Are you struggling to decide between a lathe vs mill for your machining needs? Both lathes and milling machines have their own unique functions and uses. But do you know the exact differences between these two machines? Do you know how their differences impact your workpieces and productivity?
The lathe rotates the clamped workpiece and moves the turning tool toward it, making it ideal for machining rotary body shapes like cylinders, disc, cones, and threads. Milling machines, however, use rotating tools to remove material from workpiece. It is therefore ideal for processing complex geometries such as flat surfaces, grooves, curved surfaces, etc. The choice depends on your workpiece geometry and the precision required. Understanding the differences will help you confidently select the machine that fits your project’s needs.
If you’ve ever been torn between these two machining powerhouses, this guide will clarify their strengths, applications, and key differences to help you make the right choice. Keep reading to discover which machine , lathe vs mill, is best for your workshop.
What Is a Lathe Machine?
A lathe is a versatile and essential machine tool designed to shape workpieces by rotating them against a stationary turning tool (a type of cutting tool specifically used in lathe operations). The core principle of a lathe involves securing the workpiece onto the spindle, which rotates at a controlled speed, while the turning tool—mounted on a tool post—moves linearly along the workpiece’s axial (longitudinal) or radial (lateral) direction. This combination of rotary motion and precise feed control enables the lathe to create symmetrical shapes like cylinders, discs, cones, and threads with remarkable accuracy.
Lathes are widely used across industries for machining components with rotational symmetry, such as shafts, bushings, and flanges. Their adaptability to various materials, from metals to plastics, makes them indispensable for applications ranging from automotive manufacturing to aerospace engineering. When comparing a lathe vs mill, the lathe stands out for its specialization in producing high-precision, rotational parts efficiently.

Common Lathe Machine Types
Manual Lathes
Manual lathes are widely used for straightforward machining tasks, such as turning, facing, and threading. They are ideal for small-scale projects or repair work, commonly found in workshops and by hobbyists who value hands-on control. While not as advanced as CNC lathes, manual lathes are perfect for quick repairs or prototyping tasks where automation isn’t necessary.

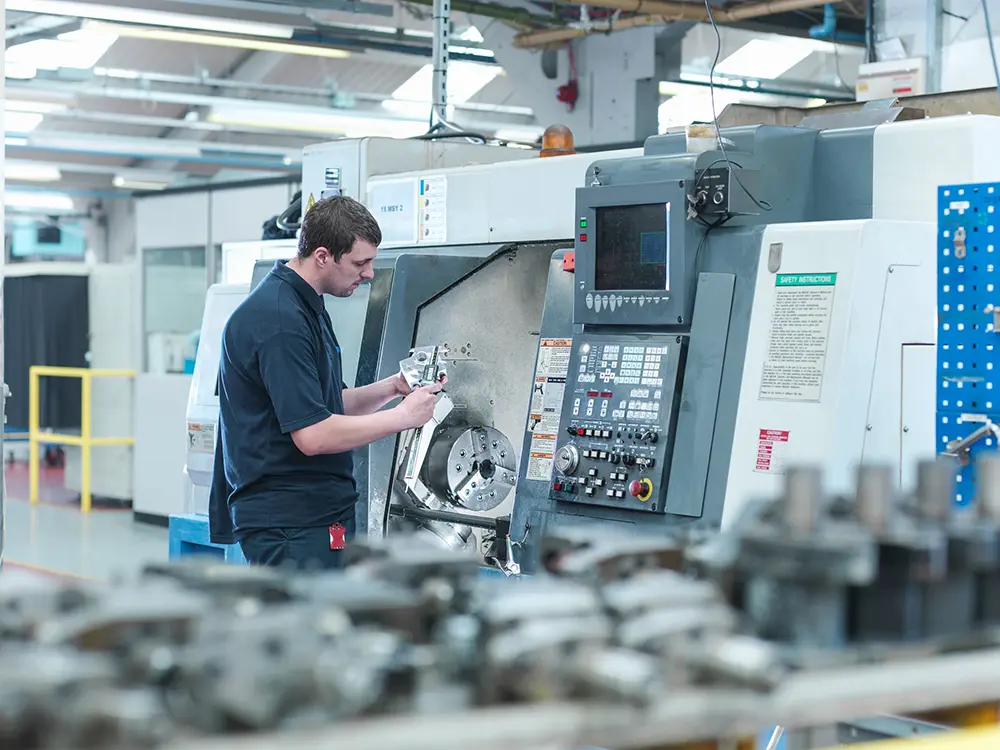
CNC Lathes
CNC lathes, controlled by computer programming, offer unmatched precision, automation, and repeatability. These machines are essential for high-volume production and excel at creating rotationally symmetrical parts such as precision shafts, flanges, and bushings. Industries such as automotive, mold manufacturing, and aerospace rely heavily on CNC lathes for their ability to produce components with micron-level accuracy while minimizing waste.
Swiss-Type Lathes
Swiss-type lathes are specially designed for machining small, intricate parts with extreme precision. Their sliding headstock allows the workpiece to be held close to the turning tool, reducing deflection and improving accuracy. These machines are indispensable in industries like medical device manufacturing (e.g., surgical tools, implants) and electronics (e.g., connectors, sensors).
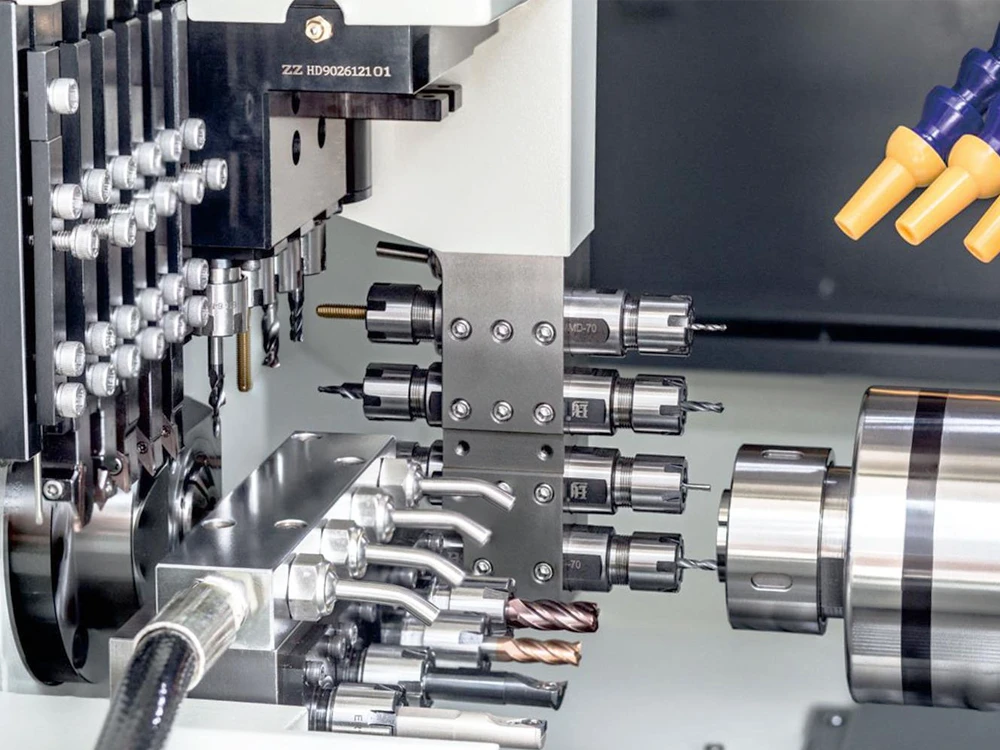
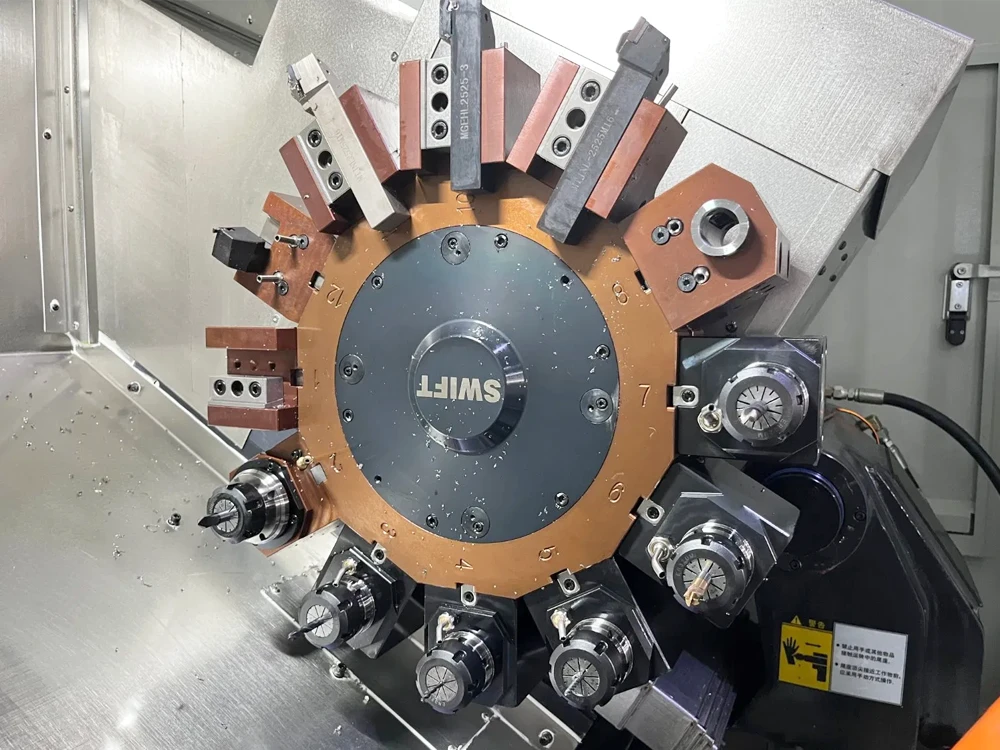
Turret Lathes
Turret lathes are equipped with multiple tool stations that enable quick tool changes during machining, making them ideal for repetitive production tasks. These lathes are frequently used for creating components such as bolts, screws, and flanges in batch production environments. Their efficiency and ability to minimize downtime make them a favorite in mass production industries.
Vertical Lathes
Vertical lathes feature a vertically oriented spindle, which provides excellent stability when machining large, heavy components. They are widely used in industries such as aerospace and energy for machining turbines, pressure vessels, and other oversized parts. The vertical orientation ensures that gravity helps secure the workpiece, allowing for precise cuts and intricate detailing on massive components.

