Limitations of CNC Lathes
While CNC lathes offer numerous advantages in terms of precision, automation, and efficiency, they also come with certain challenges and limitations. These factors need to be considered when selecting a CNC lathe for a particular application, as they can impact overall performance, cost, and the scope of operations.
Understanding the potential drawbacks helps manufacturers make informed decisions and adopt the right strategies for overcoming these challenges. Below are some of the most common challenges and limitations associated with CNC lathes.
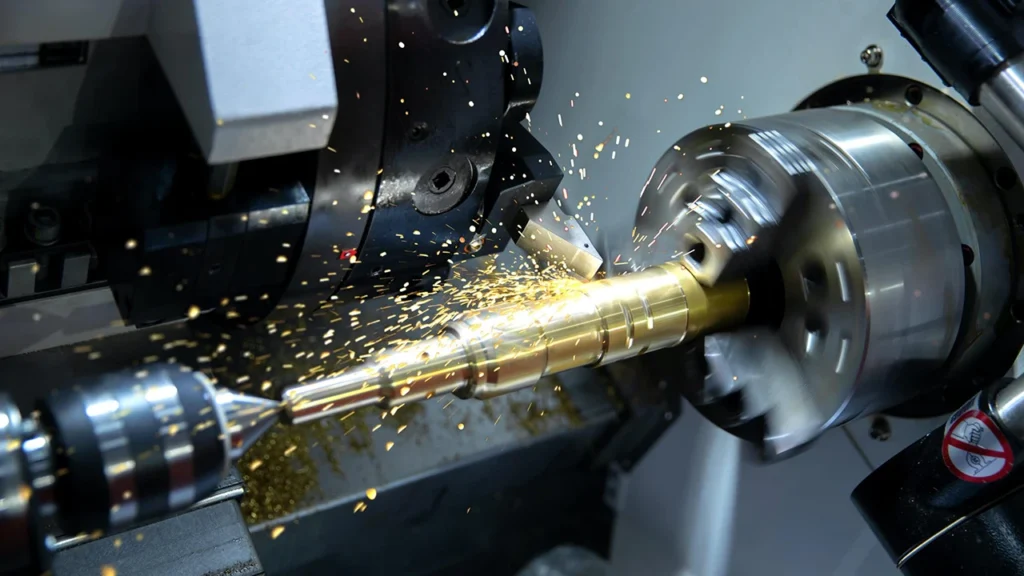
High Initial Investment
One of the biggest challenges of CNC lathes is the high initial cost. The purchase price of a CNC lathe can be significantly higher than that of traditional manual lathes due to the advanced technology, automation, and precision components involved. Additionally, costs related to installation, training, and software programming may add to the total investment.
While the long-term benefits of CNC lathes, such as increased productivity, precision, and reduced labor costs, can offset the initial investment, smaller businesses or those with limited budgets may find the upfront cost prohibitive. However, leasing options and financing programs may be available to help manage the financial burden.
Skill and Training Requirements
Operating a CNC lathe requires specialized knowledge and skills, including proficiency in programming, machine setup, and troubleshooting. CNC programming languages, such as G-code and M-code, can be complex, and operators must understand both the software and hardware aspects of the machine to optimize performance.
As a result, companies must invest in training programs to ensure their workforce is adequately equipped to handle the machine. The need for skilled operators can lead to higher labor costs, especially in smaller companies where training or hiring experienced personnel may be challenging.
Maintenance and Downtime Risks
CNC lathes are precision machines that require regular maintenance to ensure optimal performance. Routine tasks such as cleaning, lubricating, and replacing worn-out parts (such as cutting tools and ball screws) are essential to maintain machine accuracy and reliability.
Unexpected downtime due to mechanical failures, electrical issues, or software glitches can significantly impact production schedules. Additionally, maintenance costs can add up over time, especially if the machine is heavily used or exposed to harsh operating conditions. Some manufacturers opt for service contracts or preventive maintenance schedules to minimize unplanned downtime.
Programming Complexity for Advanced Operations
As CNC lathe systems become more advanced, programming for complex operations becomes increasingly difficult. Multitasking functions, multi-axis machining, and live tooling require a deeper understanding of the machine’s capabilities and the programming language.
