Have you ever wondered what a 3 jaw chuck does and why it’s so important in machining? Do you find it frustrating when your workpiece shifts, leading to inaccurate cuts and wasted time? Are you searching for a reliable solution to enhance precision and efficiency in your machining process? A 3 jaw chuck could be the answer.
A 3-jaw chuck is a self-centering work-holding device widely used in lathes, milling machines, and other various machine tools.It features three jaws that move simultaneously, enabling quick and precise gripping of round or hexagonal workpieces. Its design ensures even pressure distribution, minimizing misalignment and enhancing machining accuracy. Whether you’re a professional machinist or an avid hobbyist, understanding the mechanics of a 3-jaw chuck can optimize your workflow, improve precision, and streamline your machining process.
This guide covers the basics of a 3-jaw chuck—how it works, its benefits, and its drawbacks. We’ll compare it to other chuck types and share tips for maintenance and best use to help you get the most out of it.
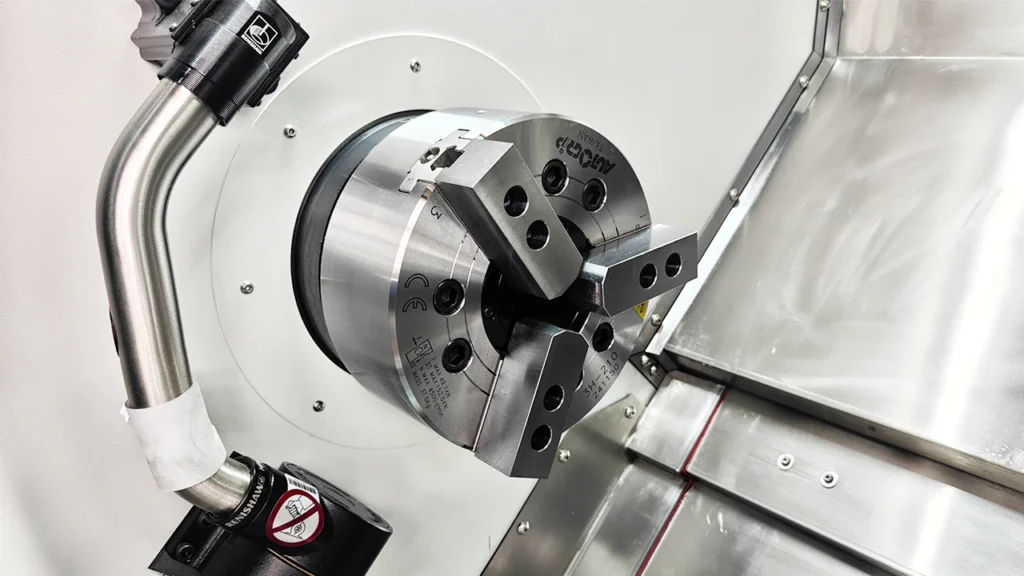
Chuck Definition: What Is a Chuck?
A chuck is a mechanical device used to hold a workpiece securely in place during machining operations. It is commonly mounted on the spindle of lathes, milling machines, and other machine tools, allowing for precise control over the workpiece. By providing stability, it ensures precise cuts, minimal vibration, and improved accuracy. Chucks come in various designs, each tailored to specific machining needs and workpiece shapes, making them essential in precision manufacturing.
What Is a 3 Jaw Chuck
A 3 jaw chuck is a self-centering work-holding device widely used in lathes, milling machines, and other various machine tools. It features three jaws that move simultaneously, enabling quick and precise gripping of round or hexagonal workpieces. Its design ensures even pressure distribution, minimizing misalignment and enhancing machining accuracy. Whether you’re a professional machinist or an avid hobbyist, understanding the mechanics of a 3 jaw chuck can optimize your workflow, improve precision, and streamline your machining process.
In this guide, we’ll break down the structure, functionality, advantages, and best practices of a 3 jaw chuck to help you maximize its potential in your projects. While it offers speed and convenience, it also has its limitations. Keep reading to explore its pros and cons, compare it to other chuck types, and learn expert tips for maintenance and optimal use.
How Does A 3 Jaw Chuck Work
A 3 jaw chuck operates on a self-centering mechanism, meaning all three jaws move simultaneously when adjusted using a chuck key. This design ensures the workpiece is automatically centered, reducing setup time and improving machining efficiency. The chuck is mounted on the spindle of a lathe, milling machine, or other machine tool, where it grips the workpiece firmly during machining operations.
The key component of a 3 jaw chuck is the scroll plate, which is a spiral-shaped disk inside the chuck body. When the chuck key is turned, the scroll plate rotates, engaging the jaw teeth and moving them inward or outward at the same rate. This synchronized movement makes it ideal for gripping cylindrical and hexagonal workpieces.
Unlike 4 jaw chucks, where each jaw moves independently, a 3 jaw chuck does not require manual adjustments to center the workpiece. However, this convenience comes at a slight cost—since all jaws move together, a 3 jaw chuck cannot hold irregularly shaped workpieces or adjust for workpieces that require off-center machining.
key steps in how a 3 jaw chuck works
- Mounting the chuck – The 3 jaw chuck is attached to the spindle of a lathe or milling machine, either through a direct screw mounting or a cam-lock system.
- Inserting the workpiece – The workpiece is placed between the three jaws, which are evenly spaced at 120° apart.
- Tightening with the chuck key – Turning the chuck key rotates the scroll plate, simultaneously moving all three jaws inward or outward to secure the workpiece.
- Ensuring stability – The even pressure distribution of the jaws minimizes misalignment, keeping the workpiece firmly in place.
- Machining the workpiece – With the workpiece securely held, machining operations such as turning, drilling, and facing can be performed with precision.
Because of its self-centering nature, a 3 jaw chuck is perfect for high-speed, repetitive machining where quick setup and accurate alignment are required. It is widely used in CNC and manual lathes, as well as some milling applications where rotational work-holding is necessary.
Common Types of 3 Jaw Chucks
Not all 3 jaw chucks are the same. While they share a common self-centering mechanism, different types of 3 jaw chucks are designed for specific machining applications. Choosing the right type can improve efficiency, accuracy, and productivity in machining operations.
Manual 3 Jaw Chuck
A manual 3 jaw chuck is the most common type found in traditional lathe machines. It operates using a chuck key, which rotates the scroll plate to move the jaws simultaneously. This type is widely used for general machining tasks and offers a balance of cost, convenience, and precision.
✔ Best for: General machining, lathe work, small-to-medium production runs.
✔ Advantages: Easy to use, cost-effective, widely available.
✖ Limitations: Requires manual adjustments, which slows down workflow in high-production environments.
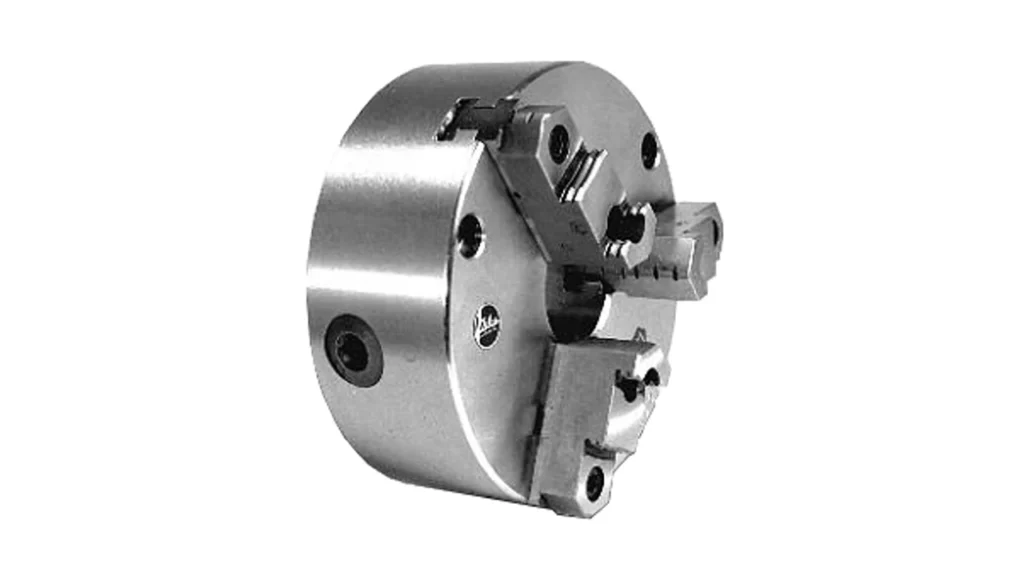
Hydraulic 3 Jaw Chuck
A hydraulic 3 jaw chuck is controlled by hydraulic pressure, allowing for automatic clamping and unclamping of the workpiece. This type is widely used in CNC machining centers and high-speed production lines, where efficiency and repeatability are essential.