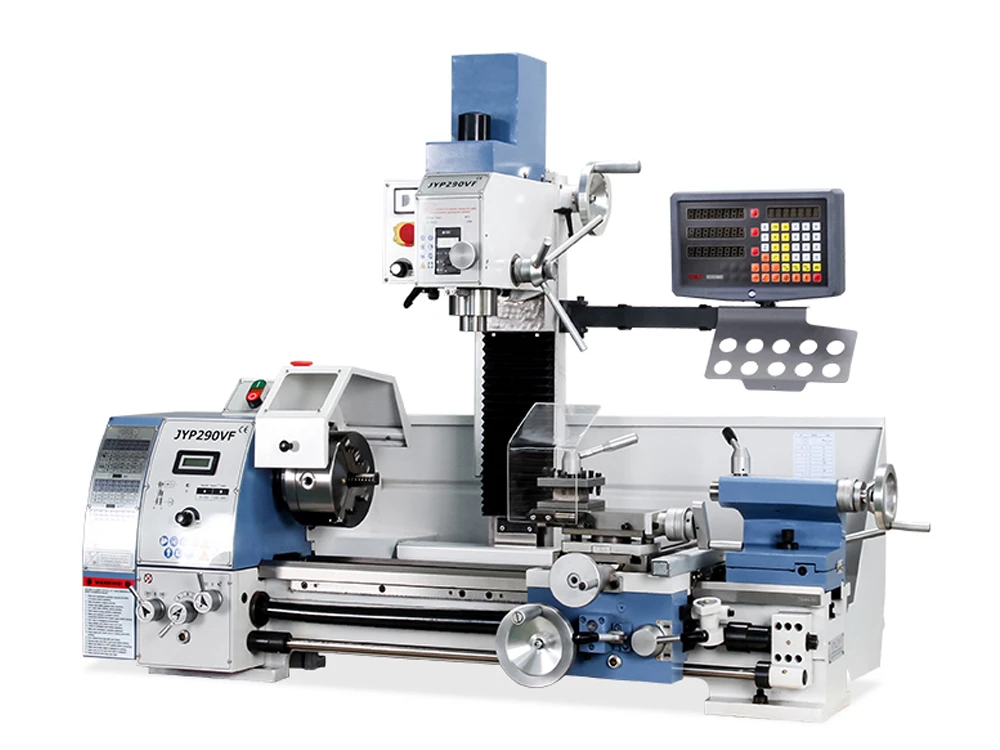
Multifunctional Lathes
Multifunctional LathesMultifunctional lathes combine turning with milling and drilling capabilities. Equipped with live tools, they allow for secondary operations such as keyway cutting, slotting, and hole drilling without removing the workpiece. This versatility makes them a popular choice for complex part production in industries like aerospace and automotive.
What Is a Milling Machine?
A milling machine is a versatile tool primarily used for milling, a process that involves removing material from a workpiece with a high-speed rotating cutting tool. Unlike a lathe, where the workpiece rotates, the milling machine’s cutting tool performs the rotational motion, while the workpiece remains stationary or moves along multiple axes.
Milling machines excel at performing milling operations to create flat surfaces, grooves, slots, curved surfaces, and even intricate geometries like mold cavities. In the milling process, the workpiece is typically clamped onto a movable worktable, which moves along the X, Y, and Z axes for precise cutting and shaping. This combination of rotary cutting and multi-axis movement makes milling machines ideal for producing highly detailed components.
In addition to milling cutters, a milling machine can replace and use a variety of processing tools, such as drills, boring bars, and tapping tools. This flexibility allows it to perform additional operations like drilling, boring, and tapping. These processes enable the machine to create holes, enlarge existing holes, and cut threads with precision and efficiency. This multifunctionality makes the milling machine a highly versatile tool, reducing the need for separate equipment in machining tasks and improving overall productivity.
Milling machines are available in different configurations, such as vertical and horizontal designs, each tailored to specific machining needs. They are widely used in industries like automotive, aerospace, and mold manufacturing due to their ability to handle non-rotational, complex geometries with precision. In the lathe vs mill comparison, milling machines stand out for their specialization in milling operations that create intricate shapes and surfaces.
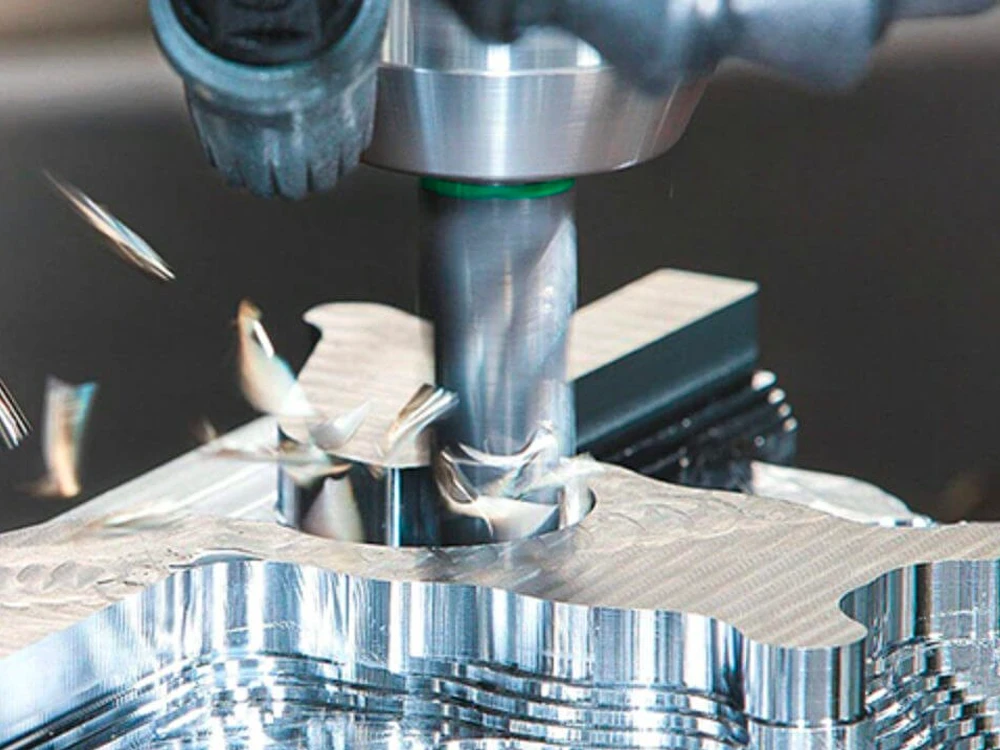
Common Milling Machine Types
Vertical Milling Machines
Vertical milling machines are among the most commonly used types in machining. With their vertically oriented spindle, they are perfect for precise tasks such as machining flat surfaces, creating slots, and shaping contours.They are widely used across industries such as mold manufacturing, automotive, aerospace, and general mechanical manufacturing for tasks ranging from prototyping to machining complex components. These machines are valued for their precision, flexibility, and ability to handle intricate jobs.


