Have you ever wondered which types of lathe machines are most commonly used in modern machining? Does the wide range of specifications and machine categories make it hard to know where to start? With so many types of lathes out there, how do you identify what really matters? What sets certain machines apart when it comes to efficiency, precision, and long-term value?
There are seven essential types of lathe machines commonly used in modern machining: engine lathe, CNC lathe, Swiss-type lathe, pipe-threading lathe, vertical lathe, turning center, and toolroom lathe. Each plays a unique role in shaping, cutting, and finishing metals, offering different levels of precision and automation. Knowing these types of lathe machines gives you a solid foundation to choose the right equipment.
Each of these lathe types serves a distinct purpose in modern machining. In the following sections, we’ll explore their features, production strengths, and where they best fit within real-world manufacturing.
What is a Lathe Machine?
A lathe machine is one of the most fundamental and widely used tools in precision metalworking. It is designed to rotate a workpiece on its axis while various cutting tools shape it through operations such as turning, facing, threading, knurling, boring, and drilling. Lathes have been at the heart of manufacturing for centuries, evolving from simple manually operated systems into today’s advanced CNC-controlled platforms.
At its core, a lathe performs a simple principle: the workpiece spins, and the tool stays fixed or moves linearly to remove material. This controlled interaction between rotation and cutting enables incredibly precise machining results, especially for symmetrical components like shafts, flanges, bushings, or threaded cylinders.
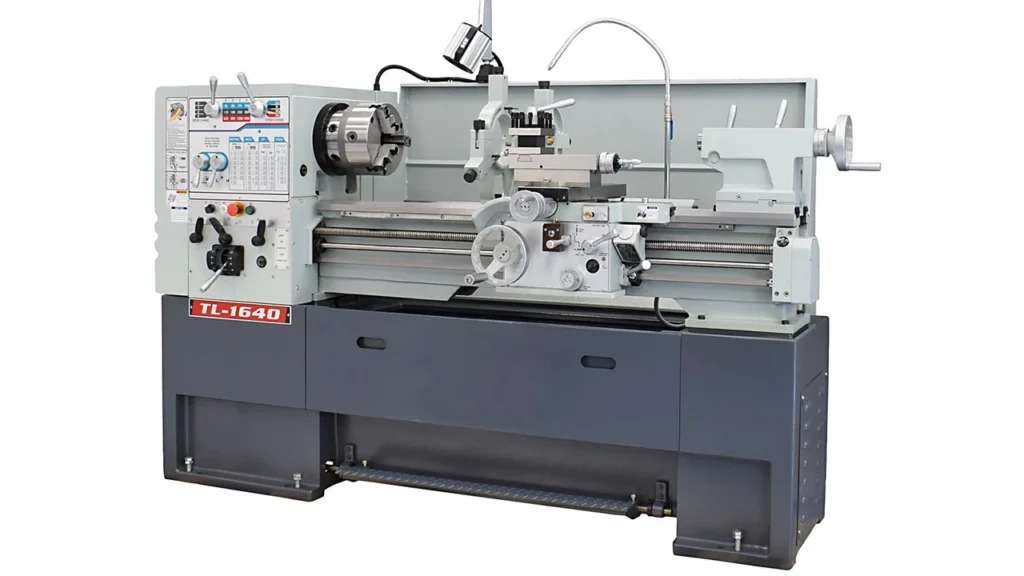
Basic Structure of a Lathe Machine
Regardless of type, most lathe machines share these core components:
- Bed: The main foundation that holds the structure together and ensures alignment.
- Headstock: Contains the motor and spindle that rotate the workpiece.
- Tailstock: Provides support for long workpieces during operation.
- Carriage and Tool Post: Hold and move the cutting tools.
- Lead Screw and Feed Rod: Drive the movement of the carriage/toolpost for threading and feeding operations.
- Chuck: A clamping device that holds the workpiece in place while it rotates.
These components work together to deliver a highly stable and controllable machining environment. In manual lathes, the operator adjusts feed and tool positions manually. In CNC lathes, all these movements are controlled digitally with extreme precision, often down to microns.
How Lathes Fit into Modern Manufacturing
Lathes are indispensable in industries ranging from automotive to aerospace, oil & gas, medical device manufacturing, and heavy equipment production. They are especially favored for producing cylindrical or conical parts that require consistent diameters and smooth surfaces. Whether it’s a turbine shaft or a dental implant, lathes play a central role in shaping modern components.
7 Essential Types of Lathe Machines
Understanding the different types of lathe machines is essential for building a versatile, high-performing workshop. Each machine type serves a distinct function, and selecting the right one can directly affect precision, efficiency, and productivity. Whether you’re shaping complex aerospace parts or fabricating automotive shafts, knowing the features and capabilities of various lathe types is the first step to making an informed investment.
In the sections below, we’ll break down the 7 essential types of lathes used across modern manufacturing, highlighting their structure, function, and ideal applications. From foundational engine lathes to advanced CNC-controlled systems, each plays a unique role in today’s precision machining world.
1. Engine Lathe
The engine lathe is one of the most traditional and widely used types of lathe machines. Often referred to as the “mother of all lathes,” it provides the foundation upon which more advanced and specialized lathe designs have evolved.
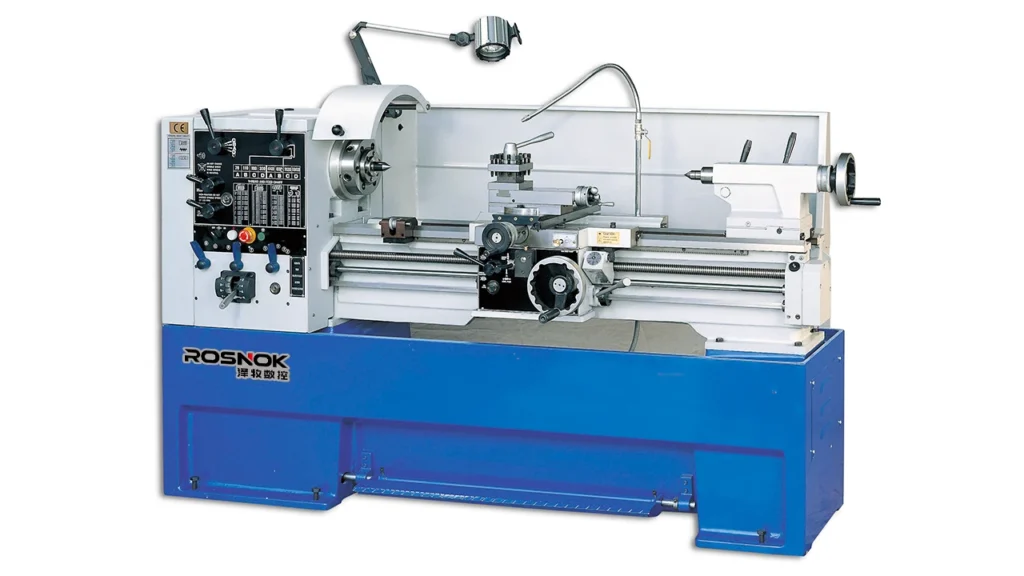
Structure and Function
Engine lathes are manually operated and equipped with a carriage, lead screw, feed rod, tailstock, and toolpost, all mounted on a rigid cast-iron bed. The workpiece is typically held in a chuck or between centers, while the operator uses a handwheel or manual feed system to move the cutting tool along the longitudinal and cross axes.
The spindle rotates the part, enabling the tool to perform essential operations such as turning, facing, and threading. With proper setup, engine lathes can also handle drilling, boring, and knurling, especially when supported by suitable accessories and experienced operation techniques.