While modern CNC systems often include user-friendly interfaces and automated programming options, the complexity of custom operations still requires a high level of expertise. In cases where intricate parts need to be designed or modified, the programming process may be time-consuming and prone to errors if not handled correctly.
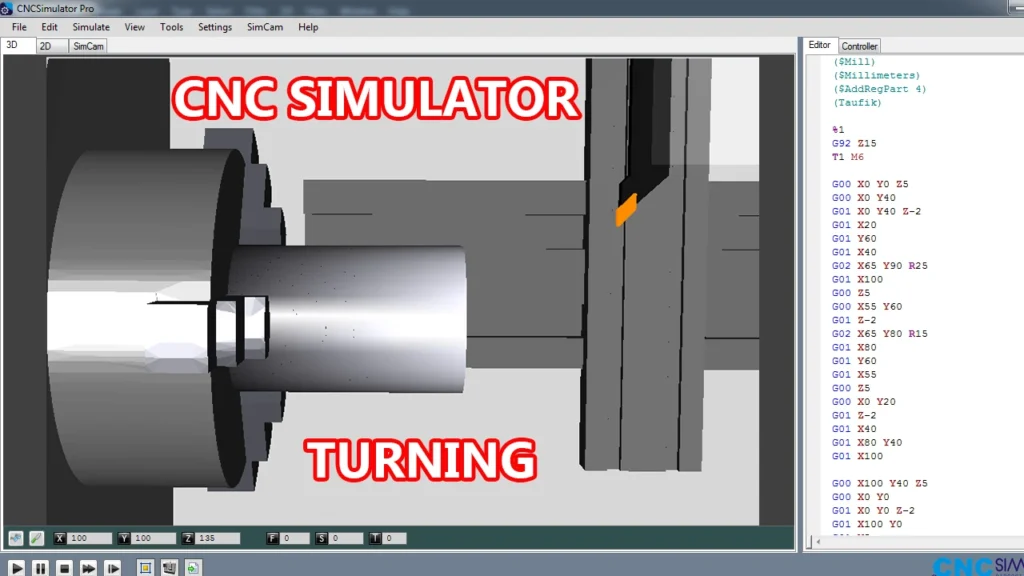
High Energy Consumption
CNC lathes, especially those with multiple axes, high-speed spindles, and live tooling capabilities, can consume significant amounts of energy during operation. The high power demands associated with maintaining spindle speed, tool movement, and other machine functions can lead to increased energy costs, particularly when operating multiple machines in a factory environment.
Manufacturers looking to reduce operating costs and improve sustainability may need to implement energy-saving measures, such as using efficient motors, optimizing machine settings, and integrating energy-efficient systems. Some newer models of CNC lathes come with energy-saving features designed to minimize power consumption.
Limited Flexibility for Low-Volume Production
While CNC lathes excel in high-volume production settings, they may not be as efficient for low-volume or one-off production runs. The setup time required to configure the machine, load programs, and adjust tooling can make small production batches less cost-effective.
For industries that require frequent design changes, custom parts, or rapid prototyping, traditional manual machining or other flexible manufacturing systems might be more appropriate. However, advancements in quick-change tooling systems and faster programming methods are helping to reduce setup times and improve the flexibility of CNC lathes for smaller production runs.
Space and Infrastructure Requirements
CNC lathes are large, heavy machines that require significant floor space and proper infrastructure. The installation area must accommodate the size of the machine and provide adequate clearance for operation and maintenance. In addition, CNC lathes may require specific environmental conditions, such as temperature control and vibration isolation, to maintain precision during machining.
In smaller shops or manufacturing environments with limited space, fitting multiple CNC machines can become a logistical challenge. Proper planning and factory layout considerations are essential to ensure that machines can be installed and operated efficiently.