Horizontal Milling Machines
With a horizontally oriented spindle, horizontal milling machines excel at heavy-duty machining tasks like gear cutting and shaft production. They are perfect for large-scale operations requiring efficient material removal, as seen in automotive and heavy machinery industries. The horizontal setup allows for greater cutting force and versatility when machining larger workpieces.
Turret Milling Machines
Turret milling machines are compact and versatile, equipped with a turret for quick adjustments in spindle orientation. Perfect for smaller workshops, they excel at tasks like drilling, boring, and tapping without needing multiple setups. These machines are commonly used for short production runs and repair work.
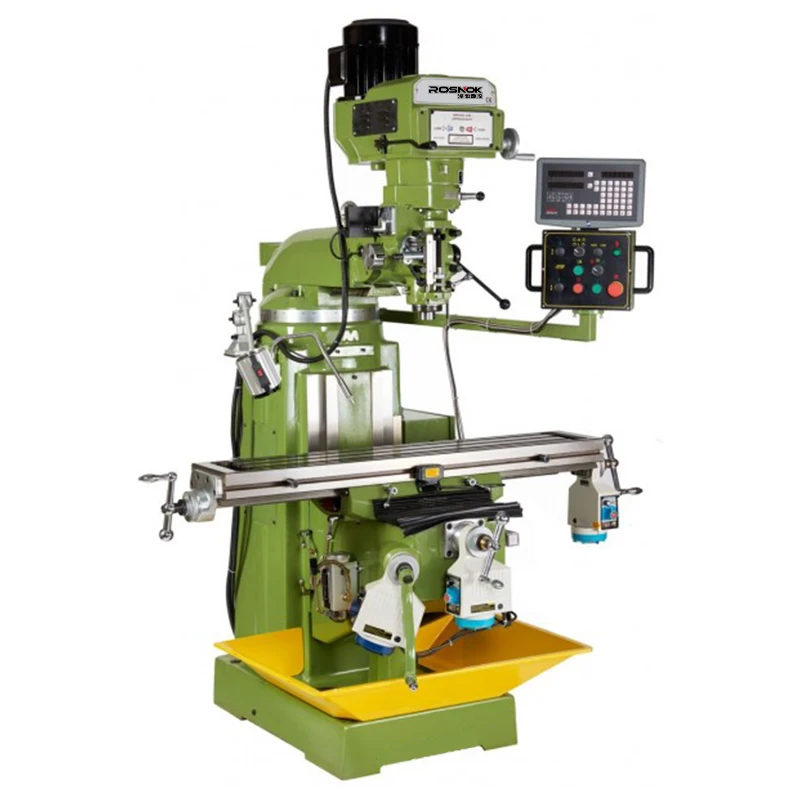

Universal Milling Machines
Universal milling machines combine vertical and horizontal milling capabilities in one system, providing unmatched versatility. Ideal for small workshops and job shops, these machines can handle both intricate and heavy-duty machining tasks without requiring multiple setups. They are often used in tooling, automotive, and aerospace industries.
CNC Milling Machines
CNC milling machines bring automation and precision to the forefront. These computer-controlled machines can perform intricate milling, drilling, and tapping tasks with multi-axis movement, making them indispensable in industries like aerospace, mold manufacturing, and automotive. Their efficiency and high production rates reduce errors and increase productivity.
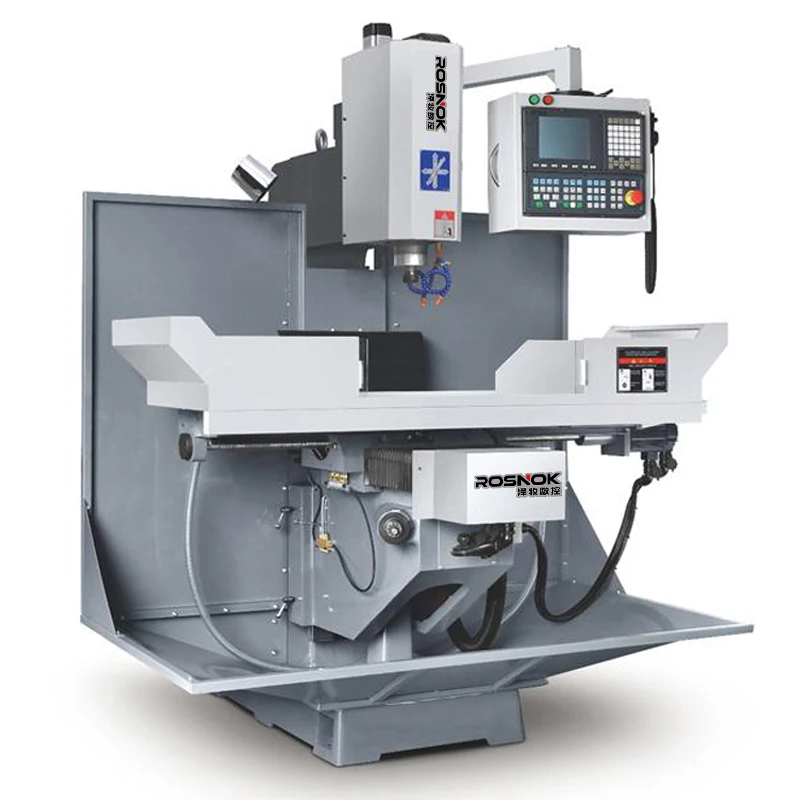

Machining Centers
A machining center is a type of CNC milling machine that combines multiple functions such as drilling, tapping, and milling within a single machine. Machining centers are highly automated, equipped with tool changers, multiple axes, and advanced software controls, allowing them to perform complex tasks without operator intervention. They are capable of operating continuously for extended periods and can be integrated into production lines for mass manufacturing.
Gantry Milling Machines
Gantry milling machines are designed for large-scale machining tasks, featuring a bridge-like structure for exceptional stability. These machines are ideal for machining oversized components like aerospace structures, ship parts, and heavy machinery. Their ability to handle large workpieces with high precision makes them essential in heavy-duty manufacturing.

Key Differences Between Lathe Machine and Milling Machine
When deciding between a lathe vs mill, understanding their key differences is critical for choosing the right tool for your machining needs. While both machines are essential in metalworking, their principles of operation, cutting tools, and application scenarios vary significantly.
1.Lathe vs mill: Machining Principles
Lathe: A lathe vs mill comparison starts with understanding their core functions. In a lathe and milling machine setup, the lathe processes workpieces by rotating the material while the cutting tool moves linearly. The workpiece is clamped on the spindle, which rotates at a constant speed to provide the main motion for machining. The cutting tool, mounted on a tool post, moves along the axial (longitudinal) or radial (lateral) direction of the workpiece. For example, when turning a cylinder, the tool removes material layer by layer as the workpiece rotates, making a lathe ideal for machining parts like cylinders, disc, cones, and threads.
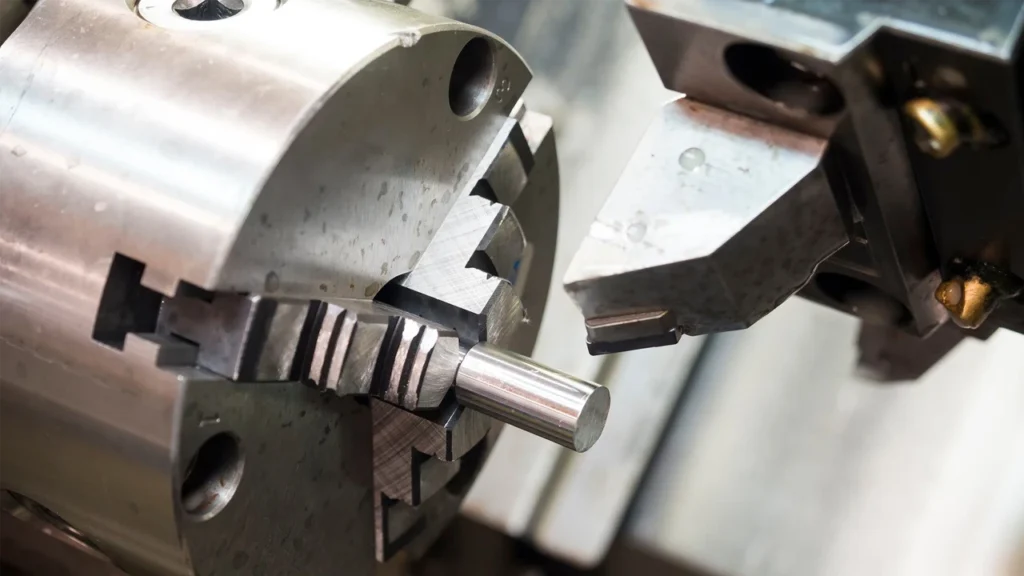
Milling Machine: When comparing a milling machine vs lathe, the primary difference lies in the movement of the tool and workpiece. A milling and lathe machine differ in how material is processed: a milling machine uses a high-speed rotating cutting tool to remove material from a stationary or movable workpiece. The workpiece is typically secured on a movable worktable, which shifts along the X, Y, and Z axes for precise positioning. This allows the mill and lathe combination to handle tasks like cutting flat surfaces, grooves, and intricate geometries. For example, milling a plane involves the rotating tool removing material layer by layer while the worktable moves the workpiece into position.