Applications
Engine lathes are commonly used in:
- Custom repair jobs
- General maintenance machining
- Vocational training workshops
- Low-volume or prototype production
- Shops requiring flexible, manual control for various part shapes
Due to their mechanical simplicity and broad adaptability, they are a go-to choice in toolrooms, technical schools, and machinist training centers.
Advantages
- Cost-effective and reliable for small-batch or single-piece jobs
- Highly versatile for various lathe machine types and operations
- Excellent for learning basic machining skills and techniques
- No dependency on digital control systems
Best For:
Entry-level machinists, training institutions, and job shops focused on small-batch production, custom part repair, and manual machining tasks. Ideal for scenarios requiring hands-on control and flexibility across different types of lathe machine operations without relying on automated systems.
2. CNC Lathe
The CNC lathe (Computer Numerical Control lathe) represents a significant advancement over traditional manual lathes. These machines automate the cutting process using pre-programmed instructions, allowing for greater precision, speed, and repeatability. Among all types of lathe machines, CNC lathes are essential for modern, high-efficiency production lines.

Structure and Control System
A CNC lathe retains many of the same mechanical components as an engine lathe—such as the spindle, chuck, turret, bed, and tailstock—but introduces digital control via a CNC controller (commonly FANUC, Siemens, or Mitsubishi). The machine interprets G-code, controlling tool movement, feed rate, spindle speed, and even coolant flow with high precision.
Modern CNC lathes come equipped with automatic tool changers, servo motors, and closed-loop feedback systems, allowing for real-time error correction and highly repeatable machining.
CNC Lathe Configurations and Features
CNC lathes are available in a variety of structural configurations to meet different machining requirements. While the core principles remain the same, manufacturers can select among several designs based on production goals:
- Flat-bed design: Best for general-purpose turning tasks with simple geometries.
- Slant-bed design: Offers improved rigidity, stability, and chip removal—ideal for continuous production.
- Live tooling support: Enables milling, drilling, and tapping operations without secondary setups.
- Multi-axis capability: 4-axis, 5-axis, or more, for complex part geometries and tight tolerances.
- Bar feeding systems: Allow for fully automated, lights-out production—especially in high-volume workflows.
Rather than representing entirely different types of lathe machines, these are variations within CNC lathe systems, designed to enhance speed, precision, and flexibility depending on production scale and complexity.
Applications
CNC lathes are widely used in:
- Automotive component manufacturing (e.g., brake rotors, shafts)
- Aerospace part production (e.g., engine components)
- Medical device machining (e.g., bone screws, implants)
- Electronics and precision connectors
- Batch production of high-precision parts
They are essential wherever tight tolerances, mass production, and consistency are required.
Advantages
- High precision and repeatability
- Minimal manual intervention
- Supports complex geometries and multi-operation machining
- Efficient for both short-run and mass production
- Easy to integrate with CAD/CAM systems
Best For
Factories requiring automated, high-precision machining, such as automotive suppliers, aerospace part manufacturers, and mass production environments. Also ideal for workshops looking to reduce manual labor and increase production consistency.
3. Swiss-Type CNC Lathe
The Swiss-type CNC lathe, also known simply as a Swiss lathe or sliding headstock lathe, is engineered for ultra-high precision machining of small, slender, and complex parts. Unlike traditional CNC lathes where the workpiece remains stationary while rotating, Swiss-type machines feed the material axially through a sliding headstock, allowing the cutting tools to work extremely close to the guide bushing—minimizing deflection and vibration.
This unique mechanism makes Swiss-type CNC lathes one of the most powerful and precise tools in high-tolerance manufacturing, particularly when handling parts with tight dimensional control and fine surface finishes.
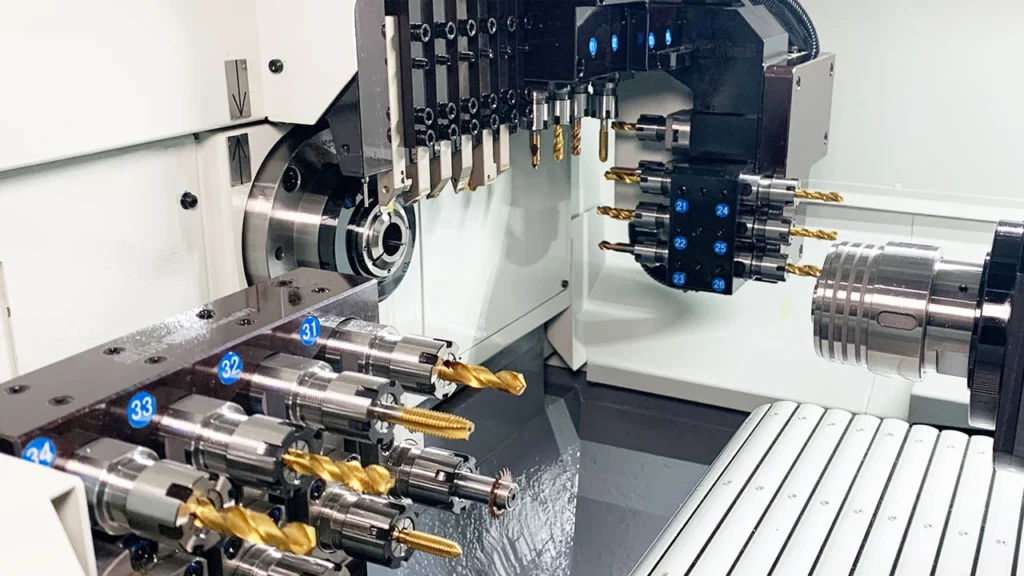
Structure and Working Principle
The key distinction in a Swiss lathe lies in its sliding spindle box and guide bushing system:
- The bar stock passes through the spindle and is held firmly by a guide bushing located near the cutting zone.
- The workpiece moves, while the tools are often mounted on a gang tool slide or turret and remain relatively stationary.
- Many Swiss lathes include live tooling, dual spindles, and multi-axis control (up to 7–9 axes or more), allowing simultaneous machining on multiple surfaces.
This design provides incredible stability for long, thin parts and reduces the need for secondary operations.
Applications
Swiss-type CNC lathes are essential for:
- Medical components (e.g., bone screws, surgical pins)
- Aerospace fasteners and micro parts
- Electronics connectors and sensors
- Watchmaking and high-end precision instruments
- Automotive micro shafts and injector nozzles
Wherever micron-level precision, small diameters, and delicate cuts are required, Swiss lathes deliver unmatched results.
Advantages
- Exceptional precision and tight tolerances
- Ideal for long, slender parts with complex geometries
- Supports both turning and milling in a single setup
- Reduces setup time and tool changes
- Enables lights-out machining for high-volume production
Best For
High-precision industries such as medical, electronics, aerospace, and micromechanical engineering. Also ideal for manufacturers looking to reduce part handling and achieve complex, multi-step machining in a single cycle.
4. Pipe Threading Lathe
The pipe threading lathe is a specialized type of lathe machine designed specifically for cutting threads on pipes, particularly large-diameter, heavy-duty pipe workpieces. Unlike standard lathes, these machines feature reinforced structures, wide beds, and large-through-hole spindles, allowing them to accommodate thick-wall pipes, tubing, and long rods typically used in oil & gas, chemical, and energy industries.
This machine is essential in industries where thread quality, pitch control, and connection integrity directly impact operational safety and performance—such as oil well casing, drill pipe threading, and high-pressure fluid transport systems.