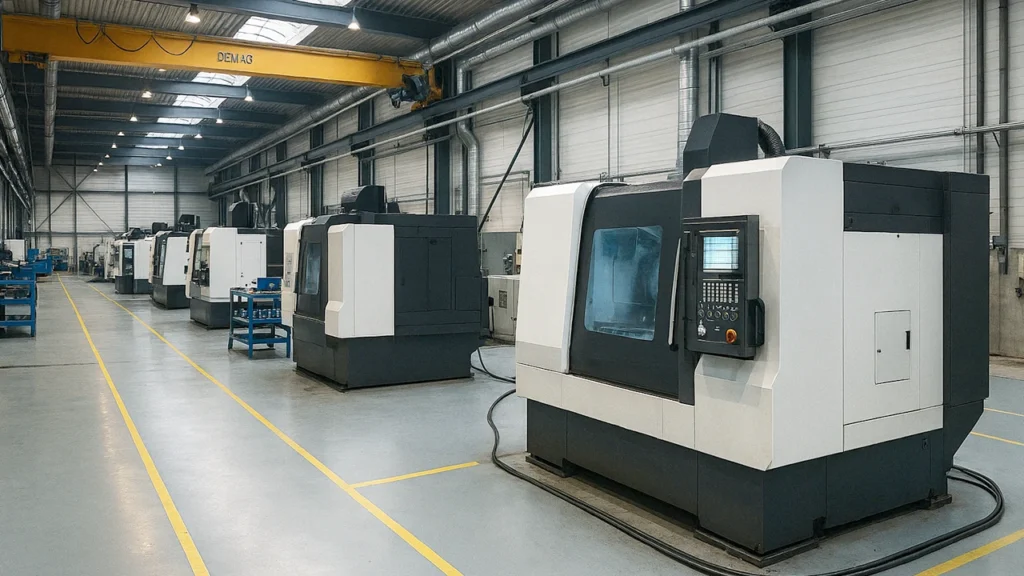
How to Choose the Right CNC Lathe
Selecting the right CNC lathe for a specific application is crucial for maximizing productivity, minimizing costs, and ensuring the desired level of precision. With so many types, features, and options available, choosing the right machine can be a challenging task. However, by carefully considering factors such as production requirements, material properties, machine specifications, and available budget, manufacturers can make an informed decision.
In this section, we’ll discuss the key factors to consider when choosing the right CNC lathe for your needs, from understanding your production goals to evaluating the technical specifications of various machines.
Understand Your Production Needs
The first step in choosing the right CNC lathe is to clearly define your production requirements. Consider the following factors:
- Volume: Are you looking for a machine for low-volume, high-precision parts or high-volume production runs?
- Part Complexity: Will you be machining simple cylindrical parts or more complex geometries that require multi-axis or live tooling capabilities?
- Material Types: What materials will you be machining? Soft materials like aluminum or tough materials like titanium may require different spindle speeds, tooling, and coolant systems.
- Tolerances: Determine the level of precision required for your parts. High-tolerance work may require a more advanced CNC lathe with higher rigidity and finer control.
By understanding these aspects, you can better determine whether a standard CNC lathe, multi-axis machine, or specialized lathe would be the best fit for your needs.
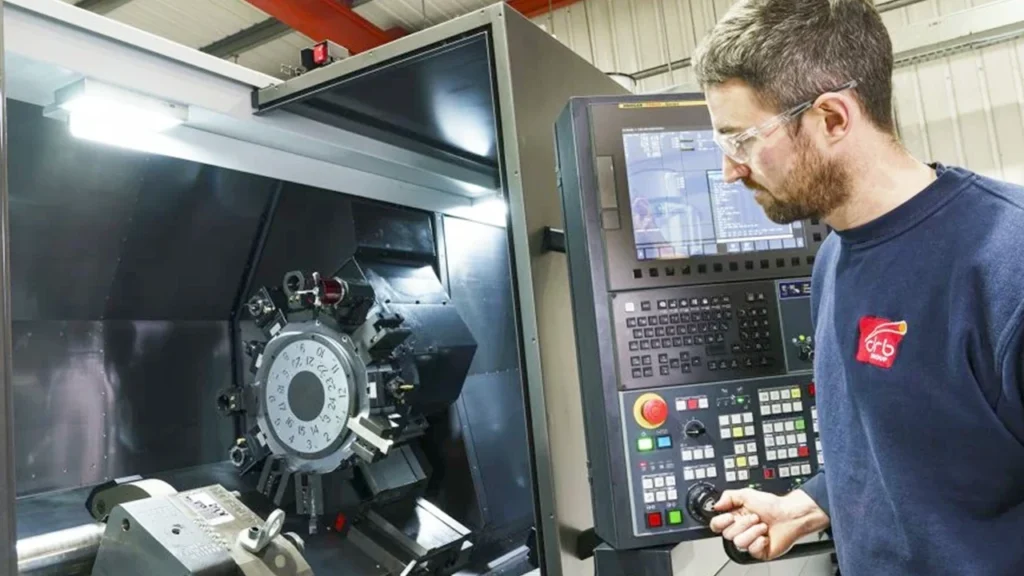
Consider Machine Size and Workpiece Dimensions
The size of the CNC lathe should match the size of the parts you plan to produce. CNC lathes come in various sizes, with different capacities to accommodate workpieces of varying dimensions and weights. Larger machines are necessary for machining bigger, heavier parts, while smaller machines are more suitable for precision machining of smaller components.