2.Lathe vs mill: Cutting Tools and Movement
Lathe Machining Tools:
In a lathe, the turning tool moves along either the axial or radial direction of the rotating workpiece. These tools are relatively simple compared to the rotating cutters of a milling machine, as their primary function is to carve out shapes such as cylinders, discs, cones, and threads by following the contour of the rotating material.

Milling Machining Tools:
In contrast, milling machines use a wide range of cutting tools, including end mills, face mills, drill bits, slot drills, chamfering tools, ball-nose cutters, thread mills, T-slot cutters, and fly cutters, to perform tasks like milling, drilling, and boring. This extensive variety of tools makes milling machines highly versatile for machining a range of shapes, from flat surfaces and grooves to intricate cavities and threads.
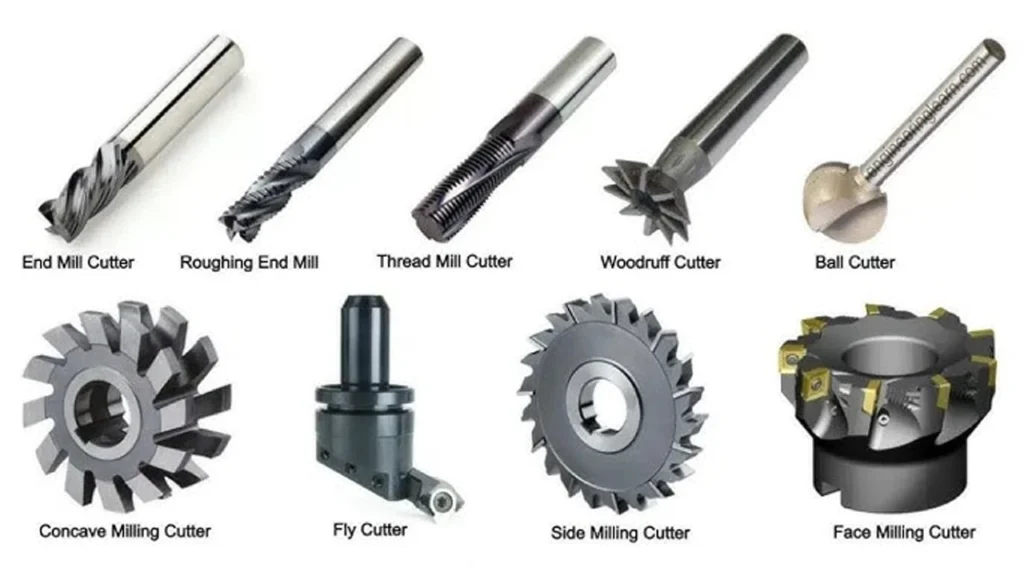
The lathe vs milling machine difference becomes apparent here: while lathes excel at producing rotational parts, milling machines are better suited for machining non-rotational or intricate geometries.
3.Lathe vs mill: Workpiece and Shape Capabilities
Lathe Workpieces:
Lathes are specialized for machining workpieces with rotational symmetry. Common parts include cylindrical shafts, cones, and even threads. Their focus is precision in controlling the dimensional accuracy of rotational parts.
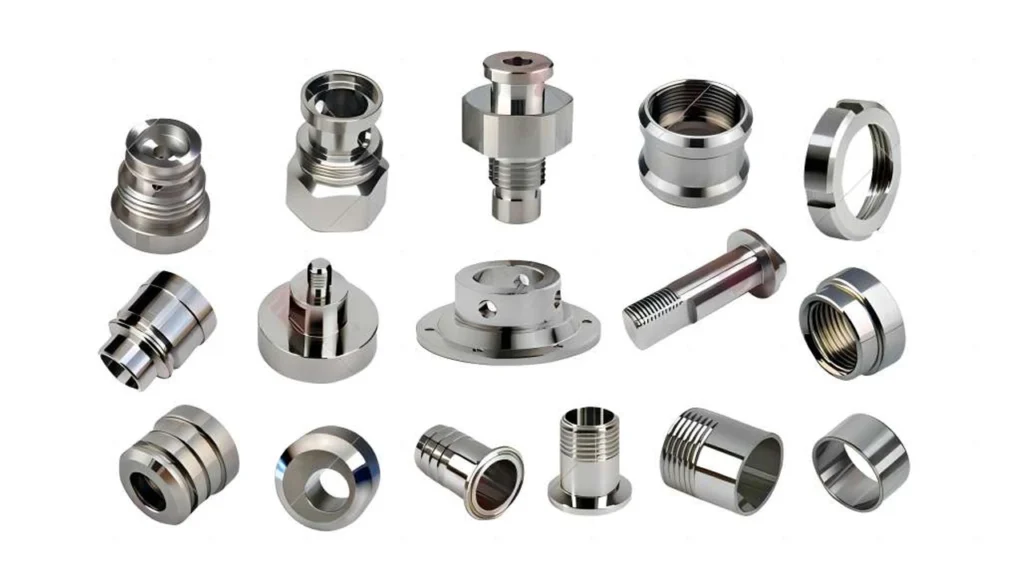
Milling Workpieces:
Milling machines shine when machining flat or irregularly shaped workpieces. Whether it’s cutting grooves in an engine block, shaping a mold cavity, or creating intricate patterns in a piece of metal, milling machines are far more flexible. This versatility is why industries like automotive part and mold manufacturing often rely on milling and turning processes for comprehensive machining.

