Are China machine tools truly reliable? Why are more global manufacturers switching from European and Japanese brands to Chinese CNC machines? Is it just low cost, or is there true innovation, reliability, and precision behind it? Can Chinese CNC machines truly meet the demands of critical, high-performance production?
Today’s China machine tool technology has transformed dramatically. Chinese CNC machines are not only affordable but offer world-class precision, robust build quality, and cutting-edge automation. Industries worldwide now trust these machines for mission-critical operations thanks to their rapid advancement, international certifications, and full-spectrum support systems. Whether you’re seeking cost-efficiency or high-end accuracy, Chinese CNC tools deliver measurable results.
Continue reading this article to discover why China machine tool products have become the trusted choice in global industries—and how Chinese CNC machines can elevate your production to a new standard.
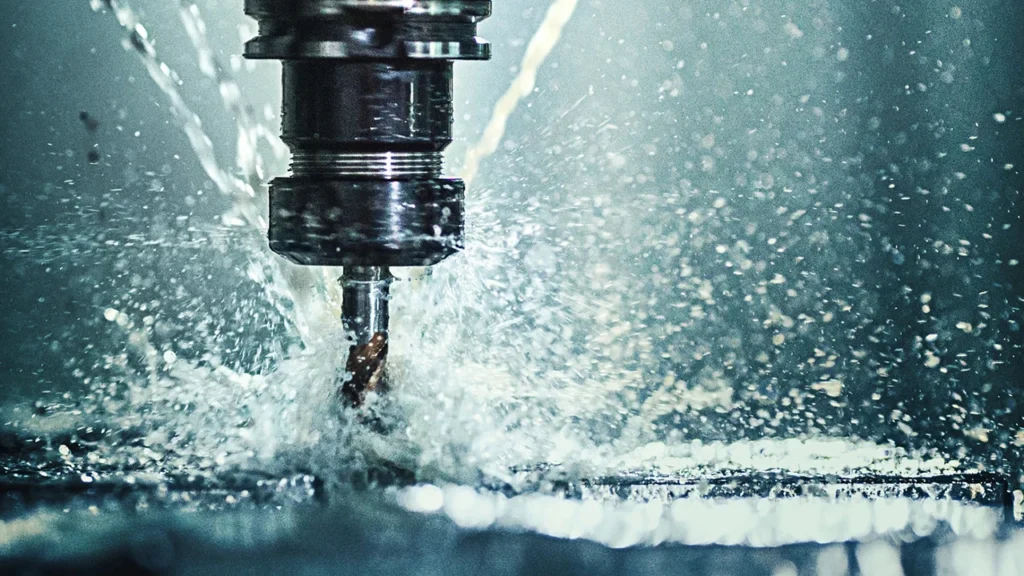
What Is a “China Machine Tool” Today?
In the past, the term “China machine tool” often conjured images of inexpensive equipment with limited precision and questionable reliability. But that perception has shifted. In recent years, Chinese machine tools—especially CNC machines—have made remarkable strides in both build quality and machining accuracy.
While top-tier machine tools from countries like Germany and Japan still dominate the high-end segment, China machine tools have evolved into a trusted solution for global manufacturers seeking dependable performance with better cost-efficiency. Today, they are no longer just an alternative for small workshops—they are actively being adopted across industries such as automotive, aerospace, energy, and medical manufacturing.
This transformation didn’t happen overnight. It is the result of decades of industrial upgrading, investment in advanced technologies, and a growing emphasis on international quality standards. With enhanced precision, automation compatibility, and production flexibility, china machine tools are now a viable and valuable choice for medium to high-level production requirements around the world.
Core Types of China Machine Tools
Today, machine tools manufactured in China cover a broad spectrum of metalworking equipment designed to meet the needs of modern industrial production.These machines are no longer limited to basic tasks—they now offer enhanced precision, higher speeds, and better durability to support medium to high-volume production.
The most common categories include:
- Lathe Machines: Essential for turning operations, these machines are widely used to produce cylindrical parts such as shafts, rings, and flanges. Chinese lathes today support both manual and CNC control, with improved rigidity and tooling options for consistent, accurate machining.
- Milling Machines: Used for cutting flat surfaces, slots, gears, and complex profiles, milling machines from China have become more stable and versatile, offering multi-axis options and automated feed systems suitable for general machining workshops and precision fabrication plants.
- Machining Centers: These are advanced systems that integrate multiple operations—milling, drilling, tapping—into a single platform. Chinese machining centers often feature automatic tool changers and CNC controls, enabling efficient one-stop machining for parts with high tolerance requirements.
- Drilling Machines: Suitable for mass production of holes, Chinese drilling machines now offer better spindle alignment, feed accuracy, and optional digital readouts for improved performance in metal fabrication and component assembly lines.
- Grinding Machines: Used to achieve fine surface finishes and precise dimensions, these machines have evolved with better vibration control, higher spindle speeds, and enhanced wheel balancing systems—supporting applications from mold finishing to high-precision shaft polishing.
- Boring Machines: Designed for internal diameter machining and precise enlargement of existing holes, boring machines in China now offer better feed control, stronger structural stability, and CNC-enabled boring heads for applications such as engine blocks and large industrial housings.
Together, these machines form the foundation of the china machine tool industry, supporting a wide array of production needs across sectors such as automotive, aerospace, energy, and heavy equipment.
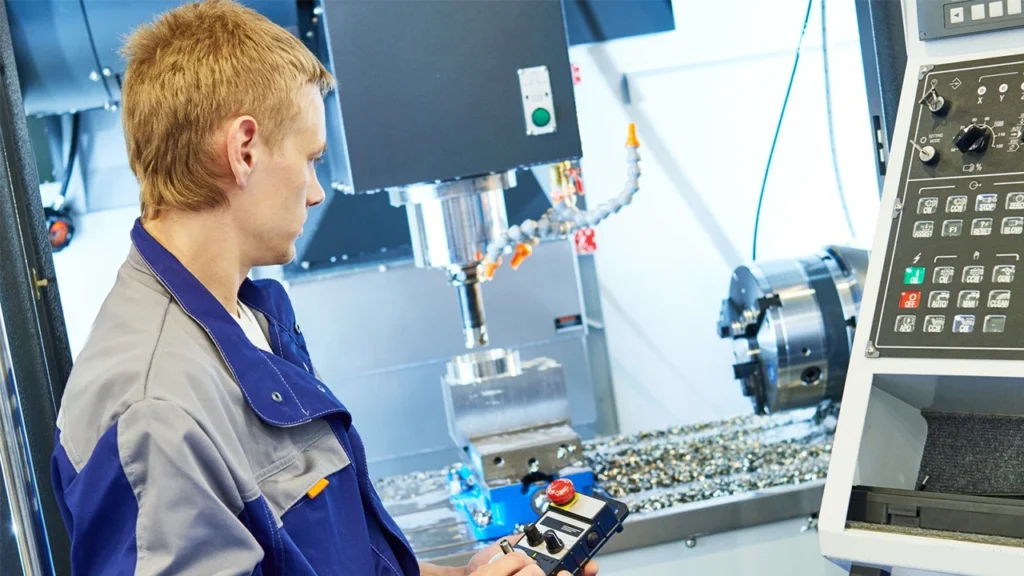
From “Made in China” to “Created in China”
The evolution of china machine tool manufacturing is best described as a shift from assembly-based production to independent innovation. In the early 2000s, most CNC machines in China were developed through imitation or basic integration of imported components. Today, many Chinese manufacturers have established their own R&D systems, CNC controller platforms, and smart production lines.
This transition has been driven by several key factors:
- Adoption of precision-grade components, such as high-speed spindles, ball screws, and servo systems from Japan and Taiwan
- Integration of globally compatible CNC controllers, including Siemens, FANUC, and increasingly capable domestic alternatives
- Development of automation-ready machine structures, supporting robotic arms, multi-station fixtures, and digital tool management
- Achievement of international certifications like CE, ISO 9001, and UL, enabling Chinese machines to access regulated markets in Europe, North America, and Southeast Asia
While Chinese machine tools are not positioned to replace the most advanced systems at the top of the industry, they have earned a reputation for being dependable, flexible, and cost-effective. In many real-world applications, they offer one of the best returns on investment available today.
The Development Journey of China Machine Tools
Over the last two decades, the development of china machine tools has been nothing short of transformative. Once viewed primarily as low-cost alternatives for basic operations, Chinese machines have steadily evolved into credible solutions for precision manufacturing. Today, while Germany and Japan continue to lead in the ultra-high-end segment, China has carved out a strong and growing position in the mid-to-high performance range—particularly where value, scalability, and technical dependability are crucial.
