Have you ever wondered how to achieve precise threads on a lathe? Are you unsure about which tools to use, how to set the machine up, or even where to start? Thread cutting on lathe might seem intimidating, especially for beginners, but with the right guidance, you can tackle it confidently. How can you avoid mistakes and achieve the perfect thread? Let’s break it down!
Thread cutting on a lathe is the process of using a single-point cutting tool to create threads by cutting into the surface of a rotating workpiece. The key to successful thread cutting is precisely controlling the feed rate and depth of cut to match the desired thread pitch. By setting the correct spindle speed and selecting the right cutting tool, you can achieve clean, accurate threads. Fine adjustments to the tool’s position and alignment ensure that the cutting edge follows the workpiece’s rotational axis, resulting in a smooth, precise thread profile.
Continue reading this guide to learn how to cut threads on a lathe, including the essential techniques, tool selection, and settings adjustments that ensure precision. We’ll also cover troubleshooting tips and how to avoid common mistakes in the threading process.
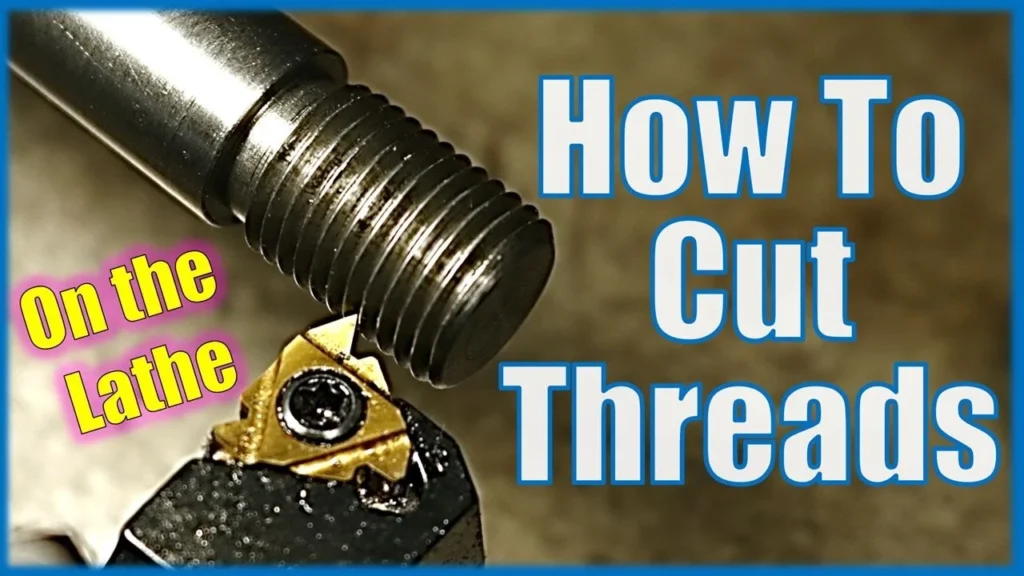
Understanding Thread Cutting on a Lathe
Thread cutting on a lathe is an essential skill for machinists, allowing them to create precision threads on a wide range of workpieces. Whether you’re working on small components, automotive parts, or larger industrial projects, thread cutting on a lathe ensures that your threads are perfectly shaped and ready for use in various applications.
What is Thread Cutting?
Thread cutting on lathe involves using a cutting tool to remove material from the surface of a rotating workpiece, forming a helical groove that serves as a thread. This process is crucial for creating threads on fasteners, screws, and other components that require a threaded connection. Whether you’re cutting a thread on a lathe manually or using a CNC lathe thread cutting machine, the goal remains the same: to create precise, accurate threads that fit perfectly with their mating parts.
How Thread Cutting on Lathe Works
The process of thread cutting on the lathe starts with securing the workpiece in the lathe chuck, followed by setting the correct lathe thread cutting parameters, including spindle speed and feed rate. As the lathe turns, the cutting tool moves along the axis of the workpiece, gradually removing material and forming a thread. The alignment of the tool and the workpiece is crucial, as even slight deviations can lead to inaccurate threads. Depending on the machine and the complexity of the task, machinists can use external thread cutting tools lathe to create threads on the outside of a workpiece or use different tooling for internal threading operations.
This process requires knowledge of the correct settings and tool usage to ensure clean, high-quality threads every time. Understanding how to set up your lathe machine for thread cutting and making necessary adjustments are vital for a successful result.
Choosing the Right Lathe for Thread Cutting
Selecting the right lathe is crucial for achieving clean and precise threads. The type of lathe you choose will determine the capabilities and limitations of your thread cutting operation. Whether you’re working on small parts, large-scale production, or specific thread types, choosing the right lathe ensures that you can achieve the desired results efficiently.
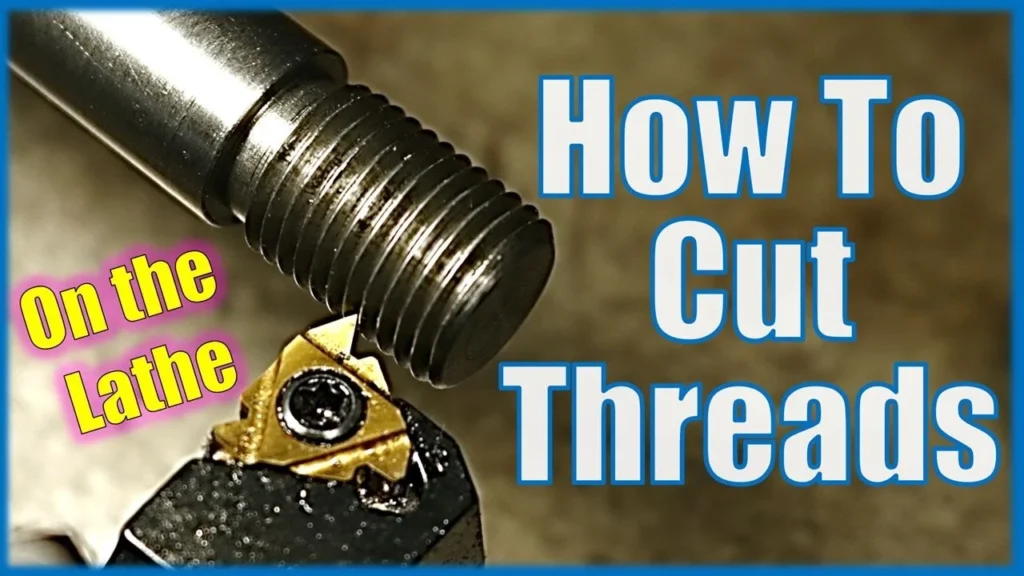
Types of Lathes Used for Thread Cutting
When it comes to thread cutting on lathe, there are several types of lathes available, each suited for different applications. CNC lathe thread cutting is ideal for high-precision, automated threading tasks, making it perfect for industries where repeatability and accuracy are key. These machines can be programmed to cut a variety of thread types and sizes with minimal operator intervention.