✔ Best for: CNC lathes, high-speed machining, mass production.
✔ Advantages: Fast clamping, high repeatability, consistent gripping force.
✖ Limitations: More expensive than manual chucks, requires a hydraulic power system.
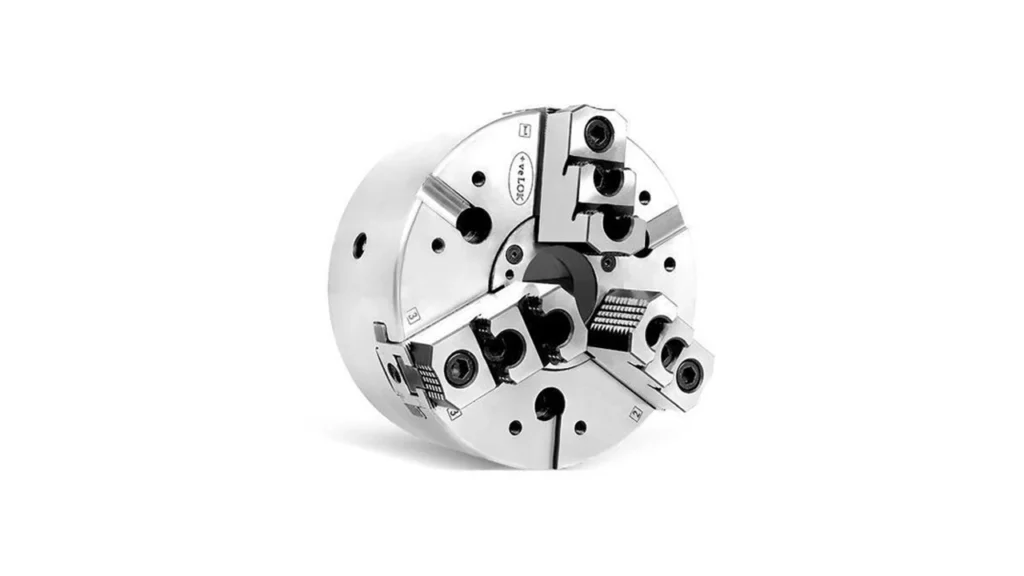
Pneumatic 3 Jaw Chuck
A pneumatic 3 jaw chuck operates using compressed air instead of hydraulic fluid. It allows for quick clamping and unclamping while maintaining good precision. It is commonly used in light-to-medium-duty machining applications, particularly where hydraulic power is not available.
✔ Best for: Automation, light-to-medium machining, clean environments.
✔ Advantages: Fast operation, lower maintenance compared to hydraulic chucks.
✖ Limitations: Less gripping force than hydraulic chucks, requires an air supply system.
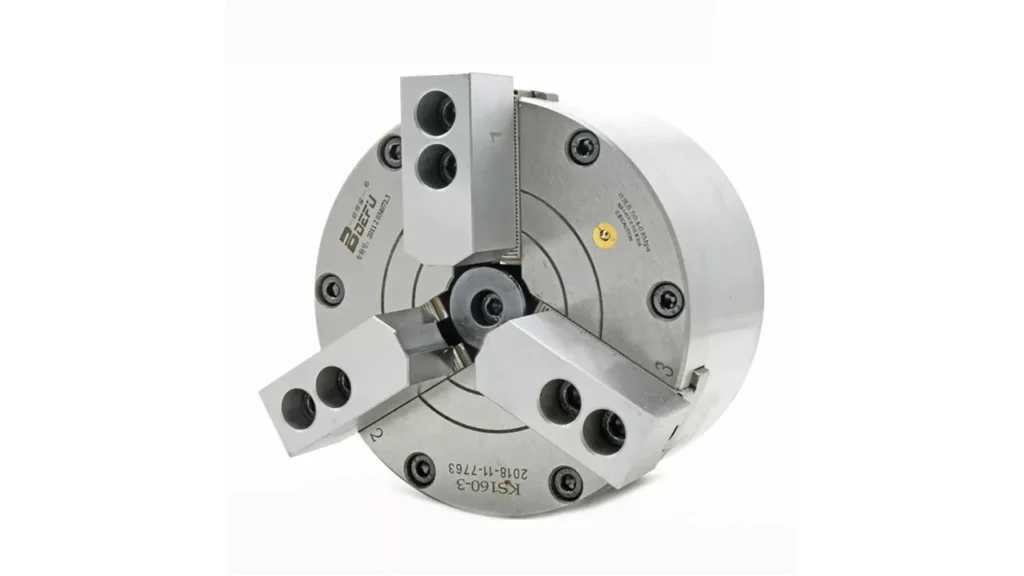
Power 3 Jaw Chuck
A power 3 jaw chuck is an advanced version of hydraulic and pneumatic chucks, commonly used in high-precision CNC machining. It features an integrated actuation system that applies consistent force to clamp the workpiece with extreme accuracy. Some power chucks also include quick-change jaws, allowing for fast switching between different workpieces.
✔ Best for: High-precision CNC machining, high-volume production, robotic automation.
✔ Advantages: Quick setup, consistent clamping force, high precision.
✖ Limitations: More complex, requires a dedicated power system.
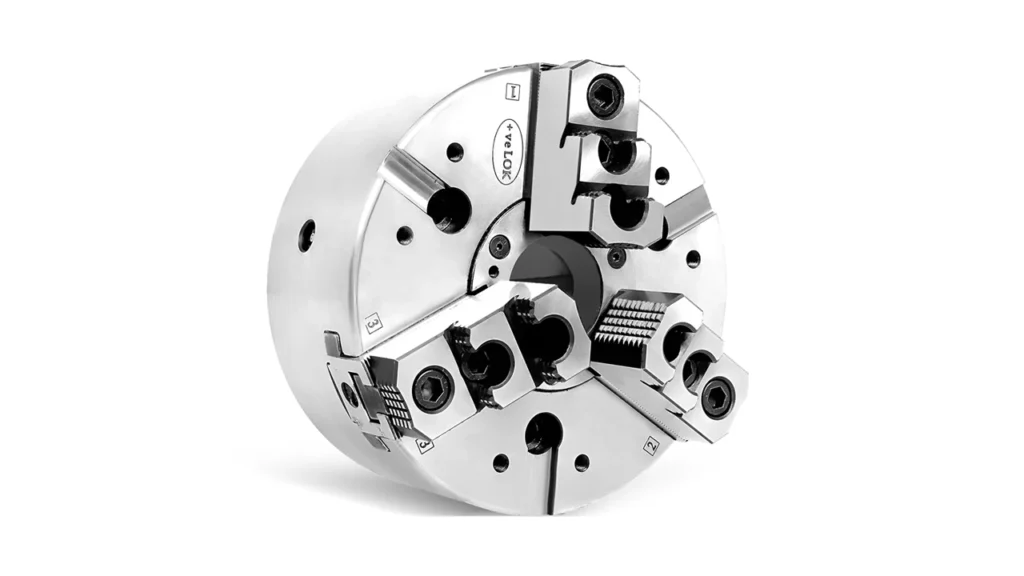
Electric 3 Jaw Chuck
An electric 3 jaw chuck is controlled by an electric motor, eliminating the need for hydraulic or pneumatic systems. This makes it ideal for clean environments such as electronics manufacturing and precision automation. These chucks can be programmed for variable gripping force, making them more versatile in delicate machining applications.
✔ Best for: CNC machining, robotic automation, environments without hydraulic/pneumatic power.
✔ Advantages: No need for external fluid/air systems, programmable clamping force, energy-efficient.
✖ Limitations: Lower clamping force than hydraulic chucks, higher initial cost, more complex electronics.