This progress hasn’t come overnight. It reflects a deliberate, multi-phase journey supported by national strategy, technology partnerships, and the maturing of a vast domestic supply chain. Understanding this evolution helps explain why more global manufacturers are now willing to invest in china cnc machines for demanding industrial applications.
The 2000s: Entry-Level Machines
In the early 2000s, china machine tools were typically built using foreign blueprints and imported components. Their role was largely to serve low-cost, low-complexity production. Accuracy, software integration, and stability were limited, but these machines met the needs of small workshops and developing markets looking for affordable equipment.
While lacking advanced capabilities, this generation laid the industrial foundation for what would become a decade of technical growth and market feedback.
The 2010s: Technology Acceleration
The 2010s marked a period of rapid advancement. National programs like “Made in China 2025” provided strong policy and financial support to upgrade industrial capabilities. Manufacturers began localizing core components, developing in-house software teams, and integrating higher-spec controllers from partners in Germany and Japan.
This was also the decade where Chinese CNC machines entered mainstream applications—no longer just for simple turning or drilling, but also for semi-complex parts in automotive, die casting, and general industrial systems.
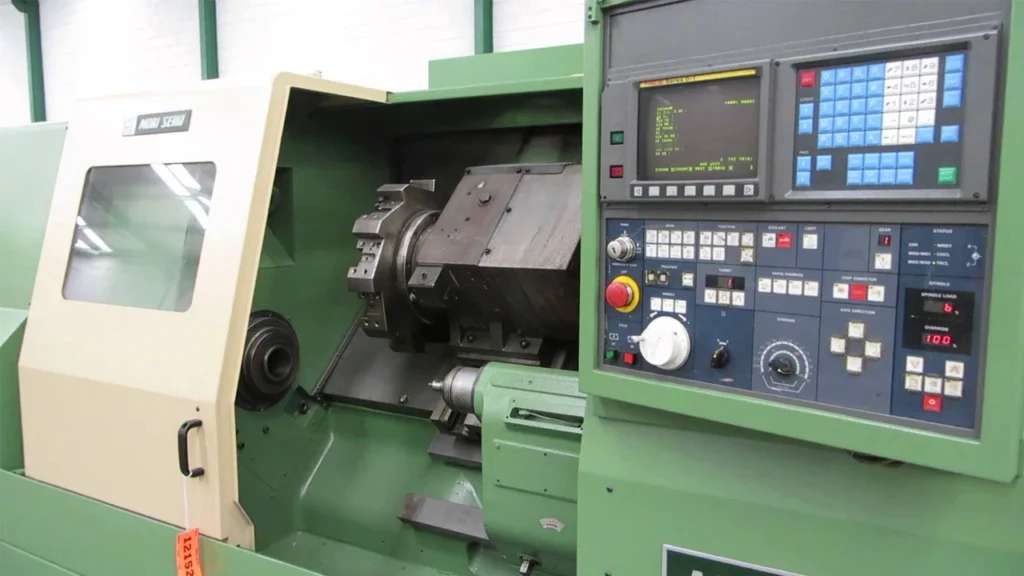
The 2020s: Global Precision Competitor
By the 2020s, the combination of refined design, localized supply chains, and better automation infrastructure allowed china machine tools to earn their place in global factories. Though still behind in some high-end precision or five-axis machining segments, Chinese machines are now widely recognized as dependable tools for medium-complexity, mid-to-high volume production.
Today, buyers in South America, Southeast Asia, Eastern Europe, and even parts of Western Europe view Chinese CNC systems as serious contenders—not just for their cost advantage, but for their improved performance, serviceability, and integration capabilities.
Why Global Buyers Trust China Machine Tool Products
As the global demand for cost-effective yet reliable machining solutions continues to grow, china machine tool products are earning increasing trust from international buyers. No longer seen as low-end or temporary alternatives, today’s Chinese CNC machines are actively chosen by manufacturers in various industries for their balanced combination of performance, value, and support.
This shift in perception is not based on marketing—it’s the result of continuous improvements in engineering, stronger service networks, and proven field performance across diverse production environments.
Technological Improvements Earn Respect
In the past, concerns around precision, long-term stability, and software integration often limited the use of china cnc machine products in high-demand applications. However, recent advancements have significantly changed this.
Modern Chinese CNC machines now feature:
- Improved structural rigidity
- Higher-quality spindles and ball screws
- Support for advanced control platforms (e.g., FANUC, Siemens, domestic equivalents)
- Add-ons such as auto tool changers, smart cooling systems, and thermal compensation
These improvements enable Chinese machines to meet tighter tolerances and support automated production—making them viable for complex machining tasks in industries such as automotive, medical devices, and industrial machinery.
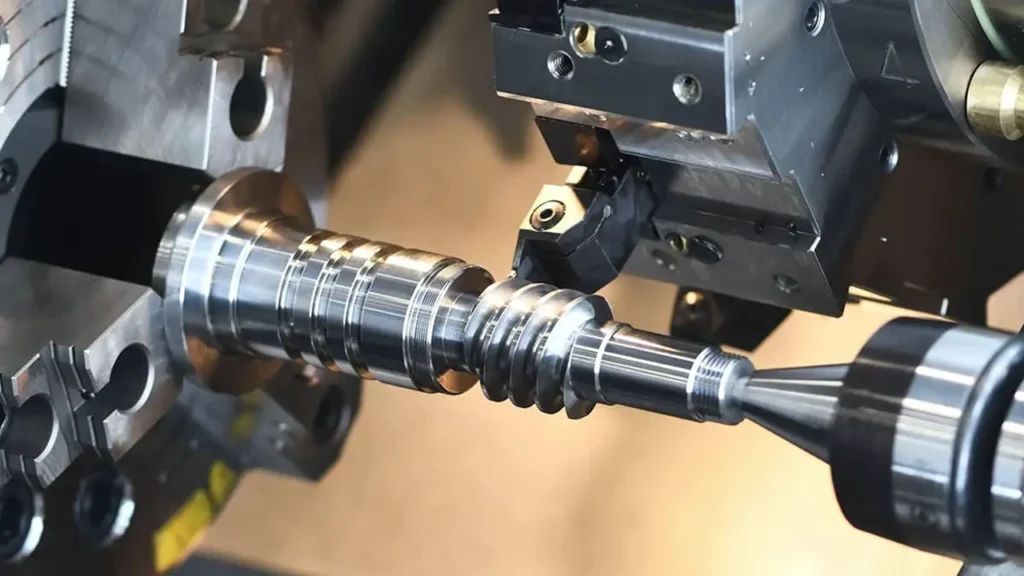
Competitive Pricing with Strong ROI
Price has long been a competitive advantage for china machine tools, but it’s no longer the only reason buyers are turning to them. Today, global manufacturers are also looking at the total return on investment (ROI), and in this regard, Chinese machines deliver.
In many cases, the cost of a Chinese machining center or CNC lathe is 30–50% lower than equivalent models from European or Japanese brands. Yet, they offer comparable performance in medium- to high-volume production environments. Lower upfront cost, combined with reliable uptime and lower maintenance requirements, leads to faster payback periods.
Improved Service and Global Support Networks
Trust doesn’t come from specifications alone—it also depends on post-sales experience. Many Chinese machine tool manufacturers have invested in:
- Faster delivery lead times
- Remote diagnostic and support systems
- Localized training and technical documentation
- Spare parts warehouses in key export regions
These developments ensure that buyers don’t just receive a machine, but a support ecosystem that helps keep operations running smoothly.
Proven in Real-World Applications
One of the strongest reasons behind growing confidence in Chinese CNC machines is real-world validation. Buyers across Southeast Asia, South America, Eastern Europe, and even parts of Western Europe are now using china machine tools in high-demand applications—from automotive component production to aerospace brackets and industrial pump parts.
These success stories serve as tangible proof that Chinese machines can deliver consistent quality over time. For new buyers, knowing that others in the same industry have adopted and validated Chinese equipment significantly reduces risk and builds confidence.
Key Technologies Behind Modern Chinese CNC Machines
The growing reputation of china machine tool products is not only the result of market strategy or price—but of tangible improvements in core technologies. Over the past decade, Chinese manufacturers have focused heavily on upgrading the components and systems that directly determine a machine’s performance, accuracy, and lifecycle. While they may not lead the global innovation frontier yet, they have built a strong technical foundation that continues to close the gap with top-tier international competitors.
This section highlights the most important technologies currently shaping the competitiveness of china cnc machines, from mechanical engineering to control systems and digital integration.