Pay close attention to the maximum swing (the largest diameter part the lathe can accommodate) and the maximum machining length (the longest part that can be machined along the Z-axis). Ensure that the machine you select can handle the typical size range of the parts you manufacture.
Evaluate CNC Control System and Software
The CNC control system is the heart of the lathe, and it plays a crucial role in determining machine performance. The control system interprets the program code (e.g., G-code) and controls the movement of the machine axes, spindle, and tool changes. Popular CNC control systems include FANUC, Siemens, Mitsubishi, and Heidenhain.
When selecting a CNC lathe, evaluate the following aspects of the control system:
- Ease of Use: Is the interface intuitive and user-friendly? A more user-friendly interface can minimize training time and reduce errors.
- Programming Capabilities: Does the control system support complex programming functions such as multi-axis machining, tool offsets, and compensation for wear and tear?
- Compatibility: Ensure that the CNC system is compatible with your CAM software and can handle the specific type of machining required for your parts.
The control system can have a significant impact on the overall productivity and ease of use, so it’s essential to choose a system that aligns with your needs.
Assess Spindle Speed and Power
Spindle speed and power are two critical factors that directly affect cutting performance and machining speed. The spindle speed determines how fast the workpiece rotates, while spindle power impacts the material removal rate and ability to machine tougher materials.
- High-Speed Spindles: Ideal for light cutting, fine finishes, and materials like aluminum, high-speed spindles often have higher RPM ranges.
- High-Power Spindles: Necessary for heavy-duty cutting, such as machining harder materials like steel, titanium, or hardened alloys.
When selecting a CNC lathe, make sure to match the spindle power and speed with the material properties and machining requirements of your workpieces.
Check for After-Sales Support and Warranty
CNC machines are complex and require ongoing support to maintain peak performance. When choosing a CNC lathe, consider the reputation and reliability of the manufacturer, particularly in terms of after-sales support.
Key factors to evaluate include:
- Warranty: Does the manufacturer offer a comprehensive warranty for parts, labor, and service?
- Technical Support: How quickly can you expect to receive assistance if the machine experiences an issue? A responsive support team is essential for minimizing downtime.
- Spare Parts Availability: Ensure that the manufacturer has readily available spare parts for quick replacements if necessary.
Strong after-sales support can significantly extend the lifespan of your CNC lathe and minimize downtime during production.
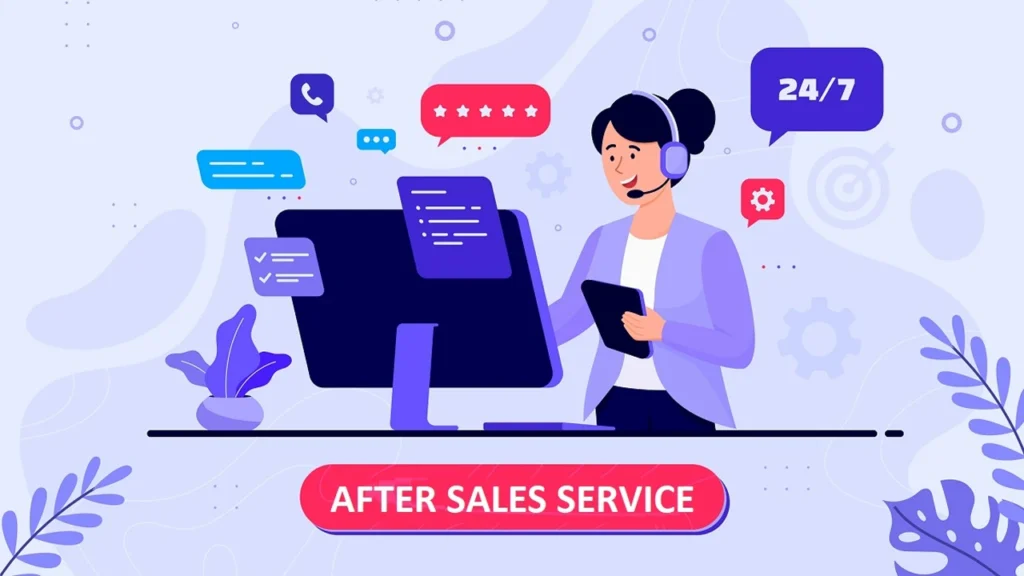
Analyze Automation and Integration Capabilities
As manufacturing processes become more automated, the ability to integrate your CNC lathe into a larger automated system can greatly enhance productivity. Features such as robotic arms, material handling systems, and automated tool changers can streamline production, reduce manual labor, and increase throughput.