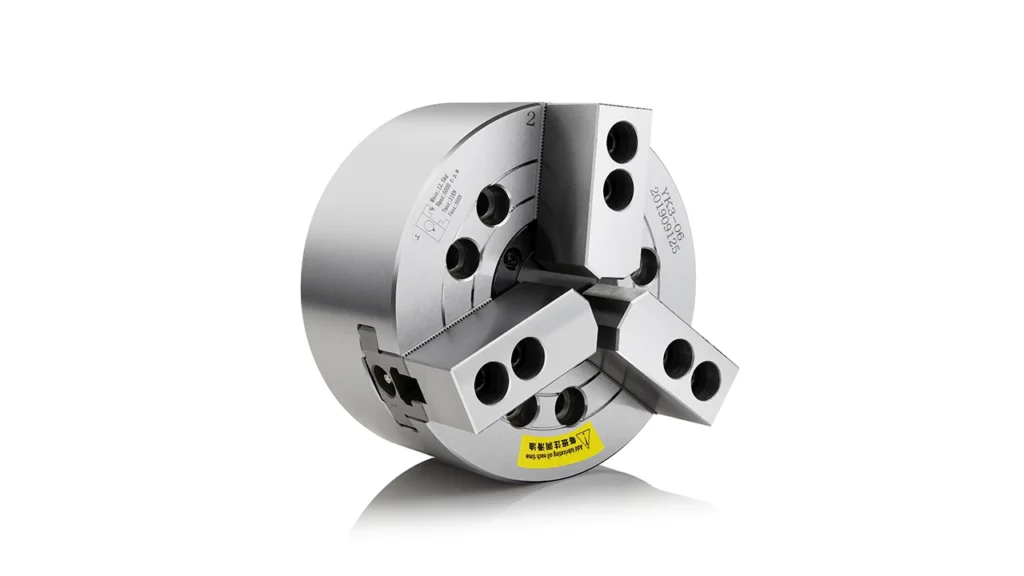
Adjustable 3 Jaw Chuck
An adjustable 3 jaw chuck allows machinists to fine-tune each jaw manually, reducing runout and increasing accuracy. This is useful for applications requiring higher precision than a standard self-centering chuck can provide.
✔ Best for: High-precision machining, reducing runout.
✔ Advantages: More accurate than standard 3 jaw chucks, minimizes errors in precision work.
✖ Limitations: Requires manual adjustments, more time-consuming to set up.
Soft Jaw 3 Jaw Chuck
A soft jaw 3 jaw chuck features machinable soft jaws that can be custom-shaped to fit specific workpieces. This improves accuracy and reduces workpiece damage, making it ideal for delicate materials and high-precision work.
✔ Best for: Machining delicate or irregular workpieces, reducing surface marring.
✔ Advantages: Customizable grip, better accuracy for special parts.
✖ Limitations: Jaws require machining, not as durable as hardened jaws.
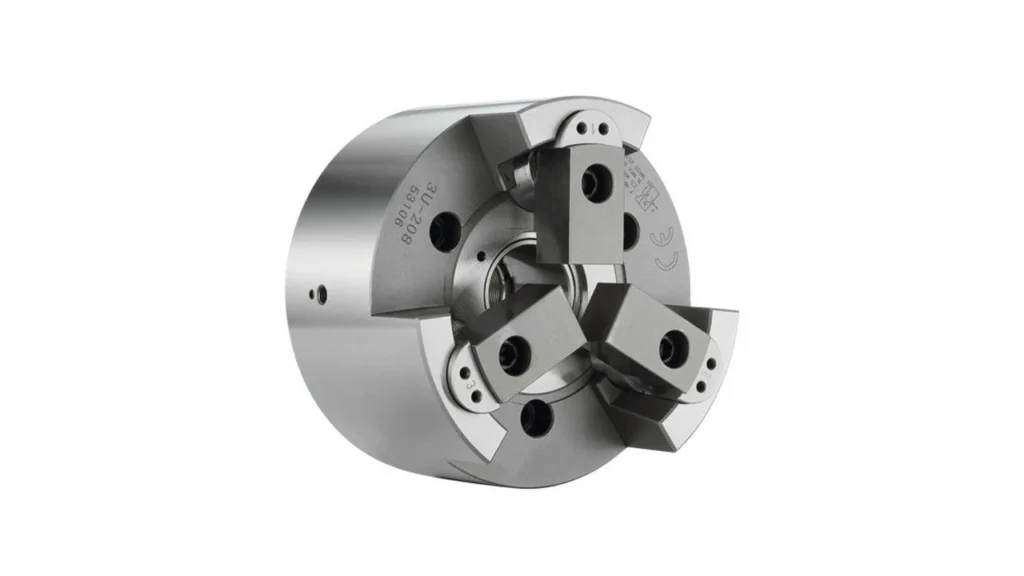
Key Differences Between Types Of 3 Jaw Chucks
Type | Best For | Advantages | Limitations |
---|---|---|---|
Manual | General machining | Easy to use, cost-effective | Slower clamping |
Hydraulic | CNC, high-speed production | Fast, repeatable clamping | Expensive, requires hydraulic system |
Pneumatic | Automation, light-duty work | Quick clamping, low maintenance | Requires air supply, less force |
Power | High-precision CNC machining | Consistent force, quick setup | Complex, requires power system |
Electric | CNC, automation, clean environments | No external fluid/air needed, programmable force | Lower clamping force, complex electronics |
Adjustable | High-precision manual work | Reduces runout, better accuracy | Requires manual tuning |
Soft Jaw | Delicate/custom workpieces | Customizable grip, protects workpiece | Jaws require machining |
By understanding the different types of 3 jaw chucks, machinists can choose the best option based on their machining requirements, precision needs, and production speed.
4. Main Components of a 3 Jaw Chuck
A 3 jaw chuck consists of several key components that work together to provide a secure grip on the workpiece. Each part plays a crucial role in ensuring stability, precision, and ease of use during machining operations. Understanding these components will help machinists make the most of their 3 jaw chuck and maintain its efficiency over time.
Chuck Body
The chuck body is the main structural component of the 3 jaw chuck. Typically made from hardened steel or cast iron, it houses all internal mechanisms, providing rigidity and durability. It is designed to withstand high-speed machining forces while maintaining precision.
- Function: Holds all moving parts inside, ensuring precision and stability.
- Materials Used: Alloy steel, cast iron, or forged steel for high strength.
- Common Sizes: Found in mini 3 jaw chucks (50mm, 80mm) to large 3 jaw chucks (10 inch 3 jaw chuck, 12 inch 3 jaw chuck).
Scroll Plate
The scroll plate is a spiral-shaped disk located inside the chuck body. It is responsible for the synchronized movement of the three jaws. When the chuck key is turned, the scroll plate rotates, engaging the teeth of the jaws and moving them inward or outward at an equal rate. This mechanism ensures automatic centering, making the 3 jaw chuck ideal for quick and repetitive machining operations.
- Function: Moves the jaws evenly to grip cylindrical or hexagonal workpieces.
- Key Feature: Ensures automatic centering, reducing the need for manual adjustments.
- Common Types: Found in manual 3 jaw chucks, pneumatic 3 jaw chucks, and hydraulic 3 jaw chucks.
Jaws
A 3 jaw chuck features three equally spaced jaws that grip the workpiece securely. The jaws move simultaneously when adjusted, ensuring uniform pressure distribution.
Types Of 3 Jaw Chuck Jaws:
- Hard Jaws – Used for standard metal machining. Provides a firm grip but is not adjustable.
- Soft Jaws – Custom-machined for special workpieces, reducing damage to delicate materials.
- Reversible Jaws – Can be flipped to grip either internal or external diameters.
✔ Function: Holds the workpiece securely in place.
✔ Key Feature: Even pressure distribution prevents misalignment.
✔ Common Variants: 3 jaw adjustable chuck for fine-tuned accuracy, 3 jaw power chuck for CNC automation.
Pinion Gears
Pinion gears are small internal gears that engage with the scroll plate. When the chuck key is inserted and turned, these gears transfer the motion to the scroll plate, allowing for smooth and even jaw movement.
- Function: Transfers motion from the chuck key to the scroll plate.
- Common Use: Found in 3 jaw manual chucks for traditional lathes and mills.