For those working with simpler projects or manual operations, a manual lathe or metal lathe is often preferred. While it requires more skill and attention from the operator, it offers greater flexibility for small to medium-sized projects. How to thread on a manual lathe involves precise manual control, allowing you to cut threads according to the exact specifications you need. For specialized applications, such as pipe threads, a pipe-threading lathe is a popular choice, designed to handle larger diameters and specific thread forms, especially in industries like petrochemical or construction.
Key Features to Look for in a Lathe
When selecting a lathe for thread cutting operation on lathe machine, there are several key features to consider:
- Rigidity and Stability: A rigid and stable machine will prevent vibrations and ensure that the tool maintains accurate contact with the workpiece, leading to smooth threads.
- Feed Mechanism: The lathe should have a reliable feed system that allows for precise control over the tool’s movement along the workpiece’s axis, critical for consistent thread pitch.
- Spindle Speed: Different materials require different spindle speeds for effective thread cutting. A lathe with adjustable speed settings allows you to match the speed to the material, ensuring clean cuts and preventing tool wear.
- Tool Post and Alignment: The lathe should have an easily adjustable tool post that allows for proper alignment of the cutting tool. Proper alignment is essential for accurate threading, especially when dealing with complex thread profiles.
Choosing the right lathe ensures that your thread cutting on lathe machine operations are efficient and produce high-quality results. Whether you’re cutting external thread cutting on lathe or performing more advanced operations, selecting the right machine is the first step to success.
Choosing the Right Lathe for Thread Cutting
Selecting the right lathe is crucial for achieving clean and precise threads, whether you’re cutting external or internal threads. The type of lathe you choose will determine the capabilities and limitations of your thread cutting operation. Whether you’re working on small parts, large-scale production, or specific thread types, choosing the right lathe ensures that you can achieve the desired results efficiently.
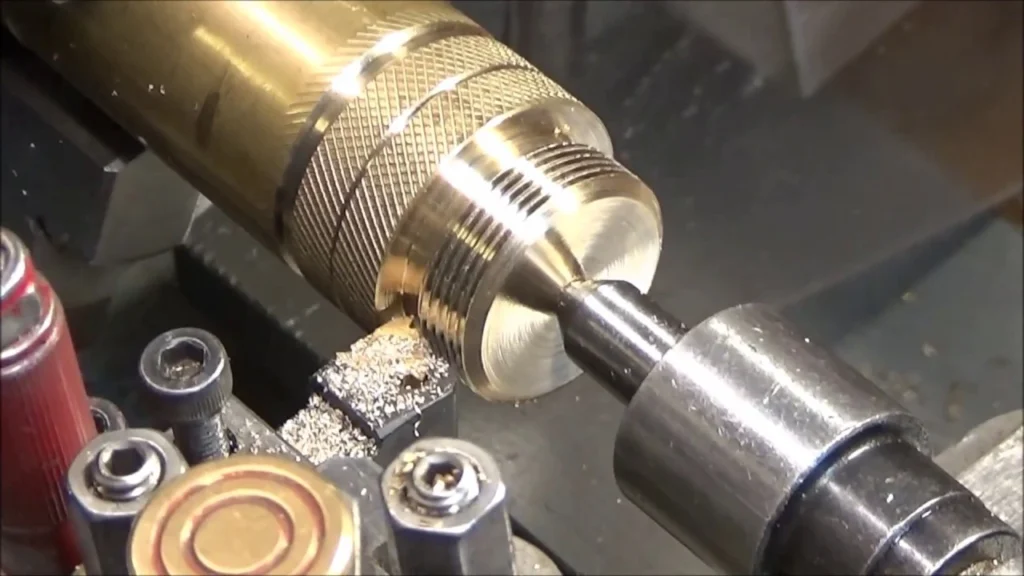
Types of Lathes Used for Thread Cutting
When it comes to thread cutting on lathe, there are several types of lathes available, each suited for different applications. CNC lathe thread cutting is ideal for high-precision, automated threading tasks, making it perfect for industries where repeatability and accuracy are key. These machines can be programmed to cut a variety of thread types and sizes with minimal operator intervention.
For those working with simpler projects or manual operations, a manual lathe or metal lathe is often preferred. While it requires more skill and attention from the operator, it offers greater flexibility for small to medium-sized projects. How to thread on a manual lathe involves precise manual control, allowing you to cut threads according to the exact specifications you need. For specialized applications, such as pipe threads or external thread cutting on lathe, a pipe-threading lathe is a popular choice, designed to handle larger diameters and specific thread forms, especially in industries like petrochemical or construction.
For internal thread cutting on lathe, specialized tools such as taps or dedicated internal threading tools are used. These tools are designed to fit into the hole of the workpiece, cutting the threads inside, which is essential for creating threaded holes or internal features in parts.
Key Features to Look for in a Lathe
When selecting a lathe for thread cutting operation on lathe machine, there are several key features to consider:
- Rigidity and Stability: A rigid and stable machine will prevent vibrations and ensure that the tool maintains accurate contact with the workpiece, leading to smooth threads.