If your business is looking to scale production or adopt a lights-out manufacturing approach, choose a CNC lathe that supports automation and integration with your existing systems. The ability to connect multiple machines and automate material loading/unloading is a valuable investment for high-volume operations.
Future Trends in CNC Lathes
As manufacturing technology continues to evolve, so do the capabilities of CNC lathes. The ongoing development of automation, digitalization, and precision machining is revolutionizing the way CNC lathes are used in industries across the globe. In the future, CNC lathes will not only become more efficient and accurate, but they will also integrate with advanced technologies to optimize production processes, improve machine intelligence, and reduce environmental impacts.
In this section, we will explore the emerging trends that are shaping the future of CNC lathe technology.
Adoption of AI and Machine Learning in Machining
Artificial intelligence (AI) and machine learning are poised to have a significant impact on CNC lathes, enabling more intelligent decision-making and automation in machining operations. By analyzing historical data and real-time sensor input, AI-powered CNC systems can optimize cutting parameters, adjust feed rates, and predict tool wear in real-time.
Machine learning algorithms can also enable predictive maintenance, identifying potential issues before they cause machine downtime. AI-driven systems can learn from previous machining cycles to continuously improve part quality, surface finish, and cycle time, making CNC lathes smarter and more autonomous.
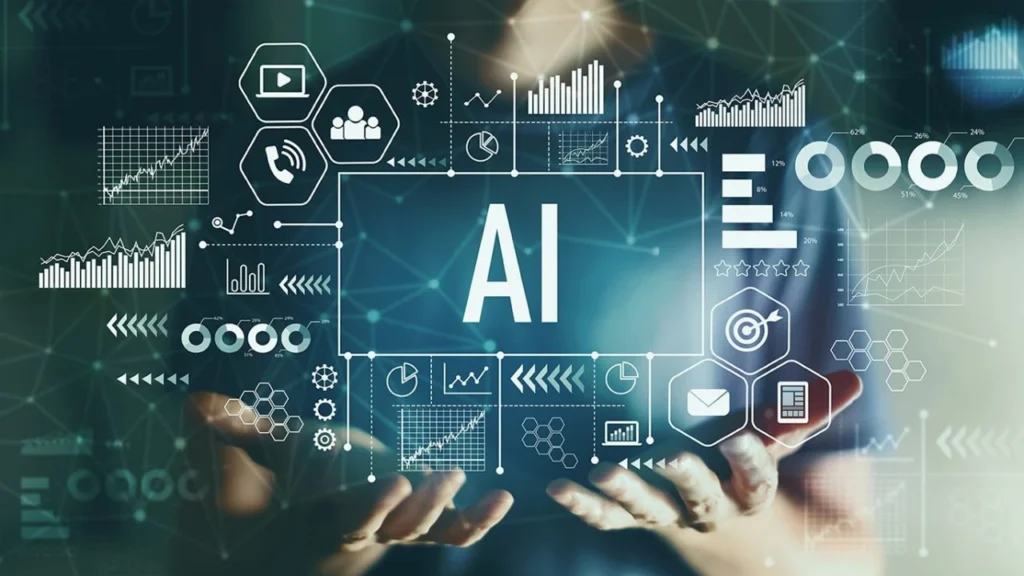
Integration of IoT and Industry 4.0 Technologies
The Internet of Things (IoT) is transforming the manufacturing industry by connecting machines, tools, and sensors through the cloud. CNC lathes equipped with IoT capabilities can communicate with other machines and devices, providing real-time data on machine performance, tool wear, and production status.