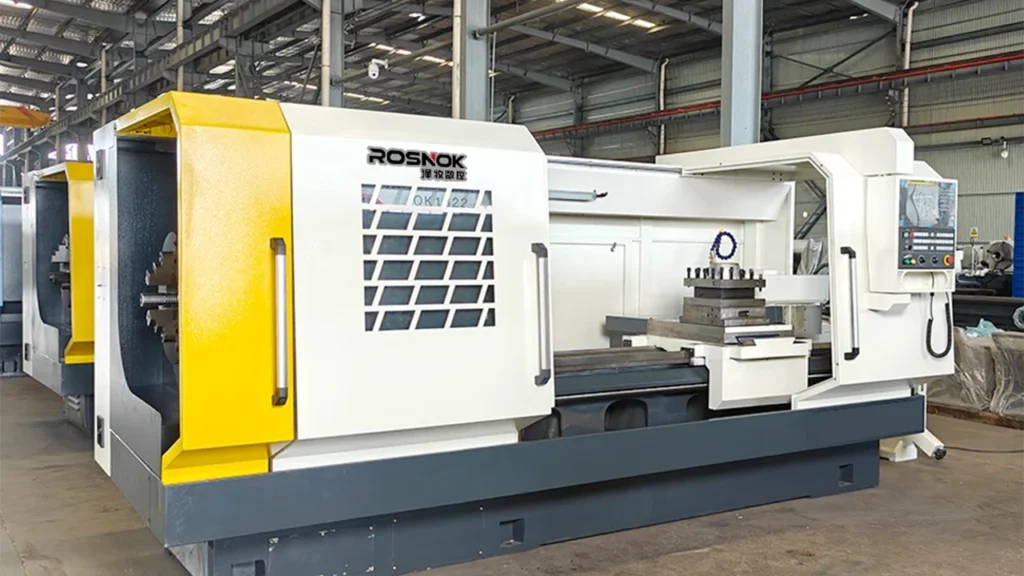
Structure and Capabilities
Pipe threading lathes differ from other types of lathe machines in several ways:
- Extra-large spindle bores: Allow long pipe stock to pass through the spindle for deep threading.
- Double chucks: One at the headstock and one at the tailstock or carriage to stabilize long workpieces.
- Robust gearboxes and heavy-duty toolposts: Handle deep cuts and multiple threading passes.
- Threading dial and synchronization system: Ensure accurate, repeatable thread pitch according to standards like API, BSP, or NPT.
These machines often support both internal and external threading, and many include features to handle taper threading or multi-start threads.
Applications
Pipe threading lathes are heavily used in:
- Oil and gas field operations (e.g., casing pipes, drill rods, couplings)
- Pipeline construction
- Hydraulic and pneumatic tubing production
- Chemical and power plant equipment manufacturing
- Thread repair and re-machining of used pipes
Anywhere threaded pipe ends are needed for fluid sealing, structural jointing, or rotational fit, this lathe is indispensable.
Advantages
- Built for large, heavy, and long pipe sections
- Highly accurate threading capabilities for industrial pipe standards
- Can perform both rough cutting and fine threading in one setup
- Ideal for batch production or custom heavy-duty threading jobs
- Available in both manual and CNC configurations
Best For
Workshops serving the oil & gas, petrochemical, or energy industries, and manufacturers of threaded pipe systems. It’s especially effective when high-strength, precision-threaded pipes are required for mission-critical applications.
5. Vertical Lathe
The vertical lathe, also referred to as a vertical turning lathe (VTL), is designed to handle large, heavy, and high-inertia workpieces. Unlike conventional horizontal lathes, the vertical lathe holds the workpiece on a rotary table positioned horizontally, while the cutting tool moves vertically. This orientation allows gravity to assist in stabilizing large components, making it ideal for heavy-duty turning applications.
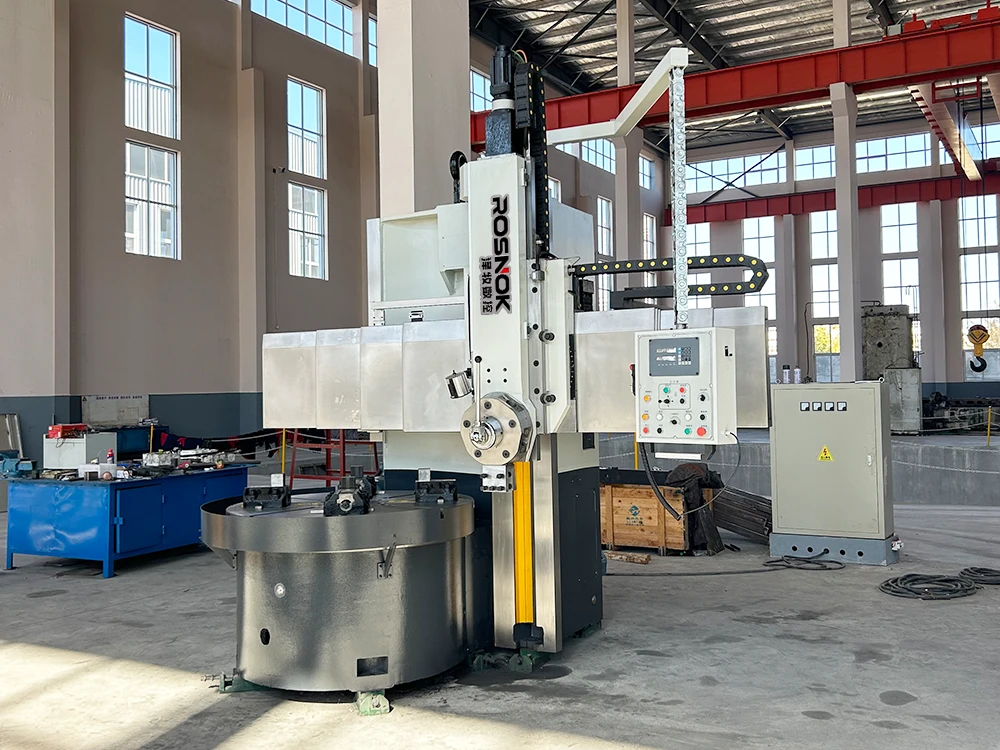
Structure and Working Principle
A vertical lathe features a large-diameter rotary table (which acts as the chuck), a vertical column housing the tool slide, and often a movable cross rail. The tool moves in X and Z axes while the table rotates the workpiece.
Because of its vertical configuration, the machine can accommodate extremely large diameters and heavy parts without needing excessive support systems. Many modern vertical lathes are CNC-controlled, with live tooling, automatic tool changers, and multi-axis control to handle more than just basic turning.
Applications
Vertical lathes are commonly used in:
- Wind energy equipment (e.g., turbine hubs, bearing seats)
- Shipbuilding (e.g., propeller housings, flanges)
- Heavy transport components (e.g., wheel hubs, brake drums)
- Aerospace and defense (e.g., large structural parts)
- Industrial machinery requiring large flanges, rings, or discs
They’re favored for their ability to handle oversized, asymmetrical parts that would be impractical or unsafe to mount horizontally.
Advantages
- Excellent stability for large, heavy components
- Gravity-assisted workholding reduces vibration
- Allows safe and easy loading of massive workpieces
- High rigidity and cutting force for deep turning and roughing
- Available with CNC systems for automation and precision
Best For
Manufacturers dealing with large-diameter parts in industries like energy, shipbuilding, aerospace, and heavy equipment. Vertical lathes are a must-have where horizontal lathes can’t manage weight, size, or cutting force requirements.
6. Turning Center
A turning center is an advanced version of a CNC lathe, offering enhanced capabilities beyond basic turning. While a traditional CNC lathe focuses primarily on rotating the workpiece and executing turning operations, a turning center often includes live tooling, Y-axis movement, sub-spindles, and sometimes even milling functions. This makes it a multi-tasking machine, capable of performing multiple machining operations in a single setup—dramatically reducing production time and improving part accuracy.