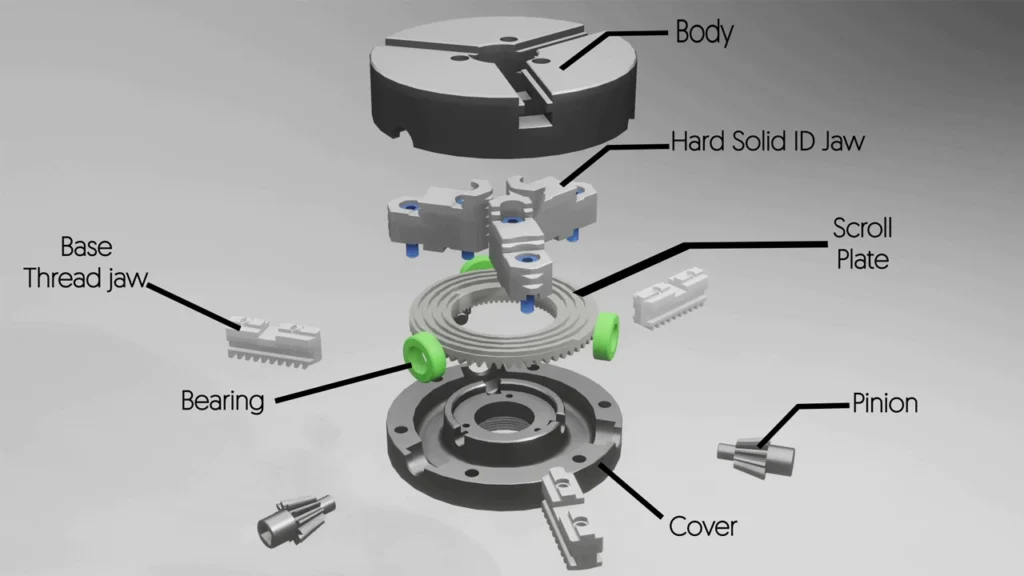
Chuck Key
The chuck key is a T-shaped tool used to tighten or loosen the jaws. It engages with the pinion gears to rotate the scroll plate, controlling the gripping force applied to the workpiece. Proper use of the chuck key ensures secure clamping without over-tightening, which could damage the chuck or workpiece.
- Function: Adjusts the jaw position for gripping or releasing the workpiece.
- Best Practices: Avoid over-tightening, as it may wear down the scroll plate.
Back Plate (Optional)
Some 3 jaw chucks feature a removable back plate, which allows for easy mounting onto different machine spindles. The back plate ensures a secure connection between the chuck and the machine, maintaining alignment and stability during operation.
key functions of each component
Component | Function |
---|---|
Chuck body | Provides structural support and houses internal mechanisms |
Scroll plate | Moves jaws simultaneously for automatic centering |
Jaws | Grips the workpiece securely |
Pinion gears | Transmit motion from the chuck key to the scroll plate |
Chuck key | Adjusts jaw movement by rotating the scroll plate |
Back plate | Helps in mounting the chuck to different machine spindles |
Each of these components works together to make the 3 jaw chuck an efficient, reliable, and widely used work-holding tool in machining operations.
Advantages of a 3 Jaw Chuck
A 3 jaw chuck is one of the most widely used work-holding devices in machining due to its self-centering mechanism, quick setup, and strong gripping power. It is commonly used in lathe 3 jaw chucks, 3 jaw chucks for milling machines, and even 3 jaw chucks for drill presses. Understanding its advantages helps machinists maximize efficiency and precision.
Quick and Easy Setup
One of the biggest advantages of a 3 jaw chuck is its fast and simple setup. Unlike a 4 jaw chuck, which requires independent jaw adjustments, a 3 jaw chuck automatically centers the workpiece.
- Self-Centering Feature – Ensures the workpiece is properly aligned without manual adjustments.
- Time-Saving – Ideal for high-volume production, where quick part changes are required.
- Effortless Operation – Requires only a chuck key to tighten or loosen the jaws.
This makes it perfect for CNC 3 jaw chucks, manual lathes, and 3 jaw chucks for wood lathes, where efficiency is key.
Strong and Uniform Gripping Force
The scroll plate mechanism of a 3 jaw chuck ensures that all jaws apply equal pressure on the workpiece. This results in:
- Firm Grasp on Round and Hexagonal Workpieces – Prevents slipping or movement during machining.
- Better Balance – Reduces the chances of vibration, improving surface finish quality.
- High Stability – Essential for 3 jaw metal lathe chucks and 3 jaw universal chucks.
For machinists working with lathe machine 3 jaw chucks, this even grip distribution means smoother cuts and more accurate machining.
Versatile Applications Across Industries
A 3 jaw chuck is used in various machining applications, including:
- Turning Operations – Common in 3 jaw lathe chucks for shaping cylindrical parts.
- Drilling Applications – Used in 3 jaw drill chucks and 3 jaw chucks for drill presses.
- Milling Machines – Securely holds workpieces for cutting and shaping.
- Woodworking – Found in 3 jaw chucks for wood lathes.
Additionally, large variations like 10-inch 3 jaw chucks and 12-inch 3 jaw chucks allow for heavy-duty machining, while mini 3 jaw chucks cater to small precision tasks.
High Accuracy and Repeatability
The 3 jaw chuck self-centering mechanism ensures that each workpiece is clamped in the same position every time. This results in:
- Consistent Machining Results – Improves accuracy across multiple workpieces.
- Minimal Adjustments – Reduces setup time compared to 3 jaw independent chucks.
- Improved Alignment – Essential for precision 3 jaw chucks and high-speed CNC operations.
This advantage is particularly useful in 3 jaw self-centering chucks used for mass production.
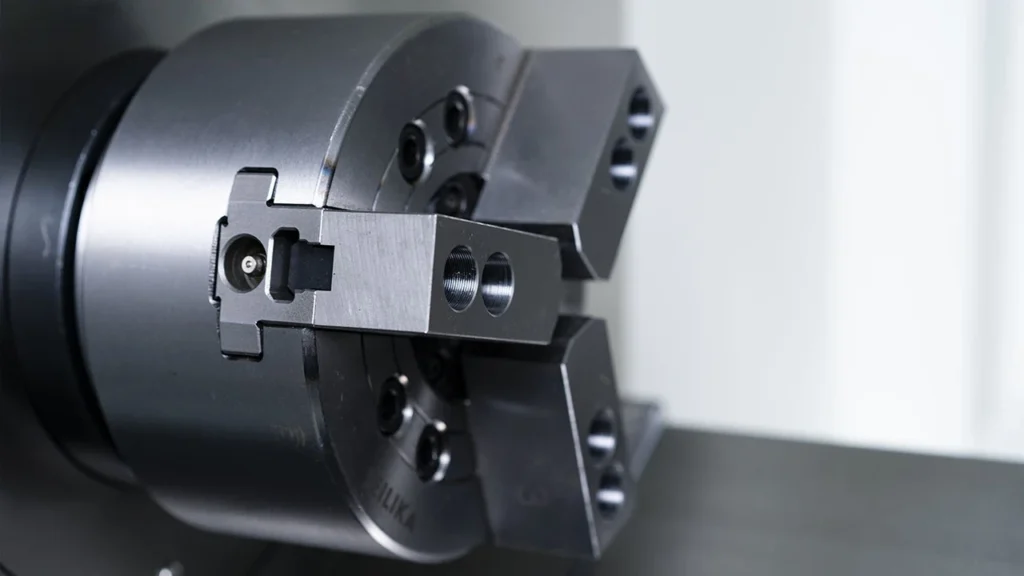
Compatibility with Different Workpiece Sizes
From mini 3 jaw chucks (50mm, 80mm) to large 3 jaw chucks (10-inch, 12-inch), there is a wide range of sizes available, making them suitable for:
- Small Precision Parts – Using 2-inch 3 jaw chucks and 3-inch 3 jaw chucks.
- Medium-Sized Workpieces – With 6-inch 3 jaw chucks and 8-inch 3 jaw chucks.
- Heavy-Duty Machining – Using 10-inch 3 jaw chucks and 12-inch 3 jaw lathe chucks.
Additionally, options like adjustable 3 jaw chucks and centering 3 jaw chucks allow for greater flexibility when working with different materials.
Low Maintenance Requirements
Unlike hydraulic 3 jaw chucks or pneumatic 3 jaw chucks, a manual 3 jaw chuck requires minimal maintenance.
- Durable Construction – Made from hardened steel for long-term use.
- Simple Cleaning Process – Regularly removing metal shavings extends lifespan.
- Fewer Moving Parts – Compared to power 3 jaw chucks, reducing maintenance needs.
For 3 jaw lathe chucks used in gener al machining, this results in longer service life with less frequent replacements.