The integration of IoT with CNC lathes enables better visibility into production workflows, allowing manufacturers to monitor machine health, detect inefficiencies, and schedule maintenance more effectively. Additionally, data analytics tools can help optimize production schedules and reduce downtime, leading to more efficient operations and cost savings.
Industry 4.0 technologies, including smart sensors, autonomous robots, and data-driven analytics, are enhancing the automation and connectivity of CNC lathes, making them a central part of the smart factory ecosystem.
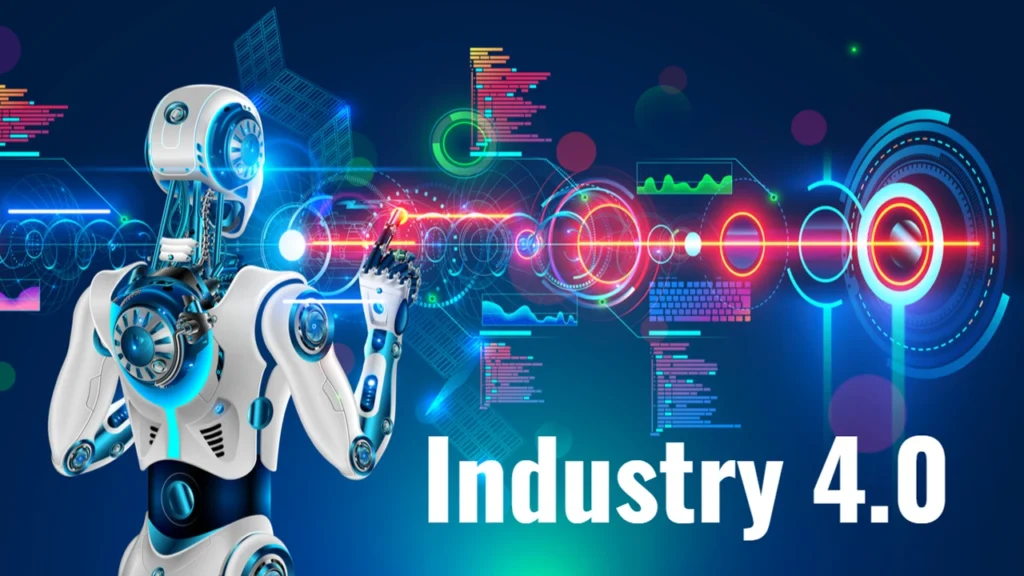
Advanced Automation and Lights-Out Manufacturing
The next frontier in CNC lathe technology is lights-out manufacturing, where CNC machines operate autonomously without human intervention. This level of automation is made possible through the integration of robotic arms, automated material handling systems, and advanced machine vision.
Robots can load and unload parts, change tools, and even perform inspections while the CNC lathe continues to run unattended. Lights-out manufacturing significantly reduces labor costs, improves throughput, and allows for continuous 24/7 production. As automation technology continues to advance, CNC lathes will become even more autonomous, further driving efficiency and reducing human labor requirements.
Growth of 5-Axis and Multi-Axis Machining
The demand for more complex parts with intricate geometries is driving the growth of 5-axis and multi-axis CNC lathes. These machines allow for simultaneous movement along multiple axes, enabling the machining of parts with complex shapes and features in a single setup.
5-axis and multi-axis CNC lathes are particularly valuable for industries like aerospace, automotive, and medical device manufacturing, where parts often have multiple angles, intricate curves, or tight tolerances. The ability to perform turning, milling, and drilling in one setup reduces part handling and increases efficiency, while also ensuring higher precision.
As the technology behind multi-axis machining becomes more affordable, more manufacturers will be able to leverage these machines for advanced manufacturing capabilities.
Digital Twin Technology for Virtual Machining
Digital twin technology is a cutting-edge trend in CNC lathes that involves creating a virtual replica of the machine or production process. This virtual model allows manufacturers to simulate machining operations, optimize programs, and predict potential issues without interrupting actual production.
