Have you ever wondered which parts of a lathe are the most important? Do you know how these essential parts contribute to the smooth and efficient operation of a lathe? Have you considered how these vital components work together to produce flawless results?
A lathe consists of several essential parts that work together to ensure precision and efficiency. The bed provides a solid foundation, maintaining alignment and stability. The headstock houses the spindle and motor, providing rotational power. The tailstock supports the end of the workpiece, ensuring accuracy. The tool post holds the cutting tool securely and allows for precise positioning and angle adjustments during machining. The guideways guide the movement of the carriage smoothly and accurately. Mastering the functions of these components allows you to produce flawless, high-quality machining results efficiently.
By the end of this guide, you’ll have a thorough understanding of the key parts of a lathe and how mastering their functions can enhance your machining precision and operational efficiency.
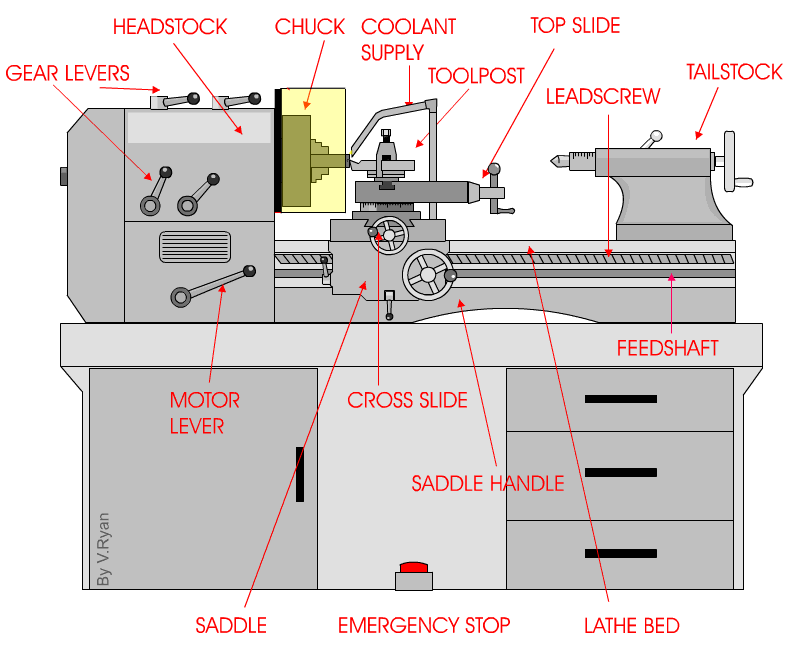
Main Parts of a Lathe Machine and Their Functions
A lathe is a powerful machining tool that consists of several essential parts of a lathe, each contributing to the production of precision-engineered components. Understanding these lathe parts and their specific functions is crucial for achieving consistent, high-quality machining results. Whether you’re operating a manual lathe or a CNC system, knowing the key parts of a lathe machine ensures smoother operations and increased efficiency. Below is a comprehensive overview of the primary parts of a lathe and their respective roles in ensuring optimal performance.
Lathe Bed
Key Parts of a Lathe: The bed is the base and the most fundamental part of a lathe. It provides a solid foundation to support the entire machine and maintains alignment between the headstock and tailstock.
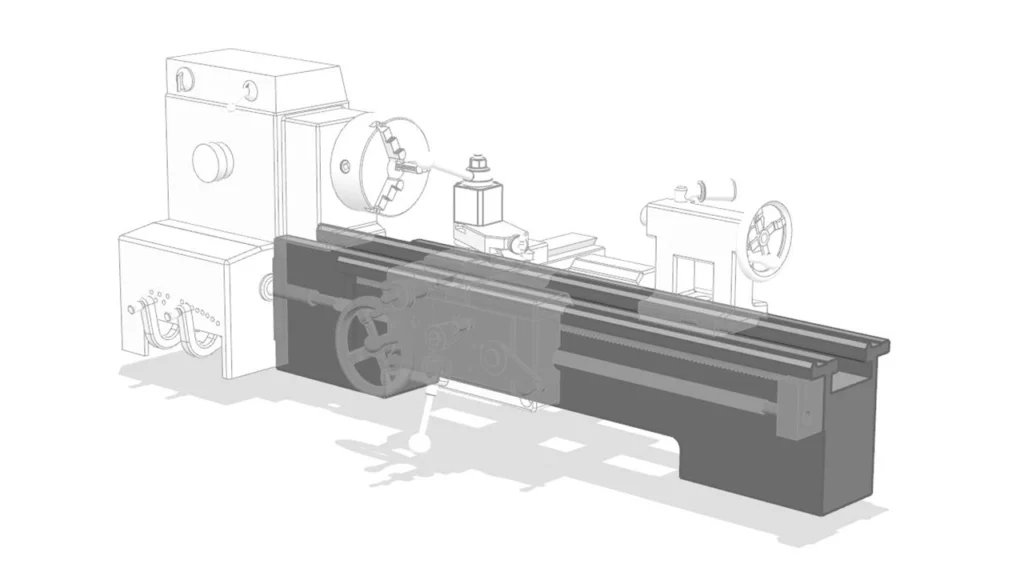
Material and Hardness
The bed is typically made from high-grade cast iron (FC25 or higher), which is chosen for its exceptional vibration-dampening properties and high tensile strength. Cast iron used for lathe beds usually has a hardness range of 180-220 HB (Brinell Hardness Number), ensuring durability and wear resistance over extended use.
Technical Features
- Precision Machined Guideways: The guideways on the bed are precisely ground to ensure the accurate movement of the carriage and tailstock.
- High Rigidity: The thick cross-section of the bed enhances rigidity, preventing deformation during heavy-duty operations.
- Anti-Vibration Design: The inherent damping properties of cast iron minimize vibration and maintain machining accuracy.
Functions of the Bed
- Supports the headstock, tailstock, and carriage.
- Ensures accurate alignment of other components.
- Minimizes vibration for consistent cutting performance.
Maintenance Tips
- Regularly clean the guideways to prevent debris buildup.
- Apply high-quality lubricants to prevent rust and ensure smooth carriage movement.
- Periodically inspect for signs of wear on the bed surface.
Headstock
Key Parts of a Lathe: The headstock is located at the left end of the lathe bed and houses the spindle, motor, and gear system. It provides rotational power to the workpiece by driving the spindle, which holds the workpiece in place.
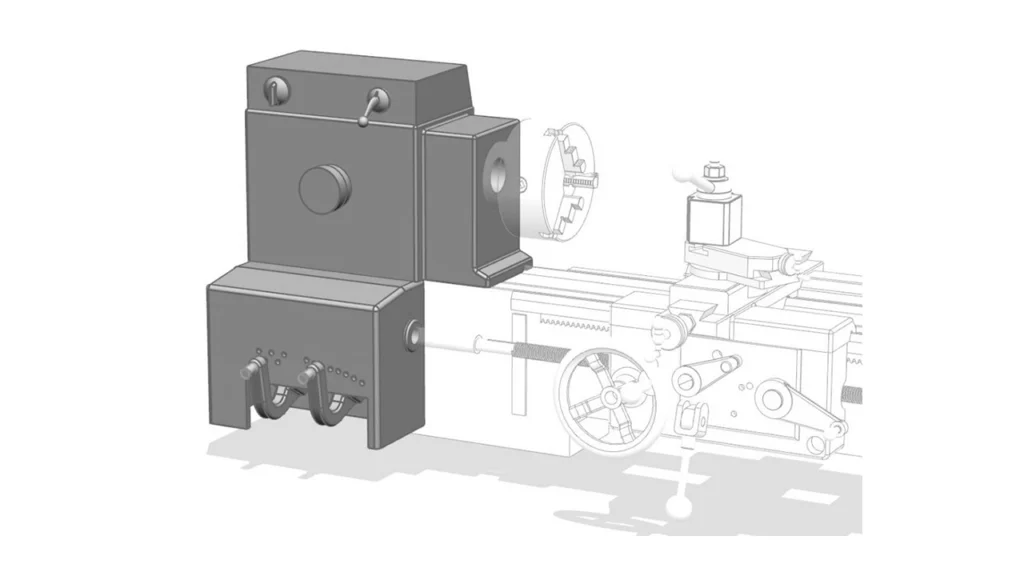
Material and Construction
The headstock is often made of hardened steel or cast iron, ensuring high strength and durability. The spindle is typically crafted from alloy steel (such as 40Cr or 42CrMo), providing excellent toughness and fatigue resistance. The spindle bearings are usually angular contact ball bearings or tapered roller bearings to ensure high-speed stability and accuracy.
Technical Features
- Spindle Speed Range: Modern lathes offer variable spindle speeds ranging from 50 RPM to 3000 RPM, depending on the machining requirements.
- Gear Train Mechanism: Enables precise control of spindle speed and torque output.
- Accuracy and Runout: High-precision lathes maintain a spindle runout tolerance within 0.01 mm (10 microns) to ensure cutting accuracy.
Functions of the Headstock
- Rotates the workpiece at varying speeds.
- Houses gears and controls that regulate spindle speed.
- Enables threading, facing, and turning operations.
Maintenance Tips
- Lubricate spindle bearings periodically to reduce friction and prevent overheating.
- Monitor spindle runout to ensure consistent machining accuracy.
- Check the gear system for wear and replace damaged gears promptly.
Tailstock
Key Parts of a Lathe: The tailstock is positioned on the opposite end of the headstock and is used to support the free end of the workpiece. It can be adjusted along the lathe bed to accommodate different workpiece lengths.
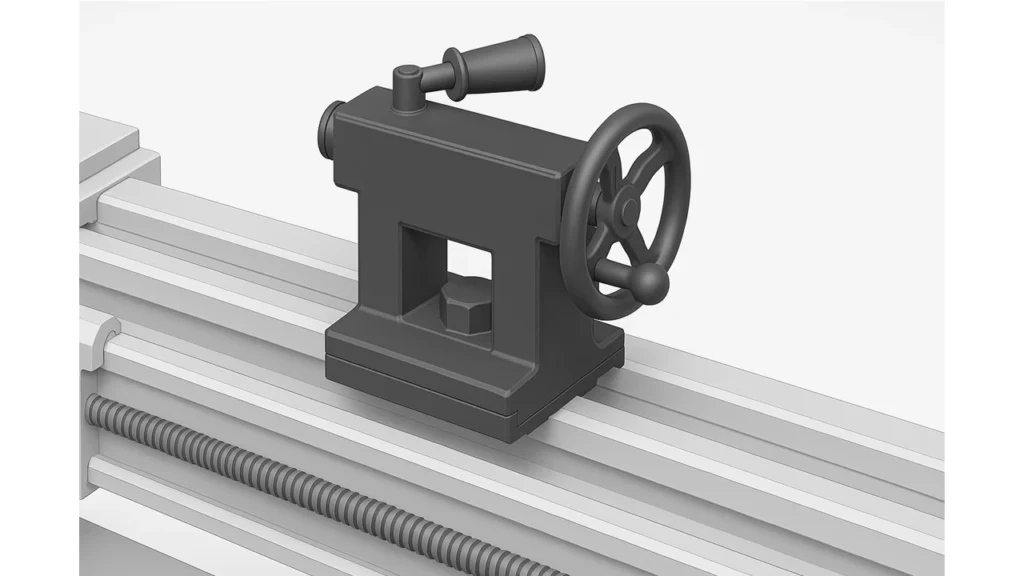
Material and Construction
The tailstock is typically made of cast iron to ensure high rigidity and stability. Its spindle is usually composed of high-carbon steel (HCS), which offers excellent strength and wear resistance.