- Feed Mechanism: The lathe should have a reliable feed system that allows for precise control over the tool’s movement along the workpiece’s axis, critical for consistent thread pitch.
- Spindle Speed: Different materials require different spindle speeds for effective thread cutting. A lathe with adjustable speed settings allows you to match the speed to the material, ensuring clean cuts and preventing tool wear.
- Tool Post and Alignment: The lathe should have an easily adjustable tool post that allows for proper alignment of the cutting tool. Proper alignment is essential for accurate threading, especially when dealing with complex thread profiles, including internal thread cutting on lathe.
Choosing the right lathe ensures that your thread cutting on lathe machine operations are efficient and produce high-quality results. Whether you’re cutting external thread cutting on lathe or performing more advanced internal threading operations, selecting the right machine is the first step to success.
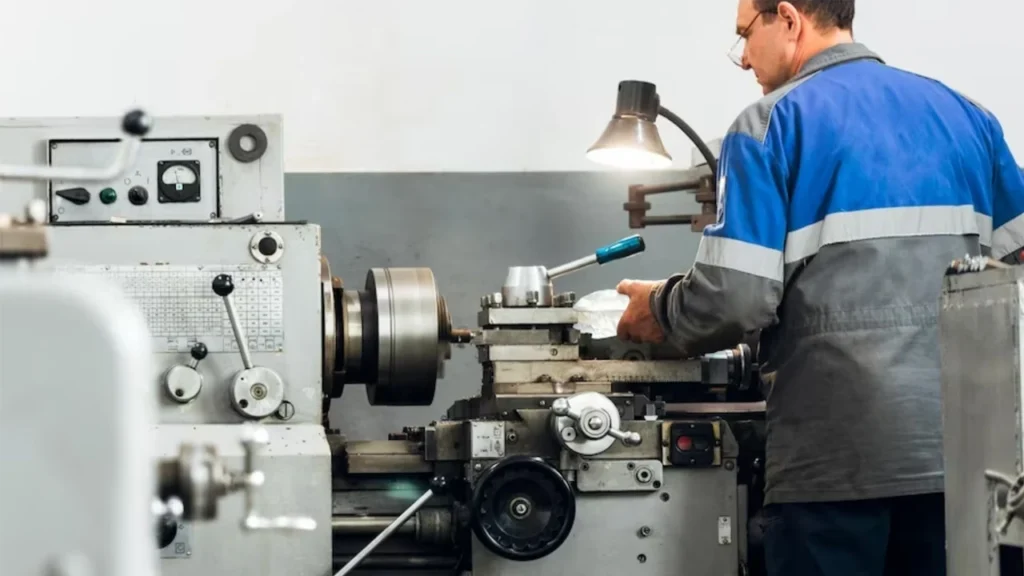
Tools Required for Thread Cutting
Choosing the right tools for thread cutting on lathe is essential for ensuring precision and achieving high-quality threads. From cutting tools to measuring instruments, selecting the correct tool will help you perform the job accurately and efficiently, whether you are cutting external thread cutting on lathe or internal thread cutting. This section will explore the tools you’ll need and how to select them based on your project requirements.
Types of Cutting Tools
When it comes to lathe thread cutting, there are several types of cutting tools available. The most common tool used for both external thread cutting on lathe and internal thread cutting is the single-point cutting tool. This tool is versatile and is typically used for cutting external threads, but it can also be adapted for internal thread cutting on lathe by using specially designed inserts or tools.
In addition to single-point tools, you may also encounter thread cutting inserts. These inserts are often made from materials like carbide or high-speed steel and are used in CNC lathe thread cutting for high-efficiency operations. They are easily replaceable, which makes them cost-effective for high-production runs. Thread cutting inserts are ideal for both internal and external threads, providing longer tool life and better resistance to wear.
For internal thread cutting on lathe, you will need tools specifically designed to fit inside a workpiece. These tools include taps, which are commonly used for cutting threads inside holes. Taps are available in various sizes and types, such as spiral point taps for through-holes and spiral flute taps for blind holes.
Choosing the Right Tool for the Job
Selecting the right tool for cutting a thread on lathe depends on several factors, such as the type of thread you need to create and the material of the workpiece. For manual lathe thread cutting, a high-speed steel (HSS) tool is a common choice, especially for softer materials. However, for harder materials like stainless steel or high-carbon steel, carbide-tipped tools are recommended for their durability and ability to withstand higher cutting speeds.
For external thread cutting tools lathe, the tool’s geometry is crucial for cutting threads accurately. You must ensure that the tool’s angle, relief, and rake are correctly adjusted for the desired thread profile. Similarly, for internal thread cutting on lathe, the tool must be carefully selected to match the internal diameter and thread depth required. The use of taps or specially designed cutting tools for internal threads is critical for ensuring the thread’s accuracy and surface finish.
To achieve the best results, it’s essential to select the right tool not only based on the material being machined but also based on the machine you’re using. While CNC lathe thread cutting can often automate some of these processes, manual lathes require more precise attention to the setup and tool choice to avoid mistakes.
Setting Up the Lathe for Thread Cutting
Properly setting up your lathe is crucial for achieving high-quality, precise threads. Whether you’re cutting external thread cutting on lathe or internal thread cutting, your setup will directly affect the accuracy and finish of the threads. In this section, we will walk you through the key steps in setting up your lathe to ensure that your thread cutting operation goes smoothly.
Adjusting Lathe Speed and Feed Rate
When performing thread cutting on lathe, adjusting the spindle speed and feed rate is crucial to achieving the desired thread pitch and surface finish. The correct spindle speed will depend on the material you’re cutting and the type of thread you’re creating. For example, cutting softer materials like aluminum may require a higher spindle speed, while harder materials like steel or stainless steel will require slower speeds to prevent tool wear and overheating.