Digital twins enable real-time monitoring and predictive analytics, making it easier to fine-tune processes, reduce errors, and improve machine uptime. They also facilitate virtual testing of new production methods, helping manufacturers innovate without disrupting the actual production line.
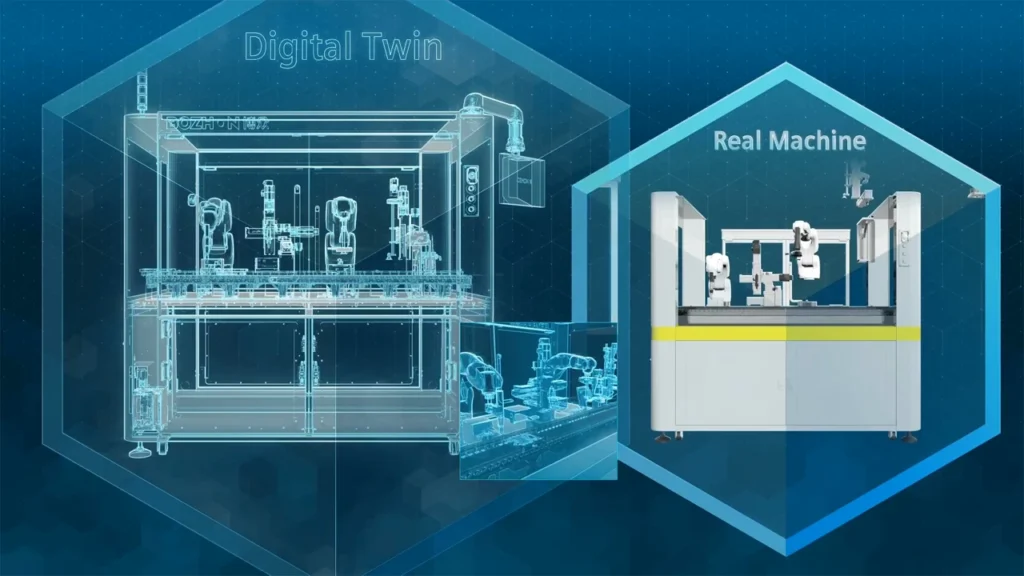
Increased Adoption of Hybrid Machining Technology
Hybrid machining combines traditional subtractive methods (like turning and milling) with additive manufacturing (such as 3D printing) on the same machine. This trend allows manufacturers to create more complex parts by adding material in specific areas during the machining process.
For example, a CNC lathe with hybrid capabilities can deposit metal in areas that require additional material for strength or geometric complexity, while still performing traditional turning and milling operations on the rest of the part. This technology is especially valuable for producing lightweight, high-performance parts used in industries like aerospace and automotive.
Emphasis on Sustainable and Eco-Friendly Machining
Sustainability is becoming a major focus in the manufacturing industry, and CNC lathe technology is evolving to meet these demands. Manufacturers are increasingly adopting eco-friendly practices, such as reducing energy consumption, minimizing material waste, and using biodegradable or recyclable cutting fluids.
Advancements in energy-efficient motors, regenerative braking, and more precise machining processes are helping to reduce the carbon footprint of CNC operations. Additionally, more efficient chip management systems and coolant recycling processes are minimizing waste and making machining operations more environmentally responsible.
Adoption of Collaborative Robots (Cobots) in CNC Lathes
Collaborative robots (cobots) are becoming more integrated into CNC lathe operations to assist with tasks such as loading and unloading parts, tool changing, and inspection. Unlike traditional industrial robots, cobots are designed to work alongside human operators safely, without the need for safety barriers or enclosures.
Cobots can be easily programmed and adapted to different tasks, making them a flexible solution for small and medium-sized manufacturers looking to automate their CNC lathes. The use of cobots improves efficiency, reduces labor costs, and enhances workplace safety by taking on repetitive or physically demanding tasks.
Expansion of AI-Driven Quality Inspection Systems
Quality control is a critical aspect of CNC lathe operations, and AI-driven quality inspection systems are revolutionizing the process. These systems use machine vision, sensors, and AI algorithms to detect defects, measure part dimensions, and verify surface finishes in real time.