Structural Integrity and Rigidity
One of the critical factors in machining accuracy is the rigidity of the machine base and frame. In modern Chinese CNC machines, cast iron beds with optimized rib structures have become standard. Many manufacturers now use finite element analysis (FEA) during the design phase to simulate load distribution and thermal deformation, ensuring the structure can withstand long-term stress without compromising stability.
In addition, the adoption of box-type guideways in heavy-duty machines and linear guideways in high-speed applications allows Chinese machines to achieve better dynamic accuracy across different load conditions.
Precision Motion Components
The motion system is at the heart of any CNC machine, and in recent years, Chinese manufacturers have made noticeable progress in localizing these critical components—particularly for mid-range applications. Domestically produced ball screws with backlash compensation, linear guideways with high repeatability, and servo motors now support many standard and mid-level china cnc machine models with reliable performance.
For applications requiring tighter tolerances or longer duty cycles, hybrid configurations are often used. These combine imported spindles or guideways from leading Japanese or German brands with domestically manufactured motion components. This allows manufacturers to balance cost and performance, ensuring consistent accuracy even under multi-shift, high-throughput production environments.
While ultra-precision motion systems are still typically sourced internationally, China’s motion control ecosystem continues to advance, and is rapidly closing the gap in quality and reliability.
CNC Control Systems and Automation Readiness
Modern china cnc machines now support a wide variety of controller platforms. While imported options like FANUC, Siemens, and Mitsubishi are still commonly integrated into premium machines, China’s domestic CNC controllers have also made notable progress. Brands such as GSK, KND, and HNC now offer:
- Multi-axis synchronization
- 3D simulation and path optimization
- Real-time diagnostics
- Remote monitoring via IoT integration
This growing controller ecosystem allows Chinese machines to work seamlessly in automated production lines, and to adapt to global factory standards without heavy customization.
Thermal Stability and Cooling Systems
Thermal expansion is a key source of inaccuracy in high-speed machining. To address this, many Chinese CNC machines now incorporate:
- Spindle cooling jackets or oil-cooling units
- Independent thermal zoning on machine columns
- Real-time temperature compensation algorithms within the control system
These technologies contribute significantly to maintaining dimensional accuracy over long machining cycles, especially when working with metals like aluminum or titanium that are sensitive to heat.
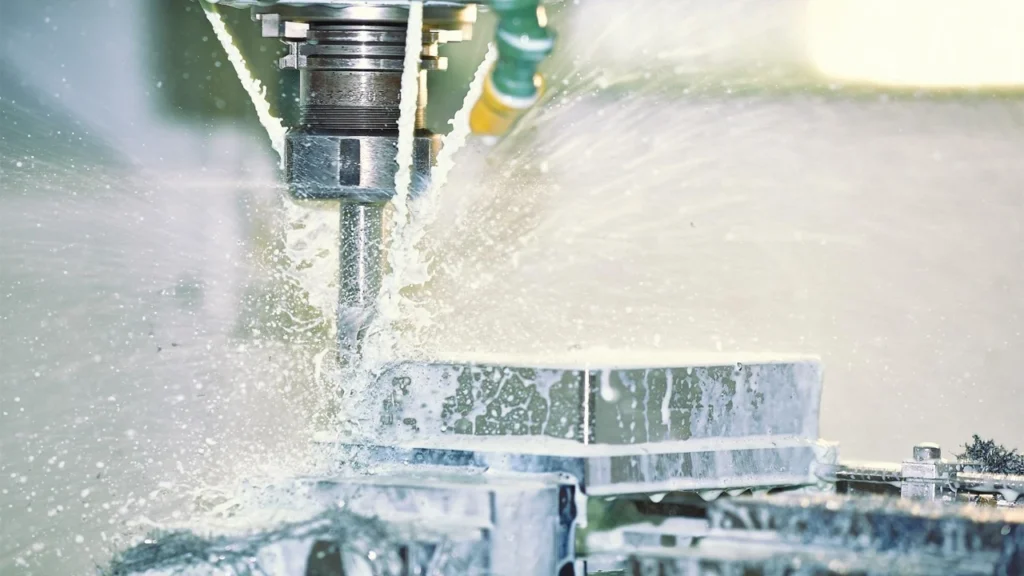
Smart Features and Industry 4.0 Compatibility
As factories become more digitized, china cnc machines are being designed with Industry 4.0 in mind. Newer models increasingly support:
- Data collection and visualization dashboards
- Predictive maintenance alerts
- Machine-to-MES system integration
- Cloud-based performance analytics
These features allow operators and managers to improve OEE (Overall Equipment Effectiveness) and reduce downtime—capabilities that were previously limited to high-end European systems.
Today’s china machine tool is not simply a cheaper alternative—it is a machine built on a solid technological backbone, capable of delivering accuracy, repeatability, and smart manufacturing integration. While some ultra-high-end capabilities remain the domain of legacy European and Japanese brands, the technical progress made by Chinese manufacturers is real, measurable, and ongoing.
For buyers evaluating their next equipment investment, understanding these underlying technologies is key to appreciating the true value behind a modern china cnc machine.
China Machine Tools vs European & Japanese Brands
When evaluating CNC machines, global buyers often find themselves comparing china machine tool products with established brands from Germany and Japan. While all three regions have their strengths, their machines serve different priorities, price points, and production philosophies. A fair comparison should go beyond just reputation and examine the practical performance and investment value each can offer.
Precision and Repeatability
German and Japanese machines are widely known for their ultra-high precision and long-term repeatability, especially in multi-axis or 5-axis machining applications. For parts requiring sub-micron accuracy, such as aerospace turbine components or semiconductor molds, top-tier brands like DMG Mori, Mazak, and Okuma are often the first choice. These machines also excel in dynamic stability, vibration control, and advanced thermal compensation.
China cnc machines, on the other hand, have made solid progress in meeting ±0.01mm repeatability and are increasingly reliable in medium-precision, batch production tasks. For example, in the automotive, general machinery, and consumer electronics sectors, Chinese machines can deliver consistent accuracy with far lower capital expenditure.
While Chinese models may not match the elite-level precision of the highest-end German or Japanese counterparts, they provide “good enough” precision for 70–80% of real-world industrial applications—especially when paired with stable fixtures, quality tooling, and proper setup.
Cost Structure and Return on Investment
One of the most notable differences lies in the cost-to-performance ratio. Machines from Germany and Japan are premium assets—with high acquisition cost, advanced features, and long-term durability. However, they also come with:
- Higher shipping, taxation, and installation costs
- More complex integration into existing automation systems
- Expensive proprietary components
In contrast, china machine tools offer:
- Upfront cost reductions of 30–50% in most configurations
- Open architecture designs compatible with multiple controller platforms
- Localized technical support in key export markets
This results in shorter ROI cycles—a key decision factor for buyers operating under budget constraints or looking to scale up production quickly.

Lead Times, Supply Chain & Support
German and Japanese machines often have longer production lead times, especially for customized builds or high-end models. Shipping, import clearance, and local commissioning can add weeks or months to the procurement timeline. Additionally, spare parts may have limited regional availability, requiring import with long wait times.
Modern china machine builders, however, have shortened standard delivery cycles significantly. Many models are kept in stock for fast shipping, and a growing number of suppliers now offer:
- Localized spare parts warehouses
- Remote diagnostics and online training
- Bilingual technical documentation and real-time customer service
This responsiveness can be a critical advantage—especially for fast-growing companies needing to deploy equipment within tight schedules.
Summary: Matching the Right Tool to the Right Task
Choosing between china machine tools and European or Japanese brands doesn’t come down to “better or worse”—it’s about fit for purpose. For ultra-precision aerospace molds or high-speed five-axis work, premium brands still dominate. But for general production, automotive components, or mass machining, Chinese CNC machines provide a competitive, scalable, and cost-effective alternative.
Buyers who prioritize value, speed of deployment, and accessible service infrastructure are increasingly finding that china cnc machines strike the right balance between performance and practicality.
Real-World Applications Across Industries
The global trust in china machine tool products is not built on marketing alone—it is solidified through real-world use across a broad range of industries. Chinese CNC machines are no longer confined to small workshops or low-stakes jobs. Today, they are actively deployed in complex, high-throughput production environments where consistency, accuracy, and adaptability are essential.
Below are key industries where china cnc machines have demonstrated consistent value and proven themselves as reliable assets on the factory floor.
Automotive: Powertrain and Precision Components
The automotive sector has become one of the most important testing grounds for china machine tools. From engine blocks and transmission casings to brake calipers and differential housings, the production of automotive parts requires tight tolerances, repeatable precision, and high-speed cycle times.