In addition to spindle speed, the feed rate is equally important. The feed rate determines how fast the cutting tool moves along the workpiece and influences the thread pitch. A slower feed rate results in a finer thread, while a faster feed rate produces a coarser thread. It’s essential to match the feed rate with the correct spindle speed to ensure that the thread’s dimensions are accurate.
When setting up for internal thread cutting on lathe, the feed rate becomes even more critical. Since the tool is cutting inside the hole, it requires more precise control to prevent tool chatter and ensure the threads are uniform. The feed mechanism on the lathe must be adjusted accordingly, whether using manual lathe thread cutting or CNC lathe thread cutting.
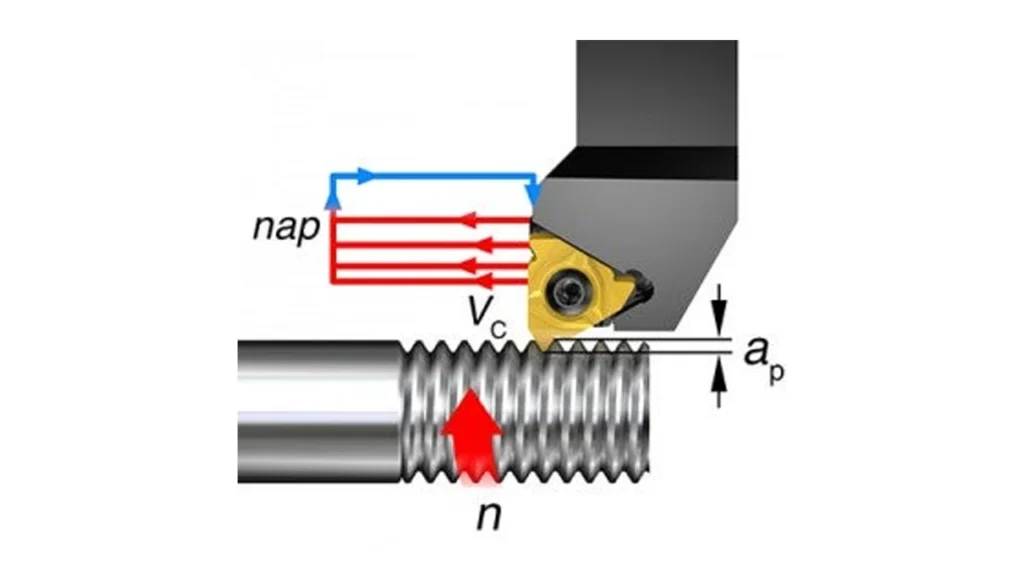
Proper Tool Alignment
Ensuring that your cutting tool is properly aligned is critical for lathe thread cutting. Any misalignment between the tool and the workpiece will result in inaccurate threads, such as uneven pitch or incorrect thread depth. To achieve proper alignment, start by positioning the cutting tool at the correct height and angle relative to the workpiece.
For external thread cutting on lathe, the tool must be set at the correct angle to match the desired thread profile. Additionally, for internal thread cutting, the tool must be positioned so it can fit inside the workpiece, ensuring that it cuts along the correct axis. Most modern lathes have adjustable tool posts that allow for easy alignment, but it’s still important to double-check the alignment before starting the cutting process.
If you’re using a CNC lathe thread cutting system, the machine’s software will help guide the tool alignment, but manual adjustments might still be needed based on the tool and workpiece being used. For how to thread on a manual lathe, the operator must make these adjustments by hand, ensuring that the tool is centered and aligned properly before beginning the cut.
Step-by-Step Guide to Cutting Threads on a Lathe
Once your lathe is properly set up, it’s time to begin the process of thread cutting on lathe. This section will provide a detailed, step-by-step guide on how to cut threads, whether you’re performing external thread cutting on lathe or internal thread cutting. Following these steps will ensure that you achieve precise and consistent threads on your workpieces.
Preparing the Workpiece
Before starting the thread cutting operation on lathe machine, you need to securely mount the workpiece onto the lathe. For external thread cutting on lathe, the workpiece is usually mounted in a three-jaw chuck, which ensures that it is firmly held and rotates evenly. For internal thread cutting on lathe, you’ll need to use the correct internal clamping method or a collet to secure the workpiece, ensuring that the internal diameter remains stable during the cut.
It’s essential to check that the workpiece is centered properly on the lathe. Any misalignment can lead to uneven threads, poor finish, or even tool damage. Use a dial indicator to check the alignment before proceeding.
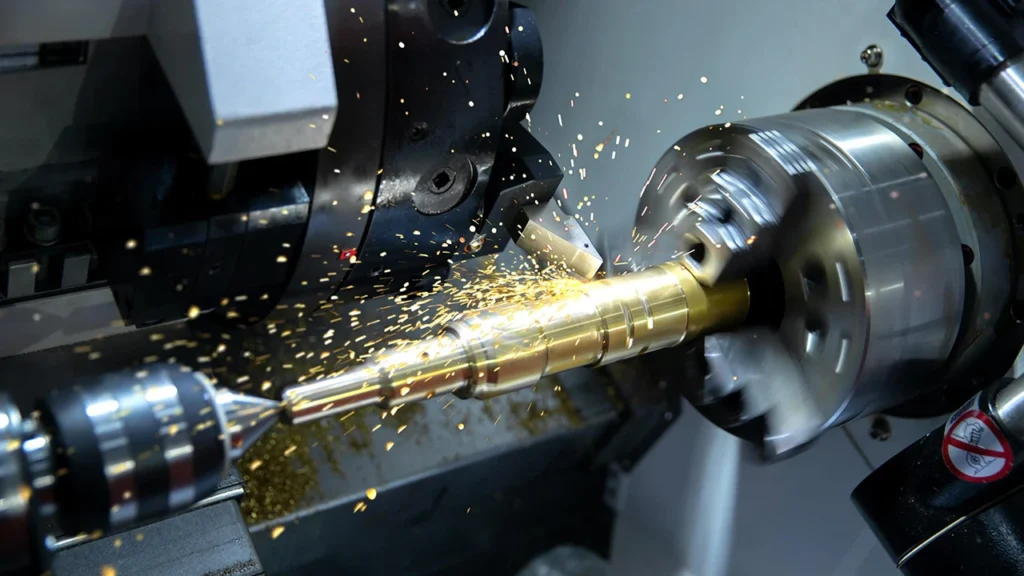
Cutting the Thread
Now that the workpiece is securely mounted, it’s time to begin cutting the thread. Start by engaging the cutting tool gently into the material. For external thread cutting on lathe, this is done by bringing the cutting tool into contact with the rotating workpiece and adjusting the feed rate. The cutting tool should be positioned at the correct angle, depending on the thread profile you’re creating.