Unlike standard CNC lathes, turning centers are typically enclosed machines designed for high-speed, automated, and continuous production. They are built with slant-bed structures for improved rigidity, efficient chip removal, and better ergonomics. Many are also equipped with automatic tool changers (ATC) and bar feeders, allowing lights-out operation with minimal operator supervision.
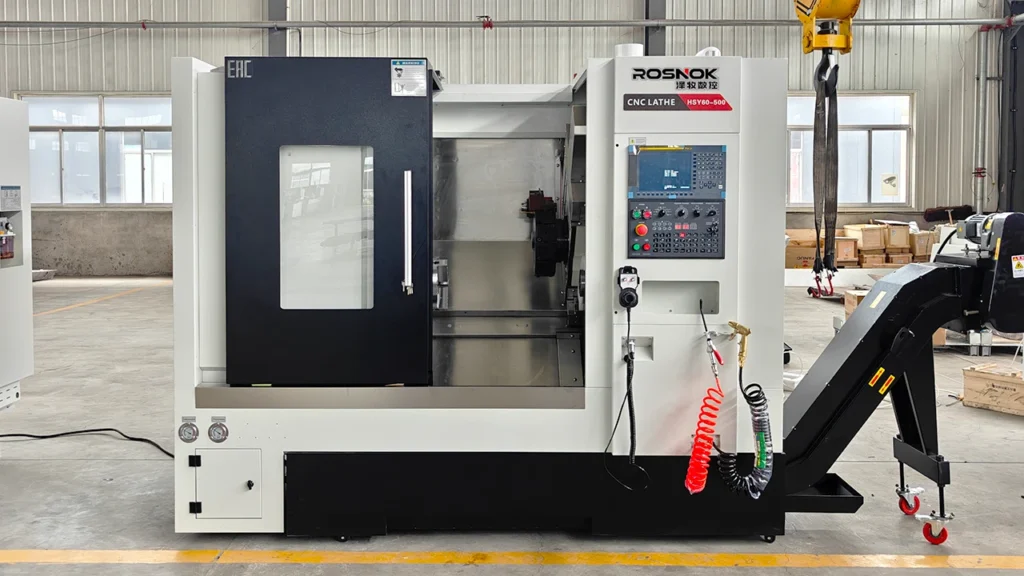
Core Features and Functions
- Live tooling systems for drilling, milling, tapping while the workpiece remains clamped
- Sub-spindles to enable complete machining on both ends of a part
- Y-axis capability to allow off-center milling or complex contouring
- Multi-tool turrets for high-speed tool indexing
- Automatic loading and unloading systems for continuous production
These features make turning centers some of the most efficient and flexible CNC lathe types in high-volume manufacturing.
Applications
Turning centers are widely used in:
- Automotive parts production (e.g., axles, gears, shafts)
- Aerospace components with multi-surface machining
- Industrial fittings and hydraulic parts
- High-precision, high-complexity parts requiring both turning and milling
They are ideal for any industry where precision, speed, and cycle-time reduction are key to productivity.
Advantages
- Performs multiple operations in one setup
- Reduces cycle time and workpiece handling
- Minimizes human error and increases consistency
- Excellent for batch production and lights-out manufacturing
- Supports complex geometries and tight tolerances
Best For
Manufacturers focused on high-speed, high-volume, and high-precision production. Perfect for industries such as automotive, aerospace, fluid power systems, and general precision machining where versatility and automation are crucial.
7. Toolroom Lathe
The toolroom lathe is a precision-focused lathe machine designed primarily for toolmaking, die work, prototyping, and maintenance tasks. While it may look similar to an engine lathe, it offers higher accuracy, smoother movement, and better control—making it ideal for small-batch production where tolerances and surface finishes are critical.
Toolroom lathes are often used in R&D departments, technical training centers, repair facilities, and custom fabrication shops. Their enhanced precision and manual control make them ideal for jobs that demand fine-tuned detail, not just high-speed output.
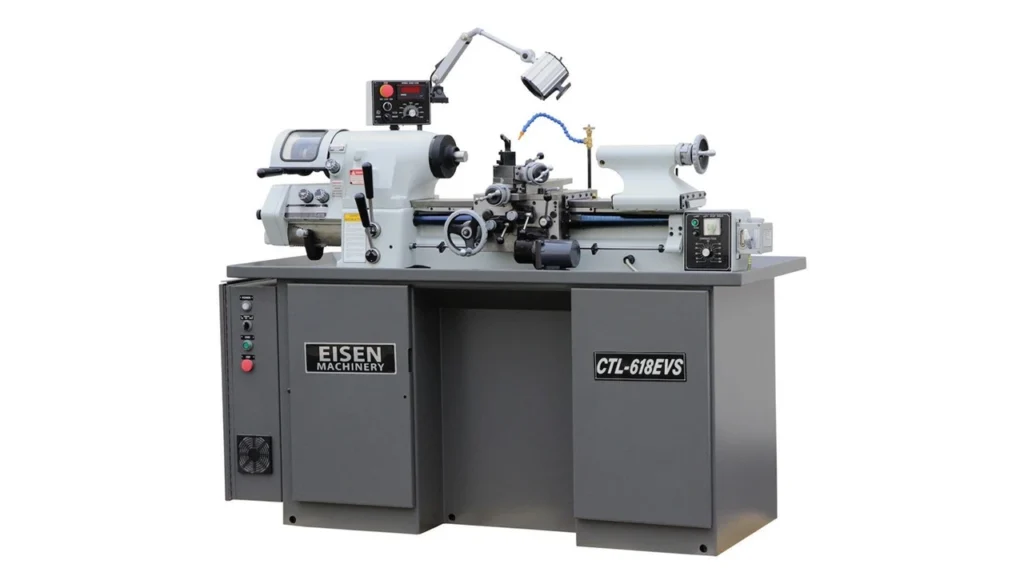
Structure and Capabilities
At first glance, a toolroom lathe closely resembles a standard engine lathe. However, the differences lie in:
- Tighter tolerances and smoother slides on the carriage and cross-slide
- Higher-precision lead screws and feed mechanisms
- Often includes a collet closer for precision part holding
- Equipped with digital readouts (DROs) for accurate tool positioning
- May offer variable speed control and high spindle RPM for fine finishing
This combination of fine adjustment and mechanical robustness allows for both intricate work and moderate-duty turning tasks.
Applications
Toolroom lathes are used in:
- Tool and die manufacturing
- Prototype development and part testing
- Mold shop applications
- Precision maintenance machining
- Technical education and operator training
Where precision and repeatability matter more than speed, toolroom lathes are a perfect fit.
Advantages
- Superior accuracy compared to general-purpose lathes
- Smooth manual controls for fine adjustments
- Flexible enough to handle different types of lathe machine operations
- Great for short runs, repair tasks, or one-off parts
- Minimal setup time, ideal for skilled hands-on machinists
Best For
Workshops focused on precision tooling, mold components, and prototypes, as well as technical schools and repair facilities. Toolroom lathes are best when manual control and dimensional precision are more important than automation or volume.
Specialty Lathes: Tailored Solutions for Unique Needs
While the seven essential types of lathe machines cover the vast majority of machining needs, certain industries demand more specialized solutions. That’s where specialty lathes come in—machines that are custom-engineered for very specific applications, part shapes, or workpiece sizes.