Technical Features
- Quill Diameter and Travel: The tailstock quill can extend to varying lengths, typically ranging from 50 mm to 150 mm, depending on the lathe size.
- Locking Mechanism: A clamping system ensures the tailstock remains securely positioned during machining.
- Tailstock Offset Adjustment: Used for taper turning applications.
Functions of the Tailstock
- Provides additional support for long workpieces.
- Holds tools such as drills and reamers for axial operations.
- Ensures accuracy and stability during machining.
Maintenance Tips
- Clean and lubricate the quill regularly to prevent sticking.
- Check the tailstock alignment periodically to ensure it remains parallel to the spindle.
- Inspect and replace worn-out locking mechanisms to maintain stability.
Tool Post
Key Parts of a Lathe: The tool post is mounted on the carriage and holds the cutting tool securely in place. It allows for precise positioning and angle adjustments, enabling the operator to perform various cutting operations.
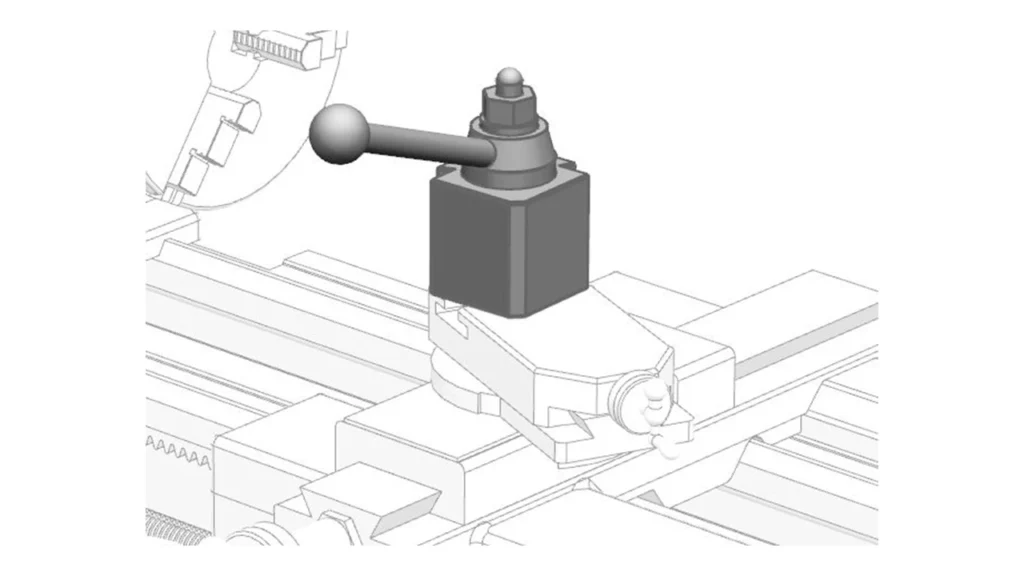
Material and Construction
The tool post is commonly made of hardened alloy steel to withstand the high forces generated during machining. Modern CNC lathes often use quick-change tool posts made of high-strength steel or aluminum alloys for faster tool changes and greater flexibility.
Technical Features
- Turret or Four-Way Tool Post: Allows for quick tool indexing and multiple cutting operations.
- Angle Adjustment: Facilitates fine-tuning of the cutting tool’s orientation.
- Locking System: Ensures stability and rigidity during machining.
Functions of the Tool Post
- Holds and positions the cutting tool.
- Enables quick tool changes and angle adjustments.
- Facilitates precise turning, facing, and threading.
Maintenance Tips
- Clean and oil the tool post regularly to prevent rust and maintain smooth tool changes.
- Inspect locking mechanisms for wear and replace as needed.
- Ensure the tool post is tightly secured to avoid tool chatter.
Guideways
Key Parts of a Lathe: The guideways are precision-machined surfaces located on the lathe bed. They guide the movement of the carriage and ensure smooth, accurate cutting by preventing misalignment.
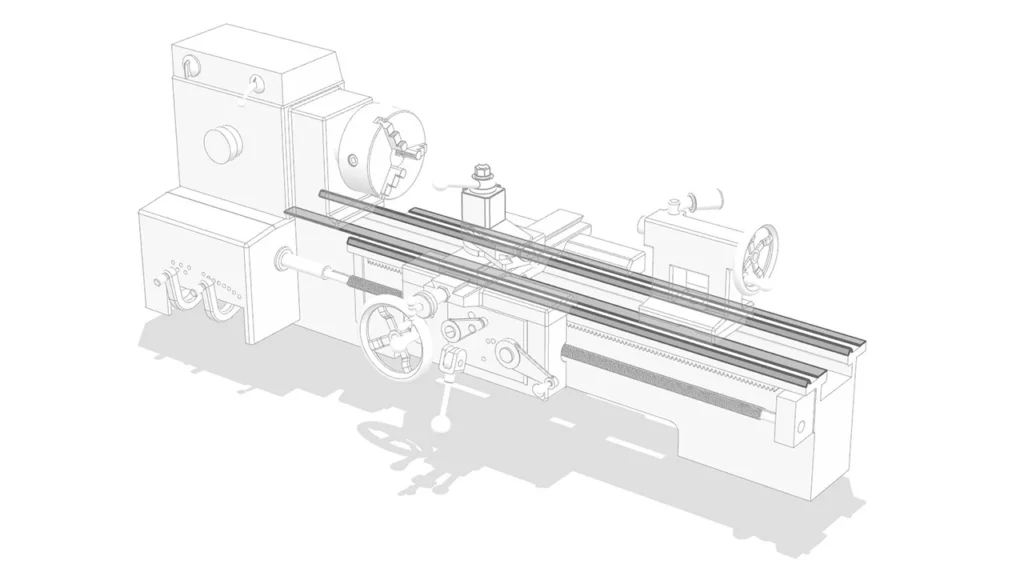
Material and Construction
Guideways are typically made from hardened and ground steel or high-grade cast iron. They undergo precise grinding to achieve a hardness of 45-55 HRC, ensuring wear resistance and long-lasting performance.
Technical Features
- Flat or V-Shaped Guideways: V-shaped guideways provide superior stability and alignment.
- Hand-Scraped Surfaces: High-end lathes often feature hand-scraped guideways to achieve ultra-high precision.
- Low Friction Coatings: Some guideways are coated with low-friction materials to enhance smooth motion.
Functions of the Guideways
- Controls the linear movement of the carriage.
- Prevents deviation during cutting.
- Maintains precision and accuracy in machining operations.
Maintenance Tips
- Clean the guideways after each use to remove debris.
- Apply a thin layer of way oil to prevent corrosion and friction.
- Check for any wear or scratches that may affect accuracy.
Chuck
Key Parts of a Lathe: The chuck is an essential component of a lathe that holds and secures the workpiece in place during machining. It is mounted on the spindle and rotates along with the workpiece.
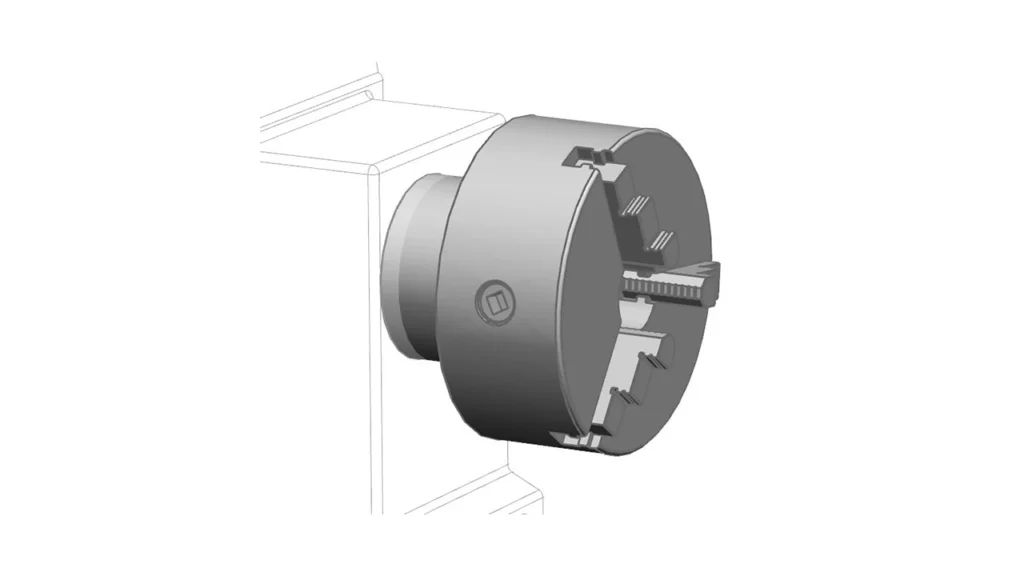
Types of Lathe Chucks
- Three-Jaw Chuck: Used for holding round or hexagonal workpieces. It is self-centering and commonly used in general machining operations.
- Four-Jaw Chuck: Provides independent jaw movement, making it ideal for holding irregularly shaped workpieces.
- Collet Chuck: Offers high precision for holding small and delicate workpieces, commonly used in CNC lathes.
- Magnetic Chuck: Suitable for holding ferromagnetic materials without mechanical clamping.
Functions of the Chuck
- Holds the workpiece securely during machining.
- Provides flexibility to accommodate different workpiece shapes.
- Ensures consistent and accurate rotation of the workpiece.
Maintenance Tips
- Clean the chuck regularly to remove metal shavings and debris.
- Apply lubricant to prevent rust and improve clamping performance.
- Check the jaws for wear and replace them if necessary.
Carriage
Key Parts of a Lathe: The carriage is a movable part that holds and controls the cutting tool’s movement along the lathe bed. It travels along the guideways to perform various cutting operations.