Modern Chinese machining centers and CNC lathes are widely used in:
- Cylinder head milling
- Crankshaft turning
- Drilling and tapping of engine housings
Thanks to multi-station setups, auto tool changers, and integration with robot arms, many automotive OEMs and tier-one suppliers in Southeast Asia, Russia, and Latin America now rely on Chinese machines for both prototyping and large-volume production.
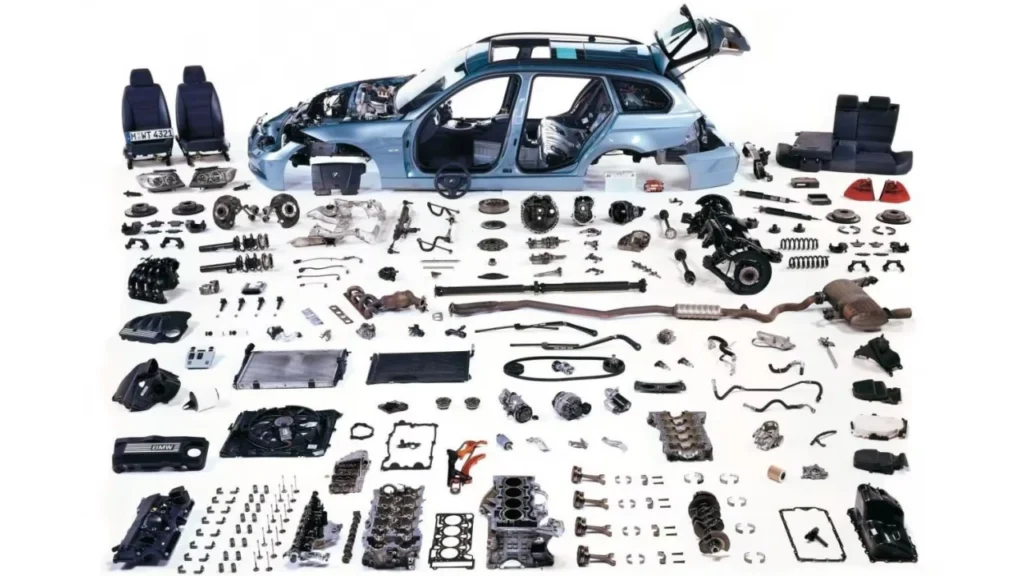
Aerospace: Non-Critical Structural Machining
While ultra-critical parts like turbine blades still rely on five-axis machines from legacy brands, Chinese CNC machines are increasingly used for secondary aerospace structures and ground support components. Applications include:
- Machining of aluminum brackets
- Drilling composite frames
- Finishing structural support rails
Many of these parts require long-stroke, stable spindle systems with adaptive feed control, which newer Chinese machines now offer. Additionally, the incorporation of 3D toolpath simulation and integrated coolant delivery allows operators to maintain quality even with difficult materials.
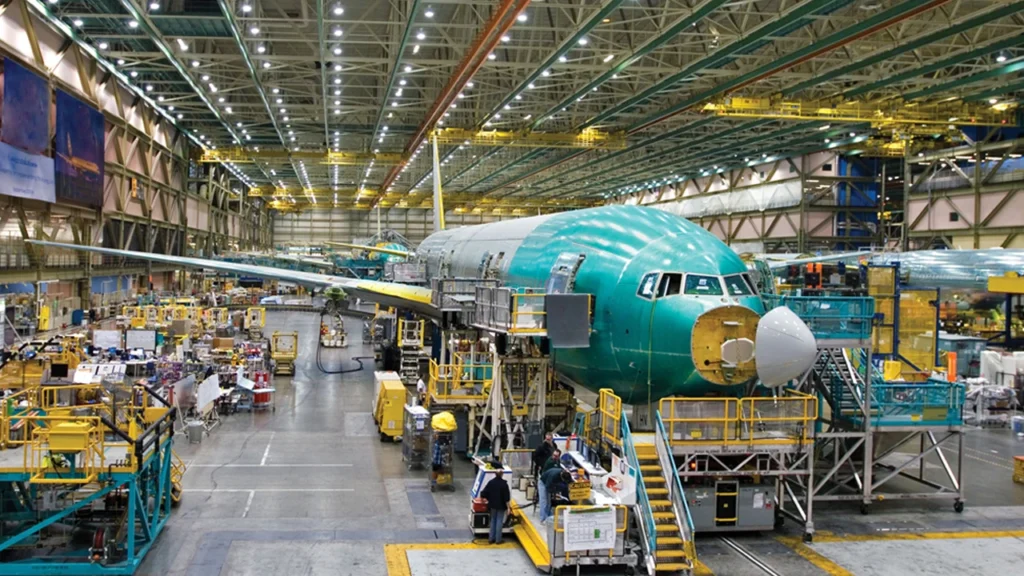
Medical: High-Precision Custom Implants and Tooling
In the medical field, china cnc machines are being used to produce:
- Titanium bone screws and orthopedic implants
- Custom dental abutments
- Surgical tool handles with ergonomic contours
These parts demand fine surface finishes, material integrity, and micro-level dimensional control. Swiss-type CNC lathes and compact 4-axis machining centers from China have shown excellent results in low-to-medium batch production, especially when combined with CAM software and in-line measurement systems.
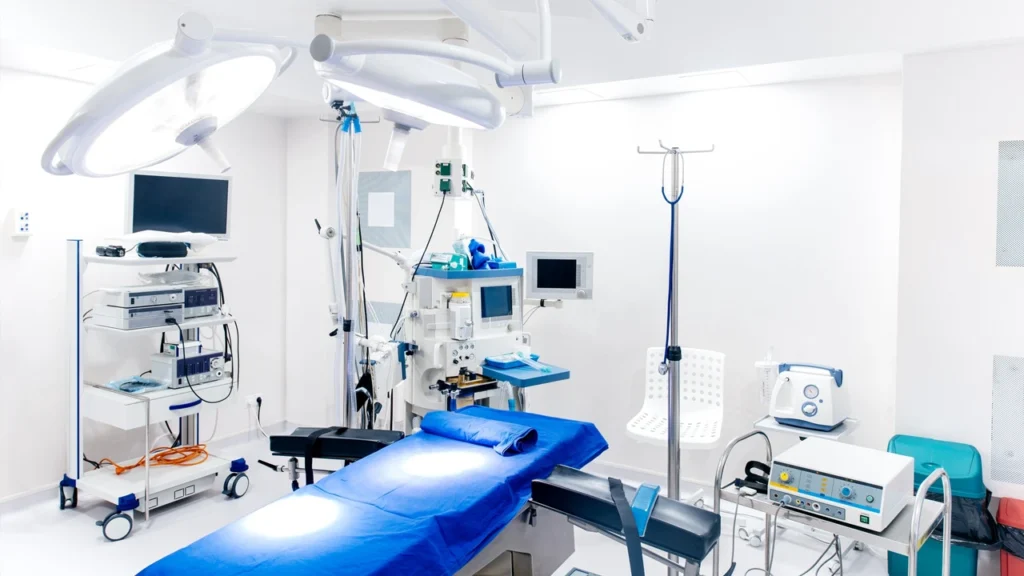
Heavy Industry and Infrastructure: Durable, High-Torque Machining
Beyond high-tech fields, china machine tool products play a vital role in traditional heavy industries such as:
- Mining
- Shipbuilding
- Rail transport
- Wind and hydro energy
Vertical lathes, boring machines, and gantry milling machines from China are used to machine:
- Large-diameter flanges
- Hydraulic cylinder bases
- Foundation plates for wind turbines
In these sectors, what matters most is machine durability, table load capacity, and stable performance over long cycles—all areas where Chinese machines have shown dependable capability.