These lathes aren’t always found on a typical shop floor, but in the right hands and environments, they’re indispensable. Below are five notable types of specialty lathes, each designed to meet unique production challenges in sectors like automotive, railway, and heavy equipment manufacturing
Gap Bed Lathe
The gap bed lathe is a modified version of the engine lathe, designed to accommodate larger-diameter workpieces near the headstock area. It features a removable section of the lathe bed that, when detached, creates a “gap” to allow for increased swing capacity. This simple yet effective design makes it ideal for shops that occasionally need to machine oversized parts without investing in a full heavy-duty lathe.
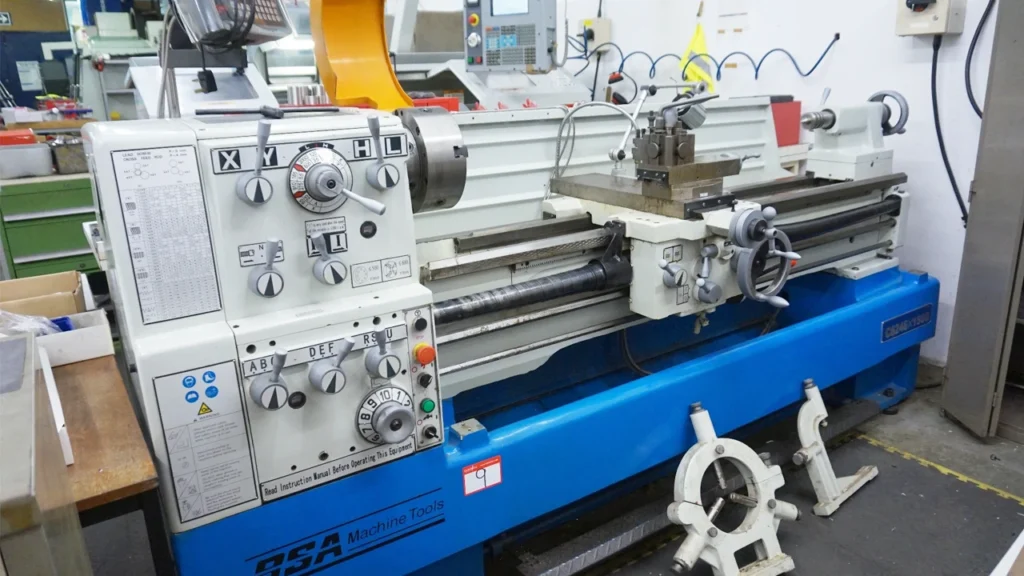
Structure and Working Principle
A gap bed lathe consists of the same basic components as an engine lathe: a headstock, tailstock, carriage, bed, and lead screw. The key difference is a removable section in the bed near the chuck. When removed, this gap enables the mounting and machining of parts with a much larger diameter than the normal swing of the machine would allow.
Once the oversized operation is complete, the gap can be filled again using the original insert, restoring the bed for conventional turning. This design maintains alignment and rigidity while offering increased versatility.
Applications
Gap bed lathes are commonly used in:
- Repair shops that handle both small and large parts
- Power plant and equipment maintenance workshops
- Machining flanges, couplings, pump housings, and pulleys
- Custom fabrication shops dealing with varied workpiece sizes
- Workshops that need to turn large face parts on occasion
They’re an ideal choice for facilities requiring a combination of standard and occasional large-swing machining capabilities.
Advantages
- Increased swing diameter without purchasing a larger lathe
- Versatile for both standard and oversized components
- Cost-effective for low-frequency large part turning
- Maintains the full function of an engine lathe when the gap is closed
- Easy to switch between gap and standard configuration
Best For
General-purpose workshops and custom job shops working in the automotive, railway, and heavy equipment industries. Particularly useful when the need to turn large-diameter components is occasional rather than continuous.
Camshaft Lathe
The camshaft lathe is a high-precision, purpose-built machine designed specifically for turning and contour machining of camshafts—components that demand tight tolerances, repeatability, and complex lobe geometry. Camshaft lathes are essential in automotive engine manufacturing and rebuild applications, where the accurate reproduction of cam profiles is mission-critical.
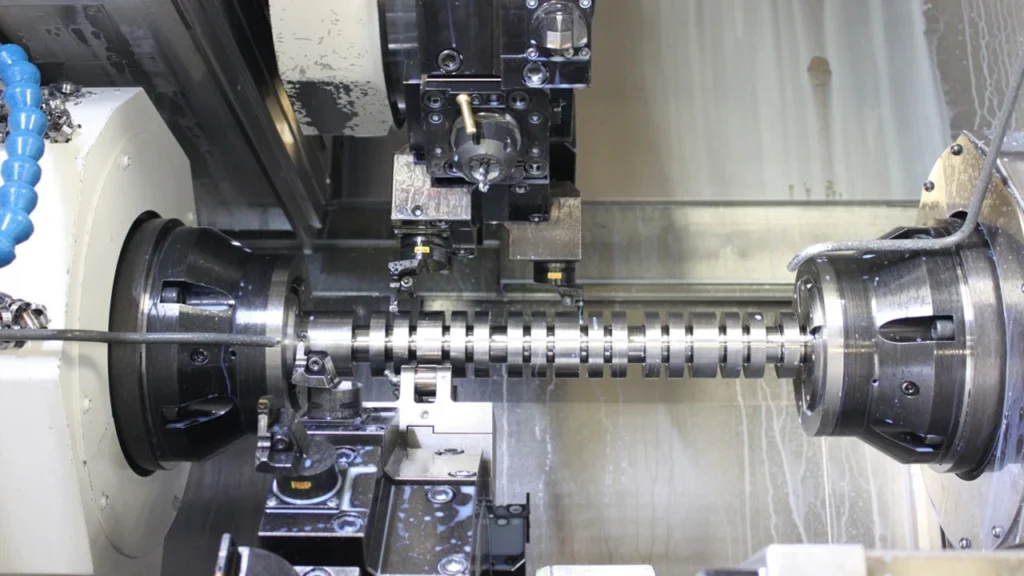
Structure and Working Principle
Camshaft lathes are typically equipped with synchronized spindle systems, CNC contour tracing capabilities, and custom tool holders or turrets. The camshaft blank is held between centers or in custom fixtures, while the machine rotates it at controlled speeds. A cutting tool then traces the predefined cam profile with extreme precision.
Some camshaft lathes also use hydraulic or mechanical profile-following systems, or integrate digital cam data directly into the CNC controller for dynamic path generation. These machines can be adapted for both rough and finish turning operations.
Applications
Camshaft lathes are commonly used in:
- Mass production of automotive camshafts
- High-performance and aftermarket engine tuning
- Motorcycle and small engine manufacturing
- Marine and heavy-duty engine component machining
- Repair or remanufacturing of worn camshaft components
These machines are ideal for repetitive jobs that require extreme consistency in cam lobe profiles and surface finishes.
Advantages
- Designed specifically for eccentric, multi-lobe shaft machining
- High rigidity and spindle stability for long, narrow components
- Supports both rough and finish profiling in one setup
- Reduces reliance on external grinding operations
- Highly accurate cam geometry reproduction at scale
Best For
OEMs and engine part manufacturers in the automotive, motorcycle, and marine industries, particularly those that require batch production of camshafts with consistent profiles and tight tolerances.
Crankshaft Lathe
The crankshaft lathe is a highly specialized lathe machine designed specifically for machining crankshafts—complex components that feature multiple journals, offset crankpins, and require high concentricity, balance, and surface finish. These machines are engineered to handle long, heavy, and often asymmetrical workpieces with multiple machining axes and synchronized control systems.
Crankshaft lathes are essential in the mass production and reconditioning of crankshafts for internal combustion engines used in automotive, marine, and heavy equipment industries.