4.Lathe vs mill: Automation and Precision
Modern CNC lathe and milling machines bring automation into the picture. CNC lathes are exceptional at producing repeatable cylindrical parts, while CNC milling machines offer multi-axis control for intricate designs. In the lathe vs milling machine debate, CNC mills excel at creating detailed parts with minimal human intervention, making them invaluable for industries like aerospace and medical device manufacturing.
When to Use a Lathe Machine
A lathe is your go-to machine for projects that require shaping cylindrical or rotationally symmetrical workpieces. Its ability to rotate the workpiece while the cutting tool moves along precise paths makes it ideal for machining components like shafts, bushings, and threads. The lathe vs mill comparison becomes clear when you need to produce rounded or tapered shapes efficiently.
Best Scenarios for Using a Lathe
- Turning Cylindrical Parts:
If your project involves machining round objects such as axles, pulleys, or rods, a lathe outperforms a mill. The lathe’s rotating spindle makes it the ideal choice for turning operations, where the cutting tool removes material layer by layer to achieve a smooth, precise surface. - Thread Cutting:
Lathes excel at creating external and internal threads on cylindrical components. Whether you’re producing screws, bolts, or specialized pipe threads for the oil & gas industry, the lathe’s thread-cutting capabilities ensure consistency and accuracy. For larger-scale threading projects, pipe thread lathes are specifically engineered to handle the unique requirements of threading pipes, such as precise tolerances and robust performance in high-pressure applications. - Facing Operations:
When you need to smooth the ends of a workpiece or reduce its length, a lathe is the perfect tool. This operation is commonly used in automotive manufacturing, for example, when machining components like brake discs. - Taper Turning and Contouring:
For parts requiring a taper or a specific contour, such as cones or curved surfaces, the lathe’s ability to move the cutting tool in radial or axial directions is unmatched. This makes it indispensable for aerospace applications like crafting shafts and landing gear components. - Machining Disc-Shaped Parts:
Lathes are particularly effective at machining disc-shaped components, such as flywheels, brake discs, and turbine rotors. The lathe’s rotational motion ensures precise material removal across the entire surface, making it ideal for achieving uniform thickness and smooth finishes. These operations are essential in industries like automotive and aerospace, where balance and precision are critical.
Material Considerations for Lathes
Lathes can handle a wide variety of materials, making them versatile for different industries. From soft plastics to hard metals like stainless steel and titanium, lathes are designed to maintain high precision regardless of the material. For example, Swiss-type CNC lathes are frequently used in medical device manufacturing to create highly accurate surgical tools and implants.
High-Volume Production
When deciding between a lathe vs mill, consider the efficiency of the lathe for high-volume production runs of rotationally symmetrical parts. CNC lathes, in particular, are well-suited for automated production of large quantities with minimal variation, reducing waste and improving efficiency. This is why industries like mechanical manufacturing and automotive heavily rely on lathes for consistent output.
Why Choose a Lathe?
In summary, a lathe is the ideal choice for applications that involve:
- Cylindrical and rotational parts like axles, shafts, and rods.
- Thread cutting for screws, bolts, and pipes.
- Facing operations to smooth or reduce the length of workpieces.
- Taper turning and contouring for cones, curved surfaces, and specialized shapes.
- High-volume production of symmetrical parts with minimal variation.
- Processing materials with rotational symmetry, including metals, plastics, and composites.
When comparing lathe vs mill advantages, the lathe’s efficiency in handling rotational parts and its precision make it indispensable in industries like automotive, oil & gas, aerospace, and general manufacturing. Its versatility and ability to maintain high accuracy across various materials ensure it remains a key tool for machining operations.
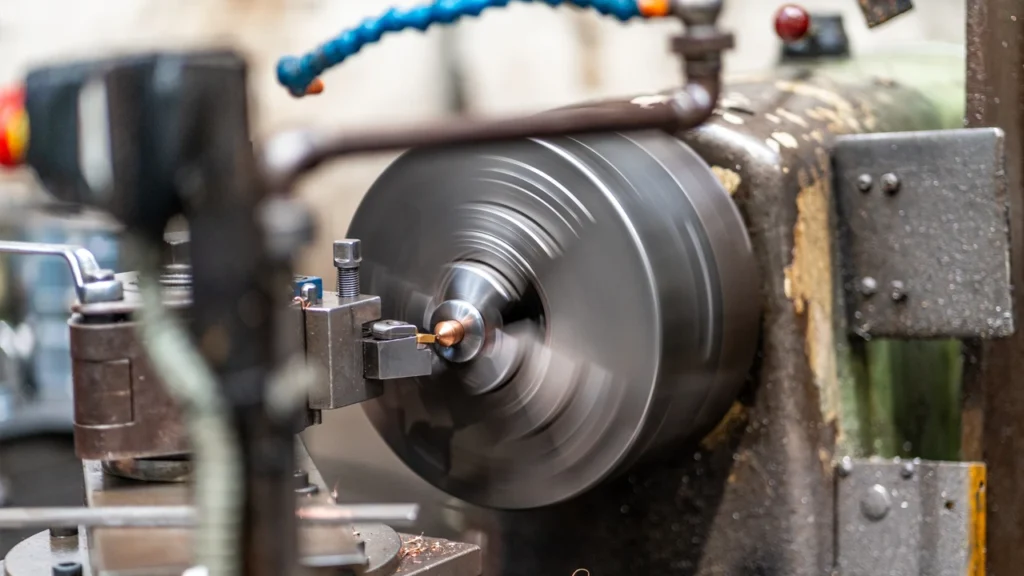
When to Use a Milling Machine
Milling machines are indispensable tools in machining applications where precision and complexity are paramount. If your project involves creating intricate geometries, flat surfaces, or detailed patterns that a lathe cannot handle, a milling machine is the superior choice. Below are specific scenarios where a milling machine outshines its counterpart in the lathe vs mill debate:
Best Scenarios for Using a Milling Machine
- Machining Flat Surfaces and Grooves:
Milling machines are the go-to option for machining flat surfaces and grooves. Tasks like milling slots, T-slots, and dovetail grooves are best performed with the high-speed rotating cutting tools of a milling machine. Unlike lathes, which are limited to cylindrical and rotational parts, mills excel in cutting precise edges and creating flat planes. For applications like mold manufacturing or machining electronic enclosures, a milling machine is indispensable. - Creating Complex Geometries:
Mills are designed for flexibility, allowing operators to produce complex shapes like cavities, channels, and contours. Industries such as aerospace and medical device manufacturing often require the detailed capabilities of a CNC milling machine to create turbine blades, implant molds, and other intricate parts. In the comparison of a lathe vs milling machine, the mill’s ability to handle multi-axis movements gives it a distinct advantage for such high-precision tasks. - High-Precision Hole Drilling:
If your project requires creating precise holes, such as for screws, bolts, or pins, a milling machine is the ideal solution. Mills equipped with advanced tools like center drills and reamers can achieve unparalleled accuracy in drilling, boring, and tapping operations. This capability is crucial in industries like automotive and aerospace, where alignment and tolerances must meet exact specifications. - Machining Non-Rotational Parts:
For workpieces that lack rotational symmetry—such as rectangular or irregularly shaped components—a milling machine is the preferred choice. The ability to move the worktable along the X, Y, and Z axes allows mills to produce intricate patterns, engravings, and surface textures on flat or irregular workpieces. This is particularly advantageous in the production of electronic circuit boards and custom tooling. - Multi-Surface Machining:
In applications where the workpiece has multiple sides or surfaces requiring machining, milling machines equipped with 4-axis or 5-axis CNC capabilities are unparalleled. These machines can machine several surfaces of a part in a single setup, significantly reducing production time and ensuring consistency. For example, creating a mold cavity with detailed features on multiple surfaces is far more efficient with a milling machine. - Prototyping and Custom Parts Production:
Milling machines are essential for prototyping and producing custom parts. In research and development or low-volume production environments, mills are versatile tools for crafting unique designs and validating concepts. Their ability to quickly switch between tools and configurations makes them ideal for creating complex prototypes.
Material Considerations for Milling Machines
Milling machines are renowned for their versatility in machining various materials. They handle softer materials like aluminum and brass effectively while also excelling at cutting harder materials such as stainless steel, titanium, and other high-strength alloys. For instance, CNC milling machines are crucial in industries like aerospace and automotive, where precision and durability are paramount. They are commonly used to machine components like aircraft structural parts and automotive engine blocks, where material quality is critical to performance.
High-Volume Production with Milling Machines
While lathes are suited for rotational parts, milling machines dominate the production of complex, non-rotational components. CNC milling machines, with their multi-axis capabilities, can automate intricate machining tasks, allowing for high-volume production with precision. Industries such as mold manufacturing and precision tooling depend on CNC milling machines for the consistent and efficient production of high-quality molds, die sets, and other intricate components. Their adaptability to complex shapes and configurations makes them indispensable for large-scale projects involving detailed geometries.
Why Choose a Milling Machine?
In summary, a milling machine stands out in applications requiring:
- Flat surfaces and grooves.
- Complex geometries and patterns.
- Precision hole drilling.
- Multi-surface machining.
- Non-rotational workpieces.
- Prototyping and custom part production.
When comparing lathe vs mill capabilities, the milling machine’s adaptability and precision make it a cornerstone in industries like automotive, aerospace, mold manufacturing, and electronics. Its ability to perform a wide range of tasks ensures efficient production while meeting the most demanding requirements.
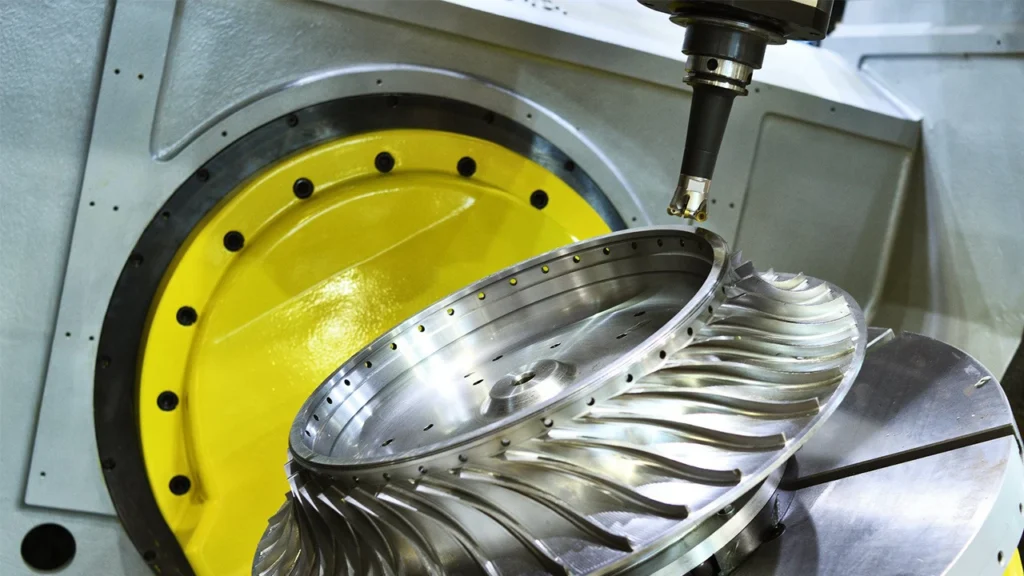
Choosing Between a Lathe vs Mill for Your Projects
When deciding between a lathe vs mill, it’s crucial to assess your project requirements, workpiece geometry, and production goals. Each machine brings unique strengths to the table, and understanding these can help you select the best tool for your machining tasks. Below are key factors to consider when choosing between a lathe and a mill for your projects:
Workpiece Geometry
- Lathe: If your project involves machining rotationally symmetrical parts, such as shafts, rods, or cones, a lathe and milling machine combination might initially seem viable. However, the lathe vs milling machine difference becomes evident here: a lathe outperforms a mill in crafting precision cylindrical parts like threads and axles.
- Mill: For non-rotational components or intricate geometries, such as molds, grooves, or flat surfaces, a mill and lathe machine work together. However, the milling machine shines due to its multi-axis capabilities, making it ideal for difference between lathe and milling machine applications like mold-making and engraving.
Precision Requirements
- Lathe: The lathe and mill duo often starts with the lathe when rotational symmetry is critical, followed by a mill for finer details.
- Mill: For precision holes and intricate geometries, the cnc lathe and milling machine combination comes into play. However, mills and lathes show clear distinction here: mills handle multi-surface details far more effectively.