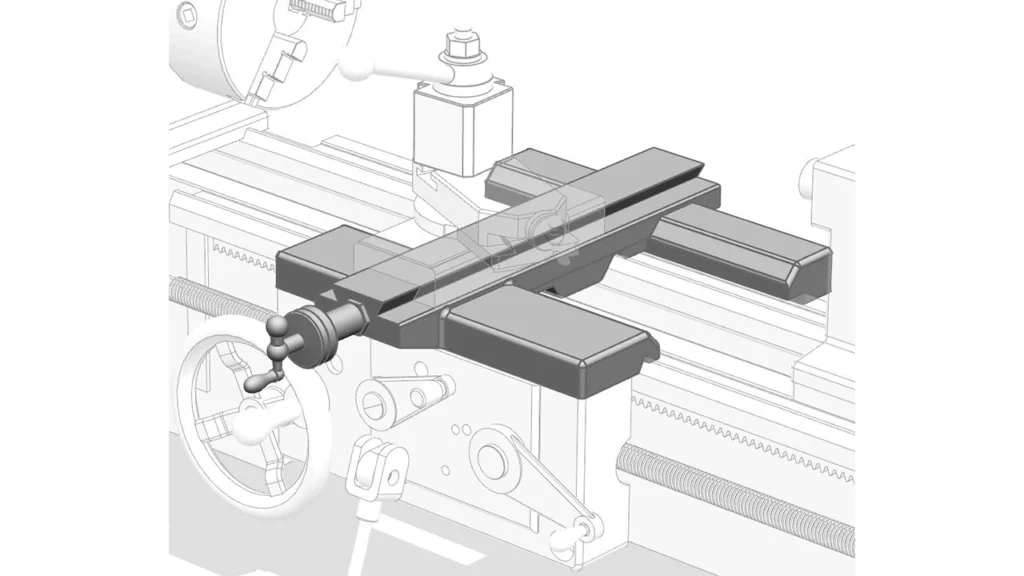
Components of the Carriage
- Saddle: Sits on the lathe bed and supports the cross slide and tool post.
- Cross Slide: Allows for lateral movement of the tool perpendicular to the spindle.
- Compound Rest: Provides angular adjustments for taper turning and precision cuts.
- Apron: Contains the mechanisms for moving the carriage and engaging automatic feed.
Functions of the Carriage
- Moves the cutting tool precisely along the workpiece.
- Allows for accurate turning, facing, and threading.
- Supports the tool post and provides stability during machining.
Maintenance Tips
- Lubricate the guideways and moving parts to ensure smooth motion.
- Clean the saddle and cross slide to prevent accumulation of chips.
- Inspect the lead screw and feed mechanisms for wear.
Lead Screw
Key Parts of a Lathe: The lead screw is a long threaded shaft that runs parallel to the lathe bed and is responsible for converting rotational motion into linear motion. It is primarily used for threading and automatic feed operations.
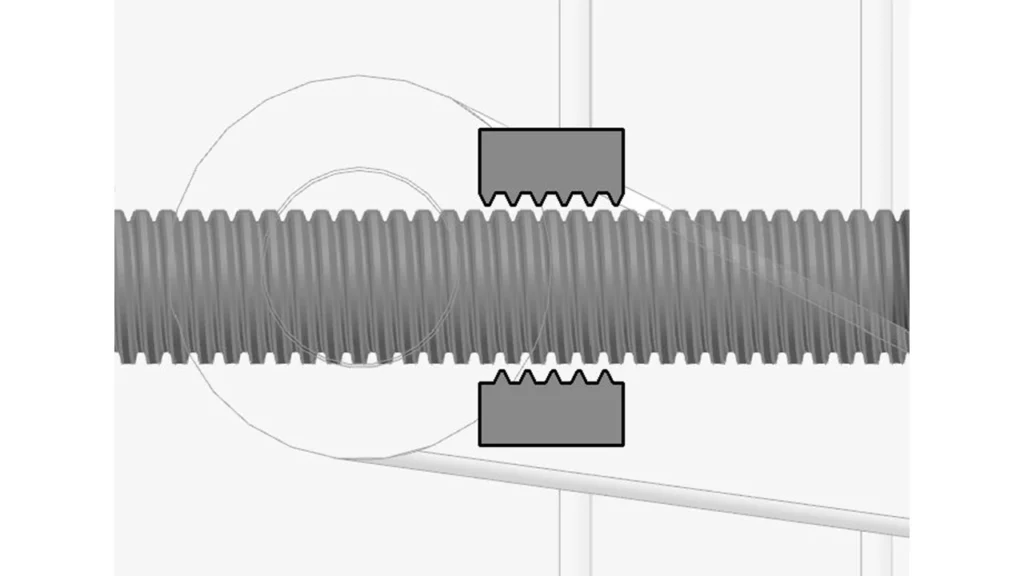
Material and Hardness
The lead screw is typically made of high-carbon steel or alloy steel to ensure high wear resistance and durability. It is often hardened to a range of 45-55 HRC to withstand prolonged use.
Functions of the Lead Screw
- Controls the movement of the carriage for threading and turning.
- Enables precise linear motion during cutting operations.
- Ensures consistent pitch and depth in threading applications.
Maintenance Tips
- Clean and lubricate the lead screw regularly to prevent wear.
- Check for signs of thread wear or misalignment.
- Avoid overloading the lead screw to maintain accuracy.
Feed Rod
Key Parts of a Lathe: The feed rod is a parallel shaft located below the lead screw that transmits power to the carriage for automatic longitudinal and cross-feed operations.
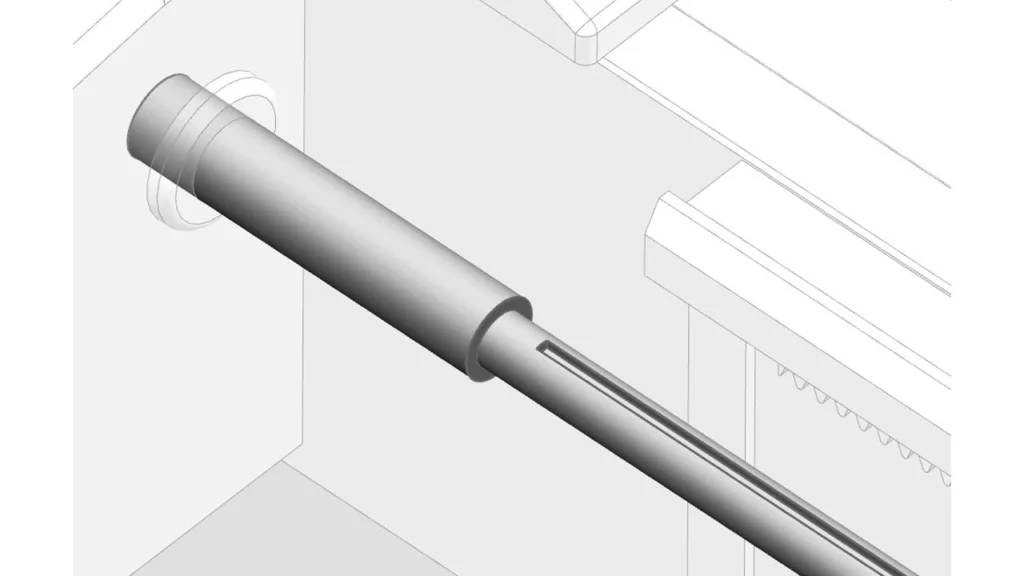
Functions of the Feed Rod
- Provides power for automatic feeding of the cutting tool.
- Enables consistent and uniform cuts during machining.
- Ensures smooth movement of the carriage and cross slide.
Maintenance Tips
- Keep the feed rod clean and free of debris.
- Apply appropriate lubricants to reduce friction.
- Inspect the gears and clutches for wear and replace if needed.
Apron
Key Parts of a Lathe: The apron is mounted on the front of the carriage and contains mechanisms that control the movement of the carriage along the lathe bed. It houses the gears, clutches, and levers that engage the feed rod and lead screw.
Functions of the Apron
- Controls the automatic feed and threading operations.
- Houses the mechanisms for moving the carriage.
- Engages and disengages the lead screw and feed rod.
Maintenance Tips
- Clean the apron regularly to remove metal chips and dirt.
- Lubricate the internal gears and clutches to prevent wear.
- Check the engagement levers for smooth operation.
Compound Rest
Key Parts of a Lathe: The compound rest is mounted on the cross slide and allows for angular adjustments to perform taper turning and intricate cuts.
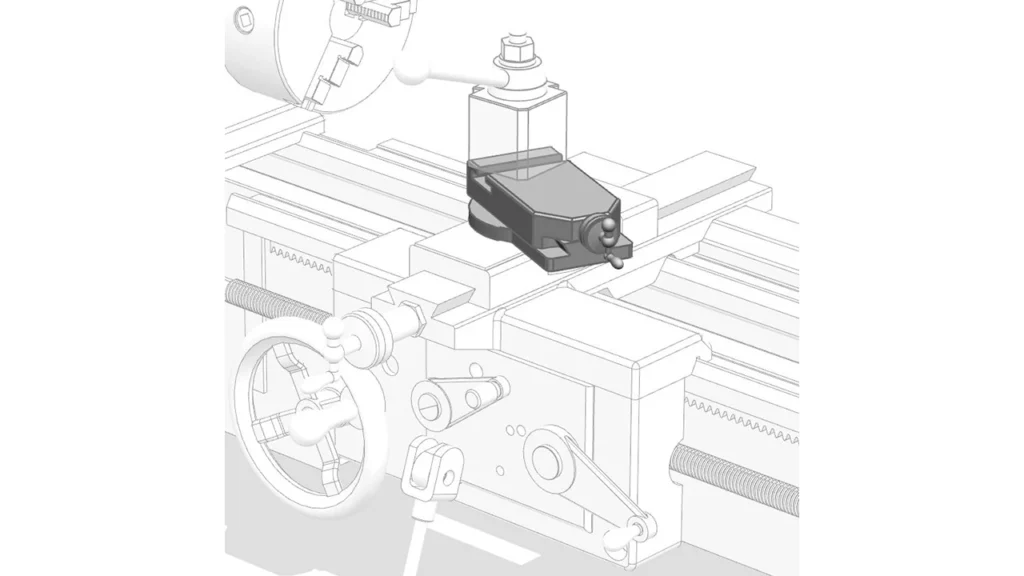
Functions of the Compound Rest
- Allows for angular adjustments for taper cutting.
- Provides fine control over the cutting tool’s position.
- Enables precision cuts for threading and contouring.
Maintenance Tips
- Ensure smooth movement by keeping the compound rest lubricated.
- Check for backlash and tighten the gibs if necessary.
- Keep the surface clean and free from chips and debris.
Faceplate
Key Parts of a Lathe: The faceplate is a large, flat disc that mounts onto the spindle and is used to hold irregularly shaped workpieces that cannot be held by a chuck.
Functions of the Faceplate
- Holds large or irregularly shaped workpieces.
- Facilitates machining of non-cylindrical parts.