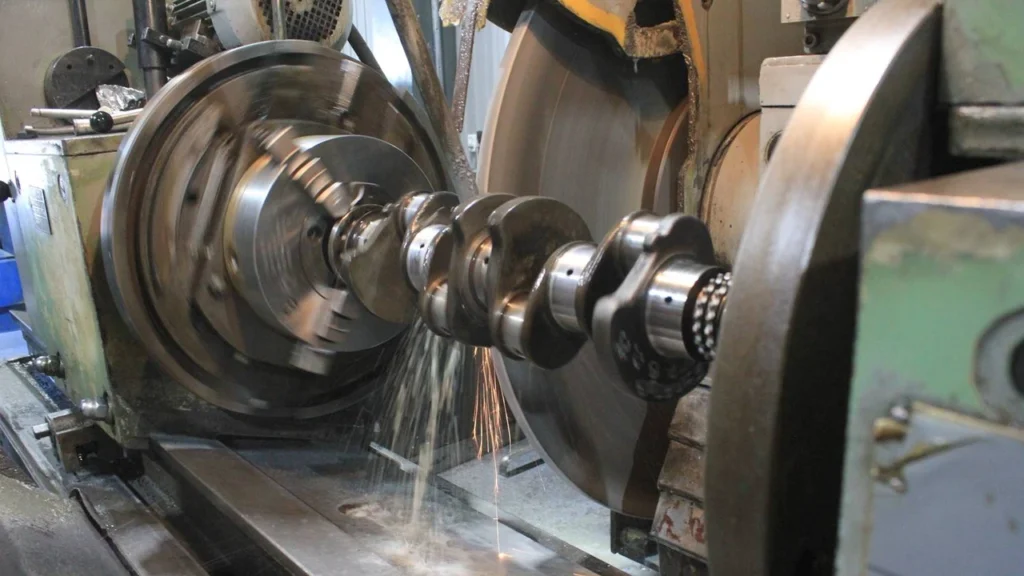
Structure and Working Principle
A crankshaft lathe typically features a robust machine bed, extra-wide support bases, and a spindle system capable of handling eccentric rotation. The workpiece is usually mounted between centers or in custom fixtures, and indexed to allow access to multiple pin positions.
These machines are equipped with CNC or hydraulic control systems that enable precise movement and positioning of cutting tools, often in multi-axis configurations. Counterweights, steady rests, and tailstocks are used to minimize vibration and ensure stability throughout the operation. Some crankshaft lathes also incorporate in-process measuring systems to verify roundness, alignment, and surface quality during machining.
Applications
Crankshaft lathes are commonly used in:
- Automotive engine manufacturing
- Remanufacturing of worn crankshafts
- Marine and locomotive diesel engine component production
- Heavy-duty engine crankshaft repair and regrinding
- Custom fabrication of large crankshafts for industrial compressors
They are indispensable for ensuring dynamic balance, consistent journal dimensions, and optimal surface finish on these critical rotating components.
Advantages
- Built for machining long and heavy shafts with eccentric geometry
- Ensures high accuracy and concentricity across multiple crank pins
- Reduces vibration and tool deflection during machining
- Allows for rough and finish turning in one machine
- Supports advanced CNC control for automated journal sequencing
Best For
Engine builders, automotive manufacturers, marine propulsion system suppliers, and heavy equipment OEMs that require reliable and repeatable machining of crankshafts with complex geometry and critical tolerances.
Wheel Lathe
The wheel lathe is a heavy-duty lathe machine specifically designed for machining the wheels, axles, and wheelsets of rail vehicles such as trains, trams, and subways. Unlike general-purpose lathes, wheel lathes are engineered to handle the large diameter, high weight, and specific profile requirements of railway wheel components.
These machines are crucial for both new wheel production and in-service maintenance, ensuring safety, stability, and smooth operation of rolling stock on the tracks.
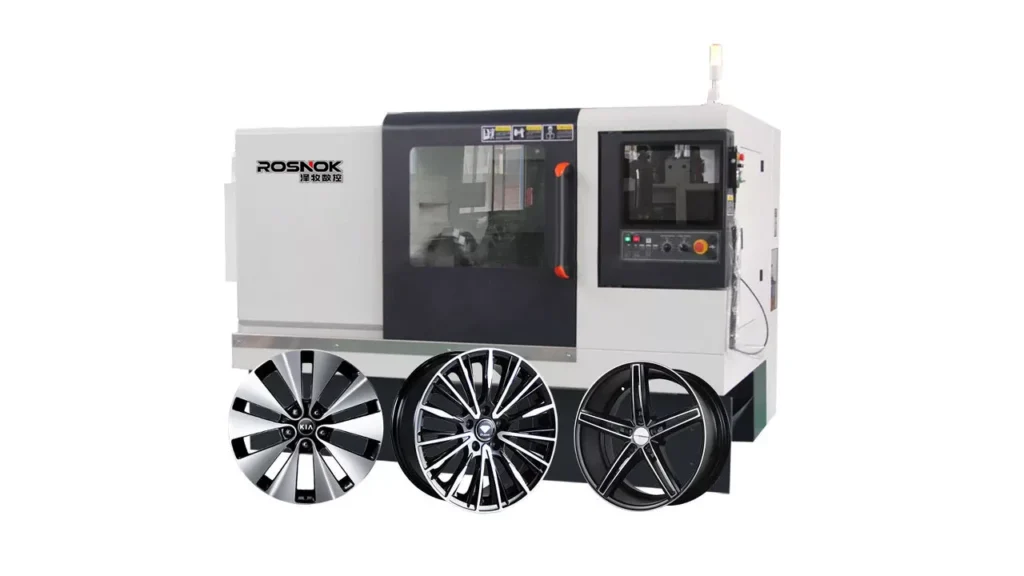
Structure and Working Principle
A typical wheel lathe is built with a wide, reinforced bed, high-torque spindle motors, and precision slideways. Depending on the configuration, wheel lathes may support:
- Underfloor machining: The wheelset remains mounted on the rail vehicle while the lathe trims the profile in place.
- Above-floor machining: The entire wheelset is removed from the train and mounted onto the lathe between chucks or rollers.
Specialized tooling is used to re-profile the wheel tread and flange, maintaining the exact geometry required by rail standards. Some advanced wheel lathes include CNC control, automated measurement systems, and profile compensation based on wear data.
Applications
Wheel lathes are commonly used in:
- Railway depots and maintenance facilities
- Rolling stock manufacturing plants
- Urban subway and light rail vehicle workshops
- Train wheel re-profiling for service extension
- Wheelset inspection and refurbishment operations
They are vital to maintaining wheel-rail contact, reducing vibrations, and preventing derailments caused by wheel wear or irregularities.
Advantages
- Designed to handle heavy and large-diameter railway wheels
- Allows for re-profiling without disassembling the axle (underfloor types)
- High repeatability and conformance to rail geometry standards
- Reduces wheel noise, vibration, and wear on both wheels and rails
- Extends wheel life and ensures consistent rolling performance
Best For
Railway maintenance depots, rolling stock manufacturers, and urban transit authorities requiring accurate, efficient machining of train wheels and axles to ensure operational safety and longevity.
Floor-Type Lathe
The floor-type lathe, also known as a heavy-duty floor lathe, is a specialized turning machine designed for extremely long, heavy, or large-diameter workpieces. Unlike traditional lathes that feature a continuous bed structure, the floor-type lathe is built with a modular, ground-mounted guide system. Its components are distributed along precision floor rails, allowing the machine to handle parts that are several meters long and weigh multiple tons.
This type of lathe is widely used in energy, marine, shipbuilding, and heavy industrial applications, where conventional lathe beds cannot support the size or mass of the components being machined.