Production Volume
- Lathe: For high-volume runs, the difference between a mill and a lathe becomes apparent. CNC lathes efficiently handle repetitive tasks involving shafts or bolts, offering consistency across large quantities.
- Mill: For complex parts, CNC mills dominate with their multi-tasking ability. In mill vs lathe vs CNC comparisons, mills often win for small-batch but intricate production runs.
Machine Versatility
- Lathe: While primarily used for turning operations, multifunctional lathes equipped with live tools can handle secondary operations like drilling and slotting, providing a degree of versatility within rotational machining.
- Mill: Milling machines outshine lathes in terms of adaptability. They can handle a broader range of tasks, from flat surface machining to engraving intricate details, making them ideal for projects requiring diverse shapes and operations.
Operator Skill Level
- Lathe: Traditional manual lathes demand a high degree of skill to achieve consistent results. However, CNC lathes simplify operations, making them more accessible for novice operators in a production environment.
- Mill: Milling machines, especially those equipped with multi-axis capabilities, require knowledge of advanced programming and setup. They are better suited for operators experienced in CNC systems.

Budget and Cost Efficiency
- Lathe: A lathe can be a more budget-friendly investment, especially for businesses focused on rotational part production. Their simpler setup often results in lower maintenance and operational costs.
- Mill: Milling machines are more expensive but provide greater value for projects demanding versatility and precision. The initial cost may be higher, but the machine’s ability to handle a variety of tasks can justify the investment for diverse manufacturing needs.
When weighing the lathe and milling difference, let the specifics of your project guide your choice. The cnc mill vs cnc lathe debate often narrows down to workpiece geometry and production needs. Lathes excel at high-speed, high-volume rotational parts, while mills master non-rotational and detailed geometries. Both tools are essential in machining, and understanding their difference between cnc lathe and cnc milling helps in optimizing production.
Cost and Maintenance Considerations for Lathe vs Mill
When deciding between a lathe vs mill, understanding cost and maintenance factors is critical to optimizing your investment and long-term efficiency. Both machines come with distinct cost structures, maintenance requirements, and overall lifetime value, influencing your decision based on your operational priorities.
Initial Costs: Lathe vs Mill
Lathes generally have a lower initial cost compared to milling machines, particularly for manual models. This makes them an economical choice for small workshops or industries focusing primarily on rotational parts. For example, a manual lathe can cost significantly less than a CNC mill while still delivering excellent performance for cylindrical machining tasks.
Conversely, milling machines—especially CNC models—tend to have a higher upfront cost due to their complex construction and multi-axis capabilities. This is particularly true for universal milling machines or 5-axis CNC mills, which offer unmatched flexibility for creating complex geometries. However, this higher cost is often justified by their versatility and productivity in industries such as aerospace and automotive.
Operational Costs: Lathe vs Mill
When comparing operational costs between lathes and mills, consider power consumption, tool wear, and setup time. Lathes typically consume less power, particularly during simple turning operations, which can result in lower utility expenses over time. On the other hand, mills, with their high-speed cutting tools and multi-axis movements, may incur higher energy costs but compensate by reducing machining time for complex parts.
Tool wear is another key consideration. Lathe tools, such as turning inserts, tend to have a longer lifespan when machining softer materials like aluminum or plastics. Meanwhile, milling cutters, including end mills and face mills, may require more frequent replacement due to their intensive engagement with harder materials and intricate cuts.
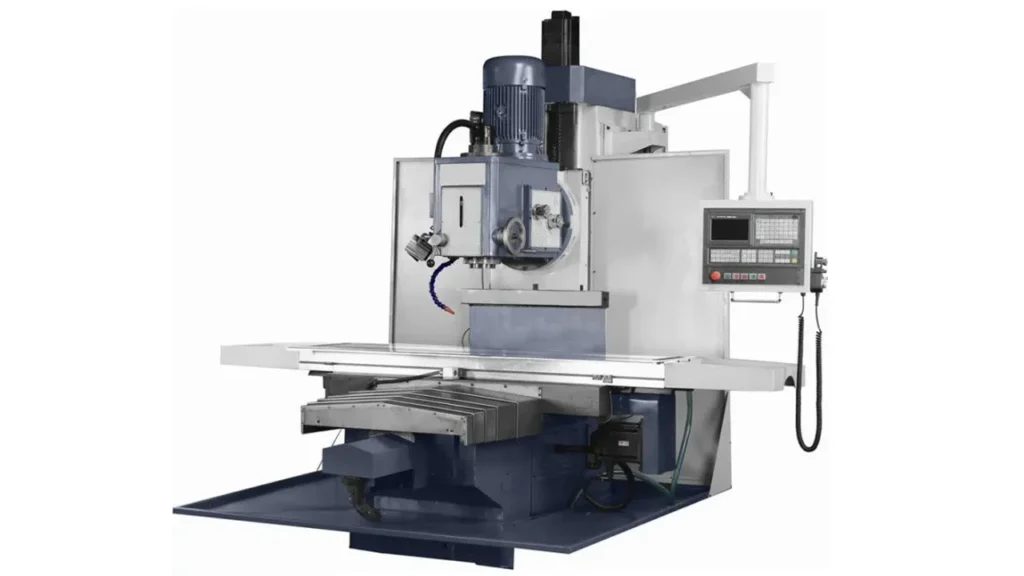
Maintenance Requirements: Lathe vs Mill
Maintenance considerations are equally important in the lathe vs milling machine debate. Lathes, with their simpler construction, are easier and less expensive to maintain. Routine maintenance for a lathe typically includes lubricating guideways, cleaning the spindle, and checking the alignment of the chuck and tailstock.
Milling machines, due to their intricate design and multi-axis capabilities, demand more comprehensive maintenance. Tasks such as spindle alignment, tool changer calibration, and periodic software updates for CNC systems are essential to ensure consistent performance. Neglecting maintenance on a CNC milling machine can lead to inaccuracies in machining non-rotational parts, impacting production quality.
Cost vs Value: Lathe vs Mill
While lathes are cost-effective for projects centered around rotational shapes such as shafts, bushings, or flanges, milling machines justify their higher cost by delivering unparalleled versatility and precision. If your operation involves producing both rotational and non-rotational components, investing in both a lathe and milling machine might be the most practical approach.
Longevity and ROI: Lathe vs Mill
Both lathes and mills, when properly maintained, can last decades, ensuring a strong return on investment (ROI). However, the complexity of your production needs will dictate which machine offers better value. For small-scale workshops, the simplicity of a lathe might suffice, whereas high-volume industries that require detailed parts will find a CNC mill indispensable.
By balancing initial costs, operational expenses, and maintenance requirements, you can make a well-informed decision between a lathe vs mill, ensuring that your investment aligns with your production goals and budget.
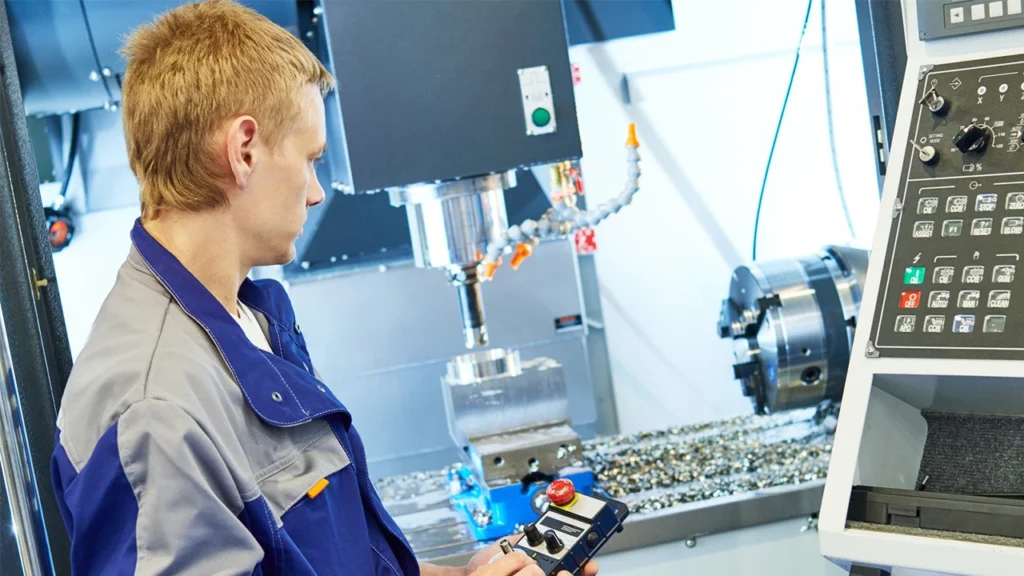
Applications of Lathe vs Mill in Different Industries
The lathe vs mill debate often hinges on their distinct applications across various industries. Each machine offers unique strengths, catering to specific machining needs. Let’s explore how lathes and mills are used in different industries.
Automotive Industry: Lathe vs Mill
- Lathes: Lathes are indispensable for machining rotational parts in automotive manufacturing. Components like crankshafts, pistons, and hub assemblies rely on the lathe’s ability to create precise, symmetrical shapes. CNC lathes are particularly valuable for high-volume production of standardized parts, ensuring efficiency and consistency.
- Mills: Milling machines are commonly used in the automotive sector for machining engine blocks, transmission housings, and intricate gear components. Their ability to handle complex geometries and multiple surfaces makes them ideal for crafting non-rotational parts with precision.