- Provides stability for off-center operations.
Maintenance Tips
- Clean the faceplate after each use to remove debris.
- Ensure the faceplate is properly balanced to avoid vibration.
- Inspect for signs of wear and replace if necessary.
Steady Rest and Follower Rest
Key Parts of a Lathe: Steady rests and follower rests are used to support long workpieces and prevent deflection during machining.
Functions of Steady Rest and Follower Rest
- Provides additional support for long or slender workpieces.
- Prevents vibration and deflection during high-speed operations.
- Ensures accuracy and consistency in machining.
Maintenance Tips
- Clean the contact surfaces and apply lubricants to prevent friction.
- Check for misalignment and adjust accordingly.
- Inspect for wear and replace damaged components as needed.
Lathe Parts Diagram With Name
To fully grasp the key parts of a lathe and their respective functions, it is essential to refer to a lathe diagram with parts labeled for clarity. A lathe parts diagram provides a visual representation of the primary parts of a lathe machine, helping machinists and learners understand the overall structure and relationship between various components. By studying a diagram of lathe machine parts, users can identify each critical component and appreciate how these lathe parts work together to ensure smooth machining operations. Below is a detailed overview of the labeled parts of a lathe shown in a typical diagram.
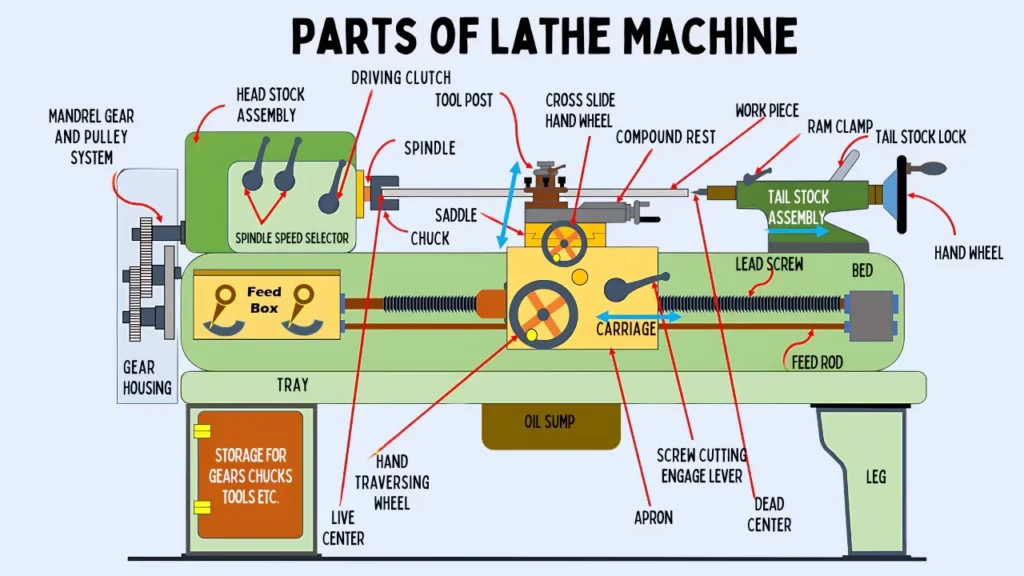
A lathe parts diagram serves as an essential reference for machinists, technicians, and learners, enabling them to fully understand the structural layout and relationship between the parts of a lathe. By studying a diagram of lathe parts, operators gain valuable insight into how different lathe machine parts interact to ensure smooth and accurate machining. This knowledge significantly enhances operational efficiency and minimizes errors, especially for those who are new to understanding the key parts of a lathe and their functions.
Specialized Lathe Components and Their Applications
In addition to the primary parts of a lathe, several specialized components are designed to enhance the precision, versatility, and operational efficiency of the machine. These lathe parts play a crucial role in complex machining processes and enable machinists to perform more advanced operations. By incorporating these specialized parts of a lathe machine, operators can significantly expand the machine’s capabilities, allowing for greater accuracy and efficiency in diverse machining applications.
Backplate
The backplate is an adapter used to mount the chuck onto the spindle. It ensures that the chuck is securely attached to the spindle and maintains alignment for precision machining.
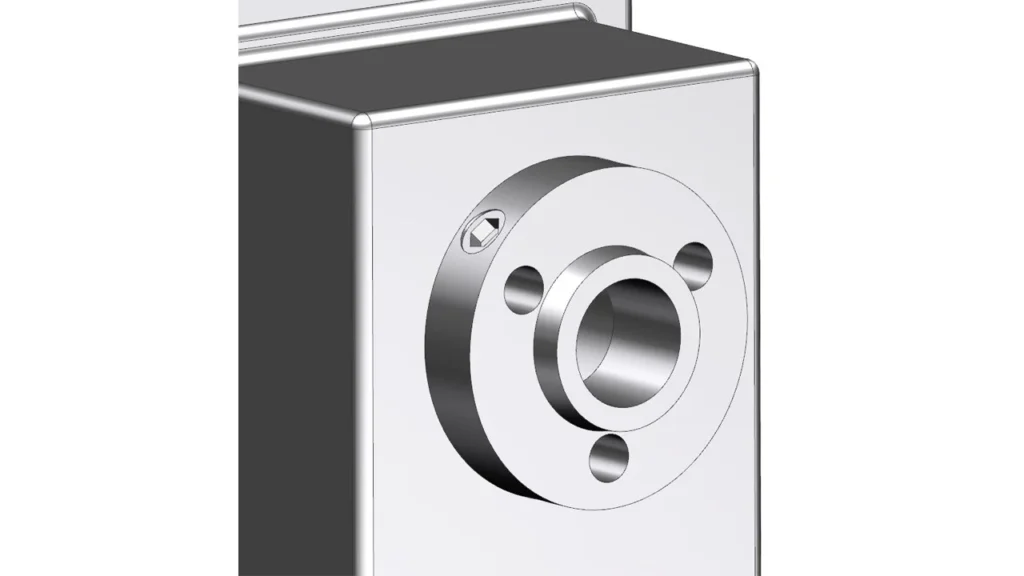
Material and Construction
- Made from high-strength cast iron or steel, ensuring high rigidity and vibration resistance.
- Precision-machined to provide accurate alignment between the chuck and the spindle.
Functions of the Backplate
- Connects the chuck to the spindle securely.
- Maintains concentricity between the chuck and the spindle.
- Provides a stable platform for high-precision machining.
Maintenance Tips
- Regularly clean the backplate to remove debris and prevent misalignment.
- Check for wear on the mounting surfaces to maintain concentricity.
- Apply anti-rust agents to prevent corrosion.
Mandrel
A mandrel is a cylindrical device used to hold hollow workpieces securely during machining. It provides a precise and stable grip, allowing for uniform machining of cylindrical components.
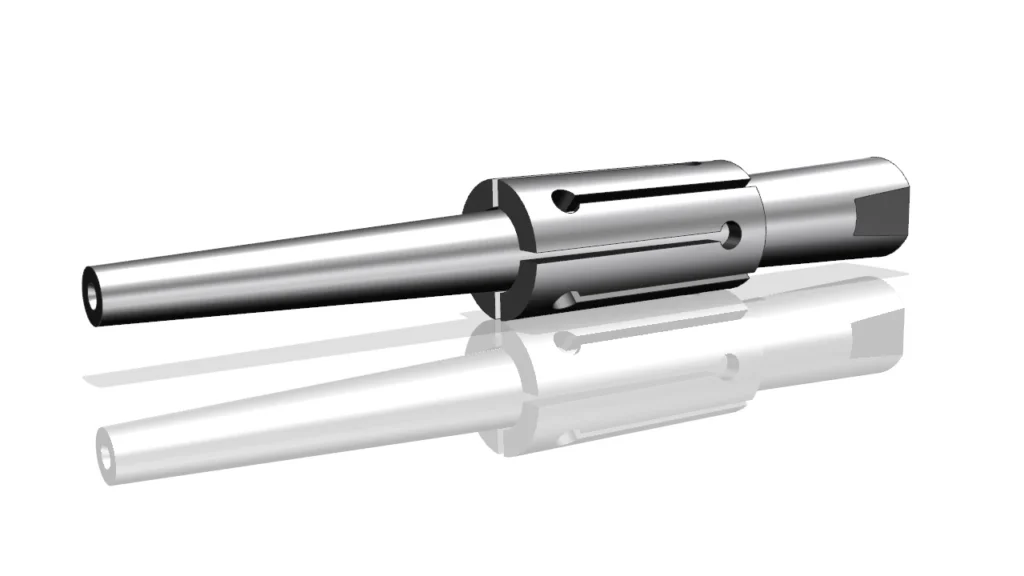
Types of Mandrels
- Solid Mandrel: Used for holding solid cylindrical workpieces.
- Expanding Mandrel: Used for gripping hollow workpieces by expanding outward.
- Taper Mandrel: Used for holding tapered workpieces securely.
Functions of the Mandrel
- Provides support for hollow and cylindrical workpieces.
- Ensures concentricity during turning operations.
- Allows for uniform machining of internal and external surfaces.
Maintenance Tips
- Inspect mandrels for wear and replace them when necessary.
- Clean mandrels after each use to remove dust and debris.
- Apply lubricants to prevent friction and corrosion.
Catch Plate
A catch plate is a component attached to the spindle to drive a workpiece or mandrel when using a lathe dog. It is commonly used in operations where cylindrical or long workpieces need to be driven securely.
Functions of the Catch Plate
- Transfers rotational motion from the spindle to the workpiece.
- Ensures secure driving of workpieces during turning operations.
- Works in conjunction with lathe dogs to stabilize the workpiece.
Maintenance Tips
- Check for cracks or wear on the catch plate to prevent slippage.
- Keep the mounting surface clean to maintain concentricity.
- Lubricate the contact points regularly to reduce friction.
Half Nut Mechanism
The half nut mechanism is an essential part of the carriage, used to engage and disengage the lead screw for automatic feed or threading operations.
Functions of the Half Nut Mechanism
- Engages the lead screw to provide automatic feed for threading.
- Disengages to allow manual movement of the carriage.
- Facilitates precision threading and turning operations.
Maintenance Tips
- Clean the threads and nut surfaces regularly to prevent debris buildup.
- Inspect the half nut for wear and replace it if it becomes loose.
- Apply lubricants to minimize friction and maintain smooth movement.
Spindle and Bearings
The spindle is the rotating axis in the headstock that holds and rotates the workpiece. It is supported by high-precision bearings to ensure smooth and stable rotation.