Key Advantages Summary
Advantage | Benefit |
---|---|
Quick Setup | Saves time; self-centering feature eliminates manual adjustments. |
Strong Grip | Even pressure distribution reduces slipping and misalignment. |
Versatility | Used in lathes, mills, drills, and woodworking. |
High Accuracy | Ensures repeatability; essential for precision machining. |
Wide Size Range | Available in mini to large sizes for various applications. |
Low Maintenance | Simple cleaning and long-lasting performance. |
With these advantages, it’s clear why the 3 jaw chuck is one of the most widely used work-holding devices in machining. However, while it excels in speed and convenience, it does have some limitations—which we will explore in the next section.
Disadvantages of a 3 Jaw Chuck
While a 3 jaw chuck offers speed, efficiency, and self-centering capabilities, it also has limitations that machinists should consider. Understanding these drawbacks can help in selecting the right chuck for specific machining needs.
Limited Flexibility in Workpiece Shapes
A 3 jaw chuck is ideal for cylindrical and hexagonal workpieces, but it cannot securely hold irregularly shaped materials. Unlike a 4 jaw chuck, which allows independent jaw movement, a 3 jaw chuck restricts work-holding capabilities.
✔ Best for: Round and hexagonal workpieces.
✖ Not ideal for: Square, rectangular, or irregularly shaped parts.
For applications requiring off-center machining or asymmetrical workpieces, a 4 jaw chuck or independent jaw chuck may be more suitable.
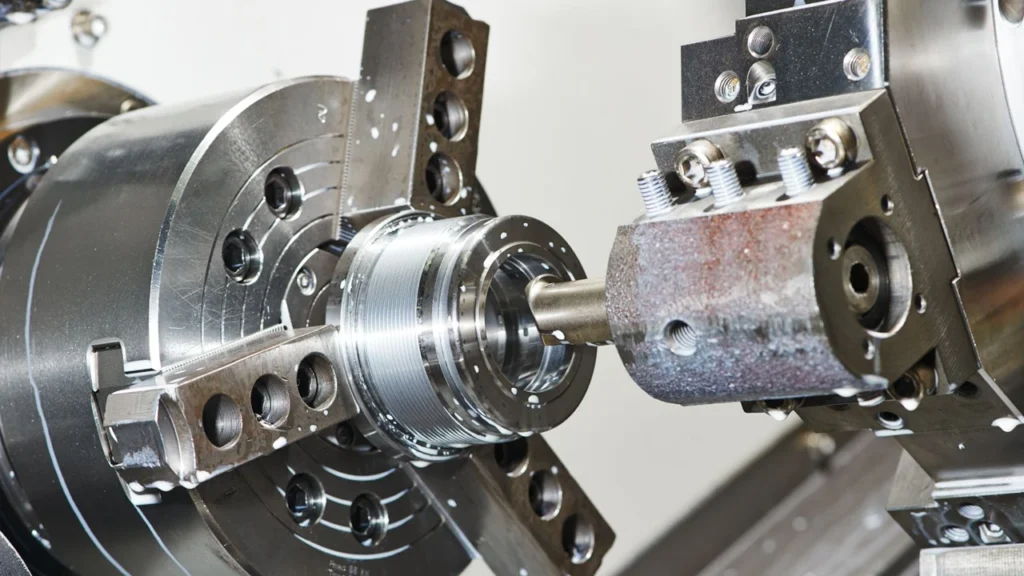
Lower Precision Compared to Independent Chucks
Although a 3 jaw chuck self-centers, it may not always be perfectly precise. This is due to:
✔ Scroll Plate Wear: Over time, the scroll plate may develop wear, causing slight misalignment.
✔ Inability to Adjust Each Jaw Independently: Unlike a 3 jaw independent chuck, this type does not allow for fine adjustments to eliminate runout.
For applications that require extremely high accuracy, such as grinding or fine finishing, machinists often opt for a 4 jaw chuck or a 3 jaw adjustable chuck for better precision.
Reduced Clamping Force Compared to 4 Jaw Chucks
A 3 jaw chuck applies uniform pressure, but the gripping force is lower than a 4 jaw chuck. This can be a disadvantage when working with:
✖ Large-diameter workpieces – A 10-inch 3 jaw chuck or 12-inch 3 jaw chuck may struggle to securely grip heavy or oversized parts.
✖ High-torque machining – When performing heavy-duty turning, workpieces may slip under extreme cutting forces.
For high-torque applications, a 4 jaw chuck or a hydraulic 3 jaw chuck can provide greater holding strength.
Inability to Offset Workpieces
A 3 jaw chuck self-centers, meaning it cannot offset workpieces for eccentric turning or specialized machining. In contrast, a 4 jaw independent chuck allows machinists to position a workpiece off-center for custom cutting and boring operations.
✔ Best for: Standard concentric machining.
✖ Not ideal for: Offset turning, specialized boring, or eccentric cutting.
If an operation requires asymmetrical machining, a 4 jaw lathe chuck is the better choice.
Requires Regular Maintenance for Accuracy
Over time, a 3 jaw chuck may develop alignment issues due to:
✔ Jaw Wear: Frequent use can cause jaw misalignment, reducing gripping accuracy.
✔ Accumulation of Debris: Metal shavings, dirt, and coolant can build up, affecting the chuck’s performance.
To maintain optimal accuracy, regular cleaning, lubrication, and inspection are necessary. A 3 jaw chuck assembly guide can help with proper maintenance procedures.
Key Disadvantages Summary
Disadvantage | Impact |
---|---|
Limited to Symmetrical Shapes | Cannot grip square, rectangular, or irregular workpieces. |
Lower Precision Over Time | Scroll plate wear can cause slight misalignment. |
Reduced Clamping Force | Less holding power for large or heavy parts. |
Cannot Offset Workpieces | Not suitable for eccentric or specialized machining. |
Requires Regular Maintenance | Debris buildup can affect accuracy. |
While a 3 jaw chuck is a go-to choice for general machining, its limitations make it less suitable for specialized tasks. Knowing when to use a 3 jaw chuck versus a 4 jaw chuck or an independent jaw chuck ensures that machinists select the best tool for their needs.
Applications of a 3 Jaw Chuck
A 3 jaw chuck is widely used in metalworking, woodworking, and precision machining due to its self-centering ability, quick setup, and strong gripping force. It is a go-to tool for many industrial and manufacturing applications, ranging from CNC machining to manual lathe operations.
Lathe Operations
A lathe 3 jaw chuck is commonly used for turning cylindrical and hexagonal workpieces. It provides secure clamping, making it ideal for:
- Turning and Facing – Creating precise outer diameters and flat surfaces.
- Drilling and Boring – Holding parts securely for accurate hole drilling.
- Thread Cutting – Essential for making threaded shafts and pipe fittings.
For machinists using CNC 3 jaw chucks or manual lathe 3 jaw chucks, the self-centering feature speeds up part alignment, reducing setup time and increasing efficiency.
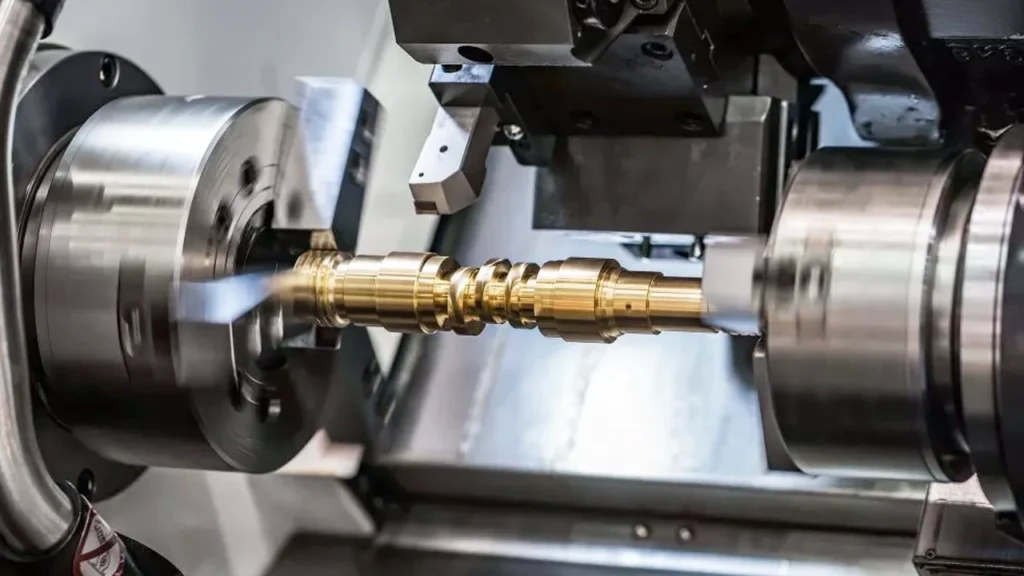
Milling Machine Applications
While primarily used in lathes, a 3 jaw chuck for milling machines is also valuable for rotary milling operations. It allows machinists to:
- Hold Round Workpieces – Useful for cutting slots and keyways in cylindrical parts.