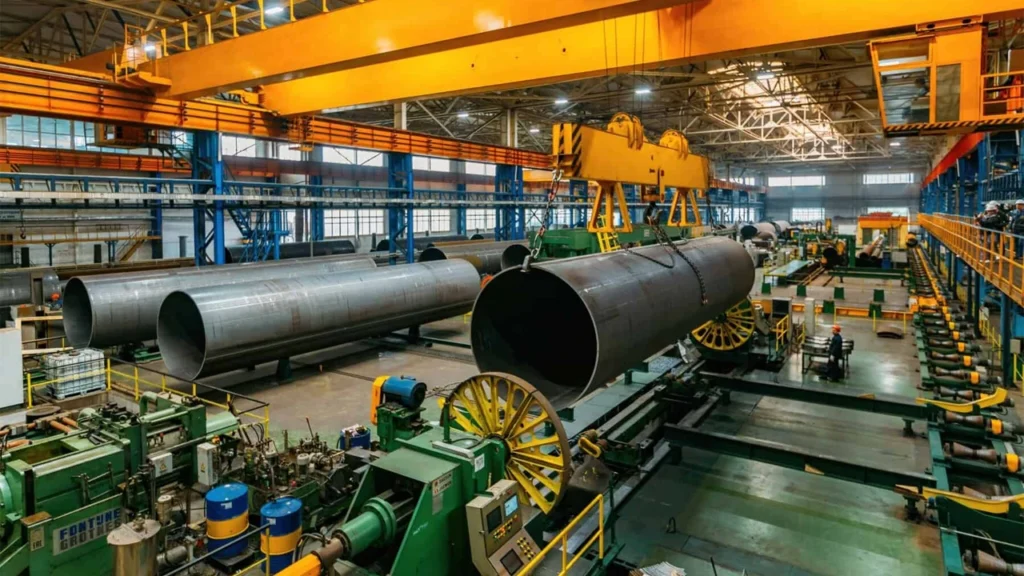
From high-speed component machining in automotive to durable infrastructure parts in energy, china cnc machines are no longer “secondary options”—they’re strategic tools deployed in real-world, high-stakes manufacturing operations. With every new application field they enter, Chinese machines reinforce the global confidence placed in their precision, versatility, and industrial reliability.
How to Choose a Reliable China CNC Machine Supplier
Sourcing a china machine tool isn’t just about picking the right model—it’s about choosing the right manufacturer. The supplier you choose can determine everything from the actual machine quality to your long-term production reliability, cost of ownership, and even after-sales experience.
With thousands of CNC machine builders across China, buyers must understand how to evaluate suppliers beyond marketing brochures or online catalogs. Here’s how to do it with confidence.
1. Verify Manufacturing Scale and Capabilities
First, check whether the supplier is a true manufacturer or simply a trading company. Genuine manufacturers will be able to:
- Show factory photos or offer virtual/on-site visits
- Provide production line details and in-house component machining capabilities
- Offer technical drawings or process flow diagrams for their machines
Ask:
- How many years have they been building CNC machines?
- How many square meters is their facility?
- Do they produce critical components (e.g. beds, castings, control cabinets) in-house or outsource them?
Suppliers who control more of the production chain are more likely to deliver stable quality and lead times.
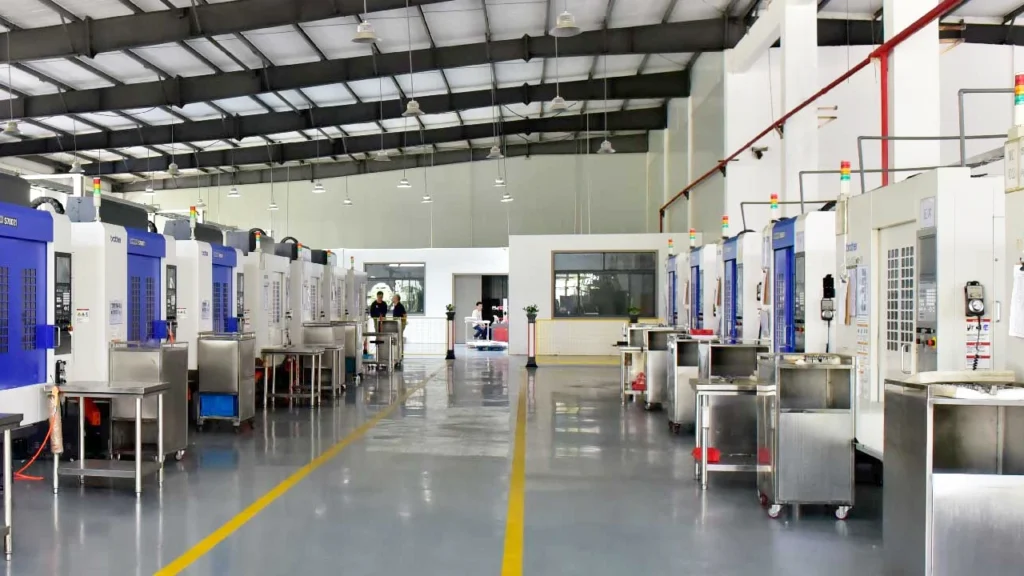
2. Look for Export and Compliance Experience
Exporting machine tools is not simply about packing and shipping. A trustworthy china cnc machine supplier should demonstrate experience in:
- International certifications: CE, ISO9001, UL, etc.
- Documentation: shipping specs, customs clearance support, technical manuals
- References: successful installations in your region or industry
Ask whether the supplier has worked with customers in your country. Can they share names or photos of installations? Have they handled voltage conversions, local standards, or installation services abroad?
These signals show that the supplier understands the realities of global business, not just local sales.
3. Prioritize After-Sales Support and Service Infrastructure
A CNC machine is not a one-time purchase—it’s an ongoing investment. What happens after the machine arrives is just as important as what happens during the sale.
A reliable china cnc machine supplier must offer strong after-sales support to keep your production running smoothly. Key areas to evaluate include:
- Warranty Coverage
Ask for clear written terms that specify coverage for:- Mechanical parts (e.g. casting, slides)
- Electrical systems (e.g. wiring, motors)
- Control units (e.g. PLC, servo, CNC controller)
- Consumables and wear parts
- Remote Troubleshooting and Diagnosis
Check if the supplier offers:- Remote access to machine diagnostics via software
- Video call-based technical support
- Error log analysis for system-level troubleshooting
- Spare Parts Availability
Confirm whether the supplier:- Has a dedicated spare parts warehouse for overseas orders
- Offers express shipping options for mission-critical items
- Can provide a recommended spare parts kit with your purchase
- Installation and Training
Ensure your supplier offers:- Installation guidance (manuals, videos, remote sessions)
- On-site or online training for your operators
- Setup support for controller configuration and fixture calibration
- Service Responsiveness
Ask:- What’s your average response time for support requests?
- Do you offer 24-hour service?
- Can you assign a support engineer for our region?
The best china machine tool manufacturers build long-term relationships by investing in service—because they know a well-supported machine is a machine that keeps running profitably.
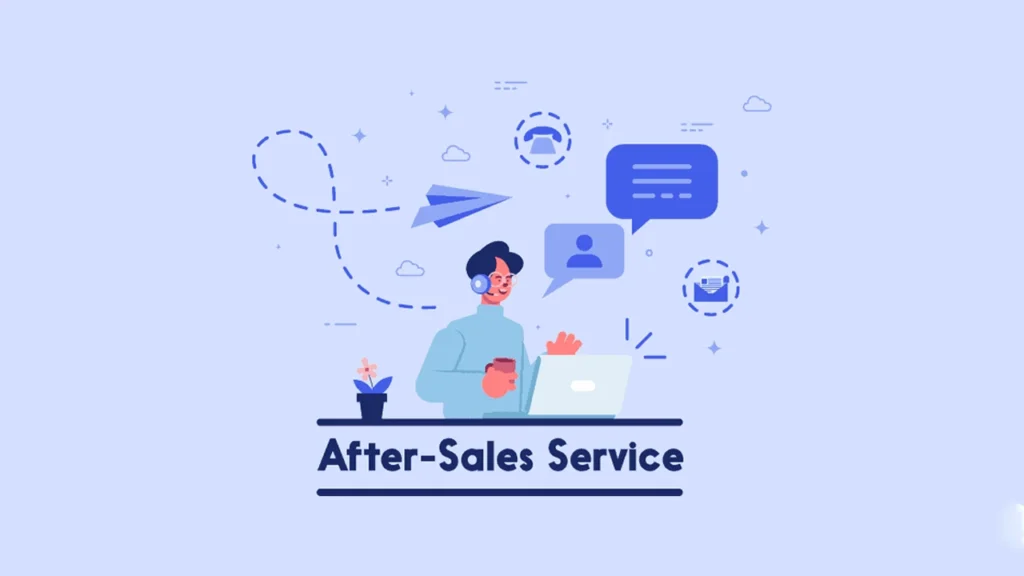
4. Review Reputation and Transparency
Finally, consider how open the supplier is in sharing information. Do they:
- Provide sample videos or trial machining reports?
- Allow video calls with engineers, not just salespeople?
- Respond promptly to detailed technical inquiries?
You can also review:
- Alibaba Gold Supplier ratings
- Verified user reviews on platforms like Made-in-China or Global Sources
- Participation in global trade fairs (CIMT, EMO, etc.)
A credible china machine tool supplier will have nothing to hide—and plenty to show.
Choosing a china cnc machine is just half the decision—the other half is choosing who to trust to deliver it. With the right evaluation process, global buyers can confidently source machines that meet not just their technical needs, but also their expectations for service, consistency, and long-term success.