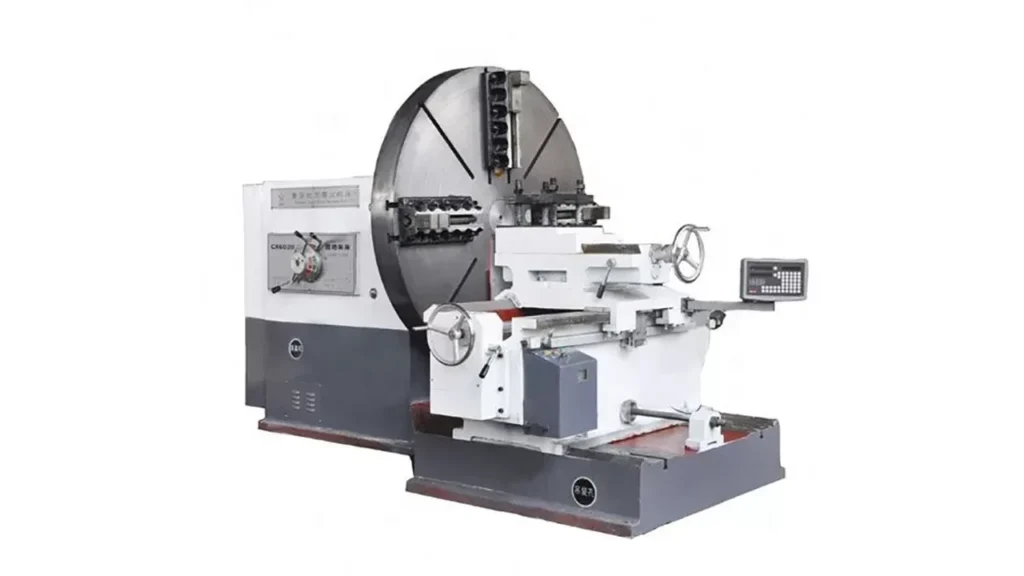
Structure and Working Principle
Floor-type lathes do not use a single integrated bed. Instead, the machine’s major assemblies—headstock, carriage, tailstock, steady rests, and tool support systems—are mounted on independent mobile platforms that travel along floor-level rails. These rails act as the guiding foundation, enabling long-range, high-precision linear motion.
The spindle and drive systems are designed to deliver extremely high torque for cutting oversized shafts, rollers, and tubes. Additional steady rests and support frames are positioned as needed along the length of the workpiece to minimize deflection, vibration, and tool chatter. Many modern models are CNC-controlled for multi-axis machining and adaptive positioning.
Applications
Floor-type lathes are commonly used in:
- Large power generation components (e.g., turbine shafts, generator rotors)
- Long marine propulsion shafts and rudder assemblies
- Metallurgical rolls and industrial rollers
- Extra-long hydraulic cylinders and oil drilling components
- Structural columns and pipes in heavy construction equipment
These machines are essential for turning extra-long parts with consistent tolerances and smooth finishes over extended working lengths.
Advantages
- No length limitation—extendable rails accommodate extremely long workpieces
- Modular system allows flexible machine setup and layout
- Designed to handle ultra-heavy parts with minimal deformation
- High rigidity and torque for deep roughing and fine finishing
- Available with advanced CNC control for precise, large-format machining
Best For
Heavy industry manufacturers in sectors such as energy, shipbuilding, and infrastructure, who require large-scale, precision turning of oversized shafts, pipes, and rollers that exceed the physical limits of conventional lathe designs.
How to Choose the Right Type of Lathe Machine
Selecting the right machine from the many available types of lathe is more than a technical decision—it’s a strategic one that affects machining accuracy, production efficiency, and long-term ROI. Whether you’re setting up a new workshop or upgrading your existing equipment, understanding how different types of lathes align with your operational needs is essential.
This section offers a clear framework to help you choose the most suitable lathe machine type based on your industry, production volume, material requirements, and budget constraints.
Know Your Application: What Are the Types of Lathe Machines for Your Industry?
The first step in choosing the right machine is knowing what operations you’ll perform most often. Each type of lathe machine is designed to serve specific applications:
Industry | Recommended Types of Lathe | Why It’s Suitable |
---|---|---|
Automotive Manufacturing | CNC Lathe, Camshaft Lathe, Crankshaft Lathe | High-volume precision machining |
Railway Maintenance & Production | Wheel Lathe, Gap Bed Lathe | Large diameters, re-profiling |
Aerospace | Swiss-Type CNC Lathe, Turning Center | Micron tolerances, complex parts |
Oil & Gas | Pipe Threading Lathe, Floor-Type Lathe | Long workpieces, deep threads |
Tooling & Prototyping | Toolroom Lathe, Engine Lathe | Fine adjustment, short runs |
Heavy Equipment & Marine | Floor-Type Lathe, Crankshaft Lathe | Large shafts, structural loads |
Understanding your primary industry use case will help narrow down the types of lathe machines that are most relevant to your needs.
Match Lathe Types to Your Production Volume
Not all lathe types are designed for the same production scale:
- Low-volume, high-flexibility
Ideal machines: Toolroom Lathe, Engine Lathe, Gap Bed Lathe
Suitable for: Prototyping, maintenance, custom fabrication - Mid-to-high volume with complexity
Ideal machines: CNC Lathe, Turning Center
Suitable for: Batch production with precision and repeatability - High-volume, automated production
Ideal machines: Swiss-Type CNC Lathe, Automatic CNC Lathe
Suitable for: Mass production with minimal operator intervention
This breakdown helps align your lathe machine types and operations with business goals and capacity planning.
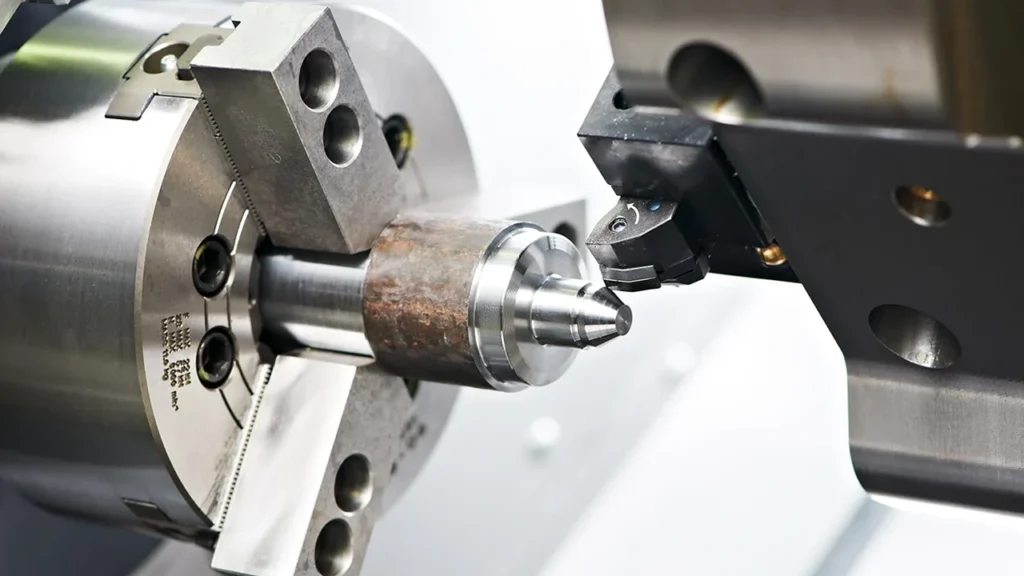
Consider Workpiece Size, Shape, and Material
Different types of lathe machines handle different workpiece dimensions and tolerances:
- Small, intricate parts → Swiss-Type CNC Lathe
- Large-diameter parts → Vertical Lathe, Gap Bed Lathe
- Long shafts → Floor-Type Lathe, Crankshaft Lathe
- Threaded pipe ends → Pipe Threading Lathe
- Multi-axis contouring → Turning Center
Material hardness also matters. For titanium, hardened steel, or exotic alloys, choose lathe types with heavy-duty construction, high-torque spindles, and proper chip removal systems.