For internal thread cutting on lathe, ensure that the tool is positioned correctly inside the hole and follows the correct axis. Start with a light cut to create a groove before deepening the thread. Gradually increase the depth of the cut with each pass to prevent overloading the tool and ensure that the threads are smooth and even.
Throughout the process, regularly check the thread depth and pitch to make sure they are consistent. Depending on the machine you’re using, the depth of the thread can be controlled through the feed settings or manually by adjusting the cutting tool’s position.
Checking Thread Accuracy
After completing the cutting process, it’s essential to check the accuracy of the threads. For external thread cutting on lathe, you can use a thread gauge or micrometer to measure the thread pitch, diameter, and depth. For internal thread cutting, use a caliper to check the internal diameter and ensure the threads are consistent.
It’s a good idea to perform a test fit of the threaded workpiece with a mating part to verify that the threads mesh properly. If you find any issues with the thread fit, it may be necessary to make minor adjustments to the feed rate or tool position and retest the fit.
By following this step-by-step guide, you can successfully perform thread cutting on lathe, whether you’re working on external thread cutting or internal thread cutting. Proper setup, cutting techniques, and careful checking are key to achieving high-quality threads that meet your specifications.
Common Problems and How to Avoid Them
Even with the best setup, thread cutting on lathe can present challenges. Whether you’re cutting external thread cutting on lathe or internal thread cutting, problems like inconsistent thread pitch, tool wear, and workpiece vibration can impact the quality of your threads. In this section, we’ll address some of the most common issues encountered during thread cutting and provide solutions to help you avoid them.
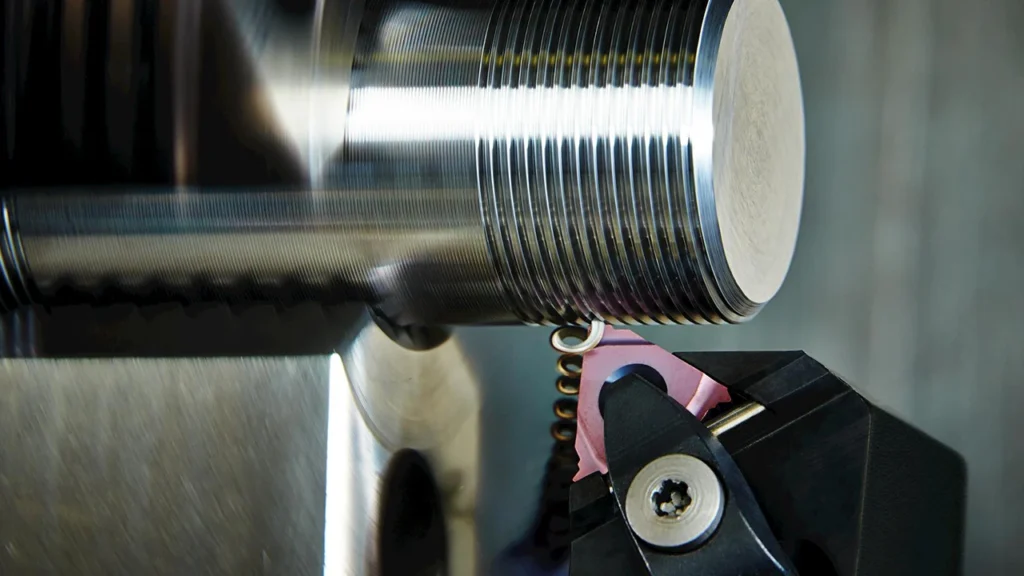
Inconsistent Thread Pitch
One of the most common problems in lathe thread cutting is inconsistent thread pitch. This occurs when the spacing between the threads is uneven, leading to misalignment with mating parts. Several factors can cause this issue:
- Incorrect feed rate: If the feed rate is too fast or too slow, the thread pitch will vary.
- Tool wear: A dull or worn cutting tool can produce inconsistent cuts, affecting the thread pitch.
How to avoid this problem: To ensure consistent thread pitch, double-check the feed rate settings before starting. For external thread cutting on lathe, ensure the tool is sharp and in good condition. If you notice any uneven pitch, stop the machine, check the tool, and adjust the feed rate or spindle speed as needed.
Tool Wear and Breakage
Tool wear is a natural part of the thread cutting process, but if left unaddressed, it can lead to poor thread quality and even tool breakage. Carbide-tipped tools are typically more resistant to wear than high-speed steel (HSS) tools, but both require proper maintenance and care.
How to avoid this problem: Regularly inspect your cutting tools for signs of wear or damage. For CNC lathe thread cutting, the machine may alert you when tool wear reaches a certain threshold, but for manual lathes, you’ll need to check the tool’s condition frequently. Additionally, ensure that you’re using the correct cutting speed and feed rate to minimize tool wear. If you notice the tool becoming dull, replace it or resharpen it before continuing with the job.