- Secure Tubing and Pipes – Ensures stability while milling round stock.
- Indexing Operations – Allows precision multi-face milling with indexing attachments.
Using a 3 jaw milling chuck enhances workpiece stability, leading to better surface finishes and improved machining accuracy.
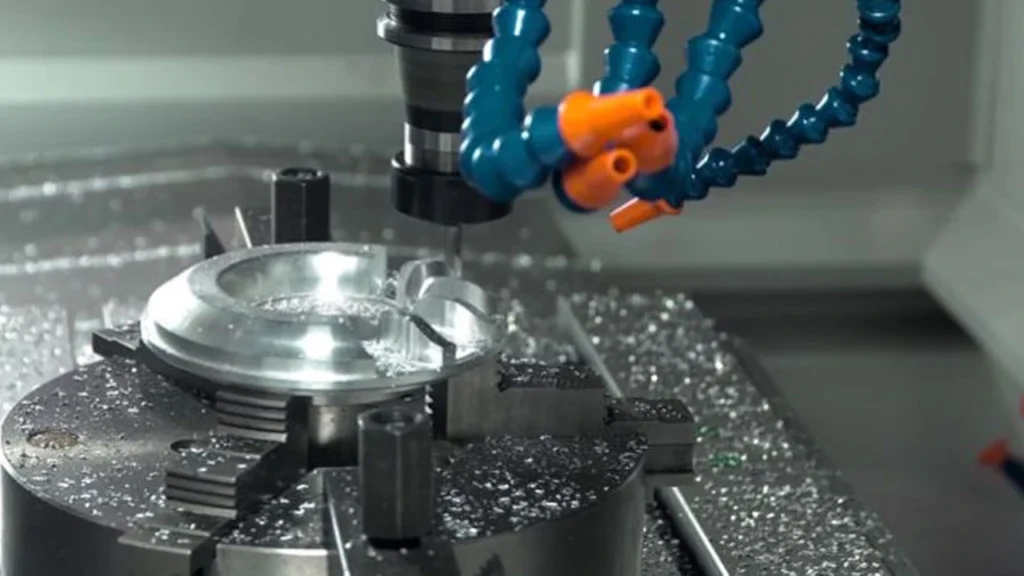
Drilling and Tapping
A 3 jaw chuck for drill presses provides a firm grip on drill bits, ensuring accurate hole placement. Common applications include:
- Metal Drilling – Used in 3 jaw drill chucks for machining steel, aluminum, and brass.
- Wood Drilling – Found in 3 jaw chucks for wood lathes for high-precision woodworking.
- Tapping – Holds taps firmly for creating internal threads.
Machinists can also use 3 jaw chucks for drill presses in vertical milling machines to hold reamers, counterbores, and spot drills.
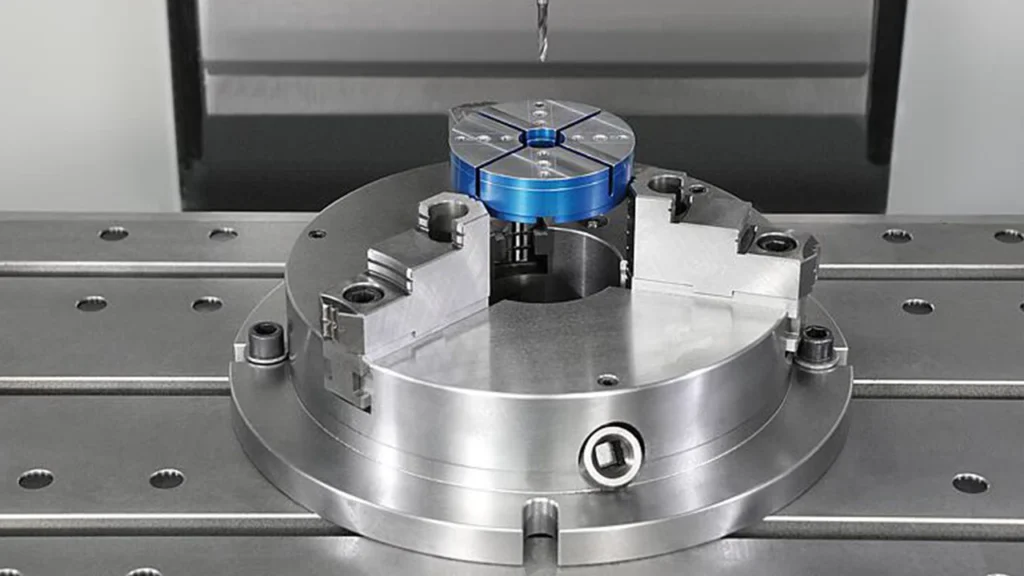
Woodturning and Woodworking
A 3 jaw chuck for wood lathes provides a secure hold on wooden blanks, making it essential for:
- Shaping Round Wooden Parts – Used for making bowls, spindles, and furniture components.
- Hollowing Operations – Allows controlled interior shaping of wood pieces.
- Ornamental Woodturning – Enables precision carving with multi-axis adjustments.
Woodworkers often use adjustable 3 jaw chucks to customize the clamping force, reducing damage to delicate materials.
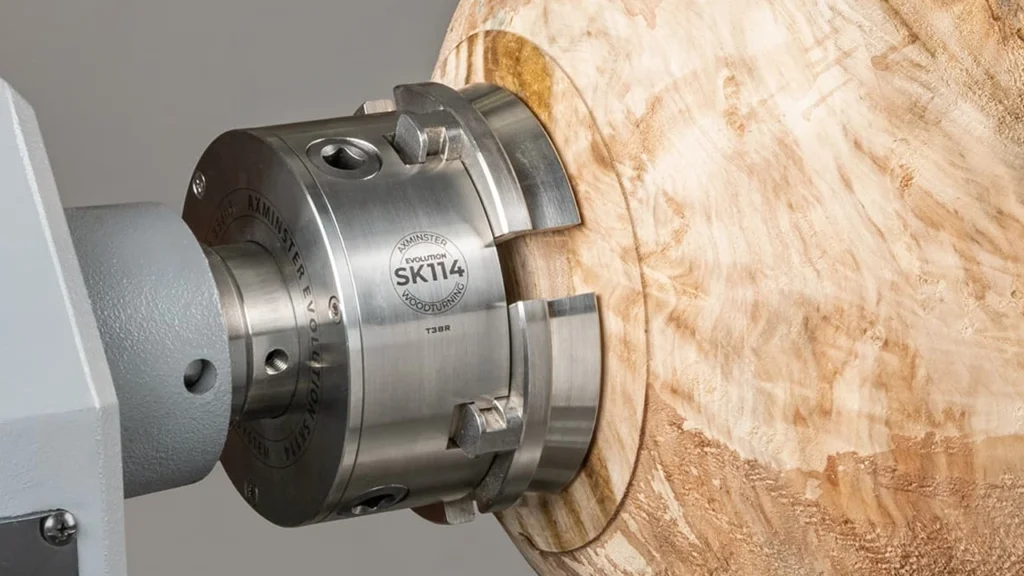
Metal Fabrication and Welding
A 3 jaw chuck for metal lathe machines plays a crucial role in fabrication shops, where it is used for:
- Holding Tubes and Pipes – Ensures accurate cutting and threading.
- Welding Positioning – Helps align workpieces for precision welding.
- Rotary Grinding – Found in 3 jaw metal lathe chucks for finishing metal surfaces.
Heavy-duty options like 10-inch 3 jaw chucks and 12-inch 3 jaw chucks handle large-diameter metal parts, while mini 3 jaw chucks are used for small precision components.