AI-powered inspection systems can identify even the smallest defects and ensure that parts meet required specifications before they leave the production floor. This reduces scrap rates, ensures higher quality, and provides manufacturers with better control over their production processes.
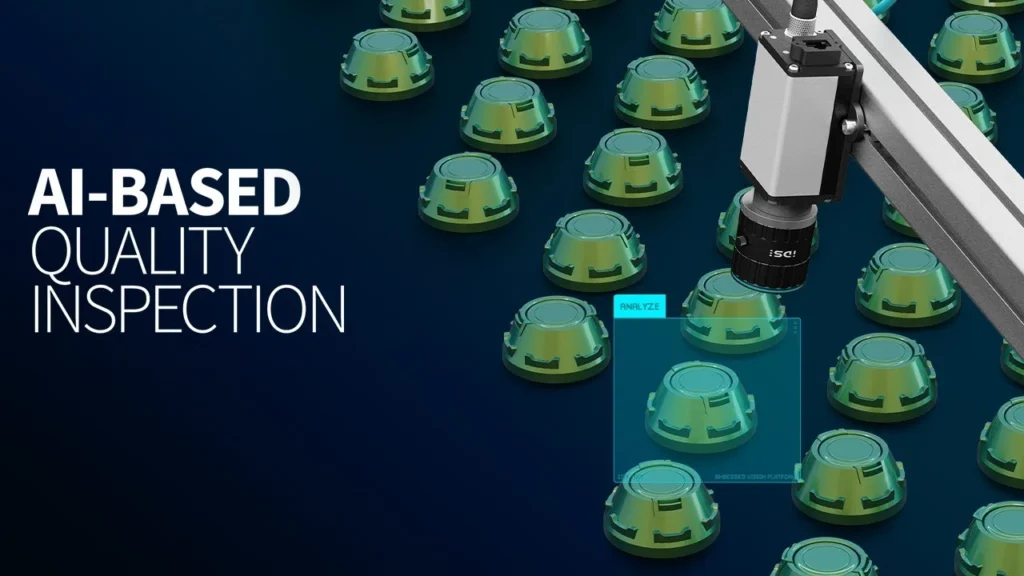
Conclusion: What is a CNC Lathe
In conclusion, a CNC lathe is a versatile, high-precision machine tool that plays a critical role in modern manufacturing. Through the use of advanced computer control systems, CNC lathes can automate turning, drilling, boring, threading, and even milling processes with incredible accuracy and repeatability. Their ability to produce high-quality parts with minimal human intervention has made them indispensable in industries ranging from aerospace and automotive to medical devices and electronics.
The future of CNC lathes looks bright, with innovations in automation, artificial intelligence, and multi-axis machining offering even greater levels of precision, efficiency, and versatility. From enhanced tool management systems to the integration of robotic assistance and predictive maintenance technologies, CNC lathes will continue to evolve and meet the growing demands of the manufacturing industry.
Choosing the right CNC lathe for your needs involves understanding your production requirements, considering machine specifications, and evaluating factors like automation capabilities, tool capacity, and after-sales support. With the right investment in a CNC lathe, manufacturers can achieve greater productivity, reduce costs, and enhance part quality, all while keeping pace with the rapid advancements in manufacturing technology.
At Rosnok, we offer a wide range of high-performance CNC lathes designed to meet the diverse needs of modern manufacturers. Backed by advanced engineering, rigorous quality control, and responsive after-sales support, Rosnok CNC lathes help you drive productivity and precision in every project.
FAQ: What is a CNC Lathe
Is a CNC lathe suitable for beginners?
Yes. Modern CNC lathes with user-friendly interfaces and conversational programming are suitable for beginners. However, basic knowledge of CNC operations, tooling, and safety is recommended before starting.
Can a CNC lathe perform milling operations?
Yes. Many advanced CNC lathes, especially CNC turning centers with live tooling, can perform milling operations along with standard turning. This allows for greater versatility and reduces the need for multiple machines.
What is the typical maintenance required for a CNC lathe?
Typical maintenance includes regular lubrication of moving parts, inspection and replacement of worn tools, cleaning of the coolant and chip removal system, checking spindle and axis alignment, and software updates. Preventive maintenance ensures optimal performance and reduces downtime.