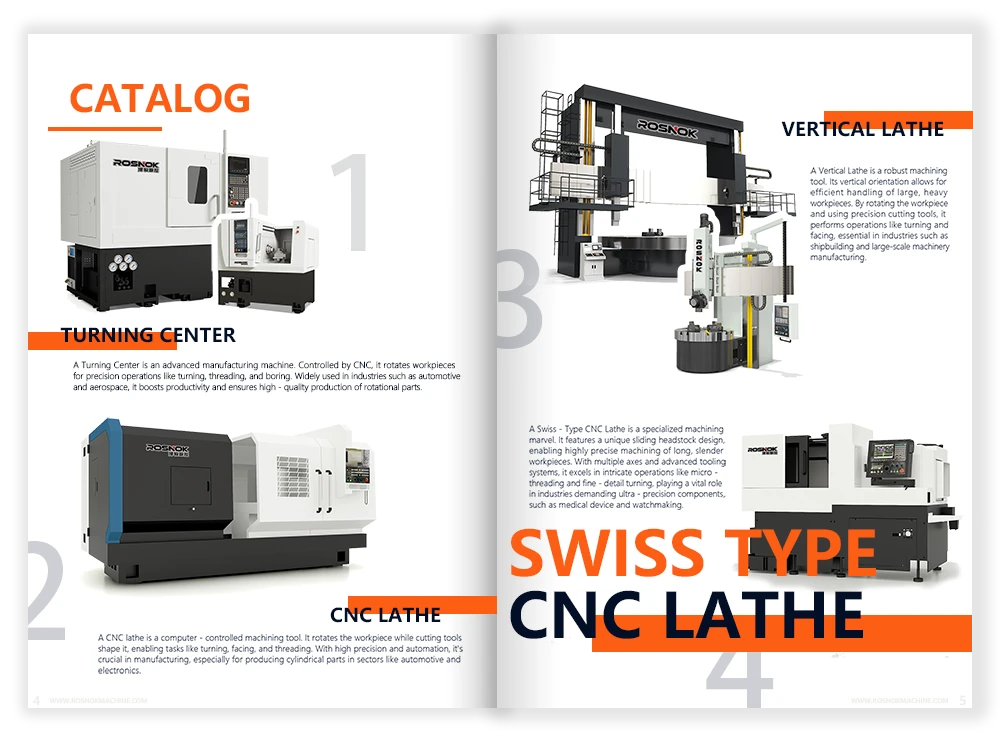
Workpiece Vibration and Misalignment
Workpiece vibration and misalignment can lead to inaccurate threads, poor surface finish, and potential tool damage. Vibration is particularly problematic during internal thread cutting on lathe, as the workpiece is typically held by a collet or chuck, which may not provide as much stability as a larger part.
How to avoid this problem: To prevent vibration, make sure the workpiece is securely clamped, whether you’re working on external thread cutting on lathe or internal thread cutting. If vibration persists, you can reduce the cutting speed or adjust the feed rate to lessen the load on the tool. Additionally, consider using a steady rest to support the workpiece, particularly for longer components, which helps reduce vibration and ensures stability during cutting.
By being mindful of these common issues and following best practices, you can prevent problems from arising during your thread cutting on lathe operations, ensuring that you achieve clean, precise threads every time.
Tips and Best Practices for Precision Thread Cutting
Achieving precision in thread cutting on lathe requires more than just the right tools and settings; it also demands a good understanding of best practices and techniques that ensure accuracy and consistency. Whether you’re cutting external thread cutting on lathe or internal thread cutting, following these tips will help you improve the quality of your threads and enhance your lathe skills.
Using Coolant Effectively
Coolant is a crucial factor in improving both the quality of the thread and the lifespan of your cutting tools during lathe thread cutting. The main function of coolant is to reduce friction between the cutting tool and the workpiece, which helps prevent overheating, minimizes tool wear, and improves the surface finish of the threads.
How to apply coolant: When cutting external thread cutting on lathe or internal thread cutting, apply the coolant directly to the cutting area. This will help to remove heat and debris, ensuring smooth cutting. For CNC lathe thread cutting, automatic coolant systems often help control the flow and distribution, but on manual lathes, you should apply coolant intermittently as needed. Ensure that the coolant is appropriate for the material you are working with, as different materials require different cooling methods.
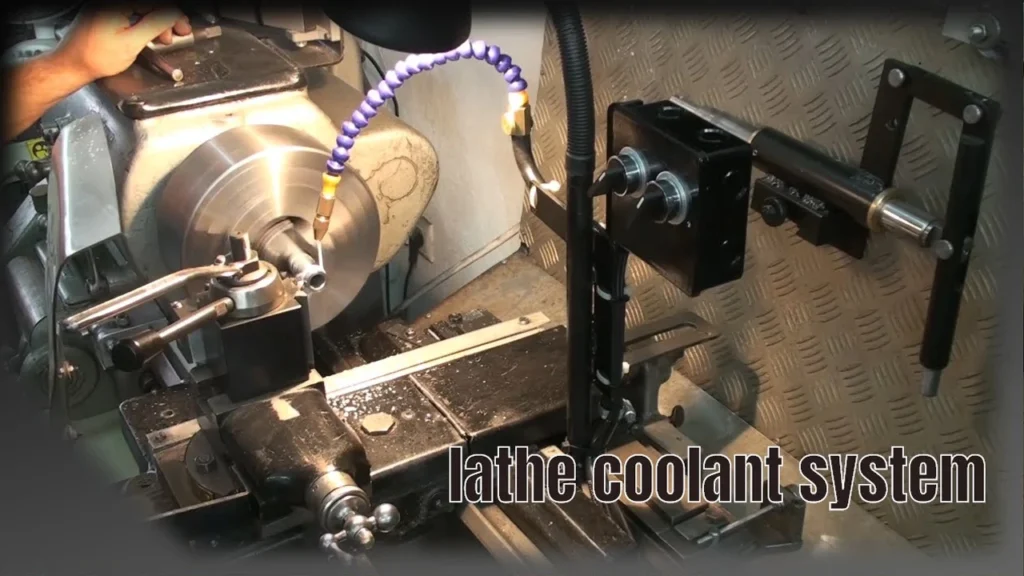
Practice and Patience
Thread cutting on a lathe is a skill that improves with practice. As with any machining process, developing proficiency in cutting a thread on lathe takes time and attention to detail. How to thread on a manual lathe or how to thread on a metal lathe may initially seem challenging, but with repeated practice, your ability to make adjustments and fine-tune settings will improve, leading to better results over time.