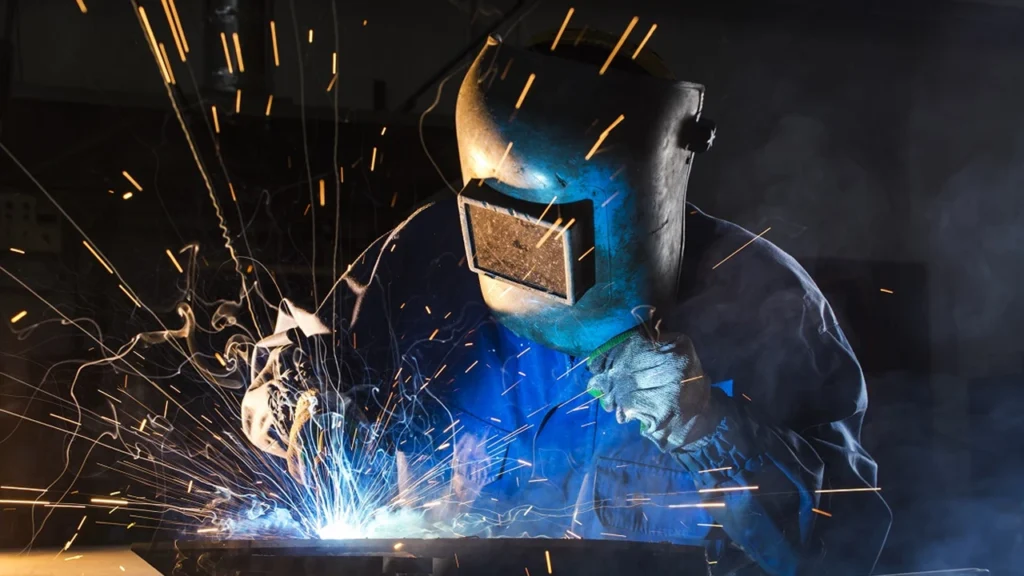
Industrial Automation and CNC Machining
CNC machines often use hydraulic 3 jaw chucks, pneumatic 3 jaw chucks, or electric 3 jaw chucks for fast, repeatable, and automated machining. These are ideal for:
- High-Speed Production – Automates clamping in CNC lathes and milling machines.
- Precision Machining – Used in high-accuracy 3 jaw power chucks.
- Robotic Assembly – Common in automated manufacturing for quick part changes.
Many CNC applications require precision 3 jaw chucks with adjustable runout control to maintain tight tolerances during mass production.
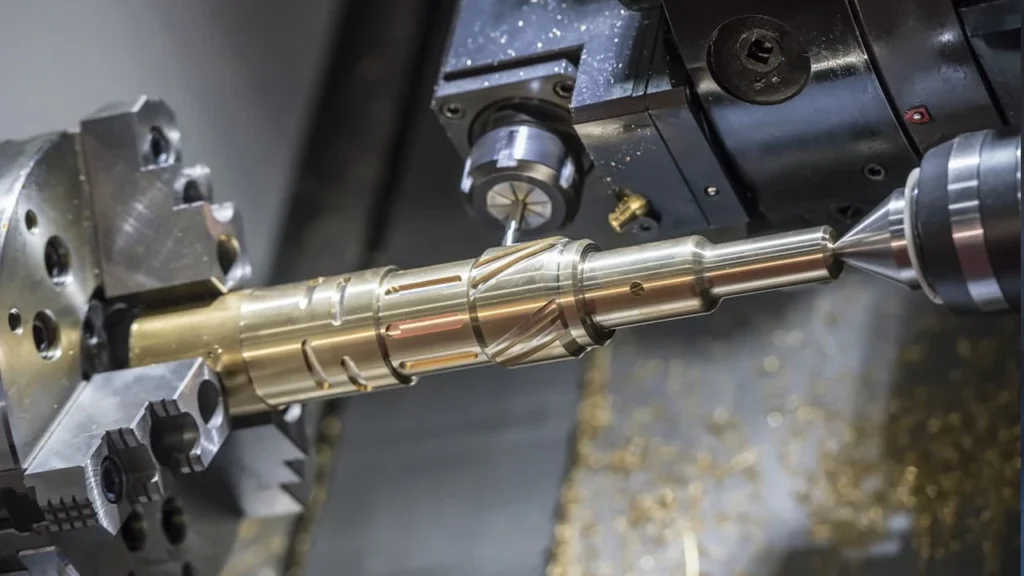
Summary of 3 Jaw Chuck Applications
Application | Common Uses |
---|---|
Lathe Operations | Turning, facing, boring, and threading. |
Milling Machines | Slotting, indexing, and pipe machining. |
Drilling & Tapping | Holding drill bits, taps, and reamers. |
Woodworking | Woodturning, hollowing, and shaping. |
Metal Fabrication | Cutting, threading, and welding. |
CNC Automation | High-speed, repeatable precision machining. |
A 3 jaw chuck is a versatile, time-saving, and essential tool for machinists, fabricators, and woodworkers. However, choosing the right chuck type and size is critical for achieving optimal performance and accuracy in different applications.
Comparison: 3 Jaw Chuck vs 4 Jaw Chuck
Both 3 jaw chucks and 4 jaw chucks are commonly used for workpiece clamping in machining, but they each have distinct advantages and applications. Understanding the differences between them will help machinists choose the right chuck for their specific needs.
Key Differences Between a 3 Jaw Chuck and a 4 Jaw Chuck
Feature | 3 Jaw Chuck | 4 Jaw Chuck |
---|---|---|
Jaw Movement | All three jaws move simultaneously (self-centering). | Each jaw moves independently. |
Workpiece Types | Best for cylindrical and hexagonal workpieces. | Can hold round, square, rectangular, and irregular shapes. |
Setup Time | Quick and easy due to self-centering mechanism. | Requires manual alignment, increasing setup time. |
Precision | Less precise due to fixed jaw movement. | Higher precision as each jaw is adjusted independently. |
Gripping Force | Even pressure distribution, but lower clamping force. | Stronger grip for off-center and asymmetrical workpieces. |
Best Use Case | High-speed production, general machining. | Eccentric turning, custom work, heavy-duty machining. |
A 3 jaw chuck is perfect for fast, repetitive machining, while a 4 jaw chuck is better suited for irregularly shaped workpieces that require manual adjustment for precision alignment.
When to Use a 3 Jaw Chuck
A 3 jaw chuck is the best choice when:
- Speed and efficiency are required, such as in high-volume production.
- The workpiece is cylindrical or hexagonal and does not require fine adjustments.
- The machining process demands quick setup and easy operation.
- The application involves CNC automation using hydraulic or pneumatic 3 jaw chucks.
Machinists often use 3 jaw chucks for lathes, milling machines, and drill presses where time efficiency is critical.
When to Use a 4 Jaw Chuck
A 4 jaw chuck is more suitable when:
- The workpiece is square, rectangular, or irregularly shaped.
- Eccentric turning (off-center machining) is required.
- Higher gripping force and adjustability are needed.
- Manual precision alignment is necessary to eliminate runout.
4 jaw independent chucks are commonly used in metal fabrication, heavy-duty machining, and precision turning applications.
Pros and Cons of a 3 Jaw Chuck
✔ Pros:
- Self-centering for quick and easy setup.
- Best for cylindrical workpieces.
- Works well in automated CNC applications.
- Even gripping pressure distribution.
✖ Cons:
- Less precise than a 4 jaw chuck.
- Limited to round and hexagonal workpieces.
- Cannot adjust each jaw independently.
Pros and Cons of a 4 Jaw Chuck
✔ Pros:
- Can hold irregularly shaped workpieces.
- Provides greater clamping force.
- Allows for precision alignment.
- Can offset workpieces for eccentric machining.
✖ Cons:
- Slower setup time due to manual jaw adjustments.
- Requires skill to center workpieces accurately.
- Not ideal for quick, high-volume production.
Which Chuck Should You Choose?
Machining Requirement | Best Choice |
---|---|
Speed and high-volume production | 3 Jaw Chuck |
General machining of round parts | 3 Jaw Chuck |
Precision turning with adjustable clamping | 4 Jaw Chuck |
Machining irregular workpieces | 4 Jaw Chuck |
Offset or eccentric machining | 4 Jaw Chuck |
A 3 jaw chuck is best for fast, efficient machining, while a 4 jaw chuck is better for precision work and irregular shapes. Many machinists keep both chucks on hand to switch between them as needed.