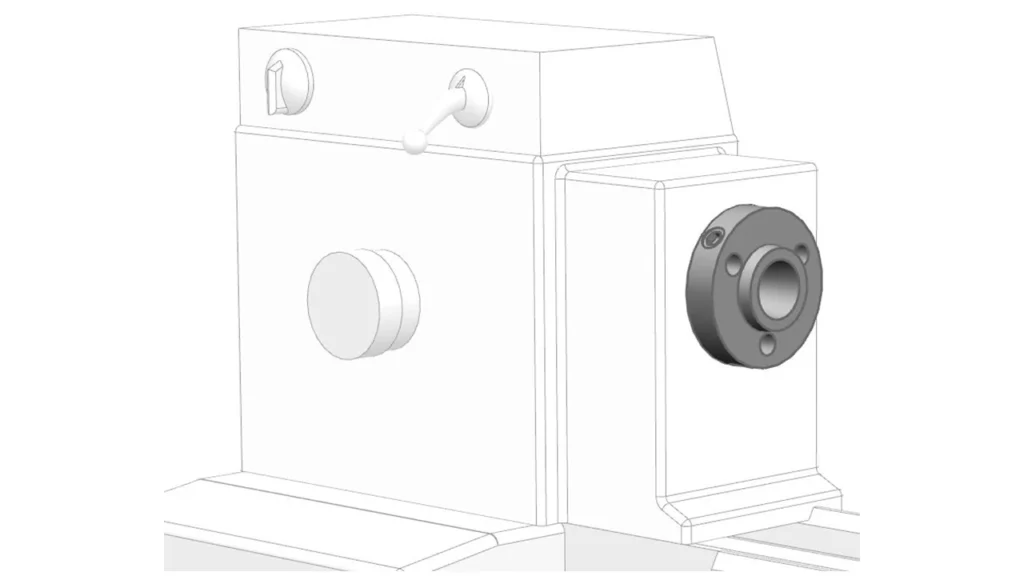
Types of Bearings Used
- Tapered Roller Bearings: Provide high load-bearing capacity and stability.
- Ball Bearings: Offer high-speed performance with low friction.
- Hydrodynamic Bearings: Ideal for heavy-duty applications due to their high damping capacity.
Functions of the Spindle and Bearings
- Provides rotational motion to the workpiece.
- Maintains spindle alignment and stability.
- Ensures high-speed precision for machining operations.
Maintenance Tips
- Regularly lubricate the spindle bearings to prevent overheating.
- Monitor spindle runout to ensure precision.
- Inspect bearings for wear and replace them if necessary.
Gears and Gearbox
The gears and gearbox in a lathe control the spindle speed, feed rate, and threading pitch by transmitting motion between the motor and the spindle.
Types of Gear Mechanisms
- Change Gears: Used for threading and speed changes.
- Quick-Change Gearbox: Facilitates easy adjustments of feed and threading settings.
Functions of Gears and Gearbox
- Controls spindle speed and feed rate.
- Allows for different threading pitches and depths.
- Ensures smooth motion transfer between components.
Maintenance Tips
- Keep the gears clean and well-lubricated to prevent wear.
- Check for misalignment and adjust if necessary.
- Replace damaged or worn-out gears to avoid operational disruptions.
Lead Screw Reverse Mechanism
The lead screw reverse mechanism is used to change the direction of the carriage’s movement, making it ideal for threading operations.
Functions of the Lead Screw Reverse Mechanism
- Changes the direction of the carriage for threading operations.
- Provides control over the longitudinal feed during machining.
- Ensures consistent thread pitch during reverse threading.
Maintenance Tips
- Regularly clean and lubricate the reverse mechanism.
- Inspect for any misalignment and correct it promptly.
- Ensure that the reversing mechanism is properly engaged to prevent damage.
Motor and Transmission System in a Lathe
The motor and transmission system form the backbone of a lathe machine, delivering the necessary rotational power and controlling the speed and torque required for precision machining. These components work in tandem to ensure that the spindle and workpiece rotate consistently, allowing for high-quality machining operations.
Motor
The motor is the primary power source of a lathe machine, converting electrical energy into mechanical energy to rotate the spindle and drive the cutting tool. Modern lathes use high-efficiency motors that offer variable speed control, enabling better control over the machining process.
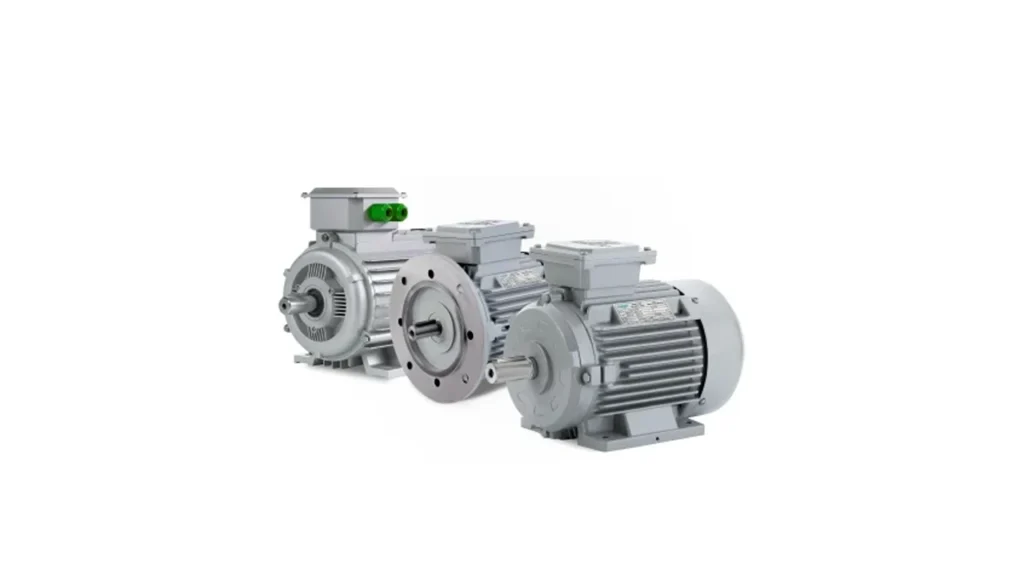
Material and Construction
- The motor casing is typically made from high-strength aluminum or cast iron, providing durability and heat dissipation.
- The rotor and stator are made from silicon steel laminations, enhancing magnetic efficiency and minimizing energy loss.
- High-quality copper windings ensure efficient current flow and reduced power loss.
Technical Features
- Power Rating: Ranges from 0.5 HP to 10 HP, depending on the size and capacity of the lathe.
- Speed Control: Offers a variable speed range from 50 RPM to 3000 RPM to accommodate different machining applications.
- Thermal Protection: Modern motors feature built-in thermal protection to prevent overheating and ensure safe operation.
- Variable Frequency Drive (VFD): Some advanced lathes incorporate VFD motors that allow smooth speed adjustments and enhanced control.
Functions of the Motor
- Converts electrical energy into mechanical motion, driving the spindle.
- Provides consistent rotational power for various machining operations.
- Allows speed adjustments to suit different workpiece materials and cutting conditions.
Maintenance Tips
- Regularly inspect and clean the motor’s ventilation system to prevent overheating.
- Monitor motor temperature and avoid prolonged operation under heavy loads.
- Check the wiring and connections for wear and ensure secure grounding.
- Lubricate the motor bearings periodically to minimize friction and prevent wear.
Transmission System
The transmission system transfers power from the motor to the spindle and other moving parts of the lathe. It controls the spindle’s speed and torque, enabling the machine to perform various cutting operations effectively. Depending on the type of lathe, the transmission system may use belts, gears, or a combination of both.
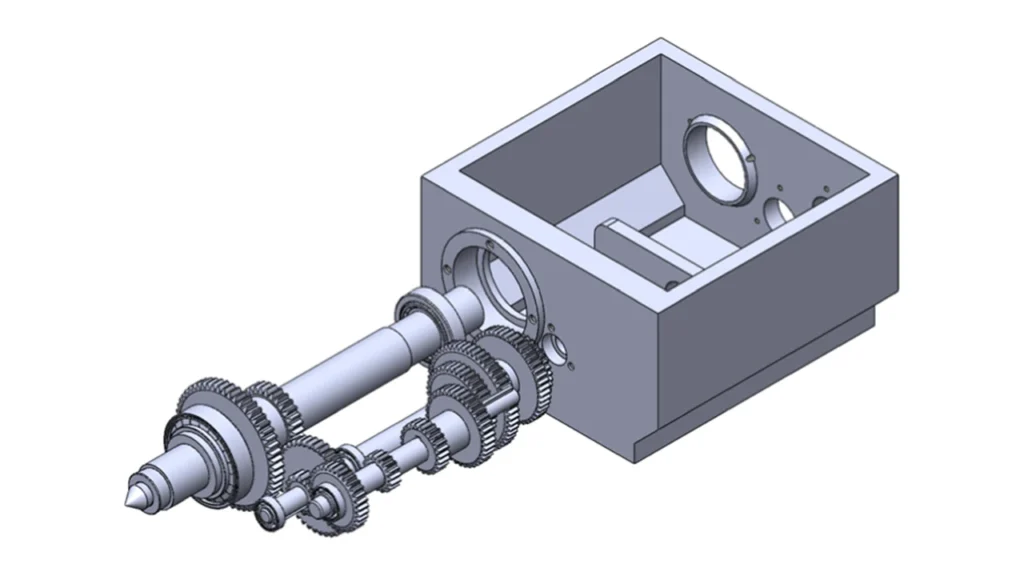
Material and Construction
- Pulleys and Belts: Made from reinforced rubber or polyurethane, ensuring flexibility and wear resistance.
- Gears and Gearbox: Typically made from hardened alloy steel to withstand high loads and maintain long-term durability.
- Gear Housing: Cast from high-grade cast iron to reduce vibration and ensure alignment.
Types of Transmission Systems
- Belt Drive System
- Uses pulleys and belts to transfer power from the motor to the spindle.
- Ideal for light to medium-duty machining applications.
- Offers quiet operation and easy maintenance.
- Gear Drive System
- Employs gears to transmit motion and change spindle speed.
- Suitable for heavy-duty operations that require high torque.
- Provides better efficiency and power transmission compared to belt drives.
- Variable Speed Transmission
- Allows for continuous speed adjustments without stopping the machine.
- Offers greater flexibility for different machining processes.
- Ideal for CNC lathes where precise speed control is required.
Technical Features
- Speed Range: Adjustable from 50 RPM to 3000 RPM, depending on the drive system.
- Torque Control: Provides high torque at low speeds for heavy-duty operations.
- Quick Gear Change: Gearboxes allow for easy speed and feed adjustments.
- Reverse Mechanism: Enables reverse rotation for specific machining applications.
Functions of the Transmission System
- Transfers power from the motor to the spindle, carriage, and feed rod.
- Controls spindle speed and feed rate for optimal cutting performance.
- Allows for different threading pitches and cutting operations.
- Reduces vibration and ensures smooth operation.
Maintenance Tips
- Inspect belts and pulleys regularly for signs of wear and replace them if necessary.