Why practice matters: Practice helps you understand how different materials behave when being cut, how to adjust the feed rate and speed for optimal results, and how to recognize signs of tool wear. Patience is essential—take your time to make minor adjustments throughout the threading process. By continually refining your technique, you’ll gain more confidence and control over your lathe operations.
Regular Tool Maintenance
To achieve consistent and high-quality threads, you must maintain your cutting tools properly. Worn-out or damaged tools can result in inaccurate threads, poor surface finish, and even damage to the workpiece. Thread cutting tools, such as external thread cutting tools lathe or internal thread cutting tools, should be regularly inspected for wear and properly sharpened when necessary.
Tool care: Regularly check for any chips or damage on your tools, and replace or resharpen them as needed. For CNC lathe thread cutting, monitor tool wear through the machine’s diagnostic tools. For manual lathes, it’s important to manually inspect the tools frequently, especially when working with hard materials. Keeping your tools in top condition ensures that you consistently achieve the best thread quality.
Maintenance and Care for Your Lathe After Thread Cutting
After completing a thread cutting operation, whether it’s external thread cutting on lathe or internal thread cutting, it’s important to properly maintain and care for your lathe. Regular maintenance ensures that your machine continues to function smoothly, helps preserve its lifespan, and keeps it ready for the next project. This section will guide you through the essential post-operation care for your lathe to maintain its accuracy and performance.
Inspecting and Cleaning the Lathe
Once you’ve finished thread cutting on lathe machine, it’s crucial to remove any metal chips, debris, and coolant residues that have accumulated during the operation. These materials can cause corrosion or affect the smooth movement of the machine’s components.
How to clean your lathe: Start by wiping down all accessible surfaces with a cloth to remove excess coolant or dirt. For areas like the tool post, carriage, and the chuck, make sure there’s no buildup of debris. Use compressed air to clean hard-to-reach areas, such as the internal components of the spindle and the feed mechanism, to prevent any material buildup that might cause operational issues. Keeping the lathe clean is a simple but important step to prolong the machine’s lifespan.
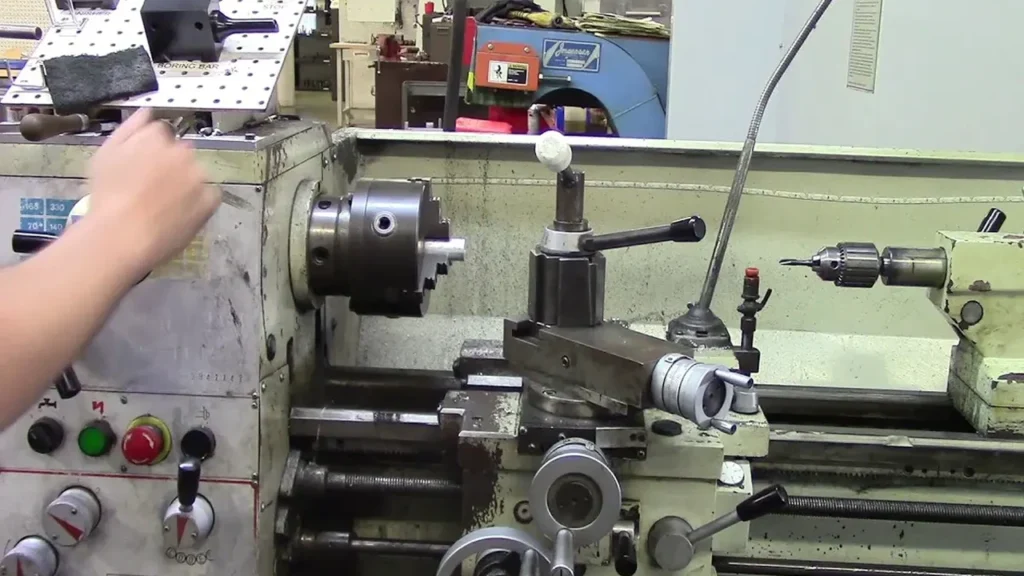
Lubrication of Moving Parts
Regular lubrication is key to preventing wear and tear on your lathe, particularly after a thread cutting operation on lathe machine. Lubricating moving parts reduces friction, ensures smooth operation, and helps maintain thread cutting precision over time.
How to lubricate your lathe: Lubricate all the key moving parts of the lathe, such as the carriage, cross slide, and tailstock, using the appropriate oils and greases. For manual lathes, you’ll need to apply lubricant to the lead screws, spindle bearings, and other high-friction areas. On CNC lathe thread cutting systems, ensure that the automatic lubrication system is functioning correctly, but also do a manual check to ensure all components are properly lubricated. Regular lubrication reduces the chances of premature wear and helps maintain the precision needed for thread cutting operations.
Checking for Tool and Part Wear
Regularly inspect critical parts of your lathe for signs of wear and tear. Over time, components like the tool post, chuck, and lead screws may experience gradual wear, especially after performing heavy operations like thread cutting on lathe. Worn-out parts can affect the accuracy and smooth operation of your lathe.
How to check and replace worn parts: Periodically inspect the chuck for any wear on the jaws or irregularities. Check the lead screws for any play or misalignment, and ensure the tool post is secure. If parts show significant signs of wear or damage, replace them promptly to prevent further issues. Keeping a detailed maintenance schedule will help you catch these problems early, ensuring your lathe continues to perform accurately during future thread cutting tasks.
Safety Precautions During Thread Cutting on Lathe
Thread cutting on a lathe, whether it’s external thread cutting on lathe or internal thread cutting, is a precise operation that requires attention to safety. Working with lathes involves spinning heavy workpieces at high speeds, and improper handling can lead to accidents or injuries. This section covers the essential safety precautions to follow during lathe thread cutting to protect yourself and others in the workshop.