Top 5 China CNC Machine Tool Manufacturers You Should Know
With thousands of machine tool companies in China, it can be difficult for overseas buyers to identify the truly top-performing brands. While some factories focus on low-cost mass production, others are leading the way in innovation, precision, and export readiness.
If you’re considering purchasing a china cnc machine, this list will give you a clear starting point. Below are five manufacturers who have proven themselves in both domestic and global markets—companies recognized for quality, scale, and customer satisfaction.
1. Jinan No.2 Machine Tool Group (JIER)
JIER is one of the oldest and most prestigious machine tool manufacturers in China, known for its large-scale CNC machining centers and metal forming equipment. With exports to over 60 countries and customers in automotive, aerospace, and shipbuilding sectors, JIER offers cutting-edge technology and fully customized solutions for high-end production lines.
Best known for:
- Heavy-duty horizontal and vertical machining centers
- Automotive press lines
- Advanced automation integration
Why consider them: If you need high-torque, large-format, precision CNC systems for industry-scale production.
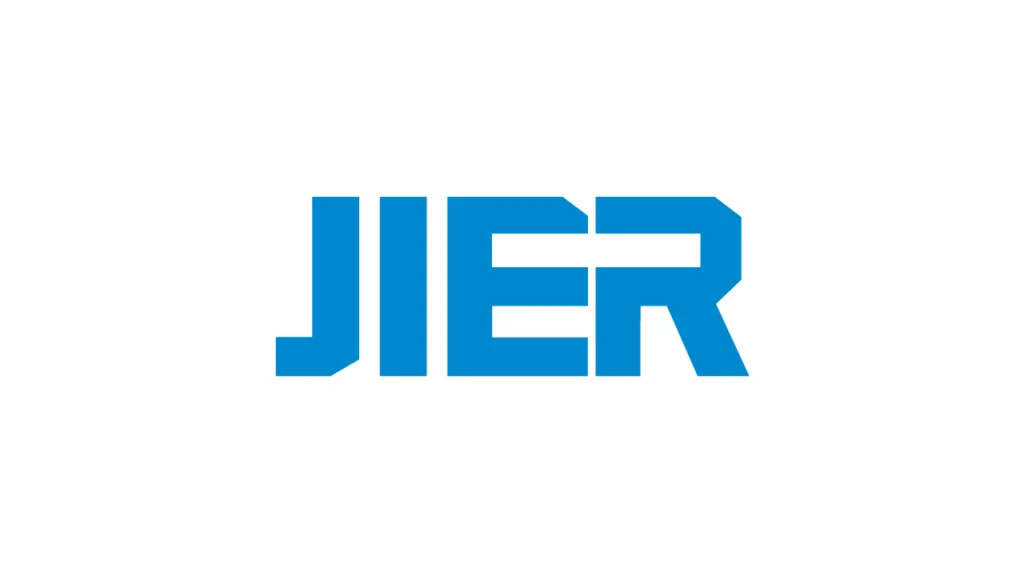
2. DMTG – Dalian Machine Tool Group
DMTG is a powerhouse in CNC lathe and machining center production, especially for mid-to-high-end industrial applications. The company has been part of several national-level intelligent manufacturing pilot projects and is known for robust machine structures and durable systems.
Best known for:
- High-precision CNC lathes
- Horizontal machining centers
- Modular production lines
Why consider them: They offer a balance of quality, service, and cost performance ideal for automotive and industrial metal processing sectors.
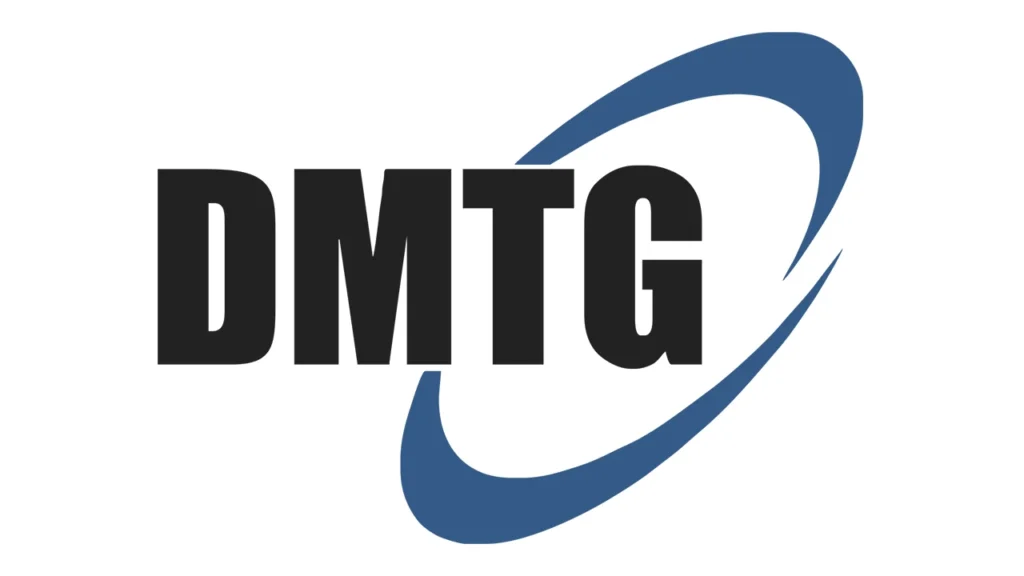
3. Qinchuan Machine Tool Group
Qinchuan specializes in precision gear machining, complex tooling systems, and aerospace-grade CNC systems. Their advanced 5-axis machining platforms and custom automation solutions are used by major aerospace and defense companies within China.
Best known for:
- High-end gear hobbing machines
- 5-axis CNC machining centers
- Aerospace and defense systems
Why consider them: When high-complexity components, toolpath precision, and automation are top priorities.
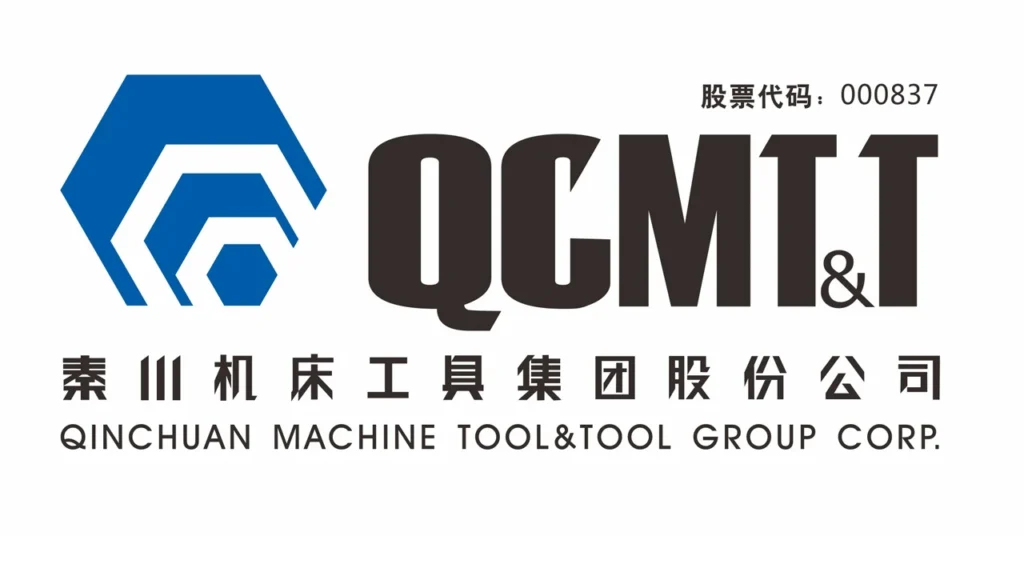
4. Hision (Haitian Precision Machinery)
Hision, the CNC division of Haitian Precision, is one of China’s largest and most recognized machine tool manufacturers, publicly listed and renowned for its scale and reliability. Backed by Haitian Group’s strong industrial foundation, Hision delivers robust, high-performance CNC machines for mass production environments across industries like automotive, general machining, and mold manufacturing.
Their product line focuses on stability, accuracy, and efficient automation—making them a preferred brand for factories that require long-term reliability at scale.
Best known for:
- Horizontal and vertical machining centers
- High-rigidity CNC turning centers
- Gantry-type machining platforms for large parts
- Modular configurations for automated production lines
Why consider them:
Hision stands out for its mass production capability, machine stability, and mature after-sales infrastructure. For manufacturers seeking dependable CNC solutions at volume, especially in automotive and heavy industry sectors, Hision offers proven machines with strong ROI and consistent performance.