- Lubricate gears and bearings to minimize friction and prolong their lifespan.
- Check gear alignment and adjust as needed to prevent misalignment and excessive noise.
- Ensure that the gear train is properly tensioned to avoid slippage.
Safety Features and Control Systems in a Lathe
Modern lathes are equipped with a variety of safety features and control systems that protect the operator, ensure machine efficiency, and prevent mechanical failures. These systems play an integral role in safeguarding the parts of a lathe machine, minimizing risks, and maintaining consistent performance throughout the machining process. By understanding how these lathe parts contribute to safety and control, machinists can prolong the life of the machine while ensuring smoother and safer operations. Below is a detailed overview of the most critical safety features and control systems associated with the key parts of a lathe.
Chuck Guard
The chuck guard is a transparent or metal safety shield that encloses the rotating chuck to protect the operator from accidental contact and flying debris. It is mounted on the headstock and swings into place to cover the chuck during machining.
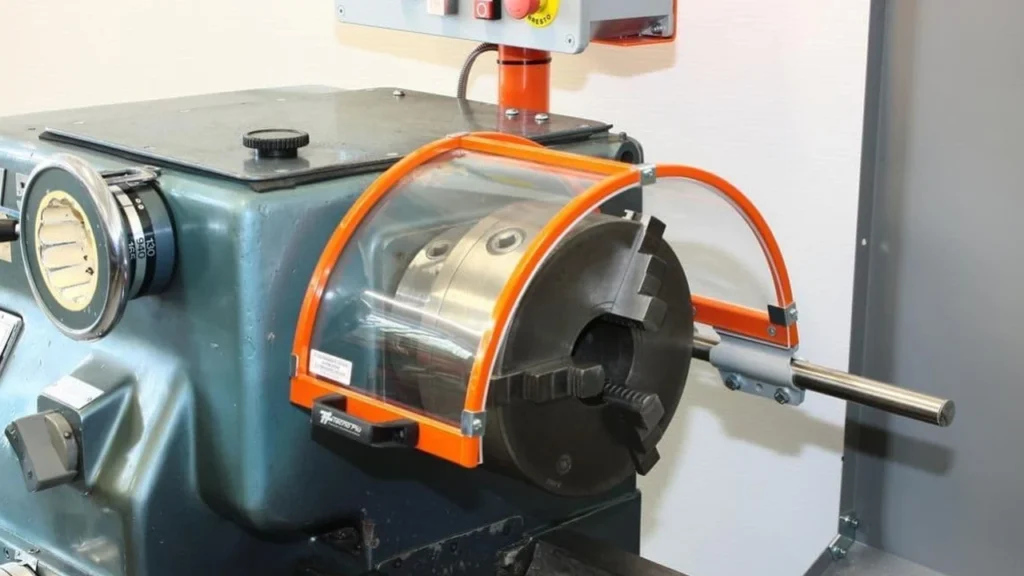
Material and Construction
- Made from high-impact polycarbonate or acrylic for maximum visibility and durability.
- Some models feature metal mesh guards for heavy-duty applications.
- Equipped with spring-loaded hinges for easy opening and closing.
Functions of the Chuck Guard
- Prevents accidental contact with the rotating chuck, reducing the risk of injuries.
- Shields the operator from metal chips, coolant splashes, and flying debris.
- Enhances visibility while maintaining operator safety.
Maintenance Tips
- Clean the guard regularly to maintain clear visibility.
- Check for cracks or damage and replace the guard if necessary.
- Ensure the hinge mechanism operates smoothly and securely locks in place.
Emergency Stop Button (E-Stop)
The emergency stop button (E-Stop) is a critical safety feature that immediately halts all machine operations when activated. It is typically located on the control panel or within easy reach of the operator.
Functions of the Emergency Stop Button
- Instantly stops the spindle, feed mechanism, and motor.
- Prevents accidents and minimizes damage to the workpiece and machine.
- Provides a quick response mechanism in emergency situations.
Maintenance Tips
- Test the E-Stop button periodically to ensure functionality.
- Inspect wiring and connections for wear or damage.
- Clean around the button to prevent dust or debris from interfering with operation.
Lead Screw and Feed Rod Interlock
The lead screw and feed rod interlock is a mechanical safety feature that prevents the simultaneous engagement of the lead screw and feed rod, which could cause mechanical damage.

Functions of the Lead Screw and Feed Rod Interlock
- Prevents accidental engagement of both mechanisms, avoiding overload and damage.
- Ensures smoother operation during threading and feed operations.
- Reduces the likelihood of operator errors during gear changes.
Maintenance Tips
- Inspect the interlock mechanism for wear and misalignment.
- Lubricate moving parts to maintain smooth operation.
- Check for loose or worn components and replace them as needed.
Automatic Overload Protection
Automatic overload protection is a system that prevents damage to the motor and transmission system by disengaging the drive mechanism when excessive load or torque is detected.
Functions of Automatic Overload Protection
- Prevents motor overheating and damage.
- Automatically disengages operations when load limits are exceeded.
- Extends the lifespan of the motor, gearbox, and other critical components.
Maintenance Tips
- Regularly inspect the overload protection system for proper operation.
- Check load sensors and switches for wear or malfunction.
- Reset the system after any overload event and inspect for damage.
Control Panel and Switches
The control panel contains an array of switches, dials, and digital displays that allow the operator to control machine functions, including spindle speed, feed rate, and emergency shutdown.
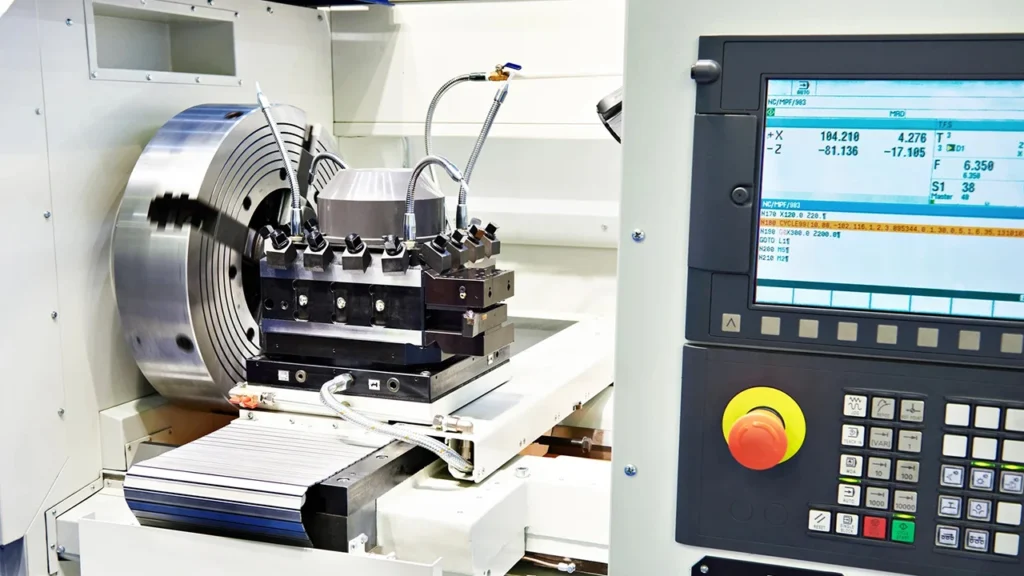
Functions of the Control Panel and Switches
- Provides easy access to operational controls and adjustments.
- Allows for precise speed, feed, and threading control.
- Enables emergency shutdown to prevent accidents.
Maintenance Tips
- Keep the control panel clean and free of dust and debris.
- Inspect switches and dials for signs of wear and replace if necessary.
- Test the emergency stop functionality regularly.
Coolant and Lubrication Systems
The coolant and lubrication systems ensure that cutting tools and workpieces remain cool and properly lubricated during machining operations, preventing overheating and reducing friction.
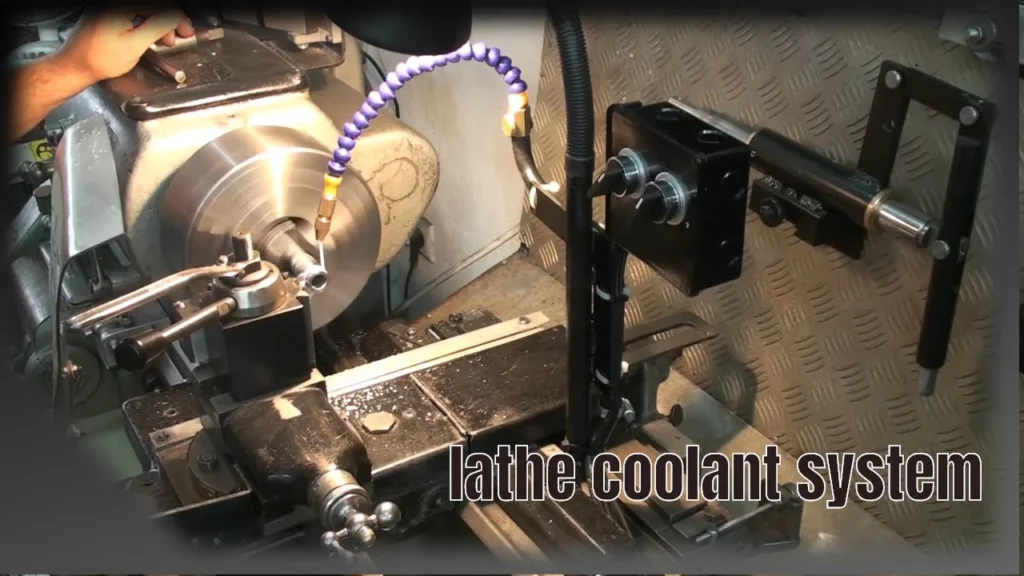
Functions of Coolant and Lubrication Systems
- Prevents heat buildup during high-speed cutting.
- Lubricates moving parts to reduce wear and friction.
- Improves tool life and surface finish.
Maintenance Tips
- Regularly check coolant levels and refill as needed.
- Clean filters and coolant lines to prevent clogging.
- Inspect the lubrication system for leaks or blockages.
Foot Brake
The foot brake is a mechanical or electronic system that allows the operator to quickly stop the spindle rotation using a foot pedal, providing an additional layer of safety.
Functions of the Foot Brake
- Stops the spindle quickly without using the E-Stop.
- Provides greater control during emergency situations.
- Enhances operator safety by enabling hands-free stopping.
Maintenance Tips
- Test the foot brake periodically to ensure responsiveness.
- Inspect for wear on the brake pads and replace if necessary.
- Lubricate the brake mechanism to maintain smooth operation.
Spindle Lock Mechanism
The spindle lock mechanism is used to prevent spindle rotation when changing the chuck or performing maintenance on the machine.