Wear Protective Gear
When performing thread cutting on lathe machine, it’s important to wear the appropriate protective gear to minimize the risk of injury. This includes safety glasses to protect your eyes from flying debris, ear protection to shield your hearing from the loud noise generated by the machine, and sturdy gloves to safeguard your hands from sharp edges or small parts.
How to wear protective gear: Make sure that your gloves fit snugly and do not get caught in moving parts. Choose gloves made of materials that provide protection without sacrificing dexterity. For CNC lathe thread cutting, it’s equally important to ensure that loose clothing or jewelry is removed, as these could get caught in the machine’s moving parts.
Ensure Proper Machine Setup
Before starting any thread cutting operation on lathe machine, always double-check the lathe’s setup to ensure everything is in place. This includes making sure the cutting tool is securely fastened, the workpiece is properly clamped, and the lathe’s safety features, such as emergency stops and safety guards, are functioning correctly.
How to check the setup: Verify that the workpiece is tightly secured in the chuck and properly aligned. Check the tool alignment to make sure it is set at the correct angle and is sharp. If using a manual lathe, always verify the feed settings and make sure there are no obstructions in the lathe’s path. Ensuring everything is properly set before starting minimizes the risk of machine malfunction or accidents.
Maintain a Clean Workspace
A clean and organized workspace is essential when performing thread cutting on lathe. Spilled oil, coolant, or metal chips can create slip hazards and make it difficult to handle the machine safely. Keeping the workspace clean not only helps maintain safety but also improves your efficiency during the operation.
How to maintain a clean workspace: Regularly clean up metal shavings and debris around the lathe, especially after each threading job. Ensure that coolant or oil is properly contained and doesn’t spill onto the floor. Clean tools and components before and after each use, as well as the machine bed, to prevent any buildup that might lead to accidents.
Stay Alert and Focused
Thread cutting, particularly when performing internal thread cutting on lathe, requires complete focus. Distractions can lead to mistakes, which could result in tool damage or even personal injury. Ensure that you remain alert and focused throughout the operation.
How to stay alert: Avoid operating the lathe if you’re tired, distracted, or rushed. Always follow proper procedures and take breaks when necessary to maintain your focus. If you’re new to how to thread on a manual lathe or how to thread on lathe, consider starting with simpler tasks to build your confidence before attempting more complex threading operations.
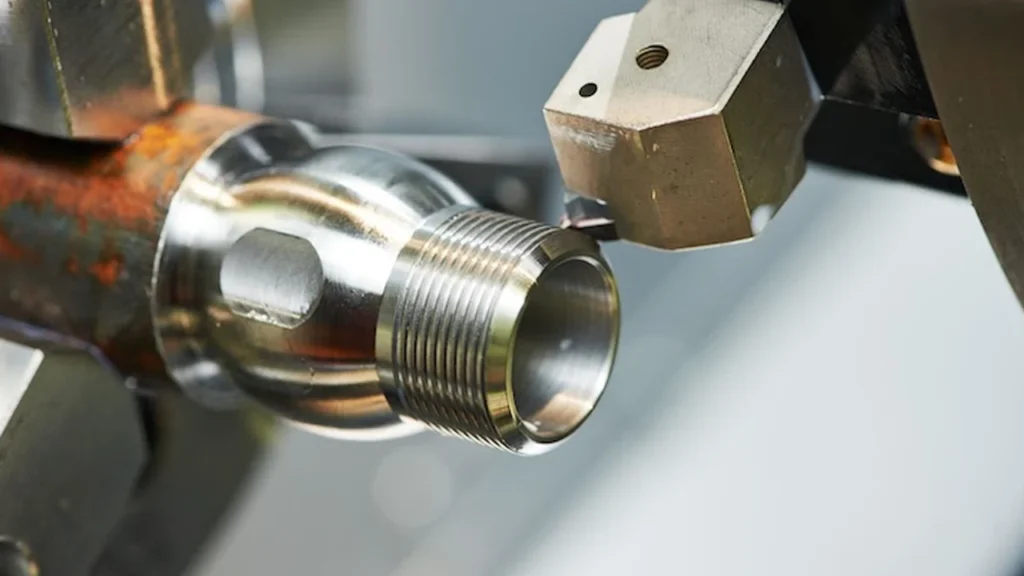
Conclusion and Further Resources for Beginners
Mastering thread cutting on lathe is an essential skill for any machinist. Whether you’re performing external thread cutting on lathe or internal thread cutting, the process requires precision, attention to detail, and a solid understanding of your tools and setup. By following the steps outlined in this guide and practicing regularly, you can produce high-quality threads that meet your specifications and improve the overall quality of your machining projects.
Recap of Key Points
Throughout this guide, we’ve covered the critical aspects of lathe thread cutting, including choosing the right lathe, selecting appropriate tools, setting up your machine, and maintaining safety throughout the process. We’ve also provided tips on troubleshooting common problems and offered best practices for achieving precision in your thread cutting operations. Whether you are just getting started with how to thread on lathe or are looking to refine your skills, these guidelines will help you avoid mistakes and achieve optimal results.
Further Resources for Learning More
If you’re eager to continue learning and mastering thread cutting on lathe, there are many resources available to deepen your knowledge. Consider exploring the following:
- Online Forums and Communities: Join machining communities to ask questions, share experiences, and learn from others in the field.
- Books and Guides: There are numerous books on lathe operations and threading techniques that provide in-depth explanations and practical tips.
- Workshops and Courses: Consider enrolling in a hands-on machining course or workshop to gain more experience and guidance from professionals.
- Manufacturer Resources: Many lathe manufacturers offer tutorials, videos, and manuals that are specific to their machines, helping you understand their features and settings in detail.
By continuing to learn and practice, you’ll be able to take your thread cutting on lathe skills to the next level, whether you’re working with a CNC lathe thread cutting machine or a manual lathe. Remember, machining is as much about patience and practice as it is about technical know-how, so keep honing your skills and stay curious.