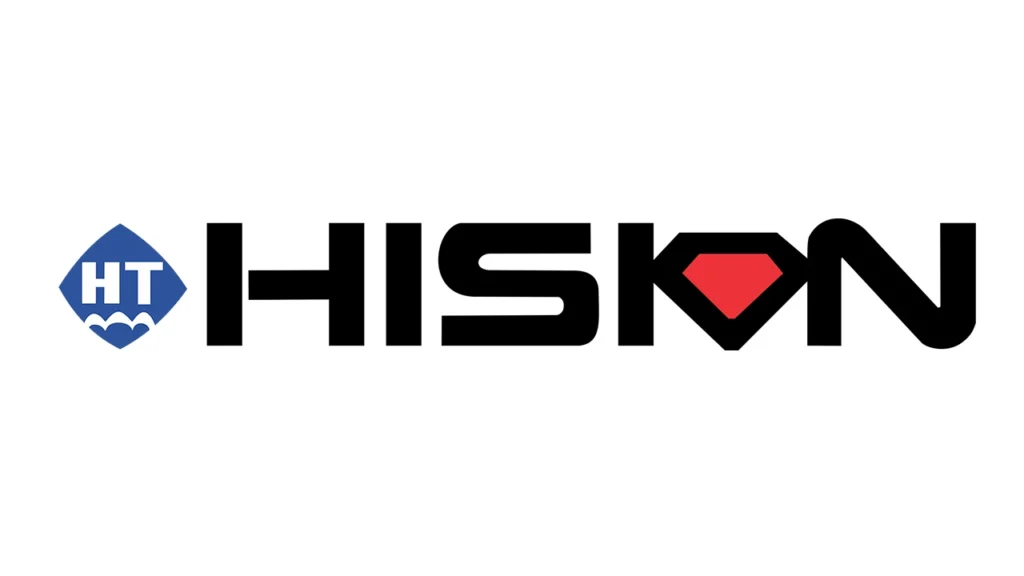
5. Rosnok CNC Machine
Rosnok is a well-established CNC machine manufacturer with over 20 years of industry experience and a global footprint. Operating across five modern production workshops totaling 60,000m², Rosnok has built a reputation for delivering highly reliable, performance-driven machines tailored to international standards.
Our portfolio covers a wide spectrum of metal machining solutions, including:
- Lathe machines
- Turning centers
- Machining centers
- Milling machines
- Boring machines
- Grinding machines
What sets Rosnok apart is our engineering depth and customization capability. Every solution we provide is designed to match our clients’ real production needs, supported by:
- Global quality certifications (CE, ISO9001, UL, FCC)
- A dedicated international service network with rapid spare parts delivery
- Competitive pricing with full value-chain support
- A proven export track record across Russia, Belarus, Southeast Asia, and South America
Our After-Sales Service: At Rosnok, we believe in long-term partnerships, not just one-time sales. That’s why we offer:
- 24/7 technical support via remote diagnostics, phone, and email
- On-site service and installation support in key regions
- Training for operators and engineers, ensuring quick mastery of the machines
- Fast delivery of spare parts and preventative maintenance services
- Comprehensive warranties, including parts and labor, to ensure the longevity of your investment
Why consider Rosnok:
If you’re seeking a china machine tool supplier that delivers precision, adaptability, and long-term reliability, Rosnok offers a trusted partnership backed by real-world results, deep technical expertise, and exceptional after-sales support.
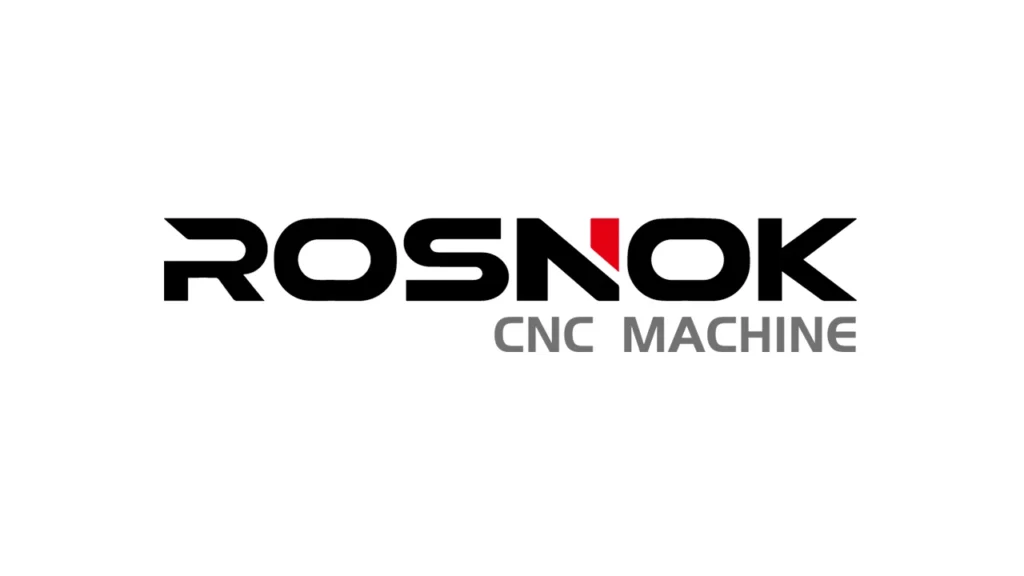
These five companies represent the best of China’s CNC machine tool manufacturing capability. Whether you need a heavy-duty press, high-speed vertical machining center, or a cost-efficient but powerful lathe, these suppliers provide a strong foundation to begin your sourcing journey.
The key is knowing your production needs—and partnering with a china cnc machine supplier that can grow with your business.
The Future of China Machine Tools
As the world’s largest manufacturing hub, China’s machine tool industry is poised for rapid transformation in the coming years. Driven by advancements in technology, smart manufacturing, and a growing commitment to sustainability, the future of china machine tools is one of both immense opportunity and rising competition. Here’s a look at what lies ahead for this dynamic industry.
1. Smart Manufacturing and Automation Integration
One of the key trends shaping the future of china cnc machine production is the widespread adoption of smart manufacturing and automation. China has long been a leader in the development and implementation of Industrial Internet of Things (IIoT) technologies, and this will continue to drive machine tool innovation.
Intelligent CNC systems, integrating sensors, real-time monitoring, and AI-powered predictive analytics, are becoming standard features in China’s machine tools. This will enable manufacturers to:
- Monitor machine health remotely, preventing downtime and minimizing unplanned repairs
- Optimize cutting processes, reducing waste and improving efficiency
- Adapt to flexible production demands, allowing for both large-scale production and customized manufacturing without additional setup time
As china machine tool manufacturers increasingly embrace Industry 4.0, expect machines to become smarter, more self-sufficient, and more integrated into a fully connected factory environment.
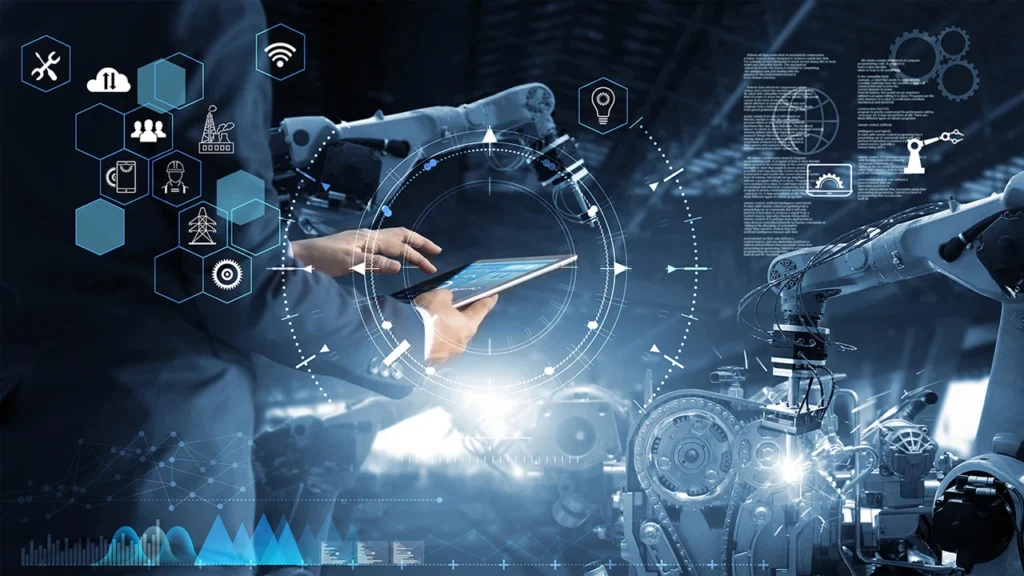
2. Energy Efficiency and Sustainability
Another major focus for china machine tool manufacturers will be improving the energy efficiency and environmental sustainability of their products. With global pressure to meet carbon reduction targets and comply with international sustainability standards, China’s machine tool makers are innovating in ways that minimize resource consumption.