Aerospace Industry: Lathe vs Mill
- Lathes: The aerospace industry leverages lathes for producing cylindrical parts like turbine shafts, landing gear components, and engine casings. Their precision in controlling rotational symmetry is critical for components that must endure extreme stress and high-speed operations.
- Mills: CNC milling machines are the go-to choice for machining complex parts such as turbine blades, aircraft panels, and fuselage components. With multi-axis capabilities, they can produce intricate, lightweight structures that meet stringent industry standards.

Oil & Gas Industry: Lathe vs Mill
- Lathes: Lathes play a pivotal role in threading pipes and couplings, ensuring tight tolerances required for high-pressure applications. Pipe thread lathes, in particular, are engineered to handle the unique demands of this sector, providing robust solutions for pipeline construction and maintenance.
- Mills: Milling machines are used to create components like valve bodies, flanges, and pump housings. Their ability to handle hard materials and precise dimensions ensures reliability in harsh environments.
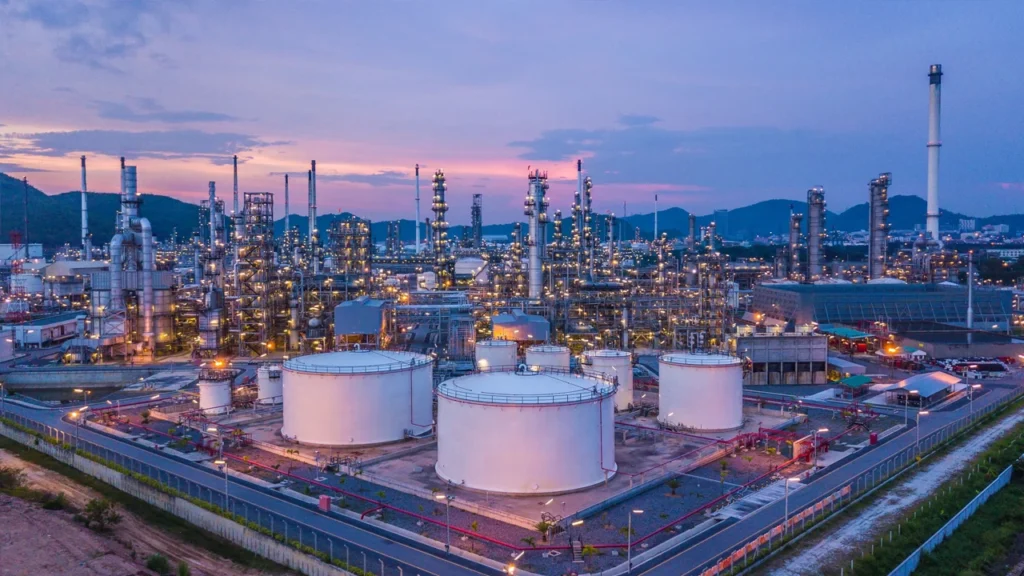
Electronics Industry: Lathe vs Mill
- Lathes: While not as commonly used in the electronics industry, lathes are sometimes employed for creating small, rotational components like connectors and pins. Swiss-type CNC lathes excel in this domain, delivering exceptional accuracy for intricate parts.
- Mills: Milling machines dominate in electronics manufacturing for machining circuit board enclosures, heat sinks, and other non-rotational components. Their precision ensures compatibility with tight design specifications.

Medical Device Manufacturing: Lathe vs Mill
- Lathes: The production of medical implants and surgical instruments often requires the precision of Swiss-type CNC lathes. These machines are adept at crafting small, intricate components like screws, bone pins, and dental implants.
- Mills: Milling machines are vital for producing molds for medical devices, custom prosthetics, and components with complex geometries. The ability to machine multiple surfaces in a single setup ensures efficiency and high precision.