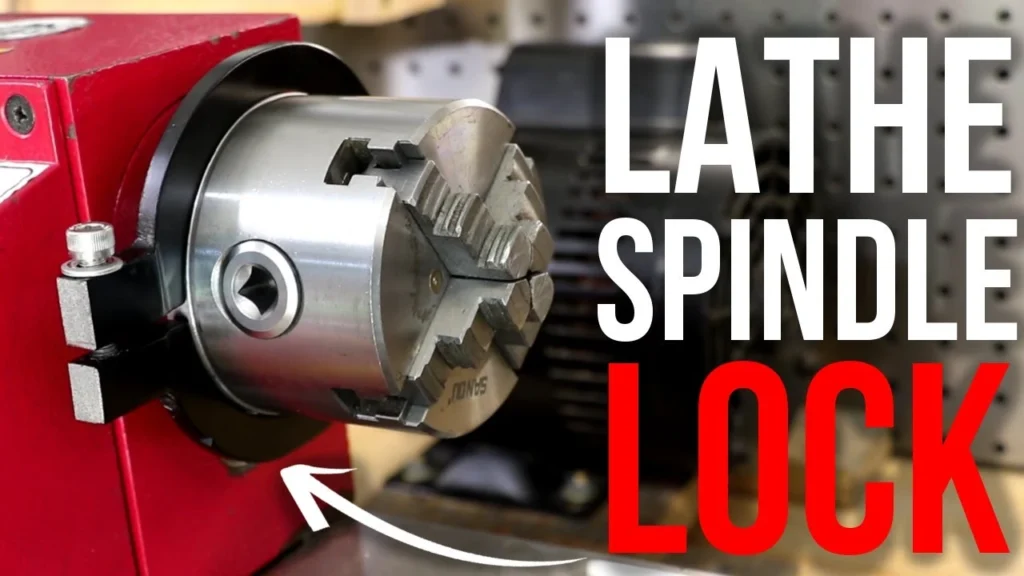
Functions of the Spindle Lock Mechanism
- Secures the spindle to prevent accidental rotation.
- Facilitates safe and easy chuck removal and installation.
- Prevents operator injuries during maintenance tasks.
Maintenance Tips
- Ensure the lock engages securely and releases smoothly.
- Inspect for wear and lubricate moving parts as needed.
- Avoid forcing the lock mechanism to prevent damage.
Types of Lathes and Their Specialized Parts
Lathes come in various types, each equipped with specialized parts of a lathe that are designed to meet specific machining requirements. These lathe machine parts enhance performance, improve efficiency, and ensure greater precision during complex operations. Understanding the differences between these types—and the unique lathe parts they incorporate—helps machinists select the best machine for their application. Below is a comprehensive overview of the most commonly used types of lathes and the specialized parts of a lathe machine that make them suitable for diverse machining tasks.
Engine Lathe
The engine lathe is the most versatile and widely used type of lathe, found in general machine shops for a variety of machining tasks. It is ideal for turning, facing, and threading, and is often used for producing cylindrical parts.
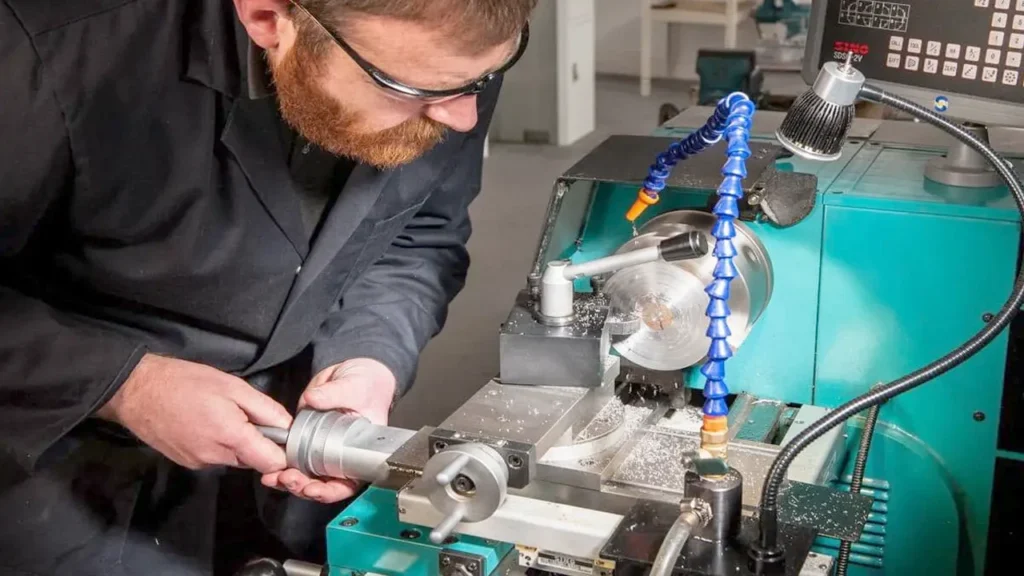
Specialized Parts in an Engine Lathe
- Quick-Change Gearbox: Allows rapid changes in spindle speed and feed rates.
- Lead Screw and Half Nut Mechanism: Facilitates threading and automatic feed operations.
- Compound Rest: Enables angular adjustments for taper turning.
Functions of an Engine Lathe
- Performs turning, facing, and threading operations.
- Suitable for producing shafts, rods, and other cylindrical components.
- Ideal for general-purpose machining with a wide range of materials.
Maintenance Tips
- Lubricate the gearbox and lead screw regularly to ensure smooth operation.
- Clean the carriage and guideways to prevent debris buildup.
- Inspect and adjust the half nut mechanism to avoid threading errors.
Turret Lathe
The turret lathe is designed for mass production and repetitive machining tasks. It features a rotating turret that holds multiple cutting tools, allowing for quick tool changes and reduced cycle times.
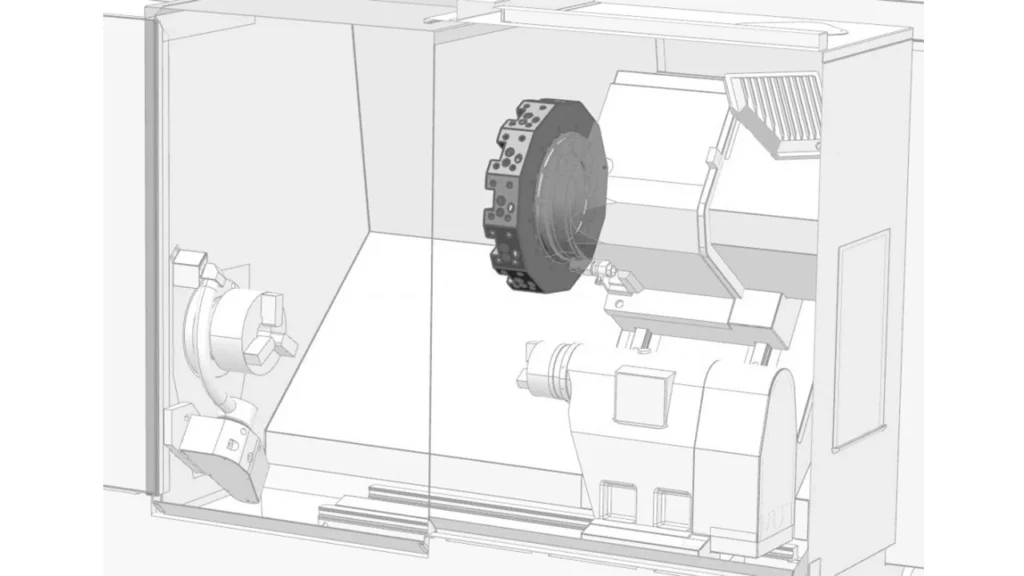
Specialized Parts in a Turret Lathe
- Turret Head: Holds multiple cutting tools and indexes automatically for sequential operations.
- Cross Slide with Tool Carriage: Facilitates precise tool positioning and rapid movement.
- Bar Feeder: Automatically feeds long workpieces for continuous operations.
Functions of a Turret Lathe
- Facilitates quick tool changes and reduces machining time.
- Ideal for batch production and repetitive machining tasks.
- Increases efficiency by minimizing operator intervention.
Maintenance Tips
- Clean and lubricate the turret head to ensure smooth indexing.
- Inspect the bar feeder mechanism for wear and adjust as needed.
- Monitor tool alignment to prevent dimensional errors.
CNC Lathe
The CNC (Computer Numerical Control) lathe is a highly automated and precision-driven machine that uses computer programming to control machining operations. It is ideal for complex and high-precision parts.
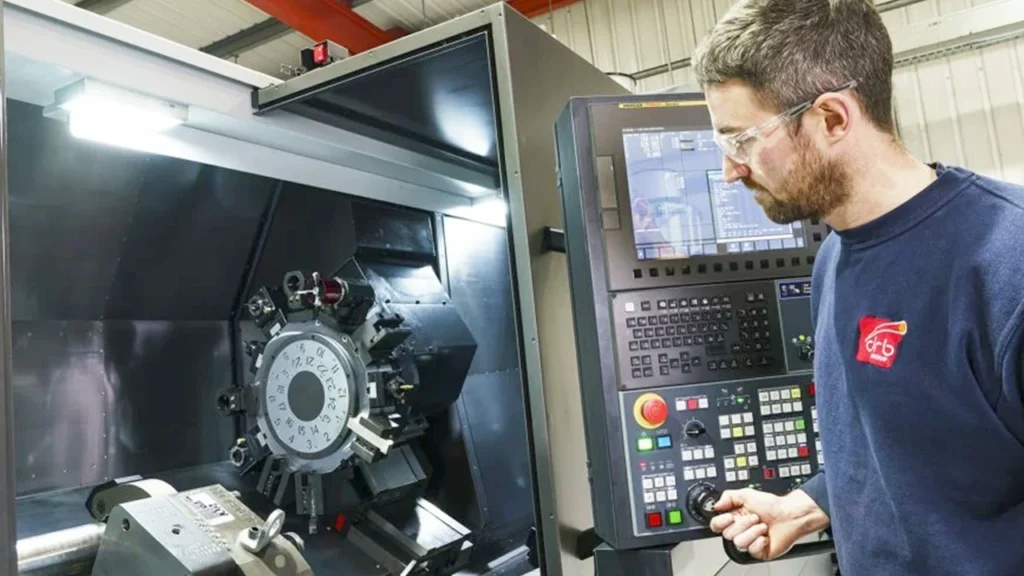
Specialized Parts in a CNC Lathe
- Servo Motors and Drives: Provide precise control over spindle speed and tool movement.
- Tool Turret with Automatic Tool Changer: Allows seamless tool switching for continuous machining.
- CNC Control Panel: Enables programming and real-time monitoring of machining parameters.
Functions of a CNC Lathe
- Performs high-precision machining with minimal human intervention.