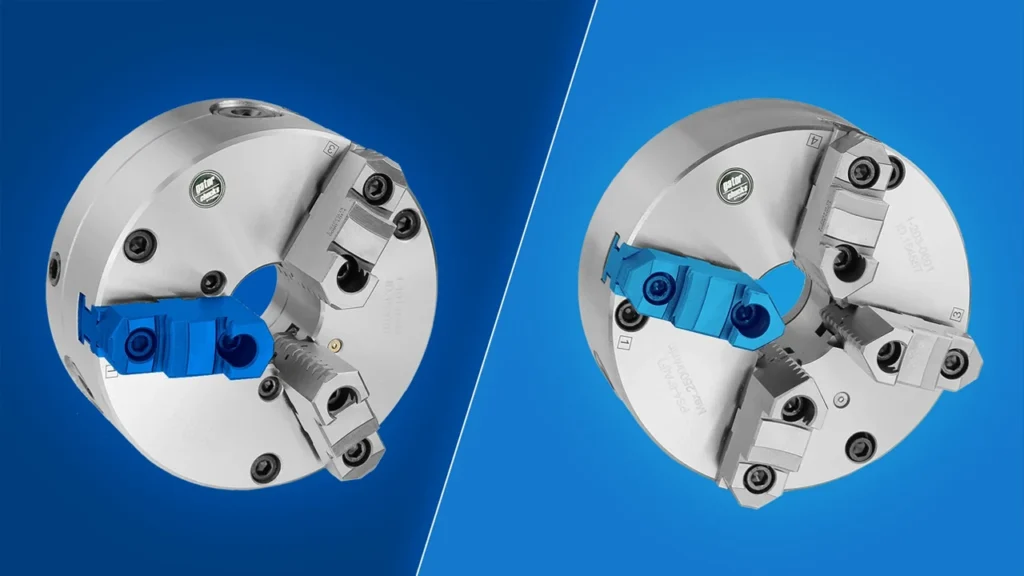
How to Maintain a 3 Jaw Chuck
Proper maintenance of a 3 jaw chuck is essential for ensuring consistent accuracy, smooth operation, and extended lifespan. Over time, debris, wear, and misalignment can reduce performance, leading to poor workpiece grip, increased runout, and machining errors. Regular care and maintenance will keep your 3 jaw chuck operating at peak efficiency.
Cleaning and Removing Debris
Metal shavings, dust, and coolant residue can accumulate inside a 3 jaw chuck, affecting its movement and precision. To prevent buildup:
- Remove the chuck from the machine – Unmount the chuck periodically for a deep clean.
- Blow out debris – Use compressed air to remove chips from the scroll plate and jaws.
- Use a cleaning solvent – Apply degreasers or machine cleaning solutions to dissolve built-up dirt and oil.
- Wipe and dry thoroughly – Moisture buildup can cause rust and corrosion.
Regular cleaning prevents misalignment issues and extends the life of the chuck’s moving parts.
Lubrication for Smooth Operation
A 3 jaw chuck consists of several moving components, including the scroll plate, pinion gears, and jaws, which require proper lubrication to function smoothly.
- Apply grease to the scroll plate and gears – Use a high-quality machine tool lubricant for smooth jaw movement.
- Use light oil on the jaws – This reduces friction and prevents wear on the clamping surfaces.
- Avoid over-lubrication – Excess grease can attract debris, causing clogging.
Lubrication helps prevent jaw stiffness, ensuring that your 3 jaw chuck self-centering mechanism remains accurate.
Checking for Wear and Misalignment
Over time, continuous use can cause jaw misalignment and uneven wear. To maintain precision:
- Inspect jaws for wear – If the jaws show signs of uneven wear, they may need resurfacing or replacement.
- Check for scroll plate wear – Excessive wear on the scroll plate can lead to poor centering accuracy.
- Test for runout – Use a dial indicator to check if the chuck is properly aligned.
For precision machining, a 3 jaw adjustable chuck allows machinists to compensate for slight wear by fine-tuning alignment.
Replacing Worn or Damaged Parts
If any component of the 3 jaw chuck becomes damaged, replacing it promptly ensures continued accuracy and safety. Common replacement parts include:
- 3 jaw chuck jaws – Worn jaws can lead to slippage and misalignment.
- Pinion gears – Damaged gears can prevent smooth jaw movement.
- Backplates – A misaligned or worn backplate may affect overall chuck performance.
Always use OEM (original equipment manufacturer) parts for replacements to maintain compatibility with your lathe 3 jaw chuck.
Best Practices for Long-Term Performance
Maintenance Task | Frequency | Purpose |
---|---|---|
Blowing out debris | After every use | Prevents chip buildup and misalignment. |
Wiping with solvent | Weekly | Removes grease, dirt, and coolant residues. |
Lubricating gears | Monthly | Ensures smooth jaw movement and reduces wear. |
Checking for runout | Every 3 months | Maintains precision and workpiece accuracy. |
Replacing worn jaws | As needed | Prevents slippage and maintains grip strength. |
By following these routine maintenance steps, machinists can extend the service life of their 3 jaw chuck and maintain optimal machining accuracy.
Conclusion
A 3 jaw chuck is a versatile, efficient, and widely used work-holding device in machining. Its self-centering mechanism, quick setup, and uniform gripping force make it an essential tool in lathe operations, milling, drilling, and woodworking.
Throughout this guide, we have explored:
- What a 3 jaw chuck is and how it works.
- Different types of 3 jaw chucks and their applications.
- The advantages and disadvantages of using a 3 jaw chuck.
- How it compares to a 4 jaw chuck.
- Essential maintenance practices to extend its lifespan.
Whether you are a professional machinist, CNC operator, or woodworking enthusiast, understanding how to properly use and maintain a 3 jaw chuck ensures higher precision, efficiency, and reliability in your machining projects.
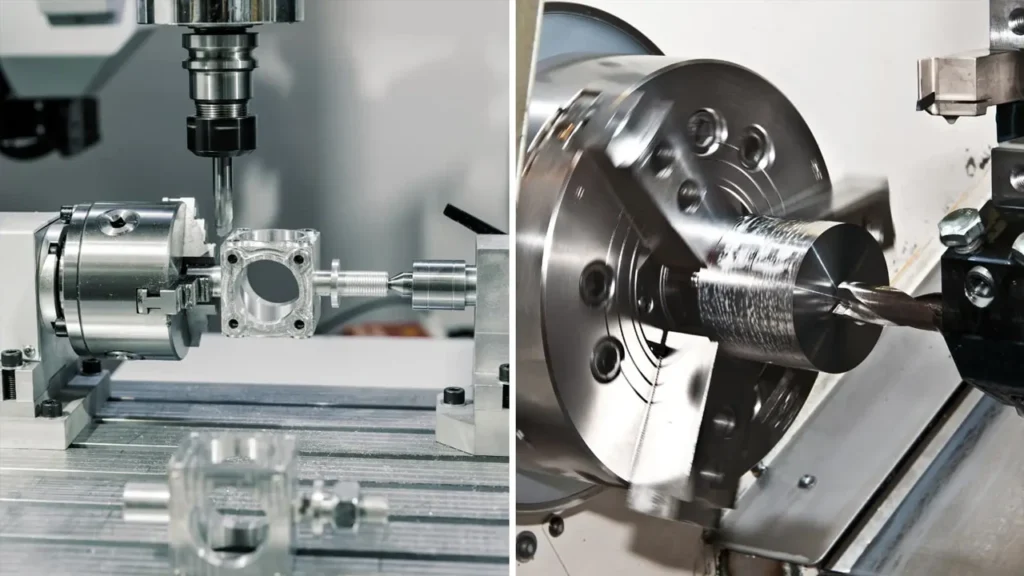
While a 3 jaw chuck is perfect for quick and repeatable clamping, it does have limitations in precision and flexibility. Choosing between a 3 jaw chuck and a 4 jaw chuck depends on the specific machining requirements of the project.
For those seeking higher precision, investing in adjustable 3 jaw chucks or hydraulic and pneumatic 3 jaw chucks can further enhance machining performance.
With proper care, lubrication, and maintenance, a 3 jaw chuck will remain a dependable tool for years, delivering consistent results in metalworking, woodworking, and industrial applications.
Need Help Choosing the Right 3 Jaw Chuck?
If you’re looking for the best 3 jaw chuck for your lathe, milling machine, or CNC setup, feel free to contact us for expert advice!