General Manufacturing: Lathe vs Mill
- Lathes: In general manufacturing, lathes are widely used for creating shafts, rollers, and other rotational parts. Their adaptability to various materials and applications makes them a staple in workshops worldwide.
- Mills: Milling machines are favored for tasks like keyway cutting, die production, and machining flat or irregular surfaces. Their versatility makes them invaluable for creating a diverse range of components.
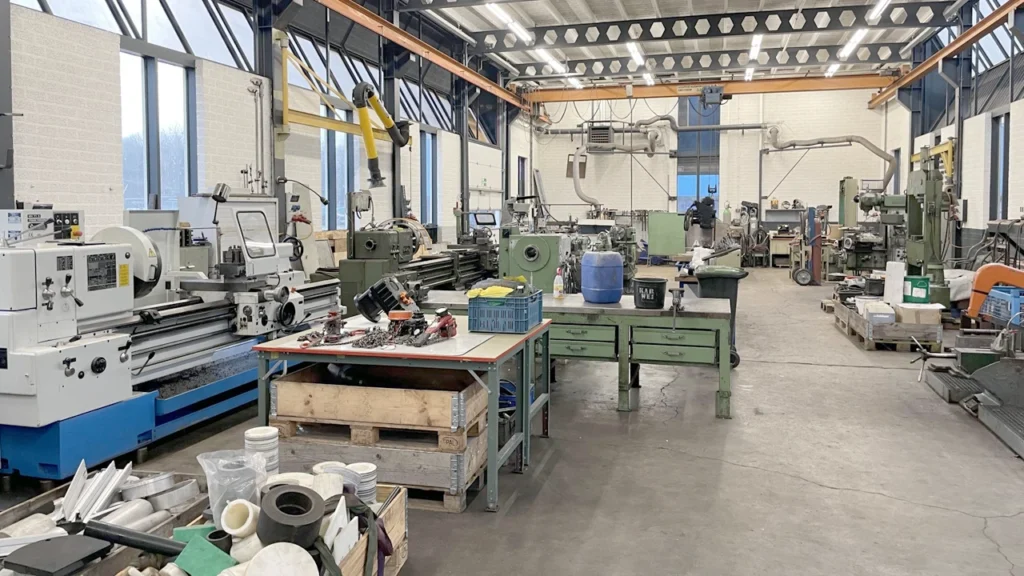
Industry-Specific Advantages of Lathes and Mills
The choice between a lathe vs mill often depends on the specific requirements of an industry. Lathes shine in machining rotational parts, providing high precision and efficiency for cylindrical shapes. Conversely, milling machines excel in handling non-rotational components, offering flexibility and precision for intricate geometries and multi-surface machining.
Industries like automotive, aerospace, and medical device manufacturing rely on these machines not only for their core functions but also for their ability to adapt to evolving technological needs. By understanding the strengths of each machine, businesses can optimize their production processes and achieve superior results.
Lathe vs Mill: Conclusion
Choosing between a lathe vs mill depends heavily on the nature of your projects and machining needs. Both machines have distinct strengths that make them indispensable in metalworking and manufacturing. While lathes specialize in creating precise cylindrical parts like shafts, cones, and threads, mills excel in producing intricate geometries, flat surfaces, and multi-sided components.
For high-volume production of rotational symmetry parts, Lathes excel in offering efficiency and precision. Conversely, if your focus is on creating non-rotational components or prototypes with detailed geometries, a milling machine is an excellent choice. Industries such as automotive, aerospace, mold manufacturing, and electronics often rely on both machines to achieve comprehensive machining solutions.
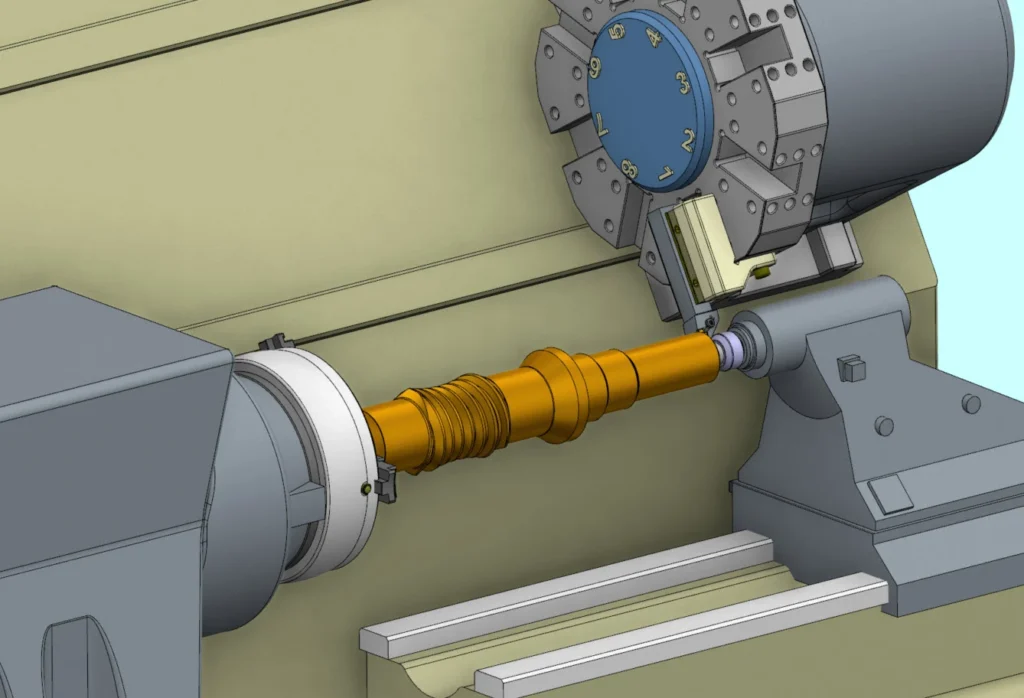
Ultimately, understanding the differences between lathes and mills ensures informed decision-making. Consider your project requirements—precision, material, shape, and production volume—and weigh them against the capabilities of each machine. The right choice not only enhances productivity but also optimizes costs and reduces downtime.
By mastering the use of these versatile machines, you can handle a wide range of machining challenges, from crafting high-precision rotational parts on a lathe to producing intricate designs with a milling machine. When in doubt, integrating CNC lathes and mills into your workshop can provide the flexibility needed for complex projects and scalable production.
Whether you’re a manufacturer or a machining enthusiast, knowing when to use a lathe vs mill will help you maximize efficiency and output quality.
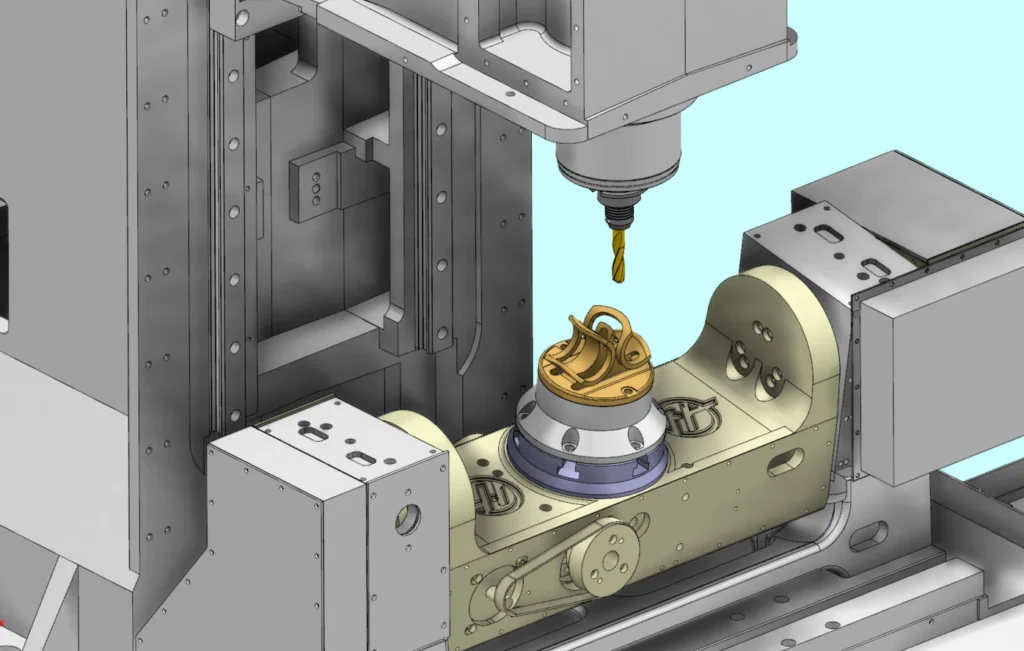
Popular Brands and Models of Lathe and Milling Machine
When investing in high-quality machinery, understanding the top brands and their standout models is crucial for optimizing your machining operations. Below are some renowned manufacturers and models for both lathes and milling machines, tailored to meet various industry requirements.
Top Lathe Brands and Models
- Mazak
Known for innovative CNC lathe technology, Mazak offers robust solutions like the QUICK TURN Series. These machines are ideal for high-speed production and complex turning operations. - Haas
Haas provides versatile CNC lathes, including the ST Series, suitable for machining intricate rotational parts with precision. Their affordability and durability make them a favorite for small to mid-sized manufacturers. - DMG Mori
The NLX Series by DMG Mori combines precision and reliability, catering to industries like aerospace and automotive that demand high tolerance and repeatability. - Okuma
The GENOS L Series from Okuma provides a perfect balance of cost-efficiency and advanced features, particularly for businesses aiming to improve ROI in high-volume production. - Rosnok
Rosnok CNC lathes deliver exceptional precision and adaptability, making them ideal for machining everything from small rotational components to large industrial parts. Backed by industry certifications like CE and ISO, our machines are trusted by industries worldwide for their high performance and cost-effectiveness.
Top Milling Machine Brands and Models
- Bridgeport
The Bridgeport VMCs are iconic in the vertical milling segment, known for their reliability in prototyping and small-batch production. - DMG Mori
Their DMU Series excels in 5-axis machining, enabling the creation of complex geometries for mold-making and aerospace applications. - Makino
The F Series by Makino focuses on high-precision milling, catering to industries requiring intricate details, such as medical devices and electronics. - Haas
Haas milling machines, including the VF Series, are renowned for their affordability and ability to handle both small-scale and large-scale machining operations. - Rosnok
Rosnok milling machines combine versatility with unmatched precision, perfect for industries like automotive, aerospace, and mold manufacturing. With customizable multi-axis systems and advanced precision engineering, Rosnok offers reliable solutions for both high-volume and intricate machining tasks.
Rosnok: Your Trusted Machine Tool Partner
At Rosnok, we pride ourselves on delivering CNC solutions tailored to meet the diverse needs of our customers. From precision lathes for small, intricate components to versatile milling machines capable of handling complex geometries, our machines are engineered to excel across a wide spectrum of applications.
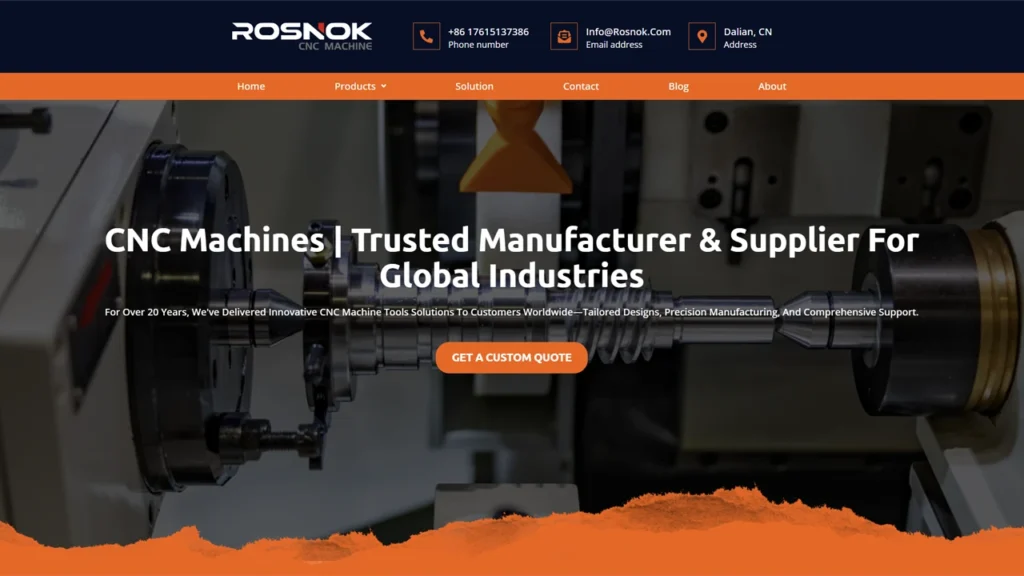
Whether you’re in automotive, aerospace, medical manufacturing, or general machining, Rosnok offers machines that deliver precision, reliability, and efficiency. With advanced features, robust performance, and responsive after-sales support, we’re committed to helping you achieve your machining goals, no matter the scale or complexity of your project.
Explore Rosnok’s product lineup and discover how we can power your production lines to success.
FAQ
Can a milling machine cut threads?
Yes. A milling machine can cut threads using a thread milling cutter or a tapping tool. However, a lathe machine is more efficient and precise for cutting external and internal threads.
Is a lathe machine suitable for machining complex parts?
No. A lathe machine is mainly used for simple round parts. Complex parts with multiple faces, cavities, or irregular profiles require a milling machine or a machining center.
Is there one machine that can perform both lathe and milling functions?
Yes. A multi-tasking CNC machine or mill-turn machine can perform both turning and milling operations. It helps reduce setups and improves production efficiency.