Manual or CNC? Understanding Lathe Machine Operations
One of the most common questions is: Should I choose a manual lathe or a CNC lathe?
Criteria | Manual Lathe | CNC Lathe |
---|---|---|
Control Method | Hand-operated | Computer-controlled (G-code) |
Flexibility | High for custom jobs | High for repeatability |
Operator Skill Needed | High | Moderate to High |
Speed & Efficiency | Low to Moderate | High |
Best Use | Repair, training, prototypes | Production, consistency, volume |
In most modern factories, both manual and CNC types of lathe coexist to balance flexibility and throughput.
Total Cost of Ownership (TCO) and After-Sales Support
Beyond machine price, consider:
- Installation costs
- Power requirements
- Maintenance and wear-part availability
- Downtime risk
- After-sales support
At Rosnok, we provide all types of lathe machines with CE, ISO, and TUV certifications, backed by responsive technical support and global parts availability. We help ensure your investment delivers performance, durability, and ROI over the long term.
Final Tips on Choosing the Right Lathe Machine
- Know how many types of lathe machine options fit your specific need—don’t overbuy or underinvest
- Think ahead—can the machine scale with your future production plans?
- Ask your supplier for test cuts, sample programs, and post-sale training options
- Verify lathe machine types and operations your team is trained for
- If in doubt, start with a versatile type of lathe like an engine lathe or turning center and expand as needed
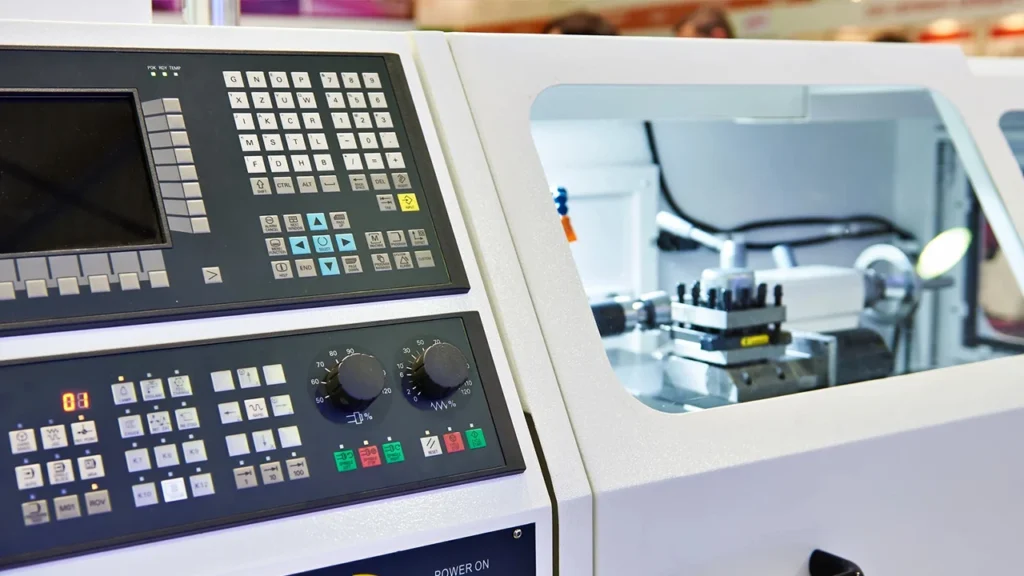
Conclusion: Types of Lathe Machines
Understanding the different types of lathe machines is essential for making informed, future-proof decisions in modern machining. From the versatile engine lathe to specialized models like camshaft and floor-type lathes, each type serves a distinct purpose, aligned with specific production needs and industry demands.
Choosing the right type of lathe is not just about machine specs—it’s about matching the tool to your workflow, part complexity, and long-term goals. Whether you prioritize flexibility, automation, or heavy-duty performance, there’s a lathe designed for your operation.
At Rosnok, we offer a full range of lathe machine types to meet the unique challenges of global manufacturers. If you’re ready to elevate your metalworking precision, our team is here to help you find the machine that fits your vision—and your business.
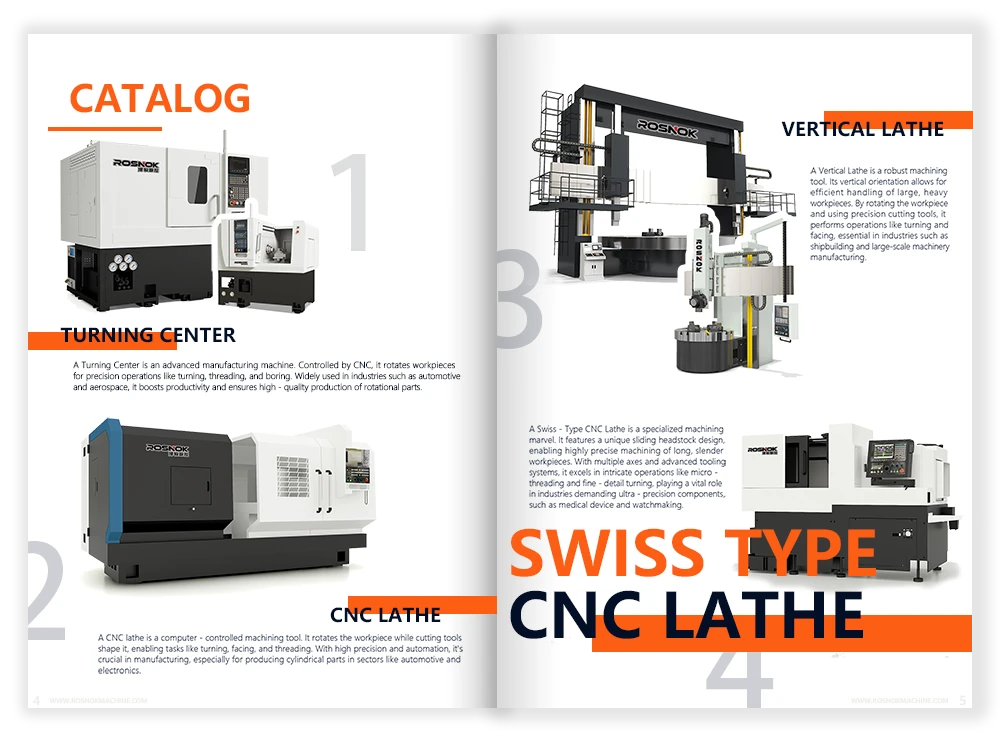
FAQ
What materials can be machined on a lathe machine?
Lathe machines can machine a wide range of materials, including various steels, stainless steel, aluminum, brass, copper, titanium, plastics, and composite materials. Cutting tools and machine settings must be adjusted based on the material properties.
Is it possible to perform threading on all types of lathe machines?
Most lathe machines can perform threading operations, but the available threading capabilities depend on the machine type and control system. Specialized lathes, like pipe threading lathes, offer enhanced threading functions and support for larger thread profiles.
Can one lathe machine handle different types of parts?
Yes. A versatile lathe machine can handle a variety of part types by using different tools and setups. However, highly specialized parts or large variations in size and shape may require dedicated lathe machines optimized for those specific applications.