- Executes complex machining operations such as contouring and threading.
- Ensures consistent part quality in high-volume production.
Maintenance Tips
- Regularly update CNC software and firmware for optimal performance.
- Lubricate moving parts to prevent friction and wear.
- Inspect servo motors and control systems for faults or errors.
Swiss-Type Lathe
The Swiss-type lathe is known for its ability to produce high-precision, small-diameter parts with tight tolerances. It is commonly used in industries such as medical, aerospace, and electronics.
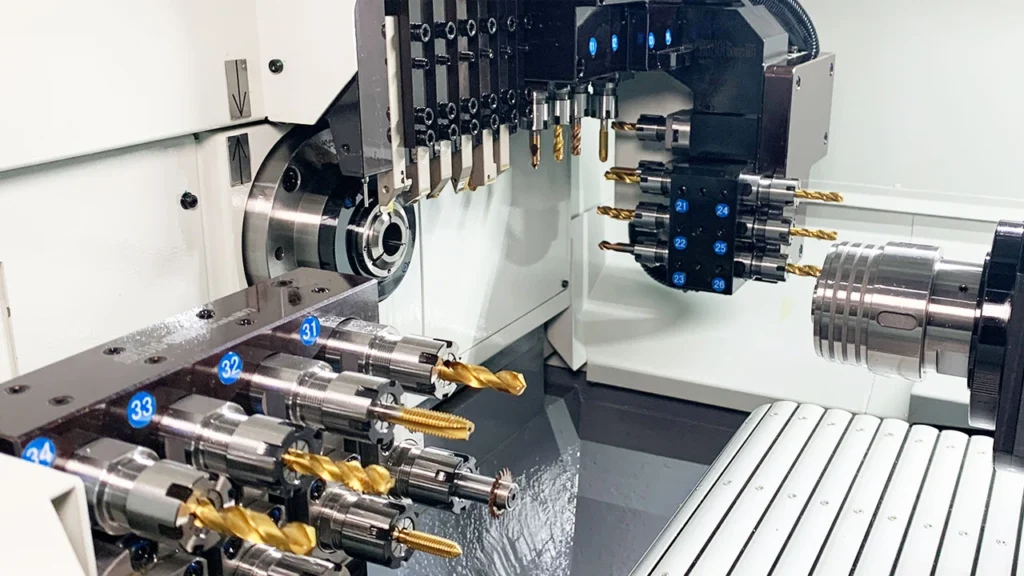
Specialized Parts in a Swiss-Type Lathe
- Guide Bushing: Provides support to long and slender workpieces during machining.
- Sliding Headstock: Moves the workpiece axially while the tools remain stationary.
- Multiple Tool Holders: Accommodates simultaneous operations to enhance productivity.
Functions of a Swiss-Type Lathe
- Ideal for producing micro-components with high precision.
- Enables continuous machining of long, slender workpieces.
- Minimizes deflection and enhances surface finish.
Maintenance Tips
- Clean and lubricate the guide bushing to prevent wear.
- Inspect the sliding headstock for misalignment or play.
- Check tool holders and replace worn tools to maintain accuracy.
Vertical Lathe
The vertical lathe (also known as a vertical turning lathe or VTL) is used for machining large, heavy workpieces with a vertical spindle orientation. It is commonly used in industries such as aerospace, automotive, and heavy machinery.
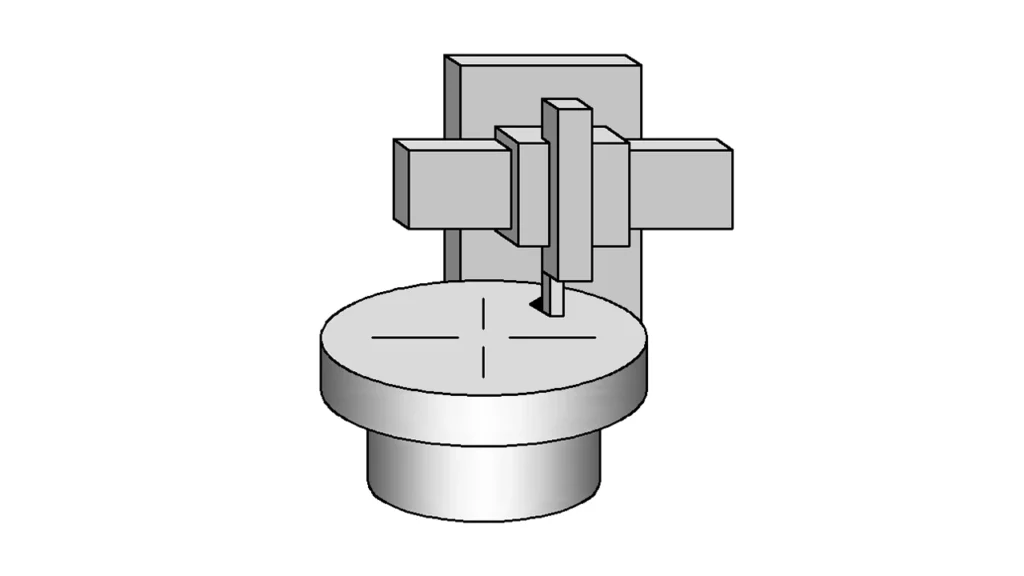
Specialized Parts in a Vertical Lathe
- Vertical Spindle: Allows gravity to assist in holding heavy workpieces.
- Cross Rail and Ram: Provides vertical and horizontal motion for cutting tools.
- Rotating Table: Supports and rotates the workpiece during machining.
Functions of a Vertical Lathe
- Handles large and heavy workpieces with ease.
- Ideal for machining turbine rotors, flywheels, and other large parts.
- Ensures stability and precision during high-load operations.
Maintenance Tips
- Lubricate the rotating table and cross rail to minimize friction.
- Clean the spindle and inspect for wear regularly.
- Check for proper alignment of the cutting tools.
Pipe Thread Lathe
The pipe thread lathe is specifically designed for threading and machining pipes used in the oil and gas industry. It provides high-precision threading capabilities and is ideal for large-diameter pipes.
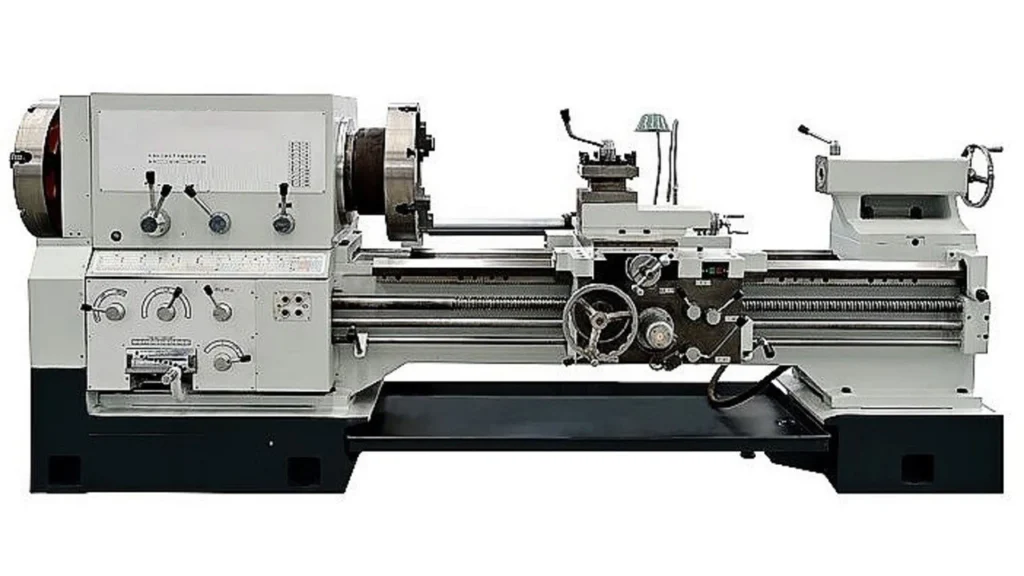
Specialized Parts in a Pipe Thread Lathe
- Threading Head: Enables high-precision threading of pipes.
- Steady Rest and Follower Rest: Supports long pipes to prevent deflection.
- Taper Attachment: Facilitates threading of tapered threads.
Functions of a Pipe Thread Lathe
- Produces precise threads on large-diameter pipes.
- Supports pipes during machining to maintain concentricity.
- Facilitates threading operations for both standard and tapered threads.
Maintenance Tips
- Clean and lubricate the threading head to prevent wear.
- Inspect steady and follower rests for alignment and smooth movement.
- Monitor the taper attachment for accuracy during operations.
Comparison of Lathe Types and Applications
Lathe Type | Specialized Parts | Common Applications |
---|---|---|
Engine Lathe | Quick-change gearbox, leadscrew | General-purpose machining |
Turret Lathe | Turret head, bar feeder | Mass production |
CNC Lathe | Servo motors, tool turret | High-precision machining |
Swiss-Type Lathe | Guide bushing, sliding headstock | Micro-component manufacturing |
Vertical Lathe | Vertical spindle, rotating table | Machining heavy workpieces |
Pipe Thread Lathe | Threading head, taper attachment | Oil and gas pipe threading |
Conclusion
Understanding the key parts of a lathe and their respective functions is essential for anyone working in the machining industry. From the lathe bed, which provides a solid foundation, to the headstock and tailstock, which maintain alignment and stability, every component plays a crucial role in ensuring precision, efficiency, and safety. The carriage and tool post enable smooth tool movement and accurate cuts, while the lead screw and feed rod facilitate controlled feed motion and threading operations.
Beyond the core components, the wide range of lathe accessories and attachments—such as faceplates, collets, mandrels, and taper attachments—further expands the machine’s capabilities, allowing for more complex and specialized operations. Additionally, various types of lathes such as engine lathes, CNC lathes, turret lathes, Swiss-type lathes, vertical lathes, and pipe thread lathes offer unique advantages for diverse machining applications.
By mastering the functions of these critical parts and utilizing appropriate accessories, machinists can optimize their lathe operations, ensuring high-precision machining, enhanced productivity, and extended machine lifespan. Whether performing simple turning tasks or complex multi-axis CNC operations, understanding how each part contributes to the machine’s overall performance empowers operators to achieve consistent, high-quality results.
As technology continues to advance, modern lathes equipped with safety features, control systems, and automation capabilities make machining safer, more efficient, and more precise than ever before. By maintaining and calibrating these critical components regularly, machinists can extend the life of their machines and ensure maximum performance.
In conclusion, a well-maintained lathe with a solid understanding of its parts and functions empowers operators to tackle a wide range of machining challenges while maintaining the highest standards of precision and efficiency. Whether you’re a seasoned machinist or a beginner learning the intricacies of lathe operations, mastering the essential parts and their functions is the key to unlocking the full potential of this versatile machine.