Expect future china cnc machines to feature:
- Energy-saving components, such as high-efficiency motors and regenerative braking systems
- Eco-friendly cooling systems to reduce water and power consumption
- Recyclable materials in machine tool manufacturing to decrease environmental impact
As industries worldwide embrace greener practices, china machine tools will become increasingly sought after for their ability to deliver high performance while adhering to sustainability standards.
3. Advanced Materials and Precision Machining
The demand for precision machining continues to rise as industries like aerospace, medical devices, and electronics push for more complex designs and tighter tolerances. To meet these challenges, Chinese manufacturers are investing heavily in advanced materials and high-precision CNC technology.
The future of china machine tools will see an increased focus on:
- Hard-to-machine materials like titanium alloys, superalloys, and advanced composites
- Micromachining capabilities for industries requiring high precision at small scales, such as medical implants or semiconductors
- Hybrid machining that integrates additive manufacturing with traditional subtractive methods, enabling even greater design flexibility and material efficiency
These developments will position china cnc machines as critical tools for the production of the next generation of advanced products.
4. Global Expansion and Increased Export Competitiveness
As China continues to rise as a global manufacturing leader, its machine tool industry will play a significant role in reshaping the global marketplace. Chinese manufacturers are already increasing their export capabilities, focusing on building partnerships in markets across Europe, North America, and Southeast Asia.
The future of china machine tools will likely see:
- Improved international standards compliance, making Chinese-made machines more competitive in high-end markets
- Faster lead times and localized manufacturing for global customers
- Stronger after-sales support systems, including remote diagnostics, spare parts availability, and comprehensive service networks
As Chinese manufacturers continue to upgrade their products, china cnc machine suppliers will increasingly offer high-quality alternatives to traditional European and Japanese brands at competitive prices.
5. The Rise of Customization and Flexible Solutions
One of the most significant advantages that china cnc machines offer is their ability to be customized. As industries demand more flexible solutions, Chinese manufacturers are leading the way in offering highly customizable machine tools that cater to specific production requirements.
In the future, expect to see:
- Modular machine configurations that can be tailored to individual production needs
- Software-driven customization for specific machining tasks, enabling quick changes in production processes without significant downtime
- Flexible automation systems that can easily scale up or down depending on production volume or complexity
This shift towards greater flexibility will allow china machine tools to meet the diverse needs of both small workshops and large-scale industrial operations.
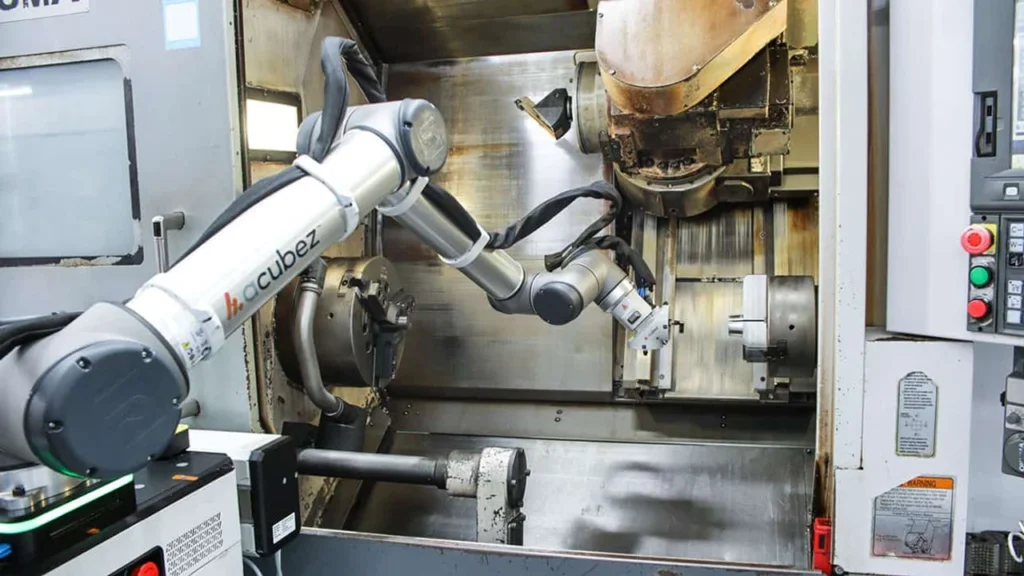
Summary: The Global Future of China Machine Tools
The future of china machine tools is a bright one. By integrating cutting-edge technology, improving energy efficiency, and expanding their global presence, Chinese manufacturers are positioning themselves as key players in the world of precision manufacturing. Whether it’s enhancing product capabilities or offering flexible, cost-effective solutions, China’s machine tool industry is set to continue its upward trajectory, providing global customers with high-performance, reliable, and innovative machinery for years to come.
Conclusion: The Global Future of China Machine Tools
As the manufacturing landscape evolves, china machine tools have firmly established themselves as integral components of global production lines. Over the past few decades, Chinese machine tool manufacturers have transitioned from basic, entry-level machines to precision-driven solutions that meet the rigorous demands of industries like aerospace, automotive, and medical. Through consistent technological advancements, competitive pricing, and an expanding global footprint, china cnc machines have earned the trust of international buyers.
While it is true that china machine tools may not yet match the absolute precision and technological sophistication of the top-tier machines from Japan and Europe, they have made significant strides in closing the gap. Today, they stand as highly capable alternatives that offer excellent value for money—enabling businesses to achieve high performance at a fraction of the cost of their Western counterparts.
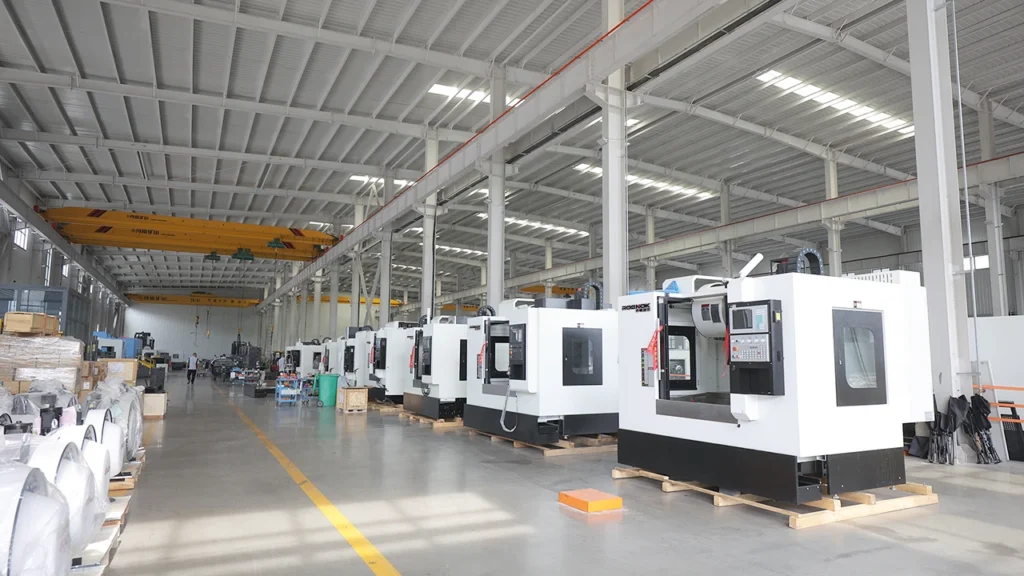
Moreover, the focus on energy efficiency, sustainability, and advanced materials ensures that china machine tools will continue to meet the evolving needs of modern manufacturing. The ongoing developments in automation, smart manufacturing, and Industry 4.0-ready features ensure that Chinese manufacturers are not only keeping pace with global trends but are also leading the charge in reshaping the future of machine tools.
As we look ahead, the potential of china machine tools to serve industries worldwide is vast. Whether you’re looking for high-precision lathes, machining centers, or customized automation solutions, china cnc machines offer the flexibility, reliability, and scalability needed to drive success in today’s competitive environment.
For businesses seeking the right balance of cost, performance, and long-term support, Chinese machine tool manufacturers are becoming the trusted solution. At Rosnok, we’re committed to providing tailored solutions that meet your needs. If you’d like to learn more about how we can support your business, feel free to reach out for more details or a personalized quote.